
1533
.pdfуровень внешних воздействий для генерации новых дислокаций, и дислокационные скопления могут состоять лишь из 2–3 дислокаций [8]. Исходя из этого Граффетом проведена оценка минимально возможного размера зерна:
dкр |
3Gb |
, |
1 v H |
где G – модуль сдвига; b – вектор Бюргерса; v – коэффициент Пуассона; Н – твердость материала.
Это выражение определяет такой критический уровень накопленных во время деформации напряжений, при достижении которого уже невозможно создать дислокационное скопление, состоящее из 2 дислокаций. Данная модель предполагает, что чем труднее идет процесс возврата в материале, тем сильнее можно измельчить микроструктуру. Это подтверждается экспериментально тем фактом, что материалы с более высокой температурой плавления (и соответственно с более высокой температурой начала возврата структуры) измельчаются сильнее (см. рис. 2.4, в). Любые способы задержки процесса возврата в структуре (многофазные материалы, композиты и т.д.) приводят к меньшему размеру зерна при измельчении при шаровом размоле.
21
elib.pstu.ru
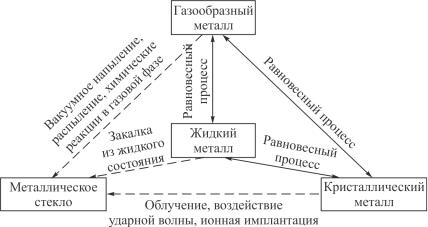
3.АМОРФНЫЕ МЕТАЛЛЫ И СПЛАВЫ
3.1.Методы получения аморфных металлов
Внастоящее время известно довольно большое число способов, позволяющих получать аморфные металлы и сплавы. Основные процессы получения аморфного (стеклообразного) состояния металлов можно описать схемой, приведенной на рис. 3.1. Равновесные обратимые процессы
изменения состояния металлов, а именно, газ жидкость, жидкость кристалл, газ кристалл показаны сплошными стрелками. Получение аморфного состояния связано с неравновесными процессами. Эти изменения состояния металловданы на рисунке штриховыми стрелками.
Рис. 3.1. Методы получения аморфных металлов
Таким образом, методы получения аморфных структур могут быть отнесены к одной из следующих трех групп:
1)осаждение металла из газовой фазы;
2)затвердевание жидкого металла;
3)введение дефектов в металлический кристалл.
В качестве методов, относимых к первой группе, можно назвать следующие: вакуумное напыление, распыление и химические реакции в газовой фазе. Ко второй группе относятся различные методы закалки из жидкого состояния. К третьей группе можно отнести методы облучения частицами поверхности кристалла, воздействия ударной волной и ряд других. Имеется также еще одна особая группа методов, которые можно было бы
22
elib.pstu.ru
с известными оговорками отнести к первой группе. Речь идет о методах электролитического осаждения аморфных пленок из растворов электролитов, главным образом водных растворов. Характеристики различных методовполучения аморфных структур представлены в табл. 3.1.
