
Статистические методы исследования качества объектов производства
.pdfМинистерство образования и науки Российской Федерации
Федеральное государственное бюджетное образовательное учреждение высшего профессионального образования «Пермский национальный исследовательский политехнический университет»
Кафедра «Инновационные технологии машиностроения»
СТАТИСТИЧЕСКИЕ МЕТОДЫ ИССЛЕДОВАНИЯ КАЧЕСТВА ОБЪЕКТОВ ПРОИЗВОДСТВА
Методические указания для выполнения практических заданий
и самостоятельной работы по дисциплине «Технологическое обеспечение качества
объектов производства»
Издательство Пермского национального исследовательского
политехнического университета
2012
Составитель д-р техн. наук, профессор В.И. Свирщёв
УДК 519.2:621.658.512 С78
Рецензент
канд. техн. наук, доцент А.С. Донсков (Пермский национальный исследовательский политехнический университет)
Статистические методы исследования качества объектов С78 производства : метод. указания для выполнения практических заданий и самостоятельной работы по дисциплине «Технологическое обеспечение качества объектов производства» / сост. В.И. Свирщёв. – Пермь : Изд-во Перм. нац. исслед. политехн.
ун-та, 2012. – 45 с.
Изложены краткие теоретические сведения о показателях качества деталей машин, погрешностях обработки и законах их распределения, критериях согласия используемых для проверки статистических гипотез. Рассмотрена методика статистического анализа показателей качества объектов обработки по их выборкам. Приведены задачи для практических занятий по дисциплине.
Предназначены для магистров, обучающихся по направлению «Конструкторско-технологическое обеспечение машиностроительных производств».
УДК 519.2:621.658.512
© ПНИПУ, 2012
2
СОДЕРЖАНИЕ |
|
1. Основные теоретические сведения................................................ |
4 |
1.1. Показатели качества деталей машин................................. |
4 |
1.2. Погрешности при получении показателей качества |
|
объектов обработки ................................................................... |
6 |
1.3. Законы распределения показателей качества объектов |
|
обработки.................................................................................... |
9 |
1.3.1. Закон нормального распределения ........................ |
9 |
1.3.2. Закон равной вероятности....................................... |
10 |
1.3.3. Закон равнобедренного треугольника |
|
(закон Симпсона)............................................................... |
11 |
1.3.4. Закон эксцентриситета (закон Релея)..................... |
12 |
2. Статистическая проверка гипотез в исследованиях качества |
|
объектов производства....................................................................... |
13 |
2.1. Задачи статистической проверки гипотез......................... |
13 |
2.2. Критерии согласия, используемые для установления |
|
распределения случайной величины........................................ |
16 |
2.3. Критерии согласия, используемые для установления |
|
равенства двух выборочных средних....................................... |
18 |
2.4. Критерий согласия, используемый для установления |
|
равенства двух дисперсий......................................................... |
21 |
2.5. Критерии согласия, используемые для установления |
|
доверительных интервалов определения выборочных |
|
характеристик генеральной совокупности............................... |
22 |
3. Исходные данные для статистических исследований |
|
качества объектов обработки............................................................. |
24 |
4. Задания для практических занятий................................................ |
26 |
Список литературы............................................................................. |
33 |
Приложения......................................................................................... |
34 |
3
1.ОСНОВНЫЕ ТЕОРЕТИЧЕСКИЕ СВЕДЕНИЯ
1.1.Показатели качества деталей машин
Качество деталей машин квалифицируют по степени их соответствия чертежу, техническим требованиям и условиям на приемку. При этом в самом общем случае различают следующие показатели качества:
–точность изготовления;
–рельеф элементарных поверхностей (микрогеометрия);
–физико-химическое и физико-механическое состояние мате-
риала;
–действительное состояние поверхностных слоев всех функциональных (в первую очередь) и прочих поверхностей.
Под точностью изготовления понимается степень приближения действительных (фактических) параметров детали к их теоретическим (расчетным) значениям. Точность изготовления деталей по геометрическим параметрам оценивается величиной расхождения их действительных размеров, форм и взаимного расположения поверхностей с их заданными значениями, указанными на рабочем чертеже и в технических требованиях.
Отступления геометрических параметров реальных деталей от проектных значений называют погрешностями. Погрешности могут возникать на всех стадиях изготовления, хранения и эксплуатации деталей, под воздействием внешней среды, внутренних изменений структуры материала, износа и других причин. Достичь абсолютной точности при обработке не удается, поэтому в целях ограничения предельных значений погрешностей конструктором устанавливаются допуски размеров, отклонений форм и расположения поверхностей, соответствующие требуемым квалитетам и степеням точности.
Для реальных поверхностей деталей машин, кроме макрогеометрических отклонений формы, характерны и так называемые
микрогеометрические отклонения теоретического профиля. Мик-
4
рогеометрия определяет рельеф поверхностей детали в целом и на отдельных участках. Основными показателями рельефа поверхности служат шероховатость и волнистость.
