
Аэрокосмическая техника высокие технологии и инновации – 2015
..pdfУДК 621.45.018.2
ИССЛЕДОВАНИЕ ГАЗОДИНАМИЧЕСКОЙ УСТОЙЧИВОСТИ ТРДД В УСЛОВИЯХ БОКОВОГО ВЕТРА
А.В. Андреянов, М.А. Ганзен
Рыбинский государственный авиационный технический университет имени П.А. Соловьева, Рыбинск, Россия
e-mail: technology@rsatu.ru
Описываются особенности экспериментального исследования работы ТРДД гражданского назначения в условиях испытаний на открытом стенде с генератором бокового ветра. Анализируется влияние скорости бокового ветра на изменение запасов ГДУ и эффективность работы противопомпажной системы.
Ключевые слова: ТРДД, испытания, боковой ветер, помпаж, газодинамическая устойчивость.
Одним из требований, предъявляемых к современным газотурбинным двигателям, особенно применяемым в гражданской авиации, является высокая газодинамическая устойчивость (ГДУ), в том числе стойкость к помпажным явлениям. Известно, что довольно большое количество авиационных происшествий (порядка 7–10 %) связано с возникновением помпажа компрессора или двигателя в целом. Наиболее часто это явление наблюдается при взлете и связывается со случайным попаданием в газовоздушный тракт двигателя посторонних предметов (птиц, элементов покрытия взлетно-посадочнойполосы (ВПП) идругихпредметов).
В последние годы все большее внимание уделяется влиянию на ГДУ внешних воздействий, в особенности сильного бокового ветра, способного вызвать срыв потока с обечайки возбухозаборника. При расположении двигателей под крылом срывные и помпажные явления также могут быть следствием образования завихрений (вихревых жгутов) от поверхности ВПП. Как правило, эти явления и их воздействие на работу двигателя исследуются при испытаниях самолета [1]. Современные
351

нормы летной годности [2] предполагают установление предельно допустимой скорости и угла бокового ветра с последующей экспериментальной проверкой устойчивости двигателей в процессе полигонных испытаний. Тем не менее логично, с точки зрения сокращения общих сроков испытаний и исключения трудоемкой доводки конструкции, проводить предварительные испытания двигателя (без самолета) с имитацией воздействия бокового ветра. В общем случае проверка ГДУ двигателя осуществляется в процессе испытаний на закрытых стендах. Как правило, при этих испытаниях различными способами создается помпаж, а затем оцениваются эффективность работы противопомпажных средств (перепуска воздуха, скольжения роторов и других), время выхода на стационарный режим и другие параметры. Также в процессе стендовых испытаний выполняется проверка двигателя на стойкость к попаданию посторонних предметов (птиц, града, дождя). Перечисленные методы испытаний в настоящее время являются типовыми, в то время как испытания с боковым ветром выполняются сравнительно редко.
Для имитации бокового ветра однозначно требуется проведение испытаний двигателя на открытом стенде. Пример конструкции генератора бокового ветра, используемого на открытом испытательном стенде ОАО «НПО «Сатурн» в Полуево, представлен на рисунке.
Рис. Открытый испытательный стенд с генератором бокового ветра
352
Генератор представляет собой 12 вентиляторов лопастного типа с электродвигателями, размещенных на едином сварном корпусе, образующем аэродинамические каналы, камеру смешения потоков и сопло, в котором достигается требуемая скорость воздуха (ветра). Для подъема генератора и направления сопла используются гидравлические механизмы.
Такая конструкция обеспечивает скорость ветра в диапазоне 5–23 м/с, высокую точность позиционирования (угла атаки) и требуемую равномерность потока ветра даже в случае выхода из строя двух вентиляторов.
Технологический процесс испытаний с генератором бокового ветра с целью определения допустимых скоростей бокового ветра и работы противопомпажной системы включает следующие операции:
1.Определение параметров двигателя при отсутствии бокового ветра:
–продувка и тарировка измерительных линий (температур, давлений);
–прогрев двигателя на режиме малого газа;
–снятие дроссельной характеристики от режима малого газа до взлетного с регистрацией контрольных точек;
–останов двигателя.
