
- •ВВЕДЕНИЕ
- •1. ЭТАПЫ АВТОМАТИЗАЦИИ
- •2.4. Системы автоматического пуска и останова объекта управления
- •2.5. Системы автоматического регулирования объектов управления
- •4. ОСНОВНЫЕ ПОНЯТИЯ АВТОМАТИКИ
- •4.2. Функциональные структуры систем управления
- •4.2.1. Ручное управление
- •4.2.2. Автоматическое управление
- •4.2.3. Автоматизированное управление
- •5.1. Характеристика дискретного автомата
- •5.2.2. Таблица выходов (функция Я.)
- •5.2.4. Граф-схемы алгоритмов
- •5.2.5. Логические схемы алгоритмов
- •7.3.1. Стабилизация скоростей
- •7.3.2. Стабилизация мощности
- •7.3.3. Двойной экстремальный вариант
- •8.1. Требования к системам автоматизации передвижки призабойной крепи
- •8.2. Способы автоматической передвижки призабойной крепи
- •8.2.1. Способ передвижки секций по принципу «десятков-единиц»
- •8.4. Схема микропроцессорной распределенной системы управления передвижкой призабойной крепи
- •9.2. Автоматизация проходческих работ буровзрывным способом
- •9.2.1. Требования к системам автоматизации буровых машин
- •10.1. Требования к системам автоматизации конвейерного транспорта
- •10.2. Принципы автоматизации пуска конвейерных линий
- •10.5. Структура алгоритма автоматического управления конвейерной линией в цифровом варианте
- •11.2. Устройство и принцип работы аппаратуры «АБСС-1»
- •12. АВТОМАТИЗАЦИЯ ШАХТНОГО ПОДЪЕМА
- •13.1. Требования к системам автоматизации шахтного водоотлива
- •13.2. Схема установки датчиков в автоматической системе шахтного водоотлива
- •13.3. Структура и принцип работы аппаратуры УАВ
- •14.1. Требования к системам автоматизации проветривания шахты
- •14.2. Структура и принцип работы аппаратуры типа УКВГ
- •15.2. Структура автоматического управления шахтных компрессорных установок
- •18.1. Регулирование параметров при бурении нефтяных или газовых скважин
- •19.1. Автоматизация группового замера дебита скважин
- •19.3. Автоматизация работы дожимной насосной станции
- •СПИСОК ЛИТЕРАТУРЫ
- •ОГЛАВЛЕНИЕ
- •Сажин Рудольф Алексеевич
- •АВТОМАТИЗАЦИЯ ТЕХНОЛОГИЧЕСКИХ ПРОЦЕССОВ ГОРНОГО ПРОИЗВОДСТВА
Рис. 92. Часть структуры алгоритма контроля
уровня жидкой фракции
Вследствие открытия задвижки этот уровень должен уменьшать ся на заданное значение, поэтому при сравнении заданного и фактиче ского уровней ветвление алгоритма произойдет в направлении «нет». После этого вновь опрашивается датчик положения задвижки, и если опа открыта, то снова подается команда на ее закрытое.
На этом этап опроса датчика уровня нефти заканчивается, и ал горитм переходит к опросу датчика уровня воды в буллите. Величи на этого уровня регулируется алгоритмом подобным образом.
19.3. Автоматизация работы дожимной насосной станции
Дожимная насосная станция (рис. 93) после первичной сепара ции нефти обеспечивает ее переток к установкам дальнейшего тех нологического цикла и поддержание там необходимого давления.

Рис. 94. Структура нижнего уровня системы управления
дожимной насосной станцией
ки положения задвижек. Аналоговые датчики давления и диффе ренциальные манометры подключены на вход модуля (порта) ана логового ввода. Двигатели всех задвижек и приводы насосов подключены к модулю (порту) дискретного вывода.
Алгоритм управления дожимной насосной станцией имеет сложную структуру, состоящую из нескольких взаимосвязанных подпрограмм. Основная программа этого алгоритма представлена на рис. 95.
