
Теория технологических процессов учебное пособие
..pdf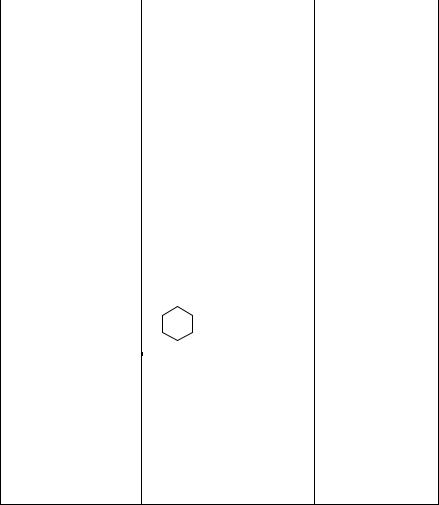
|
|
Таблица 1.1 |
|
Межмолекулярное взаимодействие в полимерах |
|||
|
|
|
|
Полимер |
Повторяющаяся |
Молярная когезия |
|
на отрезке цепи 5А, |
|||
единица |
|||
|
ккал/моль |
||
|
|
||
Полиэтилен |
–СН2СН2– |
1,0 |
|
Полибутадиен |
–СН2СН = СНСН2– |
1,1 |
|
Полиизобутилен |
СН3 |
1,2 |
|
|
| |
|
|
|
–СН2–С– |
|
|
|
| |
|
|
|
CH3 |
|
|
Натуральный каучук |
СН3 |
1,3 |
|
|
| |
|
|
|
–СН2С = CHCH2– |
|
|
Поливинилхлорид |
–СН2СНCl |
2,6 |
|
Поливинилацетат |
–СН2СH– |
3,2 |
|
|
| |
|
|
|
OCOCH3 |
|
|
Полистирол |
–СН2СH– |
4,0 |
|
|
| |
|
|
|
|
|
|
Поливиниловый спирт |
–СН2СHОН– |
4,2 |
|
|
|
|
|
Полиамиды |
–ОС(СН2)хСОNH(СН2)yNH– |
5,8 |
|
Целлюлоза |
CHOH–CHOH |
6,2 |
/\
–CH CH–O–
\/
CH – O
|
СН2ОН
Полимеры с соотношением Tg/Tm ниже 0,5 обладают короткими повторяющимися звеньями (полиэтилен, полиоксиметилен, поливинилхлорид, политетрафторэтилен). Подобные полимеры характеризуют-
11
ся высокой степенью кристалличности. Полимеры с соотношением Tg/Tm выше 0,75 обладают гораздо более сложным строением цепей (полистирол, поливинилацетат, полиэтилентерефталат – «лавсан»).
Таблица 1.2
Влияние межмолекулярного взаимодействия на температуру структурного стеклования некоторых полимеров
Полимер |
Группы влияния |
Е5А, кал/моль |
Тg, C |
Полиэтилен |
–СН2– |
1000 |
–80 |
Полибутадиен |
–СН=СН–, –СН2– |
1100 |
–60 |
Полиизобутилен |
–СН3–, –СН2– |
1200 |
–70 |
Полиизопрен |
–СН=С(СН3)–, –СН2– |
1300 |
–73 |
Поливинилхлорид |
–СНСl–, –СН2– |
2600 |
+70 |
Поливинилацетат |
–ОСОСН3, –СН2– |
3200 |
+30 |
Полистирол |
–С6Н5, –СН2 |
4000 |
+80 |
Поливинилгидроксил |
–СНОН–, –СН2– |
4200 |
+85 |
Полиамид |
–СОNН–, –СН2– |
5000 |
+90 |
Целлюлоза |
–О–, –ОН |
6200 |
+100 |
|
|
|
|
Натуральный шелк |
–СONH–, –СНR– |
9800 |
+120 |
|
|
|
|
Большинство полимеров занимают промежуточное положение и также кристаллизуются, если не являются сополимерами нерегулярного строения.
Температуры плавления некоторых полимеров приведены в табл. 1.3. Видно, что Tm возрастает по мере усложнения строения повторяющегося звена, в том числе с ростом полярности фрагментов.
