
Прикладная механика композитов
..pdfМногонаправленные углерод-углеродные композиты |
251 |
Рис. 21. Характеристики смолы и пека в зависимости от температуры тер мообработки Т [8]: 1 — пек, 2 — термореактивная смола.
ноугольная смола. Низкая плотность кокса ограничивает уро вень плотности углерод-углеродного композита. Однако в не которых областях применения может оказаться необходимой именно неграфитизированная матрица.
Свойства некоторых термореактивных смол не соответ ствуют показанным закономерностям. Эту особенность мож но использовать для управления процессом уплотнения угле- род-углеродных материалов. Например, под действием высо кого давления при повышенных температурах угли из полифурилового спирта могут графитизироваться [44]. Эффект графитизаиии под нагрузкой наблюдался также в фенольных матрицах 3-D углерод-углеродных композитов [36, 37]. Пред полагают, что усадочные напряжения в окрестности углерод ных волокон вызывают графитизацию карбонизированной
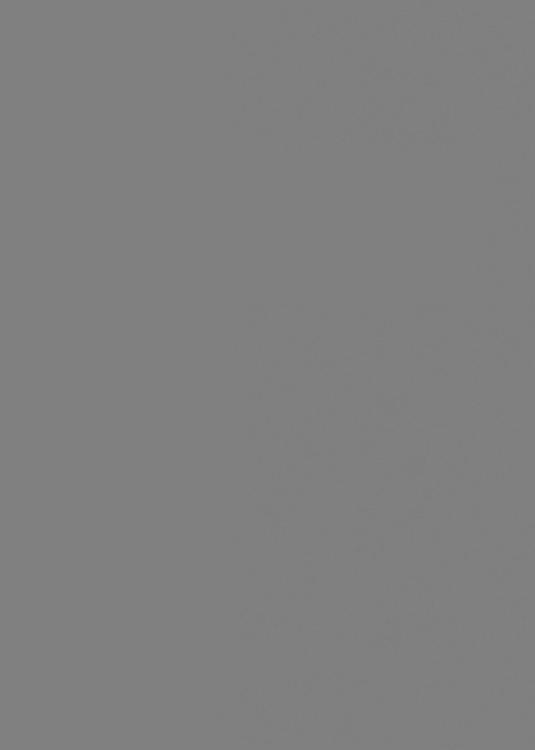
Многонаправленные углерод-углеродные композиты |
253 |
композитов с низкими характеристиками, за которые ответ ственна матрица, обеспечивающая целостность композита
[17].В многонаправленных композитах повреждение от
усадки не является серьезной проблемой ввиду отсутствия в структуре неармированных плоскостей.
Ниже перечислены особенности, которые следует прини мать во внимание, выбирая термореактивную смолу для осу ществления процесса уплотнения каркасов многонаправлен ных углерод-углеродных композитов:
(a) выход кокса от 50 % до 70 % по массе (ограниченное число данных указывает на то, что увеличение давления при карбонизации не увеличивает выход кокса);
(B) структура кокса стекловидная; графитизация не про исходит до 3000 °С;
(c) плотность кокса очень низкая (< 1,5 г/мм3);
(d)карбонизация сопровождается сильной усадкой;
(e)напряжения, приложенные извне или возникшие в процессе термообработки, могут способствовать появлению кокса с графитизированной структурой.
3.2.1.2.Пеки. Применение пеков в качестве исходного ма териала для матрицы углерод-углеродных композитов осно вано на опыте технологии обработки графита. Имеется мно жество данных о пеках из каменноугольной смолы и нефти, применяемых в процессах, которые включают пропитку, кар бонизацию и графитизацию. Как видно из табл. 8, каменно угольная смола имеет низкую температуру размягчения, низ кую вязкость расплава и высокий выход кокса. Далее будет
показано, что пеки при термообработке имеют склонность к образованию кокса с графитовой структурой.
