
Методическое пособие 805
.pdfнию количества остаточного аустенита и появлению поверхностных и приповерхностных микротрещин, изначально слабо проявляющихся. По мере наступления усталости материала при малоцикловых нагружениях в водородосодержащих средах, они сливаются в места наибольшей концентрации накопившегося деформационного потенциала, при явном отсутствии концентраторов разрушений, и несмотря на трудоемкую полировку.
В связи с этим, разработка теоретических основ и технологий локального восстановительного упрочнения поверхности сложного профиля лопаточных деталей ротора в местах повышенной дестабилизации является актуальной задачей, обеспечения стабильности эксплуатационных характеристик роторов для разрабатываемых перспективных изделий авиационно-космического назначения.
Механизм комбинированного воздействия представляет собой комбинацию двух процессов, происходящих одновременно: механического воздействия гранул на внутреннюю прерывистую поверхность и анодного растворения при низких напряжениях, исключающих короткие замыкания между гранулами и обрабатываемым материалом. Анодный процесс растворения микронеровностей происходит под действием тока в слабо-проводящей жидкой пленке технической воды, подаваемой в зону обработки в распыленном до капельной фракции виде одновременно с микрогранулами. Окисные пленки на микрогранулах и на заготовке истончаются и разрушаются, при этом достигается плотность тока, необходимая для анодного растворение поверхностного слоя материала заготовки. Разреженная капельная фракция жидкостной составляющей практически не мешает микро-гранулам получать от напора сжатого воздуха кинетическую энергию, достаточную для деформирования и осадки микровыступов и подается в зону обработки отдельно от микрогранул.
При твёрдых сферических частицах радиусом описанной окружности R, падающих на поверхность детали со средней скоростью V, средняя скорость ее деформации составляет V/R. Средняя скорость шариков при использовании газожидкостной среды:
V |
kгж k мкш Q |
, |
(1) |
(Fc 3600) |
|
где Q – расход сжатого воздуха, м3/ч; Fс – площадь поперечного сечения отверстия сопла, м2; kгж – коэффициент, учитывающий влияние на скорость шариков газожидкостной среды определенной концетрации (kгж=0,9-0,95); kмкш – коэффициент, учитывающий влияние расхода через дозатор склонных к слипанию микрошариков на скорость потока обрабатывающей среды (kмкш=0,7-0,85).
При этом шарик должен достичь кинетической энергии K необходимой для обеспечения процесса деформирования порядка 8104 мм в секунду. Параметром регулирования является, таким образом, расход обрабатывающей среды и, следовательно, скорость деформирования микровыступов обрабатываемой поверхности. Вопрос остается в достоверном определении скорости деформи-
230
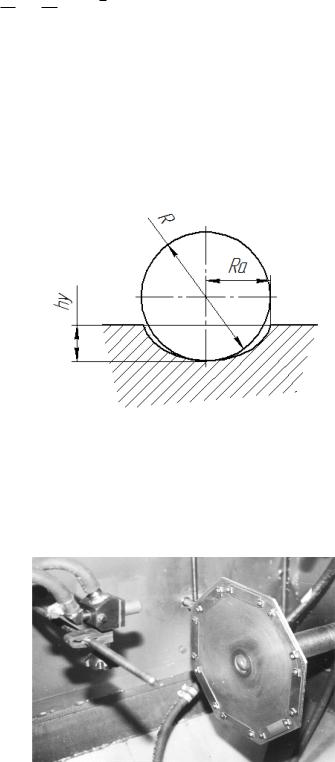
рования поверхности от микрошарика в наших условиях. Для этого надо учитывать условия движения шарика в потоке и его кинетическую энергию. В общем виде уравнение движения шарика, как показано на рис. 1, в процессе контактирования:
4 R3 dV Ra2 P |
, |
(2) |
|
3 |
dt |
где R – радиус шарика, Ra – радиус вмятины на поверхности (лунки), ρ – плотность материала детали, P – среднее давление в зоне контакта.
Стабильная пластичность наступает при значениях P = 3 Т.
Среднее давление р при соотношении E/ ТR 36, обеспечивает получение вмятины размером 0,004R для сталей, где отношение модуля текучести к модулю упругости Т/E =0,0024.
Рис. 1. Схема зоны контактирования шарика с поверхностью
Обработку образцов осуществляли при их вращении с имитатором детали в одной плоскости, с радиусом вращения центров обрабатываемых поверхностей образцов, равным 100 мм. Скорость вращения nвр=100об/мин. Имитатор с плоскими образцами в камере струйно-динамической установки показан на рис. 2.
