
Справочник технолога машиностроителя Косилов
.pdf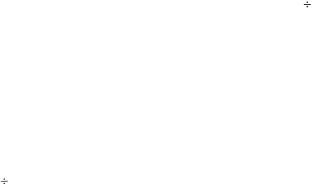
Снимаемый припуск и выбор операций за- |
связке применяют для обработки деталей из |
||||||||
висят от того, насколько нужно повысить точ- |
чугунов и закаленных сталей со снятием боль- |
||||||||
ность формы отверстия и уменьшить пара- |
ших припусков (0,05 мм и выше), из твердых |
||||||||
метр шероховатости (табл. 70 и 71). Если |
сплавов, для хонингования на автоматическом |
||||||||
основная цель операции сводится к уменьше- |
цикле с применением активного контроля, для |
||||||||
нию отклонений формы отверстия, припуск |
обработки отверстий диаметром до 10 мм, не- |
||||||||
устанавливается по разности между отклоне- |
скольких деталей пакетом, шлицевых и разоб- |
||||||||
ниями формы отверстия в исходном состоя- |
щенных поверхностей (табл. 72). |
|
|
||||||
нии и заданными отклонениями. После уста- |
Для |
обработки деталей из стали, чугуна |
|||||||
новления общего припуска назначают число |
и цветных металлов может быть также при- |
||||||||
операций, распределяют припуск по опера- |
менен абразивный инструмент (табл. 73). |
||||||||
циям и подбирают характеристику режущих |
При чистовом хонинговании с получением па- |
||||||||
брусков. Обработка в несколько операций вы- |
раметра |
шероховатости Ra = 0,1 |
0,2 |
мкм |
|||||
звана |
невозможностью |
обеспечить |
большой |
и выше следует применять алмазные бруски |
|||||
съем металла и одновременно низкий пара- |
зернистостью 80/63 на эластичной связке Р11. |
||||||||
метр |
шероховатости |
поверхности |
одними |
Число режущих брусков в хонинговальной |
|||||
и теми же брусками. Большой припуск при хо- |
головке |
выбирают максимальным. |
Наиболее |
||||||
нинговании можно снять |
крупнозернистыми |
эффективно снижает отклонения формы |
хо- |
||||||
брусками, которые, срезая металл, сохраняют |
|
|
|
|
|||||
параметр шероховатости поверхности, необхо- |
|
|
|
|
|||||
димый для самозатачивания брусков. Поэтому |
|
|
|
|
|||||
основной припуск следует снимать на первой |
|
|
|
|
|||||
операции. На чистовых операциях припуск |
|
|
|
|
|||||
должен быть достаточным лишь для удаления |
|
|
|
|
|||||
шероховатости поверхности после предвари- |
|
|
|
|
|||||
тельного хонингования. Параметр шерохова- |
|
|
|
|
|||||
тости поверхности Ra = 0,4 |
0,8 мкм надежно |
|
|
|
|
||||
обеспечивается одной операцией хонингова- |
|
|
|
|
|||||
ния. В условиях поточного производства для |
|
|
|
|
|||||
получения меньшего параметра шероховато- |
|
|
|
|
|||||
сти рекомендуется осуществлять |
хонингование |
|
|
|
|
||||
в две операции и более. |
|
|
|
|
|
|
|
||
Алмазный инструмент |
на |
металлической |
|
|
|
|
цессе |
наладки |
в зависимости от |
характера |
части станок оборудуют устройствами для за- |
|
и отклонений формы отверстия до хонингова- |
медления скорости продольного хода и вы- |
||||
ния, качества брусков и других технологиче- |
держки вращающегося хона в конце каждого |
||||
ских |
условий. |
Ширину |
брусков |
выбирают |
хода. При снятии малых припусков (до 0,02 |
с учетом числа одновременно работающих |
мм на диаметр) отверстия можно хонинговать |
||||
брусков в хонинговальной головке. Отноше- |
без замедления продольного хода короткими |
||||
ние режущей поверхности брусков к обрабаты- |
брусками, так как они изнашиваются более |
||||
ваемой поверхности отверстия должно быть |
равномерно. Длина брусков должна быть при- |
||||
равно 0,5 — 0,6 при хонинговании гладких от- |
мерно в 2 раза меньше длины обрабатываемо- |
||||
верстий и 0,8 — 1,0 при |
хонинговании шли- |
го отверстия. Многорядные отверстия хонин- |
|||
цевых отверстий. Для деталей малой жестко- |
гуют различными способами. Если обрабаты- |
||||
сти это отношение выбирают минимальным. |
ваемые отверстия расположены близко друг |
||||
При обработке глухих отверстий необходи- |
к другу, то следует применять хонинговаль- |
||||
мо предусматривать канавку для выхода бру- |
ную головку с длинными абразивными бру- |
||||
сков. Если по конструктивным соображениям |
сками, которые при каждом ходе последова- |
||||
ширина канавки не может превышать 5 мм, то |
тельно обрабатывают все отверстия (рис. 288, а). |
||||
для устранения сужения отверстия в нижней |
Во избежание отклонений формы отвер- |
стия и неравномерного изнашивания брусков необходимо хорошо направлять хонинговальную головку. Длину брусков выбирают такой, чтобы при входе в обрабатываемое отверстие они направлялись одним или двумя обработанными отверстиями.
