
паровые и газовые турбины для электростанций
.pdfПоэтому проблема интенсификации воздуховыделения при работе на огнестойком масле особенно актуальна. Она решается, в частности, установкой в баке специального воздухоотделителя.
Воздействие на конструкционные материалы, применяемые в турбинах (сталь, цветные металлы, баббит и др.), со стороны ОМТИ и минерального масла примерно одинаково. Вместе с тем многие прокладочные и изоляционные материалы, например паранит, бакелит, маслостойкие резины, полихлорвинил, растворяются ОМТИ и должны заменяться на прессшпан, шеллак, фторопласт и т.п.
Диэлектрические свойства ОМТИ хуже, чем минерального масла, но это не приводит к серьезным трудностям в работе элементов электроавтоматики турбины с ее сравнительно низким уровнем напряжения.
Токсичность ОМТИ по сравнению с токсичностью первых образцов отечественных огнестойких масел значительно снижена, и в настоящее время предельно допустимая концентрация (ПДК) аэрозо-
3
лей ОМТИ (5 мг/м ) находится на уровне ПДК аэрозолей нефтяного масла. Тем не менее при организации эксплуатации и ремонта должны быть созданы и постоянно соблюдаться безопасные условия работы с ОМТИ.
Стоимость ОМТИ в несколько раз выше, чем стоимость минерального масла, хотя и немного снижается по мере совершенствования технологии изготовления. При сопоставлении затрат следует учитывать более длительный срок службы огнестойкого масла по сравнению с минеральным.
Длительная опытно-промышленная эксплуатация системы смазки одной из турбин К-300-23,5 ЛМЗ с использованием ОМТИ показала принципиальную возможность замены минерального масла на огнестойкое не только в системе регулирования, но и в системе смазки. Она была затем подтверждена опытом промышленной эксплуатации таких систем на нескольких турбинах К-800-23,5. Применение огнестойкого масла в системе смазки является новым серьезным шагом в повышении пожарной безопасности турбоустановки. Сдерживающими факторами являются относительно высокая стоимость ОМТИ и необходимость резкого расширения его производства.
10.4. МАСЛОСНАБЖЕНИЕ СИСТЕМЫ РЕГУЛИРОВАНИЯ
Применение различных |
рабочих |
жидкостей |
в системах регулирования |
и смазки, |
например |
ОМТИ и нефтяного масла, приводит к разделению маслоснабжения турбоагрегата на две независимые друг от друга системы.
Маслоснабжение систем регулирования и защиты рассмотрим на примере паровых турбин большой мощности ЛМЗ, в которых с начала 60-х годов в качестве рабочей жидкости применяется синтетическое огнестойкое масло (сначала иввиоль, а в настоящее время ОМТИ).
Масло в системы регулирования и защиты подается двумя поочередно работающими насосами
маслонапорной станции (рис. 10.6) с приводом от электродвигателей переменного тока мощностью по 200 кВт. Потребляемая мощность в установившемся режиме работы составляет 90 кВт.
Обычно в работе находится один насос. При отключении работающего насоса контактами пускателя или электроконтактным манометром при падении давления в системе регулирования с 4,7 до 3,5 МПа включается двигатель резервного насоса. На линиях нагнетания каждого насоса установлены
обратные клапаны, предотвращающие слив жидкости из напорной линии в бак через насос, находящийся в резерве.
Насосы системы регулирования установлены на
масляном баке, расположенном на полу конденсационного помещения. В баке происходят выделение из масла нерастворенного воздуха, очистка его от механических примесей и охлаждение. Для уменьшения колебаний уровня масла в баке при пуске и остановке насосов верхняя часть бака сделана расширяющейся.
Воздухоотделитель выполнен в виде пакета листов из нержавеющей стали с отогнутыми краями, обеспечивающими их жесткость и определенное расстояние между листами при установке их один на другой. Угол наклона листов по ходу масла и к стенкам бака выбран с таким расчетом, чтобы интенсифицировать выделение воздуха и выход его в пространство между боковыми стенками воздухоотделителя и наружными стенками бака.
