
DZ_Nikolaicha
.pdf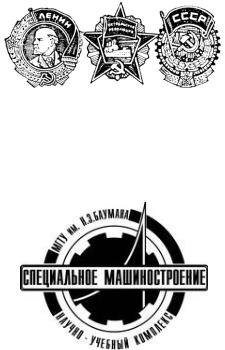
Московский ордена Ленина, ордена Октябрьской Революции и ордена Трудового Красного Знамени Государственный Технический Университет имени Н. Э. Баумана
Домашнее задание по курсу
Организация и планирование машиностроительного производства
Студент : |
Ханеня Н.Н. |
Преподаватель : Слепушкин Ю.Н.
Группа: |
СМ 1-112 |
Вариант: 37
Москва
2010
Оглавление
Часть 1: Расчет производственного цикла .................................................................... |
3 |
|
1.) |
Содержание задачи.................................................................................................... |
3 |
2.) |
Исходные данные....................................................................................................... |
3 |
3.) |
Расчет длительности технологического цикла ......................................................... |
4 |
4.) |
Расчет длительности производственного цикла ...................................................... |
6 |
5.) |
Выводы по первой части............................................................................................ |
7 |
Часть 2: Расчет и планировка поточной линии ............................................................. |
9 |
|
1.) |
Содержание задачи.................................................................................................... |
9 |
2.) |
Исходные данные..................................................................................................... |
10 |
3.) |
Решение .................................................................................................................... |
12 |
2

Часть 1: Расчет производственного цикла
1.) Содержание задачи
Рассчитать длительность технологического цикла простого процесса при последовательном, параллельном и параллельно-последовательном видах движения партии деталей в производстве.
Рассчитать длительность производственного цикла простого процесса при последовательном, параллельном и параллельно-последовательном видах движения партии деталей.
Построить в масштабе графики производственного цикла простого процесса при различных видах движения партии.
Сопоставить длительность технологического и производственного циклов простого процесса при различных видах движения партии и сделать выводы о влиянии вида движения (характере передач) на длительность технологического и производственного циклов.
2.) Исходные данные
Величина обработочной партии деталей:
n = 100
Величина транспортной (передаточной) партии деталей:
nт = 25
Продолжительность смены:
час S = 8 день
Режим работы:
q = 2 смены
Длительности межоперационных перерывов:
tМО посл = 90 мин |
- при последовательном виде движения партии деталей, |
|
tМО п−п = 30 мин |
- |
при параллельно-последовательном, |
tМО пар = 5 мин |
- |
при параллельном. |
3
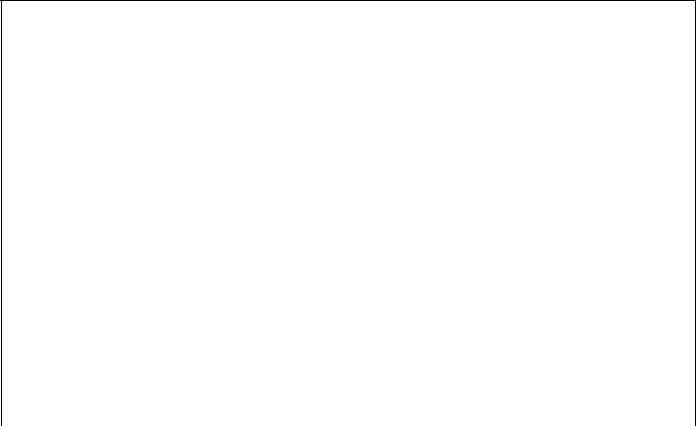
Технологический процесс с нормами времени tшт и фронтом работ С по операциям приведён в таблице 1-1 (в соответствии с номером варианта).
