
2733
.pdf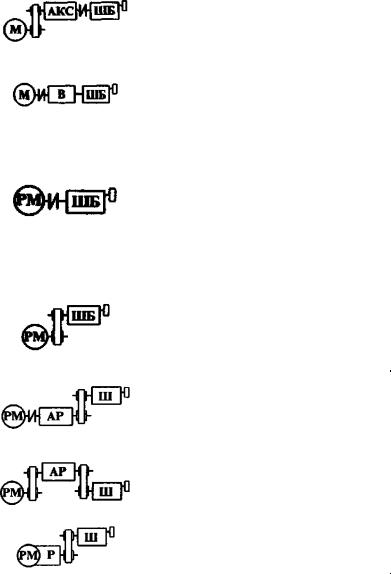
|
|
|
Продолжение табл. 1 |
|
|
|
|
1 |
2 |
3 |
4 |
|
|
|
|
|
|
М |
В станках токарных, |
|
|
фрезерных, свер- |
|
4 |
|
АКС, ШБ |
|
|
лильных (в том числе |
||
|
|
|
|
|
|
|
в станках с ЧПУ) |
|
|
|
|
|
|
М |
В легких |
|
|
токарных |
|
5 |
|
В, ШБ |
|
|
станках |
||
|
|
|
|
|
|
|
|
|
|
|
В тяжелых станках с |
|
|
|
электродвигателем |
|
|
|
постоянного тока; в |
|
|
|
станках с ЧПУ - рас- |
6 |
|
|
точных, фрезерных, |
|
|
|
карусельных, свер- |
|
|
РМ |
лильно-фрезерно- |
|
|
ШБ |
расточных |
|
|
|
|
|
|
|
В станках с ЧПУ – |
7 |
|
|
токарных, фрезерных, |
|
|
сверлильно-расточных |
|
|
|
|
|
|
|
|
|
8 |
|
|
|
|
|
РМ |
|
|
|
АР |
В токарных станках |
|
|
||
9 |
|
|
с ЧПУ, легких |
|
|
и средних |
|
|
|
|
|
|
|
|
|
10 |
|
РМ-Р |
|
|
|
|
|
71
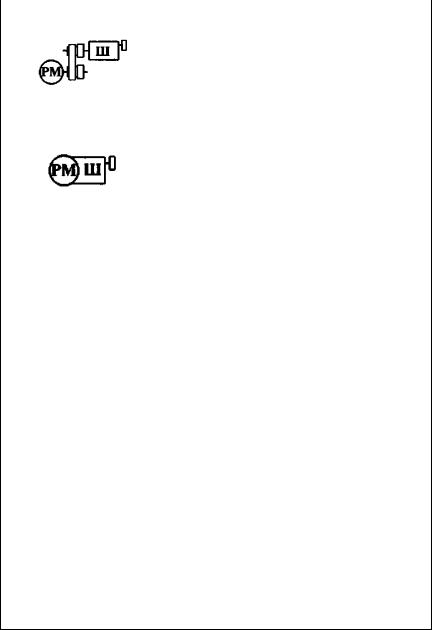
|
|
|
Продолжение табл. 1 |
|
1 |
2 |
3 |
4 |
|
|
|
|
|
|
|
|
|
В токарных и револьвер- |
|
11 |
|
РМ |
ных автоматах для крупно- |
|
|
ПР |
серийного и массового |
||
|
|
|||
|
|
|
производства |
|
|
|
|
|
|
|
|
|
В быстроходных станках |
|
|
|
|
-токарных, |
|
12 |
|
РМ-Ш |
консольно-фрезерных, |
|
|
|
|
сверлильных, шлифоваль- |
|
|
|
|
ных |
|
|
|
|
|
|
Примечания:
1. Приняты следующие буквенные обозначения узлов привода, обеспечивающих регулирование скорости:
М - нерегулируемый асинхронный электродвигатель переменного тока (одноили многоскоростной);
РМ - регулируемый (бесступенчато) электропривод с двигателем переменного или постоянного тока;
В - механический вариатор (фрикционный, цепной, зубча-
тый);
ШБ - шпиндельная бабка с встроенной коробкой скоростей и шпиндельным узлом;
Ш - шпиндельная бабка со шпиндельным узлом; АКС - автоматическая коробка скоростей с переключением
зубчатых передач электромагнитными муфтами; АР - автономный редуктор с автоматическим переключением
скоростей гидравлическим устройством; РМ-Р - электромеханический узел "мотор-редуктор";
ПР - переключаемая двух-, трехступенчатая ременная пере-
дача;
РМ-Ш - электромеханический узел "мотор-шпиндель" или "электрошпиндель".
