
Учебное пособие 800680
.pdf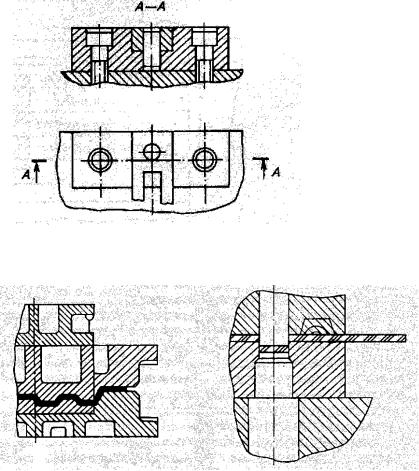
Рис. 2.23. Изображение крепѐжных деталей на сборочном чертеже штампа.
Рис. 2.24. Изображение полуфабриката или исходной заготовки в виде «обстановки» на разрезах и сечениях.
Допускается не выполнять рабочие чертежи на все или часть деталей штампа. При этом все данные для изготовления деталей, а также для сборки и наладки штампа указывают в спецификации и на сборочном чертеже в соответствии с требованиями ГОСТ 2.109. Документацию штампа без выпуска рабочих чертежей деталей выполняют на штамп,
50
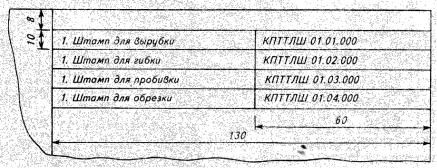
предназначенный для изготовления сложной детали, форма и размеры которой при изготовлении штампа заданы шаблоном (мастер-моделью), а также во всех случаях, когда на сборочном чертеже и в спецификации штампа можно без ущерба для ясности чертежа привести все данные, необходимые для изготовления деталей.
В зоне 8 (см. рис. 2.16) на первом листе сборочного чертежа штампа в правом верхнем углу допускается помещать таблицу, содержащую наименования и обозначения штампов, входящих в комплект для штамповки данной детали. Размеры таблицы и пример ее заполнения приведены на рис. 2.25.
Рис. 2.25. Фрагмент сборочного чертежа с табличной информацией о комплектности штампов для изготовления
детали или сборки узла.
Деталь на операционном эскизе выполняют в том положении, в каком она обрабатывается на данном штампе. На этом изображении детали должны быть указаны только те размеры, которые необходимы для изготовления и контроля штампа и для фиксации детали.
На изображении штампуемой детали предпочтительно обозначать оси штампа и угол поворота детали, если она повернута на штампе. Если штампуемая деталь на данном штампе штампуется частично, то допускается изображать на эскизе только штампуемый участок, особенно если это крупногабаритная деталь. Допускается под операционным
51
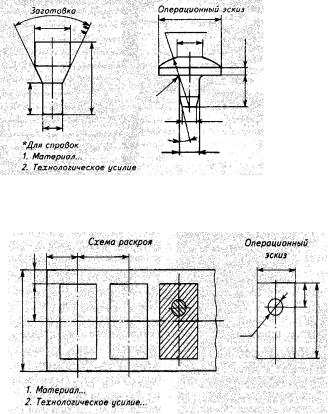
эскизом помещать необходимые сведения, например материал, технологическое усилие и другие данные, а также помещать слева от операционного эскиза изображение заготовки — исходной или полученной после предыдущей штамповочной операции (рис. 2.26). Когда исходная заготовка — полоса или лента, переходы штамповки необходимо показывать на схеме раскроя (рис. 2.27). Заготовку, схему раскроя совместно с операционным эскизом штампуемой детали допускается изображать на отдельном листе (последнем) сборочного
Рис. 2.26. Фрагмент сборочного чертежа с эскизом исходной или промежуточной заготовки.
Рис. 2.27. Фрагмент сборочного чертежа с операционным эскизом и раскроем полосы (ленты).
52
чертежа. В виде самостоятельных пунктов записываются технические требования к изготовлению и эксплуатации штампа. В технических требованиях указываются: расшифровка принятых на чертеже условных обозначений; содержание, место и способ нанесения, а также размер шрифта маркировки штампа; особенности сборки рабочих элементов; условия безопасной работы оператора-штамповщика; другие требования, обусловленные конструкцией штампа.
