
Методическое пособие 407
.pdfтехнологической среды, сведения о материале, виде заготовки
иее состоянии, штучном и штучно-калькуляционном времени.
-Против каждого технологического перехода дается информация о режущем и мерительном инструменте, расчетных размерах, режимах резания и элементах технического нормирования.
Информация о режущем инструменте включает в себя наименование инструмента, его шифр или обозначение, материал режущей части, при необходимости указываются его основные характеристики. Например, для фрезы указывается тип фрезы, ее диаметр и число зубьев – фреза торцовая Ǿ 40 мм, z = 8. Для мерительного инструмента желательно указать его тип и шифр или обозначение.
Расчетные размеры – это расчетный диаметр и длина обработки. Расчетный диаметр – это тот диаметр, который входит в формулу скорости резания. Для точения это диаметр до обработки, для растачивания после обработки, для сверления и фрезерования – диаметр инструмента.
В некоторых случаях для иллюстрации технологического процесса необходимо представить технологическую наладку. Она представляет эскиз, аналогичный операционному эскизу, но составленный для одного технологического перехода. На этом эскизе размещается весь применяемый в данном технологическом переходе режущий инструмент до или после выполнения перехода.
70
3. МЕТОДЫ ИЗГОТОВЛЕНИЯ И МАРШУРУТЫ ОБРАБОТКИ ТИПОВЫХ ДЕТАЛЕЙ МАШИН
Несмотря на громадное разнообразие в мировом машиностроении различных конструкций деталей машин, их можно систематизировать по конструкторско-технологическим признакам. Наибольшее распространение получили такие классы деталей, как валы, корпусные детали, зубчатые колеса и т. д. Детали каждого класса имеют свои особенности построения технологического процесса /2/.
3.1.Обработка валов
Вконструкциях машин и механизмов основными деталями для передачи вращательного движения и крутящего момента являются валы.
Впроцессе работы валы испытывают сложные деформации - кручение, изгиб, растяжение и сжатие. Поэтому, чтобы обеспечить нормальную работу деталей, передающих движение на вал, и узла в целом к валам предъявляются требования жесткости.
Валы очень разнообразны как по форме, так и по размерам, однако по технологическим признакам их можно привести к двум исходным формам: гладкому и ступенчатому валам.
Наиболее простую геометрическую форму имеют прямые гладкие валы постоянного диаметра, но их применение весьма ограничено.
Наиболее распространены в машиностроении ступенчатые валы, основными технологическими параметрами которых являются: общая длина вала, количество ступеней, неравномерность их перепада по диаметрам, диаметр наибольшей ступени, наличие шлицев и их форма.
Втабл. 3.1 приведены разновидности сплошных и полых ступенчатых валов.
71
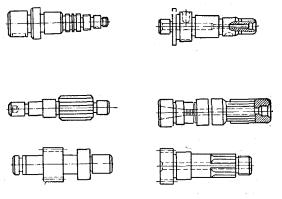
|
|
Таблица 3.1 |
Основные виды ступенчатых валов |
||
Конструктивные |
Сплошные без цен- |
Полые с централь- |
разновидности |
трального отверстия |
ным отверстием |
|
|
|
Гладкие без шлицев |
|
|
и зубчатых венцов |
|
|
Гладкие с фланцем |
|
|
|
|
|
Шлицевые |
|
|
|
|
|
С зубчатым венцом |
|
|
|
|
|
Жесткость конструкции вала определяется геометрической формой (отношением длины вала к диаметру); увеличение жесткости вала за счет уменьшения длины не всегда возможно.
Наиболее технологичными являются валы с возрастающими или убывающими диаметрами ступеней со стандартными размерами. Участки вала, имеющие один и тот же номинальный диаметр, но разные посадки, должны быть разделены канавками, четко разграничивающими обрабатываемые поверхности от необрабатываемых, при этом желательно, чтобы обрабатываемые участки вала имели равные или кратные длины, а перепады ступеней вала были бы невелики.