Таблица 1-1 – Технологический процесс обработки
Технологический процесс обработки
|
Норма штучного времени |
Фронт работ |
Номер операции |
tшт |
c |
|
[мин] |
[раб. мест.] |
|
|
|
1 |
2.8 |
1 |
|
|
|
2 |
3.7 |
1 |
|
|
|
3 |
0.9 |
1 |
|
|
|
4 |
2.7 |
1 |
|
|
|
5 |
4.8 |
2 |
|
|
|
6 |
6.1 |
1 |
|
|
|
7 |
0.8 |
1 |
|
|
|
3.) Расчет длительности технологического цикла
3.1.) Длительность технологического цикла последовательного вида движения:
|
m |
ti |
|
|
|
|
|
|
|
|
|
|
|
|
||||
TТ посл |
= n ∙ |
|
|
|
|
|
|
|
|
|
|
|
|
|
|
|
|
|
ci |
|
|
|
|
|
|
|
|
|
|
|
|
||||||
|
i=1 |
|
|
|
|
|
|
|
|
|
|
|
|
|||||
|
|
|
|
|
|
|
|
|
|
|
|
|
|
|
|
|
||
где ti |
– норма штучного времени на выполнение технологической |
|||||||||||||||||
|
операции, |
|
|
|
|
|
|
|
|
|
|
|
|
|||||
ci |
– количество рабочих мест на данной операции, |
|||||||||||||||||
n |
– обрабатываемая партия. |
|
|
|
|
|
|
|||||||||||
Подставляя данные из таблицы 1-1, получаем: |
|
|
||||||||||||||||
TТ посл |
= 100 ∙ |
|
2.8 |
+ |
3.7 |
+ |
0.9 |
+ |
2.7 |
+ |
4.8 |
+ |
6.1 |
+ |
0.8 |
= 1940 мин |
||
1 |
1 |
1 |
1 |
2 |
1 |
1 |
||||||||||||
|
|
|
|
|
|
|
|
|
4
3.2.) Длительность технологического цикла параллельного вида движения:
T |
= |
|
n ∙ |
m |
ti |
+ n − n |
∙ |
t |
|
|
|
|
|
|
|
|
|
||||||||
|
|
|
|
|
|
|
|
|
|
|
|
|
|
|
|
|
|||||||||
Т пар |
|
|
|
т |
|
|
ci |
|
|
|
т |
|
c |
max |
|
|
|
|
|
|
|||||
|
|
|
|
|
i=1 |
|
|
|
|
|
|
|
|
|
|
|
|||||||||
|
|
|
|
|
|
|
|
|
|
|
|
|
|
|
|
|
|
|
|
|
|
|
|
||
где |
nт |
|
- |
|
транспортная партия, |
|
|
|
|
|
|
||||||||||||||
|
|
t |
|
- |
|
максимальное значение отношения нормы штучного |
|||||||||||||||||||
|
|
|
|
|
|
||||||||||||||||||||
|
|
c |
max |
|
|
времени к количеству рабочих мест на операции во всем |
|||||||||||||||||||
|
|
|
|
|
|
|
процессе обработки. |
|
|
|
|
|
|
||||||||||||
Подставляя данные из таблицы 1-1, получаем: |
|
|
|
|
|||||||||||||||||||||
TТ пар |
= 25 ∙ |
2.8 |
+ |
3.7 |
+ |
0.9 |
+ |
2.7 |
+ |
4.8 |
+ |
6.1 |
+ |
0.8 |
+ 100 − 25 ∙ |
6.1 |
= |
||||||||
1 |
|
1 |
1 |
|
|
1 |
1 |
1 |
|||||||||||||||||
|
|
|
|
|
|
|
|
|
|
1 |
|
|
|
2 |
|
|
|
|
= 942.5 мин
3.3.) Длительность технологического цикла параллельно-последовательного вида движения:
|
|
|
|
m ti |
|
|
|
|
|
|
|
|
m−1 |
|
|
|
|
|
tj |
|
|
tj+1 |
|
|
|
|||||||||||||||
T |
= |
n ∙ |
|
|
|
|
|
|
− |
n − n |
∙ |
min |
|
|
|
, |
|
|
|
|
|
|
|
|
|
|
||||||||||||||
|
|
|
|
|
|
|
|
|
|
|
|
|
|
|
|
|
|
|
||||||||||||||||||||||
Т п−п |
|
|
|
|
|
|
ci |
|
|
|
|
|
|
т |
|
|
|
|
|
|
|
|
|
cj |
|
|
cj+1 |
|
|
|
||||||||||
|
|
|
|
|
|
|
|
|
|
|
|
|
|
|
i=1 |
|
|
|
|
|
|
|
|
|
|
|||||||||||||||
|
|
|
|
i=1 |
|
|
|
|
|
|
|
|
|
|
|
|
|
|