2.Определение параметров двигателя при среднем боковом ветре (10 м/с):
–прогрев двигателя на режиме малого газа;
–установка генератора бокового ветра на требуемой высоте под углом 45° к оси двигателя и скорости ветра 10 м/с;
–снятие дроссельных характеристик от режима малого газа до взлетного с регистрацией контрольных точек при различных величинах перепуска воздуха (0–6 % с шагом 2 %);
–останов двигателя.
3.Определение параметров двигателя при сильном боковом ветре (21 м/с):
–прогрев двигателя на режиме малого газа;
353
–установка генератора бокового ветра на требуемой высоте под углом 45° к оси двигателя и скорости ветра 21 м/с;
–снятие дроссельных характеристик от режима малого газа до взлетного с регистрацией контрольных точек при различных величинах перепуска воздуха (0–6% с шагом 2 %);
–останов двигателя.
4. Анализ результатов испытаний (построение дроссельных характеристик компрессоров).
Проведенные по указанной методике исследовательские испытания ТРДД гражданского назначения с двухкаскадным компрессором позволили сделать следующие основные выводы:
1.Повышение скорости бокового ветра приводит к снижению границы помпажа как для компрессора низкого давления (КНД), так и для компрессора высокого давления (КВД). При скорости бокового ветра 10 м/с помпаж двигателя зафиксирован при уменьшении величины перепуска воздуха с 2 до 0 %. При скорости бокового ветра 21 м/с помпаж двигателя зафиксирован при уменьшении величины перепуска воздуха с 6 до 4 %.
2.Степеньповышениядавлениявкомпрессорах(КНДиКВД) практическинезависитотналичияискоростибоковоговетра.
3.Наличие бокового ветра приводит к значительному снижению (до 7 %) коэффициента полезного действия КНД. Влияние наКПДвеличиныперепускавоздухаприэтомнесущественно.
Библиографический список
1.Фадин С.С., Комов А.А. Влияние ветра на работу двигателей ПС-90А-76 на пробеге самолета ИЛ-76ТД-90 с применением реверса тяги // Научный вестник Московского государственного технического университета гражданской авиации. – 2014. – № 208. – С. 76–82.
2.ОСТ 1 02791–2010. Авиационный стандарт. Воздушные суда гражданской авиации. Документация по летной эксплуатации. Общие требования. Введ. 01.07.2011 / ФГУП «ЛИИ им. М.М. Громова», ФГУП «НИИСУ». – 84 с.
354
УДК 621
ОЦЕНКА ПРЕДЕЛЬНО-ЭФФЕКТИВНОЙ УПРОЧНЯЕМОСТИ ДЕТАЛЕЙ ДИНАМИЧЕСКИМИ МЕТОДАМИ ППД
В.А. Лебедев, С.Ю. Штынь, Г.С. Гомцян
Донской государственный технический университет, Ростов-на-Дону, Россия
e-mail: dstu@mail.ru.
Предложен расчетно-аналитический подход к оценке величины предельной твердости упрочненных поверхностных слоев, основанный на термодинамической теории прочности и разрушения твердых тел. На основе структурно-энергетической интерпретации процесса поверхностного пластического деформирования (ППД) получено уравнение, описывающее предельно допустимое значение твердости упрочненного слоя, обеспечивающее эффективное влияние на повышение эксплуатационных свойств деталей. Исходя из предположения, что величина предельной плотности скрытой энергии, накапливаемой в локальном микрообъеме поверхностного слоя в процессе его упрочнения, коррелирует с известной термодинамической характеристикой металлов, определяемой как разность энтальпии данного материала в твердом состоянии при температуре плавления и энтальпии при 293 К, получено выражение для оценки предельной твердости упрочненного поверхностного слоя.
Ключевые слова: упрочнение, поверхностный слой, твердость, скрытая энергия, энтальпия.
