
Машины и оборудование для разработки мерзлых грунтов
..pdf
Недостатками этой машины являются быстрый износ привода вибратора, трудные условия работы оператора, сильные динамические нагрузки, действующие на базовую машину и, как следствие, частые поломки.
Существуют конструкции виброклиньев, установленных на прицепах. Такие схемы компоновки сохраняют долговечность базовой машины, но эти конструкции обладают малой маневренностью и зависимостью от внешнего источника питания (привод вибратора – электрический).
Расчет основных параметров:
1.Назначаются габаритные размеры, вес (Q).
2.Задаются удельной энергией удара Туд и определяют необходимую энергию одного колебания рабочего органа Т, кг·м:
Т = Тудl,
где l – длина режущей кромки клина, м.
3. Максимальная скорость колебательного движения (м/с)
V 2Tg . |
|
к |
Q |
|
(53)
(54)
4.Назначается угловая скорость вращения дисбалансов ω, 1/с.
5.Амплитуда колебаний (м)
A |
Vк |
, |
|
|
||
|
||||||
|
|
|
ω |
|||
|
|
|
|
|
||
A |
2Tg / Q |
. |
||||
|
||||||
|
|
|
|
6. Статический момент дисбалансов (кг·м)
GR 2gTQ
(кω) .
7. Мощность привода (кВт)
N 10 7 (GR)2 ω3 /(3Q) .
(55)
(56)
(57)
(58)
81
4.РАБОЧИЕ ОРГАНЫ ЗЕМЛЕРОЙНЫХ МАШИН
СГАЗОДИНАМИЧЕСКИМ ВОЗДЕЙСТВИЕМ НА ГРУНТ
Разработка мерзлых грунтов отличается широким разнообразием методов производства, постоянно возрастающими объемами, высокой энергоемкостью и стоимостью (табл. 8) [4].
Проблема разработки мерзлых грунтов в настоящее время приобретает большую актуальность и имеет важное народнохозяйственное значение. Основная задача – совершенствование существующего и создание нового рабочего оборудования, отличающегося высокой производительностью и универсальностью, основанного на эффективных и рациональных принципах работы. Перспективным направлением повышения эффективности землеройной техники наряду с повышением мощности базовых машин является интенсификация их рабочих процессов. В частности, подача в зону разрушения массива газодинамического импульса обеспечивает интенсивное разупрочнение грунтов.
Таблица 8
Сравнительные технико-экономические показатели существующих методов разработки мерзлых грунтов
Метод разработки |
Энергоем- |
Трудоемкость, |
Стоимость, руб/м3 |
|
кость, |
3 |
|
|
|
|
кВт·ч/м3 |
чел.·дн/м |
(в ценах 1984 г.) |
|
Термический: |
|
|
|
|
с предохранением от промерзания |
1,36–0,10 |
0,002–0,020 |
0,015–0,8 |
|
с оттаиванием: |
|
|
|
|
|
|
|
|
|
огневым |
130 |
0,11–0,14 |
0,3–2,9 |
|
|
||||
|
|
|
|
|
с пароводяным |
190 |
0,16 |
0,67–0,92 |
|
|
|
|
|
|
электрическим |
30–95 |
0,10–0,28 |
0,60–1,80 |
|
|
|
|
|
|
Ручная разработка |
|
1,9 |
4,6 |
|
|
|
|
|
|
Механизированным ручным инструментом |
17,7 |
0,57–0,85 |
2,3 |
|
|
|
|
|
|
Буровзрывной |
1,4 |
0,048–0,060 |
0,52–0,66 |
|
|
|
|
|
|
Термический: |
|
|
|
|
резание |
5,45 |
0,023–0,009 |
0,32–1,46 |
|
|
|
|
|
|
удар |
0,55 |
0,025–0,060 |
0,25–0 90 |
|
|
|
|
|
|
вибрация |
1,64 |
0,044–0,080 |
0,43–0,80 |
|
рыхление |
0,35–1,50 |
0,02–0,03 |
0,1–0,3 |
|
|
|
|
|
|
Разрушение рабочими органами с замкнутым |
|
|
|
|
силовым потоком |
0,25 |
0,002 |
0,17 |
|
|
|
|
|
|
82
Землеройные машины с газодинамическим воздействием на среду можно эффективно использовать для разрушения грунтов повышенной прочности. При рабочем давлении газа 4 МПа и объеме камеры 0,125 м3 практически возможно разрабатывать грунты до VI категории прочностью Суд = 70...75.
