
Строительные и дорожные машины. Основы автоматизации
.pdf454
ду собой так, что при нажатии на одну из них сбрасывается на бор кнопок двух рядов.
Предположим, что груз должен быть поднят на 25 м. Набрав в первом ряду (десятки) кнопку под цифрой, например 2, во втором ряду (единицы) цифру .5, машинист задает программу подъема. Затем закрывает затвором батарею СБ2. Магнитный усилитель МУ1 включает реле Р, и происходит разгон по заранее заданной скоростной диаграмме.
К торцу подъемного механизма крепится диск Д с отверстием. С одной стороны диска установлена лампочка ЛО, с другой − полупроводниковая батарея СБЗ. При каждом повороте диска батарея СБЗ освещается лампочкой ЛО. Дается сигнал в виде импульса на обмотку 7К−2Н усилителя МУЗ (блок БЗ). К блоку подключены катушки РШИВ и РШИН реверсивного шагового искателя. Так как программа задана на подъем, замкнут контакт В и работает катушка шагового искателя «вперед». При каждом импульсе, который подает на усилитель МУЗ батарея СБЗ, шаговый искатель поворачивается на одну ламель. Поскольку нажаты кнопки К20 и К5, то создается цепь К20 К5 − РШИ25 − KT − РТ, когда реверсивный шаговый искатель подойдет своей 25-й ламелью к сочетанию кнопок 25. Реле РТ разрывает свой контакт РТ в цепи обмотки МУЗ, в связи с чем прекращается дальнейшее движение ламелей шаговых искателей. Размыкаются контакты РТ и замыкаются контакты РТ в цепи Дрз. Двигатель реверсируется и начинается замедление привода (по заданному закону).
Регулятор замедления состоит из тахогенератора Г и тормозного двигателя ТД. К цепи Г−ТД подключена через потенциометр RK обмотки 2Н−7К усилителя МУ6 (блок Б6). С усилителя МУ6 получает питание реле Р3, срабатывающее с выдержкой времени. Параллельно якорю Г включено реле напряжения 1РС.
При разных грузах сила тока в цепи, в которую включено реле замедления, будет различной. Поэтому при легких грузах время замедления будет больше, чем при номинальном грузе. После соответствующей выдержки времени срабатывает реле РЗ, и включается контактор динамического торможения КТД. Скорость уменьшается, и реле отпускает свои контакты. Когда скорость движения становится равной скорости дотяжки, реле 1РС разомкнет свои контакты в цепи Дрз, двигатель отключится, а сельсин отработает напряжение, определяемое скоростью дотяжки. Реле РВ2 включит свои контакты в цепи обмотки 7Н−2Н усилителя МУ4. Когда отверстие диска на торце лебедки подойдет к осветителю, контактор Ти разорвет цепь контактора Дт , и привод остановится тормозом.
Допустим теперь, что в рассматриваемой системе автоматического управления краном несколько исполнительных механизмов должны действовать по определенной программе, а цикл состоит из подъема крюка, поворота платформы крана, опускания крюка и останова.
Машинист набирает программу кнопками на пульте подъемной лебедки, соответствующими заданной высоте подъема, на пульте поворота — заданному углу поворота и на пульте стрелы — определенному расстоянию до оси груза. После подъема на заданную высоту включается реле связи подъема, дающее
455
сигнал на начало поворота, а после поворота на заданный угол шагоискатель вращения включает реле связи вращения. Операции прекращаются в точках, заданных кнопками. Реле связи механизма вылета стрелы дает сигнал на опускание крюка, и кран останавливается.