Пропиточные пеки, применяемые для получения углеродуглеродных композитов, представляют собой смеси полицик лических ароматических углеводородов. В отличие от про странственно сшитых термореактивных смол они являются термопластическими. При нагреве от точки размягчения до температуры около 400 °С пеки претерпевают различные из менения, включая улетучивание низкомолекулярных соедине ний, полимеризацию, разрыв химических связей и перегруп пировку молекулярных структур. Обнаружено [6], что при температурах выше 400 °С в изотропном жидком пеке появ ляются шарики диаметром 0,1 мм и меньше. Эти шарики, на званные мезофазой, имеют высокоориентированную струк туру, свойства которой напоминают жидкие кристаллы. При продолжительном нагревании эти шарики сливаются, за твердевают и образуют большие упорядоченные области. Слоистая упаковка молекулярной структуры этих областей
254 |
Л. Макаллистер, У. Лакман |
Рис. 23. Влияние давления при карбонизации в единицах фунт/дюйм2, (МПа) на выход кокса из нефтяного пека [31].
способствует образованию графитовой структуры при после дующем нагревании до 2500 °С и выше. Графитовая структура карбонизованных пеков проявляется, как видно из рис. 21» в их высокой плотности и в меньшем межплоскостном рас стоянии.
Выход кокса из каменноугольной смолы или нефтяного пека при атмосферном давлении составляет около 50 % по массе. Это примерно соответствует выходу кокса из сильно карбонизированных полимерных смол. Однако карбонизация под высоким давлением может значительно повысить выход
кокса. Пиролиз |
каменноугольного пека при |
температуре |
550 °С в азотной |
атмосфере при давлении около |
10 МПа дает |
выход кокса порядка 90 % [26]. Было найдено, что увеличе ние давления газа выше 10 МПа мало влияет на выход кокса. Влияние давления при карбонизации на выход кокса из неф тяного пека показано на рис. 23. Эти данные свидетель ствуют, что для достижения высокого выхода кокса достаточ но давления от 6,9 до 68,9 МПа. Однако, как будет показано ниже, при выборе давления процесса карбонизации необхо димо учитывать кроме выхода кокса и другие факторы.
Микроструктура кокса, полученного карбонизацией пека, также зависит от давления и температуры. На рис. 24 пока зана микрофотография кокса из нефтяного пека, карбонизованного при давлениях 6,89 и 68,9 МПа с последующей тер мообработкой до 2700 °С [8]. При низком давлении получает ся кокс игольчатой структуры, вероятно, из-за деформации мезофазы вследствие просачивания газовых пузырьков. При более высоком давлении микроструктура кокса выглядит бо лее грубой и изотропной, по-видимому, из-за подавления про-
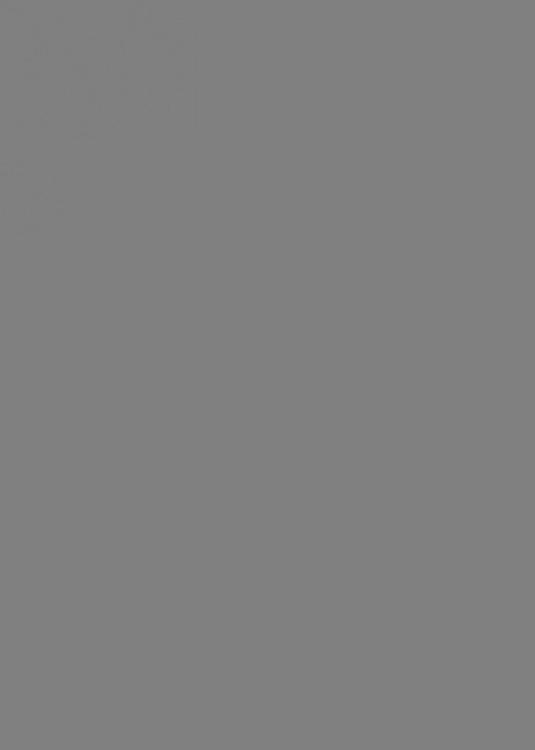
256 |
Л Макаллистер, У. |
Лакман |
3.2.2. |
Пропитка под низким |
давлением. Наиболее широко |
применяемым методом введения углеродной матрицы в много направленный армирующий каркас является пропитка заго
товки органическим |
соединением с последующей карбониза |
||||||
|
|
цией |
полученного |
компо |
|||
|
|
зита в инертной атмосфе |
|||||
|
|
ре. |
Насыщение |
матрицы |
|||
|
|
обычно |
проводят |
при ат |
|||
|
|
мосферном |
или понижен |
||||
|
|
ном давлении и для сни |
|||||
О 10 20 30 40 |
50 60 70 80 |
жения пористости до при |
|||||
М |
|
емлемого |
уровня |
повто |
|||
Рис. 25. Цикл термообработки после от |
ряют |
несколько |
раз |
||||
[36]. |