Энергоемкость разработки прочных грунтов рабочим органом газодинамического действия с учетом затрат только энергии газа на разрушение и перемещение грунта без механического воздействия составляет 2,4–2,8 кВт·ч/м3. Это соответствует энергоемкости таких землеройных машин с механическим воздействием на грунт, как баровые машины на базе многоковшовых экскаваторов и рыхлители. Производительность землеройной машины с рабочим органом газодинамического действия при разработке грунтов VI категории может достигать 200–250 м3/ч при частоте 10 газодинамических импульсов в минуту, что больше производительности машин традиционного типа более чем в 2,5 раза. Увеличение частоты газодинамических импульсов является одним из направлений получения более высокой производительности.
Широко исследованы машины с газоимпульсными устройствами двух типов: работающие на топливовоздушной смеси и на твердом топливе (пороховые заряды и заряды типа «Гидрокс»). Испытания твердотопливных газоимпульсных (взрывомеханических) устройств доказали возможность эффективной разработки траншей глубиной до 1,2 м. Удельный расход взрывчатых веществ составил 0,8–1,2 кг/м3. Это соответствует расходу обычных взрывчатых веществ при взрывах на выброс. Проведены исследования щелерезнозарядных машин, осуществляющих непрерывное нарезание вертикальной щели в мерзлом грунте и заполнение ее взрывчатыми веществами: взрыв такого заряда позволяет получить траншею длиной 300–500 м, шириной по верху 6–8 м и глубиной 2,5 м.
Щелевзрывной метод рыхления мерзлых грунтов внедрен на ряде крупных строительных объектов. Он заключается в нарезании землеройной машиной трех щелей с укладкой в средней щели удлиненных или рассредоточенных зарядов взрывчатых веществ. При таком
83
методе рыхления мерзлых грунтов сокращается объем ручных работ по зарядке камер, улучшается качество дробления мерзлого грунта, снижается разлет кусков, регулируется направленность действия взрыва за счет того, что щели во взрываемом массиве образуют дополнительные свободные поверхности и при ударе кусков грунта о поверхность компенсирующей щели происходит дополнительное дробление за счет запасенной при распространении волны сжатия кинематической энергии. Положительное значение компенсирующих щелей заключается в том, что они увеличивают объем разрыхленного мерзлого грунта. Главные недостатки – применение опасных в обращении и дорогостоящих взрывчатых веществ, а также дополнительные средства и затраты времени на распределение взрывчатых веществ по длине и высоте щели, последующее их засыпание и уплотнение. Кроме того, использование взрывчатых веществ ограничивает область применения данного способа из-за большой зоны разлета кусков мерзлого грунта, возникновения ударных волн, которые отрицательно влияют на конструкции машин и сооружений.
Производительность при рыхлении мерзлых грунтов щелевзрывным методом составляет 10–50 м3/ч.
Другим направлением механизации взрывных работ является создание оборудования по схеме с механизированной подачей зарядов массой 1–2 кг, взрываемых в непосредственной близости от отвала. Проведенные ВНИИземмаш лабораторные и полевые испытания оборудования отвального типа показали практическую осуществимость такой схемы взрывомеханической разработки грунта. Эта схема позволяет создать производительную и относительно легкую землеройную машину с двигателем небольшой мощности. Действие взрыва при данной схеме подобно действию взрыва на выброс; удельный расход ВВ при испытаниях составил 1,5–1,8 кг на 1 м3 грунта, что соответствует расходу ВВ при обычных схемах взрывания на выброс.