При длинных канатах и больших грузах на точность выполняемой операции будет оказывать влияние удлинение каната. Для устранения этого недостатка используется метод магнитных меток, нанесенных на канат записывающей головкой при пропускании через ее обмотку импульса тока. Силовые линии возникающего магнитного поля пересекают канат в продольном направлении и оставляют на нем магнитную метку (постоянный магнит). Запись магнитных меток производится через равные промежутки времени при постоянной скорости движения каната. Сигналы управления получаются непосредственно от магнитных меток на канате. Устройство воспроизведения меток подает сигнал на устройство, определяющее направление движения каната, и далее на счетчик, суммирующий и вычитающий путевые импульсы. Следующий за счетчиком дешифратор декодирует состояние счетчика, и с выхода дешифратора сигналы поступают в блок путевых команд, где усиливаются и посылаются в цепь управления системы.
Метод магнитных меток может быть применен как для систем с реверсивным шаговым искателем, так и для цифровых систем автоматического управления краном.
При постоянстве задачи использования крана и стабильной обстановки на месте производства работ каждый последующий цикл движений крановых механизмов может частично, а иногда и полностью повторять предыдущий. В этих случаях программа задается машинистом путем выполнения первого цикла перемещения органов управления вручную и тем самым закладывается в устройство памяти. В дальнейшем все рабочие перемещения производятся механизмами крана самостоятельно, а машинист лишь контролирует работу машины и вводит в программу необходимые коррективы по мере изменения обстановки. Запоминание производится путем записи программы на магнитной ленте. В устройство для считывания предварительно закладываются критерии оптимальной работы всех механизмов крана и при считывании производится автоматическая корректировка работы механизмов по заложенным критериям.
Одним из способов записи программы на магнитную ленту является предварительная запись образцовых циклов работы крана методом фазовой модуляции.
Командным сигналом в таких системах управления служат сигналы рассогласования, возникающие при появлении фазного угла между сигналом, считываемым с магнитной ленты, и сигналом обратной связи, поступающим от сель- син-датчика. Сельсин-датчик отображает истинное положение исполнительного механизма, а сдвиг по фазе равен геометрическому углу поворота ротора относительно статора.

456
Устройство программного управления для механизмов поворота и вылета стрелы состоит из стенда управления с магнитной лентой, квантователя рассогласования, релейного блока и датчика положения. Исполнительные механизмы оборудованы тормозом и стендом с контакторами и реле ускорения.
Блок-схема программного управления в режиме записи приведена на рис. 11. 12, а. В этом режиме кран управляется контроллером. На сельсин-датчик 4 поступает эталонный сигнал от генератора 1, который преобразуется и усиливается фазорасщепителем 2 и усилителем 3. С роторной обмотки сельсина 4 снимаются рабочие сигналы, промоделированные в соответствии с законом движения механизма. Рабочие сигналы одновременно с эталонными записываются на магнитную ленту.
В режиме воспроизведения (рис. 11. 12, б) рабочие и эталонные сигналы усиливаются. Эталонный сигнал от генератора расщепляется фазорасщепителем 2, усиливается в усилителе 3 и возбуждает датчик положения 4. С датчика сигнал поступает на один вход дискриминатора 6.
Рис. I1.12. Блок-схема программного управления механизмом поворота
а) − блок-схема программного управления в режиме записи; б) − блок-схема воспроизведения; р − программируемая координата; э − эталонный сигнал; 1− генератор; 2− фазорасщепитнль; 3, 5− усилители; 4− сельсин; 6− дискриминатор; 7, 8 – блоки преобразования
На другой вход дискриминатора через усилитель 5 подаются рабочие сигналы с магнитной ленты. В дискриминаторе сигналы сравниваются, и при наличии рассогласования, на выходе дискриминатора появляется непрерывный сигнал, который квантуется на несколько уровней квантователем рассогласования. В зависимости от уровня рассогласования релейный блок производит те или иные переключения на контакторной панели или включает тормоз.
В позиционных системах числового программного управления (ЧПУ) кранами значения координат перемещения задаются клавишами или автоматически от центрального электронного управляющего устройства. Сравнивающее решающее устройство производит непрерывное сравнение действительного положения по данной координате с заданным. На выход решающего устройства подключено декодирующее устройство, посылающее в схему управления исполнительным механизмом сигнал торможения, когда кран приближается к заданной позиции.

