
1533
.pdf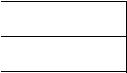
Таблица 3 . 4
Температурная зависимость предела прочности и относительного удлинения АМС на кобальтовой основе
Сплав |
Тдеф, К |
Предел прочности, МПа |
Удлинение, % |
||
Закалка |
Отжиг 723 К, |
Закалка |
Отжиг 723 К, |
||
|
|
|
30 мин |
|
30 мин |
Fe5Co70Si15B10 |
293 |
1480 |
1100 |
0,0 |
1,5 |
|
473 |
1410 |
– |
1,5 |
– |
|
573 |
1040 |
1214 |
1,2 |
2,5 |
|
723 |
710 |
603 |
0,5 |
0,5 |
Co81,5Mo9,5Zr9 |
293 |
2977 |
3119 |
0,0 |
0,5 |
|
573 |
1433 |
3200 |
0,5 |
1,0 |
|
723 |
100 |
800 |
0,0 |
0,0 |
На ленте АМС Fe81Si4B13C2 было прослежено влияние механической обработки (обкатки роликом под разной нагрузкой) на предел прочности этого сплава. Обкатку производили со стороны свободной поверхности ленты АМС вдоль оси ленты. «Дорожки» обкатки располагались на расстоянии 2 мм одна от другой. Обработанные ленты испытывали на растяжение. По результатам испытаний видно (табл. 3.5), что незначительное увеличение предела прочности наблюдается после обкатки ленты при малых нагрузках. Повышение нагрузки на ролик при обкатке ленты понижает ее прочность.
Таблица 3 . 5
Изменение предела прочности АМС Fe81Si4B13C2 после обкатки роликом под разной нагрузкой (МПа)
Нагрузка на ролик |
Предел прочности |
Нагрузка на ролик |
Предел прочности |
0,0 |
2080 |
10,0 |
1700 |
5,0 |
2280 |
15,0 |
1850 |
9,5 |
1870 |
20,0 |
1960 |
Коэрцитивная сила АМС после закалки, деформации и отжи-
га. Зависимость коэрцитивной силы Нс от степени деформации и отжига для всех исследованных сплавов представлена на рис. 3.11 и в табл. 3.6. Следует отметить, что сплавы на железной основе имеют высокое значение магнитострикции (от 30 до 13·10–6), a AMC на кобальтовой основе – низкое значение (0,1·10–6). Коэрцитивная сила ис-
51
elib.pstu.ru
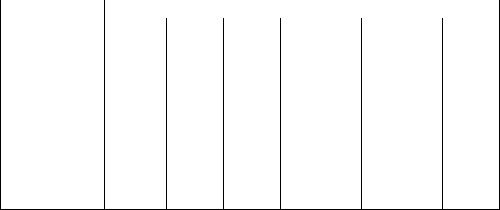
следованных сплавов небольшая по величине, и поэтому все они относятся к магнитно-мягким материалам (см. табл. 3.6). Низкотемпературный отжиг (573 К, 1 ч) не изменяет коэрцитивную силу исходного состояния и, по-видимому, благоприятен для незначительного улучшения пластических свойств АМС. Пластическая деформация (прокаткой) изменяет коэрцитивную силу, увеличивая ее на один (на начальных стадиях деформирования) и даже два порядка (с повышением степени деформации) у всех исследованных АМС (см. рис. 3.11). Причем у сплавов на основе кобальта чем выше содержание бора, тем сильнее возрастает Нс при одной и той же степени деформации, а у сплавов на основе железа эта зависимость от бора не столь существенна. По-видимому, у АМС на основе железа возрастание Нс при деформации определяется соотношением содержания железа к легирующим компонентам: чем больше содержание железа в сплаве, тем сильнее возрастает Нс при одной и той же степени деформации
(см. рис. 3.11).
