
Методическое пособие 805
.pdf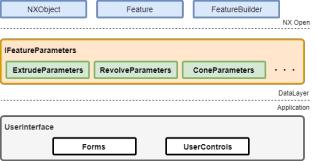
ответствует конкретным потребностям, не беспокоясь о недостающей функциональности.
Инструмент «Журнал» – это механизм быстрой автоматизации, который записывает, редактирует и воспроизводит сеансы пользователя в NX. Утилита генерирует файл, содержащий действия пользователя в виде кода на одном из доступных языков программирования [2]. Например, в NX 7.5 доступны сле-
дующие языки: Visual Basic .NET, C++, C#, Java.
Файл журнала имеет несколько применений. Во-первых, файл журнала можно воспроизвести в любой момент для повторения записанных действий пользователя. Во-вторых, записанный сеанс может быть расширен с помощью компонентов пользовательского интерфейса для создания настраиваемой программы. В-третьих, сгенерированный код можно использовать в любом другом более крупном приложении.
Block Styler – это интерактивный конструктор визуальных пользовательских интерфейсов, который позволяет создавать диалоговые окна в стиле NX [1]. Инструмент расширяет возможности устаревшего UI Styler, но в тоже время использует тот же набор блоков, которые используются во внутренних приложениях NX. Кроме того, инструмент предоставляет независимые от платформы блоки, что гарантирует одинаковую работу диалогового окна во всех приложениях и на всех платформах.
Набор блоков, используемых в конструкторе, схож со стандартными элементами управления в операционных системах. Пользователь может использовать поля ввода, выпадающие списки, флажки, радиокнопки, таблицы и т.д.
Принцип работы приложения заключается в том, что для начала работы пользователь выбирает объект, редактирование параметров которого будет производиться. На этом этапе приложение обращается к NX Open API. Следующий этап – работа с объектом. Пользователю предоставляется возможность изменить параметры, характеристики и атрибуты выбранного объекта. Все действия производятся на уровне приложения. Для сохранения внесенных изменений приложение вновь обращается к NX Open API. После применения изменений объект редактирования моментально перерисовывается в окне NX.
Архитектура приложения представлена на рисунке.
Приложение состоит из трех выделяемых слоев.
220
Первый слой – NX Open – служит для получения экземпляра редактируемого объекта или тела, а также для применения изменений, внесенных пользователем. Объект невозможно получить без обращения к NX Open API.
Второй слой – DataLayer. Этот слой является промежуточным и содержит основную логику приложения. Интерфейс IFeaturePatameters определяет набор специальных методов и свойств:
–информация о типе объекта;
–информация о идентификаторе в журнале NX;
–анализ выбранного пользователем объекта;
–применение изменений, внесенных пользователем и др.
Классы Parameters, реализующие интерфейс IFeaturePatameters, содержат информацию о соответствующих объектах. Так, например, класс ExtrudeParameters может содержать следующие свойства:
–строку, содержащую тип объекта Extrude (инструмент «Вытягивание»);
–строку, содержащую идентификатор объекта в журнале NX;
–набор свойств, отвечающих за параметры и ограничения выдавливания;
–угол уклона и смещения выдавливания;
–допуски и др.
Слой DataLayer спроектирован таким образом, что никак не взаимодействует напрямую ни с NX Open API, ни с интерфейсом приложения. Благодаря такой архитектуре достигается возможность добавления поддержки работы с любыми объектами без перепроектирования пользовательского интерфейса.
Третий слой – Application. Данный слой представляет собой интерфейс пользователя. Элементы управления окна приложения динамически формируются в зависимости от объекта, с которым работает пользователь.
Литература
1.Краснов, М. Unigraphics для профессионалов / М. Краснов, Ю. Чигишев
–Москва: «Лори», 2004.
2.Beginning Journaling using NX Journal | NX Journaling – Электрон. дан. – Режим доступа: http://nxjournaling.com/content/beginning-journaling-using-nx- journal
221
УДК 62-231
Повышение грузоподъёмности винтового телескопического домкрата
А.В. Бакуменко1, Ю.С. Ткаченко2 1Аспирант, bakumenko1992@list.ru
2Д-р тех. наук, профессор, misterba422@qip.ru
ФГБОУ ВО «Воронежский государственный технический университет»
Вданной работе рассмотрена возможность повышения грузоподъёмности винтового телескопического домкрата за счет нанесения покрытия.