Шероховатость поверхности согласно ГОСТ 2789–73 характеризуется высотными параметрами профиля (Ra, Rz, Rmax), шаговыми параметрами профиля (Sm, S) и относительной опорной длиной профиля (tp).
Волнистостью называют совокупность периодически повторяющихся неровностей поверхности, которые образуются в процессе обработки из-за вибраций или относительных колебательных движений в технологической системе станок – приспособление – инструмент – заготовка. Волнистость измеряют в сечениях, перпендикулярных к поверхности. Согласно рекомендациям РС 3951–73 волнистость характеризуется высотными параметрами (Wz, Wmax)
исредним шагом Sw волн. Считается, что параметры волнистости значительно больше аналогичных параметров шероховатости, а их
отношение (Sw/Wmax) находится в пределах 40–1000. В отдельных случаях волнистость рассматривают как часть отклонения формы поверхностей, а рельеф поверхности в целом – как элемент геометрической точности детали.
Физико-химические свойства материала, например, про-
центное содержание входящих в него компонентов и их взаимосвязь в кристаллической решетке, жидкотекучесть, красколомкость
идр., определяются техническими требованиями, установленными ГОСТ на соответствующие марки используемых материалов. Физи- ко-механическое состояние материала (прочность, твердость, упругость или хрупкость и др.) во многом зависят от вида термической обработки, применяемой к данной марке материала, и определяются главным образом назначением и условиями работы деталей.
Особое значение для длительной и надежной работы детали в изделии имеет состояние ее поверхностей. Механические свойства поверхностного слоя любой детали чаще всего отличаются от свойств основного материала. Возможные изменения свойств материала поверхностного слоя по-разному сказываются на работоспо-
5
собности детали: одни способствуют повышению долговечности
ициклической прочности, увеличивают износостойкость; другие снижают предел усталости и несущую способность, приводят к увеличению потерь на трение и т.д. Обоснование комплекса технических требований к состоянию функциональных и других поверхностей деталей при проектировании и строгое их выполнение при изготовлении позволяют существенно улучшить показатели качества многих деталей.
При изготовлении деталей с заданными показателями качества возникают разнообразные погрешности, систематические и случайные. Это вызывает необходимость статистического исследования
иоценки величин погрешностей для эффективного управления процессами обработки и достижения требуемых показателей качества.
1.2. Погрешности при получении показателей качества объектов обработки
При автоматическом обеспечении показателей качества обработки в условиях серийного и массового производства на настроенном станке величина погрешностей обработки не зависит от исполнителя, обслуживающего станок, а определяется состоянием
исвойствами технологической системы станок – приспособление – инструмент – заготовка (СПИЗ).
Погрешности разделяют на систематические и случайные.
Систематическая погрешность – это такая погрешность, которая для всех заготовок в обрабатываемой партии деталей остается постоянной или же закономерно изменяется при переходе от каждой обрабатываемой заготовки к следующей.
Впервом случае погрешность принято называть постоянной
систематической погрешностью ∆сист, а во втором случае – переменной систематической погрешностью ∆п.с.
Постоянные систематические погрешности возникают вследствие: неточности изготовления, износа и деформации станка
иприспособления; неточности изготовления мерного режущего ин-
6
струмента (сверл, зенкеров, разверток, фасонных резцов и фрез, протяжек); неточности настройки рабочего инструмента на размер; погрешности теоретической схемы обработки заготовок. Указанные погрешности полностью переносятся на объект обработки. Например, геометрические неточности станка приводят к возникновению погрешностей формы и взаимного расположения элементарных поверхностей объекта обработки. При обработке наружных и внутренних цилиндрических поверхностей резцом или фрезой неточность настройки инструмента на размер отразится на точности выполняемого размера деталей. На этот же показатель качества окажет влияние неточность изготовления мерного режущего инструмента.
Переменные систематические погрешности возникают вследствие размерного износа режущего инструмента и температурных деформаций всех компонентов технологической системы СПИЗ. Эти погрешности являются функцией времени работы технологической системы. Температурные деформации компонентов технологической системы носят временной характер. По истечении определенного времени работы технологической системы температурные деформации компонентов технологической системы стабилизируются (система входит в состояние теплового насыщения), а погрешность, возникающая по этой причине, превращается в постоянную систематическую погрешность.
При работе на настроенных станках, а также при обработке мерным инструментом размерный износ систематически изменяет размер каждой очередной детали из обрабатываемой партии на удвоенную величину износа инструмента при выполнении диаметральных размеров или только на величину износа при односторонней обработке элементарной поверхности. Размерный износ инструмента и его интенсивность зависит от обрабатываемого материала и материала инструмента, сочетания параметров режима обработки, геометрических параметров режущих лезвий и качества их заточки.
