
Резание материалов
..pdf11.Дайте определение экономической скорости резания и скорости резания, соответствующей максимальной производительности на данном рабочем месте.
12.Как различные факторы влияют на скорость резания и стойкость инструмента?
Глава 5 ВЛИЯНИЕ УСЛОВИЙ РЕЗАНИЯ
НА КАЧЕСТВО ПОВЕРХНОСТНОГО СЛОЯ ОБРАБОТАННОЙ ДЕТАЛИ
5.1.Понятие о поверхностном слое, возникающем при резании
Врезультате обработки резанием вследствие пластической деформации тонкий поверхностный слой детали толщиной 0,2…1,0 мм приобретает новые свойства, имеющие значительные отличия от обрабатываемой поверхности и внутренних свойств заготовки. Качество детали после обработки резанием прежде всего определяется:
– точностью размеров;
– геометрическими параметрами качества – шероховатостью, граностью, бочкообразностью, корсетностью и т.д.;
– физическими параметрами – глубиной и степенью наклепа, микроструктурой, остаточными поверхностными напряжениями, дислокационной структурой и т.д.
Установлено, что разрушение материала деталей в процессе эксплуатации машин обычно начинается с поверхности. В процессе механической обработки в поверхностном слое появляются остаточные напряжения, разрывы металла, микротрещины, которые при различных условиях эксплуатации могут привести к росту величины трещин и последующему разрушению. Обеспечение высокой усталостной и длительной прочности, термоусталости, износоустойчивости, коррозионной стойкости и других эксплуатационных требова-
261
ний к деталям ГТД может быть достигнуто и технологическими методами, т.е. назначением соответствующих режимов резания. Поэтому технологу нужно знать особенности образования поверхностного слоя и уметь управлять процессом резания для обеспечения наиболее благоприятных параметров качества поверхностного слоя.
5.2. Основные параметры, определяющие качество поверхностного слоя
5.2.1. Шероховатость обработанной поверхности
Реальная поверхность детали после механической обработки
вотличие от идеальной поверхности, изображенной на чертежах, всегда имеет неровности различной формы и высоты.
Под шероховатостью поверхности понимается совокупность микронеровностей с относительно малыми шагами, образующих рельеф поверхности. В соответствии с ГОСТ 2789–83, шероховатость
поверхности характеризуется высотой неровностей Rz или средним арифметическим отклонением Rа, или Rmax, в мкм.
Значения Rа и Rz шероховатости по ГОСТ 2789–83 приведены
втабл. 16.
Высота и |
форма неровностей |
поверхности, расположение |
и направление |
обработочных рисок |
зависят от принятого мето- |
да и режима обработки, геометрии режущего инструмента, свойств обрабатываемого материала, состояния используемого оборудования и т.д.
Для оценки и измерения шероховатости существует целый ряд приборов. Наиболее широкое применение в промышленности и исследовательских организациях получили оптический прибор – двойной микроскоп МИС-11 (МИС-12) конструкции академика ВЛ. Линника – и щуповые – различные модели профилографовпрофилометров. Для визуального сравнения существуют эталоны шероховатости для каждого вида обработки резанием.
262
|
|
|
Таблица 16 |
|
Классы и величина шероховатости поверхностей |
||||
|
|
|
|
|
Класс |
|
Rz, мкм |
Базовая длина, |
|
шероховатости |
Ra, мкм |
|||
(старый ГОСТ) |
|
|
мм |
|
|
|
|
||
1 |
– |
320 |
8,0 |
|
2 |
– |
160 |
||
3 |
– |
80 |
|
|
4 |
– |
40 |
2,5 |
|
5 |
– |
20 |
||
|
||||
6 |
2,5; 2,0; 1,6 |
– |
– « – |
|
7 |
1,25; 1,00; 0,80 |
– |
0,8 |
|
8 |
0,63; 0,50; 0,40 |
– |
– « – |
|
9 |
0,32; 0,25; 0,20 |
– |
– « – |
|
10 |
0,160; 0,125; 0,100 |
– |
– « – |
|
11 |
0,080; 0,063; 0,050 |
– |
0,25 |
|
12 |
0,040; 0,032; 0,025 |
– |
– « – |
|
13 |
– |
0,100 |
– « – |
|
14 |
– |
0,50 |
– « – |
Волнистость поверхности, в отличие от шероховатости, представляет собой совокупность периодически чередующихся выступов и впадин синусоидальной формы, имеющих значительно больший шаг.
В общем виде высота неровностей Rz (Rа) при точении может быть определена из следующей зависимости:
Rz = Нр + ∆Н, мкм,
где Нр – расчетная или теоретическая величина неровностей; ∆Н – отклонение фактической высоты неровностей от рас-
четной.
При этом расчетная величина неровностей при радиусе резца при вершине, равной нулю, может быть определена по формуле
263
Нр = (S tg ϕ tg ϕ1)/(tg ϕ+ tg ϕ1),
при R, не равном нулю, по формуле
Нр = S2/8R.
