
3285
.pdf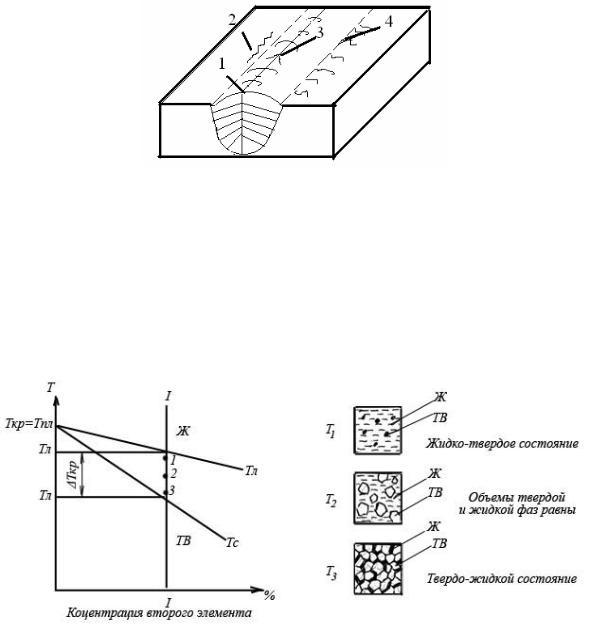
ЛЕКЦИЯ 8
8.2.ВНУТРЕННИЕ ДЕФЕКТЫ
Кэтой группе дефектов относятся горячие и холодные трещины, поры, шлаковые включения и внутренние непровары. Наиболее опасным видом дефектов являются трудно обнаруживаемые трещины и непровары, которые резко снижают работоспособность и надежность сварных конструкций
Горячие трещины при сварке – это хрупкие межкристаллитные разрушения шва и зоны термического влияния, наиболее часто возникающие в твердожидком состоянии при завершении кристаллизации (рис. 8.10).
Рис. 8.10. Виды горячих трещин в шве и околошовной зоне (1 и 2 - продольные; 3 и 4 - поперечные)
Потенциальную склонность к образованию горячих трещин имеют все конструкционные сплавы при любых видах сварки плавлением.
Горячие трещины зарождаются и развиваются при высоких температурах, когда кристаллизуется сварочная ванна. Известно, что сплавы, в отличие от чистых металлов, плавятся и кристаллизуются в некотором интервале темпера-
тур (рис. 8.11).
а) |
б) |
Рис. 8.11. Диаграмма состояния бинарного сплава (а)
и схема кристаллизации (б) сплава I-I при температурах Т1, Т2 и Т3
101

ДЕФЕКТЫ СВАРНЫХ СОЕДИНЕНИЙ
Чистые металлы (без примесей) кристаллизуются и плавятся при одной температуре: Ткр = Тпл (см. рис. 8.11,а). С увеличением концентрации легирующего элемента или примеси в сплаве при его охлаждении температура начала кристаллизации Тл, называемая температурой ликвидус (от лат. liquat – жидкий) и температура конца кристаллизации сплава Тс - температура солидус (от лат. solidus – твердый) понижаются. В интервале температур между Тл и Тс расплав находится в двухфазном состоянии, т.е. в нем присутствуют как жидкие, так и твердые частицы. Этот интервал, равный разности температур ТЛ и ТС, называется интервалом кристаллизации:
∆Ткр = Тл – Тс.
С увеличением концентрации второго элемента интервал кристаллизации увеличивается (рис. 8.11,а).
Рассмотрим процесс кристаллизации сплава 1-1. При достижении охлаждаемого сплава температуры ТЛ = Т{ в жидком металле возникают зародыши кристаллов (см. рис. 8.11, б). На базе этих зародышей при дальнейшем понижении температуры до Т2 происходит рост кристаллов, объем твердой фазы увеличивается, а жидкой уменьшается. При температуре Т3, близкой к завершению процесса кристаллизации (т.е. вблизи ТС; на диаграмме рис. 8.11 соответствует точке 3), почти весь объем занят твердой фазой. Лишь на границах кристаллитов сохраняются прослойки жидкой фазы.