|
|
Таблица 3 . 1 |
Характеристика методов получения аморфных металлов |
||
|
|
|
Метод |
Форма образца |
Аморфизируемые составы |
|
Газообразные металлы |
|
Вакуумное напыление |
Сверхтонкая пленка |
Fe, Ni, Mo, W… |
Ионное осаждение |
(10–4–10–2 мкм) |
Сплавы типа: РЗМ – ме- |
Тонкая пленка |
||
|
(10–2–10–1 мкм) |
талл, металл – металл, |
Распыление: |
|
металл – неметалл |
|
То же |
|
с низкой скоростью |
То же |
|
с высокой скоростью |
Толстая пленка |
– » – |
( 1 мкм мин) |
(несколько миллиметров) |
SiC, SiB, SiN… |
Химические реакции |
То же |
|
в газовой фазе |
|
|
|
Ионизированные металлы |
|
Металлизация (электро- |
Толстая пленка |
Ni – P, Co – P, Fe – P, |
литическая или химиче- |
(несколько миллиметров) |
Ni – B, Co – W, Fe – W, |
ская) |
|
Cr – W, Fe – Mo… |
|
Жидкие металлы |
|
Закалка из расплава (ме- |
Тонкиепластинки(не- |
Сплавы типа: металл – |
тод выстреливания, ме- |
сколькосотмиллиграммов) |
неметалл, металл – ме- |
тод молота и наковальни, |
|
талл, РЗМ – металл |
экстракция расплава) |
|
То же |
Центробежная закалка |
Тонкая лента |
|
Закалка на диске |
(ширина ≈5 мм) |
– » – |
Тонкая лента |
||
Прокатка расплава |
(ширина ≈100 мм) |
– » – |
Тонкая лента |
||
Распыление расплава |
(ширина ≈10 мм) |
– » – |
Порошок |
||
(спрей-метод) |
|
– » – |
Кавитационный метод |
– » – |
|
Распыление расплава |
|
– » – |
вращающимся диском |
– » – |
|
Электроразряд в масле |
– » – |
– » – |
Экструзия расплава |
Тонкая проволока |
– » – |
Вытягивание волокон из |
То же |
– » – |
вращающегося барабана |
|
– » – |
Вытягивание расплава в |
– » – |
|
стеклянном капилляре |
|
|
|
|
23 |
elib.pstu.ru
3.1.1. Метод вакуумного напыления
Метод вакуумного напыления 10] уже довольно давно используется для изготовления аморфных пленок простых металлов и некоторых сплавов. Суть метода состоит в следующем. Металл или сплав нагревают в вакууме (обычно 10–3–10–4 Па, предпочтительно 10–6–10–9 Па), при этом с его поверхности испаряются (сублимируются) атомы, которые затем осаждаются на массивную охлаждаемую плиту-подложку. Для нагрева образца применяются печи сопротивления, высокочастотные индукционные печи, электронный луч, а в качестве подложки используют стекло или сапфир. Напыляемые атомы металла в вакууме движутся прямолинейно, сталкиваются с подложкой и «прилипают» к ней. При этом, однако, на подложку попадают и атомы газа (например, кислорода), которые неизбежно присутствуют в вакууме, в результате эти атомы будут присутствовать и в напыляемой пленке, поэтому ее свойства оказываются существенно зависящими от степени вакуумирования и наличия остаточного газа того или иного сорта.
При изготовлении аморфных пленок методом вакуумного напыления обычно необходимо поддерживать температуры ниже комнатных. В частности, в случае напыления чистых металлов подложка должна быть охлаждена до температур порядка температуры жидкого гелия. Если температура недостаточно низка и лежит выше температуры Тх напыляемого металла, получаемая пленка не аморфизируется. Например, в случае полупроводников – кремния и германия, у которых Тх выше комнатной температуры, можно использовать подложку и при комнатной температуре, а в случае таких переходных металлов, как железо, кобальт и никель, у которых Тх очень низкая (у железа 4 К, у кобальта 33 К и у никеля ≈70 К), должна быть низкой и температура подложки.
Температура кристаллизации и, следовательно, термическая стабильность напыленных пленок существенно зависит от их толщины. Так, пленка железа толщиной 2,5 нм кристаллизуется при 50–60 К, а при толщине 15 нм железо получить в аморфном состоянии вообще не удается. Методом вакуумного напыления получают также аморфные пленки Мn, Сr, Те, Sb, Ga, As, Al, V, Pd, Zr, Hf, Re, Hb, Та, W, Mo. Мар-
ганец остается в аморфном состоянии вплоть до 400 К.
При изготовлении пленок из сплавов обычно используется одновременное напыление нескольких элементов. В основе метода лежит различие в упругости паров элементов, входящих в состав сплава. Од-
24
elib.pstu.ru
нако регулировать состав получаемой пленки довольно трудно. Поскольку обычно температура Тх у сплавов сравнительно высока, то легко добиться, чтобы температура подложки была ниже Тх, что и делают, например, в случае получения сплава железа с 10 % (ат.) германия, у которого Тх = 130 К. Все же для получения аморфных сплавов этот метод можно применять лишь ограниченно. В частности, при изготовлении аморфных сплавов, состоящих из элементов с сильно различающейся упругостью паров, необходимо тщательно регулировать скорость напыления разных элементов. При этом нужно поддерживать постоянство количественных соотношений между элементами, осаждаемыми на подложку. Здесь в последнее время начинают применяться методы машинного контроля. Скорость напыления определяется сортом элементов, уровнем вакуума, структурой подложки и обычно составляет 0,5–1,0 нм/с.
