
Методы оптимизации технологических процессов. Кузовкин А.В., Кузовкин В.П
.pdf2
МИНИСТЕРСТВО ОБРАЗОВАНИЯ РОССИЙСКОЙ ФЕДЕРАЦИИ Воронежский государственный технический университет
Кафедра “Технология машиностроения”
А.В. Кузовкин, В.П. Кузовкин, В.П. Смоленцев
МЕТОДЫ ОПТИМИЗАЦИИ ТЕХНОЛОГИЧЕСКИХ ПРОЦЕССОВ
Учебное пособие
ВОРОНЕЖ 2000

УДК 682. 3. 001.63
Кузовкин А.В. Методы оптимизации технологических процессов: Учеб. пособие / А.В. Кузовкин, В.П. Кузовкин, В.П. Смоленцев. Воронеж: Изд-во ВГТУ, 2000. 77 с.
В учебном пособии изложены теоретические основы и описаны алгоритмы оптимизации технологических процессов машиностроения, которые могут быть реализованы с помощью непрерывных дифференциальных уравнений. Приведенные сведения ориентированы на прикладное использование в САПР технологических процессов. Издание соответствует рабочей программе дисциплины "Методы оптимизации технологических процессов" и предназначено для студентов специальности 120100 "Технология машиностроения" всех форм обучения, аспирантов и инженерно – технических работников, которые работают в области поиска и принятия оптимальных решений.
Учебное пособие подготовлено на магнитном носителе в текстовом редакторе MSWord 97 и содержится в файле "Motp.rar".
Табл. 15. Ил. 39. Библиогр.: 15 назв.
Научный редактор д-р техн. наук, проф. В.П. Смоленцев
Рецензент: кафедра ремонта машин Воронежской государственной лесотехнической академии; д-р техн. наук В.Н. Старов
Издается по решению редакционно-издательского совета Воронежского государственного технического университета.
Кузовкин А.В., Кузовкин В.П., Смоленцев В.П., 2000 Оформление. Издательство Воронежского государственного технического университета, 2000
СОДЕРЖАНИЕ |
|
ВВЕДЕНИЕ......................................................................................................................................... |
4 |
1.ОСНОВНЫЕ ПОНЯТИЯ, ТЕРМИНЫ И ОПРЕДЕЛЕНИЯ ТЕХНОЛОГИИ |
|
МАШИНОСТРОЕНИЯ...................................................................................................................... |
5 |
2.ПРОЕКТИРОВАНИЕ ТЕХНОЛОГИЧЕСКИХ ПРОЦЕССОВ ОБРАБОТКИ ДЕТАЛЕЙ ....... |
8 |
2.1.Сбор и анализ исходных данных для проектирования ТП................................................... |
8 |
2.2. Технологический контроль чертежа и технических условий ............................................. |
8 |
2.3. Выбор типа производства ....................................................................................................... |
8 |
2.4. Выбор метода получения заготовки..................................................................................... |
10 |
2.5. Выбор технологических баз.................................................................................................. |
11 |
2.6. Разработка маршрутной технологии обработки детали .................................................... |
13 |
2.7. Определение оптимальных припусков на обработку......................................................... |
15 |
2.8. Определение режимов резания............................................................................................. |
19 |
2.8.1. Выбор режимов по таблицам ......................................................................................... |
19 |
2.8.2. Аналитический расчет режимов резания ...................................................................... |
20 |
2.9. Завершающие этапы разработки технологического процесса .......................................... |
21 |
3. ОСНОВНЫЕ ПОНЯТИЯ ТЕОРИИ ОПТИМИЗАЦИИ ............................................................ |
23 |
4. ОПТИМИЗАЦИЯ БЕЗ НАЛОЖЕНИЯ ОГРАНИЧЕНИЙ........................................................ |
25 |
4.1. Классический метод поиска оптимума функции ................................................................ |
25 |
4.1.1. Классический метод для функции одной переменной ................................................ |
25 |
4.1.2. Классический метод для поиска оптимума функции нескольких переменных ........ |
29 |
4.2. Поиск оптимума методом Ньютона ..................................................................................... |
31 |
4.3. Методы поиска экстремального значения функции........................................................... |
32 |
4.3.1.Методы Фибоначчи и "Золотого сечения"..................................................................... |
32 |
4.3.2. Квадратичная интерполяция функции одной переменной.......................................... |
40 |
4.3.3. Кубическая интерполяция функции .............................................................................. |
43 |
5. МЕТОДЫ ПРЯМОГО ПОИСКА ДЛЯ ФУНКЦИИ НЕСКОЛЬКИХ ПЕРЕМЕННЫХ......... |
50 |
5.1. Метод поиска по образцу ...................................................................................................... |
53 |
6. ЛАБОРАТОРНЫЙ ПРАКТИКУМ ............................................................................................. |
55 |