Рис. 2. Имитатор турбины с плоскими образцами в камере струйно-динамической установки
231
Мера эффективности поверхностного упрочнения плоских образцов – глубина наклёпа и величины остаточных напряжений сжатия. Поэтому величина Zоб прогиба образцов определена как целевой параметр эксперимента. Величина Zоб измерялась с точностью +0,01 мм [1]. База измерений прогиба составляла 70 мм.
Разработанная методика и режимы позволяют управлять комбинированным процессом локального восстановления физико-механически дестабилизированных в процессе балансировки и доводки поверхностей ротора с целью получения стабильных эксплуатации показателей лопаточных деталей.
Литература
1. Сухочев, Г.А. Технологические аспекты балансировки высокооборотных роторов / Г.А. Сухочев, В.Н. Сокольников, С.Н. Коденцев // Фундаментальные и прикладные проблемы техники и технологии. – 2016. – № 2 (316). – С. 99-105.
232
УДК 621.9.047
Повышение ресурса лопаточных деталей насосного оборудования применением комбинированной обработки
А.М. Некрылов1, А.Ю. Грымзин2, Г.А. Сухочев3 1Инженер-конструктор 1 кат., аспирант гр. аТМ-2 2Инженер-конструктор 2 кат., магистрант гр. мТМ-21 3Д-р техн. наук, профессор
ФГБОУ ВО «Воронежский государственный технический университет»
В работе рассмотрены примеры использования нетрадиционных отделоч- но-упрочняющих методов обработки лопаточных деталей насосного оборудования: виброэкструзионное шлифование; упрочнение микрошариками струйнодинамическим методом в слабо проводящей газожидкостной среде. Показаны технологические схемы и возможности методов, пояснен основной принцип действия предназначенного для этого технологического оборудования.
Ключевые слова: лопаточные детали, комбинированная обработка.
Наличие в конструкции лопаточных деталей насосного оборудования технологически труднодоступных элементов в ряде случаев исключает допуск в зону обработки инструмента для реализации формообразования поверхностей проточной части и финишных отделочно-упрочняющих операций, что в случае нештатного ужесточения условий эксплуатации не гарантирует заданного ресурса работы. Это потребовало разработки принципиально новых подходов к технологии обеспечения заданных показателей качества рабочих поверхностей деталей проточной части [1]. Обеспечение необходимых показателей качества открытых поверхностей деталей технических трудностей на представляет. В нашем случае под качеством отделочно-упрочняющей обработки лопаточных деталей подразумевается качество обработки закрытых поверхностей - межлопаточных каналов, определяющее эксплуатационные характеристики таких деталей.
Управляемые факторы характеризуют принципиальную возможность активного влияния условий обработки на показатели ее качества, поэтому эти факторы являются не только управляемыми, но и управляющими по отношению к качеству отделочно-упрочняющей обработки поверхностей межлопаточных каналов деталей.
Для обработки проточных поверхностей лопаточных деталей «закрытой конструкции» предлагается виброэкструзионная обработка. Сущность данной технологии заключается в периодическом возвратно-поступательном продвижении (экструдировании) гранулированной рабочей среды через межлопаточные каналы детали при низкочастотных вибрациях [2]. Разработка опытного оборудования для вибрационной комбинированной отделочно-упрочняющей
233
обработки лопаток колес турбин проводилась по схеме виброэкструдирования гранулированной обрабатывающей среды по межлопаточным каналам (рис.).
Для реализации процесса виброэкструзионной комбинированной обработки контейнеру с лопаточной деталью и рабочей средой от рамы вибростенда сообщается колебательное движение в вертикальной плоскости (показано на рис. 1 прямыми сплошными стрелками). Также путем поворотов корпуса 6 осуществляются периодические повороты контейнера на 180° вокруг горизонтальной оси подшипниковых опор 2 (знакопеременные повороты показаны на схеме овальными пунктирными стрелками).
Однако результаты внедрения показали, что данный способ не позволяет достичь равномерности наклепа и стабильно повышать качество поверхности в узких (менее 5 мм) криволинейных каналах с углом раскрытия канала менее 45
[1].