Для отверстий, отстоящих одно от другого на большом расстоянии, применяют хонинговальные головки с многорядным расположением абразивных брусков (рис. 288,6). Отверстия должны иметь допуск соосности 0,01 мм. Если обрабатываемые отверстия имеют различную длину, то для каждого из них подбирают соответствующую длину lх хода абразивных брусков (рис. 288, в). При этом следует, по возможности, для каждого отверстия выдержать условия l/L 3/4 и lв = 1/3 l, где l, L, lв — соответственно длины бруска, отверстия и выхода брусков из отверстия.
При обработке точных отверстий со снятием малых припусков (0,01—0,015 мм) каждое отверстие обрабатывают отдельно хонинговальной головкой с короткими брусками.
В тех случаях, когда при хонинговании нужно устранить отклонения от соосности двух коротких отверстий, далеко разнесенных друг от друга, целесообразно осуществлять хонингование «в линию». Для этого применяют головки с режуще-направляющими брусками (рис. 289), которые позволяют сохранить во время хонингования постоянный контакт брусков с двумя опорами. Режуще-на- правляющие бруски имеют три участка: в середине режущий 7 и по краям — направляющие 2. Длина направляющих участков, равная 1/3 длины режущей части, соответствует длине выхода брусков в процессе хонингования. Режущие и направляющие пластины закреплены
на одной металлической державке и представляют единый брусок. Направляющие пластины изготовляют из бронзы того же состава, что и связка алмазно-металлических режущих пластин. В процессе хонингования режущий и направляющие участки бруска работают в одинаковых условиях и изнашиваются одинаково, постоянно находясь в контакте с двумя обрабатываемыми отверстиями в любом положении головки. Этим обеспечивается взаимное выравнивание положения осей дву> обрабатываемых отверстий при хонинговании
Для обработки шлицевых и других прерывистых поверхностей требуется хонинговальная головка с шириной брусков, в 2 — 3 раза превышающей ширину паза. Алмазные бруски состоят из металлического безалмазного слоя и алмазоносного слоя.
При установке и креплении брусков важно предотвратить разновысотность брусков в одном комплекте. Необходимо, чтобы режущие поверхности брусков при сборе в хонинговальной головке располагались по одной окружности. Алмазные бруски можно считать подготовленными к хонингованию лишь в том случае, если поверхность контакта алмазных брусков с обрабатываемым отверстием будет составлять не менее 60% номинальной режущей поверхности алмазных брусков и будет обеспечен полный контакт по всей длине бру-
ска.
Алмазно-металлический брусок состоит из металлической стальной державки, на которую напаивается алмазно-металлическая пластина. Верхний алмазоносный слой пластины имеет толщину 0,6 — 2 мм и наружный радиус, соответствующий радиусу хонингуемого отверстия. Нижний безалмазный слой имеет толщину 2 — 2,5 мм. Прочность крепления алмазно-металлической пластины к державке во многом зависит от толщины и твердости безалмазного слоя.
Чтобы исключить в процессе хонингования деформацию пластины, вызывающую отрыв пластины от башмака, желательно, чтобы твердость безалмазного слоя была не менее НВ 90 и толщина не менее 2 мм.
Установка и припаивание одновременно всего комплекта брусков должны выполняться в специальном приспособлении. После пайки для более точного расположения бруски прирабатываются в сборе с хонинговальной головкой. Приработка производится притирочной пастой на хонинговальном станке по отверстию хонингуемой (бракованной) заготовки при условии равенства окружной скоро-
сти и скорости продольного хода. Притирочной пастой является абразивный порошок из зеленого карбида кремния зернистостью 5, смешанный с тавотом в пропорции 1 :2. Пасту наносят кисточкой на алмазные бруски. Приработка алмазных брусков производится до тех пор, пока площадь контакта не достигнет 60—70%. Продолжительность притирки комплекта брусков составляет 10—15 мин. Алмазные бруски на эластичной связке Р11 приклеиваются к металлической державке эпоксидной смолой.