6.1. Лабораторная работа № 1. Определение экстремума функции одной переменной........ |
55 |
6.2. Лабораторная работа № 2. Определение экстремума функции методом Ньютона ........ |
58 |
6.3. Лабораторные работы № 3 и 4. Поиск оптимума методом Фибоначчи и "золотого |
|
сечения".......................................................................................................................................... |
62 |
6.4. Лабораторная работа № 5. Определение экстремума функции с помощью |
|
аппроксимации кривыми ............................................................................................................. |
68 |
7. КУРСОВОЕ ПРОЕКТИРОВАНИЕ ............................................................................................ |
71 |
7.1. Цель и задачи курсовой работы............................................................................................ |
71 |
7.2. Объем работы по работе, оформление................................................................................. |
71 |
7.2.1. Объѐм работы................................................................................................................... |
71 |
7.2.2. Оформление работы ........................................................................................................ |
71 |
7.3. Методические указания к выполнению проекта ................................................................ |
71 |
7.4. Задание на курсовую работу ................................................................................................. |
75 |
СПИСОК ЛИТЕРАТУРЫ................................................................................................................ |
78 |
ВВЕДЕНИЕ
Настоящая книга предназначена для студентов и аспирантов, которые хотели бы использовать методы оптимизации в качестве инструмента для решения конкретной задачи проектирования и подготовки технологического процесса, но не обладают знаниями в области нелинейного программирования.
В настоящее время решение задачи разработки технологического процесса изготовления и ремонта изделий машино- и приборостроения невозможно без широкого и всестороннего использования средств вычислительной техники и систем автоматизированного проектирования технологических процессов (САПР ТП). Решение каждой задачи по проектированию ТП подразумевает под собой выбор оптимального варианта технологии и требует применения нескольких методов оптимизации и большого числа алгоритмов поиска такого оптимального решения. В связи с этим в САПР наряду с автоматизированным поиском решений применяется метод "экспертных" оценок, при котором пользователь может активно влиять на процесс принятия решения. При этом в результате диалога проектировщика с ЭВМ происходит смена типа и количества оптимизируемых параметров, выбор метода поиска оптимума функции и т.д.
Задачи, решаемые посредством автоматизированного проектирования, можно разделить на формализованные и формализованные не полностью. При этом для решения задач первого типа должны быть известны все исходные данные, а само решение может быть получено автоматизированным путем с помощью ЭВМ, которая работает по заранее разработанным алгоритмам. В не полностью формализованных задачах исходных данных недостаточно для автоматического получения однозначного ответа. При их решении окончательный выбор направления получения результата принадлежит технологу.
Как видно из вышесказанного, современному инженеру-технологу необходимо в совершенстве овладеть всеми элементами теории оптимизации: построение математической модели объекта (в нашем случае технологического процесса), численные методы оптимизации, способы применения методов оптимизации к автоматизированному проектированию, методы конструирования алгоритмов принятия решений и их программная реализация.
1.ОСНОВНЫЕ ПОНЯТИЯ, ТЕРМИНЫ И ОПРЕДЕЛЕНИЯ ТЕХНОЛОГИИ МАШИНОСТРОЕНИЯ
Совокупность методов и приемов изготовления машин, выработанных в течение времени и используемых в определенной области производства, составляет технологию этой области. Различают технологию литья, технологию обработки давлением, технологию механической обработки, технологию сборки машин и т. п. Все эти технологии в совокупности составляют технологию машиностроения, охватывающую процесс производства от получения заготовки и кончая готовым изделием. Тем не менее, под "технологией машиностроения" принято понимать дисциплину, которая изучает в основном механическую обработку деталей и сборку машин, а вопросы выбора заготовок и методы их изготовления затрагиваются лишь попутно. Это можно объяснить тем, что заданные формы, точность и качество деталей достигаются за счет механической обработки, а другие способы не всегда позволяют обеспечить конструкторские требования. При механообработке возникает наибольшее число проблем, связанных с необходимостью выполнения конкретных технологических требований. Здесь и открываются широкие возможности для применения теории оптимизации как инструмента для разрешения этих вопросов.
