
3512
.pdf
2) Зенкеры
Типы и конструкции зенкеров:
-по закреплению на станке: хвостовые и насадные
(рис. 5.8);
-по креплению режущей части: цельные (диаметром до 32 мм), составные и сборные;
-по форме хвостовика: с цилиндрическим и коническим хвостовиком;
-по назначению: для цилиндрических отверстий (рис. 5.8) и специальные: зенковки и цековки (рис. 5.9).
Рис. 5.8. Цилиндрические зенкеры: а) хвостовой цельный; б) насадной составной
Рис. 5.9. Зенковки: а) коническая; б) цилиндрическая; в) торцовая (цековка)
90
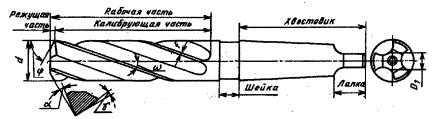
Элементы конструкции и геометрии режущей части цилиндрического зенкера показаны на рис. 5.10. Зенкеры имеют от трёх до шести зубьев и отличаются от сверл отсутствием перемычки.
Рис. 5.10. Элементы конструкции и геометрии зенкера
3) Развертки
Типы и конструкции разверток:
-по способу крепления на станке: хвостовые и насадные;
-по креплению режущей части: цельные, составные и сборные;
-по форме хвостовика: с цилиндрическим и коническим хвостовиком;
-по степени механизации: ручные и машинные;
-по форме обрабатываемого отверстия:
цилиндрические и конические;
-по постоянству размера: нерегулируемые и регулируемые.
Конструктивно развертка состоит из тех же элементов, что и зенкер, однако, у рабочей части развертки ещё имеется направляющий и обратный конусы (рис. 5.11).
Для конических отверстий развертки изготовляют комплектами из трех штук: черновой, получистовой и чистовой.
91

Геометрические элементы развертки такие же, как у зенкера.
Рис. 5.11. Конструкции цилиндрических разверток: а) цельная ручная; б) цельная машинная; в) насадная цельная; г) насадная составная; д) насадная сборная; е) регулируемая разжимная
92

3. Элементы режима резания
Рассмотрим элементы режима резания осевыми инструментами на схемах обработки отверстий (рис. 5.12).
Рис. 5.12. Схемы обработки отверстий: а) рассверливанием; б) зенкерованием; в) развертыванием
1) Глубина резания ( ) определяется через диаметр
осевого инструмента – |
и диаметр отверстия заготовки – : |
- при сверлении: |
= 0,5∙ ; |
-при рассверливании, зенкеровании и развертывании:
=0,5∙( − ).
Ориентировочно:
- при зенкеровании: = (0,1…0,15)∙ зен;
-при развертывании: = 0,005∙ раз.
2) Подача ( ) – перемещение инструмента вдоль оси на каждый зуб инструмента (подача на зуб – , мм/зуб) или за один его оборот (подача на оборот – , мм/об).
Они взаимосвязаны между собой зависимостью:
=⁄ , мм/зуб, где – число зубьев инструмента.
93

Ориентировочно: |
|
св |
|
|
, мм/об; |
|
-- |
при зенкеровании –= (0,02…0,03)∙ |
, |
|
|||
|
при сверлении – |
= (0,04…0,06)∙ |
мм/об; |
|||
- |
при развертывании – |
|
зен |
, мм/об. |
||
3) |
Скорость резания ( |
) =– (0,05…0,08)∙ |
раз |
|||
|
|
окружная |
скорость точки |
лезвия инструмента, наиболее удаленной от оси.
Скорость резания можно определить через частоту
вращения ( |
): |
|
|
диаметр инструмента, м; |
|||||
|
|
где |
– |
= л ∙ |
|
∙ ,(м/мин), |
|||
или по эмпирической зависимости: |
|||||||||
|
|
|
|
|
∙ |
|
|
|
коэффициент, стойкость |
|
|
|
= , |
|
|
|
∙ – |
||
где |
, |
, |
, |
, |
|
,(м⁄мин), |
|||
инструмента |
и показатели∙ |
∙степени |
при параметрах режима |
резания, приводятся в справочных данных.
4) Основное технологическое время (То) определяется так же, как для точения: = ∙ , (мин),
где = + + , мм – расчетная длина прохода инструмента в направлении подачи;
– глубина отверстия, мм; |
= 1…3 |
|
– величина врезания, мм, |
|
|
– величина перебега инструмента |
мм. |
|
Ориентировочно: |
|
- при сверлении – = 0,3 ;
-при рассверливании, зенкеровании и развертывании:
= 0,5( − ) ∙ |
; |
94
4.Типы сверлильных расточных станков
1)Сверлильные станки:
Вертикально-сверлильные:
-одно- и многошпиндельные;
-настольные и напольные.
Радиалъно-сверлильные применяют для обработки отверстий на крупногабаритных заготовках.
Специализированные:
-центровальные – для получения центровочных гнезд;
-горизонтально-сверлильные - для обработки глубоких отверстий;
-станки для обработки отверстий в коленчатых валах,
шатунах, фильерах и др.
Агрегатные – собираются из стандартных узлов.
2) Расточные станки:
Универсальные горизонтально-расточные – для обработки сложных корпусных заготовок (редукторов, шпиндельных бабок станков, блоков двигателей и др.).
Координатно-расточные – для обработки высокоточных отверстий шаблонов, кондукторов, пресс-форм
ит.п. Обычно имеют вертикальный шпиндель. Бывают одно-
идвухстоечные.
Вертикально-расточные – с вертикальной осью вращения шпинделя.
Алмазно-расточные – имеют повышенную точность и жесткость технологической системы, быстроходны.
Бывают: одно- и многошпиндельные, с вертикальным и горизонтальным шпинделем.
Специализированные.
95
ТЕМА № 6
ОБРАБОТКА НА СТРОГАЛЬНЫХ, ДОЛБЕЖНЫХ
ИПРОТЯЖНЫХ СТАНКАХ
1.Особенности процессов строгания, долбления и протягивания
Эти процессы имеют много общего с точением и сопровождаются такими же факторами и явлениями, что и при точении: износ инструмента, тепловыделения и др. Однако, имеются и специфические особенности, которыми являются:
-инструмент (резец, протяжка) в процессе резания работает периодически (только при рабочем ходе), а во время холостого хода охлаждается;
-врезание инструмента в заготовку сопровождается ударами.
2. Строгание и долбление
Строганием и долблением (Рисунок 6.1) обрабатываются плоские и линейчатые поверхности, пазы, канавки, зубья зубчатых колес и др.
1) Инструментом при строгании и долблении являются резцы, которые конструктивно подобны токарным, но имеют большее поперечное сечение, т.к. работают с ударной нагрузкой.
Строгальные резцы выполняются обычно изогнутыми назад, что позволяет при ударных нагрузках резцам отгибаться и уменьшать глубину резания и нагрузку на режущую кромку, сохраняя резец от поломки.
Долбежные резцы выполняются изогнутыми вперед. Геометрические параметры строгальных и долбежных
резцов такие же, как у токарных.
96

