
Теория формообразования деталей при механической обработке. Жачкин С.Ю., Сидоркин О.А
.pdf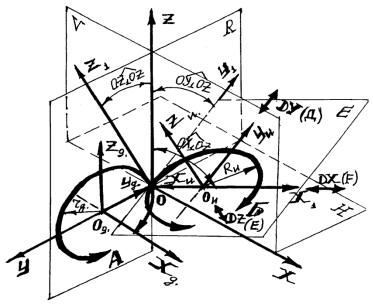
С.Ю. Жачкин, О.А. Сидоркин, Н.А. Пеньков, С.В. Сафонов
ТЕОРИЯ ФОРМООБРАЗОВАНИЯ ДЕТАЛЕЙ ПРИ МЕХАНИЧЕСКОЙ ОБРАБОТКЕ
Учебное пособие
Воронеж 2016
ФГБОУ ВО «Воронежский государственный технический университет»
С.Ю. Жачкин, О.А. Сидоркин, Н.А. Пеньков, С.В. Сафонов
ТЕОРИЯ ФОРМООБРАЗОВАНИЯ ДЕТАЛЕЙ ПРИ МЕХАНИЧЕСКОЙ ОБРАБОТКЕ
Утверждено Редакционно-издательским советом университета в качестве учебного пособия
Воронеж 2016
УДК 621.9.02
Жачкин С.Ю. Теория формообразования деталей при механической обработке: учеб. пособие [Электронный ресурс]. – Электрон. текстовые и граф. данные (5,9 МБ) / С.Ю. Жачкин. О.А. Сидоркин, Н.А. Пеньков, С.В. Сафонов. – Воронеж: ФГБОУ ВО «Воронежский государственный технический университет», 2016. – 1 электрон. опт. диск (CD-ROM): цв. – Систем. требования: ПК 500 и выше; 256 МБ ОЗУ; Windows XP; SVGA с разрешением 1024х768; CD-ROM дисковод; мышь. – Загл. с экрана.
Учебное пособие содержит вопросы, ориентированные на изучение студентами вопросов формообразования поверхностей при различных методах механической обработки.
Издание соответствует требованиям Федерального государственного образовательного стандарта высшего образования по направлению 15.04.01 «Машиностроение» (программа магистерской подготовки «Обеспечение качественноточностных характеристик при изготовлении изделий в автоматизированном машиностроительном производстве»), дисциплине «Теория формообразования деталей при механической обработке».
Табл. 7. Ил. 89. Библиогр.: 9 назв.
Рецензенты: кафедра защитных сооружений ВУНЦ ВВС «ВВА» им. проф. Н.Е. Жуковского и Ю.А. Гагарина (зав. кафедрой канд. техн. наук, доц. И.И. Звенигородский); д-р техн. наук, проф. А.В. Кузовкин
Жачкин С.Ю., Сидоркин О.А., Пеньков Н.А., Сафонов С.В., 2016
Оформление. ФГБОУ ВО «Воронежский государственный технический университет», 2016
3
ПРЕДИСЛОВИЕ
От современных машин требуются высокие эксплуатационные и технико-экономические характеристики, надежность работы. Проходя путь технологической обработки от исходного материала до готовой детали в машине, изделие подвергается обработке различными технологическими методами.
Одной из главных задач современного машиностроения является развитие, совершенствование и разработка новых технологических методов изготовления деталей машин. Одно из главных мест в технологическом процессе изготовления изделий занимает обработка металлов резанием.
Т.к. при обработке резанием около 20% материала превращается в отходы (стружку), поэтому всё большее развитие получают процессы малоотходной технологии изготовления, такие как точное литьё, обработка давлением, порошковая металлургия и другие. Однако, в настоящее время, изготовление высокоточных деталей осуществляется только лишь чистовыми и отделочными методами обработки резанием, объем которых непрерывно возрастает.
Необходимость издания этой книги связана с отсутствием учебной литературы данной тематики для студентов вузов немашиностроительных, а точнее, механических специальностей.
3
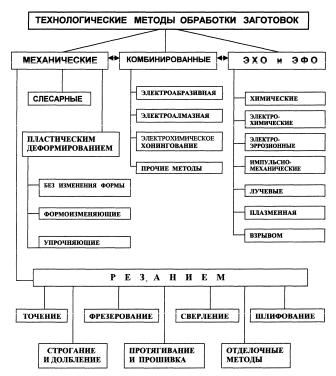
ТЕМА № 1
ОСНОВЫ ТЕХНОЛОГИИ ОБРАБОТКИ ЗАГОТОВОК И ФОРМООБРАЗОВАНИЯ ПОВЕРХНОСТЕЙ ДЕТАЛЕЙ МАШИН
1. Современные технологические методы формообразования поверхностей деталей машин
Разнообразие технологических методов формообразования поверхностей деталей машин можно представить в виде табл. 1.1.