Ключевые слова: винтовой телескопический домкрат, расчет, грузоподъемность, покрытие.
Впроцессе изготовления, ремонта и технического обслуживания в различных отраслях применяются как винтовые, так и гидравлические домкраты. Винтовые наиболее распространены в виду способности без дополнительной страховки удерживать допустимые нагрузки.
Домкраты с винтовой парой разделяются на несколько видов, в зависимости от точности, надежности и износостойкости. Наиболее распространены домкраты с трапециевидной резьбой, в виду реализации самоторможения винтовой пары.
Основной целью разработки новых конструкций и схем домкратов явля-
ется:
-повышение надежности;
-повышение нагрузочной способности;
-повышение КПД;
-уменьшение времени на подготовку работы;
-применение новых материалов более легких, прочных, износостойких. При проектировании домкратов, а так же их эксплуатации определяющи-
ми факторами является:
-высота подхвата;
-высота подъёма;
-грузоподъёмность;
-масса;
-габариты.
На сегодняшний день широкое распространение получили телескопические домкраты, их преимущество главным образом заключается в подъёме на высоту равной двум, в редких случаях трем высотам подхвата. Данные виды домкратов имеют две или три винтовые пары, а так же редуктор с электрическим приводом [1].
На рисунке представлена запатентованная конструкция винтового телескопического домкрата.
222
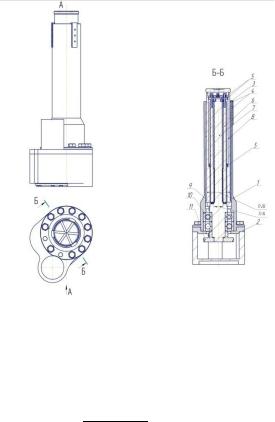
Винт 7 с винтом-гайкой 6 образуют первую винтовую пару, вторую винтовую пару образует винт-гайка 6 с гайкой 8. На верхней части винта 7 установлен механизм переключения передачи крутящего момента с винта 7 на винт гайку 8, что и является отличительной особенностью существующих аналогов. Применение муфты позволило избежать возникновения повышения нагрузки на привод во время переключения между винтом 7 и винтом-гайкой 6 [2].
Ограничение по грузоподъёмности определяется винтом 7. Входе разработки данной конструкции было выявлено, что грузоподъёмность домкрата занижается в 2,5 раза из-за контактных напряжений. Контактные напряжения задают ограничения по грузоподъёмности, с целью обеспечения ресурса.
Домкрат винтовой телескопический
Для большей подтверждения данного факта, был проведен ряд расчетов. Так как же связанна грузоподъемность и контактные напряжения. Формула 1 позволяет рассчитать минимальный диаметр винта d1.
√ |
|
. |
(1) |
[ ] |
Из формулы 1, видно что определяющими величинами является осевое усилие Q и [ ] нормальное напряжение. Нормальное напряжение зависит от осевой нагрузки и площади сечения, определяется уравнением 2.
[ |
] |
|
(2) |
|
Второй не менее важной величиной действующей на вал является касательное напряжение , определяемое уравнением 3, в сумме напряжения со-
ставляют приведенное напряжение |
определяемое уравнением 4. |
|
||||
|
|
|
|
. |
|
(3) |
|
|
|
|
|||
|
|
|
|
|
|
|
|
√ |
. |
(4) |
|||
|
223 |
|
|
|
Данные напряжения, позволяют охарактеризовать прочность винта, а износостойкость определяется удельным давлением q, которое определяется формулой 5.
|
|
|
. |
(5) |
|
|
|||
Для примера выбираем винтовую пару Tr36×3, произведя расчет, полу- |
||||
чаем следующие значения [3]: |
|
|
|
|
- внутренний диаметр винта |
= 19,68 (мм); |
|
||
- нормальное напряжение [ |
] = 10,93 (МПа); |
|
||
- касательное напряжение |
= 5,9 (МПа); |
|
||
- приведенное напряжение |
= 16,084 (МПа); |
|
||
- удельное давление q = 12,91 (МПа). |
|
|||
Для винта из стали 35 статически допустимое |
напряжение |
(МПа). Исходя из этого, явно выявлено, винт имеет почти пяти кратный запас прочности (4,97).
