
- •Т.В. КОСТЫГОВА
- •ТЕХНОЛОГИЯ ПРОИЗВОДСТВА ПРОВОДОВ
- •Костыгова Т.В.
- •1. ПРОИЗВОДСТВО ПРОВОЛОКИ
- •1.1. Металлы, обрабатываемые в кабельной промышленности
- •1.2. Изготовление медной и алюминиевой катанки
- •1.4.3. Прокатные станы
- •1.7. Травление катанки
- •1.8. Скальпирование медной катанки
- •1.10. Оборудование для волочения проволоки
- •1.12. Отжиг медной и алюминиевой проволоки
- •2. ПРОИЗВОДСТВО ОБМОТОЧНЫХ ПРОВОДОВ
- •2.1. Классификация обмоточных проводов
- •3.2.Способы наложения эмалевой изоляции
- •expfciTo)
- •3.3.2. Расчет концентрации растворителя для случая, когда скорость процесса определяется внешним массообменом (Bi < 1)
- •3*5. Условия возникновения газообразных включений на стадии пленкообразования
- •UooJ
- •3.7.1. Агрегаты для эмалирования проволоки диаметром 0,015-0,05 мм
- •3.7.4. Устройство катализаторов
- •3.8. Особенности эмалирования проводов из расплава смол
- •4. ПРОИЗВОДСТВО ОБМОТОЧНЫХ ПРОВОДОВ
- •4.1.1. Обмоточные машины для наложения изоляцни из натуральных и синтетических волокон
- •4.2. Подразделенные и транспонированные обмоточные провода
- •4.4. Обмоточные провода с пластмассовой изоляцией
- •ТЕХНОЛОГИЯ ПРОИЗВОДСТВА ПРОВОДОВ
1.10. Оборудование для волочения проволоки
Устройства, на которых осуществляется волочение при помощи одной или нескольких волок и тяговых механизмов, называются волочильными машинами.
Они могут быть однократного (одна волока) и многократного (до 25 волок) волочения.
Протягивание проволоки через волоки осуществляется с помощью тя говых барабанов (роликов), создающих силу волочения за счет трения, возникающего между поверхностью проволоки и поверхностью роликов. По мере прохождения волок диаметр проволоки уменьшается, а скорость ее движения возрастает.
Так как в процессе волочения происходит уменьшение сечения без изменения объема проволоки, то длина исходного отрезка заготовки уве личивается после каждого прохода пропорционально вытяжке. Для осуще ствления многократного волочения необходимо согласовать скорости тя говых устройств. В идеальном" случае должен соблюдаться закон равенства секундных объемов металла, проходящего через каждую волоку:
V\Fx =V2F2 =... = VnF„,
где V- скорость движения проволоки;
F - ее поперечное сечение при прохождении соответствующей волоки. По размерам протягиваемой проволоки различают следующие классы
волочильных машин:
-тяжелого волочения (фасонная проволока сечением до 300 мм2 и круглая диаметром больше 4,0 мм);
-грубого волочения (диаметр 1,0-4,5 мм);
-среднего волочения (диаметр 0,3-1,25 мм);
-тонкого волочения (диаметр 0,15-0,4 мм);
-тончайшего волочения (диаметр <0,15 мм).
Самая тонкая медная проволока, изготовляемая методом Золочения, имеет диаметр 10-12 мкм.
Машины однократного волочения применяются в основном для про изводства проволоки крупных сечений и являются, таким образом, маши нами тяжелого волочения.
В кабельной промышленности встречаются две разновидности таких машин: с горизонтальным и вертикальным тяговым барабаном. На маши нах с горизонтальным тяговым барабаном протягивают изделия самых крупных сечений: круглую проволоку диаметром больше 8 мм и фасонную проволоку сечением 300-500 мм2
Вертикальный тяговый барабан имеет коническую форму. Проволока после волоки поступает на нижнюю кромку барабана, а в верхней части барабана происходит сматывание проволоки в бухту.
Применение машин однократного волочения целесообразно в случаях, когда требуется небольшое суммарное обжатие, которое можно осущест вить за 1-2 прохода.
К машинам однократного волочения относятся машины типа B-I/750, B-I/550.
Волочильные машины многократного волочения делятся на два ос новных типа: без скольжения и со скольжением.
Вмашинах без скольжения скорости движения проволоки по выходе из волок равны окружным скоростям соответствующих тяговых роликов и барабанов. У этих машин на роликах имеется достаточный запас проволо ки, за счет которого можно временно останавливать и вновь пускать от дельные ролики, не прекращая работы всей машины. В случае остановки какого-либо промежуточного ролика запас проволоки на предшествующем ролике увеличивается, а работа последующего ролика продолжается до тех пор, пока есть проволока на остановленном ролике.