По этому алгоритму после ввода величины задающих сигна лов выполняется цикл ожидания нажатия кнопки «пуск», после на жатия которой происходит автоматический выбор насоса № 1 и задвижки Z5 в качестве рабочего оборудования технологическо го цикла. Этот выбор фиксируется присвоением единичного зна чения константам N n K .llo значению этих констант в дальнейшем будет определен выбор направления ветвления в подпрограммах алгоритма.
Эти подпрограммы запускаются основным алгоритмом сразу же после подачи команды на открытие задвижки Z1, соединяющей технологическую линию дожимной насосной станции с установкой первичной сепарации нефти. Первая из этих подпрограмм «Пуск насосов» управляет процессом запуска рабочего (или резервного) насоса, а другая подпрограмма «Контроль параметров» производит текущий контроль основных параметров технологического процес са и в случае их несоответствия заданным значениям осуществляет переключения в технологической цепочке этого процесса.
Рис. 95. Алгоритм управления
дожимной насосной станцией
Подпрограмма «Контроль параметров» запускается цикличе ски на всем протяжении рабочего цикла этого процесса. Одновре менно в этом цикле производится опрос кнопки «стоп», при нажа тии которой закрывается задвижка Z1. Затем, прежде чем остано вить основную программу, алгоритм запускает на выполнение подпрограмму «Останов насоса». По этой подпрограмме выполня ются последовательные действия по остановке рабочего насоса.
По подпрограмме «Пуск насоса» (рис. 96) первоначально про изводится анализ содержания параметра N, которым определен но мер рабочего насоса (соответственно N= 1 для насоса № 1 и N= О для другого насоса). В зависимости от значения этого параметра ал горитм выбирает ветвь запуска соответствующего насоса. Эти вет ви аналогичны по структуре, но отличаются параметрами техноло гических элементов.
Первой процедурой выбранной ветви этой подпрограммы про изводится опрос дифференциального датчика давления DM1, со держание которого определяет рабочее состояние соответствующе го фильтра на входе насосного агрегата. Показания этого датчика сравниваются с заданным предельным значением относительного давления на фильтре. При зашламованности фильтра (когда он тре бует чистки) разность давлений на его входе и выходе будет превы шать заданное значение, поэтому данная технологическая ветвь не может быть запущена в работу, и потребуется переход на запуск резервной линии, т. е. резервного насоса.
В случае нормального состояния фильтра его фактическое раз ностное давление меньше заданного, и алгоритм переходит к опросу датчика, контролирующего давление на входе выбранного насоса. Показания этого датчика сравниваются с заданным значением. В слу чае недостаточного давления на входе насоса он не сможет выйти на рабочий режим, поэтому он также не может быть запущен, что снова потребует перехода на запуск резервного насоса.
В случае нормального значения давления на входе насоса сле дующая команда подпрограммы запускает его, при этом параметру N присваивается соответствующее числовое значение, а дискрет ные датчики контроля запуска насоса контролируют этот процесс. После этого запуска опрашивается датчик, контролирующий давле ние на выходе запущенного насоса. Если это давление окажется ни же заданного уровня, насос тоже не может работать в нормальном режиме, поэто*ду и этот случай требует запуска резервного насоса, но только поелСостановки запущенного насоса.
Если же заданное давление на выходе насоса достигнуто, это значит, что он Аышел на заданный режим, поэтому на следующем шаге алгоритм открывает задвижку, соединяющую выход насоса с линией выходных фильтров системы. Открытие каждой из задви жек фиксируется дискретными датчиками ее положения.