В технических требованиях или на чертежах штампа указывают: допуск параллельности верхней (опорной) плоскости верхней плиты относительно нижней (опорной) плоскости нижней плиты (см. рис. 2.17); допуск перпендикулярности осей колонок к опорной плоскости соответствующей плиты (см. рис. 2.19).
Основная надпись и требования к ней выполняются по форме 1 в соответствии с ГОСТ 2.104. Указанное в основной надписи сборочного чертежа наименование штампа должно соответствовать ГОСТ 15830 и ГОСТ 18970.
Исходя из изложенной методики, порядка и этапов проектирования штампов сборочный чертеж разделительного штампа выполняется в такой последовательности.
Выполняется эскиз штампа (главный вид или разрез и план низа).
Определяется необходимое количество основных и вспомогательных проекций сборочного чертежа и укрупнѐнно в виде прямоугольных областей (см. рис. 2.16) наносятся на листы контуры мест под проекции и другие поля с учетом требований и рекомендаций, изложенных ранее.
Первоначально графическое изображение основных проекций сборочного чертежа штампа вычерчивается на месте главного вида (разреза) и на месте плана низа. Это графическое изображение дублирует операционный чертеж детали. Рекомендуется предварительно выполнить на сборочном чертеже операционный эскиз штампуемой детали, эскиз заготовки (или схему раскроя). Расчетным путем определяется
53
центр давления штампа, на планах низа и верха наносят оси штампа, которые на чертежах деталей штампа должны служить конструкторскими базами для указания размеров, определяющих взаимное расположение деталей на штампе (см. рис. 2.18 или 2.20). В случаях, когда центр давления штампа совпадает с точкой пересечения осей симметрии штампуемого контура и в плане верхняя часть штампа крепится хвостовиком, допускается не наносить надпись «Ось штампа».
На главном виде (разрезе) вычерчивают рабочие элементы штампа (матрицы, пуансоны, ножи) с ориентацией их к операционному чертежу детали так, чтобы их положение соответствовало сомкнутому расположению верхней и нижней частей штампа. На проекции плана низа вычерчивают контуры рабочих отверстий матрицы. Расчетным путем проверяют на прочность нестандартные рабочие элементы штампа.
Затем вычерчивают места крепления рабочих элементов штампа. При этом крупногабаритные матрицы и пуансоны крепятся непосредственно к верхней и нижней плитам штампа, а малогабаритные — соответственно в матрице и пуансонодержателях.
Вопрос об установке подкладных плит между опорным торцем инструмента и плитами блока штампа решается расчетным путем (по допустимым удельным нагрузкам на плиты).
Далее вычерчивают фрагменты проекции схемы раскроя на главном виде (разрезе) и на плане низа в целях последующего размещения элементов базирования заготовки. Элементами базирования заготовки являются: направляющие планки, трафареты, фиксаторы, упоры.
На завершающем этапе проектирования общего вида штампа компонуют элементы съема детали или отхода с пуансона, выбирают тип съемника (или буферный), вычерчивают элементы фиксации (штифты или направляющие узлы), крепления (винты, болты), съемника, трафаретов и направляющих планок. Толщину нижней и верхней плит
54
выбирают конструктивно и проверяют расчетом исходя из габаритные размеров штампа, способа крепления к плитам деталей и конструкции хвостовика.
Стандартный блок штампа выбирают с направляющими скольжения или качения, руководствуясь габаритными размерами рабочей зоны штампа в плане и принятой схемой направляющих устройств. В соответствии с расчетом уточняют толщину нижней и верхней плит.
55
3.ШТАМПЫ ХОЛОДНОЙ ШТАМПОВКИ. 3.1. Порядок проектирования штампов.
Большую группу технологической оснастки в ХШП составляют разделительные, гибочные и вытяжные штампы листовой штамповки и штампы объемной штамповки.
С помощью штампов выполняются различные операции обработки деталей приборов и машин из листового и сортового проката, а именно: отрезка, вырубка, пробивка и пр.
Применение штампов холодной штамповки для изготовления деталей машин и приборов позволяет увеличить производительность труда на операциях формообразования, сократить количество операций. Частая смена объектов производства требует создания новых конструкций штампов, знания методов их расчета, конструирования, изготовления, сокращения сроков подготовки производства. Следует иметь в виду, что в мелкосерийном и среднесерийном производствах целесообразно использовать автоматизированное оборудование с быстропереналаживаемыми штампами. В единичном производстве рационально применение универсально-переналаживаемых штампов поэлементной штамповки.