Отметим также, что существует важный класс низкомолекулярных полимеров (олигомеры) с молекулярной массой менее 10 000. Это, например, жидковязкие эпоксидные смолы и полиэфирные каучуки, отверждаемые в процессе переработки за счет реакции соответствующих функциональных групп полимера и сшивающего аген-
12

та. В итоге, в зависимости от системы отверждения можно получать стеклообразные или высокоэластичные полимерные материалы и изделия на их основе.
|
|
|
|
|
Таблица 1.3 |
|
|
Температура плавления некоторых полимеров |
|||||
|
|
|
|
|
|
|
|
Наименование полимера |
|
Tm, K |
|
Tm, °C |
|
|
|
|
|
|||
|
Полиизобутилен |
|
375 |
|
102 |
|
|
|
|
|
|
|
|
|
Полиэтилен |
|
414 |
|
141 |
|
|
|
|
|
|
|
|
|
Полипропилен |
|
456 |
|
183 |
|
|
|
|
|
|
|
|
|
Полистирол |
|
513 |
|
240 |
|
|
|
|
|
|
|
|
|
Полиэтилентерефталат |
|
557 |
|
284 |
|
|
|
|
|
|
|
|
|
Поливинилхлорид |
|
558 |
|
285 |
|
|
|
|
|
|
|
|
|
Полиэтилентерефталамид |
|
728 |
|
455 |
|
|
|
|
|
|
|
|
В свободном виде полимеры обычно не применяются. Даже рецептуры лаков и пленок содержат в разной комбинации стабилизатор химической стойкости (антиоксидант), краситель (пигмент), сшивающий агент.
Рассмотрим другие наиболее важные и емкие по рецептуре компоненты полимерных материалов, отмечая и их назначение.
1.3. Пластификаторы
Пластификаторы – индивидуальные органические соединения, имеющие в молекуле фрагменты, близкие по полярности к группам, содержащимся в цепях полимеров. Это обеспечивает термодинамическую совместимость твердого раствора «полимер–пластификатор».
Назначение пластификаторов – придание эластичности материалу, уменьшение хрупкости в широком температурном диапазоне эксплуатации соответствующих изделий. Применяются пластификаторы и в качестве энергоемких компонентов, катализаторов скорости
13

процесса горения порохов и твердых ракетных топлив. Кроме того, расплав полимера с пластификатором обладает гораздо более низкой вязкостью в условиях процесса переработки.
1.4. Растворители
Растворители – разбавители или летучие пластификаторы, удаляемые в конечном итоге из полимерного материала. Используются в лаках, эмалях и в некоторых клеях. Назначение – обеспечение высококачественного технологического процесса нанесения соответствующего покрытия.
Таблица 1.4 Пластификаторы, применяемые в полимерных композициях
Наименование |
Структура |
Tg, °C |
Тринитрат глицерина |
CH2(ONO2)–CH(ONO2)–CH2(ONO2) |
+13,5 |
Диэтиладипинат |
C2H5–OCO–(CH2)4–OCO–C2H5 |
+14,0 |
Дибутилфталат |
C6H4(COOC4H9)2 |
–35,0 |
N-дибутилферроцен |
Fe-ди-циклопентен(C4H9O)2 |
–60,0 |
Трибутилфосфат |
PO(C4H9O)3 |
–80,0 |
В табл. 1.4 представлены температуры стеклования (или кристаллизации) некоторых пластификаторов. Видно, что жидковязкое состояние указанных соединений существенно зависит от химического строения.
1.5. Дисперсные наполнители
Дисперсные наполнители – твердые частицы в виде порошка.
Степень дисперсности в международной системе единиц (СИ): 1 миллиметр (мм) = 10–3 м;
1 микрометр (мкм, микрон, µ) = 10–6 м; 1 нанометр (нм) = 10–9 м; 1 пикометр (пм) = 10–12 м.
14
Следует помнить также, что в 1 мм содержится 1000 мкм, а в 1 мкм – 10 000 ангстрем (Å).
Органические наполнители: сажа, графит, целлюлоза, древесная мука.
Неорганические наполнители: кварц, сажа белая или аэросил (SiO2); мел (CaCO3); асбест, тальк, слюда (природные комплексы оксидов Mg, Si, K, Al в различных комбинациях); алюминий и перхлорат аммония как компоненты твердых ракетных топлив.
Металлические наполнители: порошки алюминия, меди, железа, свинца и их сплавы.
Назначение – придание потребительских качеств изделиям, например, усиление (армирование) конструкций, удешевление продукции, повышение стойкости при эксплуатации полимерных материалов в агрессивных средах, а также биозащита подводной части судов от морских организмов.