Основным параметром, используемым для оценки состояния качества поверхностного слоя материалов после упрочняющих обработок, оказывающим наиболее существенное влияние на повышение эксплуатационных свойств деталей машин, является его твердость. Однако, как следует из многочисленных исследований, для каждого материала существует оптимальная степень твердости наклепанного материала и дальнейшее упрочнение является нецелесообразным. Из этого следует, что для
355
предотвращения образования трещин и обеспечения повышенной работоспособности упрочненных поверхностей у изделий требуется применение комплексного подхода к оценке новых структурных состояний. В частности, требуется оценка локальной предельной деформации упрочненных слоев, связанной с релаксационной способностью, дефектностью, кинетикой распада разных метастабильных структур во времени и т.д.
Накопленный к настоящему времени теоретический и экспериментальный материал по исследованию влияния методов упрочняющей обработки на изменение физико-механических характеристик поверхностного слоя различных по марке и наименованию материалов позволяет предложить расчетно-анали- тический подход к оценке величины предельной твердости упрочненных поверхностных слоев, основанный на термодинамической теории прочности и разрушения твердых тел [1]. Из этой теории следует, что ответственной за упрочнение поверхностного слоя является величина потенциальной (скрытой) энергии, накапливаемой в нем в процессе обработки.
В соответствии с теорией дислокаций между плотностью скрытой энергии Е и интенсивностью напряжений i , возни-
кающих в зоне локального контакта индентора с обрабатываемой поверхностью, существует взаимная связь:
i2 6GE / K 2 , |
(1) |
где G – модуль сдвига; K – коэффициент, оценивающий сте-
пень перенапряжения на межатомных связях.
Результаты статистической обработки экспериментальных данных, приведенные в работе [2], позволяют представить обобщенную зависимость между твердостью и интенсивностью напряжения в виде
i 0,067HV1,2 , |
(2) |
356

а K с достаточной степенью точности определить по следующей формуле:
K |
1 |
, |
(3) |
1,2 10 3 6,47 10 6 HV |
где HV – твердость материала по Виккерсу.
О высокой степени универсальности полученных формул свидетельствует высокой коэффициент корреляции r = 0,956.
Установленный характер зависимости интенсивности напряжений от твердости HV представляет интерес с позиций возможности прогнозирования повреждаемости поверхностного слоя при упрочнении, а также для определения предельного
значения твердости упрочненного слоя HVпс* , при которой дос-
тигается наибольший эффект упрочнения с точки зрения повышения эксплуатационных свойств деталей.
Учитывая, что интенсивность напряжений i связана с
твердостью HV соотношением (2), из выражения (1) получим зависимость для оценки плотности скрытой энергии, накапливаемой в упрочняемом поверхностном слое в виде
|
|
|
|
|
|
|
|
E K |
пр |
HV2.4 |
, |
(4) |
|||
|
|
|
|
|
|
|
|
|
|
|
пс |
|
|
||
где |
Kпр |
1 |
|
|
|
|
|
1 |
|
|
|
|
2 |
– коэффициент, харак- |
|
|
|
|
|
|
|
|
|
|
|
|
|
|
|||
|
1,2 |
10 |
3 |
6,47 |
10 |
6 |
|
|
|||||||
|
|
6G |
|
|
HV |
|
|
теризующий прочностные свойства упрочняемого материала; HVпс – твердость поверхностного слоя, формируемого в про-
цессе упрочняющей обработки.
Согласно структурно-энергетический интерпретации процесса упрочнения наибольший эффект упрочняющей обработки достигается, когда плотность накопленной в поверхностном слое обрабатываемого материала скрытой энергии Е достигает предельной величины Е*. Тогда по уравнению (4) предельно допустимое значение твердости упрочненного слоя, обеспечивающее эффективное влияние на повышение эксплуатационных свойств деталей, составит:
357
HVпс* E* / Kпр 0,42 .