Малая нечувствительность системы регулирования может быть обеспечена только при высокой степени очистки масла от механических примесей в процессе эксплуатации. Применение огнестойкого масла обостряет проблему очистки, так как создание малорасходных систем регулирования при одновременном переходе на более высокое напорное давление требует уменьшения зазоров, а следовательно, и более тонкого фильтрования.
Сетчатый фильтр грубой очистки масла разделяет бак на «грязный» и «чистый» отсеки и состоит из двух рядов сеток с размерами ячейки 0,2 × 0,2 мм. На этих сетках задерживаются крупные частицы механических примесей. Для удобства установки и очистки сетки натянуты на рамки, опускаемые в специальные пазы. Высокая степень очистки масла от шлама и механических примесей
271
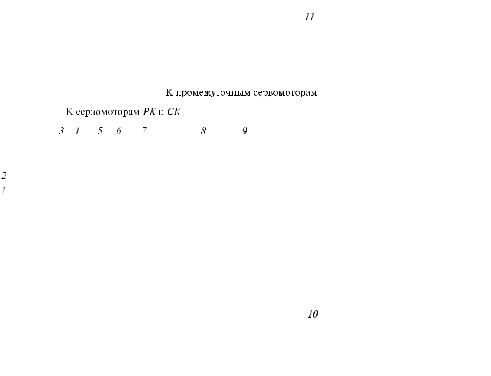
Рис. 10.6. Маслонапорная станция турбин ЛМЗ:
1 — фильтр тонкой очистки; 2 — бак систем регулирования и защиты; 3 — воздухоотделитель; 4 — сетка; 5 — указатель уровня
масла; 6 — маслоохладитель; 7 — маслоотделитель; 8 — эксгаустер; 9 — центробежный насос с электроприводом; 10 — гидрозатвор;
11 — пружинно-грузовой аккумулятор; РК, СК — регулирующий и стопорный клапаны
обеспечивается постоянной работой фильтра тонкой очистки патронного типа с применением хлопчатобумажной ткани плотного плетения.
В «чистом» отсеке бака установлен маслоохладитель, выполненный в виде двухпоточного по воде теплообменника. Наружные поверхности трубок, омываемые маслом, имеют оребрение. Для того чтобы при нарушении плотности трубной системы исключить попадание огнестойкого масла в циркуляционный контур электростанции, давление масла в маслоохладителе выбрано меньшим, чем давление воды. Охладитель может быть заменен на резервный при работе турбины. К концу операции замены охладителя температура масла не должна превышать 70 °С. Рабочая температура масла за насосами составляет (50 ± 5) °С.
Для повышения надежности маслоснабжения при электрическом приводе насосов системы регулирования необходимо обеспечить:
•аварийный переход с рабочего насоса на резервный без существенного снижения нагрузки турбины;
•нормальную работу насосов системы регулирования при снижении напряжения собственных
нужд до 70 % номинального, что может произойти при включении крупного электродвигателя, например питательного электронасоса, длительность пуска которого достигает 14—16 с;
• кратковременную (5—6 с) бесперебойную работу системы регулирования при исчезновении напряжения собственных нужд.
Уменьшение провала давления масла в напорной линии при переключении насосов и кратковременное поддержание его на необходимом уровне при потере напряжения собственных нужд и отключении в связи с этим насосов системы регулирования обеспечиваются масляным аккумулятором пружинно-грузового типа, расположенным в машинном зале рядом с масляным баком.
Объем аккумулятора выбирается из условия обеспечения нормальной работы системы регулирования в течение промежутка времени большего, чем уставка срабатывания защит на отключение блока при аварийном исчезновении напряжения собственных нужд электростанции.
При зарядке аккумулятора его поршень под действием напорного давления, развиваемого насосом системы регулирования, двигается влево и через
272
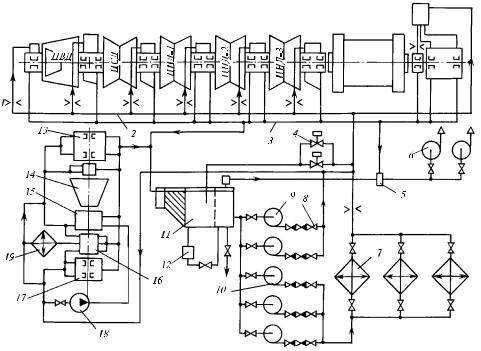
систему блоков поднимает груз. Процесс зарядки заканчивается, когда поршень достигнет левого упора.
