
Энерготехнология химических производств
..pdfСвязь между этими единицами измерения концентраций для газообразных веществ выражается соотношением
1 мг/нм3 = 22,4/μ ppm, |
(3.1) |
где μ – молярная масса вещества-загрязнителя, кг/кмоль; 22,4 – молярный объем газа при н.у., нм3/кмоль.
Например, для:
♦SO2 (μ = 64 кг/кмоль): 1 мг/нм3 = 22,4/64 = 0,35 ppm или 1 ppm =
=64 / 22,4 = 2,86 мг/нм3;
♦NO (μ = 30 кг/кмоль): 1 мг/нм3 = 22,4/30 = 0,75 ppm или 1 ppm =
=30 / 22,4 = 1,34 мг/нм3;
♦NO2 (μ = 46 кг/кмоль): 1 мг/нм3 = 22,4/46 = 0,49 ppm или 1 ppm =
=46/ 22,4 = 2,05 мг/нм3.
Вредное воздействие этих компонентов на природу и человека определяется их концентрацией в воздухе. Так как выброс тех или иных вредных веществ будет изменяться в зависимости от технологического режима источника выброса, то необходимо, чтобы концентрация вредных веществ в приземном слое воздуха в жилой зоне не превышала величину, при которой на человеческий организм оказывается недопустимое воздействие. Величины предельных концентраций разрабатываются (постоянно изменяются) по каждому компоненту санитарными службами государства и называются предельно допустимыми концентрациями (ПДК). Различают ПДК в воздухе рабочей зоны (ПДКрз) и в атмосферном воздухе (ПДКав). ПДКрз – это концентрация, которая при ежедневной работе в течение 8 часов или другой продолжительности, но не более 40 часов в неделю, за весь стаж работы не может вызвать заболеваний или отклонений в состоянии здоровья, обнаруживаемого современными методами исследования.
Уровни загрязнения нормируются раздельно для воздуха в рабочих зонах и для атмосферного воздуха в населенных пунктах. Для интегрированной оценки воздействия выбросов вредных веществ на окружающую среду и контроля за выбросами промышленных предприятий используют величину предельно допустимого выброса (ПДВ), т.е. выброса вредных веществ, величина которого декларируется предприятием и определяется нормами технологического режима. В диапазоне ПДВ предприятие платит за величину выбросов, а при превышении ПДВ на предприятие могут налагаться серь-
91
езные санкции в виде пятикратных платежей за выбросы, штрафы, и даже возможна приостановка работы предприятия.
Одним из важнейших путей уменьшения выбросов вредных веществ в атмосферу является обезвреживание выбросов. Термин обезвреживание следует понимать более широко, чем очистку. Это связано с тем, что обезвреживание включает как предотвращение или уменьшение образования веществ-загрязнителей, так
иочистку выбрасываемых газов от этих веществ.
Всвою очередь, очистка газовых выбросов от загрязняющих веществ основана на процессах удаления этих веществ из газа жидкими или твердыми поглотителями. Для очистки используются также методы, основанные на химических превращениях веществ-загрязни- телей в другие вещества, которые либо не являются загрязнителями, либо проще удаляются из газа. Если в процессе очистки веществазагрязнители образуют другие вещества, которые могут быть использованы в качестве сырья или продуктов, то следует говорить об утилизации этих веществ.
Воснове методов обезвреживания веществ-загрязнителей лежат различные физические, физико-химические и химические процессы: физическая абсорбция, хемосорбция, адсорбция, каталитические и некаталитические химические реакции. Мероприятия, связанные с выбором и соблюдением технологического режима, наилучшего с точки зрения минимизации содержания в выбросах веществ-загрязнителей, составляют основу метода обезвреживания, называемого оптимизацией технологического режима. Частным случаем этого метода является оптимизация режима горения топлива с целью минимизации образования оксидов азота.
Вкачестве методов очистки газовых выбросов от оксидов азота используются:
– селективное некаталитическое восстановление (SNCR, или СНКВ);
– селективное каталитическое восстановление (SCR, или СКВ);
– неселективное каталитическое восстановление (NSCR, или НСКВ);
– адсорбция;
– абсорбция (хемосорбция).
Для очистки от диоксида серы применяют:
♦адсобцию;
♦хемосорбцию;
♦адсорбционно-каталитическое выделение.
92
Для очистки газовых выбросов, содержащих несколько веществзагрязнителей, на этапе проектирования комбинируют последовательные системы очистки от конкретных веществ-загрязнителей с учетом взаимной совместимости процессов, условий обеспечения максимальной эффективности очистки и образующихся продуктов.