457
Позиционная система (ЧПУ) обеспечивает возможность непосредственной связи с ЭВМ, управляющей всем комплексом погрузочно-разгрузочных работ.
В системах программного управления кранами находит применение также автоматическое адресование транспортируемых грузов.
При работе башенных кранов на монтаже полносборных сооружений основными задачами управления являются подача конструкций и точная их установка на месте монтажа. С этой целью применяется комбинированная система дистанционного программного управления, включающая в себя два устройства: дистанционного управления краном и программного управления с автоматическим адресованием транспортируемых конструкций.
При монтаже операции по доставке деталей со склада или непосредственно с транспортных средств на здание осуществляются с помощью автоматической системы адресования и программного управления краном, а точная установка конструкций – дистанционным управлением на малых скоростях подъема и опускания груза.
Рассмотрим применение кранов с автоматическим управлением на примере подъемного башенного крана с системой радиопрограммного управления, предназначенного для выполнения работ по монтажу зданий из крупносборных элементов. В рассматриваемой системе автоматического управления функции машиниста заменены программным управлением по транспортированию груза и дистанционным управлением на установке и строповке элементов. Все управление краном ведется двумя операторами: такелажником на складе и монтажником на строящемся здании.
Программа определяется участками, на которые разбиты согласно технологической схеме строительства склад и здание. Здание разделено на восемь участков, склад — на четыре. Выбор такого числа участков обусловлен способом управления, при котором движение крана, имеющее наибольшую по времени длительность, уменьшается за счет совмещения движений и увеличения времени включения наименьшего из движений.
Блок-схема радиопрограммного управления (рис. 11. 13) состоит из двух пультов управления ПУ-1 и ПУ-2, приемного устройства, устройства программного управления и датчиков Д1, Д2, ДЗ и Д4, определяющих «адрес», по которому должен быть доставлен груз при отработке программы.
Рис. I1.13. Блок-схема радиопрограммного управления ПУ − пульт управления; Д − датчик адресов
458
Работает кран следующим образом. При застроповке панели на складе такелажник дистанционно управляет процессом, находясь рядом с застроповываемой панелью. После застроповки он поднимает панель на безопасную высоту, задает нужную программу («адрес») и подает сигнал «пуск». При этом кран автоматически доставляет панель в заданный участок на здании по кратчайшей траектории. Программа задается только на одну операцию.
После автоматического выполнения операции по грубому транспортированию панели на здание второй оператор (монтажник) дистанционно выполняет операции по точной установке панели и расстроповке, затем набирает «адрес» склада, выводит пустой крюк в безопасную высоту и переводит кран на автоматическое управление. Кран автоматически выполняет операцию подачи пустого крюка в заданный участок склада, затем операция повторяется.
Для обеспечения безопасной работы на кране с радиопрограммным управлением блокирована возможность одновременного управления с двух пультов, кроме сигналов «аварийный стоп» и «сирена».
11.2.Автоматизация землеройно-транспортных машин
иэкскаваторов
Земляные работы представляют собой ответственный и чрезвычайно трудоемкий класс работ, нуждающийся в дальнейшей механизации и автоматизации. Такими видами работ являются: планировка строительных площадок и дорог, перемещение масс грунта, отрывка котлованов, траншей и другие работы. Машины, используемые на земляных работах, весьма разнообразны. Основная часть земляных работ выполняется землеройно-транспортными машинами и экскаваторами.
Землеройно-транспортные машины осуществляют резание и перемещение грунта при одновременном поступательном движении самой машины. По характеру технологического процесса они могут быть разделены на машины непрерывного и циклического действия.
К землеройно-транспортным машинам непрерывного действия относятся грейдеры (автогрейдеры), применяемые, например, для планировочных работ, и грейдер-элеваторы, у которых операции резания и перемещения грунта не носят циклического характера.
Грейдеры (автогрейдеры) предназначены главным образом для профилирования и отделки земляного дорожного полотна, общей планировки и расчистки строительного участка и других видов строительных работ.
