
3492
.pdf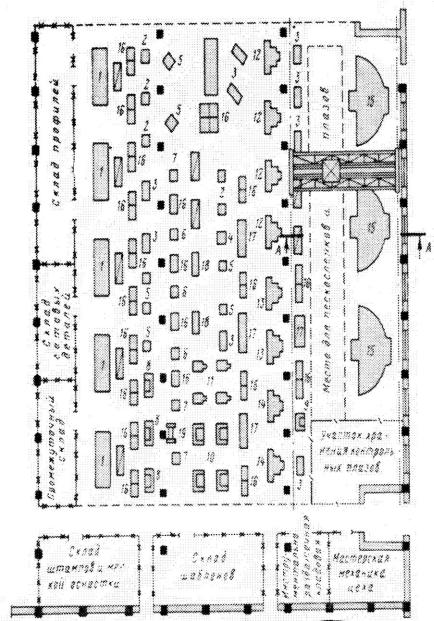
Рис.28 Планировка профилировочного цеха На рис. 24-28 приведены типовые компоновки и планировки ряда
заготовительно-штамповочных цехов. Планировки заготовительно-
штамповочных цехов должны выполняться с соблюдением принципов поточного производства из заготовок больших габаритов и массы. Цикл производства в заготовительно-штамповочных цехах при потоке поддается более эффективному контролю, лучшее используется производственная площадь. При поточном производстве крупное прессовое оборудование располагается вдоль направления движения потока. Последовательное расположение заготовительно-штамповочного оборудования делает более простыми и рациональными конструкции транспортных и загрузочных устройств. Передача деталей с одной операции на другую может быть групповой или индивидуальной для крупногабаритных деталей. Прессы можно устанавливать в две линии при штамповке деталей с малым количеством операций и поворачивать их к фронту на 45о для штамповки деталей из полосы. При производстве нормалей и мелких многооперационных деталей оборудование следует располагать по ходу технологического процесса.
4.9. Требования к помещениям
Стены покрывают светлой клеевой краской. Полы должны быть малопыльными масло- и ударостойкими. Удельные нагрузки в пределах 3- 5т.с./м2. Высоко шумные отделения должны изолироваться стеклами и перегородками из шумопоглащающего материала и иметь звукопоглощающие подвесные потолки. Стены отделений свинцовоцинковых штампов, выделяющих токсичные вещества выкладываются глазурованной плиткой .
Мероприятия понижающие уровень шума в заготовительноштамповочных цехах:
1)перевод операции раскроя листа на станки с программным управлением;
2)плазменная резка высокопрочных материалов;
3)перевод раскроя профилей с пил на механические пресса;
4)внедрение прессов с высоким удельным давлением, снижающие ручные доводочные работы;
5)замена листоштамповочных молотов электрогидравлическими
иэлектромагнитными;
6)нагрев во время штамповки;
7)установка оборудования на вибраизаляционных опорах. Уборка и переработка отходов.
Операции уборки:
1)сбор и транспортировка (краны, автопогрузчики, транспортеры);
2)разделка (ножницы, пакетировачный пресс, кран пакетировачного пресса).
Количество металла ( в т.) на годовую программу

M Q100 100 OT
где Q – масса продукции; От – отходы в процентах.
5.Проектирование агрегатно-сборочных цехов (АСЦ)
5.1.Характеристика АСЦ
Агрегатно-сборочные цеха включают производственные участки (узловых сборок, сборок агрегатов в стапелях, вне стапельных доработок). В составе АСЦ могут быть участки испытаний, отработок, сборки систем (например, антиобледенительных), монтажа систем в агрегатах, молярные отделения. Кроме производственных участков в состав АСЦ входят вспомогательные службы, склады, конторы, бытовые помещения.
Номенклатура АСЦ: узлы типа нервюр, лонжеронов, шпангоутов панелей; секции агрегатов (отсеки, части агрегатов); агрегаты.