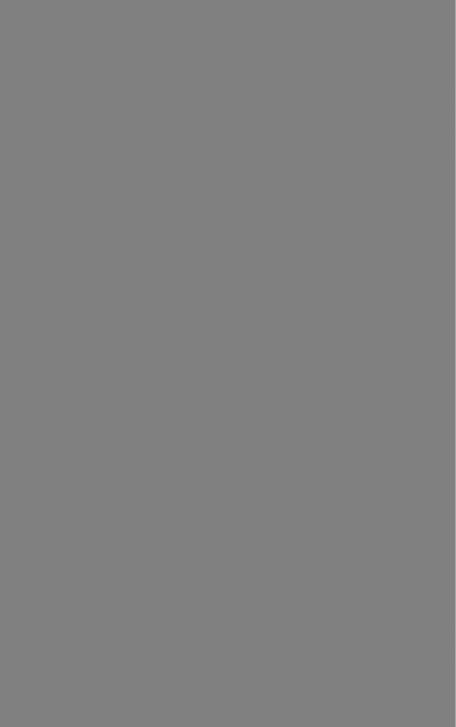
Рис. 97. Структура подпрограммы «Контроль параметров»
В этой подпрограмме, как и в предыдущей, производится по следовательный опрос тех же датчиков и сравниваются их показа ния с заданными значениями контролируемых параметров. В слу чае их несоответствия подается команда на закрытие соответствую щей задвижки и на остановку соответствующего насоса, при этом параметру N присваивается значение, противоположное предыду щему. После всего этого производится запуск подпрограммы «Пуск насоса», по которой включается в работу резервный насос.
Если все контролируемые параметры соответствуют заданным значениям, то, прежде чем выйти в основную программу, алгоритм
проверяет состояние фильтров основной магистрали. Для этой цели запускается подпрограмма «Управление задвижками Z5 и Z6» (рис. 98), по которой в случае выхода из строя одного из этих фильт ров включается в работу резервный фильтр.
[Нет |
[нет |
Закрытие задвижки Z5 |
Закрытие задвижки Z5 |
Открытие задвижки Z6 |
Открытие задвижки Z6 |
К = 0 |
К = 1 |
Рис. 98. Структура подпрограммы «Управление задвижками Z5 и Z6»
По этой подпрограмме через анализ значения параметра К в ней выбирается рабочая ветвь, по которой производится опрос диффе ренциального манометра работающего фильтра. В случае нормаль ной работы фильтра разность фактического давления между вхо дом и выходом фильтра не будет превышать заданного значения, поэтому алгоритм по условию «да» выходит из подпрограммы без изменения структуры подключения элементов в магистрали.
В случае превышения этой разницей заданного значения алго ритм следует по условию «нет», в результате чего закрывается ра ботающая задвижка и открывается резервная, а параметру N при сваивается противоположное значение. После выполнения этого производится выход из этой подпрограммы в предыдущую, а из нее — в основную программу.
Процесс контролируемого пуска рабочего насоса, а в случае его поломки — запуска резервного производится алгоритмом автома тически. Аналогично осуществляется контролируемый запуск фильтров через включение задвижек в основной магистрали.
При нажатии на кнопку «Стоп» цикл непрерывного контроля за параметрами системы прекращается, закрывается задвижка, под ключающая дожимную насосную станцию к сепарационной уста новке, и производится переход к подпрограмме «Останов насоса» (рис. 99).
Рис. 99. Структура подпрограммы «Останов насоса»
По этой подпрограмме на основе анализа параметра N выбира ется одна из двух идентичных ветвей следования алгоритма. По ней алгоритмом первоначально подается команда на закрытие задвиж ки, установленной на выходе работающего насоса. После закрытия се другая команда останавливает работающий насос. Затем новым анализом значения уже параметра К выбирается ветвь алгоритма, по которой закрывается задвижка работающего магистрального фильтра, после чего алгоритм останавливает свою работу.