|
|
|
|
|
|
|
|
|
|
|
|
|
|||||||||
где |
min |
|
tj |
, |
tj+1 |
- |
минимальное значение отношения нормы штучного |
|||||||||||||||||||||||||||||||||
|
cj |
cj+1 |
|
|||||||||||||||||||||||||||||||||||||
|
|
|
|
|
|
|
|
|
|
|
|
времени к количеству рабочих мест на операции, |
||||||||||||||||||||||||||||
|
|
|
|
|
|
|
|
|
|
|
|
определяемое для смежных операций. |
||||||||||||||||||||||||||||
Подставляя данные из таблицы 1-1, получаем: |
|
|
|
|||||||||||||||||||||||||||||||||||||
TТ п−п |
= 100 ∙ |
2.8 |
+ |
3.7 |
+ |
0.9 |
+ |
2.7 |
|
+ |
4.8 |
|
+ |
|
6.1 |
+ |
0.8 |
|
− |
|||||||||||||||||||||
|
|
|
|
|
|
|
|
1 |
|
|||||||||||||||||||||||||||||||
|
|
|
|
1 |
|
|
|
|
1 |
|
1 |
|
1 |
|
|
|
|
2 |
|
|
|
|
|
|
|
|
|
1 |
|
|
||||||||||
|
|
|
|
|
|
|
|
|
|
|
|
2.8 |
0.9 |
0.9 |
|
2.7 |
|
|
4.8 |
|
|
0.8 |
|
|||||||||||||||||
|
− 100 − 25 ∙ |
|
|
+ |
|
|
+ |
|
|
|
+ |
|
|
|
+ |
|
+ |
|
|
= |
||||||||||||||||||||
|
1 |
|
1 |
|
1 |
|
|
1 |
|
|
2 |
1 |
|
= 1175 мин
5
4.) Расчет длительности производственного цикла
4.1.) Длительность производственного цикла последовательного вида движения:
T |
|
= |
|
|
|
1 |
|
|
|
∙ T |
+ m ∙ t |
|
|
|
+ |
Te |
|
|||
|
|
|
|
|
|
|
|
|
|
МО посл |
|
|||||||||
ПЦ посл |
|
S ∙ q ∙ 2010 ∙ 60 |
|
Т посл |
|
|
24 |
|||||||||||||
|
|
|
|
|
|
|
|
|
|
|||||||||||
где |
S = 8 |
|
час |
|
|
|
|
- |
длительность смены, |
|
|
|||||||||
|
день |
|
|
|
|
|
||||||||||||||
|
|
|
|
|
|
|
|
|
|
|
|
|
|
|
|
|
||||
|
q = 2 |
|
|
|
|
|
|
- |
количество смен, |
|
|
|
||||||||
|
2010 |
|
= |
249 |
|
|
|
- |
годовой коэффициент отношения рабочих дней |
|||||||||||
|
|
|
|
|
|
|
|
к календарным дням, |
|
|
||||||||||
|
|
365 |
|
|
|
|
|
|||||||||||||
|
|
|
|
|
|
|
|
|
|
|
|
|||||||||
|
tМО посл = 90 мин |
- |
межоперационный перерыв для |
|||||||||||||||||
|
последовательного вида движения, |
|||||||||||||||||||
|
|
|
|
|
|
|
|
|
|
|
|
|
||||||||
|
m = 7 |
|
|
|
|
|
|
- |
количество межоперационных перерывов |
|||||||||||
|
Te = 0 |
|
|
|
|
|
|
- |
время естественных процессов |
|||||||||||
Получаем: |
|
|
|
|
|
|
|
|
|
|
|
|
|
|
|
|
|
|||
TПЦ посл = |
|
|
|
1 |
|
∙ |
|
1940 + 7 ∙ 90 |
+ |
0 |
≈ 3.9 кл. дн. ≈ 2570 мин |
|||||||||
|
|
|
249 |
|
|
|
||||||||||||||
|
|
|
|
|
|
|
|
|
|
|
|
24 |
|
|
|
|||||
|
|
|
8 ∙ 2 ∙ 365 |
∙ 60 |
|
|
|
|
|
|
|
|
|
График производственного цикла при последовательном движении изображен на рисунке 1-1.
4.2.) Длительность производственного цикла параллельного вида движения:
T |
= |
1 |
|
∙ T |
+ m ∙ t |
|
+ |
Te |
|
|
|
МО пар |
|
||||||
ПЦ пар |
|
S ∙ q ∙ 2010 ∙ 60 |
Т пар |
|
24 |
||||
|
|
|
|
|
где tМО пар = 5 мин - межоперационный перерыв для параллельного вида движения.