Для решения этой задачи разработана комбинированная технология, где наряду с пластическим деформированием от действия магнитных импульсов применяется локальное анодное растворение [3]. Основными показателями качества комбинированной обработки непрофилированным инструментом, которые определяют эксплуатационные свойства лопаточных деталей, являются следующие характеристики обработанных поверхностей: снижение шероховатости; степень наклепа (относительное повышение микротвердости); глубина наклепа поверхностного слоя; глубина трещиноватого слоя; величина поверхностных остаточных напряжений сжатия; степень равномерности распределения указанных показателей по обработанным поверхностям.
Комплексное влияние достигнутых показателей качества на наиболее важные эксплуатационные показатели, такие как КПД, определяется гидравлической расходной проливкой или продувкой, а ресурс работы поверхности лопатки (количество циклов до разрушения), выявляется при разгонных испытаниях турбин до разрушения. Ряд деталей нагруженных насосных агрегатов имеет тонкие литые кромки лопаток с радиусом скругления до 0,8 мм, которые не выдерживают виброударных или магнитоимпульсных воздействий гранул размерами до 2-3 мм [1]. Газожидкостная слабопроводящая среда состояла из воздуха и распыленной до капельной фракции технической воды, являющейся слабым проводником (напряжение 6–10 В). Токопроводящая рабочая жидкость
– техническая вода распыливается через форсунку в направлении подачи шариков под давлением на входе 0,2 МПа. В качестве микрошариков использовались сферические гранулы из закаленной стали ШХ-15, имеющих твердость HRC 6062 ед. и гладкую поверхность Ra не более 0,4 мкм. Достижимое изменение шероховатости в этом случае Rz max зависит от скорости анодного растворения в месте микровыступа, которая в момент контакта шарика с деталью резко увеличивается из-за повышения удельной проводимости в месте соударения в 2–3 раза в зависимости от свойств материала детали. После обработки всей поверхности в течение 60 минут ее шероховатость составила 2,5–3,2 мкм, наклеп поверхностного слоя – 5,8÷7,45%, что отвечает заданным техническим условиям.
234
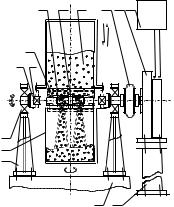
При опытном апробировании новых спроектированных процессов получены обнадеживающие результаты: после струйно-динамической и виброэструзионной комбинированных обработок шероховатость снижается на 1-2 класса от исходной, повышается микротвердость поверхностей лопаток на 20-30 %;
Промышленное внедрение вышеназванных процессов и опытных средств технологического оснащения для их реализации должно проводиться индивидуально для каждого вида изделий с наиболее полным удовлетворением заданных технических требований на изготовление и эксплуатацию.
|
7 |
8 |
9 |
10 |
11 |
12 |
|
6 |
|
|
|
|
|
4 |
5 |
|
|
|
|
|
3 |
|
|
|
|
|
|
2 |
|
|
|
|
|
|
1 |
|
|
|
|
|
|
14 13
Схема способа и установки для виброобработки каналов
сэкструдированием гранул под действием низкочастотной вибрации:
1стойка, 2 контейнер, 3 подшипник, 4 корпус, 5 подшипник, 6 приспособление для закрепления детали, 7 деталь обрабатываемая,
8заглушка, 9 среда рабочая гранулированная, 10 муфта упругая,
11 привод поворота контейнера, 12 – пульт управления, 13 постамент, 14 платформа вибростенда
Литература
1.Сухочев Г.А. Управление качеством изделий, работающих в экстремальных условиях при нестационарных воздействиях. – Воронеж.: ВГУ, 2003, 287 с.
2.Патент № RU 2173627 С2, МПК 7 В 24 В 31/06. Способ вибрационной обработки. Г.А. Сухочев, А.В. Бондарь, А.В. Левченко. Открытия. изобретения. – 2001. – № 26.
3.Патент № RU 2333822, МПК6 В 23Н 5/00. Способ комбинированной магнитоимпульсной обработки деталей лопаточных машин и устройство для его осуществления. Смоленцев В.П., Гореликов В.Н., Гренькова А.М., Сухочева Е.Г., Болдырев А.И. Опубл. 20.09.2008. Бюл. № 26.
4.Небольсин Д.М. Исследование режимов комбинированной обработки внутренних поверхностей / Д.М. Небольсин, Г.А. Сухочев, С.Н. Коденцев // Вестник Воронежского государственного технического университета. – 2011. – Т.7. – № 4.– С.44–47.