Таблица 1.1 Технологические методы обработки заготовок
4
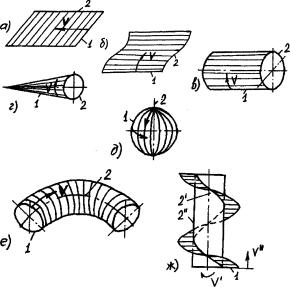
Наряду с методами механической обработки резанием, которые составляют большую применяемость, используют методы обработки пластическим деформированием без снятия стружки, а также с использованием химической, электрической и других видов энергии.
2. Кинематические основы формообразования поверхностей деталей машин
Все детали машин по конструктивным и технологическим признакам можно разделить на следующие группы или
классы:
1) валы, 2) корпусные детали, 3) втулки, 4) рычаги, 5) зубчатые колеса.
Пространственная форма детали ограничивается различ-
ными геометрическими поверхностями. Наиболее часто встречаются такие поверхности, как на рис. 1.1.
Рис. 1.1. Виды поверхностей: а) плоская, б) линейчатая, в) цилиндрическая, г) коническая, д) шаровая, е) торцовая, ж) геликоидная
5
Любую геометрическую поверхность можно рассматривать как совокупность последовательных положений (следов) одной производящей линии, называемой образующей (на рисунке. 1.1. обозначены цифрой «1»), движущейся по другой производящей линии, называемой направляющей (на рисунке
1.1. - цифрой «2, 2', 2"»).
Например, для получения плоской поверхности (Рисунок 1.1.а) образующую прямую линию 1 надо перемещать по направляющей прямой 2.
В реальных условиях образования поверхностей деталей на станках образующие и направляющие линии в большинстве случаев воспроизводятся комбинацией движений заготовки и инструмента. Таким образом, формообразующими движениями являются движения резания.
Различают четыре метода формообразования поверхностей: копирования, следов, касания и обката (огибания).
Образование поверхности по методу копирования состоит в том, что режущая кромка инструмента соответствует форме образующей линии (1) обрабатываемой поверхности детали (Рисунок 1.2.а) или обратной ей (Рисунок 1.2.б). Направляющая линия (2) воспроизводится вращением заготовки (Рисунок 1.2.а) или поступательным движением инструмента (Рисунок 1.2.б).
Этот метод используют при обработке фасонных поверхностей.
Образование поверхностей по методу следов состоит в том, что образующая линия 1 является траекторией движения точки (вершины) режущего лезвия инструмента, а направляющая линия 2 – траекторией движения точек заготовки (рис. 1.3.а). В этом случае оба движения (Dr и Ds) являются формообразующими. Этот метод формообразования наиболее распространен.
6

а) б)
Рис. 1.2. Схема формирования поверхностей методом копирования
Образование поверхностей по методу касания заключается в том, что направляющей линией 2 служит касательная к ряду геометрических вспомогательных линий, которые являются траекториями движения точек режущего инструмента (рис. 1.3.б), а образующей линией 1 служит режущая кромка инструмента. Здесь формообразующим движением является только подача (Ds).
Образование поверхностей по методу обкатки (огибания) состоит в том, что образующая линия 1 является огибающей кривой ряда последовательных положений режущего лезвия инструмента относительно заготовки. Движения заготовки (Ds2) и инструмента (Ds1) должны быть согласованы. Направляющая 2 образуется движением инструмента Dr (рис. 1.3.в).
7

Рис. 1.3. Схемы методов формообразования поверхностей: а) следов; б) касания; в) обката
3. Движения для осуществления процесса резания и схема обработки
Обработка металлов резанием - это процесс срезания режущим инструментом с поверхности заготовки слоя металла в целях получения требуемой формы, точности размера и шероховатости поверхности детали.
Для осуществления процесса резания рабочим органам станка сообщаются необходимые движения. Различают следующие движения рабочих органов: резания, установочные и вспомогательные.
Движения резания – при которых с обрабатываемой заготовки срезается слой металла и изменяется состояние
8
обработанной поверхности. К ним относятся главное движение и движение подачи.
Главное движение – определяет скорость отделения стружки. Часто за главное движение принимают скорость резания V. Главное движение (на рис. 1.4. обозначено буквой Dr) может быть вращательным, поступательным, возвратнопоступательным, непрерывным или прерывистым и др.
Движение подачи обеспечивает непрерывность врезания режущего лезвия инструмента в новые слои металла. Движение подачи (на рис. 1.4. обозначено буквой Ds) также может быть различным по направлению и по характеру.
Установочные движения обеспечивают положение инструмента относительно заготовки, при которой с неё снимается определенный слой материала (движение врезания
или наладочное).
Вспомогательные движения, не имеют непосредственного отношения к процессу резания (транспортировка и закрепление заготовки и инструмента, быстрые перемещения рабочих органов, переключения скоростей резания и подачи и т.п.).
Для проектирования любого процесса резания необходимо составить схему обработки, которая представляет собой условное изображение заготовки, её установки и закрепления на станке, закрепление и расположение инструмента относительно заготовки, а также векторы движений резания, примеры схем обработки показаны на рис. 1.4.
4. Режим резания и геометрия срезаемого слоя
Режим резания – совокупность величины элементов:
глубины резания, подачи и скорости резания.
Рассмотрим элементы режима резания на примере процесса точения (рис. 1.5).
9