
Резание материалов
..pdf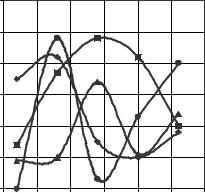
–в слое, прилегающем к поверхности, должны формироваться тангенциальные напряжения растяжения;
–зависимость максимальной величины σmax от скорости резания должна иметь характерную точку перегиба или носить экстремальный характер.
Экспериментальные исследования остаточных напряжений полностью подтверждают это предположение. Например, при протягивании жаропрочных сплавов ЭИ787-ВД и ВЖЛ14 величина максимальных остаточных напряжений имеет переменную характеристику
сминимальными значениями в области оптимальных скоростей резания 15…20 м/мин для этих сплавов (рис. 130).
σmax, |
МПа |
|
|
|
|
|
|
|
600 |
|
|
|
|
|
|
|
|
500 |
|
|
|
|
|
|
|
|
400 |
|
|
|
|
|
|
|
|
300 |
|
|
|
|
|
|
|
|
200 |
|
|
|
|
|
|
|
|
100 |
|
|
|
|
|
|
|
|
0 |
|
|
|
|
|
|
|
V , м/мин |
|
0 |
5 |
10 |
15 |
20 |
25 |
30 |
Рис. 130. Влияние скорости протягивания V хвостовиков лопаток и пазов в кольцах направляющих аппаратов из жаропрочных никелевых сплавов на глубину h и степень наклепа H протянутой поверхности
ЭИ787-ВД, острые протяжки;
ЭИ787-ВД, затупленные протяжки;
ВЖЛ14, острые протяжки;
ВЖЛ14, затупленные протяжки
Когда главным образом действует силовой фактор, то возникают сжимающие напряжения, и чем больше подача, тем при меньших Vо наблюдается перегиб (рис. 131). Характер зависимости σmax =
281
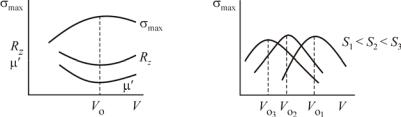
= f(S) определяется уровнем скорости (температуры) резания (рис. 132). При резании на низкой скорости Vо1 повышение подачи приводит к увеличению объема и интенсивности пластической деформации и повышению температуры; причем последняя приближается к своему оптимальному значению.
Рис. 131. Влияние скорости резания |
Рис. 132. Влияние скорости ре- |
на шероховатость Rz, коэффициент |
зания на σmax при обработке |
трения µ′ и остаточные поверхност- |
на разных подачах S |
ные напряжения σmax |
|
В этом случае повышение подачи приводит к росту остаточных тангенциальных напряжений растяжения. Снижение коэффициента трения на задней поверхности инструмента µ′ уменьшает действие силового фактора и также способствует росту напряжений растяжения.
При работе на средней скорости резания Vо2 зависимость σmax = f(S) носит экстремальный характер. Экстремальный характер функции σmax = f(S) может быть объяснен переходом температуры резания через оптимальное значение. Снижению максимальной величины остаточных напряжений после некоторого значения подачи может способствовать повышение коэффициента трения по задней поверхности µ', т.е. повышение действия силового фактора.
Для высокой скорости резания Vо3 с увеличением подачи происходит монотонное снижение тангенциальных растягивающих напряжений (рис. 133). Это может быть вызвано возрастающим действием силового фактора вследствие повышения µ'. Кроме того, при высоких скоростях резания ослабевает действие температурного фактора.
282
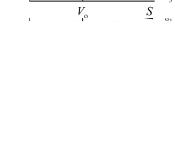
В заключение следует отметить, что между высотой микронеровностей обработанной поверхности, глубиной и степенью наклепа, остаточными напряжениями, контактными явлениями в зоне резания и интенсивностью износа инструмента при резании наблюдается тесная взаимосвязь. Все перечисленные характеристики имеют характерную точку перегиба или носят экстремальный характер. Экстремальные (или критические) точки кривых находятся в области оптимальных скоростей резания.
Главным фактором, определяющим коэффициент трения по задней поверхности резца, параметры наклепанного слоя остаточного напряжения и интенсивность износа инструмента, является средняя температура контакта, а скорость резания выступает в основном как температурный фактор.
5.4. Влияние качества поверхностного слоя на эксплуатационные свойства деталей
Установлено, что в результате приработки на трущихся поверхностях образуется оптимальная шероховатость, характерная для данных конкретных условий работы соединения. Поэтому если в процессе обработки деталей на поверхности обеспечить шероховатость, близкую к оптимальной, то время приработки на износ будет наименьшим. Оптимальная по износостойкости шероховатость поверхности зависит от вида соединений и конкретных условий эксплуатации.
