
3285
.pdf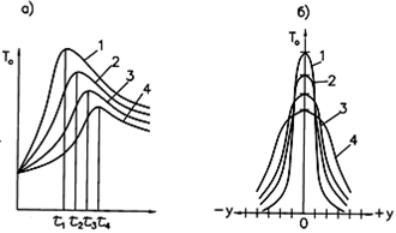
ЛЕКЦИЯ 4
По мере приближения дуги к точке (1), расположенной на оси шва (на оси Х), температура в этой точке нарастает и достигает максимума при прохождении центра дуги (0) через точку (1) (рис. 4.2). Затем, с удалением дуги, температура
вэтой точке начинает постепенно уменьшаться. Тепло, введенное в точку (1), распространяется в более холодные прилегающие участки металла, и в точках 2, 3, 4 также будет нарастать температура. Так как тепло в эти точки передается
восновном за счет теплопроводности металла, то максимальная температура в них наблюдается позже прохождения дуги через точку (1).
Причем, чем дальше находится от оси шва точка замера температуры, тем позже она достигает максимума и тем ниже максимальная температура в этой точке (рис. 4.2).
Рис. 4. 2. Изменение температуры в различных точках сварного соединения во времени (а) и распределение температуры поперек шва (б)
Чем ближе к оси шва находится точка, тем выше ее температура, тем большее время она пребывает при высокой температуре. А величина температуры и время пребывания металла при этой температуре играют решающую роль во взаимодействии металла в зоне сварки с окружающей средой и в формировании структуры металла шва и прилегающих к нему зон.
Чем выше концентрация теплового потока от сварочного источника (количество тепла на единицу нагреваемой поверхности qr), тем уже зона нагрева по оси (у), тем меньше время пребывания металла в опасном интервале температур. Величина теплового потока в зависимости от расстояния до центра пятна определяется выражением
qr = qmax e−kr2 ,
где qmaх — максимальная плотность теплового потока в центре пятна нагрева, кал/см2 с или Дж/м2 с; r — расстояние от центра пятна; k — коэффициент сосредоточенности источника, зависит от размеров нагреваемой площади и тепловой мощности источника (табл. 10).
41

ТЕПЛОВЫЕ ПРОЦЕССЫ ПРИ СВАРКЕ ПЛАВЛЕНИЕМ. ОБРАЗОВАНИЕ СВАРНОГО СОЕДИНЕНИЯ, СТРОЕНИЕ
Величина коэффициента сосредоточенности |
Таблица 10 |
|||
|
|
|||
для некоторых сварочных источников |
|
|
||
|
|
|
|
|
Источник тепла |
qmaх, кал/см2 с |
|
K, см –2 |
|
Ацетиленокислородное пламя |
50—122* |
|
0,17—0,39 |
|
Дуга с неплавящимся W- электродом |
500—600 |
|
6—14 |
|
Автоматическая сварка под флюсом |
6000 |
|
6—10 |
|
Примечание. * В зависимости от номера наконечника газовой горелки.
4.2. СВАРОЧНАЯ ВАННА
Металл, ограниченный изотермической поверхностью Т = Тпл., образует ванну расплавленного металла — сварочную ванну. В эту расплавленную зону поступает еще и расплавленный электродный или присадочный металл. Этот металл, проходя через высокотемпературную зону столба, энергично взаимодействует с атмосферой столба дуги и получает некоторые изменения в химическом составе.
При нагреве полубесконечного тела неподвижной сварочной дугой (Vсв = 0) тепло, вводимое в металл, распространяется по всем трем координатам с одинаковой скоростью. Поэтому в любой момент времени изотермические поверхности в этом случае представляют собой полусферы (рис. 4.3а).