В связи с изменением соотношения объемов твердой и жидкой фаз происходит изменение деформационных и прочностных свойств сплавов в температурном интервале кристаллизации. В жидком состоянии при Т>ТЛ расплав обладает неограниченной пластичностью и изменяет свою форму практически без приложения усилий. То есть относительное изменение размеров расплава весьма велико. С появлением твердой фазы в расплаве (при Т<Тл) пластичность расплава уменьшается и становится минимальной - εmin вблизи температуры солидус (рис. 8.12). В этот момент большая часть кристаллизующегося металла находится в твердом состоянии (см. рис. 8.11, Т=Т3).
Рис. 8.12. Изменение деформационной способности ε сплавов 1 и 2 в процессе его кристаллизации
102
ЛЕКЦИЯ 8
Известно, что при переходе металла из жидкого состояния в твердое резко сокращается его объем - усадка. Из-за усадки металла в стесненных условиях в процессе кристаллизации металла шва в нем возникают растягивающие напряжения и деформации (см. раздел 5 «Сварочные напряжения и деформации). Скорость нарастания напряжений и деформаций металла шва в основном опре-
деляется скоростью охлаждения металла ωохл = ∂Τ / ∂τ или связанным с ней темпом деформации ∂εсв /∂Τ . Графически темп деформации представляет собой тангенс угла α наклона линии εсв = f(Т) к оси температур. При высоких скоростях охлаждения ω2 темп деформации больше, чем при малых скоростях
охлаждения ω2 .
Температурный интервал, в котором при кристаллизации деформационная способность сплава снижается до минимума ( εmin ), называется температурным
интервалом хрупкости (ТИХ). ТИХ зависит от интервала кристаллизации и приближенно можно принять ТИХ = ∆ Ткр.
Если деформация металла в интервале кристаллизации по величине превысит минимальную его деформационную способность εmin , то в сварном шве
возникнут горячие (кристаллизационные) трещины. Например, при сварке сплава 1, имеющего интервал кристаллизации ∆ Т1, со скоростью охлаждения ω1 , в шве неизбежно образуются горячие трещины. Уменьшение скорости ох-
лаждения сварного соединения и связанное с этим уменьшение темпа деформации (линия ω2 ) позволяют избежать разрушения металла шва. В этом случае
величина сварочных информаций будет меньше деформационной способности сплава εmin .Если путем изменения химического состава металла шва умень-
шить величину интервала хрупкости ∆ Т2 (сплав 2, рис. 8.12), то горячих трещин в шве не будет даже при высоком темпе деформации ω1 .
Таким образом, зарождение кристаллизационных трещин зависит от трех параметров:
−величины интервала кристаллизации сплава, которая в основном определяется его химическим составом;
−величины минимальной пластичности сплава в интервале кристаллизации εmin . Она зависит от химического состава сплава, размеров кристаллитов,
образующихся при кристаллизации сварочной ванны и от направления их роста
вванне и др.;
−темпа нарастания упругопластических деформаций в процессе кристаллизации и последующего охлаждения сварного соединения. Темп деформации в основном определяется скоростью охлаждения металла и жесткостью сварной конструкции.
Варьируя эти факторы, можно найти оптимальные конструктивные и технологические варианты проектирования и производства сварных металлоконструкций, стойких против горячих трещин. Рассмотрим этот вопрос подробнее.
103
ДЕФЕКТЫ СВАРНЫХ СОЕДИНЕНИЙ
Влияние химического состава стали на склонность к образованию горячих трещин. Химический состав свариваемого металла оказывает первостепенное влияние на стойкость шва против образования кристаллизационных трещин, так как от химического состава стали зависят величина интервала кристаллизации ∆Ткр и минимальной пластичности εmin в этом интервале. Все химические
элементы, входящие в состав металла шва, условно можно разделить на три основные группы.
К первой группе относятся элементы, присутствие которых снижает стойкость металла шва против кристаллизационных трещин. Эти элементы, с увеличением их концентрации в сварочной ванне, расширяют интервал кристаллизации и, следовательно, увеличивают ТИХ. Такие элементы (или примеси) на-
зывают вредными.
Во вторую группу входят элементы, которые в зависимости от их сочетания и концентрации могут оказывать как положительное, так и отрицательное влияние на стойкость материала против горячих трещин.