указанной |
техно |
|||||
верждения изделий из фенольных смол |
По |
||||||
[41]. |
|
логии |
многонаправлен |
||||
|
|
ный |
каркас обычно про |
питывается в вакууме смолой фенольного типа либо распла вом каменноугольного, нефтяного или синтетического пека [36, 38, 40]. В некоторых случаях на одной из стадий процесса пропитка ведется под давлением с целью заполнения всех
пор в |
армирующем |
карка |
|
||||
се. Пропитанные смолой из |
|
||||||
делия отверждают и термо- |
|
||||||
обрабатывают |
для |
завер |
|
||||
шения |
процесса |
отвержде |
|
||||
ния. Характерный цикл тер |
|
||||||
мообработки |
изделия, |
про |
|
||||
питанного фенольной |
смо |
|
|||||
лой, показан на рис. 25. |
|
||||||
Изделие, |
пропитанное |
пе |
|
||||
ком, не отверждают, а сразу |
|
||||||
подвергают |
карбонизации в |
|
|||||
азотной |
|
атмосфере. |
Карбо |
|
|||
низация |
изделий, насыщен |
|
|||||
ных смолой или пеком, осу |
|
||||||
ществляется |
путем |
нагрева |
Рис. 26. Характерный цикл карбони |
||||
с заданной |
скоростью |
до |
зации [41]. |
температур 650—1100°С [38, 39,41]. Типичный цикл карбонизации показан на рис. 26.
Следующим шагом обработки является графитизация. Она обычно проводится в индукционной печи при температурах от 2600°С до 2750 °С [36,38,41]. Характерный цикл графитизации показан на рис. 27. Скорость нагрева во всех циклах может меняться в зависимости от размера и формы обраба тываемого изделия.
Многонаправленные углерод-углеродные композиты |
257 |
Схема типичного процесса пропитки, подобного рассмот ренному, показана на рис. 28 [36]. Как видно, для заверше ния процесса создания композита цикл пропитка — термообра ботка повторяют многократно. Графитизация не является обязательным этапом каждого цикла. Число циклов уплот нения, необходимых для получения многонаправлениого угле- род-углеродного композита, зависит от материала матрицы и особенностей применяемого процесса.
0 |
4 |
В |
12 |
16 Z0 24 |
28 |
|
|
|
М |
|
|
Рис. 27. Характерный |
цикл |
графитизации |
[41]. |
На рис. 29 показана характерная зависимость плотности композита от числа циклов графитизации для изделия в виде цилиндра (диаметром 228,6 мм, толщиной стенки 12,7— 17,8 мм) с многонаправленной схемой армирования, пропи танного фенольной смолой [41]. Как видно, для достижения плотности 1,65 г/см3 потребовалось шесть циклов графити зации.
В другом примере [40] для предварительного ужесточе ния многонаправленный армирующий каркас вначале был слегка пропитан фенольным связующим. Далее в качестве ве щества для пропитки был использован синтетический пек. Повторяющиеся циклы состояли из вакуумной пропитки при температуре 204°С, карбонизации при температуре выше 538°С и графитизации при температуре 2500°С. Плотность готового композита составила 1,66 г/см3, содержание откры тых пор было 12,7 %.
Основным фактором, определяющим эффективность про цесса уплотнения многоиаправленных углерод-углеродных структур, является достижение полного насыщения каркаса исходным полимерным материалом с высоким выходом угле рода. С целью исследования эффективности процесса про питки при низком давлении была изготовлена серия прямо угольных блоков, насыщенных фенольными смолами, из
*/^9 Прикладная механика
Многократный цикл
Рис. 28. Блок-схема характерного процесса уплотнения углерод-углеродного композита [36].