Вмашинах со скольжением скорость движения проволоки чаще всего меньше окружной скорости роликов, т.е. имеет место скольжение прово локи относительно тяговых роликов. Количество проволоки на роликах ограничивается одним или несколькими витками, и остановка одного ро лика вызывает необходимость остановки всей машины.
Машины без скольжения в кабельной промышленности используются
для волочения круглой алюминиевой проволоки. Скорость волочения до 16 м/с, количество волок 6- 10.
Машины многократного волочения без скольжения магазинного типа с индивидуальным приводом барабанов (ВМА-6/450; ВМА-8/450; ВМА10/450) применяются для волочения круглой проволоки диаметром более 1,0 мм. Они имеют 6-10 волок.
Машины многократного волочения со скольжением используются для волочения круглой и фасонной проволоки. Основным условием работы машины со скольжением является условие постоянства секундных объе мов проволоки, проходящей через все волоки:
V\F\ = V2F2= =FnFn = const,
где V\y V2 t...,V„ - скорость движения проволоки в 1, 2, п-й волоках; F\,F 2 y...yFn- сечение проволоки в 1, 2, и-й волоках.
На машинах со скольжением вытяжки и скорости проволоки по про ходам должны быть согласованы с окружными скоростями тяговых роли ков. В идеальном случае желательно, чтобы после каждой волоки скорость
движения проволоки и окружная скорость соответствующего ролика были равны. Но практически это не выполнимо, так как при недостаточной точ ности изготовления волок или их неравномерном износе фактическая ско рость движения проволоки отличается от расчетной. Если скорость движе ния проволоки больше скорости ролика, то ролик будет тормозить процесс волочения. Проволока, выходящая из последующей волоки, примет на себя усилие волочения через предыдущую волоку, что приведет к обрыву. По этому тяговые ролики машин со скольжением вращаются с некоторым опережением по отношению к движению проволоки, т.е. имеют запас по скорости.
Для определения относительной величины скольжения р0Тн использу ется следующее выражение:
Ротн - |
• 100% , |
где Кр - скорость вращения ролика; Упр - скорость движения проволоки.
Наглядное представление об опережении (м/мин) дает абсолютная ве личина скольжения
Рабе пр*
Нормальным считается скольжение 3-5 %. Увеличение скольжения ухудшает качество поверхности проволоки, вызывает ускоренный износ роликов, приводит к дополнительным потерям мощности на преодоление сил трения.
Машины со скольжением различаются по конструкции и расположе нию тяговых роликов. Ролики могут быть цилиндрическими и ступенча тыми, могут располагаться вертикально или горизонтально.
У машин с цилиндрическими тяговыми роликами окружная скорость каждого последующего ролика возрастает за счет увеличения его скорости вращения. Диаметры всех роликов одинаковы. Эти машины могут иметь от 5 до 9 волок (СМВ-1-5; СМВ-1-9 и др.) У машин со ступенчатыми тя говыми роликами окружная скорость после волоки возрастает за счет уве личения диаметра ролика-ступеньки. После выхода из волоки проволока поступает на следующую ступеньку тягового ролика. Эти машины наибо лее распространены в кабельной промышленности. Они могут иметь до 25 волок (табл. 1.4).
|
Технические характеристики машин многократного |
Таблица 1.4 |
|||
|
|
||||
|
|
волочения со скольжением |
|
||
Тип |
Количество |
Диаметр |
Диаметр |
Максим. |
Мощность |
машин |
волок |
заготовки, |
готовой |
скорость |
двигателя, |
|
|
мм |
проволоки, |
волочения, |
кВт |
СМВ-П-9 |
|
|
мм |
м/с |
|
9 |
8-7,2 |
4-1,6 |
15,4 |
100 |
|
ВМ-13-м |
13 |
8-7,2 |
2,3-1,2 |
15,4 |
100 |
МР 9 |
12 |
3,2-1,25 |
1,0- 0,4 |
20 |
40 |
С-212 |
19 |
2,5-1,2 |
0,4—0,2 |
25 |
28 |
При заправке волочильных машин необходимо заострить конец про тягиваемой проволоки таким образом, чтобы он свободно проходил через отверстие волоки. Для этого пользуются специальными острильными станками, которые имеют валки с нарезанными на них ручьями перемен ного сечения. При вращении валков размер калибра изменяется и введен ный в калибр конец проволоки обжимается.
Заостренная проволока протягивается через волоки на специальных затяжных станках или с помощью барабанов (роликов) самой волочильной машины.