Валы изготовляют из сталей, обладающих высокой прочностью, малой чувствительностью к концентрации напряжений, хорошей обрабатываемостью и способностью подвергаться термической обработке. Этим требованиям отвечают конструкционные и легированные стали марок 35, 40, 45, 40Г и 50Г.
72
Валы с небольшим числом ступеней и незначительными перепадами диаметров изготовляют из штучных заготовок, отрезанных от горячекатаного или холоднотянутого прутка, а имеющие более сложную конфигурацию и с большим числом ступеней или со ступенями, значительно отличающимися по диаметрам, - из заготовок, получаемых штамповкой, поперечным прокатом или ротационным обжатием. Выбор рациональной заготовки должен быть обоснован техникоэкономическими расчетами.
В массовом и крупносерийном производствах валы изготовляют из заготовок, обеспечивающих эффективное использование металла (коэффициент использования металла К = 0,65 0,7 и более) и значительное сокращение трудоемкости механической обработки.
Штучную заготовку из прутка заменяют штамповкой, если К. повышается не менее чем на 5 %. Заготовка, полученная ротационным обжатием, наиболее близко приближается по конфигурациииразмерамкготовойдетали,приэтомК.=0,85 0,95.
Заготовки небольших ступенчатых валов диаметром до 25 мм изготовляют сочетанием холодной высадки и экстрюдинг - процесс а, а именно: из штучной прутковой заготовки за несколько переходов высаживают ступенчатую часть, имеющую диаметр больший, чем исходная заготовка, а затем вытягивают ту часть, диаметр которой меньше размера исходной прутковой заготовки.
Механической обработке поверхностей вала предшествует образование единой базы для установки обрабатываемой заготовки вала на всех операциях. Основными базами вала являются торцевые поверхности и центровые отверстия, от точности выполнения которых зависит и точность исполнения последующих операций.
Основной технологической задачей, решаемой в процессе механической обработки ступенчатых валов, является обеспечение расположения осей всех обрабатываемых ступеней вала на одной геометрической линии в целях уменьшения радиального биения.
73
3.2. Обработка корпусных деталей
Корпусные заготовки изготовляют литыми или сварными. Конструкции литых заготовок (чугунных или стальных) - корпусных деталей должны отвечать требованиям машинной формовки, т. е. толщина стенок в разных сечениях не должна иметь резких переходов. Конструкции корпусных деталей из цветных сплавов должны обеспечивать возможность их литья в постоянные металлические формы.
Механическая обработка корпусных заготовок сводится главным образом к обработке плоскостей и отверстий, поэтому технологические требования, обусловливающие наименьшую трудоемкость обработки, определяют следующими основными условиями:
-форма корпусной детали должна быть возможно ближе
кправильной геометрической форме, например в поперечном сечении предпочтительнее форма четырехугольника; форма корпусной детали должна также предусматривать возможность ее полной обработки от одной базы: от плоскости и двух установочных отверстий на этой плоскости;
-обработка плоскости и торцов отверстий по возможности должна выполняться на проход, для чего плоскости и торцы не должны иметь выступов; торцам отверстий необходимо придавать удобную форму для обработки их торцевой фрезой или цековкой;
-корпусная деталь не должна иметь поверхностей, не перпендикулярных к осям отверстий как на входе, так и на выходе сверления;
-точно растачиваемые отверстия не должны иметь внутренних выступов, препятствующих растачиванию на проход; диаметры обрабатываемых отверстий внутри корпусной детали не должны превышать диаметров соосных им отверстий в наружных стенках детали;
-в корпусных деталях следует избегать многообразия размеров отверстий и резьб.
Корпусную деталь следует изготовлять без спаривания с
74
другой корпусной деталью и по возможности избегать пришабривания отдельных плоскостей или отверстий.
На диаметральные размеры основных отверстий задают допуски в пределах 6 8-го квалитетов. Допуски на межосевые расстояния основных отверстий и перпендикулярность осей отверстий задают в соответствии с назначением корпусных деталей: например для корпусов зубчатых и червячных передач - в пределах 0,04 0,06 мм и выше.
