
Методическое пособие 660
.pdfсти оборудования, так как протяжка металла проходит в условиях жестких нагрузок (изгибы, растяжение и сжатие металла). Прежде, чем использовать станок, металл обрабатывают, развертывают, сверлят, создавая максимально точные заготовки.
Станок протяжной используется для выполнения следующих операций:
-калибровка отверстия (фигурного, многогранного, цилиндрического и пр.);
-коррекция наружного профиля сложной конструкции;
-нарезка канавки шпоночной и шлица;
-обработка посадочной поверхности лопатки для турбины авиационного двигателя;
-обработка и корректировка отверстия для огнестрельного оружия нарезного типа (ствол пушки, пулемета, пистолетный ствол);
В мелкомасштабном производстве оборудование используется для создания отверстий в шестеренках и втулках, шпоночных и шлицевых канавок. Основными характеристиками протяжных станков являются:
-тяговая сила (максимальный показатель - 1 Мн);
-скорость протягивания (от 1,5 до 15 м/мин., в зависимости от назначения станка);
-длина хода каретки (максимальный показатель — 2 метра);
-конструкция привода (гидравлическая или электромеханическая);
-точность работы (от 1 до 10 класса).
Тяговая сила станка зависит от каретки. Для станков общего назначения характерна скорость протягивания от 15 до 20 м/мин. и привод, основанный на гидравлике, а для станков непрерывного действия скорость протягивания от 1,5 до 15 м/мин. и электромеханический привод.
60
В массовом производстве используются станки 1-2 класса, не допускающие погрешностей.
Их точность достаточно высока. Но следует иметь ввиду то, что станок протяжной 3-10 класса может оставлять на отшлифованных поверхностях мелкие шероховатости или неровности.
4.2. Перспективы развития и совершенствования оборудования машиностроительных производств
Стихийный переход к рынку в конце прошлого века, безусловно, положительно повлиял на развитие добывающих отраслей – как наиболее доходных, но пагубно сказался на обрабатывающих отраслях промышленности. В первую очередь – машиностроительной.
Нынешняя доля машиностроения в общем объёме промышленного производства РФ составляет около 20 %, уступая по меньшей степени в 2 раза показателям промышленно развитых стран. А по подавляющему большинству позиций в мировом экспорте машин, оборудования и транспортных средств вклад страны составляет десятые и сотые доли процента (относительное исключение представляет энергетическое оборудование – около 2,5 процентов).
Среди главных проблем отечественного машинострое-
ния:
-Наличие избыточных производственных мощностей, как правило, устаревших, и, соответственно, крайне высокие издержки на их содержание;
-Морально устаревшая инфраструктура производственных мощностей;
-Критический моральный и физический износ оборудования и технологий;
61
-Дефицит денежных ресурсов (низкая кредитная и инвестиционная привлекательность предприятий) для реализации программ стратегических преобразований;
-Неэффективная производственная кооперация промышленных предприятий;
-Дефицит квалифицированных кадров.
Всвоем сегодняшнем состоянии предприятия российского машиностроения могут осуществлять производство высокотехнологичной конкурентоспособной продукции только для сравнительно узких сегментов мирового рынка.
Современное состояние отрасли не отвечает целям и задачам повышения долгосрочной конкурентоспособности экономики и занятия устойчивых рыночных ниш на мировых рынках наукоемкой продукции.
Одним из путей выхода из такой ситуации может являться модернизация имеющегося технологического оборудования.
Модернизация или замена технологического оборудования на машиностроительных предприятиях прежде всего осуществляется с целями сокращения времени изготовления деталей, экономии затрат на сырье и электроэнергию, высвобождения персонала и производственных площадей.
Внастоящее время модернизацию станочного парка проводят по следующим направлениям:
Станки токарной группы. У станков этой группы в необходимых случаях устанавливают механизмы ускоренных продольных перемещений суппорта при холостых ходах и применяют устройства для автоматического выключения продольных подач. При использовании станка в течение продолжительного времени для обработки конусов автоматизируют подачу верхних поворотных салазок суппорта путем связи ходового вала с винтом подачи кинематической цепью, состоящей из зубчатых колес, промежуточного кронштейна и телескопического вала с шарнирами Гука по
62
концам. В необходимых случаях для автоматизации подачи пиноли задней бабки устанавливают гидропневматические устройства.