Грейдер-элеваторы представляют собой землеройно-транспортные машины, предназначенные для резания грунта и его одновременного перемещения в отвал или в транспортные средства. Рабочими органами грейдер-элеваторов являются нож и ленточный транспортер.
459
К землеройно-транспортным машинам циклического действия относятся скреперы и бульдозеры, рабочий процесс которых характеризуется периодической повторяемостью операций.
При работе скрепера последовательно выполняются операции резания, набора грунта в ковш, транспортирования и выгрузки. Цикл работы бульдозера складывается из операций рабочего хода (резание и транспортирование грунта) и операции холостого хода при возвращении в забой.
Отличительные особенности технологических процессов землеройнотранспортных машин непрерывного и циклического действия определяют целесообразность раздельного рассмотрения вопросов их автоматизации. В то же время возможен общий подход в постановке задач автоматизации, принципах и способах их решений для машин обеих групп. При этом следует различать такие задачи, как: 1) обеспечение требуемого качества обрабатываемой поверхности (например, заданного профиля поверхности); 2) поддержание нагрузки (стабилизация нагрузки) двигателя на заданном (оптимальном) уровне.
С точки зрения принципа решения задачи автоматического поддержания заданной нагрузки двигателя, определяемого технологическими задачами производства, земляные работы, выполняемые землеройно-транспортными машинами на строительстве, можно условно разделить на две группы:
1.Работы по планировке и отделке поверхности при минимальном объеме перемещаемого рабочим органом грунта. Эффективность использования машин при выполнении таких работ определяется количеством и качеством обработанной площади.
2.Работы по устройству выемок и насыпей, связанные с перемещением сравнительно больших объемов грунта, при выполнении которых эффективность использования машин определяется объемом перемещенного грунта.
В первом случае при сравнительно малом усилии на перемещение грунта поддержание заданной мощности двигателя может быть достигнуто путем изменения скорости движения машины, так как необходимость в значительном заглублении рабочего органа отсутствует.
Во втором случае необходимо большое заглубление рабочего органа, и поддержание заданной мощности двигателя может быть достигнуто изменением положения рабочего органа (толщины срезаемого слоя грунта).
Для тяжелых самоходных землеройно-транспортных машин перспективно применение электрического и гидравлического приводов, в которых электрический и гидравлический двигатель встраивается в колесо. В строительных машинах с мотор-колесами высокие регулировочные свойства электрических и гидравлических приводов сочетаются с полной кинематической независимостью компоновки любой машины, что обусловливает универсальность трансмиссий с мотор-колесами, т. е. возможность их применения в неизменном виде на машинах различного типа. Универсальные трансмиссии с индивидуальным приводом колес обеспечивают автоматическое использование максимальной тяги по сцеплению, что особенно важно для землеройно-транспортных машин
460
как непрерывного, так и циклического действия, работающих в тяжелых условиях.
Экскаваторы являются землеройными машинами, осуществляющими копание и перемещение грунта. По технологическими конструктивным особенностям экскаваторы разделяются также на две группы:
1.Экскаваторы непрерывного действия. Экскаваторы непрерывного дей-
ствия позволяют производить операции копания и перемещения грунта одновременно. В процессе работы, например, многоковшового экскаватора следующие друг за другом ковши рабочего органа разрушают, забирают, перемещают и разгружают грунт. Экскаваторы непрерывного действия применяются для строительства траншей под трубопроводы и сети коммуникаций, на мелиоративных работах и разработке карьеров строительных материалов.
2.Одноковшовые экскаваторы циклического действия. Рабочий процесс одноковшового экскаватора складывается из отдельных циклов. Цикл работы состоит из операций опускания ковша в забой, копания (отделение грунта от массива, наполнение ковша и его подъем вверх), поворота платформы, открывания ковша, разгрузки, возвращения в забой с закрыванием ковша. Универсальные одноковшовые экскаваторы, применяемые на строительных работах, имеют сменное оборудование и могут работать как лопата, драглайн или кран.
