
2733
.pdfструкторскому оформлению станки компонуются из общего набора узлов (модулей), дает возможность формализовать весь процесс проектирования и в значительной мере его автоматизировать.
1.4. Проектные критерии
При проектировании любого комплекта станочного оборудования основной целью является обработка заданного множества деталей с минимальными затратами на основе принятой технологии. Множество деталей, подлежащих обработке, характеризуется общим годовым их выпуском, номенклатурой, ритмичностью выпуска, т. е. числом переналадок в течение года.
Обеспечение годового выпуска известного множества деталей при минимальных затратах следует рассматривать как целевую функцию при проектировании комплекта станочного оборудования:
А = N / Σc → max,
где N — годовой выпуск деталей, шт.; Σс — сумма приведенных затрат, руб.
Эта целевая функция характеризует эффективность оборудования.
При конструировании новых станков, которые будут входить в состав различных комплектов станочного оборудования, следует стремиться к повышению их производительности, так как при этом можно сократить число станков в наборе и, соответственно, уменьшить стоимость комплекта оборудования. С уменьшением числа станков повышается и надежность всей системы.
С повышением степени автоматизации станочного оборудования сокращаются текущие затраты на обслуживание, и в сумме приведенных затрат наибольшая доля приходится на стоимость самих станков. В современных автоматических ли-
11
ниях и гибких производственных системах стоимость оборудования, отнесенная к одному году эксплуатации, составляет 60...80 % всех приведенных затрат, а иногда и более. Поэтому при сопоставлении проектных вариантов станочного оборудования следует, прежде всего, обращать внимание на их сравнительную стоимость. Например, при выборе целесообразного набора оборудования для гибкой производственной системы следует иметь в виду зависимость суммы приведенных затрат от вида станочного оборудования и номенклатуры деталей.
Помимо целевой функции, при проектировании комплекта станочного оборудования или при конструировании новых станков необходимо выполнять проектные ограничения.
Проектные ограничения могут быть связаны с функциональными требованиями, с характером производства, на котором будут изготовлять станки, и с условиями эксплуатации на том производстве, где станки будут работать.
К важнейшим функциональным проектным ограничениям относят требования к точности обработанных на станке готовых изделий. Имеются в виду требования к точности размеров, правильности формы отдельных поверхностей и их шероховатости, к точности взаимного расположения обработанных поверхностей. Требования к точности обработки обусловливают соответствующие проектные ограничения на допустимые геометрические, кинематические, упругие, динамические, температурные погрешности всей системы станка и его отдельных частей.
Особенности того станкостроительного производства, на котором будут изготовлять станочное оборудование, накладывают проектные ограничения на технологичность изготовления и сборки. Возможности производства ограничивают допустимый и целесообразный набор технологических операций, обработки, режущего и измерительного инструмента, оснастки, технологии сборки.
На технологичность изготовления станка большое влияние оказывает унификация, которая связана с насыщением конструкции стандартными и унифицированными деталями и
12
сборочными единицами. Стандартные детали или узлы станка должны соответствовать государственным, республиканским или отраслевым стандартам. К унифицированным частям станка относят изготавливаемые по стандартам данного предприятия и используемые в нескольких разных моделях, а также различные комплектующие изделия (за исключением крепежных и арматуры). Важные проектные ограничения могут быть связаны с условиями эксплуатации станочного оборудования. Проектные ограничения на гарантированный срок сохранения точности и на требуемую долговечность учитывают при конструировании станка и отдельных его узлов. К условиям эксплуатации относят требование учета взаимодействия станка с транспортом, манипуляторами и некоторыми другими вспомогательными устройствами. Ограничения накладывают иногда требования транспортирования, характер производственной площади.
Важными являются ограничения, связанные с эргономикой. Например, со всей, тщательностью должны быть решены вопросы удаления абразивной пыли, мелкой стружки, смазоч- но-охлаждающей жидкости и ее регенерации. Для станков с ручным управлением и обслуживанием особого внимания заслуживает внешнее оформление станка, удобство и безопасность его обслуживания. К проектным ограничениям относят патентно-правовые вопросы, которые требуют подробного обзора на начальных этапах проектирования и полной патентной чистоты вновь создаваемой конструкции.
1.5. Автоматизации проектирования
Автоматизация проектирования является одной из определяющих тенденций технического прогресса в станкостроении. Применение методов и средств автоматизированного проектирования (САПР) обеспечивает повышение качественного уровня проектов, производительности труда конструкторов и технологов и, что самое важное с экономической точки зрения,
13
резко (иногда в несколько раз) сокращает сроки технической подготовки и освоения производства новых изделий.
Методическую основу САПР составляют математические модели объектов, относящихся к конкретной предметной области. Математическая модель (ММ) отображает объект реального мира (РО) в мир информации.