3.1. Методы подавления образования оксидов азота при сжигании топлива. Методы очистки газовых выбросов от оксидов азота
Оптимизация режима горения топлива. Несмотря на то что
втопливе могут содержаться соединения азота, которые при сжигании неизменно переходят в оксиды азота (топливные), большая
часть оксидов азота (NOx) образуется в процессе горения топлива из атмосферного азота. Следовательно, организационно-технологи- ческие мероприятия должны быть направлены на выбор и соблюдение параметров, оптимальных с точки зрения минимизации образования оксидов азота. Преимущество данного метода заключается
втом, что он позволяет добиться цели без дополнительных капитальных затрат на установку системы очистки.
Сточки зрения термодинамики и кинетики процесса образования оксидов азота основные мероприятия должны быть направлены на снижение температуры факела, концентрации кислорода и времени пребывания газов в зоне высоких температур. К ним относятся:
– применение горелок с пониженным образованием оксидов азота (горелок многостадийного сжигания, горелок с рециркуляцией, щелевых подовых горелок и т.д.);
– рециркуляция дымовых газов;
– ступенчатое сжигание топлива;
– снижение температуры подогрева воздуха, подаваемого в топку;
– инжекция воды или пара в топку;
– малые избытки воздуха.
Наиболее распространенными способами снижения образова-
ния NOх являются рециркуляция дымовых газов, ступенчатое сжигание топлива, инжекция воды или пара в топку.
Рециркуляция дымовых газов в зону горения является наи-
более распространенным и хорошо изученным методом снижения количества образующихся оксидов азота, так как при этом одновременно снижается температура факела и избыточная концентрация кислорода. Так, например, при подаче газов рециркуляции с темпе-
93
ратурой 300 °С в количестве, равном 20 % от объема воздуха, поступающего на горение, максимальная температура факела снизится на 120–130 °С, что приведет к снижению скорости образования оксидов азота. Однако следует отметить, что при подаче 1 % газов рециркуляции КПД котла в среднем снижается на 0,02 % за счет уменьшения движущей силы теплопередачи. Наряду с этим отметим необходимость в специальном рециркуляционном дымососе и газоходе; при черезмерной степени рециркуляции могут появиться сажа и оксид углерода.
Ступенчатое сжигание топлива является одним из наибо-
лее перспективных методов регулирования топочных режимов и одновременно снижения образования оксидов азота. Сущность метода заключается в том, что в первичную зону горения подается воздуха меньше, чем необходимо теоретически (α = 0,7–0,95), что приведет к понижению максимальной температуры и содержания кислорода
вядре факела и, следовательно, к уменьшению скорости реакции образования оксидов азота. Кроме того, при последующем горении
вядре факела также отсутствуют зоны сверхвысоких температур.
Инжекция воды или пара в топку влияет как на скорость об-
разования оксида азота, так и на максимальную температуру в зоне горения, и позволяет снизить время пребывания в зоне высоких температур. Кроме того, подача воды или пара в ядро зоны горения дает возможность снизить образование сажи. Однако следует отметить, что ввод воды или пара в количестве более 5–6 % от массы подаваемого в горелки воздуха может оказать отрицательное влияние на полноту сгорания топлива и показатели работы котла, а подача 9–10 % пара в котел приводит к снижению его КПД на 4–5 %.
Как показывают исследования, решающее влияние на выход оксидов азота оказывает конструкция горелочных устройств, так как именно в горелке смешивается топливо с воздухом, что определяет условия образования оксидов азота, поэтому практически все методы воздействия на образование оксидов азота будут эффективны только в случае, если они влияют на условия смесеобразования и горения в корне факела.
Селективное некаталитическое восстановление (СНКВ).
Данный метод основан на вводе в камеру сгорания при температуре 850–1100 °С аммиака или других соединений, способных при разложении образовывать аммиак (карбамид, аммиачная вода и др.). Схема метода представлена на рис. 3.1.
94

Рис. 3.1. Схема метода СНКВ
В результате селективной реакции взаимодействия с аммиаком оксиды азота превращаются в молекулярный азот и воду:
6NO + 4NH3 = 5N2 + 6H2O,
6NO2 + 8NH3 = 7N2 + 12H2O.
Потребность в аммиаке для СНКВ-процесса значительно выше стехиометрической величины, поскольку при высокой температуре
иналичии кислорода некоторая часть аммиака может окисляться
ине участвовать в процессе восстановления NOх, поэтому нежелательно содержание кислорода в дымовых газах более 1 %. При этом, несмотря на избыток восстановителя, степень очистки от оксидов азота не превышает 60–70 %.
Оптимальной температурой процесса является 950 °С, но уже при температуре выше 1000 °С начинают протекать побочные реакции, такие как окисление аммиака в азот и оксиды азота, которые делают применение данного метода бессмысленным. Если же температура ниже 900 °С, то скорость восстановления оксидов азота резко падает, и будет происходить выброс избытка аммиака, который сам является токсичным веществом.