Если принять, что величина предельной плотности скрытой энергии Е*, накапливаемой в локальном микрообъеме поверхностного слоя в процессе его упрочнения, коррелирует с известной термодинамической характеристикой металлов, определяемой как разность энтальпии данного материала в твердом состоянии при температуре плавления HTS и энтальпии H293 при
293 К, то выражение для оценки предельной твердости упрочненного поверхностного слоя можно представить в виде
* |
|
|
0,42 |
, H HTS H293. |
HVпс H / Kпр |
|
Библиографический список
1.Лебедев В.А. Технология динамических методов поверхностного пластического деформирования. – Ростов н/Д: Изд.
центр ДГТУ, 2006. – 183 с.
2.Федоров В.В. Термодинамические аспекты прочности и разрушения твердых тел. – Ташкент: Изд-во ФАН, 1979. – 168 с.
358
УДК 621.438
ВОЗМОЖНОСТЬ ПРИМЕНЕНИЯ АДДИТИВНЫХ ТЕХНОЛОГИЙ В ЦЕНТРОБЕЖНЫХ КОМПРЕССОРАХ
Е.Л. Селянская, С.В. Касьянов, О.А. Мелузова
ПАО НПО «Искра», Пермь, Россия e-mail: iskra@iskra.perm.ru
Рассмотрена возможность применения аддитивных технологий (прототипирования) в узлах центробежных компрессоров. Приведены примеры изготовления рабочих колес и уплотнений ротора центробежного компрессора по технологиям литья по выжигаемой модели, стереолитографии (SLA) и селективного лазерного спекания (SLM). Указаны преимущества и недостатки изделий, изготовленных по аддитивным технологиям.
Ключевые слова: аддитивные технологии, центробежный компрессор, рабочие колеса, уплотнения.
Любая технология накладывает ряд ограничений на конструкцию изделия. В настоящее время на производственных площадях НПО «Искра» и его контрагентах проблематично или невозможно изготовить узкие рабочие колеса и уплотнения ротора типа сотовых, вследствиечегоприходитсяотказыватьсяотрядазаказов.
Для повышения конкурентоспособности центробежных компрессоров необходима технология изготовления ответственных узлов, которая позволила бы изготавливать из металлических, в том числе коррозионно-стойких, материалов сложнопрофильные изделия за относительно небольшой срок изготовления и стоимость по сравнению с существующими технологиями изготовления.
В качестве альтернативы рассматривается несколько видов аддитивных технологий:
литье по выжигаемой модели;
стереолитография (SLA);
селективное лазерное спекание (SLM).
359
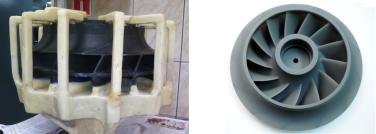
С применением технологии литья по выжигаемой модели изготавливается модельное колесо (рис. 1). Несмотря на недостатки изделия (пористость и внутренние дефекты, а также качество поверхности в части шероховатости), при времени изготовления, аналогичном времени изготовления по традиционной технологии, бесспорным преимуществом является стоимость производства – в три раза меньше. В связи с этим данная технология рассматривается только в качестве технологии изготовления колес для модельных испытаний.
В рамках НИР по технологии стереолитографии изготовлено модельное колесо из фотополимера Somos Next LV Grey (рис. 2). Несомненными преимуществами данной технологии являются точность изготовления, качество поверхности и время изготовления. Время 3D-печати без постобработки составило менее 60 ч, полный цикл изготовления (с учетом постобработки) – менее 72 ч. Несмотря на нестабильный курс доллара и то, что изготовление было осуществлено в Испании, стоимость колеса примерно в два раза меньше, чем стоимость сварного колеса.
Рис. 1. Выжигаемая модель |
Рис. 2. Модельное колесо, |
модельного колеса |
изготовленное по технологии |
с литниковой системой |
стереолитографии |
Технология селективного лазерного спекания (SLM) из-за ограничения рабочей зоны существующих установок рассматривается на примере изготовления уплотнений ротора типа сотовых.
360