Третья группа включает элементы, присутствие которых не влияет на образование горячих трещин.
Сера является одной из наиболее вредных примесей в сварных металлоконструкциях. Низкоуглеродистая сталь без примесей серы кристаллизуется в интервале 1530—1480 оС (∆Ткр = 50 оС). При наличии серы в сварочной ванне она образует химическое соединение FeS. Смесь FeS с железом кристаллизуется в отличие от стали без примесей при температуре 980 оС. Таким образом, сера увеличивает интервал кристаллизации до ∆Ткр = 1530 – 980 = 550 оС, то есть
в11 раз (см. рис. 8.3). Поэтому в шве, когда основная масса металла уже закристаллизовалась, остаются участки металла, где низкоплавкие сульфидные прослойки, располагаясь между кристаллитами, резко повышают вероятность образования горячих трещин.
Очень вредна сера и в легированных сталях с большим содержанием никеля (нержавеющие стали, жаропрочные сплавы), т. к. в них образуются еще бо-
лее легкоплавкие эвтектики на базе сульфида NiS, кристаллизующиеся при 644 оС. Усиливать вредное влияние серы могут и другие элементы, в частности,
внизкоуглеродистых сталях — углерод. В шов сера попадает из основного металла и электродной проволоки, а также из электродных покрытий и флюсов.
Концентрация серы в сталях для сварных металлоконструкций не должна превышать 0,05 % (практически в настоящее время применяют стали с содержанием серы 0,03—0,04 %). В присадочной проволоке концентрация серы колеблется в пределах 0,02—0,04 %, а в проволоках повышенной чистоты, применяемых при сварке особо ответственных изделий, серы содержится не более 0,015 %. Также жестко ограничивается содержание серы в электродных покрытиях и флюсах.
Фосфор также относится к вредным элементам. Он, как и сера, уменьшает стойкость металла против горячих трещин из-за образования легкоплавкой смеси FeP-Fe (эвтектика).
104
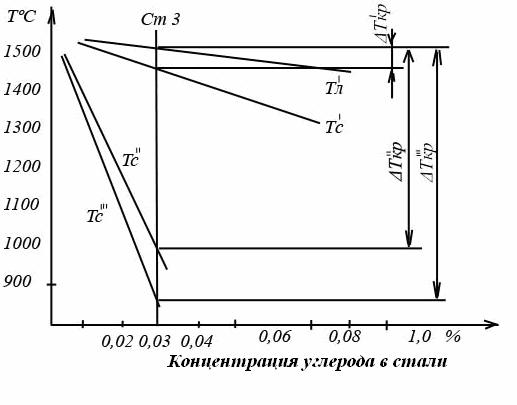
ЛЕКЦИЯ 8
Кроме того, фосфор резко снижает ударную вязкость стали, особенно при низких температурах. Нержавеющие и жаропрочные стали имеют аустенитную структуру, а растворимость фосфора в аустените меньше, чем в феррите (фер- ритно-перлитная структура характерна для низкоуглеродистых сталей).
Поэтому фосфор особенно опасен при сварке нержавеющих и жаропрочных сталей. Вредное действие фосфора усиливается при наличии в металле серы, так как в этом случае температура кристаллизации еще больше снижается (линия Т```с — см. на рис. 8.13), а интервал кристаллизации увеличивается до ∆Т```кр. Поэтому в углеродистых конструкционных сталях содержание фосфора допускается не более 0,055 %, а в легированных — не более 0,03 %, в электродной проволоке — до 0,04 %.
Обычно для уменьшения вероятности образования горячих трещин либо снижают концентрацию вредных примесей, либо связывают их в тугоплавкие прочные соединения.
Например, марганец, обладая большим химическим сродством с серой, чем железо, связывает серу в тугоплавкое соединение — сернистый марганец (MnS) и таким образом уменьшает интервал кристаллизации:
FeS + Mn = MnS + Fe.
