
2733
.pdf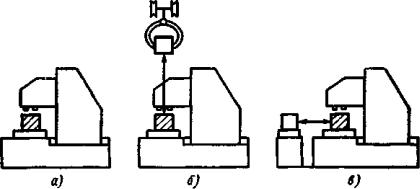
2.4. Компоновка станочных систем
При компоновке станков в станочные системы: автоматические линии, автоматические участки и производства, возможно множество вариантов. Наиболее целесообразную структуру размещения станков выбирают, исходя из минимума приведенных затрат, обеспечения требуемой производительности, минимума занимаемой площади, удобства обслуживания, простоты и надежности транспорта и манипулирующих устройств.
Автоматические линии целевого назначения для крупносерийного и массового производства состоят обычно из станков, выполняющих в заданной последовательности отдельные технологические операции. В зависимости от расположения потока обрабатываемых деталей автоматические линии предусматривают сквозной транспорт деталей через рабочую зону (рис. 11, а) или при верхнем и боковом расположении потока детали вводятся в рабочую зону дополнительным поперечным перемещением (рис. 11, б, в).
Рис. 11. Основные способы ввода потока обрабатываемых деталей в рабочую зону станка: а - сквозным транспортированием; б - вертикальным перемещением;
в - горизонтальным перемещением
41
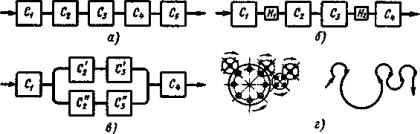
Структура автоматических линий в значительной мере зависит от характера связи станков потоком обрабатываемых деталей.
В том случае, когда деталь, обработанная на одном из станков, сразу попадает на следующий, станки оказываются технологически жестко связанными. Вынужденная остановка одного из станков (рис. 12, а) неизбежно вызывает остановку всей автоматической линии. Введение так называемых гибких связей в виде бункеров-накопителей между последовательно расположенными станками (рис. 12, б) дает возможность в ряде случаев повысить коэффициент технического использования и тем самым фактическую производительность автоматической линии.
Рис. 12. Принципиальные схемы компоновок автоматических линий: а — с жесткой технологической связью;
б — с накопителями; в — с разветвлением потока деталей; г — роторного типа; С1,...С5 — станки; Н1, Н2 — накопители
Решение вопроса о разделении всех станков автоматической линии на отдельные участки, связанные накопителями, и определяет оптимальную компоновку однопоточной автоматической станочной линии.
Выбор оптимальной компоновки автоматической линии целесообразно осуществлять на основе моделирования и использования средств вычислительной техники. Основным критерием выбора является минимум приведенных затрат. При
42
этом анализируют варианты компоновки постоянного набора станков. Незначительные различия в транспортных устройствах не влияют существенно на капитальные и текущие затраты. Оптимальный вариант можно определить по критерию наибольшей производительности.
При работе автоматической линии каждый ее участок может либо работать, либо простаивать из-за собственных отказов или отказов смежных участков. Принимая некоторое начальное состояние работы автоматической линии (например, все участки работают, а накопители пусты) и задаваясь законом распределения отказов на каждом из участков линии и в каждом накопителе, можно шаг за шагом проследить работу всей автоматической линии и определить ее фактическую производительность. Кроме того, можно проследить за изменением числа деталей в каждом накопителе.
По результатам моделирования определяются фактическая производительность и коэффициент технического использования для всех вариантов структуры и исследуется изменение запаса деталей в накопителях.
Оптимизация структуры и компоновки средствами вычислительной техники особо целесообразна при анализе сложных обрабатывающих комплексов из ряда разнородных автоматических линий. Особым видом компоновки являются роторные автоматические линии при совмещении транспортных движений с основными технологическими операциями. Детали на роторной автоматической линии перемещаются по непрерывной траектории, на отдельных участках которой они обрабатываются рабочими органами станков, которые синхронно перемещаются с обрабатываемыми деталями. Компоновка роторных автоматических линий отличается большой компактностью, а принцип их действия обеспечивает исключительно высокую производительность. Вместе с тем возможности их использования ограничиваются малым машинным временем обработки и условиями массового однотипного производства.