1.6. Волокнистые наполнители
Волокнистые наполнители – высокопрочные волокна (нити) различной природы, получаемые вытяжкой расплава через фильеры, кристаллизацией усов или крекингом (обугливанием при высоких температурах без доступа кислорода) высокопрочных полимеров полиамидного типа (табл. 1.5).
Приведенные данные показывают, что стальная проволока значительно уступает по удельной прочности (разрывная прочность, отнесенная к плотности материала) нитям из современных полимерных соединений. Это обстоятельство позволило создать полимерные композиционные материалы конструкционного назначения, которые нашли широкое применение в авиаракетостроении, судостроении, строительстве. При этом волокна вносятся в будущий материал методом намотки нитей на соответствующую технологическую оснастку (рис. 1.2) с одновременным поливом полимерного связующего в зону намотки или используются в виде ткани, изготовленной отдельно, пропитываемой связующим послойно.
15
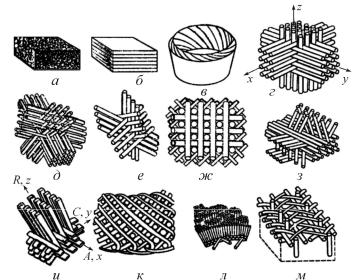
|
|
|
Таблица 1.5 |
Основные свойства армирующих волокон |
|
||
|
|
|
|
Наименование волокна |
Плотность, |
Напряжение |
Удельная |
|
г/см3 |
разрыва, МПа |
прочность, км |
Поли-п-фениленбензо-бис- |
1,56 |
4500 |
294 |
оксазол, «zylon» (Япония) |
|
|
|
|
|
|
|
Полиаромамид, «nylon», США |
1,55 |
260 |
168 |
|
|
|
|
Стеклянный ус |
2,45 |
220 |
90 |
|
|
|
|
Полиалифамид, «капрон» |
1,14 |
80 |
56 |
|
|
|
|
Полиэтилентерефталат, «лавсан» |
1,31 |
55 |
53 |
|
|
|
|
Хлопок, лен |
1,50 |
55 |
37 |
|
|
|
|
Сталь легированная |
7,85 |
280 |
36 |
|
|
|
|
Ацетат целлюлозы |
1,52 |
40 |
23 |
|
|
|
|
Рис. 1.2
16
На рис. 1.2 приведены схемы расположения волокон в углеродуглеродных композиционных материалах: а – хаотичная, б – слоистая, в – розеточная, г–з – ортогональная, и – аксиально-радиально- окружная, к – аксиально-спиральная, л – радиально-спиральная, м – аксиально-радиально-спиральная.
По физико-механическим свойствам полимерные материалы этого типа превосходят металлические (табл. 1.6). При одинаковой массе (весе) «пластики» прочнее сталей в несколько раз! И наоборот – при одинаковой прочности конструкции «пластиковая» оказывается легче металлической также в несколько раз.
Таблица 1.6 Характеристики конструкционных полимерных материалов
Наименование материала |
Плотность, |
Напряжение |
Удельная |
|
г/см3 |
разрыва, МПа |
прочность, км |
УККМ* |
1,6 |
420 |
262 |
Органопластик, «kevlar» |
1,3 |
280 |
215 |
(США) |
|
|
|
СВАМ** |
2,0 |
100 |
50 |
Сталь легированная |
7,8 |
280 |
36 |
Титановая сталь |
4,5 |
100 |
22 |
*УККМ – углерод-композитный конструкционный материал;
**СВАМ – стекловолокнистый армированный материал.
Кроме этого, полимерные материалы отличаются высокой стойкостью при эксплуатации в химически агрессивных средах, включая морскую воду. Так, например, стеклопластиковые трубы для жилищ- но-коммунального хозяйства имеют расчетный ресурс около 100 лет.
1.7. Cмешение
Cмешение – процесс формирования статистически однородной системы, содержащей ингредиенты конечного полимерного материала в соответствии с рецептурой. Исключение составляют технологи-
17
ческие стадии намотки или послойной укладки волокнистых компонентов (корпуса, трубы, емкости).
Смешение компонентов полимерных материалов в большинстве случаев происходит в ламинарном режиме течения из-за высокой вязкости среды. Напомним, что переход к турбулентности потока определяется с помощью критерия Рейнольдса ( Re =lρv / η, где – l –
характеристический размер сечения, ρ – плотность, v – скорость потока, η – вязкость композиции).