Рис. 4.3. Изменение очертания сварочной ванны с увеличением скорости сварки или уменьшением теплопроводности свариваемого металла:
а) Vсв. = 0; б) Vсв1 < Vсв2 < Vсв3; λ1 > λ2 > λ3
42
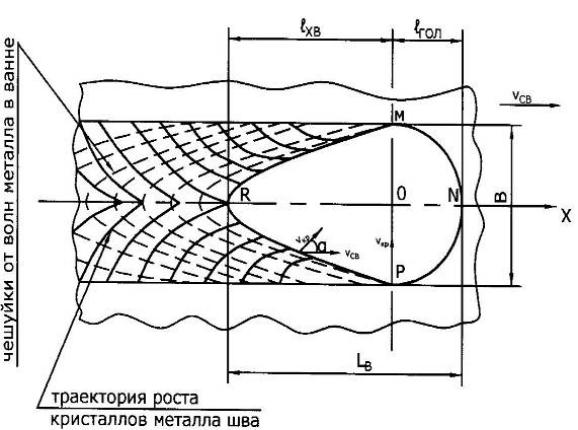
ЛЕКЦИЯ 4
Перемещение дуги по оси Х вследствие тепловой инерции металла смещает центр ввода тепла (0) относительно изотермы в сторону движения дуги (т. е. в направлении Х уменьшается расстояние (а) от точки ввода тепла до изотермы плавления). При этом с увеличением скорости сварки величина (а) уменьшается (а3 < a2 < a1; ао — расстояние от точки ввода тепла до изотермы плавления при неподвижной дуге).
Чем выше коэффициент теплопроводности свариваемого металла (например, медь), тем распределение температур в металле при движущемся источнике тепла приближается к схеме нагрева с неподвижным источником (рис. 4.3а).
С уменьшением теплопроводности величина (а) уменьшается и ванна вытягивается, как при увеличении скорости сварки (рис. 4.3, б).
В сварочной ванне различают головную (переднюю) и хвостовую (заднюю) части (рис. 4.4).
Рис. 4.4. Строение сварочной ванны (вид сверху): MNP — головная часть сварочной ванны и ее длина lгол.;
PRM — хвостовая часть сварочной ванны и ее длина lхв; Lв — общая длина ванны
Вголовной части ванны протекает процесс плавления свариваемого металла, а в хвостовой — процесс кристаллизации.
Всечении по линии RN сварочная ванна представляет собой сосуд, в котором под действием механических и электромагнитных сил из-под дуги выдувается жидкий металл, образуя углубление (рис. 4.5).
43
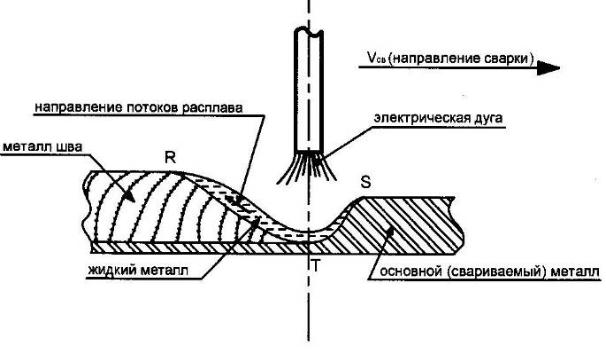
ТЕПЛОВЫЕ ПРОЦЕССЫ ПРИ СВАРКЕ ПЛАВЛЕНИЕМ. ОБРАЗОВАНИЕ СВАРНОГО СОЕДИНЕНИЯ, СТРОЕНИЕ
Рис. 4.5. Продольный разрез сварочной ванны:
ST — фронт плавления основного металла; TR — фронт кристаллизации сварочной ванны
К р и с т а л л и з а ц и я с в а р о ч н о й в а н н ы
Металл сварочной ванны кристаллизуется в специфических условиях, которые, в отличие от условий кристаллизации металла при литье, заключаются в следующем.
а) кристаллизация металла в сварочной ванне осуществляется при непрерывном вводе в металл сварочной ванны тепла от сварочного источника. Фронт кристаллизации сварочной ванны перемещается за движущимся источником сварочного тепла со скоростью сварки Vсв;
б) кристаллизация металла начинается и развивается от центров кристаллизации, находящихся в переохлажденной зоне расплава, у которого Траспл. < Тпл..