Автоматические производства высокой степени универсальности компонуют из многооперационных станков
43
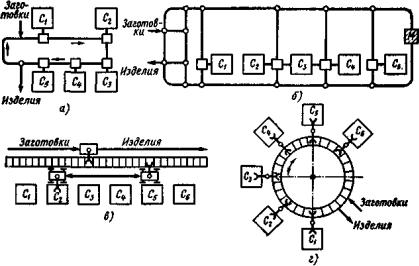
по схемам, представленным на рис. 13. Компоновка с фиксированным потоком деталей (рис. 13, а), как это выполнено в обрабатывающей системе фирмы Буркхардт и Вебер для корпусных деталей, позволяет использовать простейшие транспортные устройства, но лишена возможности оптимизировать загрузку станков и использование всей системы. Такого типа компоновки целесообразны для систем сравнительно узкого целевого назначения с небольшим набором обрабатываемых деталей.
Рис. 13. Компоновки обрабатывающих систем: а — с фиксированным потоком деталей; б — с разветвлением потока деталей;
в— с промышленными роботами;
г— кругового типа
Компоновка с разветвленной транспортной системой (рис. 13, б) дает возможность управлять потоком деталей и оптимизировать загрузку станков и технологический процесс обработки совокупности деталей по многим параметрам. Заго-
44

товки с приспособлениями-спутниками попадают в транспортную систему, и их путь от станка к станку определяется в ЭВМ оптимальным образом в зависимости от конкретной обстановки. Главным недостатком указанной компоновки с разветвленным транспортом является относительно высокая стоимость транспортных устройств и недостаточная мобильность производства.
Компоновка с адресным складированием заготовок и универсальными транспортно-загрузочными устройствами типа промышленных роботов показана на рис. 13, в. Такая компоновка является наиболее универсальной и мобильной; ее можно осуществлять на принципах агрегатирования и с различной степенью автоматизации транспортно-загрузочных устройств и всей обрабатывающей системы.
Прямолинейная компоновка по сравнению с круговой компоновкой (рис. 13, г) имеет то преимущество, что дает большие возможности для последующего изменения и модернизации обрабатывающей системы, для дополнительного включения основного и вспомогательного оборудования, а в случае необходимости и его замены.
2.5. Унификация и агрегатирование
Унификация — использование в разных станках одинаковых деталей и узлов. Степень унификации можно оценить коэффициентом унификации
k y |
ny |
, |
|
n |
|||
|
|
||
где ny — число унифицированных |
деталей (узлов) из |
||
общего количества n деталей (узлов) |
станка. |
Иногда коэффициент унификации подсчитывают по отношению массы или трудоемкости унифицированных деталей к общей массе или общей трудоемкости деталей станка. Уни-
45
фикация существенно снижает затраты на изготовление станков и повышает их надежность, однако при излишне большой унификации ухудшаются технологические характеристики станков. Таким образом, в каждых конкретных условиях существует оптимальное значение коэффициента унификации по критерию минимума приведенных затрат.
Особые преимущества дает унификация однотипных станков, выпускаемых одним производством. За счет снижения трудоемкости изготовления при этом снижаются общие затраты на производство всего размерного ряда. Снижение трудоемкости изготовления базовых деталей и узлов привода тяжелых станков намного перекрывают некоторые дополнительные затраты металла при унификации.
Унификацию станков размерного ряда широко используют как в тяжелых, так и в средних станках.
Вболее ограниченных масштабах возможна унификация
ив станках различных типов. Некоторые базовые детали и узлы привода целесообразно использовать для станков самого различного назначения. При широкой унификации возможно централизованное изготовление отдельных узлов и деталей станков со значительным увеличением серийности производства.
Агрегатирование является дальнейшим развитием унификации и сводится к тому, что станки собирают в основном из стандартных узлов — агрегатов. Наиболее успешно принцип агрегатирования используют в станках и автоматических линиях для крупносерийного и массового производства. Использование принципов агрегатирования не только удешевляет изготовление станков, но и способствует сокращению сроков освоения и выпуска, так как производство заранее ориентируется на выпуск стандартных узлов-агрегатов.
Принцип агрегатирования является весьма перспективным и при конструировании многооперационных станков, а также автоматических участков и автоматических производств с ЧПУ.
46
Агрегатирование целесообразно для различных вспомогательных устройств в автоматических станочных системах: транспортно-загрузочных и других манипулирующих устройств, средств контроля и измерения, устройств для автоматической смены инструмента, систем охлаждения и смазки и т. п.