Особенности технологического процесса и конструкции экскаваторов непрерывного и циклического действия также создают необходимость раздельного рассмотрения вопросов автоматизации работы машин указанных групп. Сложность технологического процесса и напряженность труда машиниста приводят к тому, что автоматизация работ одноковшовых экскаваторов более затруднительна, чем экскаваторов непрерывного действия.
При наличии существенного различия в рабочих режимах экскаваторов непрерывного и циклического действия имеет место общий характер отдельных процессов, что определяет известную аналогию в постановке задач автоматизации, принципах и способах их решения.
Несмотря на большое многообразие машин для земляных работ, можно указать на общие особенности их работы, которые следует учитывать в первую очередь при автоматизации: возможность резких изменений нагрузки, как предполагаемых заранее, так и неожиданных для обслуживающего персонала, тяжелый характер динамических режимов, зависимость условий работы от характеристик разрабатываемого грунта. Исходя из этого, системы автоматического управления землеройными машинами должны обеспечивать получение необходимых характеристик приводов, удобство и простоту управления машиной, надежность и безопасность производства работ и экономичность использования машины.
Особенности технологических процессов и специфика работы землеройнотранспортных машин и экскаваторов затрудняют создание систем автоматического, управления, которые полностью исключили бы участие машиниста в управлении. Это обусловливает применение автоматизации управления теми
461
процессами, которые в большей мере определяют эффективность использования машины.
В рассматриваемых ниже конкретных решениях систем автоматического управления следует отмечать общие принципы подхода к автоматизации рабочих процессов подъемно-транспортных, землеройно-транспортных машин и экскаваторов.
Автоматизация землеройно-транспортных машин непрерывного дейст-
вия. На строительстве дорог и других сооружений большой объем работ составляют планировочные и отделочные работы по устройству земляного полотна определенного профиля или грунтовых оснований, выполняемые с помощью автогрейдера.
Отклонение поперечных профилей от заданных, приводящее к необходимости применения дополнительного ручного труда для окончательной доводки поперечного профиля, определяет одну из задач автоматизации работы автогрейдера — автоматическое управление положением рабочего органа в поперечной плоскости. При этом система автоматического управления должна измерять величину наклона отвала по отношению к горизонту и после ее сравнения с заданной величиной поперечного уклона подавать управляющий сигнал на привод управления. Базой для отсчета в такой системе будет являться горизонт.
Производительность автогрейдера и качество работы определяются правильной установкой отвала не только в поперечной, но и в продольной плоскости. Обеспечение стабилизации положения рабочего органа в продольной плоскости является более трудной задачей. Рабочие операции автогрейдера могут быть определены как резание, перемещение грунта и отделка площади. При резании грунта производительность автогрейдера определяется количеством вырезанного грунта. Машинист стремится при наилучшем режиме работы двигателя срезать как можно больше грунта. Так как работы по резанию ведутся в основном на нижних скоростях, наибольшая производительность машины может быть достигнута на границе буксования ведущих колес. В соответствии с этим система автоматического управления должна контролировать загрузку машины по буксованию.
Рассмотрим некоторые из возможных решений систем автоматического управления работой автогрейдера.
Система управления отвала (рис. 11.14) содержит следующие основные элементы: датчик 6 продольного уклона, датчик поперечного профиля 4, подъемное устройство 5 щупового датчика, блок управления 1, исполнительные устройства — реверсивные гидрозолотники 2 с электрогидравлическим управлением.
Датчик 6 продольного уклона является щуповым прибором. Датчик 4 угла поперечного профиля представляет собой маятник, соединенный с подвижным контактом потенциометра, включенного в мостовую схему. Крепление датчика на тяговой раме автогрейдера осуществляется посредством хомута. Блок управ-

462
ления 1 служит для переключения режимов работы, задания уклона поперечного профиля и для кнопочного управления гидроцилиндрами подъема тяговой рамы с отвалом.