72
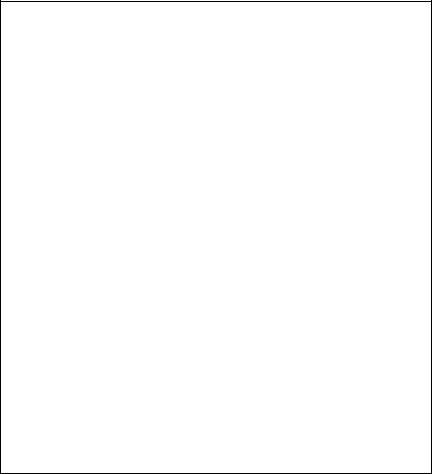
Продолжение табл. 1
2.Для схем 1...5: Достоинства ступенчато регулируемых приводов: небольшая стоимость, высокая надежность, простота обслуживания, жесткость характеристики, небольшие габариты электродвигателя, возможность получения постоянства мощности во всем диапазоне скоростей шпинделя.
Недостатки: потеря производительности (из-за ступенчатого ряда частот вращения шпинделя), сложность кинематики, ухудшающиеся шумовые и энергетические характеристики, сравнительно большие динамические нагрузки и время переходных процессов в диапазоне высоких частот вращения, сложность автоматизации переключения скоростей.
3.Для схем 6...12: Достоинства приводов с бесступенчатым регулированием: получение оптимальных по скорости режимов резания, плавное изменение скорости во время работы, удобство автоматизации управления, упрощение кинематики и конструкции приводного механизма, улучшающие его шумовые, энергетические
идинамические характеристики.
Недостатки: сравнительно высокие стоимость и габариты электропривода, ограничение: диапазона регулирования с постоянной мощностью электропривода (обычно до 3 - 4, при специальном исполнении до 5 - 8), максимальной частоты вращения (в случае двигателя постоянного тока), мощности привода (в случае частотно-регулируемого двигателя, переменного тока).
Дополнительные преимущества регулируемых приводов типа "мотор-редуктор", "мотор-шпиндель" и "электрошпиндель": компактность, высокий КПД, снижение трудоемкости изготовления и сборки станка
По компоновке приводы главного движения подразделяют на встроенные (с механизмом передач, встроенным в шпиндельную бабку, схемы 1...7) и разделенные (в которых коробка скоростей и шпиндельная бабка являются отдельными узлами, соединенными ременной передачей). В разделенном приводе в шпиндельной бабке размещен только шпиндельный узел (схемы 8...11) или, иногда, зубчатый перебор.
73
При выборе компоновки руководствуются соображениями удобства размещения узлов в пространстве, требованиями параметров шероховатости поверхности изделия и точности положения шпиндельного узла, уменьшения влияния на него источников тепловыделения и колебаний, ограничениями в передаче требуемых значений мощности, крутящих моментов и скорости вращения, стремлением максимально использовать унифицированные покупные узлы.
Область применения коробок скоростей с переключающими электромагнитными муфтами - передача мощности до 50 кВт; зубчатых приводов с переключением ступеней передвижением зубчатых колес - без ограничения передаваемой мощности; приводов с ременной передачей на шпиндель: клиновой, поликлиновой - до 50...60 кВт; зубчато-ременной до 200 кВт.