235
УДК 621.396.6.001.63;621.396.001.66
Повышение эффективности методик тестирования электронных средств на устойчивость к электростатическому разряду
Д.С. Сеимова1, М.А. Ромащенко2 1Студент гр. бРК-31, dashyli98@mail.ru
2Д-р тех. наук, профессор, kipr@vorstu.ru
ФГБОУ ВО «Воронежский государственный технический университет»
Объектом исследований являются процессы воздействия электростатических разрядов на конструкции электронных средств, их элементную базу, а также методы повышения эффективности защиты от подобных нежелательных воздействий.
Ключевые слова: электромагнитная совместимость (ЭМС), электромагнитные помехи (ЭМП), электростатические разряды (ЭСР), электронное средство (ЭС).
Существующие методы испытаний и тестирований на устойчивость к влиянию электростатических разрядов (ЭСР) ограничиваются моделированием напряжений и токов разрядов при помощи специального генератора электростатических разрядов. При производстве надежного и устойчивого к ЭСР устройства проектировщики стремятся минимизировать электростатические связи за счет комбинации определенных факторов. Чувствительность к электростатическим разрядам тем выше, чем меньше толщина диэлектрика. С учетом модернизации конструкций электронных средств (ЭС) и ориентацией кремниевых технологий на более низкие напряжения и потребностью конструирования оптимальных компонентов со сверхмалой потребляемой мощностью приводит разработчиков печатных плат к наибольшему интересу данной тематике.
В настоящее время уделяется недостаточно внимания методике, позволяющей оптимально и эффективно проектировать ЭС с учетом устойчивости к ЭСР из-за отсутствия требований в техническом задании (ТЗ) или же из-за неясности причин возникновения электромагнитных помех (ЭМП). Разработка конкурентоспособного программно-аппаратного комплекса для оценки влияния электростатического разряда на электронные средства является безусловно актуальной.
Эквивалентная модель с сосредоточенными параметрами в частотной области предлагаемого ЭСР-тестера представлена на рис. 1. Она содержит три основных компонента: компоненты разрядки пистолета (RGun, Cprs и CGun), сопротивление заземления (CG, LG и RG) и целевую нагрузку калибровки (RLoad) вместе с индуктивностью наконечника электрода (LTip).
236
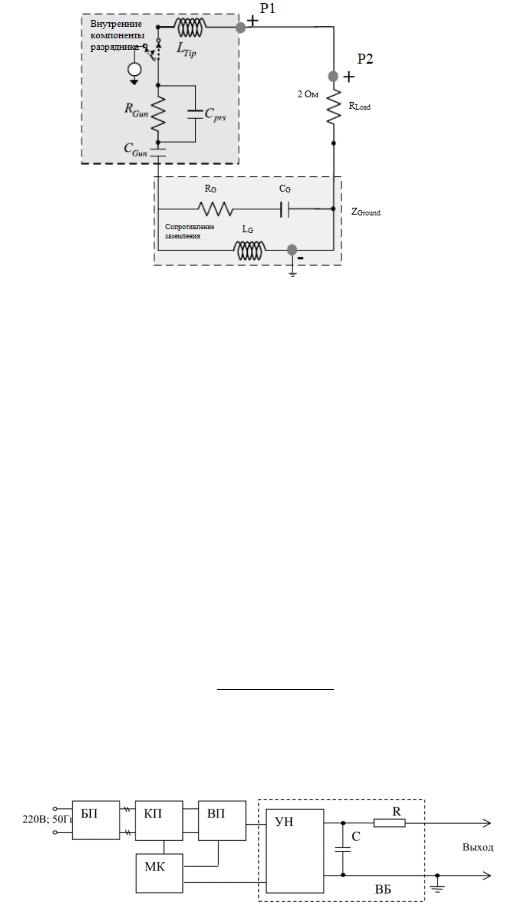
Рис. 1. Эквивалентная схема предлагаемого оборудования
Предлагаемая модель цепи имеет преимущества, позволяющие эффективно анализировать влияние разряда на внутренние компоненты (RGun, Cprs и CGun) и результаты импеданса. Входной импеданс имеет низкочастотные емкостные характеристики с наличием внутренних компонентов (RGun, Cprs и CGun). Удаление внутренних компонентов делает входной импеданс индуктивным при низкой частоте.