Принципиально новые требования, предъявляемые к штампам холодной штамповки, определены необходимостью создания гибких автоматизированных производств. В этих условиях конструкции штампов должны отвечать требованиям автоматизации наладки и переналадки технологических систем.
Унификация и стандартизация элементов штампов холодной штамповки создают основу для автоматизированного проектирования штампов с использованием персональных компьютеров, а также создают предпосылки для значительного сокращения сроков технологической подготовки производства.
Классификация штампов ХШ по назначению приведена на рис. 3.1, а классификация основных узлов и деталей
56
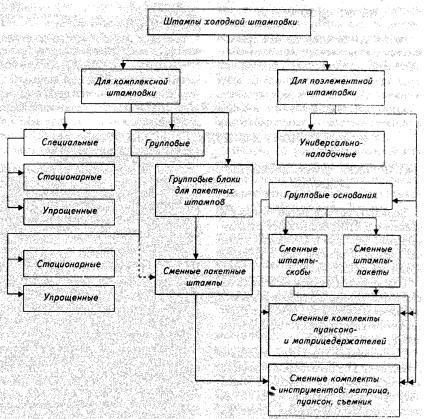
штампов — на рис. 3.2. Имея основные исходные данные,
Рис. 3.1. Классификация штампов по назначению.
приступают к выбору типа штампа и его узлов. Важнейший этап проектирования штампов — конструирование, которое требует от специалиста не только соответствующих знаний, навыков и умений, но и изобретательности, упорства, наблюдательности, смелости принятия решения, трудолюбия. Обычно этот этап является самым трудным и ответственным, так как на правильный выбор конструкции штампа оказывает существенное влияние большое число факторов. К основным из них относятся:
57

•конфигурация и размеры штампуемой детали;
•требуемая точность штамповки;
Рис. 3.2. Классификация основных узлов и деталей штампов.
•форма исходного материала (лист, полоса, лента,
отход);
•наличное оборудование штамповочного цеха;
•технические возможности инструментального цеха. Одним из решающих факторов является экономический
—количество производимых деталей и себестоимость изготовления штампа.
На первом этапе проектирования на основе подробного анализа всех особенностей формы и размеров штампуемой летали и технических требований к ней, а также с учетом объема ее выпуска, режима работы штампа, усилия штамповки и других факторов выбирают наиболее экономичный в
58
заданных условиях производства тип штампа и его ориентировочную конструкцию. В крупносерийном и массовом производствах от конструкций штампов требуются повышенная надежность в работе и высокая стойкость. Здесь оправданы штампы, которые имеют высокую степень конструктивной сложности, обеспечивающей получение деталей заданных размеров и точности.
В мелкосерийном производстве требования к стойкости и сложности штампов менее высокие, однако, здесь важно обеспечить многократное использование отдельных элементов штампа при штамповке различных однотипных деталей.
На втором этапе проектирования штампов рассчитывают требуемое усилие и работу деформации, определяют центр давления штампа, подбирают конструктивные элементы штампа и устанавливают их рабочие размеры и допуски, рассчитывают на прочность основные детали штампа, выбирают конструкционный материал для их изготовления и назначают режим термообработки, решают вопросы о необходимости применения износостойких вставок, наплавок, напылений и т. д.
На третьем этапе вычерчивают штамп в соответствии с требованиями ЕСКД. Для этого по общему виду штампа, его габаритным размерам, расчетному усилию штамповки и затрачиваемой работе деформации подбирают необходимое штамповочное оборудование, причем если для технолога достаточно знать основные параметры соответствующего оборудования (допускаемое усилие, ход рабочего органа, число ходов, размер штампового пространства, наличие амортизаторов, а также оснащенность средствами механизации), то для конструктора штамповой оснастки этих сведений недостаточно. Характеристику оборудования дополняют эскизами основных сборочных единиц со всеми необходимыми размерами, т. е. указывают места крепления штампа, расстояние от стола до направляющих и от оси стола до станины, тип и размеры выталкивателей, размеры отверстий в столе и в подштамповой плите для удаления детали, а также
59