Таблица 3 . 6
Изменение величины коэрцитивной силы в исследованных АМС после различных видов термо- и механообработки
|
|
ЗначенияНс, А/м, после обработки |
|
|||
Сплав |
Закалка |
Отжиг |
Отжиг |
Деформация Деформация |
Отжиг |
|
|
573 К, |
723 К, |
17 % |
17 % + |
823 К, |
|
|
|
|||||
|
|
1 ч |
1 ч |
|
+ отжиг |
1 ч |
Fe81Si7B12 |
40 |
40 |
1500 |
1800 |
1400*** |
5000 |
Fe81Si4B13C2 |
13 |
13 |
– |
– |
– |
– |
Fe60Cr18Ni7Si3B12 |
5 |
– |
1 |
482 |
1*** |
3600 |
Fe60Cr18Ni7Si5B10 |
9 |
– |
1 |
440 |
– |
3600 |
Fe5Co71,8Si15B8,2 |
0,1 |
0,1 |
– |
30 |
1*; 50** |
– |
Fe5Co70Si15B10 |
0,5 |
1 |
– |
≥30 |
≥8* |
– |
Fe5Co68,2Si15B11,8 |
1 |
1 |
– |
80 |
26*; 26** |
– |
Co81,5Mo9,5Zr9 |
8 |
8 |
12 |
44 |
18 |
– |
Отжиг 573 К, 1 ч в магнитном поле 11000 А/м. ** Отжиг 573 К, 1 ч без магнитного поля.
*** Отжиг 723 К, 30 мин без магнитного поля.
52
elib.pstu.ru
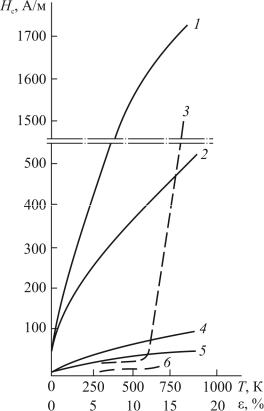
Рис. 3.11. Зависимость коэрцитивной силы АМС от степени деформации прокаткой и температуры отжига Т:
1 – Fe81Si7B12 после деформации; 2 – Fe60Cr18Ni7Si3B12 после деформации; 3 – Fe81Si7B12 после отжига; 4 – Fe5Co70Si15B10 после деформации; 5 – Fe5Co68,2Si15B11,8 после деформации;
6 – АМС на основе Co после отжига
Усиление влияния деформации на Нс для исследованных сплавов в зависимости от их состава можно объяснить следующим образом. По крайней мере две причины определяют влияние деформации на Нс: первая – величина магнитострикционных эффектов, вторая – значение температуры кристаллизации. Так, в АМС с 8,2 ат. % бора сравнительно низкая температура кристаллизации. Поэтому при пластической деформации в зонах скольжения образуются центры кристаллизации. Это приводит к частичной релаксации напряжений. При увеличении содержания бора в АМС на основе кобальта температура кристаллизации растет и поэтому при деформации создается меньше центров кристаллизации, а напряжения релаксируют слабее. Это приводит к появлению
53
elib.pstu.ru
большого количества мест перенапряжения, что вызывает развитие микротрещин. Таким образом, при увеличении содержания бора в образце при одной и той же степени деформации возрастает уровень внутренних напряжений и количество микротрещин, а следовательно, и величина коэрцитивной силы. Но это проявляется, по-видимому, только в АМС с относительно низким значением магнитострикции. В АМС с высоким значением магнитострикции, к которым относят исследованные сплавы на железной основе, этот эффект не столь существен по сравнению с величиной изменения Нс от одного и того же уровня внутренних напряжений при разном содержании железа в АМС.
Последующий отжиг при температурах ниже температуры кристаллизации сплава, как правило, понижает коэрцитивную силу, приближая ее значение к величине коэрцитивной силы исходного свежезакаленного состояния. Неоднозначное изменение коэрцитивной силы в деформированном (прокатка на 17 %) и затем отожженном (при 573 К,
1 ч) АМС Fe5Co71,8Si15B8,2 (Hс = 1 А/м после отжига в магнитном поле и Hс = 50 А/м после отжига без магнитного поля) может быть объяснено
эффектом дестабилизации доменных границ в магнитном поле [16]. Для объяснения этой неоднозначности следует, по-видимому, привлекать данные о возникновении зародышей кристаллизации при пластической деформации. Развитие таких центров кристаллизации при последующем отжиге приведет к росту Hс. В случае падения Hс при отжиге в магнитном поле следует предположить, что магнитное поле задерживает развитие центров кристаллизации.
