
Теория технологических процессов учебное пособие
..pdf
|
|
|
|
|
|
Таблица 6.1 |
Коэффициенты пористости четырехфракционных смесей |
||||||
|
|
|
|
|
|
|
|
Объемная доля фракции |
|
Коэффициент пористости |
|||
|
|
|
|
|
|
|
ϕ1 |
ϕ2 |
ϕ3 |
ϕ4 |
опыт |
по МКМ |
по МВС |
0,375 |
0,125 |
0,375 |
0,125 |
0,432 |
0,432 |
0,468 |
0,143 |
0,429 |
0,286 |
0,143 |
0,481 |
0,473 |
0,514 |
0,333 |
0,333 |
0,222 |
0,111 |
0,445 |
0,450 |
0,473 |
|
|
|
|
|
|
|
0,273 |
0,182 |
0,273 |
0,273 |
0,429 |
0,425 |
0,465 |
0,250 |
0,250 |
0,250 |
0,250 |
0,440 |
0,429 |
0,473 |
0,200 |
0,300 |
0,200 |
0,300 |
0,424 |
0,429 |
0,473 |
|
|
|
|
|
|
|
0,222 |
0,222 |
0,222 |
0,333 |
0,430 |
0,428 |
0,463 |
0,250 |
0,125 |
0,250 |
0,375 |
0,430 |
0,428 |
0,463 |
|
|
|
|
|
|
|
0,167 |
0,167 |
0,167 |
0,500 |
0,457 |
0,452 |
0,456 |
0,300 |
0,300 |
0,300 |
0,100 |
0,380 |
0,457 |
0,484 |
Точность данного метода расчета пористости или плотности хаотической упаковки частиц дисперсных наполнителей составляет около 7 %.
Оптимальный фракционный состав дисперсного наполнителя
необходим для отыскания рецептурных условий максимальной плотности хаотической упаковки частиц твердых компонентов (ϕm). Это, в свою очередь, определяет минимальный уровень эффективной степени объемного наполнения (ϕ/ϕm), влияющий на реологические и механические характеристики полимерной композиции, прежде всего на динамический коэффициент вязкости технологической массы и начальный модуль вязкоупругости готового материала.
Задача оптимизации фракционного состава дисперсных компонентов полимерного материала (для заданных среднемассовых размеров частиц фракций) с учетом выполнения условия оптимальности по другим эксплуатационным характеристикам может быть сформулирована в виде следующей постановки нелинейного программирования:
ϕm (ϕG, qG, d ) max;
81
|
|
|
|
|
|
m j |
|
|
ϕoptj = ϕj1 +ϕj 2 +ϕj3 +... +ϕjm j = ∑ϕjv ; |
||||
|
|
|
|
|
|
v=1 |
|
0 ≤ ϕminjv ≤ ϕjv ≤ ϕmaxjv ≤1, |
v =1, 2, |
3, ..., mj при j In ; |
|||
|
|
opt |
|
xoptj |
/ γj |
|
|
|
ϕj |
= |
|
, |
|
|
|
∑ xoptj / γj |
||||
G |
G |
G |
|
j In |
|
|
|
|
|
|
|||
где ϕ, q, |
d – векторы объемных долей, пористостей и размеров час- |
тиц фракций дисперсных компонентов в составе полимерного материала соответственно; ϕoptj – оптимальные объемные доли фракций
наполнителя в составе; ϕjv – объемная доля v-й фракции j-го вида наполнителя в составе; mj – число фракций j-го дисперсного компонен-
та; ϕminjv , ϕmaxjv – соответственно нижние и верхние границы для объ-
емных долей фракций твердых компонентов в составе; xoptj – опти-
мальные для соответствующего блока характеристик, например механических, массовые концентрации твердых дисперсных ингредиентов в полимерной композиции; γj – плотности дисперсных компонентов; In – множество индексов, принадлежащих видам наполнителя, входящих в рецептуру полимерного материала.
Ввиду сложности поставленная задача, включающая в себя ограничения типа равенств, преобразуется в задачу нелинейного программирования с ограничениями типа неравенств. В ней количество
независимых оптимизируемых переменных n =(mj )−m, где m –
число видов твердых компонентов полимерного материала. При этом нормирующее соотношение
m j
∑∑ϕjv = ∑ ϕoptj =1 j In v=1 j In
в случае решения задачи выполняется автоматически.