При проектировании АСЦ следует стремиться, чтобы цех и даже участок работали в режиме крупносерийного производства – поточного. Для этого могут быть организованы специализированные цехи , например , цех панелей , цех узловых сборок , которые эффективны при больших объемах производства, больших программах выпуска.
5.2. Исходные данные для проектирования АСЦ
Основными данными для проектирования АСЦ являются: программа выпуска сборочных единиц и запчастей ; чертежи общих видов;
директивная технология изготовления сборочных единиц (на ее основе делается технологическое оснащение производства); схемы технологических и эксплуатационных членений для агрегатов и секций; схема сборки;
чертежи сборочных приспособлений; технологические условия на сборку; трудоемкость сборочных работ с разбивкой по видам.
5.3 Алгоритм проектирования АСЦ
Руководствуясь исходными данными, на базе директивной технологии составляется укрупненный технологический процесс, который позволяет создать технологический комплект стапелей и стапельной
оснастки, определить состав сврлильно – зенковального оборудования, клепальных прессов, сварочного оборудования, установок для пайки, склеивания, склейки – сварки и других процессов при выполнении технологических операций агрегатно-сборочных работ на стапельной и внестапельной сборке и доработке единицы, а также состав подъемно – транспортного и конвейерного оборудования .
Далее составляется ведомость прокатного оборудования и стапелей с техническими характеристиками и сметной стоимостью.
Рассчитывается необходимое количество рабочих, инженерно – технических работников (ИТР), счетно-хозяйственного контрольного персонала (КСХ), младшего обслуживающего персонала (МОП), определяется уровень механизации и автоматизации производственных процессов. Производится расчет производственных площадей и выполняется планировка цеха .
5.4 Технологические основы проектирования
агрегатно-сборочных цехов.
В основе проектирования агрегатно-сборочного цеха должен лежать рабочий технологический процесс сборки агрегата. Разработка технологического процесса долговременна и трудоемка, поэтому при проектировании цеха пользуются ведомостями распределения сборочных работ по участкам цеха и объемов работ по видам приспособлений, стапелям, сверлильно-зенковальному, клепальному, сварочному и другому специализированному оборудованию. Внестапельные сборочно – монтажные работы компонуются в здания , объем которых должен бать равен или кратен такту подач – конвейерной линии . Ведомости распределения работ составляются на основе укрупненного технологического процесса , базирующегося на директивной технологии с учетом схем членения планера самолета на сборочные единицы ( агрегаты , секции , панели , узлы ) , характера соединений по конструктивным и эксплуатационным разъемам , новых материалов и технологических процессах , схемам и последовательности сборки ( от обшивки, по КФО, от каркаса и др.), средствами обеспечения взаимозаменяемости по стыкам и соединениям, а также сборочной оснастке, средства контроля и транспортирования. Примерная схема последовательности сборки отемной части крыла по сборочным единицам выглядит так :
1)сборка лонжеронов , нервюр , панелей;
2)сборка каркаса;
3)общая сборка;
4)внестапельная доработка;
5)испытание;
6)разделка стыковых узлов;

7)монтажные работы;
8)отработка и проверка систем;
9)сдача заказчику.
Соответственно трудоемкости сборочных работ в процентах от общей трудоемкости изделия принимается следующим:
-агрегатная сборка – 28 – 33 %;
-узловая сборка – 8 – 10 %;
-стапельная сборка – 12 – 14 %;
-внестапельная сборка – 8 – 9 %;
Распределение трудоемкости в агрегнатно – сборочных цехах по видам трудоемкости работ в процентах от трудоемкости агрегатносборочных работ:
-слесарно – сборочные работы – 33 %;
-клепально – сборочные работы – 40 %;
-клепка на прессах – 12 %;
-сверлильно-зенковальные работы – 15 %;
-прочие работы – 3 %;
Трудоемкость изготовления агрегатов в процентах от общей трудоемкости:
-крыло – 8 –11 %;
-стабилизатор – 0,8 – 1,22 %;
-киль – 0,9 – 1,4 %;
-горизонтальное оперение 1,5 – 2 %;
-фюзеляж – 16 – 19 %.