Отклонения от соосности отверстий принимают в пределах половины допуска на диаметральный размер соосных отверстий.
Для базирования заготовок корпусных деталей совмещают установочную, измерительную и сборочную базы. Для обработки базирующих поверхностей за первичную базу следует принимать черные основные отверстия детали, что обеспечивает наиболее равномерное распределение припусков при последующей обработке отверстий. В ряде случаев в качестве первичных баз предусматривают специальные приливы и бобышки.
При совмещенных установочной и измерительной базах не бывает погрешности базирования, и погрешность установки определяют погрешностью закрепления. При переменных базах погрешность базирования определяют построением размерной цепи.
Пространственные отклонения как в литых, так и в сварных конструкциях заготовок характеризуются смещением и уводом осей основных отверстий, возникающими в процессе литья или сварки. Кроме того, в процессе механической обработки заготовок, особенно после черновых операций, возникают деформации в результате перераспределения внутренних напряжений в связи с удалением верхних слоев металла. Пространственные отклонения заготовок уменьшаются в процессе механической обработки, но оказывают влияние после выполнения черновых и чистовых операций.
Таким образом, пространственные отклонения в процессе механической обработки заготовок представляют собой со-
75
вокупность остаточных пространственных отклонений заготовки и деформаций, возникающих в процессе ее обработки.
К наиболее распространенным корпусным деталям относятся: корпуса редукторов подъемно-транспортных машин и оборудования, станины кузнечно-прессового оборудования и металлорежущих станков и другие подобные детали, характеризующиеся наличием плоскостей с заданным расположением различных поверхностей, отверстий и предназначенных для соединения и координации взаимного положения основных узлов машины, агрегата, станка.
Обработку корпусных деталей выполняют в следующем порядке: вначале обрабатывают базирующие поверхности и крепежные отверстия, которые могут быть использованы при последующей установке; затем - все плоские поверхности и после них - основные отверстия. При этом для корпусов нежесткой конструкции применяют повторную (проверочную) обработку базовых поверхностей после черновой обработки всех плоских поверхностей и основных отверстий.
Однократно обрабатывают весьма жесткие конструкции корпусов при точных методах выполнения заготовок.
Окончательную обработку - шлифование или другие отделочные операции производят в том же порядке: сначала обрабатывают плоские поверхности, а затем - основные отверстия. Этот способ обработки называется обработкой от плоскости. При использовании в качестве установочной базы отверстия и прилегающего к нему торца процесс называется обработкой от отверстия. Целесообразность обработки от плоскости или от отверстия зависит от ряда условий, а именно: точности заготовки, требуемой точности обработки, производственной программы (допустимой сложности приспособлений), действующего парка оборудования и др.
Для средних и малых размеров корпусных деталей, где перестановки их в процессе обработки не вызывают трудностей, понятие обработки «от плоскости» или «от отверстия» теряют свое значение. Здесь целесообразней следовать принципу совмещения конструкторских и установочных баз.
76
Сварные конструкции корпусов, выполненные из элементов, не подвергавшихся обработке, проходят черновую, получистовую и чистовую обработки. При этом в зависимости от объема производства и точности выполнения сварочных работ корпуса обрабатывают в приспособлениях или по разметке. Поверхности сварных корпусов, выполненные из предварительно обработанных элементов, подвергают только чистовой обработке без разметки, так как такие корпуса сваривают в приспособлениях, обеспечивающих достаточную точность взаимного положения их элементов. При этом установку крупногабаритных корпусов производят с выверкой по обработанным до сварки поверхностям, а установку корпусов небольших габаритов - в приспособлениях.
Плоские поверхности корпусов в серийном производстве обрабатывают на продольно-фрезерных или продольнострогальных станках, а в массовом - на протяжных станках, фрезерных станках непрерывного действия с карусельными столами или с барабанными устройствами. Последние типы станков позволяют применять параллельно-последовательный метод черновой и чистовой обработки.
