
- •СОДЕРЖАНИЕ
- •ПРЕДИСЛОВИЕ
- •ОБЩИЕ СВЕДЕНИЯ
- •ВЫБОР МЕТОДА И СРЕДСТВА НАГРЕВА — ОСНОВНЫЕ ПОЛОЖЕНИЯ.
- •ВОПРОСЫ ЭКОНОМИКИ НАГРЕВА
- •НАГРЕВАТЕЛЬНОЕ ОБОРУДОВАНИЕ
- •Камерные нагревательные щелевые немеханизированные печи
- •Камерные нагревательные печи со стационарным подом с заслонкой
- •Нагревательные методические (кузнечные) печи
- •Щелевые механизированные конвейерные нагревательные печи
- •ТЕРМИЧЕСКОЕ ОБОРУДОВАНИЕ
- •Камерные термические тупиковые печи с выдвижным подом
- •Термические элеваторные печи
- •Вакуумные элеваторные электропечи
- •Термические пламенные ямные печи
- •Электрические ванные печи (электрованны)
- •Термические барабанные печи непрерывного действия (шнековые)
- •w ^litr
- •Индукционные закалочные установки
- •АВТОМАТИЗАЦИЯ ПЕЧЕЙ
- •Закалочные баки
- •Моечные машины
- •Камеры охлаждения
- •ЛИТЕРАТУРА
АВТОМАТИЗАЦИЯ ПЕЧЕЙ
АВТОМ АТИЗАЦИЯ ТЕПЛОВОГО РЕЖ ИМ А
Тепловой режим автоматизируют для того, чтобы обеспечить поддержание необходимой температуры и равномерности нагрева садки, экономичное использование источника тепла, безопасную работу средства нагрева.
В пламенных печах [16 с. 16, 40—54] регулируют следующие основные параметры:
температуру рабочего пространства печи; давление в рабочем пространстве печи; соотношение топливо—воздух.
Кроме того, на всех печах обычно предусматривают контроль таких важных параметров теплового режима, как температура дымовых газов на выходе из печи и воздуха (в случае его нагрева в рекуператорах), давление газа и воздуха у горелок и в общем коллекторе, расход топлива и воздуха (последний измеряют в слу чае использования регулятора соотношения).
Помимо этого предусматривается подготовка топлива:
а) при отоплении газом крупной отдельно стоящей печи уста навливают фильтр и регулятор давления газа (для группы не больших печей, питаемых от газораспределительного пункта (ГРП), эту аппаратуру можно не устанавливать). Оптимальным решением, особенно при использовании жесткой связи регулиру ющих органов, является установка индивидуального регулятора давления газа и вентилятора на каждую печь, так как колебания давления газа и воздуха в общецеховых коллекторах могут ухуд шать настройку системы регулирования теплового режима. Если это по каким-либо причинам невозможно, необходимо предусмо треть регуляторы давления газа и воздуха на цеховых коллекто рах, питающих автоматизированные печи;
б) при отоплении мазутом для печи в целом или для каждой зоны крупной печи предусматривают узел мазутоподготовки, состоящий из фильтра, регулятора давления и регулятора тем пературы подогрева мазута.
Система безопасности на печах, отапливаемых газом, предусма тривает установку предохранительных клапанов, автоматически прекращающих подачу газа как при повышении, так и при падении давления газа и воздуха сверх (ниже) установленного предела. На низкотемпературных печах, отапливаемых мазутом, также предусматривается автоматическая отсечка топлива при падении давления воздуха.
В качестве датчиков температуры для регуляторов исполь зуют: при температуре рабочего пространства печи до 1000° С —
хромель-алюмелевые термопары, до 1300° С — платинородий-пла- тиновые термопары, свыше 1300° С — платинородиевые термопары или радиационные пирометры. Применяемые регуляторы и регу лирующие органы указаны ниже. Исполнительные механизмы принимают в большинстве случаев с электрическим приводом.
На термических печах периодического действия, в которых допускается незначительное отклонение температуры от заданной графиком термообработки и требуется большая равномерность нагрева садки, особенно в конце выдержки, устанавливают регу ляторы температуры с программным задатчиком, общим для всей печи. При этом используют регуляторы типов ПИ, ПИД и им пульсные; последние могут быть применены при отсутствии воз мущений течения процесса. Двухпозиционными регуляторами не пользуются, поскольку на этих печах диапазон изменения расхода топлива широк и эти регуляторы могут дать большую статическую ошибку. Применение их допустимо только в специализированных термических печах при небольших колебаниях расхода топлива.
В зависимости от габаритов рабочего пространства, вида садки и конструктивных особенностей термические печи перио дического действия можно условно разделить на зоны с самостоя тельным регулированием температуры. При таком делении печи учитывают теплотехнические особенности тех или иных частей рабочего пространства и взаимное влияние регуляторов соседних зон для того, чтобы обеспечить заданное качество регулирования во всех зонах многозонной печи.
Регуляторы температуры воздействуют с помощью исполни тельных механизмов на регулирующие органы — Поворотные заслонки типов ЗМС и ПРЗ и краны типа КР. Краны используют на всех печах, отапливаемых мазутом, а также на печах, отапли ваемых газом при малых расходах топлива.
Регулирование давления в рабочем пространстве термических печей периодического действия осуществляется с помощью регу ляторов типа И и ПИ. В связи с изменением расходов и темпе ратур в широких пределах отбор импульса давления необходимо осуществлять на уровне подины. Поддержание при регулировании заданного нулевого или небольшого положительного давления на этом уровне препятствует проникновению холодного воздуха в рабочее пространство. Отбор импульса давления под сводом в этих печах не рекомендуется, так как при изменении темпера туры меняется разность давлений по высоте печи.
Ликвидация подсосов через неплотности печи основная задача регулятора давления на термических печах периодического действия. Печи периодического действия для регулирования давления в рабочем пространстве не делят на зоны нез^Ьисимо от числа применяемых регуляторов температуры. Это объясняется большой скоростью выравнивания давления в предела* рабочего пространства. Регулятор давления через исполнительный меха
низм воздействует на органы, изменяющие давление в рабочем пространстве: шибер, установленный в дымовом борове, или заслонку, изменяющую подачу воздуха (вентиляторного или атмо сферного) в дымосливные каналы печи.
Автоматическое поддержание заданного соотношения топливо— воздух в печах этой группы осуществляется как с помощью регу ляторов соотношения непрерывного действия типа И, основанных на пропорциональных изменениях расходов топлива и воздуха, так и применением механической связи регулирующих органов на трубопроводах топлива и воздуха. В обоих случаях предусматри вается также возможность быстрого изменения коэффициента рас хода воздуха. Это особенно важно, когда таким способом дости гается более равномерный нагрев садки. В этом случае задача экономного сжигания топлива отступает на второй план.
На рис. 130 в качестве примера дана принципиальная схема контроля и регулирования печи с выдвижным подом, предназна ченной для термической обработки ответственных изделий слож ной конфигурации. Печь отапливается с помощью рециркуля ционных горелок (расход воздуха для рециркуляции не регули руется). Температуру регулируют программным многоканальным импульсным регулятором (последовательное включение двух позиционных регуляторов с остающимися контактами и преры вателя импульсов) по показаниям сводовых термопар с меняющейся глубиной погружения.
Печь разделена на три зоны регулирования температуры. Исполнительные механизмы, обслуживающие горелки про
тивоположных сторон одной зоны, связаны между собой следя щим устройством. Давление на уровне пода печи также регули руется путем воздействия на поворотный шибер борова.
Соотношение топливо—воздух на горелках обеспечивается жесткой связью органов, регулирующих подачу топлива и воз духа.
Для регулирования температуры в нагревательных печах, к которым предъявляются менее жесткие требования в отношении точности поддержания температуры и равномерности нагрева из делий, преимущественно рекомендуются позиционные регуляторы (больше—меньше) как наиболее простые и удовлетворяющие тре бованиям технологии. Применение регуляторовнепрерывного действия, в особенности при частых возмущениях и нестабильном коэффициенте передачи объекта, неоправдано. Сложные регуля торы непрерывного действия обеспечивают практически такое же качество регулирования температуры, как и простые двухпози ционные. Позиционные регуляторы обычно соответствуют также динамическим свойствам данных печей.
Меньшая требовательность к точности поддержания темпера туры по сравнению с термическими печами и лучшее выравнива ние температуры в рабочем пространстве печи позволяют ограни-
Загрузка
/олькс
изперение
Рис. 130. Принципиальная схема теплового контроля и автоматики циркуляционной термической печи с выкатным подом:
/ — вентилятор; II — рекуператор; III — верхняя горелка; IV — нижняя горелка; 1—40 — номера линий; А — программный задатчик; Б — потенциометр с позиционным многоканальным регулятором; В — прерыватель импульсов; Г — следящее устройство; Д — потенцио метр многоточечный показывающий; Е — датчик расхода или давления; Ж — вторичный прибор; 3 — регулятор непрерывного действия; И — задатчик; К — переключатель; Л — показывающий прибор; М — сигнализатор падения давления; Н — гудок; О — сигнальная лампа
читься одним регулятором температуры даже на сравнительно крупных печах этой группы.
Задача поддержания оптимального соотношения топливо— воздух и заданного давления в рабочем пространстве решается также применением простейших средств — механической и элек трической жесткой связи регулирующих органов.