Но в сварочной ванне вследствие высоких градиентов температур, протяженность такой зоны ничтожно мала. Поэтому основную роль центров кристаллизации выполняют частично оплавленные зерна основного металла (рис. 4.6);
в) кристаллы в сварочной ванне растут в направлении, обратном максимальному теплоотводу. Фактический отвод тепла, необходимый для кристаллизации металла, определяется разностью отвода и подвода тепла в различных участках границы раздела твердой и жидкой фаз. Правее линии МР (см. рис. 4.4) подвод тепла в ванную превышает теплоотвод, поэтому по линии MNP идет процесс плавления. Левее линии МР (хвостовая часть ванны) по линии MRP осуществляется рост кристаллов.
Скорость роста кристаллов определяется скоростью теплоотвода.
44
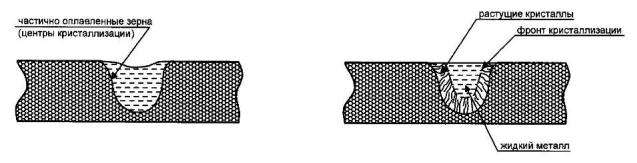
ЛЕКЦИЯ 4
Рис. 4.6. Поперечный разрез сварочной ванны:
а— ванна под дугой, б — дуга переместилась в направлении сварки
Вточках М и Р теплоотвод равен нулю (количество подводимого и отводимого тепла равны), поэтому скорость роста кристаллов в этих точках равна нулю. Максимальная скорость теплоотвода, и следовательно максимальная скорость роста кристаллов, будет в наиболее удаленной от дуги точке R. Изменение скорости роста кристаллов в сварочной ванне от границы сплавления (точка Р) до оси шва (ось ХХ) определяется формулой
Vкр = Vсв Cos α ,
где α — угол между направлением сварки направлением теплоотвода (перпендикуляр к поверхности сварочной ванны).
В точках М и Р угол между направлением теплоотвода и направлением сварки равен 90о, следовательно, Vкр = 0. В точке R (ось шва) α = 0 и скорость роста кристаллов в ней максимальна Vкр = Vсв.
Особенности условий кристаллизации сварочной ванны обусловливают формирование в металле крупнозернистой (т. к. мало центров кристаллизации) и направлений столбчатой структуры. Такая структура обладает пониженными прочностными и пластическими свойствами. Поэтому улучшение структуры металла шва является одной из важных проблем при производстве металлоконструкций.
4.3. ФОРМИРОВАНИЕ СВАРНОГО СОЕДИНЕНИЯ
Под действием тепла сварочной дуги свариваемые кромки нагреваются до температуры, превышающей температуру плавления свариваемого металла
(рис. 4.7).
Зона, нагретая выше Тпл., переходит в жидкое состояние (плавится), и под действием сил Ван-дер-Ваальса обе расплавленные кромки (рис. 4.7а) сливаются в общий объем — сварочную ванну.
Для компенсации выгорающего и разбрызгиваемого металла, а также для увеличения рабочего сечения шва в сварочную ванну вводится в виде расплавленных капель электродный металл.
45
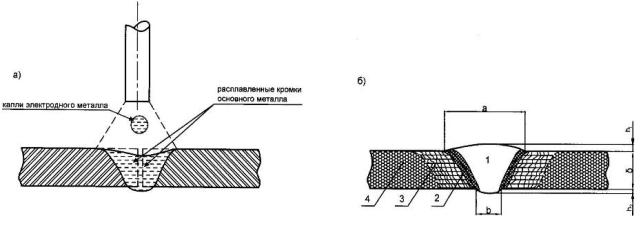
ТЕПЛОВЫЕ ПРОЦЕССЫ ПРИ СВАРКЕ ПЛАВЛЕНИЕМ. ОБРАЗОВАНИЕ СВАРНОГО СОЕДИНЕНИЯ, СТРОЕНИЕ
Рис. 4.7. Образование (а) и строение (б) сварного соединения: а и б — ширина шва и проплава соответственно;
h1 и h2 — высота шва и проплава соответственно;
δ — толщина основного (свариваемого) металла: 1 — металл шва; 2 — зона сплавления; 3 — зона термического влияния; 4 — основной металл
Поэтому после кристаллизации сварочной ванны металл шва имеет большую, чем основной металл (δ ), толщину на величину h1 + h2 (см. рис. 4.7б). В расчетах на прочность сварных соединений учитывается общая высота шва Н = δ + h1 + h2. Кроме того, в нормативах оговариваются остальные размеры: ширина шва (а) и ширина проплава (в). Для угловых швов регламентируется катет шва (к).