Созданные аппараты и смесительные установки позволяют обеспечивать периодический или непрерывный процессы изготовления сыпучих смесей, включая полифракционный наполнитель, а также жидковязких связующих. Технологические комплексы позволяют изготавливать конечные полимерные композиции и формовать различные изделия на их основе.
Статистический критерий процесса смешения. При описа-
нии однородности смеси обычно предполагают, что диспергируемая (распределяемая) фаза (например, частицы сажи) и дисперсионная среда (например, каучук) состоят из частиц-молекул одного порядка по размеру.
Теоретически показано, что разброс значений концентрации подчиняется биномиальному закону распределения. Это означает: вероятность P(x) присутствия в отобранной пробе х частиц диспергируемой фазы равна плотности биномиального распределения:
P(x) = |
N ! |
qb (1 |
−q)N −b , |
(1.1) |
||
|
|
|||||
b!(N −b)! |
||||||
|
|
|
|
где N – число частиц распределяемой фазы, содержащихся в пробе; b – число частиц дисперсионной среды в пробе; q – относительное содержание диспергируемой фазы. Естественно, под числом частиц можно понимать и массовое содержание компонентов в пробе.
При этом дисперсия распределения σ2 (генеральная дисперсия) определится из выражения
σ2 = q(1−q) / N. |
(1.2) |
18
Проверка на гомогенность (однородность) сводится к сравнению экспериментально определенных значений дисперсий концентраций диспергируемой фазы с характеристиками биномиального распределения.
Величина выборочной дисперсии концентрации диспергируемой фазы в отобранных пробах s2 определяется по формуле
|
1 |
M |
|
|
s2 = |
∑(xi − x )2 , |
(1.3) |
||
|
||||
|
M −1 i−1 |
|
где М – число проб; xi – содержание (концентрация) частиц диспергируемой фазы в каждой пробе; x – среднее значение доли фазы дисперсных частиц в смеси для М проб,
|
1 |
M |
|
|
x = |
∑ xi . |
(1.4) |
||
|
||||
|
M i−1 |
|
Для достоверного статистического анализа необходимо отбирать не менее 10 проб из разных мест емкости для смеси. Сравнивая среднее значение q и генеральную дисперсию σ2 с соответствующими значениями, определенными экспериментально, можно сделать вывод о том, является ли различие сравниваемых проб смеси случайным или оно указывает на существование систематического отклонения.
Такое сравнение возможно при соблюдении двух условий: вопервых, отбор проб должен быть произведен таким образом, чтобы значения х не сильно отличалось от q; во-вторых, число частиц в каждой пробе и их содержание должны удовлетворять соотношению
Nq(1−q) ≥9. |
(1.5) |
В этом случае биномиальное распределение может быть аппроксимировано нормальным распределением с теми же математическим ожиданием и дисперсией.
Для оценки значимости наблюдаемого расхождения рассчитывают величину нормированного отклонения z по критерию Стьюдента:
19

z = |
x −q |
M , |
(1.6) |
|
s |
||||
|
|
|
||
с помощью которого сравнивают |
экспериментальные |
результаты |
с табличными данными для функции нормированного (безразмерного) нормального (гауссового) распределения.
На практике решающее значение имеет не характер распределения диспергируемого вещества в полимерной композиции (случайный или неслучайный), а степень отклонения имеющегося распределения от случайного, т.е. степень однородности смешения. Наиболее распространенные критерии оценки степени однородности смешения основаны на использовании статистических величин. По мере приближения смеси к случайной выборочная дисперсия s2 приближается к предельному минимальному значению генеральной дисперсии σ2.
Наиболее простая форма распространенного критерия степени однородности полимерного композиционного материала (качества смешения) – индекс смешения:
I |
= |
σ2 |
. |
(1.7) |
|
s2 |
|||||
|
1 |
|
|
Критерий I1 изменяется в диапазоне от 0 до 1. Значение I1 = 0 соответствует совершенно несмешанной системе. При I1 = 1 композиция идеально смешена и является однородной в макросмысле.
Масштаб разрешения. Достоверность или порог чувствительности в определении степени однородности смеси существенно зависит от объема пробы, который должен превышать некоторый критический размер – масштаб разрешения. Эта статистическая выборка определяется как минимальная по объему в исследуемой области, в которой наличие неоднородности делает смесь непригодной для практического применения. Так, если масштаб разрешения соизмерим с размерами крупной фракции дисперсного наполнителя, то определить степень смешения оказывается практически невозможно. Статистическое определение минимальных размеров масштаба разрешения следует из неравенства (1.5).
20