Для аморфизации сплавов метод напыления более предпочтителен, чем для чистых металлов, ибо упрощается аппаратура и некоторые операции, в связи с тем, что при получении пленок сплавов не требуется глубокого охлаждения подложки. Однако, как уже указывалось, метод вакуумного напыления имеет ограничения по сортам атомов компонентов сплава. Кроме того, при использовании этого метода трудно регулировать состав сплава, поэтому для массового производства он не пригоден.
3.1.2. Метод распыления
Метод распыления [10] состоит в следующем. В газовую атмосферу с низким давлением помещаются два электрода, между которыми наводится разность потенциалов, в результате чего газ ионизируется. Ионы сталкиваются с электродом, выбивая атомы с его поверхности. При столкновении ионов газа с твердой поверхностью электрода происходят различные процессы, схематично показанные на рис. 3.2. В результате удара из металла выбиваются нейтральные атомы или молекулы (широкая черная стрелка на рисунке), т.е. происходит явление распыления металла. Для объяснения этого предложен следующий механизм. Вблизи поверхности металла ионы нейтрализуются за счет электронов ( e ), испускаемых металлом под воздействием электрического поля. Эти нейтральные атомы внедряются в твердое тело электрода, «выталкивая» атомы с его поверхности.
25
elib.pstu.ru
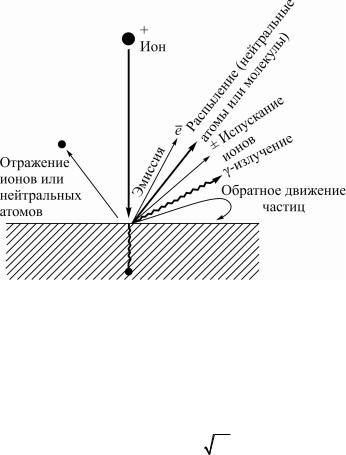
Рис. 3.2. Процессы, происходящие при соударении ионов с поверхностью твердого тела
Число атомов, распыляемое при падении одного иона, называется коэффициентом распыления (атомов/ион). Этот коэффициент изменяется с изменением энергии ионов Et. При увеличении Et до 150 эВ он возраста-
ет как Et2 ; в интервале Et от 150 до 400 эВ – растет пропорционально Et, и далее до 5000 эВ – пропорционально Et , после чего практически не
увеличивается. Когда Et достигает ≈10 кэВ, число ионов, внедряющихся в твердый электрод, становится очень большим. Это уже соответствует ионной имплантации. Для процесса распыления характерно то, что атомы напускаются в широком интервале углов, а также то, что даже если компоненты сплава имеют различную упругость пара, все равно можно получить пленку почти такого же состава, каков он у катода, с хорошей плотностью, прилегания к подложке. С другой стороны, так как в методе распыления степень вакуума составляет 1,0–0,1 Па, в пленку попадает много остаточного газа. Кроме того, довольно сильно нагревается подложка. Поэтому этот метод пригоден только для получения сплавов с высокой температурой кристаллизации. Получить же чистые аморфные металлы этим методом практически невозможно.
Известно несколько разновидностей метода распыления: простой двухэлектродный (рис. 3.3), трехили четырехэлектродный, магнетронный, высокочастотный, распыление со смещением, асимметричное рас-
26
elib.pstu.ru
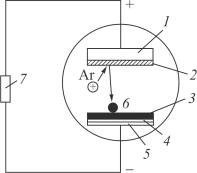
пыление на переменном токе и ряд других. Методы, в которых используются смеси химически активных газов, применяются для производства пленок химических соединений (оксидов, нитридов и т. п.).