На рис. 131 показана схема автоматизации камерной кузнеч ной печи, отапливаемой мазутом. Температура в печи регули руется при помощи сводовой термопары, воздействующей на рас ход топлива и воздуха для горения с помощью двухпозиционного регулятора. Регулирующие органы на трактах топлива и воздуха установлены для каждой форсунки отдельно для того, чтобы обеспечить равномерное распределение мазута. Регулирующие органы связаны с исполнительным механизмом валом. Одновре: менно с изменением расходов топлива и воздуха изменяется поло-
Рнс. 131. Принципиальная схема теплового контроля и автоматики камерной кузнечной печи;
1 — 14 — номера линий; |
П — одноточечный потенциометр с позиционным регулятором; |
Р — милливольтметр; |
С — звонок; остальные обозначения те же, что и к рис. 130 |
жение дымового шибера, управляемого отдельным исполнитель ным механизмом, получающим команду от того же регулятора. Крайние положения шибера выбраны так, чтобы давление в печи при минимальном и максимальном расходах топлива оставалось стабильным. Давление мазута регулируется регулятором прямого действия, а температура мазута — позиционно, включением элек трических нагревателей при помощи контактного манометриче ского термометра.
Механизмами печей периодического действия обычно управ ляет оператор, пользуясь ключами дистанционного управления. Это обусловлено тем, что операции загрузки и выгрузки изделий в этих печах осуществляют через неравномерные промежутки времени.
Термические печи непрерывного действия в отношении регули рования температуры отличаются относительно стабильными коэффициентами передачи и динамическими характеристиками, допускающими применение как непрерывных регуляторов типа П, ПИ, ПИД, так и позиционных регуляторов (во многих случаях). В этих условиях хорошее качество регулирования обес печивают не только непрерывные, но и двухпозиционные регуля торы, так как получающаяся при этом статическая ошибка нахо дится в пределах, допустимых при термической обработке.
Применение двухпозиционных регуляторов на этих печах целесообразно также и по следующим причинам. Печи непрерыв ного действия делят на зоны регулирования температуры, исходя из условий обеспечения заданного графика термообработки по длине печи и взаимного влияния регуляторов соседних зон. Таких зон может быть несколько. При использовании позицион ного регулирования может быть установлен один многоканальный позиционный регулятор температуры, выполняющий разные за дачи по каналам регулирования. При непрерывном же регулиро вании число регуляторов должно быть равно числу зон регулиро вания, что значительно усложняет эксплуатацию системы авто матики.
На печах, где часто происходят возмущения, связанные с за грузкой и выгрузкой изделий, регуляторы непрерывного дей ствия не обеспечивают требуемого качества регулирования. Едва регулятор успевает зарегулировать предыдущее возмущение, как возникает новое. Двухпозиционные регуляторы в этих условиях быстрее справляются с возмущениями и дают лучшее приближение средней температуры к заданной. Эти обстоятельства не исклю чают, однако, применения непрерывных регуляторов температуры на некоторых термических печах непрерывного действия. Они Могут, например, обеспечить хорошее качество регулирования на печах с малыми возмущениями. Однако непрерывные регуляторы не следует устанавливать там, где с задачей поддержания заданной температуры могут справиться простые позиционные регуляторы.
На печах непрерывного действия в связи с незначительными колебаниями расхода топлива можно устанавливать форсунки низкого давления и инжекционные горелки; при использовании последних можно применять электромагнитные клапаны, выпол няющие одновременно роль исполнительного механизма и регу лирующего органа.
Регулирование давления в рабочем пространстве осуще ствляется воздействием на дымовой шибер или на заслонку, изме няющую подачу воздуха в дымосливные каналы. Поддержание заданного давления в многозонных печах осуществляется с по мощью регулятора непрерывного действия типа ПИ независимо от типа применяемых регуляторов температуры. Это объясняется тем, что изменение количества продуктов сгорания при работе отдельных регуляторов температуры составляет небольшую долю всего объема дымовых газов в печи, вследствие чего колебания давления в рабочем пространстве незначительны. На однозонных печах возможно применение тех же средств поддержания давления, которые используют на нагревательных печах периодического действия. Число регуляторов давления на печах непрерывного действия зависит от конструкции печи. Если печь состоит из не скольких камер с самостоятельными отводами дымовых газов в боров, давление регулируется в каждой камере. В связи с незна чительными колебаниями температуры и расхода в печах непре рывного действия импульс давления для регуляторов можно от бирать в любом месте.
Автоматическое поддержание заданного соотношения топливовоздух осуществляется механической связью регулирующих ор ганов на трубопроводах топлива и воздуха либо установкой конеч ных выключателей на исполнительных механизмах, раздельно управляющих подачей топлива и воздуха. Применение регуля торов соотношения расходов на многозонных агрегатах затруд нительно, а при двухпозиционном регулировании температуры — нецелесообразно.
На рис. 132 приведена схема автоматизации проходной терми ческой печи, отапливаемой газом. Печь разделена на восемь зон регулирования температуры не только по длине, но и по ширине (печь, предназначенная для обработки широких тонких заготовок, характеризуется большой шириной при незначительной высоте рабочего пространства). Температура регулируется с помощью многоканального двухпозиционного регулятора с различными задачами по отдельным каналам регулирования. Термической об работке подвергаются ответственные изделия, поэтому регулиру ющие термопары дублируются измерительными. Регулируется также давление в рабочем пространстве печи, причем регулятор воздействует на два шибера (дымовые газы удаляются по двум боровам). Синхронизация работы электрических исполнительных механизмов, управляющих этими шиберами, достигается исполь
зованием следящего устройства. Для регулирования давления газа применяют регулятор непрямого действия, поскольку печь питается газом от цехового коллектора низкого давления.
Для регулирования температуры нагревательных печей не прерывного действия, допускающих нагрев заготовок с максималь ной скоростью, может быть использован многоканальный пози ционный регулятор, работающий с одной задачей для всех каналов регулирования. При применении такого регулятора облегчается также изменение задания при переходе печи с нагрева одних за готовок на нагрев других. При равных габаритах рабочего про странства число зон регулирования 'на нагревательных печах может быть меньше, чем на термических. Кроме того, из нагрева тельных печей по различным причинам довольно часто прекра щается выдача заготовок, что учитывается введением режима холостого хода; это обстоятельство особенно важное значение имеет для печей безокислительного нагрева.
На рис. 133 приведена принципиальная схема автоматизации теплового режима методической кузнечной печи безокислитель ного нагрева. Печь, отапливаемая природным газом, с желобча тым подом предназначена для безокислительного нагрева открытым пламенем заготовок под ковку. На этой печи приборами для сжи гания топлива служат две горелки низкого давления, установлен ные в торцовой стене на стороне разгрузки.
В методической зоне, где господствует наивысшая температура (1450° С), а = 0,5, что позволяет получить безокислительную атмосферу. Вторичный воздух, подаваемый в сварочную зону печи с температурой ~900° С, служит для дожигания топлива при а = 1. При прекращении выгрузки,изделий (холостой ход) печь переводится на минимальный расход топлива, вторичный воздух в печь не подается и во всей печи создается безокислительная атмо сфера, что предохраняет заготовки от окисления при длительном пребывании их в печи. В этом случае весь вторичный воздух подается в коллектор третичного воздуха, чтобы дожечь все топ ливо при а = 1 в камере дожигания и предохранить рекуператор от пережога.
В печи предусматривается двухпозиционное регулирование температуры по показаниям радиационного пирометра в методи ческой зоне. Регулятор воздействует одновременно на исполни тельные механизмы, управляющие расходом газа, первичного, вторичного и третичного воздуха, а также на исполнительный механизм, перемещающий дымовой шибер. Крайние положения исполнительных механизмов выбирают так, чтобы в рабочем про странстве печи устанавливались необходимый состав атмосферы и одинаковое давление при минимальном и максимальном расходе топлива. Для перевода печи на режим холостого хода используют те же исполнительные механизмы, а также исполнительный ме ханизм, переключающий вторичный воздух.
to
о
*
Рис. 132. Принципиальная схема теплового контроля и автоматики проходной термической печи:
/ — рекуператор; II — вентилятор; III — механизм загрузки; IV — шибер; V — горелка; VI — механизм выгрузки; 1—63 — номера линий. Обозначения те же, что и к рис. 130, 131
|
Условные обозначения-. |
|
Г ------ |
f - |
природный газ |
-В1-------- |
* - |
воздух первичный |
-В 2-------- |
* - |
воздух вторичный |
-ВЗ-------- |
* - |
воздух третичный |
-ВН-------- |
1 - |
воздух горячий первичный |
-вГ2-------- |
1 - |
воздух горячий вторичный |
-ДГ------ |
* - |
дымовые газы |
Рис. 133. Принципиальная схема теплового контроля и автоматики методической кузнечной печи безокислительного нагрева'металла: / — вентилятор; I I — рекуператор; I I I — печь; 1 — 3 0 — номера линий; Т — многоточечный^ потенциометр с сигнальным контактом,
остальные обозначения те же, что и к рис. 130
Автоматическое регулирование электротермических установок для нагрева и термической обработки в машиностроении приме няется как для управления температурным режимом электропечей сопротивления и некоторых индукционных установок, так и для управления электрическим режимом последних [4, с. 16—18 и 57].