Суммарная величина отклонений ∆Н может быть представлена выражением
∆Н = ∆Нпл.деф + ∆Нупр.деф + ∆Нтр.зад + ∆Ннар + ∆Нвибр + ∆Нh,
т.е. учитывает влияние пластической ∆Нпл.деф и упругой ∆Нупр.деф деформаций, трения задней поверхности инструмента о деталь ∆Нтр.зад, наростообразование ∆Ннар, вибрации ∆Нвибр, износ инструмента ∆Нh и т.д.
Необходимо отметить, что пластическая деформация и другие факторы воздействуют на Rz таким же образом, как они действуют на интенсивность износа инструмента при резании. Так, чем выше трение, тем больше интенсивность износа, тем хуже обработанная поверхность и т.д.
Поскольку расчетная высота неровностей Нр находится из чисто геометрических соображений и от других параметров процесса резания не зависит, то изменение шероховатости обработанной поверхности связано с изменением ∆Н.
На величину ∆Н (или на Rz) оказывают влияние следующие основные факторы: скорость резания, свойства обрабатываемого материала, свойства инструментального материала, жесткость системы станок–приспособление–инструмент–деталь и др.
5.2.2.Наклеп поверхностного слоя при резании металлов
Под наклепом металла следует понимать повышение его прочностных свойств и твердости при его пластическом деформировании. Первоначальная пластическая деформация металла, образующего поверхностный слой, протекает в зоне стружкообразования, так как начальная граница этой зоны (линия СЕ), как правило, лежит ниже линии среза (рис. 118). Другой причиной деформации поверхностно-
264

го слоя (а следовательно, и упрочнения) является то, что резание металлов осуществляется инструментом, лезвие которого всегда имеет некоторый радиус округления ρ. Для заточенных алмазным кругом резцов радиус ρ может быть в пределах от 3 до 10 мкм. Для резцов, имеющих износ hз от 0,1 до 0,3 мм, радиус округления составляет
20...60 мкм.
Рис. 118. Схема процесса резания с образованием наклепа глубиной упрочнения Hу
При наличии ρ часть металла выше линии АВ уходит в стружку, а слой металла толщиной Нсж не срезается, а подминается округленной частью резца, подвергаясь упругой и пластической деформации.
Третьей причиной деформации поверхностного слоя является частичное упругое восстановление несрезанного деформированного металла на величину Hy. Это приводит к появлению на задней поверхности инструмента нормальных и касательных сил, а следовательно, и к дополнительной пластической деформации поверхностного слоя.
Таким образом, металл, образующий поверхностный слой, в процессе резания претерпевает неоднократное пластическое деформирование. Это приводит к изменению всех физико-механи- ческих свойств и структуры металла. Основными характеристиками
265
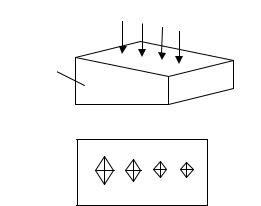
наклепа являются: степень наклепа H и глубина наклепанного слоя hс. Степень наклепа определяется по формуле
H = (H1 – H)100%/H,
где H1 – микротвердость детали непосредственно с поверхности; Н – микротвердость исходного металла.
Методы определения наклепа. В соответствии с изменениями, происходящими в поверхностном слое, глубина наклепанного слоя определяется или по изменению микротвердости по сечению детали, или рентгеноструктурным методом по изменению характера интерференционных линий на рентгенограммах при послойном стравливании исследуемой поверхности.
Наиболее распространенным методом исследования глубины и степени наклепа в настоящее время является метод измерения микротвердости. Метод заключается в исследовании микротвердости материала (металла) на участке наклонного микрошлифа (рис. 119),
Воздействие алмазной пирамиды
1
а
б
Рис. 119. Измерение микротвердости образца по глубине поверхностного слоя: а – схема нагружения; б – следы алмаза; 1 – образец
266
изготовленного на специальном приспособлении. Для измерения глубины и степени наклепа обработанных поверхностей используется микроскоп ПМТ-3 и метод косых шлифов. Для проведения исследований изготовлены специальные косые образцы. Измеряя на косом срезе отпечатки алмазного наконечника, по формулам или по таблицам определяют микротвердость образца на разной глубине.
Между hс и Н существует тесная взаимосвязь hс = K·Н, где K – коэффициент пропорциональности.
Наклеп поверхностного слоя в значительной степени зависит от многих технологических факторов – элементов режима резания, геометрических параметров инструмента и состояния его режущего лезвия, свойств инструментального и обрабатываемого материалов, вида СОЖ и т.д.
5.2.3. Остаточные поверхностные напряжения
Остаточными напряжениями называют такие внутренние напряжения, которые сохраняются в детали при снятии внешней нагрузки. Различают напряжения I, II и III рода.
Напряжения I рода имеют макроскопический характер, уравновешиваются они в пределах всего объема детали или большей части его. По своему действию напряжения I рода приравниваются к рабочим напряжениям и оказывают благоприятное или вредное влияние на работоспособность детали.
Напряжения II рода представляют собой местные кристаллические напряжения, охватывающие объем одного или нескольких зерен металла (межкристаллические напряжения).
