
2733
.pdf
быстроходных станков. Основными средствами такого рода являются сокращение кинематической цепи и уменьшение числа валов, передающих вращение на шпиндель; применение сложенных структур привода; ограничение величины предварительного натяга в опорах; использование подшипников с малым трением; применение циркуляционной смазки с нормированной подачей смазочной жидкости или масляного тумана.
Рис. 17. Мощность холостого хода главного привода станков: 1 — токарно-револьверного; 2 - вертикально-
фрезерного; 3 — токарного
Мощность на дополнительные потери появляется при передаче полезной мощности за счет соответствующего увеличения нагрузок на передачи и опоры. Эта дополнительная потеря возрастает с увеличением полной передаваемой мощности и может быть выражена уравнением
61

Nэ Nп N х ,
где η — общий КПД привода, подсчитываемый по формуле
i i ,
где ηi — КПД конкретной передачи или опоры; αi — число однотипных передач с одинаковым КПД.
Дополнительные потери составляют обычно не более 10...15% всей потребляемой мощности, что позволяет ими пренебречь при приближенных расчетах. Выбор мощности двигателя относится к задачам на определение оптимального значения, если их рассматривать как задачи техникоэкономические.
Оптимальную мощность привода определяют по критерию экономической эффективности на основе минимума тех приведенных затрат, которые зависят от выбора этой мощности. В общем случае все виды затрат, связанные с мощностью привода, можно условно представить в виде
С = С1 + С2 + С3,
где C1 — затраты во время вспомогательных перемещений, когда потребляется мощность холостого хода Nx; C2 — затраты во время резания с неполным использованием номинальной мощности электродвигателя; С3 — затраты во время резания с неполным использованием режимов резания из-за ограниченной мощности двигателя.
Существенно, что с увеличением мощности некоторые виды затрат (стоимость станка, затраты на электроэнергию) возрастают, при этом уменьшаются и потери производительности (составляющая С3) от недоиспользования режимов резания. Эти противоположные тенденции приводят всегда к неко-
62
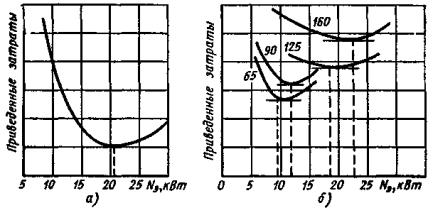
торому значению номинальной мощности двигателя, обеспечивающей минимум приведенных затрат.
Рис. 18. Оптимизация мощности двигателя главного привода по минимуму приведенных затрат для станков:
а — токарного с ЧПУ, б — для гаммы горизонтальнорасточных (цифры обозначают диаметр шпинделя)
В качестве примера на рис. 18, а приведен график С = f (Nэ), определяющий оптимальное значение мощности главного привода токарного станка с высотой центров 200 мм оснащенного системой ЧПУ. В качестве исходной кривой распределения мощности принята зависимость, полученная на основе анализа множества деталей, обрабатываемых на станке подобного назначения. При расчете проанализирована возможность изменения исходных данных в тех реальных пределах, которые могут иметь место при эксплуатации станка. Оказалось, что при изменении исходных данных в широких пределах оптимальное значение мощности двигателя колеблется в пределах ±3,5 кВт; это соответствует всего лишь половине интервала ряда мощностей стандартных асинхронных электродвигателей, На рис. 18, б приведены кривые выбора оптимальной мощности двигателя привода главного движения гаммы гори-
63
зонтально-расточных станков (на кривых указан диаметр шпинделя станка в мм).
3.6. Выбор расчетных нагрузок
Нагрузки в станках возникают под действием сил резания, сил сопротивления и сил, создаваемых массами.
Силы резания зависят преимущественно от свойств обрабатываемого материала и параметров процесса резания: ширины и глубины срезаемого слоя, площади износа по задней поверхности резца, а также от многих других факторов, учет которых при конструировании станков либо затруднен, либо невозможен.
При проектировании станков режимы резания, а соответственно силы резания и мощности резания обычно заранее известны. Для станков целевого назначения (специализированных и специальных) их выясняют и уточняют в ходе предварительных лабораторных исследований, а для станков общего назначения и станков с высокой степенью универсальности собраны обширные статистические данные о фактических силах резания и вероятности их использования в станках.
Силы сопротивления связаны с трением в подвижных соединениях станка (направляющих, опорах, передачах). При смешанном трении силы трения зависят преимущественно от нормальной нагрузки и от скорости относительного перемещения. Кроме того, при покое эта сила (ее рубежное значение) увеличивается со временем неподвижного контакта. Важным для точностных расчетов является разброс значений силы смешанного трения от влияния случайных факторов. По данным ряда исследований, дисперсия сил трения в опорах и направляющих станков нередко того же порядка, что и среднее ее значение.