Фрезерные станки. У продольно-фрезерных станков с установкой фрезерных головок вручную механизируют перемещения, связанные с ее установкой; вводят механизм ускоренного перемещения стола; механизируют и автоматизируют подачу деталей к станку, их установку, закрепление и измерение в процессе отработки; применяют многопозиционные приспособления для непрерывного фрезерования; механизируют процесс удаления стружки со стола станка и т.п. Так же как и на токарных станках, применяют гидравлические копировальные устройства.
Сверлильные станки. Ступенчатошкивный привод заменяют редуктором и вводят кнопочное управление электродвигателем («Вперед», «Стоп», «Назад»).
Шлифовальные станки. У станков этого типа создают механизмы ускоренного подвода и отвода шлифовального круга или обрабатываемой детали. При патронной работе на круглошлифовальных станках вспомогательное время сокращают внедрением устройства торможения шпинделя передней бабки.
Строгальные станки. У поперечно-строгальных станков автоматизируют подачу суппорта. У крупных продоль- но-строгальных станков создают ускоренные перемещения суппортов, иногда механизируют установочные перемещения траверсы.
Но следует учитывать, что замена оборудования на более производительное сама по себе не даст ощутимых эффектов, так как время изготовления отдельных деталей составляет незначительную долю в производственном цикле. Для достижения ощутимых эффектов модернизация должна сопровождаться внедрением современных принципов и подходов в организации и управлении производством.
63
Еще одним возможным путем модернизации является оснащение имеющегося станочного парка системами числового программного управления (ЧПУ).
Числовое программное управление (сокр. ЧПУ;
англ. computer numerical control, сокр. CNC) — компьютери-
зованнаясистема управления, управляющая приводами технологического оборудования, включая станочную оснастку.
Оборудование с ЧПУ может быть представлено:
станочным парком, например, станками (станки, оборудованные числовым программным управлением, называются станками с ЧПУ) для обработки металлов (например, фрезерные или токарные), дерева, пластмасс;
приводами асинхронных электродвигателей, использующих векторное управление;
характерной системой управления современными промышленными роботами;
периферийные устройства, например: 3Dпринтер, 3D-сканер.
Вопросы для самоподготовки
1.Какое металлообрабатывающее оборудование используется на заготовительных участках машиностроительных предприятий?
2.Какое металлообрабатывающее оборудование используется на механообрабатывающем производстве на машиностроительных предприятиях?
3.Что такое металлообрабатывающий станок?
4.Что такое числовое программное управление?
5.Какие существуют перспектива развития металлообрабатывающего оборудования?
64
ЛЕКЦИЯ № 5
ИНСТРУМЕНТАЛЬНОЕ ОБЕСПЕЧЕНИЕ МЕХАНИЧЕСКОЙ ОБРАБОТКИ
Теоретическиевопросы
5.1.Методы получения поверхностей резанием
5.2.Конструктивные элементы режущего инструмента
5.3.Процесс образования стружки
5.1.Методы получения поверхностей резанием
Подавляющее большинство деталей машин приобретают окончательную форму и размеры только после механической обработки резанием.
Заготовка отличается от детали тем, что в тex местах детали, где при получении ее литьем, обработкой давлением, сваркой невозможно обеспечить необходимую точность размеров и качество поверхности специально оставляется слой металла называемый припуском.
Процесс снятия припуска режущим инструментом с целью получения деталей заданной формы, размеров и точности называется резанием. Металл, удаляемый в процессе резания с заготовки, подвергается пластическому деформированию и разрушению. В результате этого материал припуска, отделенный от обрабатываемой заготовки, приобретает характерную форму и называется стружкой.
Обработка конструкционных материалов резанием на металлорежущих станках - весьма распространенный производственный процесс. На большинстве машиностроительных предприятий трудоемкость обработки резанием составляет 45 — 60 % от общей трудоемкости изготовления машин. В связи с этим актуальнейшей народнохозяйствен-
65
ной задачей являются: с одной стороны уменьшение объема обработки резанием, с другой — совершенствование технологии резания металлов.
Методы формообразования поверхностей деталей машин
В элементарной геометрии поверхность определяется как граница тела. Рассматривая границу тела различных деталей машин можно видеть, что она состоит, как правило, из отдельных участков, представляющих собой геометрически правильные поверхности.
Имеется ряд классификаций поверхностей:
1)поверхности вращения;
2)плоскости;
3)контурно-сложные линейчатые поверхности;
4)винтовые поверхности;
5)пространственно-сложные поверхности.
Ряд геометрических поверхностей может быть получен как след движения образующей линии по направляющей линии. К числу таких поверхностей относятся поверхности, входящие в первые четыре группы.