Рис. 8.13. Угол диаграммы состояния железо — углерод: Тл — линия ликвидус (начало кристаллизации);
Тс` , Тс `` и Тс ``` — линия солидус (окончание кристаллизации) для стали без серы, с серой и при одновременном присутствии в стали серы и фосфора соответственно;
∆Т`кр, ∆ Т``кр, ∆ Т```кр — интервалы кристаллизации
105
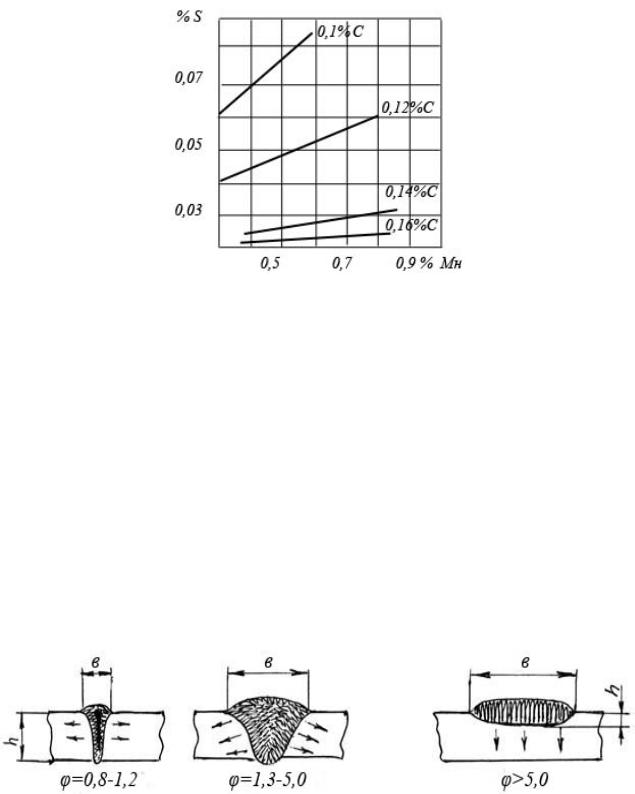
ДЕФЕКТЫ СВАРНЫХ СОЕДИНЕНИЙ
Совместное влияние серы, углерода и марганца на образование горячих трещин в сварных соединениях из низкоуглеродистой стали показано на рис. 8.14.
Рис. 8.14. Совместное влияние S, Mn и C на стойкость швов
противкристаллизационных трещин (выше линии трещины в шве есть, ниже линии трещин нет)
Из рис.8.14 следует, что вредное действие серы в присутствии углерода усиливается.
Например, при содержании углерода в стали 0,1 % трещины в шве не образуются даже при наличии 0,06 %, а введение в сталь 0,6 % Mn позволяет получать швы без трещин с содержанием серы до 0,085 %. При увеличении концентрации углерода в стали требуется снижать допустимую концентрацию серы в металле шва. Марганец ослабляет ее вредное действие и, следовательно, повышает стойкость швов против горячих трещин.
Влияние формы сварочной ванны. Изменение режимов сварки приводит к изменению формы сварочной ванны (формы шва), которая влияет на направление теплоотвода и, как следствие, на направление роста кристаллитов в шве. Конфигурация шва характеризуется коэффициентом формы шва φ = b/h, где b — ширина шва, h — глубина проплавления (рис. 8.15).
Рис. 8.15. Влияние формы шва на направление роста кристаллитов (стрелками показано направление теплоотвода)
106
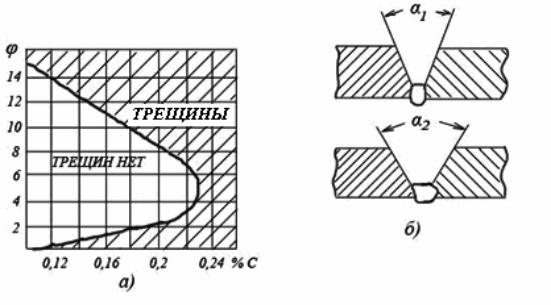
ЛЕКЦИЯ 8
Кристаллиты в шве растут в направлении, обратном теплоотводу. При узком швеи глубоком проваре (φ = 0,8–1,2, см. рис. 8.15) кристаллиты растут навстречу друг другу.
При этом в зоне срастания кристаллитов может скапливаться легкоплавкая эвтектика с повышенным содержанием S и P (черная полоса на рисунке) и высока вероятность образования кристаллизационных трещин.
