
Методическое пособие 660
.pdfдет выше твердости сердцевины, образуется так называемый наклепанный слой, наклеп.
Величины упругого восстановления обработанной поверхности, твердости поверхностного слоя, глубины расположения наклепанного слоя и эпюры напряжений зависят от физико-механических свойств обрабатываемого металла, геометрии режущего инструмента, условий обработки, режимов резания. Чем больше упругопластические свойства обрабатываемого материала, чем больше применяемые глубина резания и подача и чем меньше скорость резания, тем больше величина упругого восстановления обработанной поверхности, твердость поверхностного слоя и тем глубже распространен наклеп.
Вопросы для самоподготовки
1.Что получают механической обработкой металлов?
2.Для чего используется кузнечная обработка при изготовлении изделий?
3.На каком оборудовании осуществляют обточку де-
талей?
4.Какова роль механической обработки в изготовлении изделий?
5.Какие существуют процессы обработки резанием?
40
РАЗДЕЛ 2. ТЕХНОЛОГИЧЕСКОЕ ОБЕСПЕЧЕНИЕ МЕХАНИЧЕСКОЙ ОБРАБОТКИ
ЛЕКЦИЯ № 4
ОБОРУДОВАНИЕ МАШИНОСТРОИТЕЛЬНОГО ПРОИЗВОДСТВА И ПЕРСПЕКТИВЫ ЕГО РАЗВИТИЯ
Теоретическиевопросы
4.1.Оборудование машиностроительного производства
4.2.Перспективы развития и совершенствования оборудования машиностроительных производств
4.1.Оборудование машиностроительного производства
Объем и качество изготовления продукции машиностроения постоянно повышаются, совершенствуется номенклатура изделий, поэтому для реализации и освоения новых мощностей необходимы квалифицированные кадры, подготовка которых ведется по нескольким направлениям.
Заготовительное оборудование предназначено для производства заготовок. Заготовка — это полуфабрикат, предназначенный для дальнейшей обработки, в результате которой получают готовое изделие.
Заготовка должна иметь минимальный припуск, заданную геометрическую форму, шероховатость и др. Главное требование — при минимальных затратах изготовить изделие высокого качества, для чего должен быть разработан наиболее рациональный технологический процесс его производства.
На машиностроительных заводах широко применяются штампованные заготовки, поковки и отливки, получаемые соответственно штамповкой, ковкой и литьем.
41
Отрезные и шлифовальные металлоасбестовые круги используют для разрезания и зачистки различных материалов. Централизованно изготовленные, обозначенные соответствующим цветом и надписями круги предназначаются для обработки различных марок сталей, в том числе и закаленных, жести (стали толщиной до 2 мм), цветных металлов и их сплавов, высококачественных сталей, литья и камня.
Абразивные круги применяют для разрезания сталей различных марок как в закаленном, так и в незакаленном (сыром) состоянии, с охлаждением и без охлаждения. Обычно используют абразивные круги диаметром 80…400 мм и толщиной 0,5…5 мм на вулканитовой или бакелитовой связке.
Сегментные круглые пилы применяют для резания материалов, которые различаются как по свойствам, так и по размеру и профилю. Пилы выпускают диаметром 30 … 2 000 мм и толщиной 5 … 15 мм. Достоинство этих пил — возможность замены сегментов с зубьями, крепящихся заклепками на пильном диске, после износа до предельного размера.
Пилами трения (беззубыми пилами) режут металл различных размеров и профилей (уголок, пруток, двутавр, квадрат и др.), а также листы и трубы. Принцип работы пил трения основан на расплавлении и удалении жидкого металла из зоны резания. Разогрев металла до жидкого состояния происходит за счет теплоты, образующейся при трении быстровращающейся пилы о разрезаемый матери- ал. Пила трения представляет собой диск диаметром до 1 м и более.