Исходя из этого для повышения грузоподъёмности с 2,4 тонны до 6,5 тонн. Необходимо повысить износостойкость винта, при этом с повышением нагрузки возрастает как = 38,91 (МПа), так и q = 34,97 (МПа). Вследствие чего, запас прочности снижается до 2.
В результате получаем при исходных габаритах винтовых пар, домкрат грузоподъёмностью в 6,5 тонн.
Но достигнуть данные результат возможно, лишь нанося износостойкое покрытие на винтовые поверхности деталей домкрата, гальваническим способом или плазменным напылением [4]. Так как полученное покрытие будет обладать высокой износостойкостью и твердостью возникает необходимость финишной обработки алмазной шлифовкой, альтернативой которой является поверхностное лазерное выглаживание.
Литература
1.Тихонов А. С., Щёголев С. Н. Использование современных винтовых механизмов в домкратах // Молодой ученый. – 2013. – №3. – С. 105-108.
2.Патент на изобретение №2652364.
3.В.И. Анурьев Справочник конструктора машиностроителя: в 3-х т.: Т. 2. – 8-е изд., перераб. и доп. Под ред. И.Н. Жестковой. – Москва: Машиностроение, 2011. – 912 с.:ил. – С. 777-780.
4.Бакуменко А.В., Ткаченко Ю.С. Перспективные технологии по-
вышения качества поверхности деталей машин/ Бакуменко А.В., Ткаченко Ю.С.//Авиакосмические технологии. Труды XVIII Международной научнотехнической конференции и школы молодых ученых, аспирантов и студентов. –
2017. – С. 191-194.
224
УДК 621.793.74
Повышение износостойкости деталей машин с помощью плазменного напыления
Г.И. Трифонов1, А.В. Бирюков2, С.Ю. Жачкин3, Н.А. Пеньков4 1Младший научный сотрудник ВУНЦ ВВС «ВВА», trifonov_gi@mail.ru 2Аспирант кафедры АОМП , grishakip@yandex.ru
3Д-р. техн. наук, профессор, zhach@list.ru
4Канд. техн. наук, myth_np_nikit@mail.ru
ФГБОУ ВО «Воронежский государственный технический университет»
В данной статье рассмотрены известные методы упрочнения поверхности деталей машин. Проанализирован процесс плазменного напыления, а также разработаны программные продукты для автоматизации необходимых расчетов при планировании применения технологий напыления.
Ключевые слова: плазменное напыление, износостойкость, программный продукт.
Введение. На сегодняшний день процессы изнашивания сложны и включают в себя механические, физические и химические воздействия. Несмотря на весьма длительное изучение процессов изнашивания к настоящему времени ещё не созданы универсальные методы борьбы с ним, а также отсутствуют общепринятые критерии износостойкости.
Износостойкость – это одно из самых важных свойств деталей машин, режущего инструмента и механизмов, определяющее их работоспособность [1]. Износостойкость зависит не только от износостойкости материалов, но и от их конструкции деталей и их условий эксплуатации.
Все известные методы упрочнения подразделяются на шесть основных классов [2]:
1.Упрочнение с образованием пленки на поверхности;
2.С изменением химического состава поверхностного слоя;
3.С изменением структуры поверхностного слоя;
4.С изменением энергетического запаса поверхностного слоя;
5.С изменением микрогеометрии поверхности и наклепом;
6.С изменением структуры по всему объему материала.
Внастоящее время известен широкий спектр способов и методик по повышению износостойкости. Подробный анализ того или иного способа или метода в одной научной статье не возможен, поэтому было решено ограничиться сведениями и описать лишь некоторые способы по повышению износостойкости деталей.
Общий анализ по методам повышения износостойкости деталей:
1.Наклёп (дробеструйная обработка).
225
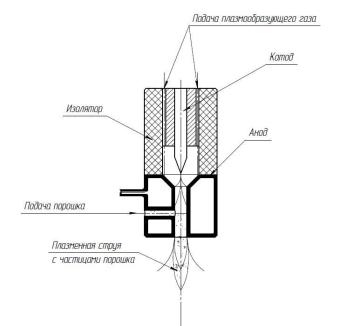
2.Поверхностная термообработка (поверхностная закалка и последующая обработка дробью, лазерная и электронно-лучевая обработка, закалка ТВЧ).
3.ХТО (цементация, закалка, ионно-плазменное азотирование).