В режиме питания от аккумулятора при падении давления в напорной линии ниже определенного уровня поршень под действием веса груза перемещается вправо и, вытесняя масло в напорный коллектор, поддерживает в нем давление на уровне, не вызывающем существенного изменения нагрузки турбины.
Характеристики маслоснабжения можно улучшить быстрым пуском резервного насоса в дополнение к работающему, при этом через 1—2 с можно получить удвоение подачи маслоснабжающей установки.
Для предотвращения попадания в машинный зал аэрозолей огнестойкого масла предусмотрена вытяжная вентиляция из бака, обеспечивающая разрежение во всех узлах регулирования, которое не должно превышать 0,4 кПа для того, чтобы количество вносимых с наружным воздухом механических примесей (угольной и цементной пыли и др.) было минимальным.
Трубопровод системы регулирования должен проходить гидравлическое испытание на плотность
при увеличении рабочего давления в 2 раза. Для этого предусмотрена возможность последовательного включения рабочего и резервного насосов системы регулирования.
10.5. ЦЕНТРАЛИЗОВАННАЯ СИСТЕМА СМАЗКИ ПАРОТУРБИННОЙ УСТАНОВКИ
Переход к автономным масляным насосам
с электроприводом и удаление масляного бака от переднего подшипника турбины создали условия для организации независимой от системы регулирования централизованной системы смазки турбоустановки, которая обеспечивает маслом подшипники главной турбины, генератора, питательных насосов, гидромуфты питательных электронасосов. Одну из таких систем рассмотрим на примере энергоблока с турбиной К-800-23,5-3 ЛМЗ (рис. 10.7).
Для обеспечения слива масла из питательных насосов масляный бак 11 располагается на полу конденсационного помещения. Он состоит из трех отсеков: «грязного», промежуточного и «чистого». Масло из сливного коллектора 3 поступает в «грязный» отсек ниже уровня находящегося в нем масла.
Рис. 10.7. Централизованная система смазки паротурбинной установки мощностью 800 МВт:
1 — дозирующая шайба; 2 — напорный коллектор; 3 — сливной коллектор; 4 — сливной клапан; 5 — маслоуловитель; 6 — эксгау-
стер; 7 — маслоохладитель; 8 — обратный клапан; 9 — аварийный насос; 10 — основной насос; 11 — масляный бак; 12 — масло-
очистительный агрегат; 13 — питательный насос; 14 — турбопривод; 15 — блок регулирования; 16 — редуктор; 17 — бустерный
насос; 18 — вспомогательный электромасляный насос; 19 — дополнительный маслоохладитель
273
Перед промежуточным отсеком установлен дырчатый лист для равномерной раздачи масла по всему сечению отсека, в результате чего улучшается работа прямоточного воздухоотделителя. После воздухоотделителя установлен двухрядный сетчатый фильтр. Для непрерывной более тонкой фильтрации на промежуточном отсеке бака размещен фильтр тонкой очистки, через который проходит часть масла.
К масляному баку подключены три основных насоса 10 с электроприводом переменного тока (один или два рабочих и резервный, работающих попеременно) и два аварийных насоса 9 с электроприводом постоянного тока. Насосы располагаются на стенках бака, что уменьшает сопротивление на всасывании, обеспечивает надежную работу насоса при более глубоком снижении уровня масла в баке и исключает скопление воздуха в резервном насосе. По сравнению с насосами погружного типа такая схема установки насосов дает возможность уменьшить объемы «чистого» отсека и бака в целом. Чтобы полностью исключить утечки масла через неработающие насосы, за каждым из них установлено по два обратных клапана 8.
Мощность каждого двигателя переменного тока (100 кВт) выбрана с двойным запасом, что обеспечивает работу насоса при падении напряжения собственных нужд до 70 % номинального и быстрый разворот (за 1 с) насоса, находящегося в резерве.
Масло из напорного коллектора основных насосов поступает в маслоохладители 7, из которых два постоянно работают, а третий находится в резерве.