Поддержание на постоянном уровне с необходимой точностью заданной температуры рабочего пространства электропечи осу ществляется путем изменения количества потребляемой ею элек троэнергии, что может быть достигнуто плавным или ступенчатым изменением мощности электропечи.
Методы, обеспечивающие плавную регулировку мощности, сложны и связаны либо с понижением коэффициента полезного действия, либо коэффициента мощности электропечи и поэтому их применяют редко. При использовании этих методов последова тельно с электропечью включают сопротивление — активное (рео стат с регулируемым сопротивлением) или индуктивное (регули руемый дроссель насыщения).
Регулирование мощности изменением величины питающего напряжения путем применения трансформаторов и автотрансфор маторов с переключателями ступеней напряжения находит при менение лишь для электропечей с неметаллическими электронагре вателями (карборундовыми, силитовыми и др.) и соляных элек тродных ванн.
Регулирование мощности переключением обычно отдельных групп электронагревателей нередко применяют в однофазных электропечах путем переключения их с параллельного соединения
на |
последовательное с уменьшением мощности данной группы |
в |
4 раза, в трехфазных электропечах — путем переключения |
с треугольника на звезду с уменьшением мощности данной группы в 3 раза.
Автоматическое регулирование температуры в электропечах сопротивления достигается применением обычно релейных двухили трехпозиционных регуляторов, реже импульсных и регуля торов непрерывного действия. Схема двухпозиционного регулиро вания температуры электропечи сопротивления с блоком питания на магнитных усилителях приведена на рис. 134.
Релейные регуляторы для позиционного, главным образом двухпозиционного, регулирования температуры из-за своей про стоты получили наибольшее распространение. Однако при приме нении позиционного регулирования в целях повышения долговеч ности коммутирующей аппаратуры и улучшения показателей ре гулирования рекомендуется уменьшать как частоту, так и ампли туду колебаний температуры. Учитывая значительную инерцион ность большинства электропечей сопротивления и применяемых конструкций термопар, уменьшения частоты и амплитуды колеба ний температуры можно было бы достигнуть уменьшением избытка
Рнс. 134. Схема двухпозиционного регулирования температуры электропечи сопротивле ния с блоком питания на магнитных усилителях:
СМ У — силовой магнитный усилитель (например типа УСО); ПМУ — промежуточный магнитный усилитель (например, типа ТУМ); 10У — обмотка смещения; 20У — управ ляющая обмотка; ЗОУ — обмотка отрицательной обратной связи по напряжению H at'pe-
вателя; ТР-1, ТР-2 — трансформаторы питания цепей смещения; ТР-3 — трансформатор питания цепей обратной связи; ТР — электронный потенциометр; К — минимальным контакт регулирующего устройства электронного потенциометра; JR—4R — сопротивле ния для подрегулировки тока смещения; 5R — 6R — то же, токов обратной связи; 8R — 9R — то же, тока управления; I — термопара; 2 — электропечь; 3 — нагреватель
мощности. Однако такое уменьшение избыточной мощности при вело бы к увеличению времени разогрева и противоречило бы современной тенденции достигать в ряде случаев так называемого «скоростного нагрева», когда именно избыточная мощность спо собствует созданию в первых зонах нагрева значительного пере пада температур рабочего пространства й садки. Поэтому наиболее рациональным в таких случаях является трехпозиционное регу лирование, при котором при разогреве осуществляется регули рование по принципу «вся мощность» или «частичная мощность», а при выдержке — по принципу «частичная мощность» или «все отключено» вместо только «вся мощность» или «все отключено» при двухпозиционном регулировании.
Регулирование частоты включенной мощности может быть совмещено с автоматическим регулированием температуры термо регулятора или осуществлено с помощью постоянно вращающегося импульсного барабанного прерывателя, обеспечивающего возмож ность изменения частоты и продолжительности циклов включения и отключения электропечи. Чем больше будет частота таких циклов, тем ближе импульсное регулирование будет приближаться к непрерывному.
Таким образом, применение регуляторов непрерывного дей ствия, обеспечивающих высокую точность заданной температуры
310
путем плавного регулирования подводимой мощности, целесооб разно лишь применительно к малоинерционным электропечам, в которых теплоемкость изделий значительно превышает теплоем кость средств нагрева, и применительно к электропечам* в которых необходимо регулирование температуры по строго заданной программе и, наконец, в случаях осуществления скоростных методов нагрева деталей или заготовок, когда используются боль шие удельные мощности.
В целях резкого снижения (в 10—15 раз) значительного пере пада температуры на электронагревателях, достигающего при применении двухпозиционного регулирования до ±20-^40 град, рекомендуется применять голые термопары со снятыми чехлами и наконечниками с установкой их таким образом, чтобы место горячего спая находилось у самого электронагревателя. Такой же результат может быть в случае необходимости достигнут и при применении фиксированного на электронагревателе радиацион ного пирометра.
Усилительной частью систем бесконтактного регулирования температуры электропечей сопротивления являются блоки пи тания БПМ, предназначенные для непрерывного и позиционного контактного регулирования в системах, отвечающих повышенным требованиям к температурному режиму и надежности.
Блоки питания БПМ выпускаются 9 типоразмеров для:
1) однофазной нагрузки при напряжении 220 в мощностью от 0,375 до 96 квт\ 2) трехфазной нагрузки при напряжении 380 в мощностью от 1,125 до 288 кет.
Блоки питания выполнены полностью бесконтактными на стан дартных элементах с отрицательными обратными связями по напряжению нагрузки, что обеспечивает обработку основного возмущения — колебания напряжения сети в контуре усиления без существенного влияния на температуру электропечи.
Выходной сигнал блока составляет 0—20 ма, величина нагрузки 1250 ом, точность стабилизации 1,5—2% (по среднему значению) при колебаниях напряжения в пределах + 5 —15 в.
Блок питания может работать совместно с прецизионным регулятором температуры АПР завода «Лентеплоприбор» или с регулятором на основе потенциометра ЭППЛ/10, обеспечивая точность стабилизации не ниже ±0,25-^ ±0,5 град/
Блок питания состоит из подавителя нуля ПТ-1, узкопредель ного измерительного и записывающего потенциометра ЭПП-49, регулирующего непрерывного устройства типа РУ4-11.
При позиционном регулировании используется ЭПП-09-1/10 с выходным позиционным устройством, которое непосредственно управляет блоком питания.
При непрерывном регулировании потенциометр ЭПП-09-1/10 с реостатным датчиком на выходе соединяется с регулирующим устройством РУ4-11. Аналогично этому в системе регулирования
совместно с блоком питания может быть применен любой потен циометр ЭПП, ЭПД, ПСР и др.
Блоки питания на магнитных усилителях сравнительно дороги и отличаются значительными габаритами, поэтому появилась тенденция заменить их в ряде случаев кремниевыми управляемыми вентилями-тиристорами.
Автоматическое регулирование электрического режима индук ционных закалочных установок повышенной частоты обычно сводится к использованию возможности непрерывного регулиро вания напряжения генератора повышенной частоты и за счет этого непрерывного поддержания оптимального значения силы тока.
Система регулирования индукционных закалочных установок повышенной частоты может быть наилучшим образом осуществлена или совместным применением регулятора коэффициента мощности и регулятора напряжения генератора повышенной частоты (регу лирование возбуждения с отсечкой по току), или изменением числа витков индуктора.
Так как цикл нагрева в индукционных закалочных установках обычно измеряется секундами, то системы регулирования этих уста новок отличаются быстродействием и в них применяют магнитные усилители с минимальными собственными постоянными времени.
В результате достигаемого при регулировании постоянства напряжения на индукторе обеспечивается более интенсивный нагрев закаливаемого изделия в результате повышения средней за цикл мощности и сокращается общее время нагрева.
Для определенного типа изделий при условии стабилизации напряжения можно цикл нагрева ограничить по времени и, введя в схему автоматики реле времени, обеспечить своевременное отключение главного контактора и возвращение схемы автоматики в исходное положение для следующих циклов нагрева.
Схема автоматического управления нагревом с помощью реле дозирования высокочастотной энергии, работающего по принципу индукционного ваттметра и исключающего влияние колебаний напряжения и частоты генератора, разработана Всесоюзным научно-исследовательским институтом токов высокой частоты, однако промышленного распространения еще не получила.
Помимо регулирования электрических параметров индукцион ных закалочных установок, применяют обычно выполненные на бесконтактных магнитных элементах индивидуальные системы автоматического управления такими отдельными технологическими операциями, как подача изделий в индуктор, перемещение и выдача изделий, управление спрейерным охлаждением и др.
Автоматическое регулирование индукционных установок для нагрева заготовок под обработку давлением предусматривает
восновном возможно более равномерный их прогрев по сечению
стем, чтобы перепад температур между поверхностью и центром заготовки не превышал 80—100 град.
В нагревательных установках непрерывного действия при за ранее установленном оптимальном значении скорости нагрева можно ограничиться стабилизацией напряжения на индукторе или силы тока в нем. В нагревательных установках периодического действия, когда параметры контура изменяются в процессе дли тельного нагрева, может оказаться целесообразным также и авто матическая стабилизация мощности.
При сильных колебаниях напряжения питающей сети нагрева тельные установки включают через автотрансформатор, управ ляемый регулятором по напряжению. Необходимая длительность нагрева устанавливается на реле времени, которое отключает индуктор по окончанию заданного периода, или определяется автоматически по температуре поверхности заготовки, измеряемой обычно с помощью фотоэлектрического пирометра.