Далее определяется вектор оптимальных объемных долей фрак- |
||
Gopt |
opt |
; j In ; v =1, 2, 3, ..., |
ций наполнителя в композиции: ϕ |
= (ϕjv |
|
82 |
|
|
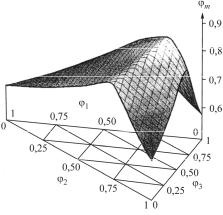
mj ), где ϕoptjv – оптимальная объемная доля v-й фракции j-го вида
наполнителя.
Переход к оптимальным массовым концентрациям соответст-
вующих фракций твердых компонентов xGoptj |
=(xGoptjv ; j In ; v =1, 2, |
|
3, ..., mj ) проводится по формуле xoptjv |
=(ϕoptjv |
γj )/ (ϕoptj / γj ) P, где |
m j |
|
|
P = ∑∑ xoptjv = ∑ xoptj |
||
j In v=1 |
j In |
|
является суммой массовых концентраций твердых компонентов.
На рис. 6.7 показана зависимость предельного объемного наполнения полимерного связующего твердого ракетного топлива от соотношения объемных долей фракций перхлората аммония (табл. 6.2) в виде поверхности отклика, наглядно демонстрирующей оптимальную область.
Рис. 6.7
Из этих данных следует, что искомый оптимальный фракционный состав смеси указанного наполнителя, соответствующий максимальному значению предельного объемного наполнения (ϕm), следующий:
83

размер фракции, мкм |
1 |
30 |
240 |
доля фракции ϕm |
0,138 (13,8 %) |
0,279 (27,9 %) |
0,583 (58,3 %) |
Таблица 6.2 Характеристики фракций перхлората аммония
Характеристика |
1 (мелкая) |
2 (средняя) |
3 (крупная) |
Среднемассовый размер частиц, мкм |
1 |
30 |
240 |
Пористость (объемная доля пор) |
0,379 |
0,384 |
0,450 |
Коэффициент пористости |
0,610 |
0,623 |
0,818 |
Таким образом, оптимизацию фракционного состава смеси всех твердых компонентов полимерного материала необходимо осуществлять в условиях ограничений на влияющие факторы и функции отклика любым из известных методов симплекс-решетчатого планирования, например, Бокса и Уилсона.
6.2. Применение симплекс-решетчатого планирования численного эксперимента
Симплекс-решетчатый метод планирования эксперимента, включая численный эксперимент, позволяет наглядно представлять результаты исследования структурно-реологических свойств наполненных полимеров.
На рис. 6.6 показана расчетная диаграмма Гиббса «состав– свойство», являющаяся проекцией поверхности отклика [ηr =
= f (ϕкр : ϕср : ϕм ) на плоскость треугольника Гиббса. Диаграмма
содержит линии равных значений относительной вязкости гипотетического полимерного связующего, постоянно наполненного (ϕ = 0,75) смесью трех фракций перхлората аммония – 600, 240 и 15 мкм – в различном соотношении. Там же нанесены линии равных значений среднемассового размера ( d , мкм) частиц смесей, влияющего на скорость горения смесевого твердого ракетного топ-
84
лива как энергосодержащего полимерного композиционного материала.
На диаграмме видно, что при неизменном химическом составе относительный динамический коэффициент вязкости полимерной суспензии в области оптимального объемного соотношения указанных фракций в десятки раз меньше, чем при неблагоприятных соотношениях.
Соответствующие расчеты предельного объемного наполнения (ϕm =1−ϕpl ) были проведены комбинаторно-мультипликативным
методом. Переход от насыпного (исходного) состояния смесей фракций перхлората аммония к состоянию, сопряженному с контактом частиц наполнителя и молекул полимерного связующего, осуществлялся при условии определения объемных предельных наполнений индивидуальными фракциями вискозиметрическим методом
(см. табл. 6.1).
Тема 7. Теория основных методов формования изделий из полимерных материалов
Рассматриваемые вопросы. Формование полимерных волокон методом экструзии. Формование листов, труб и пленок непрерывной экструзией. Формование кабельной продукции. Методы вальцевания и кландрования. Анализ методов формования методом конечных элементов. Литье термопластов под давлением. Свободное литье. Переработка реакционно-активных полимерных композиций.