Рис. 6.1. Схемы резания: а) при строгании; б) при долблении
2) Элементы режима резания Рабочими движениями являются:
-главное движение – возвратно-поступательное перемещение резца в горизонтальной (при строгании) и вертикальной (при долблении) плоскости;
-движение подачи – продольное, поперечное или круговое движение заготовки.
Глубина резания (t) равна толщине срезаемого слоя за один проход резца (при строгании) или ширине резца (при долблении).
Подача (S) – величина перемещения детали за один двойной ход резца, измеряется в мм/дв. ход.
Скорость резания (V) – средняя скорость рабочего хода резца (или заготовки – при продольном строгании) в м/мин.
Основное технологическое время (То), силу резания (Рz) и
мощность (Nр) определяют по тем же зависимостям, что и при точении.
97

Строгание и долбление применяют при единичном и мелкосерийном производстве, чаще при ремонте, вследствие дешевизны инструмента, при достаточной точности обработки меньшей стоимости станков по сравнению с фрезерными и протяжными станками.
3. Протягивание
Протягивание – метод обработки наружных и внутренних поверхностей деталей многолезвийными режущими инструментами – протяжками или прошивками. Форма протягиваемых поверхностей может быть различной: круглые, квадратные, прямоугольные, овальные и другие отверстия, шлицевые и шпоночные пазы. Формообразование поверхностей производится копированием режущих лезвий инструмента на обрабатываемой заготовке.
Протягивание выполняется только главным движением, которое придается инструменту или заготовке. Движение подачи отсутствует, её функции заложены в конструкции протяжки.
Протяжка состоит из основных частей, показанных на рис. 6.2.
Рис. 6.2. Конструктивные элементы круглой протяжки: l1 – передняя замковая часть;
l2 – шейка;
l3 – передняя направляющая часть; l4 – режущая часть;
l5 – калибрующая часть;
l6 – задняя направляющая часть; l7 – задняя замковая часть
98

Передняя замковая часть (l1) служит для закрепления протяжки в рабочем патроне (тяговом устройстве) станка. Передняя направляющая часть (l3) служит для центрирования заготовки относительно оси протяжки, размер её сечения соответствует размеру отверстия заготовки.
На режущей части (l4) располагают режущие зубья, которые срезают весь припуск. Высота каждого последующего зуба режущей части больше высоты предыдущего на величину , которую называют подачей на зуб. При обработке деталей из различных материалов принимают от 0,005 до 0,3 мм. Число режущих зубьев ( ) определяют в зависимости от
припуска:
= + (2…4),
где - припуск на обработку.
Шаг режущих зубьев (Рр) устанавливают в зависимости от длины протягиваемой поверхности (lд): = (1,5…1,9) д, (мм).
Геометрия режущих зубьев: = 5…20° ; = 4…10°.
Калибрующая часть (l5) придает обрабатываемой поверхности окончательные размер и шероховатость. На калибрующей части располагают 3…7 зубьев одного размера
без стружкоделительных |
канавок с шагом между зубьями |
|||
= (0,6…0,7)∙ калибрующих |
|
= 0…5° ; |
= |
|
. |
|
зубьев: |
||
. |
|
|||
Геометрия |
|
|
|
|
0,5…1° |
|
|
|
|
Задние направляющая (l6) и замковая (l7) части необходимы для правильного выхода протяжки из обрабатываемого отверстия и поддержания протяжки от провисания.
99