
Учебное пособие 800680
.pdf
Продолжение табл. 3.20
170

Окончание табл. 3.20
3.7. Расчет стойкости штампов.
В настоящее время основными способами определения стойкости штампов ХШ являются экспериментальные исследования, а также обобщение производственного опыта.
Использование расчетно-аналитического метода, основанного на обобщении статистических данных, позволяет технологам и конструкторам заранее рассчитать потребное число штампов и более обоснованно решать вопросы планирования подготовки производства.
Расчет стойкости вырубных и пробивных штампов. По данным Беньи, на стойкость штампа до переточки влияют толщина и химический состав исходного материала, материал
171

рабочих частей штампа, конструкция штампа и вид операции (пробивка отверстий, вырубка и т. д.), степень сложности изделия, качество изготовления штампа, способы смазки штампуемого материала, состояние пресса, точность наладки и др.
Формула Беньи для определения стойкости штампа Т до полного износа имеет следующий вид:
T |
h |
T |
zmax |
zmin |
T K |
|
K |
K |
|
K |
K K |
|
, |
|
|
|
f |
sz |
b |
||||||||
|
|
a |
|
2h1 |
t |
|
a |
|
|
||||
|
h1 |
2tg |
|
|
|
|
|
|
|
|
здесь h — суммарная высота допустимого для сошлифовки слоя за все переточки,
hzmax zmin ,
2tg h12
где а2 —уклон стенок рабочего отверстия матрицы; h1 — толщина сошлифовываемого слоя при переточке штампа; Та — исходная стойкость, обычно равная 25 000 штампоударам + 20 % (в зависимости от условий работы штампа); zmax — зазор (для материалов толщиной 0,05…6 мм zmax равен 10…20 % от толщины материала); zmin = (0,4…0,5)×zmax; Кf — коэффициент, учитывающий тип штампа (для вырубного Kf = 1,0, для пробивного или комбинированного Kf = 0,8); Kt — коэффициент, учитывающий характер направления рабочих частей (без направления Kf - 0,8, для пакетного направления Кt = 1,0, для блока штампа на колонках Кt = 1,5); Ksz — коэффициент, учитывающий материал рабочих частей (для углеродистой сталиKsz, = 1,0, для легированной — Кsz = 1,5); Ка — коэффициент, учитывающий механические свойства штампуемого материала (для углеродистой стали с σв > 500 МПа Ка = 1,0, с σв > 500 МПа Ка = 0,8, для легированной стали с σв < 900 МПа Ка = 0,7, с σв > 900 МПа Ка = 0,6, для твердой бронзы Ка = 1,5, для мягкой бронзы Ка = 1,8, для алюминия Ка = 2,1); Kδ — коэффициент, учитывающий толщину штампуемого материала
(для δ = 0,05 ÷ 0,3 Kδ = 1,0, для δ = 0,3÷ 1,0 Kδ = 1,1, для δ = 1,0 ÷ 3,0 мм Kδ =0,8, для δ = 3,0 ÷ 6,0 мм Kδ = 0,5); Кb —
коэффициент, учитывающий сложность контура детали (для
172

простого контура Кb = 1,0, усложненного — Кb = 0,8, для сложного — Кb = 0,6).
Расчет стойкости по формуле Беньи дает результаты,
которые согласуются с практикой. |
|
|
|
Для |
ориентировочного |
расчета |
стойкости |
(штампоударов) штампа до полного износа Т0 Д. А. Вайнтраубом рекомендована упрощенная эмпирическая формула, пригодная для вырубных (на провал) и последовательных штампов при толщине листа до 5…6 мм и материале рабочих частей из стали У10А:
|
Kф106 |
To |
(12 t) , |
в
где σв — предел прочности штампуемого материала, МПа; t — толщина материала, мм; Кф — коэффициент формы контура, значения которого в зависимости от простой, усложненной и сложной формы контура штампа принимаются соответственно
8, 6,5 и 5.
Для пробивных и совмещенных штампов Т0 будет ниже на 15…20 %.
Расчет стойкости вырубных (пробивных) штампов ведется но стойкости матрицы, так как на практике основное значение имеет износ рабочего отверстия матрицы, а не пуансона. Размер рабочей части пуансона всегда больше высоты рабочего пояска отверстия матрицы или размера сошлифовываемой части у матрицы с конусным рабочим отверстием.
Расчет стойкости матрицы производится исходя из следующих соображений. Количество переточек п, которое можно сделать до окончательного износа матрицы, определяется выражением:
n h ,
где h — высота пояска матрицы или сошлифовываемой части у матрицы с конусом от зеркальной ее поверхности; δ —
173

толщина слоя металла, снимаемая при каждой заточке и зависящая от толщины материала S: при S до 1,5 мм δ= 0,1 ÷ 0,2 мм, при S от 1,5 до 4 мм δ= 0,2 ÷ 0,4 мм.
Стойкость штампа до смены матрицы С1 определяется по формуле:
С1 |
h |
1 C |
, |
|
здесь Сη — стойкость штампа до переточки, определяемая из табл. 3.21; η — коэффициент, учитывающий снижение стойкости вырубного штампа после каждой переточки (примерно на 5…10 %). Стойкость штампа до полного износа:
C2 C1 m 1 ,
где m — возможное количество замен износившихся матриц. Из вышеизложенного следует, что износ вырубного
штампа (при заданных форме, размерах и материале детали) зависит в основном от точности взаимного расположения его рабочих частей и их износоустойчивости.
Таблица 3.21 Средняя стойкость различных типов штампов между
двумя переточками или ремонтами (тыс. ударов).
174