7.1. Формование полимерных волокон методом экструзии
Формование волокна представляет собой процесс экструзии (продавливания) расплава или раствора полимеров через металлическую пластину, имеющую ряд симметрично расположенных отверстий малого диаметра, в результате чего образуются жидкие полимерные струи. Последующая обработка струй включает в себя вытяжку расплава, охлаждение и холодную вытяжку. Диаметр по-
85
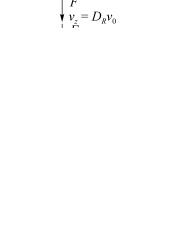
лученных волокон значительно меньше диаметра струй. Волокна являются анизотропными (макромолекулы полимера ориентированы
|
вдоль оси вытяжки), механически |
|
|
очень прочны, так как практически |
|
|
полностью оказываются кристалли- |
|
|
ческими (рис. 7.1). Это достигается |
|
|
за счет вытягивания и одновремен- |
|
|
ного охлаждения выходящего экс- |
|
|
трудата (продукта формования) в |
|
|
виде нескольких струй (волокон). |
|
|
Затем не полностью остывшие во- |
|
|
локна подвергают продольной вы- |
|
Рис. 7.1 |
тяжке путем намотки на тянущие |
|
барабаны; при этом их диаметр |
||
|
уменьшается в 10–15 раз, что приводит к усилению нитей за счет кристаллизации. Типичные примеры синтетических волокон: «капрон» (алифатический полиамид), «нейлон» (ароматический полиамид), «лавсан» (полиэтилентерефталат).
Фильеры обычно представляют собой короткие капилляры, у которых 1 < L/D0 < 5. Канал фильеры имеет плавный контур, что позволяет придать потоку на входе форму «рюмки» и свести до минимума искажения формы экструдата, обусловленные эластическим восстановлением.
С увеличением скорости вытяжки и ориентационного напряжения величина отношения D/D0 быстро уменьшается. Приблизительное выражение для оценки эластичного восстановления струи при наличии вытяжки имеет следующий вид:
|
B |
|
6 |
λef |
|
4F |
|
B2 |
||
|
|
|
=1− |
|
|
|
|
|
|
, |
|
µ |
|
πD |
2 |
6 |
|||||
B(0) |
|
|
|
|
[B(0)] |
86
где B = D/D0; B(0) – коэффициент восстановления струи при осевом усилии F = 0; λef = µ/G – время релаксации макромолекул расплава полимера; µ – условно фиксированный динамический коэффициент вязкости; G – функция, описывающая диссипацию внутренней энергии потока.
Гогос и Моретт численными методами решили задачу о течении в капилляре расплава поливинилхлорида с уменьшающейся вследствие термодеструкции вязкостью. Для этого полимера, подчиняющегося степенному закону течения Освальда де Виля, уравнения сохранения энергии и количества движения следующие:
|
|
dP |
|
|
1 d |
|
|
|
dv |
|
|
n−1 |
dv |
z |
|
|
|
|
|
|
|
|||||
|
|
|
|
|
|
|
|
|
|
|
||||||||||||||||
|
− |
|
|
+ |
|
|
|
|
rη e∆E / RT |
|
z |
|
|
|
|
|
|
|
= 0; |
|
|
|||||
|
|
|
|
|
|
|
|
|
|
|
|
|
|
|
|
|||||||||||
|
|
dz |
|
|
r dr |
|
0 |
|
dr |
|
|
|
dr |
|
|
|
|
|
|
|
||||||
|
|
|
|
|
|
|
|
|
|
|
|
|
|
|
|
|
|
|
|
|
|
|
|
|
|
|
ρcpvz |
dT |
= |
1 ∂ |
|
∂T |
+η0e∆E / RT |
|
dv |
z |
|
|
n−1 dv |
z |
2 |
||||||||||||
|
|
|
||||||||||||||||||||||||
|
|
|
|
|
|
rk |
|
|
|
|
|
|
|
|
. |
|||||||||||
dz |
|
|
|
|
dr |
|
|
|
|
|
||||||||||||||||
|
|
|
r ∂r |
|
∂r |
|
|
|
|
|
|
|
|
|
dr |
Здесь при рассмотрении энергетического баланса интенсивность теплового потока за счет работы сил вязкого трения, отнесенная к единице объема (ev) описывается выражением
dv |
2 |
(n+1)/2 |
|||
ev = η |
|
z |
|
, |
|
|
|
dr |
|
|
|
|
|
|
|
|
|
где
η= η0e∆E / RT .