Характерным для последнего способа является интенсивное рыхление грунта и частичное дробление твердых включений в зоне перед отвалом, что обеспечивает снижение усилий внедрения отвала в грунт и возможность разработки плотных и мерзлых грунтов.
84
Производительность оборудования с механизированной подачей заряда определяется частотой циклов подачи и взрывания зарядов. При технически осуществимой частоте взрывов и ширине отвала 3 м производительность землеройной машины может соста-
вить 2000–3000 м3/ч.
Исследование возможности использования метательных ВВ (порохов) для разработки грунтов было проведено ВНИИземмаш в 1969–1972 гг. Принципиальная схема рабочего органа, использующего энергию метательных ВВ, представлена в табл. 9. Рабочий орган состоит из отвала с ножом и камеры сгорания, в которую периодически подаются пороховые заряды. Верхняя плоскость полого ножа выполнена в виде решетки. Камера сгорания имеет затвор с устройством инициирования зарядов. Над камерой монтируется кассета с зарядами. На отвале установлен рассекатель, направляющий выбрасываемый грунт в сторону.
Многочисленные исследования показали техническую осуществимость рабочих органов взрывомеханического действия. Производительность землеройного оборудования с подобными рабочими органами определяется в основном расходом ВВ и частотой циклов. На экспериментальном оборудовании была достигнута частота 20 циклов в минуту при массе заряда 0,9 кг и удельном расходе ВВ 0,8–1,0 кг на 1 м3 грунта. Техническая производительность землеройной машины с такими параметрами, снабженной двумя камерами сгорания, составляет 2000–2500 м3/ч. Рассчитанный по результатам испытаний механический КПД взрывомеханической установки достигает 23 %.
Отрицательными сторонами использования порохов являются относительно высокая стоимость работ и повышенная опасность эксплуатации оборудования.
Копание грунта отвальным рабочим органом с газодинамическим устройством осуществляется с использованием как механической энергии, которая передается на рабочий орган от движителя, так и энергии сжатого газа высокого давления, передаваемой непосредственно на грунт, минуя движитель [4].
85

Таблица 9
Основные схемы взаимодействия рабочего оборудования с грунтом при газодинамическом интенсификаторе [25]
Схема взаимодействия обору- |
Ожидаемый эффект |
|||||
|
|
|
дования с грунтом |
|||
|
|
|
|
|||
|
|
|
|
|
|
Грунт разрушается, отделяется от массива и отбрасывается |
|
|
|
|
I |
||
|
Р |
|
|
|||
|
|
|
|
за пределы воронки газодинамическим импульсом. Отвально- |
||
|
|
к |
|
|
|
|
|
|
|
|
|
|
|
|
|
|
|
|
|
ножевая система подрезает неровности дна и боковых стенок |
|
|
|
|
|
|
Рк |
|
|
|
|
|
|
|
II |
Грунт отделяется от массива отвально-ножевым оборудованием. |
||
|
|
|
|
|
|
|
Накапливаемый перед отвалом грунт отбрасывается потоком |
||||
|
|
|
|
|
|
|
|
|
|
|
|
|
|
|
|
|
|
|
|
|
|
|
сжатого газа |
|
|
|
|
|
|
|
|
|
|
|
|
|
|
|
|
|
|
|
|
|
|
|
|
Рк |
|
|
|
|
|
III |
|
Энергия газа используется для рыхления грунта в области ножа. |
|||
|
|
|
|
|
|
Призма грунта формируется отвально-ножевым оборудованием, |
|||||
|
|
|
|
|
|
|
|
|
|
|
отбрасывание призмы осуществляется потоком сжатого газа |
|
|
|
|
|
|
|
|
|
|
|
|
|
|
|
|
|
|
|
|
|
|
|
|
|
|
|
|
|
|
|
|
|
|
|
|
|
|
|
|
|
|
|
|
|
|
|
Энергия газа используется только для интенсификации процесса |
Рк |
|
|
|
|
|
|
IV |
||||
|
|
|
|
|
|
рыхления грунта. Накапливаемая перед отвалом призма грунта |
|||||
|
|
|
|
|
|
|
|
|
|||
|
|
|
|
|
|
|
|
|
|
|
|
|
|
|
|
|
|
|
|
|
|
|
удаляется отвально-ножевой системой механическим путем |
|
|
|
|
|
|
|
|
|
|
|
|
|
|
|
|
|
|
|
|
|
|
|
Сочетание механического воздействия отвально-ножевой системы с газоимпульсным в процессе копания позволяет получить четыре основные схемы разработки грунтов (см. табл. 9).