Многонаправленные углерод-углеродные композиты |
259 |
которых после заданного числа циклов пропитки были взяты пробы для измерения плотности и пористости [38]. Резуль таты этих исследований показаны на рис. 30. Оказалось, что
после каждого цикла пропитки |
|
|
|||||||||
композит |
является |
по |
суще |
|
|
||||||
ству |
открыто |
пористым. |
Это |
|
|
||||||
подтверждается |
совпадением |
|
|
||||||||
результатов расчета с экспери |
|
|
|||||||||
ментальными |
данными. |
Ука |
|
|
|||||||
занный |
|
характер |
пористости |
|
|
||||||
позволяет производить пропит |
|
|
|||||||||
ку блоков почти до достиже |
|
|
|||||||||
ния |
теоретической плотности, |
|
|
||||||||
равной |
1,8 г/см3!). Однако |
с |
|
|
|||||||
точки зрения производительно |
|
|
|||||||||
сти процесса достижение такой |
|
|
|||||||||
плотности неоправданно. Фак |
|
|
|||||||||
тическая |
плотность |
готовых |
|
|
|||||||
блоков составляла от 1,6 до |
|
|
|||||||||
1,65 г/см3 при содержании от |
|
|
|||||||||
крытых пор от 8 до 10 %. Рас |
Рис. 29. |
Зависимость плотности |
|||||||||
пределение размеров |
пор ком |
||||||||||
цилиндра |
из многонаправленного |
||||||||||
позита |
с |
содержанием откры |
углерод-углеродного композита от |
||||||||
тых |
пор |
10,7 % |
приведено |
в |
числа циклов графитнзации [41]. |
табл. 11. Диаметр пор нахо дился в пределах от 17 до 0,08 мкм и определялся методами ртутной и гелиевой порометрии.
Таблица 11. Распределение размеров пор
в многонаправленном |
углерод-углеродном композите [38] |
О б ъ е м н а я д о л я п о р , % |
Д и а м е т р п о р , м к м |
0,5
3,3
3,4
0,1
3,4
Всего 10,7
о
10—17 1 —10 0,1 —1 000 1р <0,08
На основании проведенных исследований был сделан вывод о том, что процесс уплотнения многонаправленных
*> Теоретическая величина плотности 1,8 г/см3 определяется исходя из того, что по строению углеродной цепи вискозные волокна и феноль ная матрица являются стекловидными (иеграфитными) формами углерода.
260 |
Л. Макаллистер, У. Лакман |
Рис. 30. Экспериментально определенная зависимость плотность — пори стость для многонаправленного углерод-углеродного композита [38]. 1 — максимальная теоретическая плотность монолитного композита; 2 — расчетная зависимость; 3 — плотность тканой заготовки.
углерод-углеродных композитов можно проводить при низком давлении, используя для пропитки как синтетические смолы, так и пек. Применение такой технологии целесообразно для производства композитов с содержанием открытых пор около 10 %.
3.2.3. Пропитка под высоким давлением. Как видно из рис. 23, при карбонизации пека под давлением выход кокса может увеличиться от 50 % при атмосферном давлении до 85 % при давлении 68,9 МПа. Это свойство пеков является основой процесса уплотнения углерод-углеродных композитов, назван ного давление — пропитка — карбонизация (pressure — im pregnation— carbonisation — PIC). Для обеспечения эффек тивной пропитки и уплотнения углерод-углеродных компо зитов на этапах плавления и коксования матрицы в цикле карбонизации применяется изостатическое давление [7, 10]. Уплотнение высоким давлением отличается от пропитки при низком давлении (описанной в разд. 3.2.2) только примене нием дополнительного давления при карбонизации. Схема цикла уплотнения высоким давлением показана на рис. 31.
При подготовке процесса уплотнения высоким давлением пропитка заготовки производится горячим пеком [16]. Твер дый пек расплавляется под вакуумом в емкости, нагретой до 250°С; заготовки (т. е. армирующие каркасы), помещенные