Температурные условия достаточны для снятия внутренних напряжений, и при деформации не возникли микротрещины, поэтому коэрцитивная сила в результате отжига приняла практически исходное (до деформации) значение.
Как видно из табл. 3.3–3.6, АМС Fe81Si7B12 после отжига при 723 К, 30 мин или после деформации потерял свойства магнитно-мягкого материала, в то время как прочностные свойства его оказались более температурно и механически стабильными. Это указывает на то, что у механических и магнитных свойств АМС разная чувствительность к структурным превращениям, возникающим в аморфном сплаве.
Итак, АМС относятся к материалам с нестабильной структурой, когда низкотемпературная обработка может вызвать релаксационные процессы, сопровождающиеся перераспределением атомов компонентов сплава и выделением фаз. Пластическая деформация (растяжение,
54
elib.pstu.ru
прокатка) сопровождается возникновением в АМС сдвиговых полос, отражающих зону деформации, в которой возникают внутренние напряжения, микротрещины, зародыши кристаллической фазы.
Механические свойства АМС в свежезакаленном состоянии достаточно температурно стабильны у сплавов Со–Mo–Zr, Fe–Cr–Ni–Si–В и Fe–Si–В–С, хотя температура кристаллизации у последнего ниже, чем у первых двух.
Отжиг при 723 К, 30 мин приводит к выделению в структуре всех сплавов фаз (дисперсных – в температурно стабильные) и вызывает дополнительное увеличение предела прочности в сплаве Со–Mo–Zr; незначительное уменьшение предела прочности в сплаве Fe–Cr–Ni– Si–В и значительное понижение прочности в остальных исследованных сплавах. При этом во всех исследованных сплавах возникает немонотонная температурная зависимость предела прочности в интервале температур деформирования (293–573 К) и наблюдается увеличение относительного удлинения.
Пластическая деформация изменяет коэрцитивную силу АМС, увеличивая ее от одного до двух порядков у сплавов, имеющих как высокую, так и низкую магнитострикцию. Изменение Нс, производимое последующим отжигом деформированных аморфных сплавов, связано со снятием внутренних напряжений и развитием процессов стабилизации междоменных границ, а также кристаллизации с выделением различных фаз.
55
elib.pstu.ru
4. ПОЛУЧЕНИЕ НАНОСТРУКТУРЫ МЕТОДАМИ ПЛАСТИЧЕСКОЙ ДЕФОРМАЦИИ
В работе [17] сформулированы несколько требований, которые следует учитывать при развитии методов интенсивной пластической деформации (ИПД) для получения наноструктур в объемных образцах и заготовках. Это, во-первых, возможность получения ультрамелкозернистых структур, имеющих преимущественно большеугловые границы зерен, поскольку именно в этом случае происходит качественное изменение свойств материалов. Во-вторых, возможность формирования наноструктур, однородных по всему объему образца, что необходимо для обеспечения стабильности свойств полученных материалов. В-третьих, образцы не должны иметь механических повреждений или разрушений, несмотря на их интенсивное деформирование. Эти требования не могут быть реализованы путем использования обычных методов обработки металлов давлением, таких как прокатка, вытяжка или экструзия.
Для формирования наноструктур в объемных образцах необходимыми являются использование специальных механических схем деформирования, позволяющих достичь больших пластических деформаций материалов при относительно низких температурах, и определение оптимальных режимов обработки материалов. Начиная с пионерских работ по получению объемных наноструктурных материалов [8, 17], два метода ИПД – кручение под высоким давлением и равноканальное угловое (РКУ) прессование – получили наибольшее внимание и развитие. Вместе с тем в последние годы происходит активное развитие и иных методов получения нано- и субмикрокристаллических структур в металлах и сплавах с использованием всесторонней ковки, РКУ вытяжки и др. Рассмотрим подробнее принципы основных методов ИПД, их схемы и режимы.