20. АВТОМАТИЗАЦИЯ РАБОТЫ
ГАЗОПЕРЕКАЧИВАЮЩЕЙ СТАНЦИИ
Газоперекачивающие станции предназначены для поддержа ния необходимого давления газа в магистральных газопроводах и устанавливаются на всем протяжении трассы газопровода. В тех нологическом процессе работы газоперекачивающей станции ис пользуются турбокомпрессорные установки с приводом от газотур бинного авиационного двигателя, топливом для которого является часть транспортируемого газа. Технологическая схема такой уста новки показана на рис. 100. На схеме изображена только та часть га зотурбинного авиационного двигателя, в которой расположена си ловая газовая турбина.
Технология работы турбокомпрессорной установки следую щая. Газ из магистрального трубопровода через задвижку ЗМ1 заса сывается в турбокомпрессор и поступает в полость нагнетателя,
вкоторой он под воздействием лопаточного аппарата турбины сжи мается до требуемого уровня. При сжатии газа его объем сокраща ется, поэтому рабочая полость турбонагнетателя имеет коническую форму, а его ротор воспринимает определенное осевое воздействие
впроцессе сжатия газа.
Сжатый в турбокомпрессоре газ через задвижку ЗМ2 поступает в напорную магистраль газопровода, по которой он транспортиру ется до следующей газоперекачивающей станции или поступает по требителю.
Для нормальной работы турбокомпрессора и его приводного двигателя необходимо под давлением смазывать все их трущиеся части. Это обеспечивается системой принудительной смазки, в ко торой масло циркулирует под определенным давлением и с задан ной предельной температурой. Рабочее давление масла в системе смазки создается насосом с приводом от независимого двигателя.
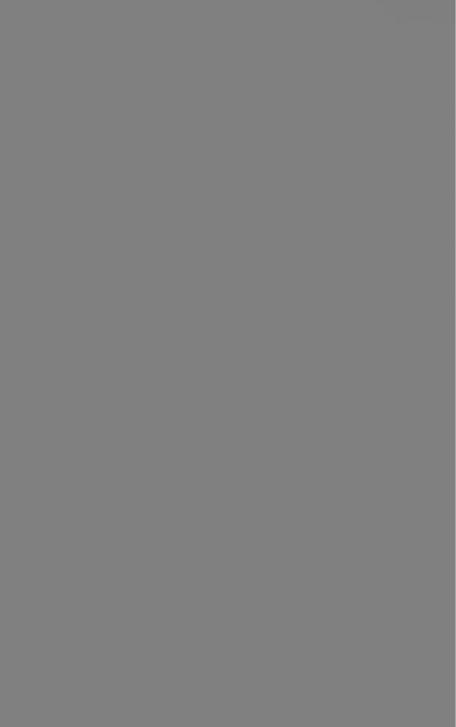
В системе автоматизации турбокомпрессора установлены сле дующие датчики и исполнительные устройства:
-71 —температура газа на входе турбокомпрессора;
-72 — температура газа на выходе турбокомпрессора;
-73 — температура масла в системе смазки;
-ТА — температуры подшипников компрессора;
-Р1 — давления газа на входе турбокомпрессора;
-Р2 — давления газа на выходе турбокомпрессора;
-РЗ — давления масла в системе смазки;
-РА — предельное давления газа при продувке компрессора;
-QI — расхода газа на входе турбокомпрессора;
-Q2 — расхода газа на выходе турбокомпрессора;
-ЗМ1 — задвижка входная газовая магистральная;
-ЗМ2 — задвижка выходная газовая магистральная;
-В1 — вентиль продувки компрессора;
-В2 — вентиль сброса газа при продувке;
-ВЗ — вентиль перепуска газа.
Величина температуры, расхода и давления газа в магистрали регистрируется соответствующими датчиками. Кроме того, контро лю подлежит температура и давление масла в системе смазки как турбокомпрессора, так и авиадвигателя.
Все датчики и исполнительные устройства системы автомати ки турбокомпрессора подключены к соответствующим портам мик роконтроллера, являющегося основой его системы управления. Структура этой системы показана на рис. 101.