В процессе обработки партии заготовок на настроенных станках показатели качества их обработки непрерывно колеблются
7
в определенных диапазонах, отличаясь друг от друга и от настроечного размера на величину случайной погрешности.
Случайная погрешность – это такая погрешность, которая для разных заготовок обрабатываемой партии имеет различные значения, причем ее появление не подчиняется никакой видимой зависимости. В результате возникновения случайных погрешностей происходит рассеяние показателей качества объектов обработки, достигаемых при одних и тех же условиях. Рассеяние вызывается совокупностью многих причин случайного характера, не поддающихся точному предварительному определению и проявляющих свое действие одновременно и независимо друг от друга. К таким причинам относятся: колебания твердости обрабатываемого материала и величины снимаемого припуска; изменения положения исходной заготовки, связанные с погрешностью установки ее в приспособлении; неточность установки положения суппортов по упорам и лимбам при формообразовании элементарных поверхностей; колебания температурного режима обработки и упругих отжатий компонентов технологической системы СПИЗ под влиянием нестабильности сил резания и т.д.
Таким образом, при обработке каждой детали из партии возникают свои переменные систематические и случайные погрешности, и кроме того, у каждой детали имеется общая постоянная систематическая погрешность. Ввиду того, что все эти погрешности возникают одновременно, вместе они образуют суммарную погрешность обработки детали, которая и будет определять действительное отклонение показателя качества обработки от требуемого значения. В силу изменчивости переменных систематических и случайных погрешностей суммарная погрешность обработки каждой детали будет своя, что приводит к рассеиванию показателей качества деталей в партии, обработанных с одной настройкой станка. Это рассеивание может подчиняться различным законам распределения.
Для выявления и анализа закономерностей распределения показателей качества при их рассеянии успешно применяются методы математической статистики.
8
1.3. Законы распределения показателей качества объектов обработки
1.3.1. Закон нормального распределения
Для оценки и исследования показателей качества объектов обработки обычно применяют закон нормального распределения. Выбор закона нормального распределения для исследования погрешностей качества объектов обработки обосновывается теоремой Ляпунова, которую для рассматриваемого случая можно трактовать следующим образом.
Если наблюдаемая величина Х показателя качества объекта обработки является суммой частных величин Хi, вызванных действием значительного числа случайных и некоторого числа систематических факторов, при этом:
–все случайные факторы взаимно независимы и число их не изменяется во времени;
–влияние всех случайных факторов на суммарную величину одного порядка, т.е. среди них нет доминирующих;
–число систематических факторов остается одинаковым и по-
стоянным во времени,
то при достаточно большом числе частных величин Хi сумма последних будет следовать закону нормального распределения, независимо от закона их распределения.
Опыт показывает, что когда процесс обработки на настроенных станках протекает в нормальных условиях (система СПИЗ находится в исправном состоянии), и среди возникающих случайных погрешностей обработки нет доминирующих, и систематические погрешности не изменяются существенно во времени, то распределение действительных показателей качества в партии деталей, обработанных на настроенном станке, обычно подчиняется закону нормального распределения.
Использование закона нормального распределения позволяет проводить объективную оценку показателей качества объектов об-
9
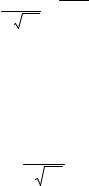
работки при выполнении отдельных операций технологического процесса изготовления деталей.
Закону нормального распределения подчиняются многие непрерывные случайные величины, которыми могут являться показатели качества объектов обработки. Плотность вероятности случайной величины, подчиняющейся закону нормального распределения, имеет следующее выражение:
(x−x )2
ϕ(x)= σ 12π e− 2σ2 ,
где х – переменная случайная величина; x – среднее значение (математическое ожидание) величины х; σ – среднее квадратическое отклонение случайной величины х от x.
Интегральный закон нормального |
распределения запишется |
|||
в виде |
|
|
|
|
F(x)= ∫x ϕ(x)dx = |
1 |
∫x e− |
(x−x )2 |
|
2σ2 dx. |
||||
−∞ |
σ 2 π −∞ |
|
|
Фактическое поле рассеяния показателей качества деталей партии (с вероятностью 99,73 %) принимается равным ∆ = 6σ.
1.3.2. Закон равной вероятности
Закону равной вероятности следует рассеяние показателей качества, зависящее преимущественно от переменных систематических погрешностей (например, от износа режущего инструмента). В этом случае непрерывная случайная величина х принимает все значения интервала (a, b) с одинаковой плотностью вероятности.
Плотность вероятности случайной величины, подчиняющейся закону равной вероятности, имеет следующее выражение:
|
1 |
при |
a ≤ x ≤b, |
|
ϕ(x) = |
|
|||
b −a |
||||
|
при x < a, x >b. |
|||
0 |
||||
|
|
|
10 |
|