Основные понятия:
Производственный процесс - это совокупность отдельных процессов, осуществляемых с целью получения из материалов готовых изделий. Наряду с основными, связанными с изготовлением и сборкой деталей машин, в производственный процесс включается и все вспомогательные операции: транспортировка, контроль, изготовление приспособления и инструмента и т. д.
Технологический процесс - это последовательное изменение формы, размеров, свойств материала с целью получения детали или изделия в соответствии с заданными техническими требованиями. Технологический процесс - это часть производственного процесса. По ГОСТ 3. 1109 - 73 технологический процесс может быть проектным, рабочим, единичным, типовым, стандартным, временным, перспективным, маршрутным, операционным, маршрутнооперационным.
Производственный процесс может быть разделен на следующие этапы:
1)изготовление заготовок;
2)обработка заготовок с удалением слоя материала, например обработка резанием, для получения детали с окончательными размерами и формами;
3)сборка отдельных деталей в узлы и агрегаты (сборочные единицы);
4)регулировка и испытание готового изделия
Структура технологического процесса
Весь процесс механической обработки деталей состоит из отдельных час-
тей:
Технологическая операция - часть технологического процесса, выполняемая на одном рабочем месте и охватывающая все последовательные действия рабочего и оборудования по обработке заготовки.
Установ - это часть операции, выполняемая при одном закреплении заготовки на станке или приспособлении.
Позиция - это каждое отдельное положение заготовки, занимаемое ею относительно станка при неизменном ее закреплении. Изменение положения происходит под воздействием перемещающих или поворотных устройств.
Операция разделяется на переходы - технологические и вспомогательные. Технологический переход - законченная часть технологической операции, который характеризуется постоянством применяемого инструмента, по-
верхностей, режимами резания.
Вспомогательный переход - законченная часть технологической операции, состоящая из действий, которые не сопровождаются изменением формы, размеров, шероховатости поверхности, но необходимых для реализации технологического перехода.
В свою очередь переход состоит из рабочих и вспомогательных ходов: Рабочий ход - часть технологического перехода, охватывает все действия,
связанные со снятием одного слоя материала.
Вспомогательный ход - законченная часть технологического перехода, которая заключается в однократном перемещении инструмента относительно заготовки, не сопровождаемого изменением формы, размеров, шероховатости поверхности или свойств материала, но необходимого для выполнения рабочего хода.
Наряду с тем, что при проектировании технологического процесса технологом определяется план и метод обработки деталей, одновременно происходит выбор технологического оснащения и оборудования для реализации каждой операции.
Выбор типа оборудования определяется его возможностью обеспечить выполнение технических требований, предъявляемых к обрабатываемой детали. Другим критерием выбора оптимального типа оборудования является его производительность. Этот показатель определяет экономическую эффективность применения станка и зависит от времени работы станка и типа производства. Окончательное решение о выборе конкретного типа оборудования принимается на основе технико-экономического сравнения обработки детали как минимум на двух сопоставляемых станках.
При проектировании технологического процесса обработки деталей, когда составляется план и выбирается метод обработки, одновременно с выбором станка назначают тип и вид приспособления, используемого на данном станке на данной операции. Приспособление может являться принадлежностью станка (кулачки, тиски и т. п.) или быть универсально-сборными (УСП). Нередко возникают ситуации, когда для данной операции требуется специальное приспособление, разрабатываемое и проектируемое технологом. Выбор приспособления во многом определяется типом производства. В единичном и мелком производстве используют приспособления универсального типа, а специальные практически не проектируют и не используют. Крупносерийное и массовое производство характеризуется применением специальных приспособлений. Их
применение дает существенный экономический эффект за счет сокращения основного и вспомогательного времени выполнения операции.
Выбор станка и приспособления на каждую операцию сопровождается выбором необходимого режущего инструмента, обеспечивающего наибольшую производительность, требуемую точность и шероховатость поверхности. Выбор типа инструмента зависит от нескольких факторов: вид станка; метод обработки; материал заготовки; ее размер и конфигурация; требуемой точности и шероховатости; типа производства. Основным элементом, влияющим на эксплуатационные свойства режущего инструмента, является режущая часть, ее геометрия и материал.