Системы автоматического управления отдельными технологи ческими операциями нагревательных установок, аналогично зака лочным установкам, являются индивидуальными и проекти руются отдельно для каждого технологического процесса.
Для автоматизации вновь проектируемых или действующих индукционных нагревательных установок промышленной и повы шенной частоты могут быть применены типизированные автомати ческие регуляторы типа АРИК, АРИС и АРИВ.
Автоматические регуляторы коэффициента мощности индукци онных нагревательных установок типа АРИК (зона чувствитель ности ±3%) выпускают четырех типоразмеров: АРИК-16-5; 32-6; 32-9 и 64-10, где первая цифра означает число регулируемых сту пеней емкости и вторая — число исполнительных контакторов.
Автоматические регуляторы симметрии нагрузки по фазам
типа |
АРИС выпускают |
трех типоразмеров — АРИС-4; 8 и 16, |
где 4, |
8 и 16 — числа |
ступеней реактивных сопротивлений. |
Автоматические регуляторы возбуждения машинных генера торов повышенной частоты АРИВ с точностью поддержания напря жения установок индивидуального питания ±2% , централизо ванного ± 1 % и глубиной регулирования напряжения 1 10 и 1 : 2 соответственно выпускают трех типоразмеров на силу тока возбуждения не более 20, 50 и 100 а — АРИВ-1И, 2И и Ц2; где И —
индивидуальное, Ц — централизованное питание; 1—100 в, 2— 200 в.
АВТОМ АТИЗАЦИЯ УПРАВЛЕНИЯ МЕХАНИЗМАМИ
Цель автоматизации управления механизмами заключается в обеспечении заданной последовательности операций по загрузке, транспортировке и выгрузке обрабатываемых изделий.
В качестве характерного примера ниже приводится общее описание системы автоматического управления механизмами за- калочного-отпускного агрегата, включающего следующее обору дование: проходную толкательную пламенную п§чь с размерами
^оператора |
|
Время, |
|
|
|
сен |
|
1 |
1ш |
6 |
|
? |
N |
|
4.5 |
3 |
я |
|
Н-7 |
4 |
JIJ |
|
9.8 |
5 |
IF |
|
6,2 |
6 |
а |
|
7,0 |
7 |
ч |
|
9,5 |
8 |
л |
|
9,7 |
9 |
w |
|
8,3 |
10 |
7 |
|
6.2 |
JJ |
ш |
|
3,0 |
12 Ш |
|
6,0 |
|
и |
ш |
|
и |
ы |
ш |
|
9,9 |
15 |
ш |
|
4,7 |
16 |
ш |
|
6,2 |
17 |
ш |
|
4,0 |
18 |
ш |
|
9.5 |
19 |
X |
35,1 |
|
20 |
X |
29,9 |
|
21 |
в _ |
|
6,2 |
22 |
ш |
|
2,6 |
23 |
XS |
|
4,0 |
24 хш |
|
8,0 |
|
25 хш |
|
5.1 |
|
26 П |
jn Q |
||
1U, L |
|||
■27 |
I |
10,2 |
|
28 Е |
10.0 |
||
19 |
I |
|
9,0 |
|
|
|
|
|
|
|
|
|
|
в р е м я , се к |
|
|
|
0 |
|
|
|
|
700 |
|
|
|
200 |
|
300 |
900 |
|
|
|
|
|
|
|
I |
______________________________________ I__________________________________I__________________________________ I_____ |
||||||
|
|
|
|
1 |
|
|
• Ss |
|
§ |
|
|
|
|
|
|
|
|
Ч |
1 |
|
1 |
§ |
1 |
— Темп оьшачи not>ооноо / мин |
|
|
|
|
|
|
/ |
7------------- ------- |
|
& |
^ |
^ |
|
|
|||
|
------------- |
|
------------- — |
|
|
^ |
|
|
|||||
|
|
|
|
|
Ц |
1 |
^ |
& |
§ |
|
|
|
|
|
|
X |
|
|
r S |
Vj |
|
|
|
|
|
||
|
|
|
|
h |
! |
§ |
! |
|
|
|
|
||
|
' § |
? |
М |
- |
|
|
|
|
|
|
|
|
|
|
M l |
|
|
l— 1 S |
S s ' § |
|
|
|
|
||||
|
1 |
ч |
* |
|
|
|
“H |
|
tv. |
|
|
|
|
|
|
|
|
|
|
|
|
1 |
^ |
|
|
|
|
|
|
|
|
|
H?4trp,/ |
|
Ц |
%f |
Дпрмя ?at/Qг! |
|
|
||
|
|
|
|
|
|
|
|
'£>) |
H-3чин |
||||
. |
S |
i |
s |
|
\JUffuCrt |
|
|
|
|
|
|
|
|
|
|
|
|
|
L _ |
|
|
|
|
||||
|
^ |
|
и |
|
|
|
|
|
|
|
|
|
|
|
|
|
____________________________________________________ _ П ______________________________________________________ |
|
|
||||||||
|
^ |
|
V |
|
|
|
|
|
L |
|
XV7 Опои |
__ Время Вь/держни (переменно?) |
|
. |
¥ |
1 < |
? |
|
|
|
|
|
|
LiL |
_ VUfUOCn |
||
|
|
|
|
|
1 |
|
|
пореле времени |
|||||
|
|
|
|
|
|
|
|
|
|
|
|||
|
|
|
|
|
|
|
|
|
|
|
|
|
|
h |
1 Х О и и |
|
|
|
|
|
|
l1 |
|
|
|
||
|
|
|
|
|
|
|
1# |
|
|
|
|
||
|
|
|
|
|
|
|
|
Отлютие насоса |
|
|
|
||
|
|
|
|
|
|
|
|
1 ^ noреле Времена |
|
|
|
||
|
Время передамtnnrnp Qm/nnt/it |
|
|
|
Выдержна Оман |
|
|
|
|||||
|
|
|
|
^ 1 |
1 |
|
|
||||||
|
В отлуснную т?Vb |
|
|
|
|
|
|
|
|||||
|
|
|
|
|
|
|
|
|
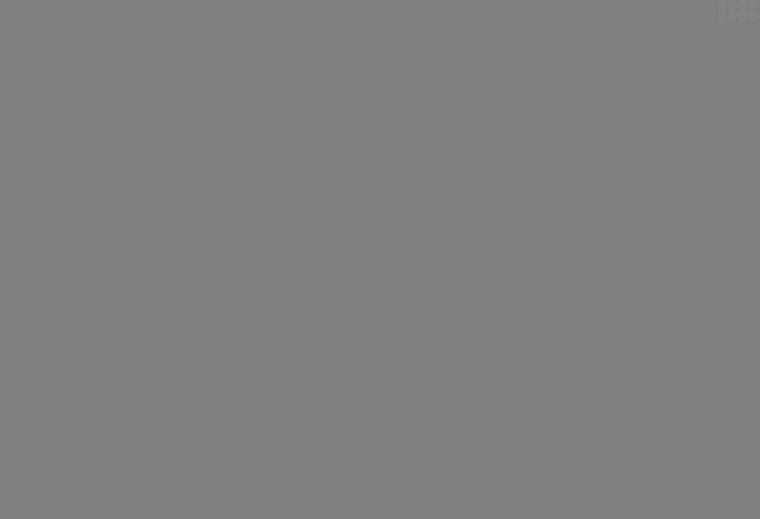
№ |
Наименование операции |
|
операции |
||
|
8Толкатель-выталкиватель закалочной печи «из печи»
9Стол закалочного бака «В» «вниз»
10Заслонка выгрузки закалочной печи «вниз»
11Заслонки спрейерного устройства «вверх»
12Толкатель—выталкиватель спрейера «в печь»
13Заслонка выгрузки отпускной печи «вверх»
14Толкатель—выталкиватель спрейера «из печи»
15Заслонки спрейерного устройства «вниз»
16Заслонка выгрузки отпускной печи «вниз»
17Опрокидыватель «вверх»
18Заслонка загрузки отпускной печи «вверх»
19Ход толкателя отпускной печи «в печь»
20 |
» |
» |
» |
» «из печи» |
21Заслонка загрузки отпускной печи «вниз»
22Опрокидыватель «вниз»
23Подъемник выхода «вверх»
24Сталкиватель «вперед»
25 |
» |
«назад» |
26Подъемник выхода «вниз»
27входа «вверх»
28Работа цепного переталкивателя «ход вперед на 1 шаг»
29Подъемник входа «вниз»
Срабатывают элементы гидропривода
тип |
Q, л/мин |
р, Мк/ж* |
4Г73—44 |
70 |
12,5 |
5Г73—44 |
70 |
12,5 |
КДП—20Р |
70 |
20,0 |
4Г73—44 |
70 |
12,5 |
4Г73—44 |
70 |
12,5 |
4Г73—44 |
70 |
12,5 |
4Г73—44 |
70 |
12,5 |
4Г73—44 |
70 |
12,5 |
4Г73—44 |
70 |
12,5 |
4Г73—44 |
70 |
12,5 |
4Г73—44 |
70 |
12,5 |
4Г73—44 |
70 |
12,5 |
4ПГ73 |
140 |
8,0 |
4ПГ73 |
140 |
8,0 |
4Г73 |
70 |
12,5 |
4Г73 |
70 |
12,3 |
5ПГ73—35 |
140 |
8,0 |
,[К ДП -25Р |
100 |
200 |
4Г73—44 |
70 |
12,5 |
4Г73—44 |
70 |
12,5 |
! 5ПГ73—35 |
140 |
8,0 |
КДП—25Р |
100 |
200 |
5ПГ73—35 |
140 |
8,0 |
* К ДП -25Р |
100 |
2000 |
i |
Электрический |
|
5ПГ73—35 |
140 |
8,0 |
КДП—25Р |
100 |
2000 |
пода 6,96x2,32 м для нагрева изделий под закалку с двумя за слонками, расположенными с торцов печи; проходную толкатель ную пламенную печь с размерами пода 9,41x2,32 м для отпуска изделий с двумя заслонками, расположенными с торцов печи; два толкателя, предназначенные для продвижения заготовок в пе чах; два вытаскивателя, предназначенные для выгрузки заготовок из печей; закалочный водяной бак с отпускным столом для погру жения поддонов с изделиями в бак; спрейерную установку; ме ханизм возврата поддонов, включая подъемники поддонов на выходе из агрегата и на входе в него; опрокидыватель поддонов и сталкиватель 1.