Таким образом, при применении данного метода необходимо:
–точно определять место ввода раствора восстановителя в то-
почный газ, поскольку процесс восстановления NOх аммиаком эффективно протекает лишь в узком температурном интервале и в течение определенного времени пребывания, а для котлов, у которых температура топочного газа меняется в зависимости от нагрузки, необходимо оборудование нескольких точек ввода раствора восстановителя;
–регулировать концентрацию кислорода в дымовых газах на минимально возможном уровне (производить сжигание топлива при коэффициенте избытка воздуха близким к единице);
95
–соблюдать строгие требования процесса восстановления в зависимости от температуры потока, нагрузки по топливу, его калорийности и т.д., что может ограничить мощность сжигающего устройства;
–учитывать возможность выброса в атмосферу аммиака и других побочных токсичных продуктов;
–учитывать возможность забивки теплообменных поверхностей котла сульфатами аммония, при сжигании высокосернистого топлива, а при использовании в качестве восстановителя раствора карбамида – циануровыми кислотами;
–для исключения термического разрушения форсунок подачи восстановителей использовать защитный водяной пар, что приведет
кпонижению КПД энергетической установки.
Селективное каталитическое восстановление (СКВ).
Для очистки от оксидов азота отходящих газов, богатых кислородом, также можно использовать аммиак в качестве селективного восстановителя, но только с использованием катализатора. В данном процессе аммиак будет реагировать с оксидами азота на катализаторе по следующим уравнениям реакций:
6NO + 4NH3 = 5N2 + 6H2O,
6NO2 + 8NH3 = 7N2 + 12H2O.
Для обеспечения высоких степеней превращения оксидов азота (до 98 %) восстановление проводят при небольшом избыточном содержании аммиака по сравнению со стехиометрическим. Для процесса очистки используют алюмованадиевый и алюмомарганцевованадиевый катализаторы, срок службы которых составляет 2–5 лет. Принципиальная технологическая схема метода представлена на рис. 3.2.
Существенным ограничением применимости данного метода очистки от оксидов азота является наличие узкого температурного интервала, что требует точно регулировать температуру процесса (180–320 °С). При низких температурах процесс тормозится адсорбцией взрывающихся самопроизвольно нитратов аммония и других солей на катализаторе. Увеличение температуры выше 320 °С приведет к резкому снижению степени восстановления оксидов азота, вызванному протеканием реакции окисления аммиака до NO:
4NH3 + 5O2 = 4NO + 6H2O.
96
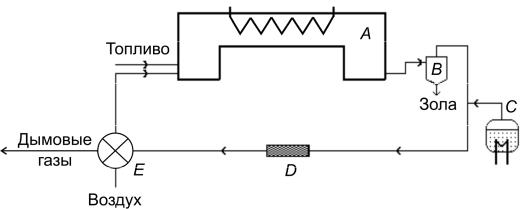
Рис. 3.2. Схема метода СКВ:
A – котел; B – система пылеочистки;
C – испаритель аммиака; D – каталитический реактор; E – воздухоподогреватель
Для проведения эффективной очистки очищаемых газов от оксидов азота необходима точная дозировка восстановителя. В случае значительного превышения концентрации аммиака выше стехиометрической может происходить его выброс с дымовыми газами в атмосферу.
Токсичность аммиака создает определенные сложности при его транспортировке и хранении, особенно в населенных пунктах. Поэтому автоматическое регулирование температуры и скорости подачи аммиака в соответствии с требуемой концентрацией приобретает большое значение. По данной причине достаточно часто аммиак заменяют растворами карбамида. Например, для очистки выхлопных газов автотранспорта от оксидов азота применяют раствор с торговой маркой AdBlue, содержащий 32,5 % карбамида. Однако в данном случае для обеспечения гидролиза карбамида в аммиак используют дополнительный слой катализатора гидролиза, который устанавливается перед слоем СКВ-катализатора.
Как и все каталитические методы, метод СКВ чувствителен к большому содержанию пыли и каталитических ядов, например серо-, фтор- и хлорсодержащих веществ.
Неселективное каталитическое восстановление (НСКВ).
Данный метод предназначен для обезвреживания содержащихся в газах оксидов азота (NOх) путем их восстановления на катализаторе до элементарного азота восстановительным газом, содержащим водород (H2), моноокид углерода (CO) или их смесь по реакциям:
2NO + 2H2 (или CO) = N2 + 2H2O (или CO2),
2NO2 + 4H2 (или CO) = N2 + 4H2O (или CO2).
97

Принципиальная технологическая схема представлена на рис. 3.3. В зависимости от состава восстановительного газа получаются водяные пары, углекислый газ или их смесь.