Разработка технологического процесса на каждой операции завершается выбором мерительного инструмента, необходимого для контроля формы и размеров детали в процессе ее изготовления. Выбор того или иного вида инструмента определяется в первую очередь типом производства:
1)При единичном и мелкосерийном производстве применяется инструмент общего назначения (штангенциркуль, микрометр, линейка и т. п.). Это связано с тем, что повторяемость деталей определенного типоразмера в таких условиях очень мала.
2)При серийном и массовом производстве с частой повторяемостью деталей одних и тех же размеров применяют специальный мерительный инструмент - калибры, шаблоны, измерительные приспособления, приборы, автоматические устройства.
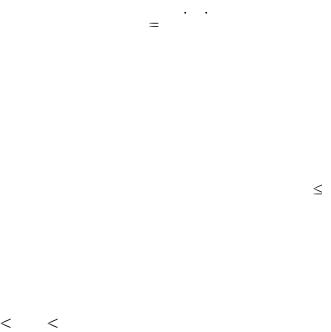
2.ПРОЕКТИРОВАНИЕ ТЕХНОЛОГИЧЕСКИХ ПРОЦЕССОВ ОБРАБОТКИ ДЕТАЛЕЙ
Разработка технологического процесса производства деталей на машиностроительном заводе ведется в определенной последовательности и состоит из нескольких этапов, о которых рассказано ниже.
2.1.Сбор и анализ исходных данных для проектирования ТП
Исходные данные: чертеж детали, технические условия на ее изготовление, годовая программа выпуска.
2.2. Технологический контроль чертежа и технических условий
При этом проверяют: достаточное количество проекций, размеры, требования к точности и шероховатости поверхности детали и др. требования. Целью контроля рабочего чертежа является выявление возможности улучшения технологичности конструкции детали; уменьшения размеров обрабатываемых поверхностей для снижения трудоемкости механической обработки; повышение жесткости детали для обеспечения возможности многоинструментальной обработки и высокопроизводительных режимов резания; облегчения подвода и отвода режущих инструментов для снижения вспомогательного времени; обеспечение удобного и надежного базирования заготовок, а при простановке размеров - возможность совмещения технологических и измерительных баз и др.
2.3. Выбор типа производства
Тип производства определяется по такту выпуска изделий, который можно определить по выражению:
tв |
60 F k |
, |
(2.1) |
|
N |
||||
|
|
|
где F – полный (календарный) фонд времени работы оборудования; при односменной работе он составляет 2070 часов в год, при двухсменной – 4140 ч, при трехсменной – 6210 ч;
N – годовая программа выпуска данных деталей, шт;
k – коэффициент потерь времени на ремонт оборудования, при односменной работе k =0,99, при двухсменной – k =0.98 и трехсменной – k =0.96.
Если такт выпуска изделия отвечает условию Tшт 0,5tв , где Tшт – штучное время на наиболее характерной операции обработки, то деталь изготавливается по принципу серийного производства. К каждому станку закрепляют несколько типов деталей и обработку их ведут партиями, обеспечивая при этом высокую загрузку станка.
Если такт выпуска изделия близок или несколько ниже среднего штучного времени 0,5tв Tшт tв , то производство принимают массовым.
Кроме того определяют коэффициент серийности kс , который зависит от числа операций по обработке деталей, закрепляемых за станком в течение года:
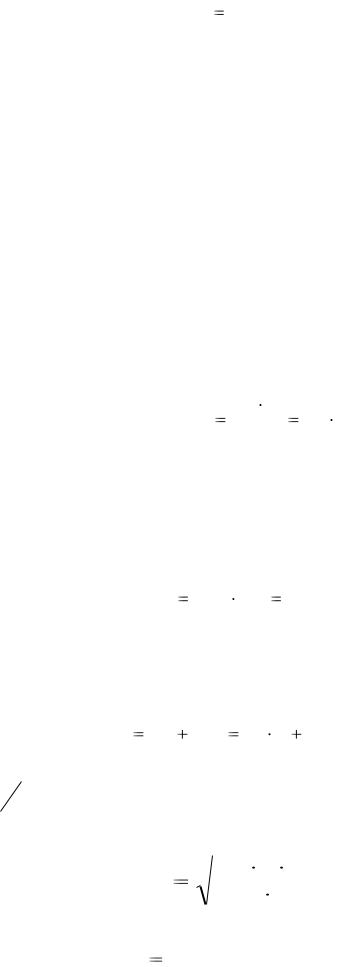
|
kс |
tв |
. |
(2.2) |
|
Tшт |
|||
|
|
|
|
|
Примерные значения коэффициента серийности в зависимости от типа |
||||
производства приведены в табл. 2.1. |
|
|
|
|
|
|
|
|
Таблица 2.1 |
Значения kc для различных типов производств |
||||
|
|
|
|
|
Значение kс |
|
|
|
Тип производства |
1 |
|
|
|
Массовое |
2...10 |
|
|
|
Крупносерийное |
10...20 |
|
|
|
среднесерийное |
>20 |
|
|
|
Мелкосерийное |
На данном этапе разработки технологического процесса в качестве задачи, решаемой методами оптимального проектирования является определение количества партий деталей "m", обрабатываемых в течении года на данном станке с минимальными экономическими затратами. Затраты на переналадку оборудования в год определяются по выражению:
|
Сn |
N |
|
|
|
Сзп |
|
|
Cn |
m, |
(2.3) |
n |
|
||||
|
|
|
|
|
где Cn - стоимость одной переналадки, руб.;
N- годовая программа выпуска деталей, шт.; n - количество деталей в партии, шт.