Обрабатываемые изделия, уложенные на поддоны, двигаясь по направляющим закалочной печи, нагреваются и затем погру жаются в закалочный бак. Прошедшие закалку заготовки на под донах поступают в отпускную печь, а оттуда — в спрейерную установку для охлаждения, после чего происходит разгрузка поддонов и возврат пустых поддонов на загрузку в закалочную печь. Привод механизмов для подъема и опускания заслонок, а также для загрузки, перемещения и выгрузки обрабатываемых изделий — гидравлический, привод механизма возврата поддо нов — электрический.
Последовательность и темп работы механизмов агрегата соот ветствуют циклограмме (рис. 135).
Управление механизмами предусмотрено как в автоматическом режиме, так и в режиме дистанционного и местного управления. В автоматическом режиме требуемый порядок операций, осуще ствляемых механизмами, обеспечивается с помощью магнитного командоконтроллера конструкции ЗИЛ; в режиме дистанционного и местного управления включение и выключение механизмов осуще ствляется с помощью кнопок, расположенных на пульте и по месту.
Командоконтроллер представляет собой переключающее уст ройство на 48 позиций, каждой из которых соответствуют два контакта, замыкающиеся одновременно при нахождении ползу нов командоконтроллера в данной позиции. Один из контактов позиции включен в командную цепь соответствующего механизма, другой подготавливает перемещение командоконтроллера на сле дующую позицию, если команда выполнена. Таким образом, для перехода командоконтроллера на следующую позицию необхо димо, чтобы были замкнуты контакт командоконтроллера преды дущей позиции и контакт, свидетельствующий о том, что преды дущая команда выполнена. В этом случае получает питание элек тромагнит, который с помощью храпового механизма переводит ползуны на другую позицию.
В конце цикла командоконтроллер оказывается на позиции, начиная с которой контакты командоконтроллера включены
1 Проект № 32375 института «Теплопроект».
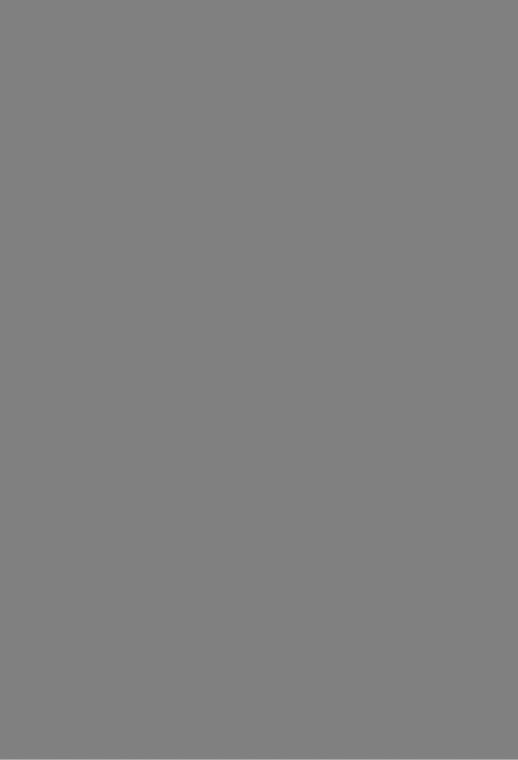
исходном положении сталкивателя; механизм возврата поддонов делает ход на 1 шаг только при поднятом подъемнике входа.
Указанные блокировочные связи осуществляются путем вклю чения контактов соответствующих конечных выключателей или промежуточных реле в цепи управления механизмами.
ГЛАВА VI
ВСПОМОГАТЕЛЬНОЕ О БО РУ ДО ВА Н И Е1
УСТАНОВКИ ДЛЯ ПРИГОТОВЛЕНИЯ ИСКУССТВЕННЫХ (КОНТРОЛИРУЕМЫХ)
АТМОСФЕР (68, 69]
Исходным сырьем для приготовления искусственных атмосфер служат широко распространенные природные углеводородсодер жащие газы, жидкий аммиак, сжиженные пропан-бутановые смеси, технический азот кислородных станций и другие технические газы.
В табл. 102 приведены типизированные размерные ряды газо приготовительных установок, в комплекте которых предусматри-
1 Данные, приведенные в настоящем разделе, относятся в основном к объек там, начатым изготовлением промышленностью. Более подробные предложения по типизации вспомогательного и комплектующего оборудования — см. [14].
|
|
|
|
|
|
|
ТАБЛИЦА |
102 |
|
|
|
Установки для очистки |
|
|
|
||
водорода от кислорода |
азота от кислорода |
инертных газов |
|
|||||
|
химический |
|
химический |
|
химический |
|||
|
состав, |
% |
|
состав, % |
|
состав |
|
|
ВО-2 |
99,995 |
Na: |
АЗ-2 |
96 N2; |
4 Н2 |
ИО-2 |
Гелий, аргон |
|
|
менее 0,005 Оа |
|
(точка |
росы |
|
или другой |
||
|
|
|
|
—40-=— 60° С) |
|
инертный |
газ |
|
ВО-6 |
|
|
АЗ-6 |
|
|
ИО-6 |
|
|
ВО-20 |
|
|
АЗ-20 |
|
|
ИО-20 |
|
|
ВО-60 |
|
|
АЗ-60 |
|
|
ИО-60 |
|
|
|
_ |
|
АЗ-125 |
90—96 N,; |
|
_ |
|
|
|
— |
|
АЗ-250 |
10 Н2 |
|
|
|
|
|
|
(точка росы |
|
— |
|
|||
|
|
|
АЗ-500 |
—40ч-—60° С) |
|
|
|
|
|
|
|
|
|
|
|
|
ваются средства автоматического регулирования состава искус ственной атмосферы. Все установки выполнены из отдельных блоков, допускающих различные модификации сборки и компо новки в зависимости от технологической схемы, требований к со ставу атмосферы и условий, определяемых производственной площадью цеха. Применение кольцевых и змеевиковых реторт в эндотермических генераторах и диссоциаторах аммиака, а также использование цеалитов для очистки и осушки экзогаза позво ляют обеспечить высокую производительность в небольших сравни тельно установках.
|
|
|
|
|
ТАБЛИЦА 103 |
Технологическая |
Обрабатываемый материал |
Диапазон |
Требуемый |
||
операция |
температур |
вид поверх |
|||
|
|
|
|
°С |
ности |
|
|
Без науглероживания |
|
|
|
Отжиг |
|
Средне- и |
высокоуглероди |
650—800 |
Светлая *2 |
|
|
стые стали *г |
700—870 |
|
|
|
|
Легированные стали *1 |
Чистая *3 |
||
|
|
Быстрорежущие стали |
800—900 |
||
Нормализация |
Легированные стали средне- |
815— 1100 |
Светлая |
||
|
|
и высокоуглеродистые |
|
|
|
Закалка |
Высокоуглеродистые и це |
760—950 |
|
||
|
|
ментованные стали |
760—950 |
|
|
|
|
Легированные стали средне- |
|
||
|
|
и высокоуглеродистые |
980— 1320 |
|
|
|
|
Быстрорежущие инструмен |
|
||
|
|
тальные стали |
|
|
|
Пайка |
в печах мед |
Средне- и высокоуглероди- |
1120 |
|
|
ным припоем |
стые стали |
|
|
|
|
То же |
|
Легированные стали средне- |
1120 |
|
|
|
|
и высокоуглеродистые |
|
|
|
Пайка |
серебряным |
Средне- и |
высокоуглероди |
700—870 |
Чистая |
припоем с флюсом |
стые стали |
|
|
|
|
Спекание |
Средне- и |
высокоуглероди |
980—1150 |
Светлая |
|
|
|
стые черные металлы |
|
|
|
|
|
С науглерооюиванием |
|
|
|
Газовая |
цементация |
Малоуглеродистые стали |
870—950 |
Чистая |
|
с добавкой природно |
|
|
|
|
|
го газа |
или пропана |
|
|
|
|
Восстановление угле |
Средне- и |
высокоуглероди |
815—900 |
|
|
рода |
|
стые стали простые и леги |
|
|
|
|
|
рованные |
|
|
|
*1 Для коротких циклов термической обработки.
**Светлая — без изменения первоначального цвета.
**Чистая — поверхность, потерявшая первоначальный цвет.
Предложение по комплектации газоприготовительных устано вок щитами управления приведено на стр. 356—359.