Кручение под высоким давлением Р (рис. 4.1) и РКУ прессование (рис. 4.2) относятся к числу первых методов, с помощью которых были достигнуты большие пластические деформации с истинными степенями, равными 10 и более, без разрушения образцов. Отметим при этом, что оценка и сопоставление степеней деформации, достигнутых при реализации различных методов ИПД, весьма неоднозначны.
56
elib.pstu.ru
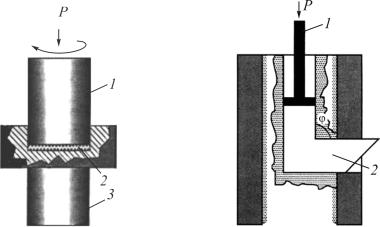
Рис. 4.1. Интенсивная пластическая |
Рис. 4.2. Интенсивная пластическая |
деформация кручением под высо- |
деформация РКУ прессованием: |
ким давлением: 1 – пуансон; 2 – об- |
1 – пуансон; 2 – заготовка; φ – угол |
разец; 3 – суппорт |
пересечения каналов |
Расчет величин эквивалентной пластической деформации при реализации различных методов ИПД может быть основан либо на кинематическом подходе (изменение геометрических размеров деформируемой заготовки), либо на энергетическом подходе, связанном с одинаковыми значениями выполненной работы пластической деформации. При этом обращается внимание на осложнения, возникающие при расчете степени деформации, протекающей в условиях изменения ее маршрута, и связанные с изменением характера движения дислокаций в деформируемом материале. Для учета данных осложнений предполагается ввести факторы эффективности, зависящие от свойств исследуемого материала.
4.1. Деформация кручением под высоким давлением
Установки, в которых деформация кручением была проведена под высоким давлением, являются развитием известной идеи наковальни Бриджмена. В первых работах эти установки были использованы для исследования фазовых превращений в условиях интенсивных пластических деформаций, а также изучения эволюции структуры и изменения температуры рекристаллизации после больших пластических деформаций.
57
elib.pstu.ru
Доказательства формирования наноструктур с неравновесными большеугловыми границами зерен при использовании ИПД кручением явились новым и принципиально важным моментом. Это позволило рассматривать метод кручения под высоким давлением в качестве нового способа получения наноструктурных материалов.
Рассмотрим механические аспекты интенсивной пластической деформации кручением. При деформации кручением под высоким давлением (см. рис. 4.1) как исходные, так и полученные образцы имеют форму дисков. При этом образец помещается между бойками и сжимается под приложенным давлением (Р) в несколько гигапаскаль. Нижний боек вращается, и силы поверхностного трения заставляют образец деформироваться сдвигом. Геометрическая форма образцов такова, что основной объем материала деформируется в условиях гидростатического сжатия под действием приложенного давления и давления со стороны внешних слоев образца. В результате, несмотря на большие степени пластической деформации, образец не разрушается.
Для расчета степени деформации при кручении под высоким давлением применяются различные соотношения. Так, в работе [18] для расчета истинной логарифмической степени деформации е использовали формулу
е = ln (vr/h), |
(4.1) |
где v – угол вращения, рад; r, h – соответственно радиус и толщина диска.
Данная формула аналогична соотношению, используемому при расчетах истинной степени деформации образцов, подвергнутых растяжению. Однако если в случае растяжения формула (4.1) имеет физическое обоснование, то оно отсутствует в случае кручения. В частности, согласно этому соотношению, при кручении под давлением после одного оборота логарифмическая степень деформации по периметру типичных образцов диаметром 20 мм и толщиной 1 мм составляет 4,1, а по периметру образцов диаметром 10 мм и толщиной 0,2 мм – 5,7. В то же время в центре этих образцов она равна нулю. Между тем, как показывают результаты многочисленных исследований, в ходе реализации данной схемы ИПД в центральной части образцов после нескольких оборотов структура также измельчается и является обычно однородной по радиусу образцов. Это подтверждается и результатами обнаружения близких значений микротвердости в различных точках, как в центре,
58
elib.pstu.ru

так и на периферии деформированных образцов. При расчете степени сдвиговой деформации ес в данном методе часто также используют формулу, применяемую в случае обычного деформирования кручением для расчета степени сдвиговой деформации на расстоянии R от оси образца в форме диска:
e 2R |
N |
, |
(4.2) |
c |
h |
|
где N – число оборотов; h – толщина образца.