На износ деталей оказывают влияние не только высота, но и направление неровностей исходной шероховатости трущихся поверхностей. Шероховатость поверхности оказывает существенное влияние на усталостную прочность деталей и коррозионную стойкость.
283
С уменьшением шероховатости поверхности коррозионная стойкость деталей повышается.
Установлено, что наклеп поверхностного металла, созданный специальными технологическими приемами или полученный в результате механической обработки, приводит к увеличению контактной жесткости и контактной выносливости. Кроме того, наклепанный поверхностный слой деталей уменьшает интенсивность проявления всевозможных геометрических и структурных концентраторов напряжений в поверхностных слоях, повышая тем самым усталостную прочность деталей. Вместе с тем наклеп поверхностного слоя деталей после механической обработки понижает в большинстве случаев коррозионную стойкость деталей.
Наиболее заметно влияние остаточных напряжений в поверхностном слое на усталостную прочность деталей. При этом сжимающие напряжения повышают предел выносливости, а растягивающие – уменьшают его. Имеются данные о том, что сжимающие остаточные напряжения в поверхностных слоях детали повышают прочность и надежность соединений с натягом, поэтому необходимо стремиться, чтобы в поверхностном слое формировались сжимающие напряжения возможно большей величины.
При обработке деталей в результате действия высоких температур в поверхностном слое могут происходить структурные изменения, которые приводят к вторичной закалке и образованию поверхностного слоя повышенной твердости по сравнению с основной структурой металла. При обработке закаленных металлов в поверхностном слое может происходить отпуск различной степени.
5.5. Особенности образования поверхности при чистовой лезвийной и абразивной обработке
Чистовая лезвийная обработка деталей машин проводится на таких операциях окончательной обработки, как чистовое точение, чистовое фрезерование, зенкерование и развертывание отверстий, протягивание наружных и внутренних поверхностей. Основная зада-
284
ча чистовой обработки – обеспечить заданное качество поверхностного слоя и заданную точность поверхности. В качестве режущих инструментов применяются лезвийные инструменты с доведенными режущими гранями и кромками. Припуски на обработку обычно составляют 0,2…0,5 мм. Требуется обеспечить шероховатость обработанной поверхности по Ra не более 2 мкм, а точность в пределах
0,02…0,1 мм.
Для этого применяют специальные прецизионные станки, приспособления и инструменты. Обработку ведут на повышенных скоростях резания, минимальных подачах с оптимальной геометрией инструмента.
Чистовая абразивная обработка проводится с помощью раз-
личных видов абразивного инструмента методами шлифования, полирования, доводки, притирки, обдувки и т.п. Припуски на обработку составляют 0,05…0,2 мм. При этом шероховатость поверхности может достигать величины по Ra в пределах 0,05…1,25 мкм
Особенности процессов отделения срезаемого слоя металла при чистовой лезвийной обработке рассмотрены нами в предыдущих главах, поэтому далее рассмотрим процессы абразивной обработки.
5.5.1. Понятие об абразивном инструменте. Характеристики абразивного инструмента
Шлифование представляет собой операцию обработки поверхности заготовки абразивным инструментом.
Под абразивными понимаются материалы естественного или искусственного происхождения, зерна которых обладают высокой твердостью и способностью резания. Абразивные инструменты могут быть изготовлены со связанными зернами (шлифовальные круги, головки, сегменты, бруски, шкурки) и в виде несвязанных, свободных зерен (пасты, суспензии, порошки). Абразивные инструменты характеризуются материалом зерен и их величиной, видом связки, твердостью, структурой, формой и размерами.
Алмазные круги и бруски дополнительно характеризуются конструкцией и маркой алмазов.
285
Абразивные материалы и инструменты. Абразивные мате-
риалы делятся на искусственные (синтетические) и естественные (природные). Более широкое применение в промышленности в настоящее время имеют искусственные абразивные материалы: электрокорунд, карбид кремния (карборунд), карбид бора, синтетические алмазы, кубический нитрид бора (эльбор).
Связующие вещества (связки): неорганические (керамическая, магнезиальная и силикатная); органические (бакелитовая, глифталиевая, вулканитовая); металлические (порошки меди, алюминия, олова и др.).