По схеме I грунт разрушается, отделяется от массива и отбрасывается за пределы воронки газодинамическим импульсом. Такая схема работы может быть использована при копании траншей глубиной 1,5–2,0 м за один проход.
Схемы II, III и IV характеризуют работу оборудования при наличии призмы волочения. По схеме II грунт разрушается и отделяется от массива отвально-ножевым оборудованием. Призма грунта перед отвалом отбрасывается из траншеи потоком сжатого газа. Рассматриваемый вариант позволяет разрабатывать грунты послойно.
86

При схеме III энергия газодинамических импульсов используется только для рыхления грунта, находящегося в области ножа, активизируя его внедрение в массив. Призма грунта формируется от- вально-ножевым оборудованием; последующее отбрасывание призмы осуществляется потоком газа специального назначения. Схема работы предполагает оборудование рабочего органа двумя газоимпульсными камерами. Одна из камер должна работать с большей частотой газодинамических воздействий, чтобы поток газа разрушал грунт у ножа, вторая, с меньшей частотой, должна периодически отбрасывать призму грунта в сторону. Оборудование по данной схеме может быть и с одной камерой. Но последняя должна иметь возможность подавать сжатый газ в соответствующие зоны отвала. Такой вариант приводит к снижению среднего сопротивления копанию как за счет предварительного разрушения грунта, так и за счет отброса призмы волочения потоком сжатого газа.
При схеме IV энергия газовых импульсов используется только для интенсификации процесса рыхления грунта. Накапливаемая перед отвалом призма грунта удаляется отвально-ножевой системой механическим путем. Данная схема позволяет эффективно разрабатывать грунты при давлении 0,8–1,5 МПа. При этом можно использовать рабочее оборудование без элементов системы сжигания топлива. Достаточно подавать в рабочую камеру сжатый воздух от компрессора.
Давление газа рекомендуется определять на базе анализа уравнения силового баланса взаимодействия потока сжатого газа с грунтом (рис. 38).
Объем грунта, разрушаемого и перемещаемого или только разрыхленного за один цикл,
V |
h Bа cosα |
р |
Bh2ctgα |
сд |
2 |
, |
(59) |
гр |
р |
p |
|
|
|
где hр – глубина резания;
В – ширина рабочего органа; а – ширина ножа; αр – угол резания;
αсд – угол сдвига грунта.
87
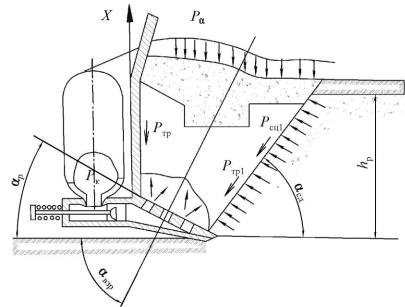
Рис. 38. Схема взаимодействия импульса сжатого газа с грунтом
Давление газа в рабочей камере, необходимое для разрушения и перемещения грунта, определяют из уравнения равновесия сил, характеризующих процесс. Сила сцепления, действующая на отделяемый элемент грунта по поверхности сдвига,
|
Pсц1 BhpCw / sin αсд , |
|
|
(60) |
||||
где Сw – коэффициент сцепления грунта, МПа; |
|
|
|
|||||
сила трения по этой поверхности |
|
|
|
|
|
|||
Р |
γ |
гр |
Bh2ctgα |
сд |
tgρ /(2cosα |
сд |
) , |
(61) |
тр1 |
|
p |
|
|
|
где γгр – объемный вес грунта; ρ – угол внутреннего трения.
