
Методическое пособие 407
.pdfили при ее большой длине за базу для зубонарезания принимают конструктивную базу, или в виде цилиндрической шейки под подшипники, или специально создаваемую для базирования шейку.
Каждый вид зубчатых колес имеет свои технологические особенности изготовления. Вместе с тем различные зубчатые колеса, принадлежащие к тому или иному классу, могут иметь технологические процессы, несколько отличающиеся друг от друга по содержанию и последовательности выполнения ряда операций, в зависимости от специализации производства. Так, например, методы изготовления зубчатых колес в авиационной промышленности существенно отличаются от методов, применяемых при производстве зубчатых колес аналогичных размеров для грузоподъемных машин. Технология производства турбинных передач существенно отличается от технологии производства таких же по размерам передач для прокатных станов и т. д.
Таким образом, условия работы и требования конструкции данного механизма существенно влияют на технологический процесс изготовления зубчатого колеса.
В авиационных передачах зубчатые колеса должны при минимальных габаритах и массе передавать большие крутящие моменты, в то же время передача должна иметь особую точность и надежность.
Эти требования заставляют авиационные зубчатые колеса делать из высоколегированных сталей с применением цементации и закалки, что усложняет технологический процесс, обусловливая необходимость введения шлифовальных операций (предварительных и окончательных), большего количества проверок и операций термообработки.
В автостроении, тракторостроении и станкостроении шлифованию зубьев подвергают только некоторые пары. Зато находят широкое применение такие процессы, как шевингование, притирка и т. д.
Зубчатые колеса общего машиностроения и подъемнотранспортных машин имеют другую специфику производства.
80
Здесь преобладают колеса, изготовленные из улучшенных сталей, без последующей термообработки готовой детали. Технологический процесс при этом упрощается, однако требования к точности зубообрабатывающих станков и инструмента не снижаются.
Технологический процесс изготовления зубчатых колес можно подразделить на два этапа:
-первый этап состоит из комплекса операций, связанных с образованием геометрической формы заготовок зубчатого колеса до наре-зания зубьев;
-второй этап включает зубонарезание и все последующие процессы, связанные с отделкой зубьев или восстановлением баз относительно нарезанного зубчатого венца.
Основная специфика изготовления зубчатых колес проявляется на втором этапе; в свою очередь, построение второго этапа процесса оказывает существенное влияние на порядок и содержание первого этапа.
В настоящем разделе приводится описание в основном технологии производства зубчатых колес в первом этапе, так как в главе XXVII уже были ранее рассмотрены особенности обработки зубчатых поверхностей. Однако в приводимых схемах технологических процессов (примеров) соответственно указаны и зубообрабатывающие операции в той последовательности выполнения, которая вытекает из условий работы передачи (зубчатого колеса) и конструктивного назначения.
Материал зубчатых колес. Зубчатые колеса изготовляют из конструкционных сталей, серого чугуна, бронзы и синтетических материалов.
В автотракторостроении зубчатые колеса изготовляют из хромо-марганцовых сталей марок 18ХГТ, 30ХГТ, хромомолибденовой стали марки 30ХМ. Сталь марки 18ХГТ благодаря наличию титана обладает повышенной прокаливаемостью, прочностью и меньшей чувствительностью к перегреву. Эта сталь отличается высокой способностью сопротивляться смятию. Сталь 30ХГТ содержит несколько больше углерода, чем сталь 18ХГТ, и широко применяется для сильно нагруженных
81
зубчатых колес с модулем свыше 5 мм. Она обладает в термически обработанном состоянии высокими показателями прочности сердцевины в сечении зубьев.
Зубчатые колеса металлорежущих станков изготовляют из углеродистых сталей марок 45 и 50, а также из легированных хромистых сталей 40Х; реже применяют легированные стали марок 18ХГТ, 30ХГТ, 12ХН3А и др.
Получает распространение для изготовления зубчатых колес малолегированная борсодержащая сталь марки 20ХГР, 25ХГР. Введение небольших количеств бора (0,002 - 0,005 %) значительно увеличивает прокаливаемость, прочностные характеристики и вязкость. После закалки и низкого отпуска твердость сталиHRC36 40.
Зубчатые колеса, изготовленные из синтетических материалов (текстолита, нейлона, капрона и др.), могут работать при высоких скоростях (до 40 - 50 м/сек). Колеса из синтетических материалов обеспечивают бесшумность, плавность передачи и гашение вибрации.