4.Диффузионная металлизация (хромирование).
5.ППД (накатывание, обкатывание).
6.Физикотермическая обработка (электротермическая обработка).
7.Напыление износостойких соединений (высокотемпературное напыление на поверхности самофлюсующихся сплавов с последующим их оплавлением).
После сравнительного анализа по экономическим и функциональным аспектам вопроса по повышению износостойкости деталей, а также выдвигаемым требованиям различных производств был сделан вывод, что на сегодняшний день перспективным направлением по созданию надежных, долговечных и износостойких покрытий является плазменное напыление [3].
Технология плазменного напыления является экономичной, универсальной и перспективной для создания и нанесения разнообразных высококачественных покрытий.
Основная часть. Процесс плазменного напыления представлен на рисунке. Между катодом и медным водоохлаждаемым соплом, которое служит анодом, возникает дуга, которая нагревает поступающий в сопло горелки рабочий газ, истекающий из сопла в виде плазменной струи. Поток плазмы характеризуется следующими показателями: температура в ядре от 20 000 до 30000 К, скорость струи 300 ... 2000 м/с [4].
Схема плазменного напыления
226
В струю от специального питателя подается многокомпонентный порошок, который ускоряется, расплавляется и оседает на поверхности детали, образуя покрытие. Как показывает практика [5], наиболее распространенная схема подачи распыляемого материала – перпендикулярно плазменной струе на срезе сопла. Но стоит учитывать, что детали имеют разнопрофильные рабочие поверхности, которые в той или иной степени подвергаются активному износу в ходе эксплуатации. Поэтому схема с вертикальной подачей напыляемого материала не всегда актуальна.
Качество износостойкого покрытия характеризуют следующие показатели: адгезия, когезионная прочность (прочность напыленного покрытия), пористость, равномерная толщина покрытия, шероховатость, твердость, а также уровень остаточных напряжений [6]. Результаты работ таких ученых, как Ильющенко А.Ф., Пузряков А.Ф., Тополянский П.А., Табаков В.П., позволили получить представление о влиянии различных факторов на параметры плазменного покрытия.
Результаты исследований. При планировании применения технологии плазменного напыления можно выделить специфические проблемы, характеризующие конкретную деталь и её функциональный слой. В частности, появляется необходимость моделирования математической модели кинематических режимов плазменного напыления для сложнопрофильной поверхности детали.
Следовательно, создание программного продукта для автоматизации разработанных математических моделей плазменного напыления является важной и краеугольной задачей.
ГОСТами на создание программных продуктов предусматриваются пять этапов их разработки: формулировка технического задания, разработка технических предложений по созданию программного продукта, разработка технического проекта, рабочее проектирование, испытание программного продукта.
Следуя данным этапом на базе ВУНЦ ВВС «ВВА имени Н.Е. Жуковского и Ю.А. Гарина» (г. Воронеж) и «Воронежского государственного технического университета» были разработаны и созданы расчетные программные продукты, которые благодаря своему функционалу помогают в обучении курсантам и в расчетах инженерам, которые по своей специальности связаны с машиностроением.
Первый программный продукт предназначен для расчета кинематических режимов плазменного напыления, таких как скорость вращения детали, число оборотов главного привода, контурная скорость распылителя, радиальная и продольная скорость перемещения распылителя, а также скорость движения напыляемых частиц в плазменной струе. Второй программный продукт направлен на расчет кинематических режимов плазменного напыления для винтовой поверхности детали, толщины плазменного покрытия и толщины удаляемого слоя, скорости и температуры частиц в плазменной струе (воздушной), расчет пористости методом гидростатического взвешивания, а также, основываясь на уравнениях геометрической составляющей винтовой поверхности, и на уравнениях, описывающих габаритные размеры сложнопрофильных деталей, прово-
227
дится расчет интенсивности изнашивания плазменного покрытия и величины абразивного износа плазменного покрытия винтовой поверхности детали.
Вывод. В ходе изучения процессов повышения износостойкости деталей машин, в частности плазменного напыления, были разработаны программные продукты, которые в перспективе помогут вывести автоматизацию технологических процессов напыления на новый уровень развития.