Напряжения III рода уравновешиваются в пределах субмикроскопических объемов данного зерна, т.е. охватывают объем нескольких кристаллических ячеек.
Наиболее интересными с точки зрения долговечности детали, т.е. с точки зрения влияния состояния поверхностного слоя детали на долговечность, являются напряжения I рода, которые и рассмотрим подробнее.
267
Напряжения I рода могут быть технологическими и конструкционными. Конструкционные – при клепке, сборке. Технологические – от литья, ковки, сварки, резки, механической обработки и т.д. Напряжения I рода делятся на растягивающие (+) и сжимающие (–), кроме того, могут быть тангенциальные и осевые (σт и σо).
Сфизической точки зрения возникновение напряжений связано
снеобратимыми изменениями объема металла в зоне деформации, нагрева и т.д.
При пластическом деформировании уменьшается плотность и возрастает объем поверхностного слоя металла, а поскольку он связан с нижележащими недеформированными слоями металла, то в процессе обработки в наружном слое будут возникать сжимающие, а в нижележащих – растягивающие остаточные напряжения.
Следовательно, одной из причин возникновения остаточных напряжений в поверхностном слое деталей является пластическое деформирование.
Другими причинами возникновения остаточных напряжений могут быть:
–неравномерность пластической деформации поверхностных слоев и формирования в них остаточных напряжений сжатия;
–локализованный нагрев тонких поверхностных слоев в зоне резания и формирование в них остаточных поверхностных напряжений растяжения;
–фазовые превращения различных слоев металла, приводящих
кобразованию в них различных структур, обладающих различной плотностью и формирующих в этих слоях неодинаковые остаточные поверхностные напряжения различного знака.
Образование остаточных напряжений от действий силового фактора. Пластическая деформация металла поверхностного слоя приводит к изменению всех его физико-механических свойств, в том числе к уменьшению плотности удельного веса, а следовательно,
кувеличению удельного объема. Увеличение объема металла распространяется только на глубину проникновения пластической деформации и не затрагивает нижележащих слоев. В результате в слое,
268

прилегающем к поверхности, возникают сжимающие напряжения, а в нижележащих – напряжения растяжения.
Иначе это можно объяснить так: резец режет, поверхностные слои растягиваются настолько, что деформируются, а нижележащие слои упруго деформированы. После снятия нагрузки напряжения в упруго растянутой зоне будут стремиться сняться, но их снятию препятствуют пластически растянутые поверхностные слои; в результате внутренние слои частично упруго растянуты, а внешние слои упруго сжаты.
Итак, при условии, когда привалирует силовой фактор, в поверхностном слое формируется напряжение сжатия, а в нижележащих слоях – уравновешивающие их остаточные напряжения растяжения (рис. 120).
Влияние температуры резания на образование остаточных напряжений. Выделяющееся в зоне резания тепло мгновенно нагревает тонкие поверхностные слои металла до высоких температур. Металл в верхних нагретых слоях, стремясь к увеличению своего объема, встречает противодействие со стороны окружающего металла нижележащих слоев, это приводит к образованию напряжений сжатия. При охлаждении объем верхних нагретых слоев металла стремится уменьшиться, однако сжатию препятствуют нижележащие слои холодного металла. Вследствие этого под воздействием тепла, выделяющегося в зоне резания, в поверхностном слое образуются остаточные напряжения растяжения, а в нижнем – сжатия. Однако следует отметить, что формирование растягивающих напряжений под действием температуры может быть только в том случае, если внутренние напряжения, возникающие при нагреве, превзойдут по своей величине предел текучести данного материала.
269
Методы определения остаточных напряжений. Остаточные напряжения определяют в основном двумя методами: механическим и рентгеноструктурным. Оба метода имеют свои достоинства и недостатки.
Преимущества рентгеноструктрного метода – объективность, отсутствие посторонних факторов, воздействующих на образец в процессе измерения, возможность определения напряжений без разрушения детали. Однако точность метода низкая и составляет
50 %.
Основным преимуществом механического метода является возможность быстрого получения более точного эпюра остаточных напряжений по глубине поверхностного слоя. Недостаток метода – требуется вырезка образцов из готовой детали, т.е. метод дорогой и разрушающий.
Существует еще несколько методов определения остаточных напряжений, например метод Давиденкова и метод Закса.
Измерение величины и характера распределения остаточных напряжений по глубине поверхностного слоя проводятся на вырезанных из деталей прямоугольных образцах (рис. 121) с помощью прибора ПИОН-2 при травлении поверхностного слоя по методу Н.Н. Давиденкова. Процесс определения остаточных напряжений механическим методом состоит из следующих этапов:
–вырезка, подготовка и крепление образца;
–электрохимическое травление;
–определение глубины залегания искомых остаточных напряжений с помощью регистрации деформации в процессе травления;
–расчет и построение эпюра остаточных напряжений.
Образцы вырезаются таким способом, чтобы операция вырезки не внесла дополнительных остаточных напряжений (электроискровой метод, вырезка шлифовальным кругом с большим охлаждением и малой подачей). Образцы для определения величины остаточных напряжений вырезаются электроэрозионным методом, например, из ободов дисков турбин (рис. 122).
270