В двухэлектродном методе распыления атомы испускаются мишенью (катодом), а пленка осаждается на подложке (аноде). В качестве источника тока можно использовать как постоянный электрический ток, так и переменный ток высокой частоты. Разработана аппаратура для распыления со смеще-
нием, позволяющая |
уменьшить |
Рис. 3.3. Принципиальная схема |
|
количество адсорбированного газа, |
двухэлектродного метода распы- |
||
и |
аппаратура для |
распыления |
ления: 1 – катод; 2 – мишень; 3 – |
с |
использованием асимметричного |
образец; 4 – подложка; 5 – анод; |
|
переменного тока. Эти методы при- |
6 – атом; 7 – источник питания |
||
меняются к сплавам |
типа РЗМ – |
(постоянный ток или ток высокой |
|
переходный металл (Gd–Со, Cd–Fe |
частоты) |
||
|
и др.), имеющим пузырьковую доменную структуру. В последнее время их начали применять и для получения аморфных сплавов типа металл – металлоид и металл – металл.
Скорость осаждения при использовании метода распыления обычно составляет 0,1 мкм/мин.
Условия распыления и его характеристики различаются для разных методов, поэтому необходимо правильно выбирать метод в зависимости от требуемых свойств получаемых пленок.
3.1.3. Методы металлизации
Известны две разновидности метода металлизации [10]: электролитическая и неэлектролитическая (химическая) металлизации. Последний метод называют также методом получения покрытий восстановлением.
Электролитическая металлизация. В основе метода лежит восста-
новление и осаждение на катоде-подложке ионов металла, образующихся при растворении анода в электролите. В качестве электролитов обычно используются водные растворы, в которых в определенной пропорции смешаны хлориды металлов (например, NiCl2·6H2О, СоС12·6Н2О) и соли
27
elib.pstu.ru
метафосфорной (Н3РО3) и ортофосфорной (Н3РО4) кислот. Катодом обычно служит медь или графит. Электролиз проводится при температуре 50– 90 °С при плотности тока 0,5–4 А/см2. В результате получаются аморфные пленочные покрытия из никеля или кобальта, содержащие большие количества фосфора. Этим методом можно получать аморфные сплавы Ni–Р,
Со–Р, Fe–Р, Со–Ni–Р, Со–W, Со–Re, Fe–W, Сr–W, Fe–Mo, Cr–Fe, причем особенности метода накладывают сильные ограничения на состав сплавов. Важно, чтобы строго соблюдались необходимые пропорции при приготовлении электролитов, а также чтобы была предусмотрена возможность регулировки электрического тока на электродах и температуры электролита.
Химическая металлизация. Аморфные пленки типа Ni–Р получают осаждением из водных растворов хлоридов металлов. Для этой цели используют ванны, представляющие собой смесь гипофосфитов и гидрида бора. Подбирая соответствующим образом состав ванны, получают аморфные сплавы Со–Р, Ni–В и Ni–Fe–В.
В этом методе в качестве отрицательного полюса используют не только металлы, но и различные диэлектрики: стекла, пластмассы и т. п. Главная реакция представляет собой реакцию растворения ионов металла. Фосфор попадает в пленку в результате протекания побочной реакции, что позволяет контролировать его количество, регулируя концентрацию восстановителя. Метод позволяет получать сплавы на основе никеля и кобальта, содержащие фосфор и бор, но номенклатура сплавов крайне ограниченна. Преимуществом метода является сравнительно простое получение пленок с большой площадью.
3.1.4. Методы закалки из жидкого состояния
Методы охлаждения расплавов металлов и сплавов с большими скоростями, позволяющими достигать больших степеней переохлаждения жидкости и в конечном счете «замораживать» жидкое состояние, объединяются под общим названием «методы закалки из жидкого состояния» или «методы закалки из расплава (melt quenching)». Эти методы применяются очень широко, так как позволяют получить металлические аморфные порошки, тонкую проволоку и ленту.