Электрокорунд (А12О3). Большая часть (~ 80 %) абразивного инструмента изготавливается из электрокорунда, который получают путем плавки глинозема в электрических печах. Существует несколько разновидностей электрокорунда:
–Э – электрокорунд нормальный (91…99 % А12О3) (марки: 16А, 15А, 14А, 13А, 12А);
–ЭБ – электрокорунд белый (97…99 % А12О3) (марки: 25А, 24А, 23А, 22А);
–ЭХ – электрокорунд хромистый (марки: 34А, 33А, 32А);
–ЭТ – электрокорунд титанистый – 37А (содержит ≈ 97 %
А12О3 и 2 % ТiO2);
– М – монокорунд, зерна которого представляют отдельные кристаллы и имеют большое число режущих граней (марки: 45А, 44А).
Титанистый электрокорунд представляет собой соединения А12О3 + 1,5 % ТiO2, отличается от нормального электрокорунда большей вязкостью и стабильностью свойств, что хорошо для доводочнопритирочных работ.
Монокорунд – разновидность электрокорунда. Он получается из боксита оксисульфидным способом в виде зерен, состоящих из изометрических кристаллов корунда различной величины. Сущность способа получения монокорунда состоит в сплавлении боксита с сернистым железом и восстановителем – антрацитом или коксом – в электропечах.
286
Зерна электрокорунда ЭХ, ЭТ и М имеют более высокие режущие свойства, чем Э и ЭБ.
Карбид кремния (SiС) – химическое соединение кремния с углеродом, получается при плавке кварцевого песка и кокса. Зерна SiС имеют более высокую твердость, чем электрокорунд. Применяются две разновидности карбида кремния: черный КЧ (95…97 % SiС) ма-
рок 55С, 54С, 53С, 52С и зеленый КЗ (98…99 % SiС) марок 64С, 63С, 62С. Недостаток карбида кремния – высокая хрупкость и малая прочность. Поэтому при обработке сталей он почти не применяется. Карбид кремния применяется при абразивной обработке хрупких материалов: чугунов, бронзы; тугоплавких сплавов, металло- и минералокерамики.
Карбид бора (В4С) – химическое соединение бора с углеродом – получают плавлением борной кислоты В2О2 с нефтяным коксом при температуре 2000...2350 °С. Карбид бора имеет высокую твердость, большую хрупкость и применяется в виде порошков для доводочных процессов и при ультразвуковой обработке хрупких материалов.
Борсиликарбид в отличие от карбида бора не содержит вредной примеси графита, отличается большей стабильностью свойств, более прочен и дешевле. На операциях доводки показал на 30…40 % более высокую производительность, чем карбид бора.
Окись хрома – порошок темно-зеленого цвета для доводки. Получается из бихромата калия с примесью серы.
Окись железа (крокус) – тонкий полировальный порошок, состоящий в основном из кристаллической окиси железа. Получается переработкой железного купороса и щавелевой кислоты.
Синтетические алмазы (АС) получают в виде мелких кристаллов, размеры обычно не более 1 мм. Синтез алмазов происходит в результате воздействия на графит высоких давлений (до 1,7·10 кгс/см2) и высоких температур (до 2500 °С). В присутствии металлического катализатора происходит перекристаллизация углерода из гексагональной структуры графита в кубическую структуру алмаза. Синтетические алмазы в зависимости от прочности делятся на пять марок:
287
низкой прочности (АСО), повышенной прочности (АСР), высокой прочности (АСВ), монокристальные (АСК и АСС).
Кубический нитрид бора (КНБ, боразон или эльбор) состоит из 44 % бора и 56 % азота; твердость его уступает лишь алмазу, а теплостойкость в 2 раза выше алмаза. Круги из эльбора наиболее эффективны при чистовом шлифовании, заточке и доводке инструментов из быстрорежущих сталей повышенной производительности (кобальтовых и высокованадиевых).
К естественным материалам относятся кварц (кремнезем SiО2), наждак, корунд и алмаз. Природные абразивные материалы, за исключением алмаза, имеют низкие режущие свойства и для абразивной обработки металлов почти не применяются.
Природный алмаз А – минерал, состоящий из кристаллического углерода. Природные технические алмазы содержат небольшие примеси окислов алюминия, железа, кальция, кремния, марганца, которые придают им различный цвет. Атомы углерода в кристаллической решетке алмаза очень прочно связаны, что обеспечивает высокую твердость и износостойкость. Твердость алмаза по шкале Мооса равна 10, микротвердость – 10 060 кгс/мм2, модуль упругости 9·104 кгс/см2, плотность 3,52 г/см3.
Недостатки алмазов: высокая хрупкость, большая способность к адгезии с титаном, сталью и другими металлами, сравнительно низкая теплостойкость (800…900 °С). Натуральные технические алмазы применяются для изготовления алмазных резцов, наконечников к приборам, фильер для волочения, для правки шлифовальных кругов.