Ниже приведено описание наиболее часто применяемых уста новок.
У с т а н о в к и т и п а ЭН. Эти установки предназначены для получения эндотермической атмосферы из углеводородсодер жащих газов при коэффициенте расхода воздуха а = 0,25ч-0,4.
Области |
применения |
этой |
атмосферы |
приведены |
в |
табл. 103, |
|||||
основные технические |
данные |
установок — в табл. |
104. |
|
|||||||
Установки (общий |
вид |
одной из них приведен на рис. 136) |
|||||||||
состоят |
из блока |
сероочистки 2, блока |
(или |
нескольких блоков) |
|||||||
|
|
|
|
|
|
|
|
|
|
ТАБЛИЦА 104 |
|
|
Параметры |
|
|
ЭН-16 |
э н -30 |
ЭН-60 |
ЭН-60Г |
ЭН-125 ЭН-250Г |
|||
Производительность, |
м?/ч |
|
16 |
30 |
|
60 |
60 |
|
125 |
250 |
|
Установленная мощность: |
кет |
12 |
32 |
|
37 |
6 |
|
45 |
22 |
||
электрооборудования, |
|
|
|||||||||
горелок, кет |
|
|
— |
— |
|
— |
40 |
|
— |
220 |
|
Напряжение сети, в |
|
|
220 |
380 |
|
380 |
380/220 |
|
380 |
380/220 |
|
Удельный |
расход электроэнер |
0,4 |
0,7 |
|
0,6 |
0,075 |
|
0,4 |
0,09 |
||
гии, квт-ч/м3 |
|
|
|
|
|||||||
Расход воды, м3/ч |
|
|
0,3 |
1,0 |
|
2,0 |
2,0 |
|
2,5 |
5,0 |
|
Расход газа для получения ат |
3,3 |
6,2 |
|
12,4 |
12,4 |
25,6 |
51,2 |
||||
мосферы (100% СН4), м3/ч |
|
|
|||||||||
Давление |
газа, кн/м2: |
|
|
|
|
4,0—5,0 |
|
|
|
||
на входе в установку |
|
|
|
|
|
|
|
||||
» выходе из установки |
|
|
|
2,0—3,0 |
|
|
|
||||
Габаритные размеры, |
мм: |
|
1400 |
2850 |
2835 |
2985 |
3030 |
9000 |
|||
длина |
|
|
|||||||||
ширина |
|
|
1000 |
1600 |
|
1600 |
1685 |
|
1750 |
2500 |
|
высота |
|
|
2250 |
2850 |
2850 |
2850 |
2900 |
4000 |
|||
Общая масса, т |
|
|
!,6 |
3,05 |
|
3,57 |
3,67 |
4,64 |
9,7 |
Рабочая температура (газогене- |
1050 |
|
ратора . |
|
Природный газ, городской газ, сжиженные |
Исходный |
газ |
пропан-бутановые смеси |
Готовая атмосфера (при 100% |
|
|
СН4): |
|
18-20% СО; 38-40% Н2; <1% С02; |
состав |
|
|
точка |
росы, °С |
<1% СН4 |
—11ч--1-16 |
£
006Z
3030
Рис. 13G. Установка типа ЭН-125 (ОКБ-1049) для приготовления эндотер мической атмосферы:
/ — блок газогенератора; 2 — блок сероочистки
Рис. 137. Схема автоматического регулирования состава эндотермического газа по точке росы:
/ — регулирующий кран KP-G; 2 — исполнительный механизм ИМ-2/120; 3 — нзодромный регулятор РУ-4-16Л; 4 — блок измерительного прибора ИВ-439У; 5 — блок датчика ИВ-439У
генератора 1, системы смешения и пропорционирования газа и воздуха, системы автоматического регулирования состава газа по точке росы рис. 137, щитов теплового контроля и понижающих трансформаторов.
Блок сероочистки состоит.из камеры сероочистки и трубчатого холодильника. Камера сероочистки представляет собой шахтную электропечь, футерованную огнеупорными и теплоизоляционными материалами. В рабочем пространстве камеры установлена ре торта с серопоглотителем ГИАП-10 или 601. Трубчатый противоточный холодильник служит для охлаждения газа, очищенного от сернистых соединений.
Система смешения и пропорционирования состоит из газодувки, смесителя, регулятора нулевого давления и приборов для измерения расхода газа и воздуха. Газодувка типа РГН обес печивает подачу в газогенератор газовоздушной смеси под давле нием 20—30 кн/м2. Производительность газодувки определяется производительностью газоприготовительной установки.
Блок генератора включает генератор, трубчатый холодильник противоточного типа и фильтр очистки газа, идущего к щиту авто матического регулирования влажности атмосферы. Газогенератор представляет собой футерованную электропечь с жароупорной ретортой, заполненной катализатором ГИАП-3. Реторты генера торов изготовляют из литых труб сплава Х18Н35Л с толщиной стенки 15 мм. У генераторов производительностью до 30 м?Ы реторту выполняют круглого сечения, свыше 30 м*1ч — кольце вого сечения. На генераторе установлены два напоромера типа НМ-П1, показывающие давление газа перед генератором и после него. Производительность установок контролируется ротаметром, а при производительности выше 125 м31ч — дифманометром.
Эндотермические генераторы выполняют также и с газовым обогревом. Для обогрева генераторов большой производительности (125, 250 мъЫ и более) используют панельные горелки, при меньшей производительности — инжекционные.
Система автоматического регулирования состава атмосферы работает по схеме, приведенной на рис. 137. При отклонении влажности готовой эндотермической атмосферы от заданного значения чувствительный элемент датчика автоматического изме рителя влажности, представляющий собой пластинку из микропо ристого эбонита с разветвленной поверхностью токосъема, дает команду исполнительному механизму ИМ 2/128, соединенному тягой с регулирующим краном КР-6, увеличить или уменьшить подачу дополнительного воздуха в предварительно приготовлен ную газо-воздушную смесь.
Более перспективным методом определения и автоматического регулирования углеродного потенциала эндотермической атмо сферы следует считать определение концентрации С 02 с помощью оптико-акустических (инфракрасных) газоанализаторов, характе
ризуемых простотой обслуживания, более высокой точностью и
надежностью, |
а также меньшей инерционностью по сравнению |
с приборами |
измерения точки росы [60]. |
Для гашения пламени и перекрытия трубопровода в случае распространения пламени из генератора в линии газо-воздушной смеси установлена пламенная заслонка с пламегасителем, обрат ным клапаном и тепловой защитой от обратного распространения пламени. При разогреве биметаллических пластинок до 90° С клапан перекрывает линию и выключает газодувку.
На линии исходного газа установлен электромагнитный кла пан, сблокированный с газодувкой и прекращающий подачу исход ного газа при ее остановке. Установка снабжена регуляторами для автоматического поддержания давления исходного газа и го товой атмосферы.
Типовая технологическая схема установки приведена на рис. 138. Исходный газ из сети поступает в установку через регу лятор давления. Давление газа после регулятора составляет 4—5 кн1м2. Газ очищается от сернистых соединений в камере серо очистки при температуре 350° С, затем охлаждается до окру жающей температуры в трубчатом холодильнике, смешивается с воздухом и подается в реторту генератора. Здесь при температуре 1000—1050° С на никелевом катализаторе происходит процесс приготовления эндотермического газа. Выходящий из генератора газ охлаждается в трубчатом противоточном холодильнике до окружающей температуры.
У с т а н о в к и т и п а ЭК. Такие установки предназначены для получения экзотермического газа путем частичного сжигания
углеводородных газов |
при коэффициенте |
расхода воздуха |
а = |
|
= 0,6—0,9. |
Исходное |
сырье — природный газ, городской |
газ, |
|
сжиженные пропан-бутановые смеси. |
атмосферы приведены |
|||
Области |
применения экзотермической |
в табл. 105, основные технические данные установок — в табл. 106. Установки для приготовления неочищенного газа состоят из блока сжигания газо-воздушной смеси и смесительно-пропорцио- нирующей системы. В установки типа ЭК-0 дополнительно вклю
чают блоки осушки и очистки газа от двуокиси углерода.
Блок сжигания состоит из камеры сжигания и противоточного трубчатого холодильника с гидравлическим затвором. Камера снабжена горелкой для сжигания газо-воздушной смеси, глядел кой для наблюдения за процессом горения и термопарой для кон троля температуры.
Смесительно-пропорционирующая система состоит из регуля тора нулевого давления на линии газа, смесителя, газодувки и приборов для измерения расхода газа и воздуха.
Блок очистки и осушки газа состоит из емкости с цеалитами, поочередно работающих по следующей схеме: поглощение С 02 и Н 20, продувка горячим воздухом, охлаждение.