Стабилизация положения рабочего органа в продольном направлении производится следующим образом: при движении автогрейдеpa щуп датчика перемещается по опорной базе, определяющей требуемый продольный профиль поверхности. В качестве базы можно использовать проволоку или трос, натянутый вдоль поверхности, которую необходимо профилировать. Если угловое положение щупа превысит величину зоны нечувствительности системы, с датчика поступает сигнал на усилитель в блоке управления. В результате замыкается цепь питания электромагнита гидрозолотника. С помощью гидроцилиндра происходит перемещение рабочего органа, которое прекращается, когда щуп, скользя по опорной базе, снова возвратится в зону нечувствительности. При этом электромагнит гидрозолотника отключается.
Рис.11.14. Установка элементов автоматики на автогрейдере:
1− блок управления; 2− гидрозолотник; 3− гидропривод; 4− датчик поперечного профиля; 5− подъемное устройство; 6− датчик продольного профиля
Стабилизация положения рабочего органа в поперечном направлении осуществляется с помощью маятникового датчика угла, который установлен на тяговой раме автогрейдера и воспринимает поперечный уклон отвала. Требуемое угловое положение задается в блоке управления. С помощью мостовой схемы производится сравнение сигнала датчика угла с сигналом, соответствующим заданному угловому положению. При рассогласовании сигналов включается электромагнит реверсивного золотника, и гидроцилиндр перемещает орган в сторону уменьшения рассогласования (до заданного углового положения).
Электрическая схема системы управления (рис. 11.15) состоит из чувствительных элементов датчиков, усилителей сигналов и исполнительных устройств, а также выключателя 1В, электромагнитного арретира ЭА углового датчика, гасящего сопротивления 4, позиционного переключателя 1П выбора режима работы, четырех кнопок 1КУ– 4КУ ручного управления, сигнальных ламп Л1– Л10, переключателей 2П– 4П на режимы «работа — настройка» и предохранителя Пр.
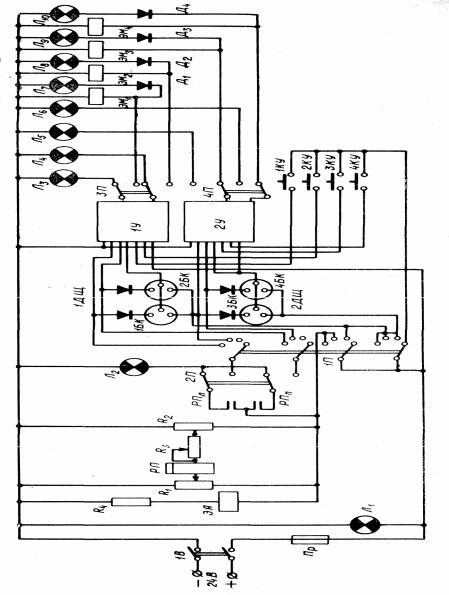
463
Рис.11.15. Электрическая схема управления автогрейдера
Чувствительными элементами щуповых датчиков 1ДЩ и 2ДЩ являются бесконтактные датчики 1БК– 4БК. Генерируемые импульсы этих датчиков преобразуются диодом в постоянное напряжение отрицательной полярности. При введении в паз датчика пластинчатого сектора с выхода усилителя сигнал поступает на усилители 1У или 2У, предназначенные для включения электромагнитов исполнительных механизмов ЭМ1 – ЭМ4 с задержкой по времени, исключающей влияние кратковременных возмущений на работу системы. Чувствительный элемент углового датчика поперечной стабилизации выполнен по мостовой схеме, в которую входят потенциометр датчика угла R1, задающий потенциометр R2 и поляризованное реле РП, включенное в диагональ моста.
Реле РП через свои контакты РПП и РПЛ обеспечивает работу системы с заданным порогом чувствительности, регулируемым потенциометром ЗР («Загрубление»). Диоды Дг−ДА служат для защиты сигнальных ламп Л7 −Л10. При