4.4.СТРОЕНИЕ СВАРНОГО СОЕДИНЕНИЯ
Всварном соединении различают четыре зоны (см. рис. 4.7, б): 1 — металл шва, 2 — зона сплавления, 3 — зона термического влияния или околошовная зона, 4 — основной металл.
1. Металл шва — результат переплава основного и электродного (присадочного) металлов. Если электродная проволока по химическому составу отличается от свариваемого металла, то концентрацию i-го элемента можно ориентировочно вычислить, учитывая соотношение долей основного и присадочного металлов в шве (рис. 4.8).
Доля основного металла в шве:
γ ом = F1/Fш,
где Fм = F1 + F2+ F3 — общая площадь шва.
Доля электродной проволоки:
γ э = (F1+ F2)/ Fш.
46
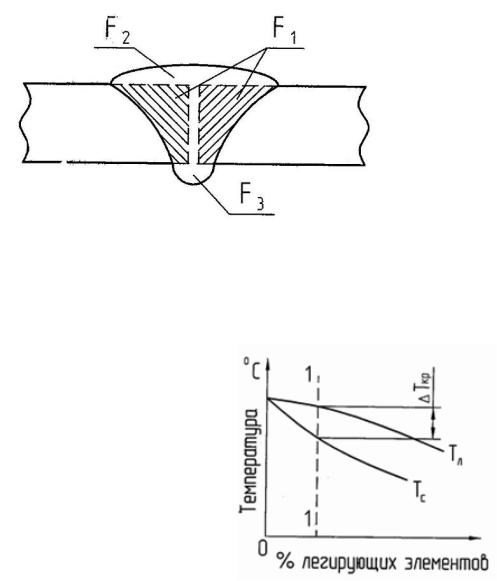
ЛЕКЦИЯ 4
Если проволока содержит Сэ процентов i-го элемента, а основной металл — Сом, то содержание этого элемента в шве будет равно
Сш = γ эСэ + γ ом Сом.
Рис. 4.8. Участие основного и присадочного металлов в формировании шва:
F1 — площадь сечения шва, полученная за счет расплавления кромок основного металла; F2 и F3 — площади сечения шва, полученные за счет электродной проволоки
2. Зона сплавления. Конструкционные |
|
|
стали, являющиеся сплавами железа с уг- |
|
|
леродом и раскисляющими или легирую- |
|
|
щими элементами (Mn, Si, Cr, Cu и др.), в |
|
|
отличие от чистого железа кристаллизу- |
|
|
ются в некотором интервале температур. |
|
|
При этом чем больше в стали концентра- |
|
|
ция этих элементов, тем шире интервал |
|
|
кристаллизации (рис. 4.9). |
|
|
При нагреве свариваемого металла |
|
|
дугой температура уменьшается с удале- |
|
|
нием от центра дуги (рис. 4.10) и поэтому |
|
|
свариваемый металл, нагретый в интерва- |
Рис. 4.9. Изменение температур |
|
ле температур Тл — Тс = ∆Ткр, в зоне тол- |
||
ликвидуса (Тл) и солидуса (Тс) |
||
щиной ∆Х будет находиться в двухфазном |
||
в зависимости от содержания |
||
твердожидком состоянии. То есть эта зона |
легирующих элементов в сплаве: |
|
будет состоять из частично оплавленных |
∆Ткр. = Тл — Тс — интервал |
|
зерен, между которыми находится жидкая |
кристаллизации сплава (1-1) |
|
фаза. Зона сплавления играет важнейшую |
|
роль в формировании прочного сварного соединения, т. к. на базе этих частично оплавленных зерен начинается рост кристаллов металла шва. И по сути дела эта зона является ответственной за прочность соединения металла шва с основным металлом.