Анализ
Рис. 138. |
Типовая |
технологическая |
схема |
установок для получения эндотермической контролируемой атмосферы: |
|||
/ — регулятор давления; |
2 — краны; |
3 — вентиль с электромагнитным проводом; 4, 5 — краны; 6 — ротаметр; 7 — |
|||||
регулятор |
нулевого давления; 8 — смесительно-пропорционирующий клапан; 9, 10 — верхние холодильники реторты; |
||||||
11 |
— измеритель влажности; 12 — ротаметр; |
13 — фильтр; 14, 15 16, 17, 18, 23, 26, 32, 33, 34, 35, 42, |
43 — краны; |
||||
19, |
22 — тягонапоромеры; |
20 — водяной затвор; 21 — холодильник; 24 — нижнее уплотнение реторты; |
25 — фильтр; |
||||
27 — газогенератор; |
28, 29 — ротаметры; 30 |
— кран регулирующий; 31 — исполнительный механизм; 36 — заслонка; |
|||||
|
37 — регулятор |
давления смеси; 38 — холодильник; 39 — вентиль; 40 — газодувка; 41 — камера сероочистки |
Технологи |
Обрабатываемый материал |
Диапазон |
ческая |
температур |
|
операция |
|
°С |
Отжиг |
Малоуглеродистые стали |
650—730 |
||
|
Кремнистое |
электротехническое |
800—1100 |
|
|
железо |
|
|
|
|
Нержавеющие стали |
980—1150 |
||
|
Медноникелевые сплавы |
430—760 |
||
|
Медь |
|
|
260—650 |
|
Латуни и бронзы |
430—760 |
||
|
Средне- |
и |
высокоуглеродистые |
650—800 |
|
стали |
|
|
|
|
Средне- |
и |
высокоуглеродистые |
700—870 |
|
легированные стали |
|
||
|
Быстрорежущие стали |
800—900 |
||
Нормали |
Малоуглеродистые стали |
870—1010 |
||
|
|
|
|
|
зация |
Легированные. средне- и высоко |
815—1100 |
||
|
||||
|
углеродистые стали |
|
Требования
металлургического и химического характера
—
Снятие напряжений и пони жение потерь (для коротких циклов термообработки)
—
—
—
—
Отсутствие обезуглерожи вания
То же
Отсутствие обезуглерожи вания
Отсутствие, обезуглерожи вания
к поверх |
к защитной |
ности |
атмосфере |
Светлая |
Неочищенный, |
|
а = 0,6-^0,7 |
Чистая |
То же |
Светлая |
|
|
|
Неочищенный, |
|
|
а = |
0,9-0,95 |
Чистая |
|
То же |
Светлая |
Очищенный, |
|
и чистая |
а = |
0,6-.-0,7 |
Чистая |
|
То же |
Чистая |
Очищенный, |
|
|
а = |
0,6-т-0,7 |
Чистая |
Неочищенный, |
|
и светлая |
а = |
0,6-т-0,7 |
То же |
Очищенный, |
|
|
а = |
0,7— 0,8 |
Технологи
ческая
операция
Закалка
Пайка в печах
Спекание
Обрабатываемый материал |
Диапазон |
температур |
|
|
°С |
Высокоуглеродистые, цементиро- |
760—950 |
|||
ванные и легированные стали |
760—950 |
|||
Средне- |
и |
высокоуглеродистые |
||
стали |
|
|
|
980—1320 |
Быстрорежущие |
инструменталь- |
|||
ные стали |
|
|
|
|
Малоуглеродистые стали |
1120 |
|||
Нержавеющие стали |
1120 |
|||
Средне-, высокоуглеродистые и |
700—870 |
|||
легированные стали |
1120 |
|||
Средне- |
и |
высокоуглеродистые |
||
стали |
|
|
|
700—870 |
Чугунное литье |
|
|||
Медь или латунь |
|
700—870 |
||
Малоуглеродистые |
черные ме |
980—1150 |
||
таллы |
|
|
|
980—1150 |
Средне- |
и |
высокоуглеродистые |
||
черные металлы |
|
700—1040 |
||
Цветные |
металлы: медь—медь— |
|||
свинец, |
медь—свинец—графит |
|
|
Требования |
|
металлургического |
к поверхно |
к защитной |
и химического характера |
сти |
атмосфере |
То же |
|
|
|
Очищенный, |
|
|
|
|
а = 0,64-0,7 |
|
|
|
|
То же |
Медный припой |
|
|
Светлая |
Неочищенный, |
|
|
|
|
а = 0,64-0,7 |
Медный припой |
(без |
флю |
|
То же |
сов) |
|
|
|
|
Серебряный припой (с флю |
Чистая |
Очищенный, |
||
сом) |
|
|
Чистая |
а = 0,64-0,7 |
Медный припой |
(без |
обез |
Очищенный, |
|
углероживания) |
|
|
|
а = 0,64-0,7 |
Серебряный припой (с флю |
|
Неочищенный, |
||
сом) |
|
|
|
а = 0,64-0,7 |
Серебряный припой |
|
|
Неочищенный, |
|
|
|
|
|
а = 0,94-0,95 |
|
|
|
Светлая |
Неочищенный, |
|
|
|
и чистая |
а = 0,64-0,7 |
Без обезуглероживания |
То же |
Очищенный, |
||
|
|
|
|
а = 0,64-0,7 |
— |
|
|
|
Неочищенный, |
|
|
|
|
а = 0,64-0,7 |
|
|
|
|
|
|
Типы установок |
|
|
|
|
|
Параметры |
ЭК-8-0 |
ЭК-60 |
ЭК-125-0 |
ЭК-125 |
|
|
|
|
|
|
||||
Производительность, |
мъ1ч |
8 |
60 |
125 |
125 |
|||
Установленная мощность электрообо- |
|
|
|
|
||||
рудования, |
кет |
|
1,27 |
1,7 |
7,3 |
4,5 |
||
Напряжение сети, в |
|
|
380/220 |
|
||||
Рабочая температура (камеры сжига |
|
1000--1100 |
|
|||||
ния), °С |
|
|
|
|
|
|||
Удельный |
расход |
электроэнергии, |
0,16 |
0,03 |
0,06 |
0,03 |
||
кет • ч/м? |
|
|
|
|||||
Расход исходного газа (при 100% |
|
|
|
|
||||
СНД м3/ч: |
0,9 |
|
1,07 |
7 |
16,7 |
14,3 |
||
при а = |
|
|||||||
» |
а = |
0,6 |
|
1,23 |
8,6 |
19,2 |
— |
|
Расход |
воды, |
м31ч |
|
0,3 |
1 |
2 |
5 |
|
Давление газа на входе в установку, |
|
4 - 5 |
|
|
||||
кн/м2 |
|
|
|
|
|
|
|
|
Давление газа на выходе из уста |
2 ,5 -3 |
2,5—3 |
1,5—2 |
2 ,5 -3 |
||||
новки, |
кн/м2 |
|
мм: |
|||||
Габаритные размеры, |
|
|
|
|
||||
длина |
|
|
|
1750 |
2250 |
4400 |
3030 |
|
ширина |
|
|
1290 |
1150 |
3700 |
2000 |
||
высота |
|
т |
|
2000 |
2100 |
2565 |
2800 |
|
Общая |
масса, |
|
U |
1,13 |
6,66 |
3,15 |
||
В установках некоторых типов в одних и тех же емкостях сов |
||||||||
мещают |
осушку |
при помощи силикагеля |
и очистку от С 02 цеа- |
литами.
Исходный углеводородсодержащий газ поступает в установку из газопровода через регулятор давления при 3—3,5 кн/м2, про ходит регулятор нулевого давления и поступает в смеситель, где смешивается в небольшом соотношении с воздухом, поступа ющим через фильтр из атмосферы. Газо-воздушная смесь подается газодувкой в горелку камеры сжигания, перед которой установ лен пламегаситель. Продукты сгорания охлаждаются в противоточном холодильнике водой до температуры 25—35° С.
Установки можно выполнять таким образом, чтобы смешение газа и воздуха происходило в горелке, в которую поступает активная воздушная струя; при этом давление газа при входе в установку должно составлять 10—20 кн/м2, смеситель в этом случае из схемы исключается.
Общий вид и технологическая схема одной из последних уста новок — ЭК-125-М4 — со скруббером для отмывки механических примесей показаны на рис. 139. Установка состоит из следующих основных элементов: камеры сжигания с горелкой и водоохлажда емым газоотводом, трубчатого двухходового холодильника, скруб- бера-промывателя, влагоотделителя, двух гидрозатворов, кон трольно-измерительных приборов и щита управления.
Камера сжигания имеет водоохлаждаемый кожух, футерован ный огнеупорным материалом, и горелку. В нижней части горелки происходит смешение газа с воздухом за счет турбулентной диф фузии. Газ подводится к смесителю снизу, а воздух — сбоку. Затем газ проходит по трубе и через отверстия выходит струйками в движущийся поток воздуха. Окончательное смешение газа с воздухом производится двумя лопастными крыльчатками, вра щающимися при помощи потока смеси.
Трубчатый холодильник выполнен горизонтальным, двухходо вым. Конденсат, образующийся при охлаждении газа, удаляется в гидрозатвор. Также в гидрозатвор удаляется вода, омывающая газ в скруббере-холодильнике.
Исходный газ из газопровода подводится к регулятору давле ния на линии газа (нуль-регулятор) 4 через ротаметр. На трубо проводе подвода газа к горелке камеры сжигания 6 установлен кран, обеспечивающий возможность достижения заданного соот ношения воздух газ. Воздух из атмосферы через фильтр 2 за бирается газодувкой 1 и под давлением подается в горелку. Про дукты горения газо-воздушной смеси предварительно охлаждаются и затем поступают для окончательного охлаждения до температуры 20—30° С в трубчатый холодильник. Охлажденный газ через скруббер-промыватель 10 и затем через влагоотделитель 9 посту пает к потребителям. Через гидрозатворы 11 не только удаляется конденсат, но и сбрасывается газ при повышении давления в си стеме.