Плоские поверхности корпусов больших размеров обрабатывают на портально-фрезерных станках фрезерными головками, перемещающимися относительно заготовки, установленной на неподвижной плите станка.
Базовые поверхности корпусных деталей небольших размеров обрабатывают на обдирочно-шлифовальных станках с вертикальной осью вращения.
Плоские поверхности корпусов окончательно обрабатывают шлифованием на плоскошлифовальных станках, тонким строганием широким резцом, тонким фрезерованием и шабрением.
Основные отверстия корпусных деталей обрабатывают на универсальных горизонтально-расточных станках или на агрегатных многошпиндельных станках.
Диаметральные размеры отверстий получают обработкой соответствующим мерным инструментом (развертки, рас-
77
точные блоки и расточные головки), установленным на расточных оправках или борштангах, а также односторонне расположенными резцами с точной регулировкой на размер.
Точность межосевых расстояний, параллельность и перпендикулярность осей и другие требования к расположению отверстий обеспечивают обработкой отверстий с направлением инструмента в кондукторе или обработкой отверстий без направления инструмента, с использованием универсальных способов координации положения инструмента.
В массовом и крупносерийном производствах основные отверстия корпусных деталей обрабатывают на многошпиндельных станках одновременно с двух или трех сторон заготовки. Положение отверстий определяют соответственно расположенными в головках агрегатных станков шпинделями и инструментом, направляемым кондукторными втулками установочного приспособления.
Основные отверстия корпусов небольших габаритных размеров могут быть обработаны на вертикальносверлильных станках с применением кондукторов и многошпиндельных головок и на радиально-сверлильных станках с применением поворотных кондукторов.
В серийном производстве основные отверстия в корпусных деталях обрабатывают на универсальных горизонтальнорасточных станках с направлением инструмента по кондуктору. Межосевые расстояния и параллельность осей отверстий обеспечивают перемещением стола и направлением расточной скалки оправки по кондуктору, а перпендикулярность осей - поворотом стола станка с закрепленной на нем заготовкой.
Чтобы повысить производительность труда при работе на расточных станках, применяют многошпиндельные расточные головки для одновременной обработки нескольких отверстий с параллельными осями.
Обработку с направлением инструмента по кондукторным втулкам ведут на агрегатных станках и на универсальных расточных станках при установке обрабатываемых корпусов в кондукторе на установочные пальцы по двум базовым отвер-
78
стиям, расположенным на плоской поверхности основания. Для обработки отверстий, расположенных на разной вы-
соте, шпиндель устанавливают, перемещая шпиндельную бабку по колонне станка.
Втяжелом машиностроении, кроме расточных станков с подвижным столом, применяют расточные станки с неподвижным столом, у которых все необходимые рабочие движения совершает шпиндельная бабка. Расточные операции, производимые на этих станках, обычно не разделяют на предварительные и чистовые, а выполняют при одной установке. После выполнения всех переходов и по достижении заданных размеров и чистоты поверхностей переходят к обработке отверстий на следующей оси.
Втяжелом машиностроении применяют переносные станки и агрегатные установки (расточные, сверлильные, фрезерные и др.) для одновременной обработки корпусных деталей.
3.3. Обработка зубчатых колес
Технологический процесс изготовления зубчатых колес должен обеспечивать получение деталей, соответствующих условиям эксплуатации и требованиям точности при наименьших затратах.
Основными факторами, влияющими на выбор технологического процесса, являются: конструкция и размеры зубчатого колеса; вид заготовки и материал; требования к точности и качеству термической обработки колеса; объем производства.
Детали класса «втулка» имеют центральное отверстие, концентричное наружной цилиндрической, конической или глобоидной поверхности. В одних случаях центральное отверстие является конструктивной базой колеса, в других - технологической базой.
В деталях класса «вал» базой в большинстве случаев являются центровые отверстия. При малой жесткости детали
79