Заготовки для несиловых зубчатых колес малых размеров изготовляют спеканием. Применение металлокерамики сокращает расход металла и снижает трудоемкость изготовления колес.
Заготовки зубчатых колес. Для изготовления зубчатых колес, как правило, необходимы заготовки, по форме и размерам приближающиеся к форме и размерам готовой детали.
Качество заготовки влияет на технологический маршрут механической обработки и ее трудоемкость. Конфигурация колеса, его материал и объем выпуска предопределяют способ получения заготовки.
Заготовками для стальных зубчатых колес являются штампованные поковки и нормальный катаный пруток. Цилиндрические колеса диаметром до 50 мм и плоские колеса без ступицы диаметром до 65 мм целесообразно изготовлять из горячекатаного или холоднотянутого прутка или из штучной заготовки, отрезанной от прутка. Прутковые заготовки поступают на токарные и револьверные станки и многошпин-
82
дельные автоматы (крупно-серийное и массовое производства), где производится предварительная черновая обработка с отрезкой штучных заготовок.
Цилиндрические колеса с наружным диаметром более 50 мм обычно изготовляют из поковок, получаемых штамповкой на кривошипных ковочно-штамповочных прессах, молотах, горизонтально-ковочных машинах.
Для выполнения требуемых эксплуатационных качеств в передачах с цилиндрическими зубчатыми колесами при их изготовлении должно быть обеспечено: получение соответствующей кинематической точности, плавности зацепления, необходимой величины и положения зоны прилегания боковых поверхностей, величины и постоянства боковых и радиальных зазоров в передаче, а также соответствующая чистота боковых поверхностей зубьев. Кинематическая точность зубчатых колес зависит от точности станка и инструмента, участвующих в зубонарезании, и от точности установки заготовки в процессе зубонарезания. Правильность установки, или, как ее иногда называют, правильность базирования, в свою очередь зависит от точности заготовки колеса, поступающей на зубонарезане.
Отверстия в заготовке являются технологической базой при нарезании зубчатого колеса, а в готовом зубчатом колесе - основной, измерительной и монтажной базами, т. е. отверстие определяет точность обработки при зубонарезании и точность измерения при контроле готового зубчатого колеса. Таким образом, на заготовках для зубчатых колес 3-й и 5-й степеней точности диаметры базовых отверстий следует выполнять не грубее 6 -го квалитета, 6-й и 7-й степеней точности - не грубее 8-го квалитета, а для колес степени точности 8 и ниже - не грубее 9-го квалитета.
На выбор схемы первого этапа технологического процесса изготовления зубчатого колеса влияет конструкция зубчатого колеса. Так существенно различаются схемы технологических процессов изготовления зубчатых колес, принадлежащих к классам «втулка» и «вал». Это различие распростра-
83
няется как на первый, так и на второй этапы технологического процесса и будет существовать независимо от других конструктивных особенностей зубчатого колеса, а также типов и видов производства.
Принадлежность зубчатого колеса к деталям класса «втулка» с учетом особенностей конструкции позволяет выбрать определенную схему технологического процесса его изготовления. При выборе схемы обработки зубчатого колеса руководствуются следующими соображениями: как правило, за первоначальную базу обработки колеса должны быть выбраны необработанные поверхности, которые должны быть концентричны обрабатываемым поверхностям, а необрабатываемые торцевые плоскости штамповки должны быть параллельны обрабатываемым торцевым плоскостям.
От первоначально установленных баз производится первая операция, которая заключается в сверлении и развертывании центрального отверстия и подрезании с той же установки одного из торцов ступицы. Цель этой операции — подготовка центрального отверстия под протягивание и создание обработанной торцевой базы для последующей операции.
Вторая операция - протягивание выполняется от созданной торцевой базы и сводится к образованию шлицевого или другого профиля отверстия.
Базой для дальнейшей обработки уже будет являться посадочная поверхность отверстия (шлицев).
Третья и четвертая операции являются заключительными для первого этапа и сводятся к чистовой обработке зубчатого колеса под нарезание зубьев; выполняется она с базированием по элементам шлицевого соединения или другого профиля отверстия. В этой операции должны быть особо соблюдены требования к заготовке под нарезание, изложенные выше и сводящиеся к обеспечению концентричности наружной поверхности шестерни — посадочной поверхности отверстия - и перпендикулярности обработанных торцевых плоскостей относительно оси отверстия.
Пятая операция - предварительное и чистовое нарезание
84
зубьев выполняется на зубофрезерном станке. Базой для этой операции является посадочный диаметр шлицевого или другого профиля отверстия и один из торцов зубчатого венца.