При чашеобразной форме шва (φ = 1,3 – 5,0) образуется дезориентированная мелкозернистая структура, легкоплавкие составляющие распределяются более равномерно по сечению шва.
При наплавочных работах, когда укладываются широкие швы с малой глубиной проплавления (φ > 5,0), кристаллиты растут снизу вверх, вытесняя легкоплавкие составляющие на поверхность шва, при этом в верхних слоях шва возможно возникновение горячих трещин, обнаруживаемых внешним осмотром.
Зависимость критического содержания углерода в стали, выше которого в шве возникают горячие трещины, от коэффициента формы шва (рис. 8.16) свидетельствуют о том, что наиболее благоприятной формой, стойкой против образования кристаллизационных трещин является чашеобразный шов
(φ = 1,3 – 5,0).
Рис. 8.16. Зависимость критического содержания углерода в стали от коэффициента формы шва (а) и влияние угла разделки на форму корневого шва (б)
Р е г у л и р о в а н и е т е м п а д е ф о р м а ц и и
Как уже было сказано, темп деформации определяется в основном скоростью охлаждения металла шва. Согласно исследованиям академика
107
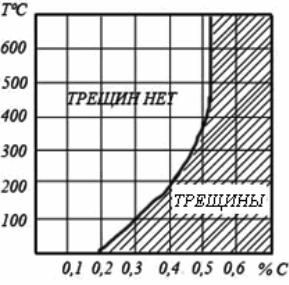
ДЕФЕКТЫ СВАРНЫХ СОЕДИНЕНИЙ
Н. Н. Рыкалина скорость охлаждения, ω, оС/с, при сварке листов встык в один проход можно вычислить по формуле
ω = Αδ2(T −To )2 , q}
где А — коэффициент, зависящий от теплопроводности, теплоемкости и удельного веса свариваемого металла; δ— толщина свариваемого листа; q/V — погонная энергия дуги; Т — температура, при которой вычисляется скорость охлаждения; То — начальная температура изделия или температура сопутствующего подогрева.
Из приведенной формулы следует, что уменьшение скорости охлаждения, а следовательно, и темпа деформации можно достичь увеличением температуры сопутствующего подогрева (То) или увеличением погонной энергии (например, за счет снижения скорости сварки V).
Предварительный или сопутствующий подогрев изделия является эффективной мерой, обеспечивающей уменьшение темпа деформации кристаллизующегося металла.
Температура подогрева, при которой исключается образование горячих трещин, зависит от химического состава металла шва. Чем больше углерода в металле шва, тем более высокая требуется температура подогрева (рис. 8.17).
На практике свариваемые изделия подогревают в печах или газовым пламенем. В зависимости от химического состава стали подогрев осуществляют в температурном интервале 150—500оС. Кроме изменения температурного режима, величину растягивающих напряжений и темп деформации металла в интервале кристаллизации можно уменьшить за счет рационального конструирования узлов и элементов (уменьшения количества и сосредоточенности швов, выбора оптимальной разделки кромок (см. рис. 8.15, б), устранения излишней жесткости сварных узлов и др.).
Влияние размеров первичных кри-
сталлов в шве. Деформация металла шва при высоких температурах в процессе его кристаллизации и последующего остывания осуществляется, в основном, путем скольжения и поворота кристаллитов относительно друг друга. Следовательно, чем меньше размеры кристалликов в шве, тем больше плоскостей
108
ЛЕКЦИЯ 8
скольжения, тем более пластичен металл, тем больше значение εmin в интервале
кристаллизации. Кроме того, измельчение кристаллитов в шве в процессе кристаллизации способствует уменьшению степени химической неоднородности шва, то есть уменьшению концентрации вредных примесей на границе кристаллитов. Поэтому швы с мелкозернистой структурой обладают более высокой стойкостью против кристаллизационных трещин.
Х о л о д н ы е т р е щ и н ы
В отличие от кристаллизационных трещин холодные образуются в сварных соединениях при остывании шва и околошовной зоны до относительно невысоких температур, как правило, ниже 200 оС. К этому моменту металл шва и околошовной зоны приобретает высокие упругие свойства, присущие ему при комнатной температуре.