В зоне контакта отвальной поверхности с грунтом возникает сила трения Ртр грунта по металлу:
Pтр 1σBhp tgδ Bhp , |
(62) |
где μ1 – коэффициент трения грунта по металлу;
88
σ – предел прочности грунта, для ориентировочных расчетов можно принять σ ≈ Cw, Сw – коэффициент сцепления грунта;
Вhр – площадь отвала.
Давление газа приближенно определяют по эмпирической формуле
Pг qгVгр Pк /(Vк К) , |
(63) |
где qг – удельный расход газа (м3 газа / м3 грунта); Рк – давление в камере сгорания; К – показатель адиабаты расширения газов; Vк – объем камеры сгорания.
4.1. Основные параметры и режимы работы оборудования
Важным этапом проектирования рабочего оборудования с газодинамическим интенсификатором является установление основных параметров рабочего органа и режима его работы. Исходными данными расчета являются производительность машины, тип, физикомеханические характеристики разрабатываемого грунта и вероятность их появления, функциональное назначение машины (для разработки траншей с конкретными параметрами – шириной и глубиной Н; для производства вскрышных работ и т.д.).
По заданным физико-механическим характеристикам грунта
ипараметрам разрабатываемой траншеи согласно рекомендуемым зависимостям определяют силу сопротивления грунта копанию. Для этого можно использовать программу для ЭВМ. Рассчитанное значение силы сопротивления копанию является основой для выбора тягового усилия базовой машины. Затем определяют удельный расход газа
в соответствии с полученными рекомендациями.
Подачу компрессора (м3/с) находят по удельному расходу газа
изаданной производительности машины [4]:
Пк Пq /(K pз λ 3600) , |
(64) |
где П – производительность машины, м3/ч;
q – удельный расход газа (м3 газа / м3 грунта);
89
Крз – отношение давления рз зарядки камеры к атмосферному давлению ра;
λ – степень повышения давления за счет сжигания топлива в газоимпульсной камере, λ = 7...8.
Далее определяют объем грунта, разрабатываемого рабочим органом за один газодинамический цикл:
V Bh2 /(2tgα |
сд |
) , |
(65) |
|
|
|
где В – ширина отвала, м; h – глубина копания, м;
αсд – угол, образуемый между передней поверхностью сдвига и горизонтальной плоскостью (экспериментальное значение αсд = = 45...50°).
Номинальное давление газа в камере
рк.ном рз λ .
Суммарный объем газоимпульсных камер, установленных на рабочем органе, можно определить по удельному расходу воздуха:
Vк qVpa / pк .
Кроме того, суммарный объем газоимпульсных камер можно вычислить по известным значениям энергоемкости и соответствующему коэффициенту эффективности.
Глубина копания отвальным рабочим оборудованием газодинамического действия определяется, во-первых, тяговым усилием и типом грунта; во-вторых, параметрами газодинамического устройства (объемом камеры и номинальным давлением) и технологической схемой взаимодействия рабочего органа с грунтом. Для схемы I (см. табл. 9) рациональную глубину копания определяют параметры газодинамического устройства. Для схемы II необходимо определять глубину копания по тяговому усилию и по энергетическим параметрам газоимпульсного устройства и выбирать наименьшее значение. В схемах III и IV глубину копания определяет тяговое усилие. Наибольшая глубина копания 0,7–1,4 м в зависимости от типа грунта может быть достигнута по схеме I при давлении газа в камере 5–6 МПа.
90