Резонансная частота и соответствующие значения импеданса со стороны инжекции ЭСР (т.е. ZGround) получены из экспериментальных данных S- параметра. Индуктивность LG может быть рассчитана с использованием аналитического подхода парциальной индуктивности. Затем можно рассчитать сосредоточенное значение CG, используя формулу резонансной частоты. Последний компонент RG определяется с помощью передаточной функции. Значение паразитной емкости (Cprs) и индуктивности наконечника (LTip) оптимизируются для получения точной формы напряжения электростатического разряда.
| |
На рис. 2 показана структурная схема, используемая для разработки генератора.
Рис. 2. Структурная схема предлагаемого генератора ЭСР
237
Блок питания (БП) генерирует напряжение 12В, затрачиваемое для зарядки аккумулятора. Высоковольтный преобразователь (ВП) совместно с умножителем напряжения (УН) генерирует напряжение от 2 до 25 кВ, затрачиваемое для зарядки накопительного конденсатора (C). Микропроцессорный контроллер (МК) адаптирован для управления ЖКдисплеем, контроллером питания (КП) и высоковольтным преобразователем (ВП). (КП) регулирует зарядку аккумулятора и обеспечивает требуемое напряжение для остальных блоков генератора ЭСР. Сменный высоковольтный блок (ВБ) состоит из умножителя напряжения (УН), накопительного конденсатора (С) и разрядного резистора
(R).
В настоящее время предложена сравнительно простая и эффективная схема генератора ЭСР. Формы сигналов ЭСР, создаваемые разработанными моделями, хорошо согласуются со стандартами спецификаций IEC. Предложенная схема может быть использована в качестве надежного источника возбуждения ЭСР и построения на ее основе перспективного автоматизированного тестера-ЭСР. Разработана концептуальная структура программно-аппаратного комплекса для оценки влияния электростатического разряда на электронные средства.
Литература
1.Кечиев Л.Н., Пожидаев Е.Д. Защита электронных средств от воздействия статического электричества / - Москва: Изд. дом «Технологии», 2005.
2.Gauthier J. Li, R., Joshi A., Lundberg M., Connor J., Chang S., Mitra S., Muhammad M., Predictive full circuit ESD simulation and analysis using extended ESD compact models: methodology and tool implementation / Proc. EOS/ESD Symp. – 2010 – Р. 25.
238
УДК 338.2
Позиции России на международном рынке науки и технологий
Е.А. Головина1, О.М. Белянцева2
1 Студент гр. Б821, golovinaekaterina99@gmail.com
2 Канд. экон. наук, доцент, darabel02@mail.ru
ФГБОУ ВО «Воронежский государственный технический университет»
Проанализированы место и роль России на международном рынке научных ресурсов. Выявлены связанные с этим проблемы инновационного развития страны. Предложены меры по укреплению позиций РФ на мировом рынке науки и технологий.
Ключевые слова: научные ресурсы мира, международный рынок технологий, научный рейтинг страны, инновационная модель экономики.
Вэпоху бурного международного научно-технического развития существенно возросла роль технологий как фактора экономического роста.
Правильный выбор приоритетов развития науки и техники, создание и поддержание эффективного функционирования национальной инновационной системы позволяет обеспечить устойчивое развитие и необходимые темпы экономического роста страны [1].
Россия входит в число лидеров по ряду важнейших направлений исследований и разработок, в том числе в таких областях, как нанотехнологии, живые системы, охрана окружающей среды, атомная и водородная энергетика, энергосберегающие системы, прикладные программные средства и др.
Однако в настоящее время реальных предпосылок для позиционирования отечественной экономики как инновационно-ориентированной крайне мало.
Вэкономике сформировался значительный разрыв между созданием технологий в сфере НИОКР и их использованием в массовом производстве. Ситуация усугубляется тем, что материально-техническая база российской науки и испытательных центров значительно устарела [3].
По данным за 2018 год, Россия занимает 10-е место в мире по абсолютному уровню затрат (в пересчете по паритету покупательной способности) на научно-исследовательские и опытно-конструкторские разработки (НИОКР). По этому показателю, нас значительно опережают такие признанные мировые лидеры, как США и Китай, а также Япония и Южная Корея. В целом, российские затраты на НИОКР находятся примерно на уровне европейских стран: выше уровня Италии, но ниже Германии, Франции, сопоставимы с Великобританией (рис. 1) По соотношению затрат на науку в валовом внутреннем продукте (ВВП) Россия с показателем 1,1% отстает от ведущих стран мира и находится на 34-м месте, а по величине затрат на исследования и разработки в расчете на одного исследователя Россия занимает 47-е место – 93 тыс. долл. в год[4].
239