Критериальные ММ (КММ) содержат информацию о связи технических характеристик РО с его конструктивными параметрами. Их обычная математическая форма - конечные (алгебраические или трансцендентные) зависимости. Морфологические ММ (МММ) описывают структуру, форму и размеры РО и являются обобщением известного понятия геометрической ММ. Их математическая форма - системы алгебраических и тригонометрических уравнений, уравнений дифференциальной геометрии, отношения дискретной математики.
ММ поведения (ММП) применительно к металлорежущим станкам, узлам и механизмам описывают кинематику и динамику движений. Их адекватная математическая форма - системы дифференциальных уравнений в обыкновенных и частных производных, которые подвергают различным преобразованиям, например отображению в комплексное пространство для получения решений в частотной области, или численно интегрируют, воспроизводя в выбранном масштабе движения реального объекта.
Между тремя типами ММ существует тесная взаимосвязь. Так, КММ часто получают как результат исследования ММП. При этом параметрами КММ могут быть геометрические размеры, определяющие вид МММ. Последняя, в свою очередь, содержит данные, являющиеся исходными для определения параметров ММП.
Все три вида моделей, будучи формами отображения одной и той же реальности, воспроизводят разные ее стороны. Для различных типов ММ, несмотря на различия их математических конструкций, может быть принята единая форма представления, используемая в технической кибернетике. Эта форма имеет вид
14

y = Wz,
где z - вектор входных величин, принадлежащий некоторому, пространству Z; у - вектор выходных величин, принадлежащий пространству Y; W - оператор, преобразующий вход z в выход у. Данную универсальную форму ММ можно интерпретировать как некий многополюсник, имеющий n входов и m выходов (рис. 1). Физический смысл входов и выходов зависит от предметной области, типа модели, физической сущности оператора W.
Рис. 1. Универсальная форма представления математической модели
1.6. Основные методические принципы автоматизированного проектирования
1. Принцип композиции. Новые технические объекты создаются посредством объединений (композиции) стандартизованных (нормализованных, унифицированных) элементов в единое целое по определенным физическим, логическим и семантическим правилам. При автоматизированном проектировании каждый элемент отображается в информационный мир соответствующей ММ.
Совокупность элементов образует элементную базу, используемую для проектирования. В САПР элементная база интерпретируется как база данных (БД), содержащая соответствующие ММ. Каждый элемент, входящий в элементную базу данной предметной области, характеризуется определенным физическим качеством и вектором параметров. Физическое
15
качество определяет функциональное назначение элемента и зависит от его внутренней структуры. Качество отображается содержательным наименованием (именем) элемента, а также названиями (именами) тех входов и выходов, с помощью которых данный элемент может связываться с другими. Вектор параметров описывает количественные характеристики элемента.
Понятие элемента является иерархическим, поскольку любое целое, составленное из элементов (i - 1)-го уровня, может быть объявлено элементом i-го уровня и использоваться для композиции на (i + 1)-м уровне. В зависимости от того, к какому иерархическому уровню относится элемент, и степени детализации структурных свойств, его имя может быть простым или сложным, т.е. состоять из одного или нескольких слов. Например, имя "подшипник" характеризует класс объектов, обеспечивающих требуемое положение оси вращающегося вала в пространстве, однако оно не раскрывает внутренней структуры элемента. На следующем уровне имеются два имени: "подшипник качения" и "подшипник скольжения", которые указывают тип трения, возникающий при вращении вала, и содержат указания, позволяющие судить о внутренней структуре элемента. Еще больше информации об этой структуре содержат имена следующею уровня, например, "подшипник качения шариковый" и т.д. При таком подходе к образованию имен элементов всю элементную базу можно описать в виде множества древовидных графов понятий, с помощью которых можно затем отыскивать нужные элементы. В некоторых случаях графы могут иметь и сетевую структуру (семантическая сеть).
Необходимые для композиционного проектирования правила совместимости, устанавливающие соответствие входов и выходов элементов, а также количественные отношения между компонентами векторов их параметров, содержатся в базе знаний, относящейся к конкретной предметной области. Располагая элементной базой и базой знаний, можно решать задачи проектирования на основе принципа композиции.
16
2. Принцип подобия. Новые технические объекты создаются посредством обобщенного преобразования подобия некоторой, заранее сформированной структуры.
Обобщенное преобразование подобия выполняется в n- мерном координатном пространстве, причем в качестве координат могут выступать физические величины любой природы: геометрические, механические, электрические и т.д. Параметры нового объекта определяются расчетным путем в зависимости от его конкретного назначения и технических требований.