47
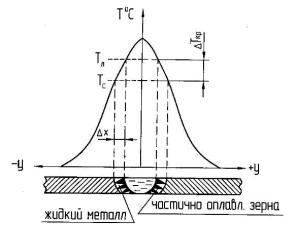
ТЕПЛОВЫЕ ПРОЦЕССЫ ПРИ СВАРКЕ ПЛАВЛЕНИЕМ. ОБРАЗОВАНИЕ СВАРНОГО СОЕДИНЕНИЯ, СТРОЕНИЕ
3. Зона термического влияния —
это зона, в которой под действием тепла, отводимого от сварочной ванны в основной металл, проходят структурные изменения, приводящие к изменению прочностных и пластических свойств металла. Сплавы на основе железа, в частности углеродистые стали, широко используются для изготовления различных металлических конструкций и изделий.
Для сварных конструкций наибольшее применение получили низкоуглеродистые стали, содержащие до
0,2—0,25 % С. Достаточно хороший комплекс свойств этих сталей, который дает возможность при сварке получать равнопрочные основному металлу сварные соединения, позволяет применять их при изготовлении металлических строительных конструкций, котлов, корпусов судов и т. д.
Основным легирующим элементом малоуглеродистых сталей, обеспечивающим предел прочности при растяжении около 40 кгс/мм2 (~390 Мн/м2), при относительном удлинении более 20 % и ударной вязкости более 15 кгс м/см2 (~1,5 МДж/м2), является углерод. Марганец в них содержится в относительно небольших количествах (около 0,4 %). Кипящие стали содержат до 0,03 % Si, а спокойные — до 0,3 % Si (т. е. в 10 раз больше).
Низкоуглеродистые нелегированные стали малочувствительны к скорости охлаждения и практически не закаливаются (т. е. в них даже при очень больших скоростях охлаждения не образуется мартенситная структура). Поэтому свойства металла после сварки по сравнению с горячекатаным состоянием изменяются мало. При сварке холоднокатаных листов в околошовной зоне наблюдается снижение прочности из-за снятия наклепа при высоких температурах.
Для этой группы сталей успешно применяют контактную электросварку, ручную дуговую штучными электродами, автоматическую и полуавтоматическую под флюсом и в защитной атмосфере углекислого газа, электрошлаковую (для сварки металла больших толщин) и газовую (для тонкого металла).
Зона термического влияния при сварке низкоуглеродистой стали может быть охарактеризована в связи с диаграммой состояния Fe-C (рис. 4.11). В околошовной зоне (зоне термического влияния) можно выделить 5 участков или зон (рис. 4.11).
Рассмотрим эти зоны применительно к сварному соединению из низкоуглеродистой стали (С ≤ 0,25 %):
1 — зона сплавления имеет небольшую ширину, т. к. интервал кристаллизации малоуглеродистых сталей невелик (около 30—40 оС) — 0,08—0,1 мм при дуговой сварке и 0,15—0,20 при газовой;
48
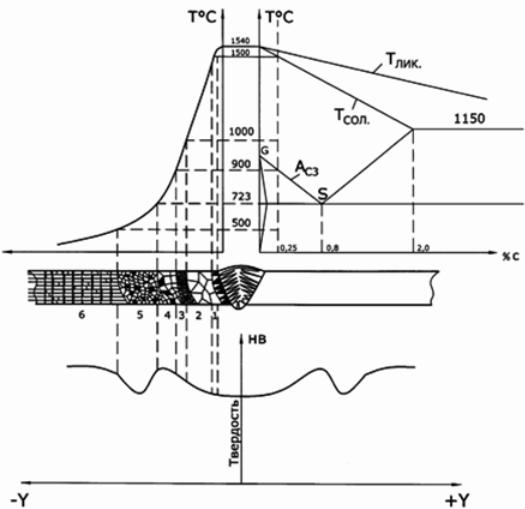
ЛЕКЦИЯ 4
2— зона перегрева. Металл, характеризуемый крупнозернистой структурой, в этой зоне нагревался выше 1000оС, поэтому здесь происходил интенсивный рост зерна. Чем ближе к зоне сплавления, тем крупнее зерно. Эта структура называется видманштеттовой и характеризуется большой хрупкостью (ударная вязкость падает в 5—7 раз по сравнению с вязкостью основного металла).