Диаметр и толщина диска зависят от размеров нарезаемых заготовок. Диски изготавливают из низкоуглеродистой стали с содержанием марганца 0,8 … 1,2 %. Пилы мо-
42
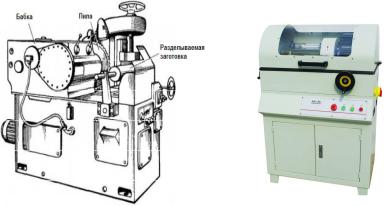
гут быть с гладкими поверхностями резания (образующими) или иметь зубья в виде накатки или насечки.
Оборудование для резки металла ножом. К этой группе оборудования относятся отрезные ножовочные и ленточнопильные станки, с которыми ознакомимся подробно. Отрезной ножовочный станок предназначен для резания следующих видов проката:
-круглого — диаметром до 250 мм;
-квадратного — со стороной до 250 мм;
-двутаврового — до № 24;
-швеллерного — до № 24.
Отрезные станки - это станки, предназначенные для распилки деталей из любого вида металлов, начиная от алюминия и заканчивая толстыми стальными прутками. Если вы хотите отрезать профиль, то это можно сделать под двумя углами: прямым, а также в 45 градусов.
С помощью отрезного станка можно производить пиление и отрезание труб большого и малого диаметров.
Устройство и основные узлы отрезного станка показаны на рис. 9.
Рис. 9. Общий вид отрезного станка
43
Отрезные станки бывают одноголовочные, двухголовочные, с фронтальной, маятниковой и нижней подачей – эти отрезные станки отличаются друг от друга наименованием головок для резания, возможностью производить резание под различным углом.
Наихудшими характеристиками по производительности обладает одноголовочные отрезной станок. Лучшие производительные характеристики имеет двухголовочный отрезной станок, он также может работать как шаговая пила, такие станки устроены следующим образом, одна головка закреплена неподвижно, а другая имеет возможность всё время перемещаться.
По подаче режущего инструмента, самыми лучшими характеристиками выделяется отрезной станок с нижней подачей, на таком станке наклон инструмента полностью автоматизирован, пределы работы его широки и работа им осуществляется в любом направлении.
Любой отрезной станок имеет следующий принцип работы. Сначала в целях техники безопасности проверяют. В каком состоянии находиться пильный диск, его целостность и острота и закрепленность.
Производить отрезание детали можно, только если диск отрезного станка наберёт нужные обороты. Чтобы деталь не болталась, при резании диском её жестко зажимают в тиски. Выбирая пильный диск, нужно всегда знать какой материал им будет обрабатываться.
Пильный диск для отрезного станка с мелким шагом берут для тонкостенных деталей и заготовок, с большим шагом для деталей, имеющих мягкую форму и сплошную форму.
К основным техническим характеристикам отрезных станков относят: габаритные размеры, мощность станка, размер диска и параметры заготовок.
44
Используя классификацию по технологическим признакам все оборудование, использующиеся на машиностроительном предприятии, можно подразделить на следующие обобщенные группы:
I – машины и линии для механической обработки; II – сборочное оборудование;
III – химико-технологическое оборудование;
IV – контрольно-измерительное оборудование.
К оборудованию механической обработки относят машины и линии для переработки объектов (деталей) методом снятия стружки (металлообработка), давлением (штамповка, прокатка, волочение) и т.п.
Сборочное оборудование выполняет операции меха-
нического соединения деталей, пайки, сварки и сопутствующие сборке операции.
На химико-технологическом оборудовании выпол-
няют операции термообработки, гальванообработки, металлизации, луженения, окраски, обезжиривания, сушки, маркировки.
Контрольно-измерительное оборудование предна-
значено для послеоперационного контроля (для определения промежуточных и выходных параметров) изделия с целью определения качества и рассортировки на годные и брак, разделения годных изделий по классам точности или селекторным группам.
Главным вопросом, изучаемым в настоящей лабораторной работе, является исследование возможностей основного технологического оборудования металлообрабатывающего производства, и, в частности, металлорежущих станков.
Станки классифицируются по множеству признаков, и прежде всего, по виду осуществляемой технологической операции.