На рис. 7.2 представлено распределение давления вдоль оси капилляра, найденное с помощью уравнения
|
∆PD0 |
|
D0 |
|
∆P |
|
|
τw = |
4L |
= |
|
|
|
|
, |
4 |
L + N |
D + N |
D |
||||
|
|
|
|
|
ent 0 |
ex 0 |
|
где τw – скорректированное (поправка Бэгли (N) для уточнения тече-
ния при входе полимерного расплава в капилляр) напряжение сдвига на стенке для полностью установившегося течения; Nent и Nex – вели-
87
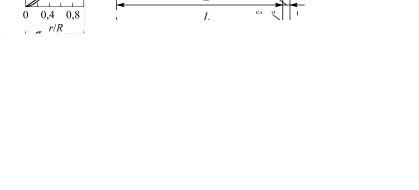
чины, на которые возрастает длина капилляра на входе и выходе соответственно. При этом продольное распределение давления выражается так:
−dP / dz = ∆P / L = ∆P(L + ND0 ).
Рис. 7.2 |
Рис. 7.3 |
Распределения градиентов скоростей сдвига по радиусу капилляра для полимерного расплава при µ = η (изотермическое течение с постоянным объемным расходом потока) в сравнении с течением ньютоновской жидкости показаны на рис. 7.3, где µ = η = 0,1 МПа·с; ∆P = 34,5 МПа; R = 0,1 см; L = 5 см. Видно, что в случае степенных жидкостей (n = 0,5) диссипативное тепловыделение наиболее велико
устенки капилляра.
7.2.Формование листов, труб и пленок непрерывной экструзией
Формование листов и пленок. Полимерные листы получают непрерывной экструзией расплава через листовальную головку, выходное отверстие которой представляет собой узкую длинную щель обычно прямоугольной формы. На выходе из головки листовой материал утолщается за счет высокоэластичного восстановления до ве-
88
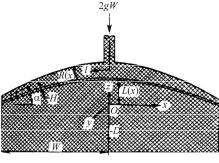
личины, определяемой физико-химическими свойствами полимера, температурой, отношением длины к входному диаметру и напряжением сдвига на стенке головки.
Полимерные листы охлаждают без вытяжки конвективным потоком холодного воздуха (или инертного газа), погружением в ванну с жидкостью или протягиванием между охлаждающими барабанами.
Плоские полимерные пленки обычно вытягивают и ориентируют в одном направлении и затем охлаждают каким-либо из указанных выше способов. Прозрачные пленки изготавливают методом полива и одновременного охлаждения на полированных барабанах.
Уравнения для расчета головок. Большинство листовальных головок имеют либо Т-образную форму с центральным подводом расплава, либо форму плечиков для одежды («вешалка») (рис. 7.4).
В обоих случаях расплав вводится в центр коллектора, имеющего круглое или каплевидное сечение. Из коллектора расплав полимера подается в подводящий канал, из которого выходит через щелевое отверстие, проходящее вдоль всего подводящего канала. Щель имеет ширину H. Ввиду малой кривизны коллектора будем счи-
тать, что dR/dx << 1. Полагая, что давление на входе в коллектор постоянно и что течение изотермическое, необходимо обеспечить однородность условий в поперечном направлении, т.е. постоянный объемный расход полимерного потока при z = 0.
Поскольку размеры щели головки экструдера, формующей листовой полимерный материал, постоянны, то
dP / dz = a = const. |
(7.1) |
Это условие справедливо для всей области потока, ограниченной образующими щелевое отверстие параллельными стенками,
89
в которой линии z = const являются изобарами. Интегрируя уравнение (7.1), получим
[L(0) − L(x)]a = P0 − P′(l), |
(7.2) |
где P′(l) – давление в коллекторе в направлении l; P0 – давление на
входе в коллектор; x и l определяются геометрической формой коллектора.
Дифференцируя уравнение (7.2) по l, получим соотношение между градиентом давления в коллекторе, его формой и градиентом давления в области щелевого отверстия формующей головки:
dP′ |
= a dL . |
(7.3) |
dl |
dl |
|
Это соотношение является основным уравнением для расчета головок, удовлетворяющих указанным выше требованиям, и применимо для любого жидковязкого потока.
Рассмотрим далее течение полимерного потока, подчиняющегося закону Освальда де Виля, через плоскощелевой канал формующей головки. В области плоскопараллельного течения z-компонента искомого уравнения сохранения количества движения сводится к виду
− |
dP |
− |
dτyz |
= 0. |
(7.4) |
|
dy |
dy |
|||||
|
|
|
|
Для полимерной жидкости, подчиняющейся степенному закону, имеем
|
n−1 dvz . |
|
|
τyz = −m |
dvz |
(7.5) |
|
|
dy |
dy |
|
Используя соответствующие граничные условия, отмеченные выше, и предполагая, что течение установившееся, получим после определенного интегрирования (изотермический поток полимерного расплава вдоль отрицательного направления оси z):
90