Силы, проявляющиеся в виде нагрузки от массы узлов станка, сил и моментов инерции при переходных режимах и колебаниях, центробежной нагрузки при высоких скоростях вращения, в отдельных случаях должны быть учтены. Если
64
определение массы и центра тяжести основных узлов станка обычно не вызывает трудностей, то расчет динамических нагрузок, возникающих в сложных нелинейных многомассовых системах, какими является большинство станков, требует использования специальных методов. Общую оценку динамического характера проявления нагрузки можно получить на основе введения коэффициента динамичности как отношения величин деформаций упругой системы при динамическом и соответственно статическом воздействии
kдин = δдин / δст.
Динамические перегрузки в приводе станков, связанные с пуском двигателя, зависят от характеристики самого двигателя и свойств упругой системы привода.
4. ПРОЕКТИРОВАНИЕ И РАСЧЕТ ПРИВОДОВ СТАНКОВ
4.1.Приводы главного движения
4.1.1.Назначение приводов главного движения
Приводы главного движения металлорежущих станков служат для обеспечения относительного перемещения заготовки и режущего инструмента, при котором инструмент производит резание металла. Главные движения могут быть как вращательными (вращение заготовки в станках токарной группы или инструмента во фрезерных, многоцелевых, шлифовальных станках), так и возвратно-поступательными (перемещение заготовки в строгальных, долбежных, протяжных станках).
В общем случае приводы главного движения выполняют следующие основные функции: передача мощности (крутящего момента); регулирование скорости; понижение или повы-
65
шение скорости (от двигателя к рабочему органу); включение, выключение, торможение, реверсирование.
4.1.2.Виды приводов
Вметаллорежущих станках преимущественно применяют электромеханические приводы главного движения, у которых электрическая часть (электропривод) состоит из электродвигателя переменного или постоянного тока и преобразующих и управляющих устройств, а механическая - из отдельных передач (зубчатых, червячных, ременных, фрикционных и др.), передаточных механизмов (зубчатых редукторов, коробок скоростей, кулисных и кулачковых механизмов) и их комбинаций.
Встанках с прямолинейным (возвратно-поступательным) главным движением - строгальных, долбежных, протяжных - наряду с электромеханическими приводами используют гидравлические приводы. Гидропривод главного движения включает гидродвигатель (силовой гидроцилиндр или гидромотор)
систочником энергии - насосом и управляющими устройствами и передачу (устройство, механизм) от гидродвигателя к рабочему органу.
4.1.3.Требования к приводам
К приводам главного движения станков предъявляется ряд требований - общих и специфических, связанных с назначением станка конкретного типа:
•соответствие основных характеристик привода (максимальных скоростей перемещения, мощности, крутящего момента, характера и диапазона регулирования скорости и т.д.) технологическим требованиям, обеспечивающее обработку деталей заданной номенклатуры с заданными производительностью, точностью и параметрами шероховатости поверхности;
•обеспечение заданных конструктивно-технических требований по характеристикам точности перемещений рабочего
66
органа, уровню автоматизации управления приводом, удобству компоновки;
•достаточная надежность привода в эксплуатации (в том числе ограничение перегрузок при переходных процессах);
•минимальные энергетические потери (высокий кпд привода);
•ограничение уровня шума допустимым пределом;
•широкое применение унифицированных, типовых, стандартизованных, покупных узлов, агрегатов и элементов главного привода;
•рациональные габариты, материалоемкость, стоимость привода.
4.1.4. Виды и способы регулирования
Регулирование скорости в приводах осуществляется:
-изменением частоты вращения (скорости перемещения) двигателя;
-изменением передаточного отношения между двигателем и рабочим органом в приводном механизме.
Регулирование может осуществляться:
1) при постоянной предельной мощности во всем диапазоне скоростей;
2) при постоянном предельном моменте;
3) при комбинировании того и другого вида регулирова-
ния.
По условиям оптимального процесса обработки деталей для подавляющего большинства станков требуется регулирование скорости главного движения при приблизительно постоянной мощности в диапазоне, определяемом диапазонами изменения скоростей резания и размеров детали (станки токарной группы) или инструмента (фрезерные, сверлильные и т.п.). В станках с универсальным характером работ постоянная мощность требуется в средней части диапазона скоростей шпинделя (наибольшая мощность резания) и в верхней части диапазона (скоростные режимы с наибольшими потерями
67
мощности в механизме), а в нижней части диапазона (вспомогательные операции) уровень используемой мощности невысокий. Поэтому для таких станков применяют приводы с комбинированным регулированием: в нижней части диапазона - с постоянным предельным моментом, а в остальной части - с постоянной предельной мощностью.
Требуемые диапазоны регулирования на шпинделе:
RШП.Р до 250 - для станков универсальных с широкой номенклатурой деталей, обрабатываемых в единичном и мелкосерийном производстве (токарных, карусельных, расточных, фрезерных и других) общий диапазон регулирования RШП.Р до 25...40 для станков с постоянной мощностью;
RШП.Р до 15...20 - для станков универсальных - легких (до 1 т ) и средних (до 10 т), предназначенных для мелко- и среднесерийного производства;
RШП.Р до 8...12 - для станков специализированных, предназначенных для крупносерийного производства;
RШП.Р = 2...6 - для быстроходных станков, оснащенных инструментом для скоростного резания (минералокерамика,
композит и т.п.) с Vрез > 400 м/мин (токарные, револьверные, фрезерные), с Vрез, > 60 м/с (шлифовальные), выпускаемых для
эксплуатации в крупносерийном и массовом производстве (полуавтоматы и автоматы разных групп).