Метод обезвреживания оксидов азота называется неселективным, поскольку восстановители (Н2 и СО) взаимодействуют на катализаторе с кислородом, содержащимся в газовом потоке. Данное взаимодействие (каталитическое горение) проходит параллельно процессу обезвреживания оксидов азота, что требует значительного избытка восстановителя.
Рис. 3.3. Схема метода НСКВ:
A – котел; B – система пылеочистки; C – генератор восстановительного газа; D – каталитический реактор; E – каталитический реактор дожигания восстановителей; F – воздухоподогреватель
Вследствие того что в процессе выделяется большое количество тепла, применение метода целесообразно при содержании кислорода в газовом потоке не более 3 % (чтобы разогрев слоя катализатора в результате реакции кислорода с восстановителями не приводил к его разрушению). При больших концентрациях кислорода необходимо проводить процесс в несколько ступеней с промежуточным охлаждением газа. Необходимое количество восстановителей можно получить непосредственно на установке путем неполного горения топлива или его каталитической конверсией, либо подать их извне, используя различные технологические газы, их содержащие.
Таким образом, высокая степень очистки дымовых газов от оксидов азота (более 90 %), наряду с каталитическим дожиганием избытка кислорода, позволяет получить коэффициент избытка воздуха всей установки близким к единице, а утилизация тепла, образующе-
98
гося в результате реакции оксидов азота и кислорода с восстановителями, – повысить КПД теплоагрегата до максимально возможного.
Факторами, ограничивающими применение данного метода, являются:
–содержание в очищаемых газах каталитических ядов (серо-, фтор-, хлорсодержащих веществ) и пыли, загрязняющей поверхность катализатора;
–температура, определяемая типом катализатора (для большин-
ства типов катализаторов: при Т менее 150 °С катализатор не работает, а при Т более 600 °С происходит его термическое разрушение);
– содержание кислорода более 3 % об., так как температура катализатора в результате процесса может превысить 600 °С.
Преимуществами данного метода являются:
♦отсутствие необходимости в дополнительных реагентах (восстановители получаются из топлива);
♦более высокая по сравнению с другими каталитическими методами скорость процесса и, следовательно, меньший размер системы очистки;
♦полное отсутствие вредных компонентов в очищенном газе;
♦возможность достижения величины коэффициента избытка воздуха для всей установки, равного единице.
Адсорбция. Метод адсорбции оксидов азота заключается в поглощении их твердыми веществами: активированным углем, цеолитами (природными или синтетическими молекулярными ситами), силикагелем и др. Принципиальная технологическая схема метода представлена на рис. 3.4.
Особенность метода заключается в том, что процесс адсорбции является периодическим, поскольку адсорбент может поглотить только определенное количество вещества, после чего требуется его регенерация либо утилизация.
Основным достоинством метода является то, что адсорбция позволяет снизить содержание загрязняющих веществ до следовых значений (удаляется не менее 95 % оксидов азота).
К недостаткам метода следует отнести:
–температура дымовых газов должна быть ниже 120 °С;
–процесс адсорбции непосредственно применим только для диоксида азота, а монооксид азота может быть выделен только на специально модифицированных сорбентах;
–линейная скорость газа в сечении адсорбера не должна превышать 0,3 м/с, что требует значительных размеров аппаратов;
99

–необходимость установки дополнительного тягодутьевого оборудования для компенсации гидравлического сопротивления системы очистки;
–обеспечение возможности регенерации или замены отработанного насыщенного адсорбента;
–значительные затраты на регенерацию адсорбента, особенно термическим способом;
–большие капиталовложения, так как из-за периодичности процесса требуется двойной комплект оборудования.
Рис. 3.4. Схема метода адсорбции:
А– котел; B – система пылеочистки; C – адсорбер на поглощении; D – адсорбер на регенерации
Абсорбция (хемосорбция). Абсорбционный способ очистки газовых выбросов, содержащих оксиды азота, достаточно широко применяется в промышленности (скрубберная очистка), несмотря на то что применение абсорбции наиболее эффективно при значительных концентрациях газообразных загрязнителей (более 1 % об.) и низкой температуре (менее 50 °С).
Наиболее часто в качестве абсорбентов используются растворы соды, «известковое молоко», реже применяются растворы NaOH и карбоната аммония. Для активации процессов абсорбции NOх вводят в абсорбенты различные окислители (NaClO2, KMnO4, Н2О2 и др.), что позволяет частично производить процесс окисления в жидкой фазе. Кроме того, для избирательного поглощения монооксида азота применяют селективные хемосорбенты – сульфаты, а также органические соединения Fe (II), образующие при взаимодействии с NO комплексные соединения, способные при регенерации выделять поглощенный монооксид азота.
100