Предельные скорости ремней в главном приводе станков: клиновых - 25 м/с, поликлиновых и узких клиновых – 30...90 м/с, зубчатых – 40...45 м/с, плоских – 30...35 м/с (при особой конструкции и технологии изготовления до 80 м/с).
4.1.5. Особенности проектирования и расчета привода главного движения станков
Алгоритм проектирования главного привода металлорежущих станков включает следующие процедуры:
-предварительный анализ исходных технологических данных по обработке заданной совокупности деталей и технических требований к станку и определение технических ха-
рактеристик - номинальной мощности Рном, значений nшп.min, nшп.max диапазонов регулирования скорости и других, необходимых для кинематического синтеза и проектировочных силовых расчетов;
-выбор схемы построения привода (табл. 1), обеспечивающей основные технические требования и характеристики;
-выбор приводного электродвигателя по номинальной мощности и схеме построения привода;
74
-синтез кинематики привода на основе выбранной схемы построения, определяющий кинематическую схему механизма;
-проектировочный силовой расчет приводного механизма и эскизное проектирование;
-разработка рабочего проекта и проведение комплекса поверочных расчетов.
4.1.6. Определение мощности электродвигателя
Мощность приводного электродвигателя расходуется на полезную работу в процессе резания и на различного рода потери в приводе. Определение номинальной мощности двигателя осуществляют на практике разными методами приближенно или более точно и надежно. Приближенный способ - по наиболее тяжелому режиму, допускаемому режущим инструментом, или по станку-аналогу, применяется в основном для универсальных станков различных типов и ведет, как правило, к завышению мощности, габаритов и стоимости привода и станка
вцелом. Более точный метод определения на основе полной картины нагружения - распределения (гистограммы, нагрузоч-
ного графика) мощности резания Рэф и крутящего момента Мэф, учета характера и длительности циклов обработки изделий, возникающих динамических нагрузок используется и для универсальных, и для специальных, специализированных, агрегатных станков.
Значения Рэф и Мэф подсчитывают по эмпирическим формулам для всех технологических переходов процесса обработки деталей-представителей (универсальные станки) или конкретных деталей, предназначенных для обработки на данном станке (специальные и специализированные станки), а затем пересчитывают для вала электродвигателя с учетом потерь
вмеханизме, кинематических соотношений и характеристик регулирования. Для полученных распределений определяются характеристики, необходимые при выборе мощности и крутящего момента электродвигателя - эквивалентные (среднеквад-
75

ратичные) Рэкв и Мэкв и максимальные (рабочие и пусковые)
значения Рmax, Мmax и Мп.
Выбор мощности Рпот на основе распределения нагрузки на валу приводного электродвигателя проводится по техническим критериям - предельно допустимому нагреву и перегрузкам и технико-экономическому критерию - наибольшей производительности или наименьшим приведенным затратам. Технические критерии для всех случаев берутся одни и те же. При определении мощности двигателя для станков специальных, специализированных, а также некоторой части универсальных, используется критерий максимальной производительности в виде условия обеспечения наибольшей мощности рабочего режима. Выбор Рпот электродвигателя осуществляется по расчетному значению мощности Ррасч, причем Ррасч = Рэкв,
если |
Pmax |
Рэкв , и Ррасч = |
Pmax |
, если |
Pmax |
Рэкв . Здесь Кп - |
|
|
|||||||
|
|||||||
Кп |
|
|
|||||
|
|
К п |
К п |
коэффициент нагрузочной способности двигателя по мощности: отношение номинальных значений мощности при длительном непрерывном режиме работы и при тридцати (пятнадцати) минутном режиме (обычно Кп = 1,3...1,4 для регулируемых электродвигателей и Кп = 1,5...1,6 для нерегулируемых асинхронных двигателей). Для станков с большими пусковыми нагрузками проводится дополнительная проверка двигателя по этому критерию.