Эта система устроена по уровневому типу. На верхнем инфор мационном уровне этой системы расположен компьютер операто ра, связанный через информационную сеть с функциональными элементами нижележащих уровней. На нижнем уровне расположе ны управляющие контроллеры. Один из них управляет технологи ческим процессом работы турбокомпрессоров, а другой управляет работой приводного газотурбинного авиационного двигателя.
Система автоматики газотурбинного авиационного двигателя обеспечивает его безаварийную работу на всех режимах газопере качивающей станции. Эта система связана с управляющим компью тером верхнего уровня и контроллером турбокомпрессора через ин формационную сеть этой системы управления. Режим работы газо турбинного авиационного двигателя определяется нагрузкой на
Рис. 101. Структура системы автоматизированного управления турбокомпрессором
турбокомпрессор газоперекачивающей станции, поэтому он задает этим турбокомпрессором управляющую сеть.
Алгоритм управления работой газоперекачивающей станции со стоит из двух функциональных частей. По первой части этого алго ритма производится запуск турбокомпрессора в работу, а по второй части этого алгоритма производится контроль параметров и поддер жание заданного режима работы этого турбокомпрессора.
После нажатия кнопки «Пуск» алгоритм запуска турбоком прессора в работу делится на три этапа. На первом этапе через вен тили В1 и В2 осуществляется предварительная продувка газом не подвижного турбонагнетателя. При этом часть газа вентилем В2 сбрасывается на «свечу», т. е. сжигается. Через заданное время вен тиль В2 закрывают, в результате чего пламя «свечи» гаснет и во внутренней полости нагнетателя начинает возрастать давление га за. Как только это давление достигнет заданной величины датчик Р4 подаст сигнал на открытие магистральной задвижки ЗМ1 и пере пускного вентиля ВЗ. После этого вентиль В1 закрывается. Далее подается команда на запуск специального пускового устройства (турбодетандора), с помощью которого происходит раскрутка рото ра газотурбинного двигателя и ротора турбонагнетателя в «закольцванном» режиме. В этом режиме газ с выхода нагнетателя через вентиль ВЗ снова поступает на его вход.
На втором этапе запуска, когда обороты вращения ротора дос тигнут 400-1000 об/мин, на запальное устройство камеры сгорания газотурбинного авиационного двигателя подается топливный газ одновременно включается система зажигания. Как только топлив ная смесь загорит, система автоматики двигателя начинает увели чивать подачу топливного газа до величины, необходимой для его прогрева до температуры 150-200 °С. Прогрев двигателя длится 10 мин. При этом происходит постепенное увеличение оборотов ро тора двигателя. При достижении оборотов 40-45 % от номинально го значения турбина двигателя выходит на режим самоходности, при котором пусковое устройство (турбодетандор) отключаются.
На третьем этапе запуска происходит дальнейший разгон тур бины в режиме самоходности за счет увеличения подачи топливно го газа. Как только обороты турбины достигнут номинального зна чения, открывается магистральная задвижка ЗМ2 и закрывается пе репускной вентиль ВЗ, при этом нагнетатель с «закольцованного» режима переходит на режим нормальной работы, т. е. начинает по давать газ через задвижку ЗМ2 в магистральный трубопровод..
Газоперекачивающая станция укомплектована несколькими турбоагрегатами, часть из них находится в работе, другая часть ос тается в резерве. Этот резерв может быть «холодным» (ХР) и «горя чим» (ГР). В режиме «холодного резерва» все системы и агрегаты газокомпрессорной установки находятся в полной готовности к пуску, но нагнетатель остается незаполненным газом. В случае «горячего резерва» нагнетатель заполнен газом, давление которого постоянно поддерживается.
Система автоматизации газоперекачивающей станции, кроме автоматического запуска турбоагрегата по вышеизложенному алго ритму, обеспечивает постоянный контроль параметров всех турбо агрегатов. Контролируемые параметры передаются на верхний уро вень системы управления, где они оперативно анализируются, по сле чего заносятся в архив. В случае возникновения аварийных ситуаций данные из архива извлекаются для анализа аварийного случая.