Для большинства станков при работе в нижней и средней части диапазона скоростей шпинделя требуется снижение частоты вращения и увеличение крутящих моментов (сравнительно о значениями полученными на валу электродвигателя) до 3...10 раз в станках небольшого и среднего размера и до 80...100 раз в тяжелых станках.
Нужные значения диапазона RШП.Р и редукции скорости получают:
1) сочетанием односкоростного нерегулируемого (или многоскоростного) асинхронного электродвигателя переменного тока со ступенчато регулируемым механизмом (коробкой скоростей, редуктором, набором сменных зубчатых колес или шкивов и т.п.);
68
2) соединением бесступенчато регулируемого электродвигателя с упрощенным ступенчато регулируемым механизмом (переключаемыми передачами, редуктором и т.п.).
Типовые схемы построения привода главного вращательного движения металлорежущих станков представлены в табл. 1.
Вбольшинстве станков без числового управления, за исключением тяжелых, широко применяют приводы с асинхронными нерегулируемыми электродвигателями и ступенчато регулируемыми передаточными механизмами - зубчатыми многоскоростными коробками скоростей (табл. 1, схемы 1...5).
Встанках с ЧПУ, большинстве тяжелых и быстроходных станков, станках с коротким циклом обработки при больших моментах инерции и станках, предназначенных для торцового точения, применяют приводы главного движения с регулируемыми электроприводами постоянного и переменного тока.
Наибольшее распространение получили приводы с двухзонным регулированием скорости двигателя в сочетании с двухчетырехступенчатой коробкой скоростей (схемы 6...9). Перспективным для легких и средних станков можно считать построение главного привода по схемам 8...10 с использованием частотно-регулируемых асинхронных электродвигателей, обладающих высокой надежностью, малыми потерями, простотой обслуживания.
Одной из тенденций развития приводов станков является создание интегрированных электромеханических узлов, объединяющих в едином конструктиве элементы регулируемого электродвигателя и приводного механизма.
Вэлектромеханическом узле "мотор-редуктор" в качестве мотора применяют регулируемый электродвигатель переменного или постоянного тока, а пристроенный к нему механизм выполняют в виде двухступенчатого зубчатого или планетарного редуктора с двумя передаточными отношениями (1 : 1 и 1 : 4 или 1 : 3,17) и автоматическим переключением ступеней. Такой привод позволяет обеспечить диапазон регулирования с постоянной мощностью на шпинделе до 16...20.
69
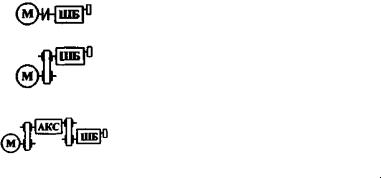
В станках быстроходных с небольшими крутящими моментами на шпинделе (токарных, консольно-фрезерных и др.) получают развитие безредукторные приводы с электромеханизмами типа "мотор-шпиндель", в которых на шпиндель насажен ротор регулируемого электродвигателя переменного тока (схема 12). По такой же схеме выполняют привод с высокоскоростным частотно-регулируемым асинхронным двигателем - электрошпиндель, применяемый для обработки легких сплавов, сотовых конструкций, печатных плат в фрезерных и сверлильных быстроходных станках с nшп. max ≤ (9000...10 000)
мин -1, а также для некоторых типов шлифовальных станков.
Таблица 1 Типовые схемы построения привода главного
вращательного движения
|
|
|
Узлы регули- |
|
||
|
|
рования скоро- |
|
|||
схемы |
|
|
сти |
|
||
Схема |
Электропривод |
Область применения |
||||
|
||||||
|
|
|
||||
№ |
|
|
|
|||
|
|
передаточный |
|
|
||
|
|
|
|
|
||
|
|
|
механизм |
|
||
|
|
|
|
|
|
|
1 |
2 |
3 |
|
4 |
||
|
|
|
|
|
|
|
1 |
|
|
|
|
В станках токарных, |
|
|
|
|
|
фрезерных, сверлиль- |
||
|
|
|
М |
|||
|
|
|
ных, зуборезных |
|||
|
|
|
ШБ |
|||
|
|
|
и других |
|||
2 |
|
|
|
|
||
|
|
|
|
|
||
|
|
|
|
|
|
|
|
|
|
|
|
В станках токарных, |
|
|
|
|
М |
фрезерных, свер- |
||
3 |
|
|
АКС, ШБ |
лильных (в том числе |
||
|
|
|
|
|
в станках с ЧПУ) |
|
|
|
|
|
|
|
70