Получаем: |
|
|
|
|
|
|
|
TПЦ пар = |
|
1 |
|
∙ 942.5 + 7 ∙ 5 + |
0 |
|
≈ 1.5 кл. дн. ≈ 977 мин |
|
249 |
|
24 |
||||
|
8 ∙ 2 ∙ |
∙ 60 |
|
||||
|
365 |
|
|
|
График производственного цикла при параллельном виде движения изображен на рисунке 1-2.
6
4.3.) Длительность производственного цикла параллельно-последовательного вида движения:
T |
= |
|
1 |
|
|
∙ T |
+ m ∙ t |
|
|
|
+ |
Te |
|
|
|
|
|
МО п−п |
|
||||||||
ПЦ п−п |
|
S ∙ q ∙ 2010 ∙ 60 |
Т п−п |
|
24 |
||||||||
|
|
|
|
|
|
|
|||||||
где tМО п−п = 30 мин - |
межоперационный перерыв для параллельно- |
||||||||||||
|
|
|
|
|
|
последовательного вида движения. |
|||||||
Получаем: |
|
|
|
|
|
|
|
|
|
|
|
||
TПЦ п−п = |
|
1 |
|
∙ 1175 + 7 ∙ 30 |
+ |
0 |
|
≈ 2.1 кл. дн. ≈ 1385 мин |
|||||
|
249 |
|
|
||||||||||
|
|
8 ∙ 2 ∙ |
∙ 60 |
|
|
24 |
|
|
|
||||
|
|
365 |
|
|
|
|
|
|
|
|
График производственного цикла при параллельно-последовательном виде движения изображен на рисунке 1-3.
5.) Выводы по первой части
а) Последовательный вид движения партии деталей
Преимущества:
Простая организация производственного процесса; самый высокий коэффициент загрузки оборудования из всех трех видов движения; легкая организация производственных участков и цехов по технологическому принципу, что актуально при частой смене технологических процессов; самые низкие транспортные расходы из всех трех видов движения.
Недостатки:
Самый длительный технологический и производственный циклы из всех трех видов движения.
Выводы:
Применяется в единичном (опытном) и в мелкосерийном производстве.
7
б) Параллельно-последовательный вид движения партии деталей
Преимущества:
За счет частичной параллельности выполнения операций значительно сокращается технологический и производственный циклы; сохраняется коэффициент загрузки оборудования, т. к. на каждой операции производство осуществляется непрерывно; транспортные расходы значительно меньше, чем при параллельном виде движения, за счет возможности групповой передачи транспортных партий.
Недостатки:
Длительность цикла больше, чем у параллельного вида движения; возможность возникновения объемов незавершенного производства.
Вывод:
Применяется в серийном и массовом производстве.
в) Параллельный вид движения партии деталей
Преимущества:
Самый короткий ТЦ и ПЦ из всех трех видов движения; первая транспортная партия за минимально возможное время поступает в дальнейшее производство.
Недостатки:
Повышенные транспортные расходы (самые высокие из всех трех видов движения); простои оборудование увеличивается, но, так как данный вид движения в основном в массовом производстве (иногда в крупносерийном производстве), то простои оборудование не дает больших потерь; самый низкий коэффициент загрузки из всех трех видов движения, актуальность которого незначительна, так как применяется специализированное оборудование, недорогое, с повышенным сроком эксплуатации. Этот недостаток компенсируется использованием параллельного вида движения в непрерывнопоточном производстве.
Вывод:
Применяется в массовом производстве.
8
Часть 2: Расчет и планировка поточной линии
1.) Содержание задачи
Определить такт работы поточной линии при заданном объёме выпуска изделий, учитывая при этом регламентные перерывы.
Рассчитать потребное количество рабочих Сi и их загрузку по операциям технологического цикла.
Выбрать тип поточной линии, наиболее соответствующей условиям производства, и вид транспортных средств.