Наиболее часто холодные трещины возникают в сварных соединениях из среднелегированных и высоколегированных сталей перлитного и мартенситного классов, т. е. сталей, восприимчивых к закалке. Значительно реже они образуют в сварных соединениях из низколегированных ферритно-перлитных сталей и высоколегированных сталей аустенитного класса.
Основными причинами возникновения холодных трещин являются образование закалочных структур (закалочные трещины) и наличие водорода в металле шва (водородные трещины). Образование закалочных структур происходит при температуре 200оС и ниже, т. е. процесс происходит тогда, когда металл приобрел высокие упругие свойства. При этом, вследствие выделения мартенсита, на его границах возникают напряжения, которые, складываясь с остаточными растягивающими напряжениями, могут привести к образованию холодных трещин в шве или околошовной зоне.
Водородные трещины появляются в случае, если в процессе сварки в шве накопилось много водорода, последний при остывании шва диффундирует из наводороженного металла шва в околошовную зону, где его концентрация ничтожна.
Здесь, скапливаясь в микропустотах и превращаясь в молекулярный водород 2[H ]→ H2 , он создает громадное давление (более 100 атм), под действием
которого происходит разрушение металла (образуются холодные трещины). Наличие внутренних дефектов в сварном соединении (пор, шлаковых включений) увеличивает вероятность накопления в них водорода и образования холодных трещин.
Совместное действие образования закалочных структур и водорода усиливает опасность возникновения холодных трещин в сварных соединениях из средне- и высоколегированных сталей перлитного и мартенситного классов.
Исходя из описанного выше механизма образования холодных трещин для предотвращения их возникновения рекомендуются следующие меры.
109
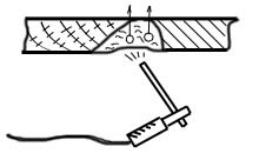
ДЕФЕКТЫ СВАРНЫХ СОЕДИНЕНИЙ
1.Надо стремиться к уменьшению содержания водорода в шве. Это достигается тщательной очисткой свариваемой зоны от ржавчины, содержащей много влаги, просушиванием и прокалкой электродов и флюсов, осушкой и контролем содержания влаги в защитных газах.
2.Необходимо проводить мероприятия по предотвращению образования закалочных структур в шве и околошовной зоне. Это достигается за счет снижения скорости сварного соединения путем применения предварительного сопутствующего и последующего подогревов, применения аустенитной электродной проволоки (она не образует мартенситную структуру), охлаждения сваренного узла в печи, утепления асбестом и др.
П о р ы и н е м е т а л л и ч е с к и е в к л ю ч е н и я
Поры и неметаллические (шлаковые) включения возникают в металле шва в результате взаимодействия металла с окружающей средой как на стадии плавления, так и в процессе кристаллизации сварочной ванны.
Поры в сварных швах образуются, если в период кристаллизации сварочной ванны происходит выделение растворенного газа в жидком металле газообразование и пузырьки газов не успевают удалиться из металла до его затвердевания.
Газовыделение в сварочной ванне возможно по двум причинам:
−в связи с химическими реакциями в расплавленном металле, при которых продуктами реакции являются газы;
−в связи с выделением из жидкого металла растворенных в них газов.
При сварке сталей одной из основных причин образования пор в металле
шва является реакция углерода с окисью железа, которая присутствует в сва-
рочной ванне. В результате этой реакции в сварочной ванне выделяется окись углерода:
FeO + C = Fe + CO↑ .
Так как окись углерода (СО) нерастворима в жидком железе, то в сварочной ванне происходит бурное выделение газовых пузырьков, всплывающих вверх. В результате этого поверхность ванны пузырится, кипит. Если при сварке в нижнем положении время существования сварочной ванны tв = Lв \ Vсв (Lв — длина сварочной ванны) достаточно большое (при малых скоростях сварки), то пузырьки успеют всплыть на поверхность сварочной ванны и металл шва будет плотным.
При сварке в потолочном положении удаление СО из металла шва за счет всплывания газовых пузырьков невозможно (рис. 8.18). При наличии в металле элементов с большим срод-
Рис. 8.18. Всплывание газовых пузырьков 110 при потолочной сварке