Для размотки и подачи проволоки в волочильные машины применя ются отдатчики различных конструкций. Различаются два типа отдатчи ков: инерционные - с подвижной катушкой или бухтой и безынерционные - с неподвижной катушкой или бухтой.
Инерционный отдатчик представляет собой деревянный или металли ческий конус, который вращается вместе с бухтой вокруг вертикальной оси. Недостаток такого отдатчика - большая инерционность, иногда она является причиной запутывания или даже обрыва проволоки.
В безынерционном отдатчике заготовка снимается витками с уложен ной на полу или стеллаже бухты. Во избежание запутывания проволоки направляющий ролик должен быть установлен достаточно высоко. Так как бухта лежит неподвижно, то можно, не останавливая волочильной маши ны, приварить к нижнему концу установленной бухты верхний конец сле дующей бухты, в этом случае обеспечивается непрерывность подачи заго товки.
Отдатчики с неподвижной катушкой применяются на машинах сред него и тонкого волочения. Проволока продевается через ушки водилки, укрепленной на оси катушки. При движении проволоки водилка вращается в сторону, противоположную намотке, обеспечивая разматывание прово локи. Заготовка при этом практически не испытывает натяжения. Недос
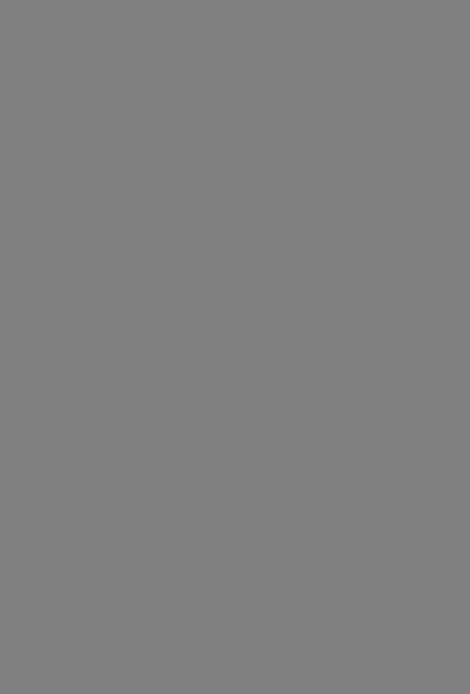
Для волочения проволоки применяются в основном монолитные во локи. В процессе волочения волока подвергается сильному давлению из нутри и может разрушиться, если не имеет достаточно прочной опоры сна ружи. Роль такой опоры играет металлическая обойма, в которую крепится волока.
К характеристикам волочильного инструмента относятся: материал инструмента и его механические свойства, геометрия рабочей поверхно сти, наружная форма волоки и устройства для установки и крепления ин струмента.
Для изготовления волок применяют материалы, обладающие высокой твердостью, износостойкостью, антикоррозийной стойкостью, хорошей полируемостью.
Для производства волок в основном используются металлокерамиче ские сплавы, естественные и искусственные алмазы, некоторые марки стали.
Металлокерамические сплавы состоят из 90-98 % карбида вольфрама и 2-10 % кобальта, который цементирует карбид и обеспечивает однород ность смеси всех компонентов. Металлокерамические сплавы по твердости близки к алмазу (88-90 HRC), а кобальт придает сплаву требуемую вяз кость.
Для волочения проволоки диаметром менее 0,3 мм применяются ал мазные волоки. Это необходимо, так как при волочении тонкой проволоки канал волок из металлокерамических сплавов быстро изнашивается и обеспечить точный размер проволоки не представляется возможным.
Для изготовления обойм используется сталь или латунь.
Для придания каналу волоки надлежащих размеров и формы, а также для получения высокого класса чистоты поверхности этого канала волоки подвергаются шлифовке. Изготовление или перешлифовка волок относят ся к числу наиболее ответственных процессов. Обработке подвергаются как новые волоки, так и волоки, бывшие в употреблении.
После шлифовки производится доводка, т. е. механическая обработка канала с целью придания ему точных размеров, и полировка - получение гладкой поверхности рабочего канала.
Технические неграненые алмазы используются для изготовления во лок лишь в отдельных случаях. В основном кабельные заводы получают заготовки алмазных волок. Эти заготовки сначала подвергаются огранке. После огранки алмазы центруются обычно на глубину 1/3 толщины камня. Затем производится их сверление и шлифовка на специальных станках при помощи притиров (иголок), на концы которых нанесена алмазная пудра. Угол заточки притиров последовательно изменяется, благодаря чему полу чается радиальная форма волочильного канала. После сверления произво