5.5.Расчет количества сборочных приспособлений, оборудования
ирабочих мест.
Базой для расчета является схема членения на сборочные единицы и схемы технологических процессов сборки этих сборочных единиц.
Количество сборочных мест определяется формулой
КСТ |
|
ТП |
, |
||
|
|
|
|||
Ф |
Д . Р |
. mn |
|||
|
|
где КСТ – расчетное количество стапелей или рабочих мест ; П. – годовая программа выпуска агрегатов с учетом запасных частей
;
Фд. р. - действительный ( расчетный ) годовой фонд времени работы
в стапеле и рабочем месте, часах ;
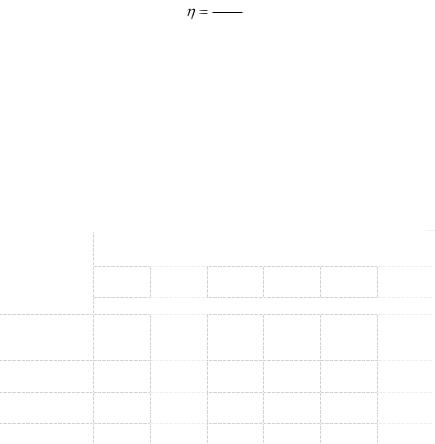
n – число рабочих, одновременно работающих на стапеле или плотность работ;
m – число смен;
Величена расчетного количества стапелей или рабочих мест округляется в большую сторону до целого числа и называется принятым количеством стапелей или приспособленный Кпр.
Отношение расчетного количества стапелей к принятому называется коэффициентом загрузки стапелей и рабочих мест по времени
КСТ . К пр
Среднее значение коэффициента загрузки стапелей при сборке:
-панелей – 0,4 – 0,6;
-центропланов – 0,5 – 0,7;
-крыла – 0,5 – 0,8;
-фюзеляжа – 0,6 – 0,9;
-стабилизатора – 0,4 – 0,7 .
В агрегатно-сборочных цехах, наряду с основным расчетным оборудованием устанавливается дополнительное (не расчетное) оборудование (станки, пресса, верстаки для доделочных вне стапельных операций). Состав дополнительного оборудования определяется по таблице
1
Таблица 1
|
Количество производственных рабочих в цехе |
|
|||||
Наименован |
|
|
|
|
|
|
|
ие |
101- |
201- |
301- |
401- |
501- |
601- |
|
оборудовани |
|
||||||
200 |
300 |
400 |
500 |
600 |
700 |
|
|
я |
|
||||||
|
Количество оборудования |
|
|
||||
|
|
|
|
||||
Настольно- |
3 |
4 |
5 |
6 |
7 |
8 |
|
сверлильный |
|
|
|
|
|
|
|
станок |
|
|
|
|
|
|
|
Клепальный |
2 |
2 |
3 |
3 |
4 |
4 |
|
пресс |
|
|
|
|
|
|
|
Точило |
1 |
2 |
2 |
3 |
3 |
4 |
|
наждачное |
|
|
|
|
|
|
|
Верстак |
6 |
9 |
12 |
15 |
18 |
21 |
|
|
|
|
|
|
|
|
|
В мастерской цеховой механики и ремонта приспособлений устанавливаются токарновекторезный, вертикально – сверлильный, универсально фрезерные станки, наждачное точило, разметочная плита и 4
– 6 слесарных верстаков.

Количество механизированного инструмента принимается в процентах от числа производственных рабочих:
-пневмодрели – 27 %;
-пневмомодотки – 24 %;
-пневмоотвертки – 9 %;
-пневмогайковерты – 6 %.