Режимы хонингования начинаются с выбора скорости возвратно-поступательного движения головки. Большинство моделей станков допускают хонингование со скоростью продольной подачи Удр = 12 20 м/мин. Для уменьшения инерциальных нагрузок при хонинговании коротких деталей применяют меньшие скорости поступательного перемещения. Для выбора числа двойных ходов головки в минуту можно принимать следующие скорости поступательного движения в зависимости от требуемой длины хода: 18 — 20 м/мин при длине хода больше 150 мм; 12—16 м/мин при длине 100—150 мм; 8 — 12 м/мин при длине 50—100 мм; 5 — 8 м/мин при длине меньше 50 мм.
контроля в процессе хонингования является автокалибр. Например, при обработке отверстия зубчатых колес (рис. 290) калибр-пробка 2 расположена над головкой 1 и постоянно поджата пружиной 4 к торцу корпуса головки. Наружный диаметр автокалибра соответствует окончательному диаметру обрабатываемого отверстия. В процессе хонингования калибр 2 совершает вместе с головкой 1 воз- вратно-поступательные движения. Когда диаметр обрабатываемого отверстия зубчатого колеса 3 достигнет заданного размера, калибр, следуя за брусками, войдет в отверстие колеса и фланцем через рычаг 5 разомкнет контакт электродатчика 6. Последует команда на окончание процесса и отвод брусков в исходное положение. Система автокалибра обеспечивает точность хонингуемого отверстия 15 мкм. Автокалибром можно проверять гладкие и разобщенные обрабатываемые поверхности.
Суперфиниширование
Суперфиниширование — отделочный метод обработки абразивными брусками. Для него характерны колебательные (осциллирующие) движения (рис. 291) и продольные подачи абразивных брусков или детали, постоянная сила прижатия бруска к детали и малое давление в зоне обработки. Обработка происходит без существенного изменения размеров и макрогеометрии поверхности. По мере снятия вершин гребешков увеличивается контактная поверхность, уменьшается давление брусков, стружка заполняет поры брусков, режущая способность брусков снижается, процесс обработки прекращается.
В начальный период обработки следующей детали абразивные бруски, соприкасаясь с ше-
роховатой поверхностью, |
самозатачиваются |
|
и восстанавливают режущие свойства. |
||
Суперфинишированием |
можно |
обрабаты- |
вать цилиндрические, конические, |
плоские |
и сферические поверхности деталей из закален-
ной стали, реже —из чугуна и бронзы. При этом шероховатость поверхности снижается до Ra = 0,012 0,1 мкм, опорная поверхность увеличивается с 20 — 30 до 80 — 90%, удаляется дефектный поверхностный слой.
Припуск на сторону на 10 — 20% должен превышать высоту неровности поверхности, чтобы не оставалось следов предыдущей обработки после суперфиниширования (табл. 75). В качестве режущего инструмента применяют главным образом абразивные бруски, реже — чашечные и плоские круги.
При обработке деталей из чугуна, цветных металлов и незакаленной стали применяют инструмент из карбида кремния; бруски из электрокорунда используют для суперфиниширования деталей из закаленных сталей.
В процессе суперфиниширования работоспособность брусков быстро снижается из-за заполнения режущей поверхности и пор металлической стружкой, вызывающей засаливание брусков. Поэтому наиболее эффективным для суперфиниширования является применение абразивных брусков, у которых поры заполнены серой, стеарином, кумарином и другими органическими веществами, выполняющими роль твердого смазочного материала. Под влиянием выделяющейся теплоты в зоне резания на режущей контактной поверхности бру-
ска |
смазочный материал частично плавится |
и |
смазывает рабочие участки инструмента |
и детали, уменьшает работу трения и препятствует налипанию металлической стружки на режущую поверхность бруска. В результате достигается увеличенный съем металла при одновременном снижении параметра шероховатости обрабатываемой поверхности и повышении стойкости брусков.
По сравнению со стандартными абразивными брусками бруски с твердым смазочным материалом обеспечивают увеличенный на 30-50% съем металла, двух-, трехкратное снижение параметра шероховатости
поверхности и до 5 раз повышают стойкость инструмента. Для эффекта смазывания необ-
ходимо подобрать режимы суперфиниширования, обеспечивающие достаточное выделение теплоты для расплавления смазочного материала на режущей поверхности бруска.
Характеристика абразивных брусков, работающих с твердым смазочным материалом, должна отличаться от характеристики стандартных не пропитанных брусков; твердость брусков, подлежащих пропитке, обычно выбирают на 10 — 20 единиц HRB ниже. Диапазон разброса твердости брусков в комплекте