Для проверки правильности выбора электродвигателя на последующих стадиях проектирования рекомендуется провести сопоставление диаграмм максимальных значений мощности (крутящих моментов) на шпинделе, соответствующих технологическим требованиям обработки (на различных nшп, инструментами из разных материалов), с учетом перспективных режимов резания и располагаемых приводом.
Для универсальных станков целесообразно определять оптимальную мощность, соответствующую минимуму приведенных затрат (на изготовление и эксплуатацию), если известен весь набор конкретных экономических данных, входящих
76
в функцию затрат, связанных с мощностью привода. На практике из-за упрощенного подхода к анализу исходных технологических данных и потерь мощности, отсутствию оценок оптимальности часто отмечается завышение мощности двигателя по крайней мере на одну ступень или габарит.
Потери мощности и КПД механической части привода и электропривода необходимо знать для определения обеспечиваемой станком мощности резания, правильного выбора типа привода и мощности электродвигателя, уточнения расчетных нагрузок для силовых расчетов, оценки расхода и потерь электроэнергии.
В приводах современного автоматизированного оборудования при определении потерь учитывают влияние регулирования скорости и изменения уровня нагрузки, новые типы конструктивных элементов - ременных передач, шпиндельных опор, новые виды смазочных материалов, влияние температуры смазки и т.п.
Величина потерь в механической части зависит от типа и сложности кинематической схемы и схемы построения привода, смазки, вида вращающихся (перемещающихся) элементов
и их параметров, величины nшп и Рэф.
Для уменьшения потерь холостого хода и общих потерь в механической части привода выбирают схемы с короткими кинематическими цепями, применяют регулируемый электродвигатель с упрощенным передаточным механизмом, сложенные кинематические структуры, используют для опор скоростных валов подшипники с малым трением и системы минимальной смазки.
В приводах с регулируемыми электродвигателями и короткими кинематическими цепями (табл. 1, схемы 6...12) КПД по мощности механической части составляет при полной нагрузке ηм ≈ 0,9...0,95 на расчетной частоте вращения nшп.р и
ηм = 0,7...0,8 на nшп.max (nшп.max ≤ 4000 мин -1). В приводах с асинхронным нерегулируемым двигателем и многоступенча-
тыми механизмами (схемы 1...5) ηм = 0,75...0,85 (при nшп.р) и
ηм = 0,6...0,75 (при nшп.max).
77
Потери мощности электрической части привода определяются суммой потерь в электродвигателе и преобразователе.
С учетом потерь в электроприводе общий КПД по мощности главного привода с регулируемым двигателем (схемы 6...12) составляет при полной нагрузке ηо = ηм ηэл ≈ 0,7...0,8 на
nшп.р и ηо = 0,5...0,7 на nшп.max. В приводе с нерегулируемым электродвигателем и развитым многоступенчатым механизмом
(схемы 1...5) ηо = 0,65...0,75 на nшп.р и ηо = 0,5...0,7 на nшп.max.
Приводы с упрощенной механической частью, но более сложным электроприводом в отношении общего КПД и суммарных энергетических потерь примерно равнозначны приводам с простым односкоростным электродвигателем и многовальной многоступенчатой коробкой скоростей или редуктором.
КПД по электроэнергии привода (отношение расхода электроэнергии на работу, совершаемую на выходе привода станка, к расходу электроэнергии на работу, совершаемую на входе привода, при заданных режимах нагружения и времени работы), определенное с учетом типовых переменных режимов работы главного привода, составляет: для механической части
(по схемам 6...12) ηэм = 0,7...0,9; 0,6...0,7 (по схемам 1-5). Общий ηэо = 0,5...0,75 (схемы 6 - 12), ηэо = 0,45...0,65 (схемы 1...5).
Синтез кинематики включает выбор подходящих вариантов схем построения привода, разбиение диапазона регулирования и общего передаточного числа и между электроприводом и соответствующими узлами механической части, расчет вариантов структурных сеток, построение графиков частот вращения и кинематической схемы механизма.