1)Поверхности вращения могут быть получены пе-
ремещением образующей линии той или иной формы, расположенной в осевой плоскости, по круговой линии, которая является направляющей.
2)Контурно-сложная линейчатая поверхность
может быть получена при перемещении образующей линии, остающейся параллельной своему начальному положению, вдоль направляющей прямой линии.
Если образующая имеет форму прямой, то при ее перемещении образуется плоскость. Кроме того, контурносложная линейчатая поверхность может быть получена при перемещении прямой линии (образующая) по линии имеющей ту или иную форму. При этом прямолинейная обра-
66
зующая должна быть перпендикулярной к плоскости, в которой расположена направляющая линия. Поверхности полученные таким образом называются цилиндрическими.
При обработке поверхностей на металлорежущих станках образующие и направляющие линии в большинстве случаев отсутствуют. Они воспроизводятся путем относительного перемещения инструмента и заготовки относительно друг друга.
Механическая обработка заготовок деталей машин реализует четыре метода формообразования поверхностей:
а) метод копирования; |
|
|
|
б) метод следов; |
|
|
|
в) метод касания; |
|
|
|
г) метод обкатки. |
|
|
|
Образование поверхностей по |
методу |
копирования |
|
состоит в том, что |
режущая |
кромка |
инструмен- |
та соответствует форме |
образующей обрабатываемой по- |
верхности детали. Направляющая линия воспроизводится вращением заготовки. Движение подачи необходимо для того, чтобы получить геометрическую поверхность определенного размера. Движение резании -формообразующее,
Образование поверхностей по методу следов состоит в том, что образующая линия является траекторией движения точки (вершины) режущей кромки инструмента, а направляющая линия - траекторией движения точки заготовки. Движение резания - формообразующее.
Образование поверхностей по методу касания состоит в том, что образующей линией служит режущая кромка инструмента, а направляющая линия поверхности касательная к ряду геометрических вспомогательных линий
-траекториям точек режущей кромки инструмента. Формообразующее движение
-движение подачи.
67
Образование поверхностей по методу обкатки (огибания) состоит в том, что направляющая линия воспроизводится вращением заготовки. Образующая линия получается как огибающая кривая к ряду последовательных положений режущей кромки инструмента относительно заготовки благодаря согласованию двух движений подачи. Скорости движения согласуют так, что за время прохождения круглым резцом расстояние L он делает один полный оборот относительно своей оси вращения.
Методы обработки металлом резанием различаются между собой конструкцией используемого режущего инструмента и характером относительных движений, совершаемых инструментом и обрабатываемой заготовкой.
Заготовку и инструмент закрепляют в рабочих органах металлорежущих станков. Кинематика станков основана на использовании механизмов, сообщающих исполнительным органам только два простейших движения - вращательное и поступательное. Сочетания и количественные соотношения этих двух движений определяют все известные виды обработки резанием. Комплекс всех движений, сообщаемых заготовке и инструменту, можно разделить на основные и вспомогательные. К основным относят движения процесса резания, а к вспомогательным - движения необходимые для подготовки и завершения обработки резанием.
Основных движений два:
Dr - движение резания (главное движение) и Ds -движение подачи.
Движение резания (главное движение) - это движение, определяющее скорость деформирования материала и отделение стружки.
Движение подачи - движение, обеспечивающее врезание режущей кромки инструмента в материал заготовки.
68
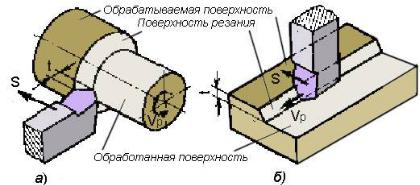
Характер выполняемых работ, вид режущего инструмента и сочетание основных движений определяют метод обработки резанием: точение, сверление, фрезерование, строгание, шлифование, протягивание и т. д.
При точении движение резания (вращательное) сообщается заготовке, а движение подачи (поступательное) - инструменту.
При сверлении на сверлильных станках как движение резания (вращательное), так и движение подачи (поступательное) обычно сообщаются инструменту.
При фрезеровании движение резания (вращательное) сообщается инструменту, а движение подачи (поступательное) заготовке. Заготовки, предназначенные для обработки резанием при изготовлении деталей машин, имеют исходные поверхности. В процессе обработки резанием с заготовки срезается припуск. При этом срезается исходная поверхность и образуется новая.
Поверхности на заготовках, срезаемые за каждый очередной проход инструмента, принято называть обрабатываемыми поверхностями (рис. 22).
Рис. 22. Поверхности на заготовке, образующиеся при резании:
а) при точении; б) при строгании
69