5.6. Организация транспортных работ
Своевременное и бесперебойное обеспечение рабочих мест предметами труда зависит от организации транспортных работ. По схемам транспортных потоков выделяются три основные группы производственных участков агрегатно-сборочных цехов: сборки узлов; участки стапельной и внестапельной сборки. Основной формой организации сборочного производства является поточная и поточно – конвейерная сборки.
На участках узловых сборок для технологически и конструктивно подобных сборочных единицах обычно применяются многопредметные линии с перемещающимися объектами. На таких линиях межоперационная передача может осуществляется вручную с использованием тары, а также с применением конвейерных устройств.
На стапельной сборке агрегатов, секций и крупных узлов на однопредметных поточных линиях с неподвижными объектами сборки в качестве транспортных средств применяются верхние подъемнотранспортные средства. Для выемки агрегатов из стапеля используются краны со специальными такелажными приспособлениями или технологическими тележками.
На участках вне стапельных и монтажных работ, с однопредметными технологическими поточными линиями, с перемещающимися объектами, при неподвижных рабочих местах детали поступают из складов на рабочие места с помощью электрокар. Межоперационные транспортные работы при монтаже могут осуществляться пульсирующими напольными и подвесными конвейерами.
5.7.Расчет пульсирующего конвейера с принудительным движением для участков внестапельной сборки
и монтажа агрегатов
Рабочий такт (в часах), т.е. промежуток времени за который изделие сходит с пульсирующего конвейера, вычисляются по формуле
ФД .Р.
n П ,
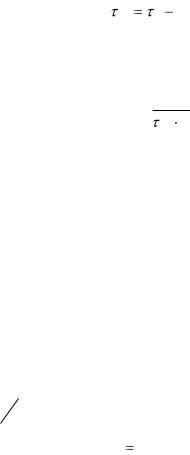
где ФД.Р. – действительный (расчетный) фонд времени на рабочем месте в планируемый отрезок времени (смена, сутки, год) в часах;
П – программа выпуска агрегатов в тот же отрезок времени в штуках.
Такт пульсирующего потока с учетом времени передвижения конвейера на длину рабочей зоны или на один конвейерный стенд в минуту определяется формулой
пл |
п |
tпер , |
где tпер – время перемещения конвейера с одной позиции на другую в минуту.
Расчетное количество стендов на поточно– пульсирующей линии зависит от трудоемкости вне стапельных работ и определяется формулой
C p Tсб n ,
пл
где Тсб – трудоемкость сборки на единицу изделия по данному виду работ в человеко-часах;
n – средняя плотность работ, или количество работающих на одном стенде конвейера.
Суммарное количество стендов на конвейере равно сумме всех видов монтажей систем самолетов. При недогрузке стендов для заданного вида монтажей необходимо перекомпоновывать стендовые задания, увеличивая объем работ в стенде за счет других монтажей.
Длина рабочей зоны конвейера определяется по формуле
L = l + И,
где l – длина стенда в метрах (длина изделия, установленного на тележку); И – расстояние между двумя стендами в метрах.
Длина всей конвейерной линии внестапельных и монтажных работ
равна
Lкл = Cпр L
где Спр – принятое количество стендов для одного вида работ.
Скорость движения пульсирующего конвейера (обычно принимается равной 1 – 3 м мин )
Vк |
L |
, |
|
||
|
tпер |
где Vк – скорость конвейера.