Шестая, седьмая и двенадцатая операции относятся к отделочным видам обработки. Здесь базой являются те же поверхности.
Конические зубчатые колеса, так же как и цилиндрические, могут относиться к деталям классов, «втулка» и «вал», что определяет выбор принципиальной схемы технологического процесса их изготовления.
Вместе с тем конструкция конических зубчатых колес и их зацепление имеют свои специфические особенности, существенно влияющие на построение отдельных операций технологического процесса.
Первый этап технологического процесса изготовления конических зубчатых колес выполняется по указанным выше для деталей классов «втулка» и «вал» принципиальным схемам. Наиболее значимой в первом этапе является чистовая токарная обработка заготовки зубчатого колеса.
В большинстве случаев чистовая токарная обработка конических колес производится или в две операции, или по крайней мере за две установки.
Первая чистовая токарная операция (или первая установка) состоит из обработки базового торца и наружной поверхности колеса; во второй токарной операции (или второй установке) производится обточка конусов и других поверхностей. При этом за базу принимают торцевые поверхности, обработанные в первой операции. Для конических зубчатых колес с косыми зубьями, имеющих опорный монтажный торец со стороны малого дополнительного конуса, обработка опорных поверхностей производится во второй операции. Для уменьшения перестроек резцов на размер иногда обтачивание наружного конуса выделяют в отдельную операцию.
85
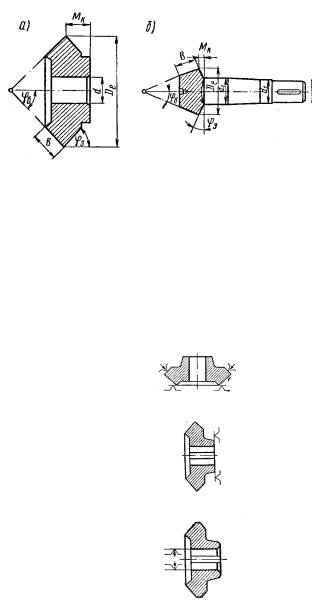
Рис. 3.1. Заготовки конических зубчатых колес:
а) насадного (класса «втулка»); б) валкового (класса «вал»)
Таблица 3.2
Технологическая схема изготовления конического зубчатого колеса класса «втулка»
№ опера- |
Содержание опе- |
Эскиз |
Оборудование |
||
ции |
рации |
|
|
|
|
1 |
Сверление |
|
цен- |
|
Вертикально- |
|
трального |
отвер- |
|
сверлильный |
|
|
стия и подрезание |
|
станок |
||
|
торца |
|
|
|
|
2 |
Протягивание |
|
Протяжной |
||
|
круглого |
отвер- |
|
станок |
|
|
стия и шпоночно- |
|
|
||
|
го паза (последо- |
|
|
||
|
вательно |
в |
две |
|
|
|
операции) |
|
|
|
|
3 |
Обтачивание |
на- |
|
Токарный ста- |
|
|
ружной |
поверх- |
|
нок |
|
|
ности, подрезание |
|
|
||
|
базового торца и |
|
|
||
|
снятие фасок |
|
|
|
|
|
|
|
|
|
|
86

|
|
|
|
Продолжение табл. 3.2 |
|
4 |
Обтачивание |
ко- |
|
Токарный ста- |
|
|
нусов, подрезание |
|
нок |
||
|
второго |
торца, |
|
|
|
|
снятие фасок |
(в |
|
|
|
|
одну или две-три |
|
|
||
|
операции) |
|
|
|
|
5 |
Предварительное |
|
Горизонталь- |
||
|
нарезание зубьев |
|
но-фрезерный |
||
|
|
|
|
|
станок |
6 |
Чистовое |
строга- |
|
Зубострогаль- |
|
|
ние зубьев |
|
|
|
ный станок |
Достаточно высокую сложность представляет технологический процесс обработки червячных пар, состоящих из червяка и червячного колеса. Как червяк, так и червячное колесо могут иметь различное конструктивное оформление.
Червяк может быть насадным на вал, и в этом случае он будет относиться к деталям класса «втулка», но может быть выполнен и сплошным в виде вала.