Зернистость абразивных материалов. Абразивные материалы подвергаются дроблению, обогащению и классификации на зернистость. Согласно ГОСТ 3647–71 по размерам они делятся на три группы: шлифовальные зерна от № 200 до 16 (зерна основной фракции размером от 2000 до 160 мкм); шлифовальные порошки от № 12 до 3 (зерна от 125 до 28 мкм); микропорошки от М40 до М5 (зерна от
40 до 3 мкм).
Сортировка зерен от № 200 до 3 производится просеиванием через сита, и зернистость определяется размером стороны ячейки сита
288
(в сотых долях мм). Например, зерно № 16 просеивается через сито с размером ячейки 0,16 мм и остается на сите с размером ячейки 0,12 мм. Размеры зерен микропорошков определяются микроскопическим методом измерения или фотоэлектрическим – по скорости осаждениязерен.
Алмазные зерна (по ГОСТ 9204–70) делятся на две группы: шлифпорошки, получаемые путем рассева на ситах с контролем зернистости ситовым методом (12 зернистостей от 630/500 до 50/40); микропорошки, полученные путем классификации в жидкости и контролем размера зерен под микроскопом (11 зернистостей от 60/40 до 1/0). Зернистость алмазов обозначается дробно: числитель соответствует наибольшему, а знаменатель – наименьшему размеру зерен основной фракции.
В нашей стране освоено промышленное производство алмазных субмикропорошков, т.е. порошков с размером зерен 0,7; 0,5; 0,3 и 0,1 мкм. При помощи паст на основе субмикропорошков получают минимальную высоту неровностей и незначительную толщину дефектного слоя.
В качестве связки абразивных зерен применяют следующие: неорганические, органические и металлические.
К неорганическим связкам относятся керамическая, магнезиальная и силикатная. Наиболее распространена керамическая связка К, из которой изготовляют более 50 % всего абразивного инструмента. В ее состав входят огнеупорная глина, полевой шпат, тальк и др. Инструменты, изготовленные на керамической связке, теплостойки, прочны, обладают химической стойкостью и не боятся влаги. Их недостаток – большая хрупкость.
Органические связки – бакелитовая Б, глифталиевая Г и вулканитовая В. Бакелитовая связка, наиболее распространенная среди органических связок, изготавливается из фенолформальдегидной смолы. Инструмент на бакелитовой связке прочен, эластичен и допускает большие окружные скорости. Однако его химическая и тепловая стойкости невысоки. Глифталиевая связка состоит из глицерина и фталиевого ангидрида. Круги на глифталиевой связке имеют повышенную
289
упругость и применяются на чистовых и доводочных работах. Вулканитовая связка состоит из каучука и серы, обладает высокой прочностью и эластичностью. На вулканитовой связке можно изготовить очень тонкие круги (0,5 мм) с относительно большим диаметром (150 мм). Инструмент на этой связке применяется для отрезных и прорезных операций, а также при бесцентровом шлифовании.
Металлические связки, состоящие из металлической основы (порошки меди и алюминия, олова и др.) и наполнителя, применяют в алмазных кругах и частично в кругах из карбида кремния для электроалмазного шлифования. Металлические связки МИ и МК на медной основе имеют наполнитель – карбид кремния и электрокорунд; связка М5 – с основой из алюминия и меди; связка М1 – с основой из меди и олова. Необходимо отметить, что металлические связки прочнее удерживают зерна и обеспечивают более эффективное использование режущих свойств алмазов, чем органические связки.
Под твердостью абразивного инструмента понимается сопротивляемость связки вырыванию абразивных зерен под действием внешних сил. В России установлено 7 классов твердости (М, СМ, С, СТ, Т, ВТ, ЧТ): мягкий – М1, М2, М3; среднемягкий – СМ1, СМ2; средний – С1, С2; средне-твердый – СТ1, СТ2; твердый – Т1, Т2; весьма твердый – ВТ1, ВТ2; чрезвычайно твердый – ЧТ1, ЧТ2.
При выборе твердости абразивных инструментов учитывают физико-механические свойства обрабатываемого материала, требования к точности и качеству поверхности.
Под структурой абразивного инструмента понимают процентное содержание объемов зерен vз, связки vс и пор vп (vз + vс + vп = = 100 %).
Различают четыре группы структур: плотные (№ 0–3), среднеплотные (№ 4–6), открытые (№ 7–12); высокопористые (№ 13–18). Нулевая структура имеет минимальное расстояние между зернами и наибольший их объем (vз = 62 %). При повышении номера структуры на единицу объем абразивных зерен vз уменьшается на 2 %. У высокопористых кругов объем пор vп может достигать 75 % объема круга.
290