Затраты, связанные с задержкой оборотных средств и хранением деталей на складе в течении года, определяются по выражению:
Сзоб |
Сс |
n |
|
P |
Cc |
N p |
, |
|
||
|
|
|
|
|
(2.4) |
|||||
2 |
100 |
200m |
||||||||
|
|
|
|
|
где Cзоб. - себестоимость обработки одной детали, руб.;
p - коэффициент, учитывающий расходы на хранение и задолженность оборотных средств, %. p = 2...15% от стоимости незавершенного производства.
Общие расходы на производство партии деталей
Собщ Сзп Сзоб Сn m Cc |
N p |
|
, |
(2.5) |
|
200m |
|||||
|
|
|
Для определения оптимального количества партии вычисляем производную dCобщ. dm , и приравняв ее к нулю получаем оптимальное количество партий:
mопт |
|
Сс |
p N |
|
|
|
|
, |
(2.6) |
||
|
|
||||
|
|
200 Cn |
|
Оптимальный размер партии при этом составит:
|
N |
(2.7) |
|
nопт |
|
, |
|
mопт |
|||
|
|

2.4. Выбор метода получения заготовки
Выбор метода получения заготовки определяется следующим образом:
а) технологической характеристикой материала, т. е. его литейными свойствами и способностью подвергаться пластическим деформациям при обработке давлением, а также структурными изменениями материала заготовки в процессе ее изготовления (величина зерна в отливках, расположение волокон в поковках и т. д.);
б) конструктивными формами и размерами заготовки; в) требуемой точностью получения заготовки, шероховатостью и качест-
вом ее поверхностей; г) программой выпуска и сроком ее выполнения.
Выбранный метод должен обеспечивать наименьшую себестоимость изготовления детали, т. е. затраты на материал, получение заготовки и последующую обработку должен быть минимальным. Как видно - это еще одна задача по оптимизации проектирования технологического процесса, которая может быть решена на основе минимизации уравнения для определения себестоимости производства детали:
Сg G |
tштз |
lз |
1 |
|
z |
з |
|
E100 |
tштз k |
tшто lo 1 |
|
zo |
, |
(2.8) |
||
|
|
|
|
|
|
|
|
|||||||||
100 |
N |
100 |
||||||||||||||
|
|
|
|
|
|
|
|
где G - масса одной заготовки, кг.;
- стоимость одного кг. материала, руб.;
tштз - штучное время производства одной заготовки, мин.;
lз - тарифная ставка рабочего заготовительного цеха за одну заготовку, руб./мин.;
tштз lз. - производительная заработная плата рабочего заготовительного
цеха за одну заготовку, руб.;
zз - накладные расходы по заготовительному цеху без учета издержек Е на специальную оснастку (штампы, пресс формы и др.), %;
N - программа выпуска продукции, на которую распределяются расходы на оснастку, шт.;
k - затраты на эксплуатацию оборудования заготовительного цеха в 1 мин., руб./мин.;
tштз k - затраты на эксплуатацию оборудования заготовительного цеха
при производстве партии заготовок;
tшто - штучное время на каждую операцию механической обработки, мин.; lo - тарифная ставка рабочего обрабатывающего цеха, руб./мин.;
tшто lo - производственная заработная плата рабочих механического цеха
на производство одной детали, руб.;
zo - накладные расходы по механическому цеху, %.
На основе выражения (2.8) можно определить себестоимость изготовления деталей при разных методах изготовления заготовок и последующей меха-