Литература
1.Трифонов Г.И. Плазменное напыление и другие способы повышения износостойкости деталей / Г.И. Трифонов // Инновационные технологии и оборудование машиностроительного комплекса. Межвуз. сб. науч. тр. Воронеж: ФГБОУ ВО «Воронежский государственный технический университет», 2016.
Вып. 19. С 60–69.
2.Ильющенко А.Ф. Процессы формирования газотермических покрытий
иих моделирование / А.Ф. Ильющенко, А.И. Шевцов, В.А. Оковитый, Г.Ф. Громыко // Минск: Беларус. навука, 2011. – 357 с.
3.Жачкин С.Ю. Плазменное напыление и его применение в области ремонта машин и оборудования / С.Ю. Жачкин, Г.И. Трифонов, А.С. Богачёв // Инновационные технологии и оборудование машиностроительного комплекса. Межвузовский сборник научных трудов. / Воронеж: ФГБОУ ВПО «Воронежский государственный технический университет», Вып. 19, 2018. С.76 –80.
4.Пузряков А.Ф. Теоретические основы технологии плазменного напыления // Учеб. Пособие по курсу «Технология конструкций из металлокомпозитов». 2-е изд., перераб. и доп. – М.: Изд-во МГТУ им. Н.Е. Баумана, 2008. – 360 с.
5.Жачкин С.Ю. Моделирование кинематики плазменного напыления на сложнопрофильные поверхности / С.Ю. Жачкин, Г.И. Трифонов, М.Н. Краснова, Н.А. Пеньков // Труды ГОСНИТИ. – 2017. – Т. 128. С.133–139.
6.Жачкин С.Ю. Факторы, определяющие прочностные свойства плазменного напыления / С.Ю. Жачкин, Г.И. Трифонов // Повышение эффективности использования мобильных энергетических средств в различных режимах движения: материалы международной научно-практической конференции, посвященной 115 годовщине со дня рождения профессора Харитончика Ефима Мироновича (Россия, Воронеж, 6 апреля 2017 г.). – Воронеж: ФГБОУ ВО Воронежский ГАУ, 2017.
С.186–191.
228
УДК 621.234.123
Повышение работоспособности высокооборотных роторов в местах доводки комбинированными методами
В.Н. Сокольников1, Г.А. Сухочев2, А.В. Норман3 1Аспирант 4 курса кафедры «Технология машиностроения», sokolnikovv@inbox.ru
2Д-р техн. наук, проф., suhotchev@mail.ru
3Канд. техн. наук ФГБОУ ВО «Воронежский государственный технический университет»
Исследованы причины возникновения поверхностных дефектов в процессе эксплуатации лопаточных деталей. Разработан комбинированный метод устранения наследственных дефектов поверхностного слоя после проведения балансировки роторов.
Ключевые слова: комбинированный метод, упрочнение микрошариками, балансировка, поверхностный слой металла.
Высокие нагрузки: статические и динамические; воспринимаемые в процессе работы на высоких оборотах авиационно-космической техники влияют, в первую очередь, на работоспособность колес турбин и крыльчаток турбонасосных агрегатов, как наиболее нестационарно нагружаемых составляющих ротора. Сложная силовая схема знакопеременных нагрузок, воздействующих на лопатку, способствуют тому, что некоторые элементы конструкции работают в области упругопластических деформаций. Требуемая долговечность лопатки при обеспечении циклической усталостной прочности при высоком уровне напряженности элементов конструкции достигается устранением остаточного дисбаланса, наследованного от предыдущих этапов изготовления ротора.
Все лопаточные детали таких роторов подвергают в процессе изготовления отделочно-упрочняющей обработке, повышающей ресурс рабочих поверхностей. Однако, снятие металла при балансировке в локальных зонах приводит к снижению твердости на предварительно упрочненных поверхностях и неуправляемому перераспределению остаточных напряжений в поверхностном слое материала и смене их направления. Следы механической обработки на поверхности становятся нежелательными концентраторами растягивающих напряжений, особенно в местах наибольшего снятия металла в зонах, прилегающих к галтелям у «корня» лопатки.
Негативное влияние на свойства поверхностного слоя и усталостную прочность лопаточной детали оказывают механическая зачистка фрезами и обработка абразивом по принципу получения минимальной шероховатости в этих местах. Неорганизованное ручное снятие излишков материала образует в тонких приповерхностных слоях структурную неоднородность, приводит к шаржированию, образованию остаточных напряжений растяжения, возраста-
229