Основы агрегатирования могут быть заложены и при компоновке обрабатывающих станочных систем из однотипных исходных элементов — так называемых технологических ячеек, которые включают станок и загрузочно-транспортные устройства. Набор технологических узлов снабжают транспортным устройством или роботом для передачи деталей от одного технологического узла к другому. Из набора технологических узлов компонуют обрабатывающие системы различного технологического назначения и разной степени автоматизации. По такому агрегатному принципу осуществляют проектирование автоматических участков для обработки зубчатых колес и некоторых других видов деталей машиностроительного производства.
3. ВЫБОР ТЕХНИЧЕСКИХ ХАРАКТЕРИСТИК СТАНКОВ
3.1. Уточнение служебного назначения станков
Любой станок или станочная система предназначены для обработки определенного множества деталей. Уточнение понятия множества деталей, для которых обработка экономически целесообразна именно на данном станке, достаточно сложная задача и решается средствами вычислительной техники на основе методов исследования операций.
Обрабатываемые на станках детали характеризуются совокупностью параметров, основными из которых являются форма, размеры, материал и точность обработки. Форму деталей можно определить совокупностью поверхностей, ее ограничивающих, причем отдельные обрабатываемые поверхности
47

принято называть операционными элементарными поверхностями (ОЭП) или элементарными технологическими поверхностями (ЭТП). Разработана классификация элементарных поверхностей на основе схемы, условно изображенной на рис. 14. При этом выделяется определенное число групп элементарных поверхностей, из которых образуется подавляющее большинство машиностроительных деталей, обрабатываемых на станках и станочных системах.
Рис. 14. Схема классификации обрабатываемых деталей
Статистический анализ множества деталей, обрабатываемых в машиностроении, свидетельствует о том, что почти половина наименований всех деталей — тела вращения (рис. 15), на трудоемкость изготовления которых приходится до 25...30%. Другую большую группу деталей машиностроения образуют базовые детали; на их долю приходится примерно 15% наименований и до 50% трудоемкости изготовления. Прочие детали, главным образом небольшие по габаритам, при
48

значительном числе наименований составляют небольшую долю всей стоимости изготовления деталей машиностроения.
Рис. 15. Типичные детали машиностроения
Исходные данные о совокупности деталей и совокупности операционных элементарных поверхностей используют для последующего уточнения различных технологических операций, необходимых для изготовления всего рассматриваемого множества деталей. При уточнении служебного назначения станков общего назначения можно использовать понятие о представительных деталях. На основе имеющихся статистических данных о распределении всего ассортимента деталей их можно объединить в группы по некоторым общим признакам и каждую группу обрабатываемых деталей условно заменить одной представительной деталью, геометрические и технологические параметры которой являются средневзвешенными для всей группы.
Технологический процесс обработки, который служит основой для выбора технических характеристик станка, анали-
49
зируют для каждой детали как совокупности ОЭП по следующим особенностям:
последовательности обработки и числу переходов, виду и числу режущих инструментов,
режимам резания (скорости рабочих движений, силы и мощности резания).
Построение технологического процесса для обрабатываемой детали является многовариантной задачей, требующей оптимизации. Выбор оптимального технологического процесса осуществляют на основе минимизации приведенных затрат на обработку детали. Приведенные затраты, приходящиеся на одну операцию, рассматривают как целевую функцию, зависящую от многих параметров: набора режущего инструмента, выбора режимов резания и т. д. Целевую функцию и все накладываемые на нее ограничения (например, по предельным режимам обработки) заменяют соответствующей математической моделью — системой уравнений, решение которой и дает возможность минимизировать целевую функцию
С = f (v, s, n1, n2...) → min,
где v, s, nl, n2... — соответственно скорость резания, подача, число переходов, число режущих инструментов и другие параметры.
Оптимизация вариантов технологических процессов возможна также на основе использования методов идентификации. Сопоставление вариантов технологических процессов осуществляют путем перебора различных значений параметров в условиях, характерных для передовых предприятий. Моделирование реального технологического процесса осуществляется на основе представления этого процесса как оператора с преобразованием входных параметров (формы и размеров деталей, условий производства) в выходные параметры (себестоимость обработки, время изготовления детали). Случайные отклонения, характерные для производства, рассматриваются как шумы.
50