3— участок, нагреваемый в интервале температур 900—1000 оС, характеризуется мелкозернистой структурой и высокими прочностными свойствами (прочностью, пластичностью, вязкостью) — зона нормализации.
4— участок, нагревавшийся в интервале температур 750—900 оС, характеризуется почти не изменяющимся ферритным зерном с некоторым дроблением и сфероидизацией перлитных участков (зона перекристаллизации).
5— зона, нагревавшаяся до температуры ниже 500 оС, почти не меняет свою структуру горячекатаной стали, в холоднокатаной стали в этой зоне происходит отжиг (снятие наклепа) и собирательная рекристаллизация — укрепление зерен.
Рис. 4.11. Строение околошовной зоны:
а— распределение температуры в сварном соединении; б — диаграмма состояния Fe-C;
в— изменение твердости стали в околошовной зоне (перпендикулярно оси шва)
49
ТЕПЛОВЫЕ ПРОЦЕССЫ ПРИ СВАРКЕ ПЛАВЛЕНИЕМ. ОБРАЗОВАНИЕ СВАРНОГО СОЕДИНЕНИЯ, СТРОЕНИЕ
Чем концентрированнее нагрев металла в зоне сварки, тем меньше общая протяженность зоны термического влияния. Ширина этой зоны в некоторой степени зависит от толщины свариваемого металла (табл. 11).
Таблица 11
Ширина участков зоны термического влияния при сварке низкоуглеродистой стали
Ширина участков зоны |
|
Способ сварки |
|
||
|
|
Электро- |
|
||
термического влияния, мм |
Газовая |
Дуговая |
|||
шлаковая |
|||||
|
|
|
|
||
Толщина металла, мм |
3 |
10 |
50 |
10 |
|
Зона сплавления (зона № 1) |
0,2 |
0,15—0,2 |
0,15 |
0,1 |
|
Зона перегрева (зона № 2) |
4—7 |
10—12 |
3—5 |
1,0 |
|
Зона нормализации |
3—5 |
9—10 |
3—4 |
1,5—2,0 |
|
(зона № 3) |
|||||
|
|
|
|
||
Участок частичной пере- |
3,0 |
5,0 |
2—5 |
1,0 |
|
кристаллизации (зона № 4) |
|||||
|
|
|
|
||
Участок рекристаллизации |
4,0 |
8,0 |
5—7 |
1,5—2,0 |
|
(зона № 5) |
|||||
|
|
|
|
||
Общая ширина зоны |
12—13 |
25,0—30,0 |
15—20 |
3,0—5,5 |
|
термического влияния, мм |
При сварке закаливающихся сталей в околошовной зоне и в металле шва образуется закалочная мартенситная структура, которая обладает высокой прочностью, твердостью, но имеет низкую пластичность. Образование мартенситной структуры связано со скоростью охлаждения металла и температур выше температуры ТАС3 (линия GS на диаграмме Fe-C на рис. 4.12).
Низкоуглеродистые низколегированные стали малочувствительны к изменению скорости охлаждения с температурой ТАС3. Повышение содержания углерода в стали или введение легирующих элементов в низкоуглеродистые стали затормаживает распад аустенита (переход аустенита в феррит) при охлаждении. В результате металл приобретает значительную упругость: вместо феррита выделяются иглообразные структурные образования — мартенсит. Чем ниже температура распада аустенита, тем более вероятно образование мартенситной структуры. Температура распада аустенита зависит от химического состава стали и скорости охлаждения металла. С повышением концентрации легирующих элементов и скорости охлаждения возрастает вероятность появления в металле закалочной структуры (рис. 4.12). Итак, увеличение содержания углерода и легирующих элементов в стали, увеличение скорости ее охлаждения от температуры выше ТАС3 приводят к образованию мартенситной структуры. У низкоуглеродистых сталей распад аустенита происходит при высоких температу-
50