В табл. 3.22 приведены данные о стойкости разделительных штампов, оснащенных твердым сплавом.
Таблица 3.22 Стойкость штампов, оснащѐнных твѐрдым сплавом между
переточками.
Номограмма для ориентировочного расчета полной стойкости разделительных штампов по эмпирической формуле Д. А. Вайнтрауба приведена в табл. 3.23. Исходная ячейка номограммы определяется координатой изменения толщины и σв штампуемого материала, затем корректируется по сложности контура и типу штампа. Для материалов рабочих частей вводится поправка от 0,5 до 1,6. Число, находящееся в ячейке, умножают на 10°.
175
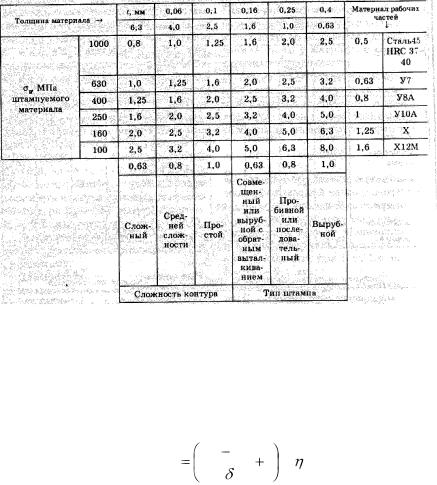
Таблица 3.23 Номограмма для расчѐта полной стойкости разделительных
штампов (Т0×106 ударов).
Расчет стойкости гибочных и вытяжных штампов. Для гибочных и вытяжных штампов окончательный износ их рабочих частей обусловливается изменением зазора между матрицей и пуансоном за пределы допустимого либо сильным искажением ради уса закругления кромок штампа.
Расчет стойкости этих штампов до полного износа (смены) рабочих частей C1' можно установить из выражения
С' |
D1 |
D0 |
1 C' ' , |
|
|
||
1 |
2 |
' |
|
|
|
а до полного износа штампа С'2 из зависимости С'2 = C'1(m'+ 1).
здесь D1 — максимально допустимый внутренний размер (диаметр) гибочной или вытяжной матрицы; D0 — начальный размер (диаметр) матрицы: δ' — толщина слоя (по радиусу),
176

снимаемого при каждом исправлении матрицы; С — стойкость штампа до исправления; т' — возможное количество замен матрицы; η’— коэффициент снижения стойкости, примерно равный л,.
Расчет стойкости штампов для объемной штамповки.
Расчет стойкости указанных штампов до исправления ведут с момента появления небольших дефектов, которые еще могут
быть исправлены механическим или другими способами (хромированием, наплавлением), а до полного износа — с того момента, когда отштампованные на них детали перестают отвечать требованиям чертежа или техническим условиям.
Нормы стойкости штампов XIII. В табл. 3.24 приведены данные о стойкости различных типов штампов ХЛШ до полного износа.
Втабл. 3.25 приведены данные изменения стойкости штампов ХОШ при обработке различных конструкционных материалов.
Втабл. 3.26 и 3.27 приведены ориентировочные данные о стойкости штампов ХОШ до полного износа.
Таблица 3.24 Стойкость штампов ХЛШ до полного износа (тыс. дв. ходов).
177

Таблица 3.25 Стойкость штампов ХОШ при обработке различных
материалов (тыс. ударов).
Таблица 3.26 Стойкость штампов ХОШ до полного износа (тыс. ударов).
Таблица 3.27 Стойкость штампов холодного выдавливания трубчатых
деталей до полного износа (тыс. ударов)
178
3.7.1. Меры, повышающие стойкость штампов.
Очистка поверхности штампуемого материала от загрязнений. В целях сохранения штампов от преждевременного износа необходимо применять металл с чистой поверхностью. Наличие окалины или песка на поверхности заготовки вызывает повышенный износ штампов. При этом на вырубных штампах износ выражается обычно в преждевременном затуплении режущих кромок матрицы и пуансона, на формоизменяющих штампах — в образовании преждевременных царапин и рисок из-за въедания и прилипания частиц металла к стенкам матрицы. Для предохранения от вышеуказанных явлений материал или заготовку перед штамповкой необходимо подвергнуть травлению в соответствующих кислотах с последующей промывкой в холодной и горячей воде и нейтрализацией в слабых щелочных растворах при температуре 60…70°С.
Стойкость штампов при штамповке травленых материалов 1 (мягкая сталь) толщиной до 1,5 мм на 16…20 % выше, чем при штамповке нетравленых материалов 2 (рис.
3.36).
Смазочные материалы штампуемого материала и штампа. Смазочные материалы при вырубных операциях оказывают влияние на усилие проталкивания детали, а следовательно, и на общее усилие вырубки.
При работе без смазки усилие на проталкивание возрастает на 30…40 % по сравнению с проталкиванием со смазкой, что влияет и на стойкость штампа.
Применение смазочного материала повышает стойкость инструмента еще и потому, что он
охлаждает режущие кромки пуансона и матрицы, которые во время работы заметно нагреваются.
При вырубке материалов толщиной до 2 мм стойкость штампов с применением смазочного средства 1 повышается на 20…30 % и больше по сравнению со стойкостью штампа без смазочного средства 2 (рис. 3.37). В качестве смазочного
179