Выполнить расчёты, определяющие компоновку и условия работы линии:
а) |
для рабочего конвейера: шаг конвейера 0, скорость движения транспортёра v, |
|||||||
|
длина рабочих зон по операциям р, |
длина дополнительной (резервной) зоны |
||||||
|
доп для одной наиболее трудоёмкой |
операции |
при |
условии |
колебания |
|||
|
фактического времени выполнения её в пределах (0,8÷1,3) tшт, длина рабочего |
|||||||
|
участка линии Lраб и общая длина |
транспортёра |
Lобщ |
, длительность |
||||
|
производственного цикла. |
|
|
|
|
|
|
|
б) |
для распределительного конвейера: шаг конвейера 0 , скорость движения |
|||||||
|
транспортёра v, необходимый комплект разметочных знаков (период) П, длина |
|||||||
|
рабочего |
участка линии Lраб и общая |
длина транспортёра Lобщ , разметка |
|||||
|
конвейера |
и закрепление знаков |
за |
рабочими |
местами |
по |
операциям |
технологического процесса (в виде таблицы и на схеме планировки линии), длительность производственного цикла, «косой график».
в) для прямоточной линии: регламент работы линии, период комплектования выработки (ритм работы линии) R, график загрузки рабочих мест на линии с учётом возможного совмещения обслуживания и максимальной загрузки оборудования, величина межоперационных оборотных заделов Z , эпюра межоперационных оборотных заделов на линии.
Скомпоновать и вычертить в масштабе схему планировки выбранной поточной линии, габаритные размеры станков приведены в таблице 2-2. Определить величину производственной площади.
Определить потребное количество основных рабочих на линии, учитывая возможное совмещение профессий (и операций).
Определить сменную выработку на одного рабочего и один квадратный метр производственной площади.
9
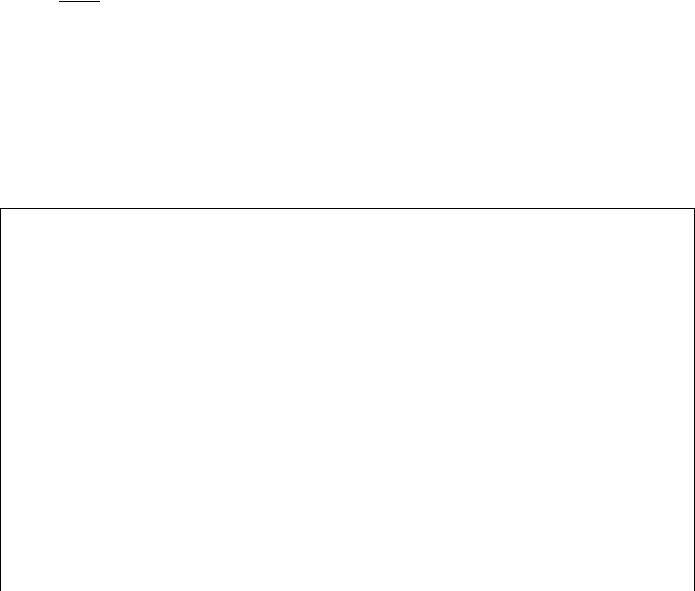
2.) Исходные данные
Наименование изделия:
Шестерня повышающей передачи промежуточного вала
Программа запуска:
Nв = 240 штук в смену
Регламентированные перерывы:
Tрегл = 0 минут в смену
Вес изделия:
4,6 кг
Габаритный диаметр изделия:
120 мм
Продолжительность смены:
час S = 8 день
Режим работы:
q = 1 смена
Технологический процесс обработки с нормами времени по операциям приведён в таблице 2-1 (в соответствии с номером варианта).
Таблица 2-1 – Технологический процесс обработки детали
Технологический процесс обработки детали
№ |
Наименование операций |
Тип оборудования |
Норма времени |
|
tшт [мин] |
||||
|
|
|
||
|
|
|
|
|
1 |
Черновое обтачивание и растачивание |
Токарно-винторезный 1К62 |
8,3 |
|
|
|
|
|
|
2 |
Чистовое обтачивание и растачивание |
Токарно-винторезный 1К62 |
7,9 |
|
|
|
|
|
|
3 |
Фрезерование зуба |
Зубофрезерный 5310 |
10,5 |
|
|
|
|
|
|
4 |
Зачистка заусенцев |
Верстак |
5,75 |
|
|
|
|
|
|
5 |
Фрезерование канавки |
Горизонтально-фрезерный 6Н82 |
5,8 |
|
|
|
|
|
|
6 |
Сверление отверстий, |
Вертикально-сверлильный 2А135 |
3,8 |
|
равнорасположенных по окружности |
||||
|
|
|
||
|
|
|
|
|
7 |
Контроль |
Контрольный стол |
2,8 |
|
|
|
|
|
|
|
|
|
10 |