Структура объекта проектирования предполагается неизменной, а в составе вектора количественных характеристик выделяют одну или несколько фундаментальных компонент, значения которых определяют проектировочным расчетом исходя из технических требований к объекту. Остальные компоненты определяются по формулам, часто эмпирическим, связывающим их с фундаментальными компонентами. Несмотря на известный "консерватизм" принципа подобия (имеется в виду неизменность структуры), он позволяет решить задачу автоматизации проектирования до конца, т.е. до выдачи полного комплекта конструкторской и технологической документации, включая управляющие программы для обработки деталей на станках с ЧПУ. В истекшем десятилетии на вычислительных средствах третьего поколения были созданы высокоавтоматизированные САПР, ориентированные на проектирование таких изделий, как подшипники качения, асинхронные электродвигатели, силовые трансформаторы, и др.
На основе принципа подобия наиболее просто удается создать интегрированные системы конструкторскотехнологического назначения.
Принципы композиции и подобия существуют и применяются во взаимосвязи друг с другом. Так, например, с помощью принципа композиции из элементов (i - 1)-го иерархического уровня можно сформировать объект, который, в свою очередь, станет элементом i-го уровня. Если для этого элемента с помощью принципа подобия построить размерный ряд, то
17
в дальнейшем его можно использовать для композиции на (i + 1)-м уровне.
1.7. Структура САПР МРС
Эффективность САПР в значительной мере зависит от степени интеграции всех стадий конструкторской и технологической подготовки производства в единый информационный процесс. Такая интеграция обеспечивает согласованность конструкторских и технологических решений, сокращает количество ошибок как принципиального характера, т.е. связанных с принятием ошибочных решений, так и тех, которые возникают в связи с оформлением конструкторской и технологической документации. При использовании отдельных, автономных средств автоматизации инженерного труда общее количество ошибок может возрастать за счет операций перекодировки информации при переходе от одной стадии проектирования к другой.
Поэтому в современных САПР организуются информационные связи, в первую очередь, между блоками проектирования деталей и технологии их изготовления (включая подготовку управляющих программ для станков с ЧПУ). Такие системы получили в зарубежной научно-технической литературе название CAD/CAM (Computer Aided Design и Computer Aided Manufacturing).
Одной из важнейших компонент САПР является блок, связанный с принятием принципиальных технических решений на основе проведения достаточно сложного комплекса инженерных расчетов и математического моделирования. Подобные средства получили название САЕ (Computer Aided Engineering). Их интеграция с предыдущими компонентами приводит к появлению CAE/CAD/CAM-систем. Общую структуру конструкторско-технологической САПР металлорежущих станков можно представить в виде схемы, приведенной на рис. 2, согласно которой ход всех проектных работ определяется
18
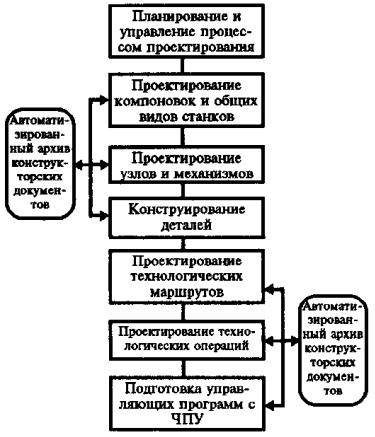
блоком планирования и управления процессом проектирования.
Рис. 2. Общая структура САПР металлорежущих станков
В соответствии с принципом композиции новые станки создаются в основном на базе унифицированных узлов либо, в соответствии с принципом подобия, посредством модификации ранее выполненных проектов.
19
Процесс автоматизированного проектирования станка состоит из следующих основных этапов:
1.анализ технических требований к проектируемому станку (по данным заказа);
2.технологическое обоснование основных технических характеристик станка и требований к его узлам (агрегатам);
3.поиск в автоматизированном архиве (АА) подходящего проекта из числа ранее выполненных;
4.проектирование (доработка) компоновочной схемы
станка;
5.проектный расчет компоновочной схемы (оценка точности, жесткости, динамических свойств, предварительное моделирование и оптимизация);
6.подбор унифицированных узлов из базы данных (ар-
хива);
7.проектирование компоновочного чертежа (общего вида) станка;
8.проверочные расчеты и уточненное моделирование;
9.проектирование (доработка) электрооборудования;
10.проектирование (доработка) гидрооборудования, системы смазки и охлаждения;
11.проектирование (доработка) пневмооборудования;
12.проектирование спецоснастки (наладки);
13.проектирование (доработка) схемы окраски;
14.проектирование упаковки;
15.оформление полного комплекта технической документации (на машинных носителях) и, при необходимости, на бумаге;
16.помещение готового проекта в АА.
Процесс автоматизированного проектирования узлов состоит из следующих основных этапов:
1. анализ технических требований к проектируемому уз-
лу;
2.поиск в АА близкого аналога (прототипа);
3.формирование структуры (принципиального решения) проектируемого узла;
20