Для сопоставления степени сдвиговой деформации при кручении со степенью деформации при других схемах деформирования первую обычно преобразовывают в так называемую эквивалентную деформацию еэкв. Согласно критерию Мизеса,
е |
ес |
. |
(4.3) |
|
|||
экв |
3 |
|
|
|
|
|
Относительно уравнения (4.2) справедливы два замечания [8]:
1) расчеты с помощью данного уравнения приводят к выводу о том, что деформация должна изменяться линейно от нуля в центре образца до максимального значения на концах его диаметра, однако на самом деле это, как отмечалось выше, экспериментально часто не наблюдается;
2) в процессе деформации исходная толщина образца под воздействием высокого сжимающего давления уменьшается примерно в 2 раза, поэтому использование, как это обычно делается, в качестве h исходной толщины образца занижает рассчитанные значения деформации по сравнениюс истинными.
Оба эти замечания свидетельствуют о том, что степени деформации, рассчитанные с помощью уравнений (4.1)–(4.3), лишь примерно равны реальным степеням деформации. Более того, формирование наноструктуры при ИПД происходит под действием не только внешних, но и внутренних напряжений. Вместе с тем между величиной последних и истинными деформациями нет жесткой связи. Подтверждением этого является возможность формирования однородной структуры по диаметру образцов, подвергнутых ИПД кручением, хотя в соответствии с выражениями(4.1) и (4.2) в центре образцов не должно происходить существенного измельчения микроструктуры. В связи с этим при исследовании процессов эволюции микроструктуры в ходе ИПД кручением часто более правильно рас-
59
elib.pstu.ru
сматривать число оборотов, а не величину деформации, рассчитанную с помощью аналитических выражений. Это положение становится особенно важным при обработке труднодеформируемых или хрупких материалов, где возможно проскальзывание между бойками и образцом или растрескивание последнего. Для устранения последних двух нежелательных эффектов необходимо повышение приложенного давления, но это создает дополнительные технологические трудности в подборе более прочного материала бойков, оптимизации конструкции оснастки.
Полученные ИПД кручением образцы имеют форму обычных дисков размером 10–20 мм и толщиной 0,2–0,5 мм. Существенное измельчение структуры наблюдается уже после деформирования на полоборота [8], но для создания однородной наноструктуры требуется, как правило, деформация в несколько оборотов. Например, на никеле показано, что увеличение числа оборотов до 5 и более и приложенного давления до 5 ГПа и более позволило существенно повысить однородность распределения микротвердости по всему диаметру образцов 8 .
В образцах, полученных методом ИПД кручением, размеры зерен зависят от исходного состояния деформируемого материала, температуры проведения процесса и некоторых других факторов. Например, аустенитная сталь Х18Н10Т после обработки ИПД кручением при комнатной температуре имеет размер зерен порядка 70 нм. Эта же сталь, но легированная молибденом, ванадием и азотом измельчается до 40–50 нм. Низкоуглеродистая сталь (до 0,25 % С) после обработки при комнатной температуре приобретает частичную наноструктуру с зерном приблизительно 100 нм. При обработке этой стали при температуре около 500 С формируется более однородная структура, но размер зерна при этом несколько увеличивается. Алюминиевые сплавы Al Cu Mg и Al Mg Si в исходно закаленном состоянии измельчаются до 50 нм.
Недавние исследования показали также, что ИПД кручением может быть успешно использована не только для измельчения структуры, но и как метод консолидации порошков. При этом обнаружено, что высокие давления, равные нескольким гигапаскалям, при деформации кручением при комнатной температуре могут обеспечивать достаточно высокую плотность, близкую к 100 %, в получаемых наноструктурных образцах в форме дисков. При этом для получения таких образцов консолидацией ИПД кручением могут использоваться не только обычные порошки, но также и порошки, подвергнутые обработке вшаровой мельнице.
60
elib.pstu.ru