Состав готовой атмосферы может регулироваться в зависи мости от коэффициента расхода воздуха: при увеличении а от
0,6 до 0,9 содержание СО уменьшается |
от |
10—12 до |
2%; С 02 |
|
увеличивается от 4—6 до 10—12%; |
Н 2 |
уменьшается |
от 15—20 |
|
до 2%; N2 — остальное. |
этого |
типа предназначены |
||
У с т а н о в к и ДА. Установки |
для получения азотно-водородной атмосферы из аммиака в ре зультате его диссоциации и последующего частичного дожигания водорода в смеси с воздухом. Исходным сырьем служит жидкий аммиак. Атмосферу состава 75% Н 2 и 25% N2 применяют для отжига высокохромистых и трансформаторных сталей, для спека ния металлокерамики и других материалов. Атмосферу состава 4—20% Н 2, остальное М2 применяют в процессах отжига и норма лизации низко- и среднеуглеродистой стали, спекания металло керамики.
Рис. 139. Установка типа ЭК-125-М4 для приготовле ния экзотермической атмо сферы:
а — схема |
установки; б — |
общий вид; |
1 — газодувка; |
2 — фильтр; |
3 — дифмано- |
метр; 4 — регулятор давле ния на линии газа; 5— реле протока; 6 — камера сжига ния; 7 — холодильник; 8 — напоромер; 9 — влагоотделнтель; 10 — скруббер; 11 —
гндрозатвор
3950
ь
Установка типа ДА-ЗОс (ОКБ-674), показанная на рис. 140, состоит из блока диссоциатор—испаритель, блоков сжигания, охлаждения и блока осушки газа.
В состав блока диссоциатор—испаритель входят испаритель аммиака, диссоциатор и трубчатый холодильник. Испаритель
Рис. 140. Установка типа ДА-ЗОС (ОКБ-674) для приготовления контролируемой атмо сферы из аммиака:
/ —испаритель; 2—диссоциатор; 3— камера сжигания; 4—трубчатый холодильник; 5— ка мера охлаждения; 6—блок осушки; 7 — система пзодромного регулирования состава газа
представляет собой металлический сосуд высокого давления со сферическими днищами и предохранительным клапаном; испари тель оборудован змеевиковым и электрическим подогревателями жидкого аммиака, снабжен указателем и регулятором уровня, а также электроконтактным термометром типа ЭКТ-1 со шкалой О—100° С для автоматического поддержания температуры жидкого аммиака. Диссоциатор представляет собой шахтную электропечь с жароупорной ретортой, заполненной катализатором ГК-2.
Блок камеры сжигания состоит из собственно камеры, си стемы контроля и автоматического регулирования состава газа по водороду и воздуходувки. Камера сжигания частично заполнена катализатором горения и снабжена водоохлаждаемым кожухом для отвода избыточного тепла. Система контроля и автоматиче ского регулирования включает газоанализатор типа ТП-1120 на водород, изодромный регулятор РУ-4-16А, исполнительный механизм ИМ-2/120, регулирующий кран КР-6 и ротаметры.
Блок камеры охлаждения газа состоит из трубчатого холо дильника с гидравлическим затвором, камеры охлаждения с ре бристыми охладителями и холодильной установки.
Блок осушки состоит из двух силикагелевых осушителей и электрокалорифера для подогрева воздуха.
Принцип действия установки показан на типовой технологи ческой схеме (рис. 141). Жидкий аммиак из баллонов под давле нием 0,7—0,8 Мн1м2 поступает в испаритель, где испаряется при температуре 25—30° С и в виде паров при избыточном давлении около 0,1 Мн/м2 поступает в диссоциатор; здесь, проходя через слой катализатора типа ГК-1 или ГК-2 при температуре 600— 650° С, диссоциируется на азот и водород. Затем азото-водородная смесь поступает в змеевик испарителя, подогревает жидкий аммиак и проходит в трубчатый холодильник. Охлажденный газ и воздух подаются одновременно в горелку камеры сжигания. В зависи мости от их соотношения содержание водорода в атмосфере может быть получено в пределах от 4 до 20%. Выходящий из камеры сжигания газ охлаждается и осушивается до точки росы —40 ч— 50° С. Подача воздуха, необходимого для сжигания водорода, осуществляется с помощью воздуходувки и автоматически регу лируется в зависимости от заданного содержания водорода в вы ходящей из камеры сжигания атмосфере:
Техническая |
характеристика |
установки: |
30 |
|
производительность, м3/ч |
кет |
|||
установленная мощность, |
29 |
|||
рабочая температура диссоциатора, °С |
650—700 |
|||
Удельный расход электроэнергии, кет - ц/м- |
0,45 |
|||
Состав получаемой |
атмосферы, %: |
75 Н2, 25 N2 |
||
без дожигания |
водорода |
|
||
с дожиганием |
водорода |
|
4—20 Н2, 80—96 No |
|
Точка росы, |
°С |
|
|
—4 0 ^ —50 |
Габаритные |
размеры, мм |
|
3400Х ЗЗООХ 2325 (высота) |
|
Общая масса, т |
|
|
4,5 |
3 |
<t 5 |
13 20 |
21 |
22 |
23 |
|
18 |
rG fM / дрН |
* w\ |
,^ . ц |
|
Sb/ход го |
|||||
|
тового газа |
||||||||
|
|
|
|
|
|
|
|
||
|
|
|
|
|
|
А |
|
|
|
|
|
|
|
f 1 |
u |
I P " |
|
|
|
|
|
|
|
L |
H |
|
|
|
|
|
Оиссоцоировамьш |
|
|
|
|
|
|
|
|
|
|
|
|
|
|
|
|
2128 29 |
30 |
Р и с . 1 4 1 . Т и п о в а я т е х н о л о г и ч е с к а я с х е м а у с т а н о в к и д л я п р и г о т о в л е н и я к о н т р о л и р у е м о й а т м о сф ер ы и з а м м и ак а: |
|
||||||||
/ — аммиачные баллоны; |
2 — поплавковый регулятор |
уровня; 3 — предохранительный клапан; 4 — испаритель; 5 — манометры; 6 — вен |
|||||||
тиль редуцирующий |
и |
регулятор давления; |
7 — охладитель газа; |
8 — диссоциатор; |
9 — газовый запальник; 10 — камера сжигания; |
||||
11, 12 — ротаметры; |
13 — регулирующий кран; |
14 — исполнительный механизм; 15 — водяной затвор; 16 — сигнализатор |
падения |
||||||
давления; 17 — воздуходувка; 18 — охладитель |
газа; |
19 — блок |
фильтрации газа; |
20 — газоанализатор; 21 — камера охлаждения; |
22 — холодильная машина; 23 — термометры; 24 — осушители; 25 — термопара; 26 — калорифер; 27— измеритель влажности; 25—фильтр;
29 — н а п о р о м е р ; 30 — р о т а м е т р
Следует отметить некоторые положения, относящиеся к за рубежной практике [61 ].
Термическую обработку заготовок и изделий из меди и ее спла вов осуществляют в искусственных атмосферах — чаще всего в экзотермической или нейтральной (в отечественной практике используют водяной пар).
Для проводимой в искусственных атмосферах термообработки изделий из хромоникелевой стали, не содержащей титана, наи более эффективным считается чистый водород, осушенный до точки росы —70° С; при термообработке особо ответственных изделий нередко используют азот повышенной чистоты марки 99,999%, полученный при диссоциации аммиака.
Многие зарубежные фирмы предлагают печи, в которых при меняется универсальная искусственная атмосфера, пригодная для термообработки изделий из стали различных марок, незави симо от содержания в ней углерода, утверждая, что при этом отпадает необходимость в высокой квалификации обслуживающего персонала, вынужденного обычно подбирать состав печной атмо сферы для стали той или иной марки. Такие печи заполняют так называемым «нейтральным» газом (1—2% СО; 0,02% С 02) с регу лируемым содержанием водорода в пределах 2—7%. Вследствие незначительного восстановительного потенциала «нейтрального» газа печи, рассчитанные на его применение, должны быть пол ностью герметизированы, а подвергаемые термообработке изде лия — тщательно очищены от следов масла, изменяющего при сгорании заданный состав печной атмосферы.
Тщательности очистки изделий перед термообработкой в искус ственной атмосфере за рубежом вообще придают большое зна чение. Считается, что в целях получения наибольшего эффекта изделие перед термообработкой в искусственной атмосфере после обычной очистки травлением, промывки содовым раствором и промывки от соды следует обдувать паром и дополнительно про мывать в дистиллированной и деминерализованной воде.
ОБ ОРУДОВАНИЕ ДЛЯ ЗАКАЛКИ, ПРОМЫВКИ, СУШКИ И ОХЛАЖДЕНИЯ ОБРАБАТЫВАЕМЫХ ИЗДЕЛИЙ [18, 62]
Вэтом разделе приводятся размерные ряды и дается описание наиболее распространенного оборудования, компонуемого со сред ствами нагрева металлов при термической обработке. Установки для охлаждения масла упоминаются при описании баков для за калки в масле.
Вдальнейшем применяется следующая инденсация. Буквы:
первая Б — бак закалочный (замочный), М — моечная машина, X — холодильник (камера охлаждения); вторая (конструкция) — Б — барабанная, К — конвейерная, Р — рольганговая, Т — тол