В приводе с регулируемым электродвигателем разделение общего диапазона между двигателем и механической частью стремятся осуществить таким образом, чтобы обеспечить необходимое перекрытие соседних поддиапазонов частот вращения шпинделя или небольшой разрыв между ними (если это оправдано характером технологического процесса). При ступенчатом и комбинированном регулировании для синтеза кинематики используют закономерности геометрического ряда ступеней скорости. При расчете структурных сеток передаточ-
78
ные отношения зубчатых передач ограничивают величиной редукции 4 и повышения 2.
Кинематические структуры применяют двух видов - множительные (с последовательно соединенными группами передач между соседними валами) и сложенные (с пропуском ряда валов при реализации некоторых ступеней скоростей). Множительные структуры обычно приводят к длинной многоваловой кинематической цели, а сложенные позволяют упростить конструкцию, уменьшить число зубчатых колес, сократить габариты, металлоемкость и стоимость привода. Сложенные структуры способствуют уменьшению потерь мощности на высоких скоростях, повышению КПД и надежности, улучшению динамического качества. При отборе подходящего графика частот вращения (варианты которых представляют различные сочетания передаточных отношений, удовлетворяющие заданным ограничениям) руководствуются в первую очередь следующими критериями: длиной кинематических цепей привода, его габаритами и трудоемкостью изготовления.
Сокращение длины и упрощение кинематических цепей улучшает экономические показатели, повышает надежность привода и КПД, улучшает динамические характеристики и уменьшает число источников погрешностей.
Габариты передач, влияющие на размеры и массу корпусных деталей, существенно зависят от частоты вращения валов nв, поскольку nв обратно пропорциональна диаметру вала в четвертой степени и модулю зубчатого колеса в кубе. Рекомендуют входной и первые промежуточные валы проектировать достаточно быстроходными, наибольшую редукцию осуществлять в передачах на шпиндель и предшпиндельной, соблюдая, по возможности, принцип веерообразного построения графика частот вращения.
Трудоемкость и сроки проектирования и изготовления привода значительно сокращаются для тех вариантов кинематики, которые позволяют компоновать привод (полностью или частично) из покупных, унифицированных узлов (модулей) - коробок передач, редукторов, мотор-редукторов, шпиндель-
79
ных бабок и т.п. Централизованное изготовление таких узлов на специализированных производствах обеспечивает более высокое качество и надежность привода, однако при непродуманной унификации могут ухудшиться возможности главного привода по обеспечению технологических характеристик станка.
Основные методы уменьшения динамических нагрузок и колебаний, возникающих в главном приводе при переходных процессах и прерывистом резании:
оптимизация процессов разгона и торможения на любой частоте вращения шпинделя применением в главном приводе регулируемых электроприводов, позволяющих настройку переходных процессов по требуемому закону; подбор рациональных параметров конструкции и кинематики привода, влияющих на величину изгибно-крутильной жесткости и собственных частот системы;
применение демпфирующих и предохранительных элементов и устройств (ременные передачи, муфты с упругими и упругодемпфирующими элементами, специальные демпферы и динамические гасители колебаний).
Значения динамических характеристик при переходных процессах в приводах с регулируемыми электродвигателями зависят от кратности приведенного момента инерции привода γ0 и установленного токоограничения в электроприводе. Время пуска и торможения для таких приводов зависит, кроме того, от типа реверса электропривода и некоторых других электротехнических характеристик.
Динамические характеристики при пуске и торможении в приводах с нерегулируемым асинхронным электродвигателем
зависят от γ0, коэффициента Кλmax = Мдв.max / Мдв.н (из каталога электродвигателей), отношения низшей собственной частоты
f1 привода к частоте электросети f0. При наличии в приводе автоматизированной коробки скоростей (передач) АКС с электромагнитными муфтами динамический момент в механизме определяется импульсом электромагнитной муфты на входном
80