45
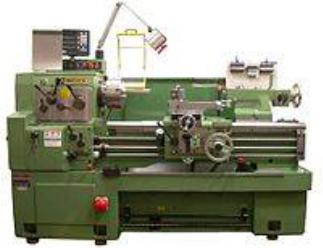
Металлорежущий станок — агрегатный механизм,
предназначен для обработки металлических и неметаллических заготовок.
Обычно имеет шпиндель либо планшайбу. Работы на данном оборудовании осуществляются механическим способом с применением резцов, свёрл и пр. режущего инструмента.
Токарный станок (рис. 10) — станок для обработки резанием (точением) заготовок из металлов, древесины и других материалов в виде тел вращения.
На токарных станках выполняют обточку и расточку цилиндрических, конических и фасонных поверхностей, нарезание резьбы, подрезку и обработку торцов, сверление, зенкерование и развёртывание отверстий и т. д.
Рис. 10. Общий вид токарного станка
Заготовка получает вращение от шпинделя, резец — режущий инструмент — перемещается вместе с салазка-
46
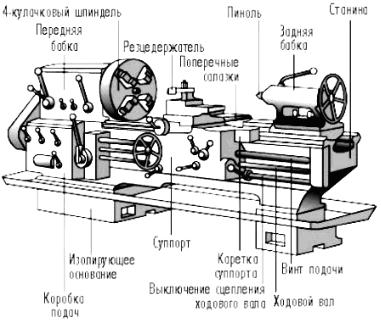
ми суппорта от ходового вала или ходового винта, получающих вращение от механизма подачи.
Устройство и основные узлы токарного станка показаны на рис. 11.
Для определения точности изготовления базовых деталей и, в частности, коробки скоростей, задней бабки, станины, суппортной группы (для токарно-винторезного станка) необходимо в первую очередь знать заданную точность обработки поверхностей деталей
Рис. 11. Основные узлы токарного станка
На рис. 12 приведена конструкторская размерная цепь, позволяющая определить точность изготовления базовых деталей токарного станка в зависимости от требуемой точности обработки поверхностей детали.
47
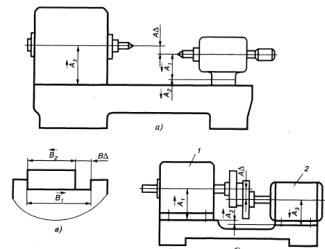
Рис. 12. Схемы размерных связей поверхностей
Размерная цепь состоит из следующих звеньев:
А1 — расстояние от основания задней бабки до оси центра задней бабки (приведена укрупненная схема размерной цепи токарного станка),
А2 — толщина основания задней бабки;
звено A3 — расстояние от основания коробки скоростей станка до оси центра передней бабки,
АА — величина несовпадения центров передней и задней бабок.
От величины АА и будет зависеть точность обработки на станке. По техническим требованиям для токарных станков нормальной точности величина несоосности центров не должна превышать 0,02 мм.
Отсюда, зная величину У4А (0,02 мм), можно определить допуски на изготовление базовых деталей токарного станка, используя при сборке станка один из пяти методов достижения точности: полной взаимозаменяемости, непол-
48
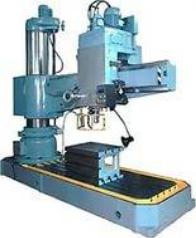
ной или частичной взаимозаменяемости, групповой взаимозаменяемости, пригонки или регулировки.
Сверлильный станок (рис. 13) - станок, предназначенный для получения сквозных и глухих отверстий в сплошном материале, для чистовой обработки, расточки (зенкерования, развёртывания) отверстий, образованных в заготовке каким-либо другим способом, для нарезания внутренних резьб, для зенкования торцовых поверхностей.
Устройство и основные узлы сверлильного станка показаны на рис. 14.
Расточной станок (рис. 15) - станок, предназначенный для обработки заготовок крупных размеров в условиях индивидуального и серийного производства.
На этих станках можно производить растачивание, сверление, зенкерование, нарезание внутренней и наружной резьб, обтачивание цилиндрических поверхностей, подрезку торцов, цилиндрическое и торцовое фрезерование.
Рис. 13. Общий вид сверлильного станка
49