Таблица 3.3
Технологическая схема изготовления конического зубчатого колеса класса «вал»
№ опера- |
Содержание |
|
Эскиз |
Оборудование |
|||
ции |
операции |
|
|
|
|
|
|
1 |
Фрезерование |
и |
|
Фрезерно- |
|||
|
центрование |
|
|
центровачный |
|||
|
торцов |
|
|
|
|
полуавтомат, |
|
|
|
|
|
|
|
модель 4815 |
|
2 |
Токарная |
обра- |
|
|
|
||
|
ботка |
хвостови- |
|
|
|
||
|
ка |
|
|
|
|
Многорезцо- |
|
3 |
Токарная |
обра- |
|
вый |
станок, |
||
|
ботка |
хвостови- |
|
модель 1722 |
|||
|
ка |
«головки» |
|
|
|
||
|
колеса |
|
|
|
|
|
|
|
|
|
|
87 |
|
|
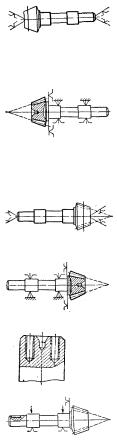
Окончание табл. 3.3
4 |
|
Предваритель- |
|
Круглошлифо- |
||||
|
|
ное шлифование |
|
вальный |
ста- |
|||
|
|
шеек |
|
|
|
нок, |
модель |
|
|
|
|
|
|
|
312М |
|
|
5 |
|
Предваритель- |
|
|
|
|
||
|
|
ное |
нарезание |
|
|
|
|
|
|
|
зубьев |
|
|
|
Станок модели |
||
6, 7 |
|
Чистовое |
наре- |
|
||||
|
|
5А27 С-1 |
|
|||||
|
|
зание вогнутой и |
|
|
||||
|
|
|
|
|
|
|||
|
|
выпуклой сторон |
|
|
|
|
||
|
|
зубьев |
|
|
|
|
|
|
10 |
|
Чистовое |
шли- |
|
Круглошлифо- |
|||
|
|
фование шеек |
|
вальный |
ста- |
|||
|
|
|
|
|
|
нок, |
модель |
|
|
|
|
|
|
|
312М |
|
|
11 |
|
Шлифование |
|
Зубошлифо- |
||||
|
|
зубьев |
|
|
|
вальный |
ста- |
|
|
|
|
|
|
|
нок, |
модель |
|
|
|
|
|
|
|
5872 |
|
|
12 |
|
Сверление и на- |
|
Вертикально- |
||||
|
|
резание резьбы в |
|
сверлильный |
||||
|
|
двух |
торцевых |
|
станок 2А35 |
|||
|
|
отверстиях |
|
|
|
|
|
|
13 |
|
Фрезерование |
|
Шпоночно- |
|
|||
|
|
шпоночного паза |
|
фрезерный |
|
|||
|
|
|
|
|
|
станок, |
модель |
|
|
|
|
|
|
|
692А |
|
|
|
Примечание. Нижеперечисленные номера операций означают: |
|||||||
8 - термообработка: 9 - зачистка центров; 14 - контроль. |
|
|
||||||
|
|
|
|
|
|
|
|
|
Червячное колесо обычно изготовляется сборным из двух деталей: венца и ступицы; только в передачах малых размеров встречаются червячные колеса, выполненные в виде одной детали. Такая конструкция колес объясняется тем, что в червячных передачах имеет место скольжение поверхностей
88
витков червяка и зубьев колеса с высокими скоростями, вследствие чего в качестве материала для червячного колеса используется антифрикционный чугун или бронза, обладающие улучшенными антифрикционными свойствами, в то время как сама ступица может изготовляться из менее дефицитного и более дешевого материала.
Указанные конструктивные особенности червяков и червячных колес определяют выбор принципиальной схемы технологического процесса их изготовления.
Обработка червяков в первом этапе технологического процесса принципиально не отличается от изготовления цилиндрических зубчатых колес соответствующего класса.
Схема обработки в первом и во втором этапах червячных колес сходна с обработкой цилиндрических или конических колес в осевой установке червячного колеса (а в глобоидных передачах - и червяка) при токарной и зубообрабатывающей операций.
Второй этап технологического процесса изготовления червяков и червячных колес имеет свои специфические особенности, несвойственные другим видам передач и в значительной мере зависящие от выбранной геометрии зацепления пары.
Выбор схемы технологического процесса изготовления червяков и червячных колес производится с учетом:
а) конструкции детали (принадлежности ее к определенному типовому классу); геометрии боковых поверхностей витков червяка, материала червяка, вида термообработки, степени точности;
б) объема производства и его специализации.
Для второго этапа изготовления несборных червячных колес остается действительной только последняя часть процесса, начиная с четвертой операции.
89