Методы закалки из жидкого состояния имеют несколько разновидностей (см. табл. 3.1). Методы выстреливания, молота и наковальни, а также экстракции расплава позволяют получать тонкие аморфные пластинки массой до нескольких сот миллиграммов. Методами, ис-
28
elib.pstu.ru
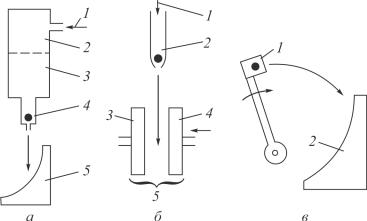
пользующими закалку на центрифуге, закалку на диске, прокатку расплавленного металла, можно получить непрерывные тонкие ленты. Эти методы могут быть использованы для промышленного производства аморфных металлов. В настоящее время для производства порошков начинают применяться такие методы, как распыление расплава (в том числе и центробежное распыление), кавитация, электроэрозия. Для производства тонкой проволоки используются методы экструзии расплава, вытягивания расплава в стеклянном капилляре и ряд других.
Получение тонких пластинок. Методы изготовления аморфных металлов в виде пластинок массой до нескольких сот миллиграммов применяются для получения образцов для экспериментов по определению некоторых физических свойств. Практическое использование этих образцов ограничено из-за их неопределенной и нерегулируемой формы. Однако преимуществом этих методов является возможность достижения высоких скоростей охлаждения (до 109 °С/с), что позволяет аморфизировать сплавы в широком диапазоне составов. Принципиальные схемы различных методов получения мелких пластин показаны на рис. 3.4. Такие пластинки образуются при выстреливании небольших капель расплавленного металла и сплава либо при помощи газа под давлением, либо механическим путем намеднуюохлаждаемую плиту (холодильник).
Рис. 3.4. Методы получения тонких пластинок: а – метод выстреливания: 1 – газ под давлением, 3 – камера низкого давления, 4 – капля расплава, 5 – холодильник; б – метод молота и наковальни: 1 – газ под давлением, 2 – капля расплава, 3 и 4 – плиты (молот и наковальня), 5 – холодильник; в – метод экстракции расплава (вра-
щающейся катапульты): 1 – каплярасплава, 2 – холодильник
29
elib.pstu.ru
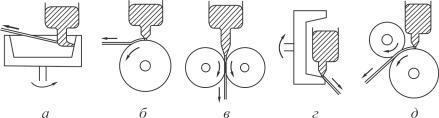
Получение тонкой ленты. Тонкие непрерывные аморфные ленты необходимы не только для определения физических свойств аморфных металлов. Такие ленты с регламентированной формой имеют весьма разнообразное практическое применение. Здесь можно выделить три основных метода: центробежной закалки, закалки на диске и прокатки расплава между двумя валками. На рис. 3.5 приведены принципиальные схемы этих методов. Общим для них является, во-первых, плавление металла при электрическом или индукционном нагреве и, во-вторых, выдавливание расплава из сопла под действием газа и затвердевание его при соприкосновении с поверхностью вращающегося охлаждаемого тела (холодильника). Различие состоит в том, что в методах центробежной закалки и закалки на диске расплав охлаждается только с одной стороны. Основной проблемой является получение достаточной степени чистоты внешней поверхности, которая не соприкасается с холодильником. Метод прокатки расплава позволяет получить хорошее качество обеих поверхностей ленты, так как они одновременно охлаждаются, но управлять процессом в этом случае довольно сложно. Для каждого метода имеются свои ограничения по размерам лент, поскольку есть различия и в протекании процесса затвердевания, и в аппаратурном оформлении методов. Если при центробежной закалке ширина ленты составляет <5 мм, то прокаткой получают ленты шириной 10 мм и более.
Метод закалки на диске, для которого требуется более простая аппаратура, позволяет в широких пределах изменять ширину ленты в зависимости от размеров плавильных тиглей. Данный метод позволяет изготавливать как узкие ленты шириной 0,1–0,2 мм, так и широкие – до 10 мм, причем точность поддержания ширины может быть ±3 мкм. Разрабатываются установки с максимальной вместимостью тигля до 50 кг.
Рис. 3.5. Методы получения тонкой ленты путем закалки из расплава:
а– центробежная закалка; б – закалка на диске; в – прокатка расплава;
г– центробежная закалка; д – планетарная закалка на диске
30
elib.pstu.ru