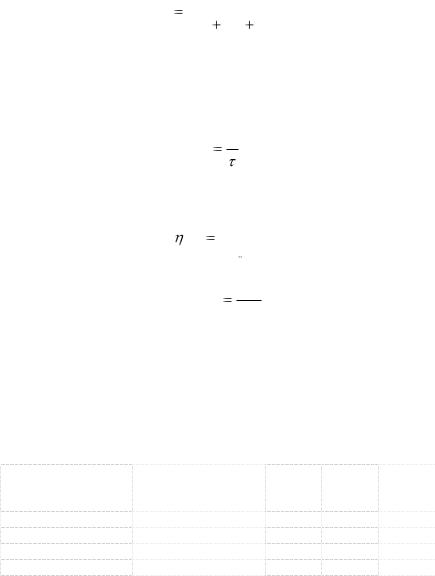
Коэффициент использования конвейерной линии определяется по формуле
kкл |
|
Т сб |
|
, |
Т сб |
tТР t |
|
||
|
ост |
где Тсб – трудоемкость сборочных работ на конвейере в человеко-часах; tост – потери времени на остановку конвейера по организационным неувязкам;
tТР – время транспортировки в часах.
Количество производственных работ на поточной линии определяется формулой
Pn T ,
где Т – трудоемкость работ на всей линии в человеко-часах; Отношение расчетного количества рабочих к принятому называется
коэффициентом загрузки рабочего места
|
РП |
. |
|
PМ |
РП пр |
||
|
|||
|
|
Количество рабочих на стапеле определяется по формуле
Р ТП ,
Фдр'
где Т – трудоемкость сборки в человеко-часах; П – программа выпуска агрегатов в цехе;
Ф’др - действительный (расчетный) фонд (годовой) производственного рабочего.
Количество вспомогательных рабочих, ИТР, КСХ и МОП определяется в процентном отношении от числа производственных рабочих по таблице 2
|
|
|
|
Таблица 2 |
Численность |
Вспомогательные |
ИТР |
КСХ |
МОП |
производственных |
рабочие |
|
|
|
рабочих в цехе |
|
|
|
|
до 100 |
40 |
25 |
3,5 |
2 |
до 200 |
35 |
20 |
3 |
1,5 |
до 400 |
30 |
1,5 |
2,5 |
1 |
до 600 |
25 |
12 |
2 |
0,8 |
5.8 Расчет площадей
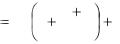
Основой для предварительного (перед компоновкой и планировкой) расчета площадей агрегатно-сборочного цеха является программа выпуска агрегатов. На ее основе составляется ведомость зависимости числа рабочих от трудоемкости работ и программа выпуска.
Рабочая площадь цеха определяется формулой
Sp = SП + SB + Sc,
где SП , SB – производственная площадь (площадь, на которой собирают и испытывают узлы и агрегаты, площади под конвейерами и транспортным оборудованием, рабочими верстаками, стендами, инструментальными шкафчиками, местами для деталей и заготовок, узлов, местами контроля, испытаний и отработки, площади проходов, узлов, местами контроля, проездов, промежуточных складов ПРОСК и материальных авансовых складов МАСК)
SB – вспомогательная площадь (площадь участков ремонта оборудования и инструмента);
Sc – складская площадь.
Производственная площадь определяется с помощью норм удельных площадей по формуле
SП = ОП + Sуд,
где
ОП – количество единиц принятого оборудования;
Sуд – удельная площадь на единицу оборудования в м2. Вспомогательная и складская площади рассчитываются в процентах: а) площади энергоузлов (тепловых вводов, вентиляции, отопления)
принимаются в размере 2 – 2,5 %; б) для магистральных (обще корпусных) проездов 4 – 8 % общей
площади корпуса.
Общая площадь цеха определяется формулой
So |
S p |
1 |
a |
в |
S |
|
|
|
|
быт |
|||||
100 |
|||||||
|
|
|
|
|
где
Sбыт – площадь бытовок;
а – коэффициент вспомогательной площади в %; в – коэффициент, учитывающей площадь, занятую проходами,
вентиляционными площадками, транспортными проездами и т.д. в %. Общая площадь цеха может быть определена как
So = Sп + 0,25Sn
где
0,25Sn – учитывает вспомогательную и складскую площади. Графики норм удельных производственных площадей на единицу
оборудования или одно рабочее место приводятся на рис. 1 – 6.