Чтобы снизить нагрузку на аккумуляторные батареи, мощность приводных двигателей аварийных насосов выбрана значительно меньшей (37 кВт). Поэтому подача аварийного насоса составляет только 0,6—0,7 номинальной и они включены в обвод маслоохладителей. При включении в работу аварийного насоса и невозможности быстрого вос-
становления маслоснабжения с помощью электронасосов переменного тока турбина должна быть остановлена.
После маслоохладителей масло направляется на подшипники главного турбоагрегата, к узлам смазки турбопитательного насоса и через сливные клапаны 4 по линии рециркуляции обратно в маслобак. В турбинах последних выпусков вместо сливных устанавливается редукционный клапан, автоматически поддерживающий постоянное давление «после себя» дросселированием всего расхода масла без слива его в бак, что улучшает работу бака. Для повышения надежности маслоснабжения часть масла дросселируется помимо клапана.
Масло к вкладышам подшипников подводится из напорного коллектора 2 через бачки, встроенные в крышки подшипников. Для коррекции расхода масла перед бачками устанавливаются дозирующие шайбы
1, диаметр которых выбирается таким, чтобы при работе с номинальной частотой вращения ротора давление в бачке составляло 40—70 кПа.
Через напорный коллектор также питаются маслом подшипники питательного насоса 13, его турбопривода 14 с блоком регулирования 15, редуктора 16 и бустерного насоса 17. На линии подвода масла к зацеплению редуктора бустерного насоса установлены два дополнительных маслоохладителя
19 (на схеме показан один). При пуске турбопитательного насоса включается вспомогательный электромасляный насос 18.
Для вентиляции системы смазки предназначены два эксгаустера 6 (один из них резервный), подключенных через бачки-маслоуловители 5 к маслобаку и сливному коллектору. Маслоочистительный агрегат 12, в который входят центрифуга, пресс-фильтр, нагреватель и вакуумный аппарат, включается для периодической очистки грязного масла, скапливающегося в придонной части маслобака.
274
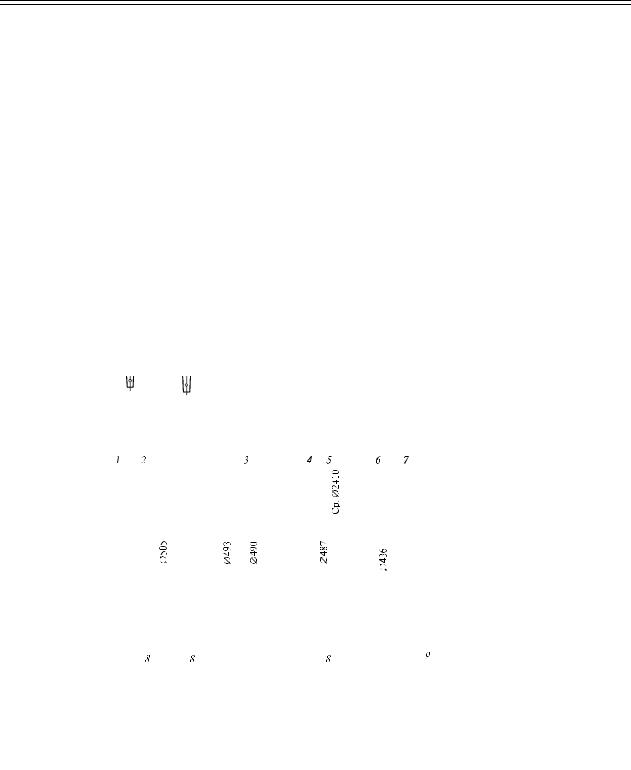
Глава одиннадцатая
КОНСТРУКЦИИ ПАРОВЫХ ТУРБИН
11.1.УСТРОЙСТВО ПАРОВОЙ ТУРБИНЫ
Вгл. 3 и 4 рассмотрено конструктивное выполнение элементов проточной части (рабочих лопаток, диафрагм, уплотнений), которая является наиболее важной составляющей турбины и определяет
ееэкономичность. Ниже описываются конструкции других элементов турбины, основы ее устройства в целом и примеры их конструктивного исполнения.
11.1.1.Валопровод т рбины
В а л о п р о в од турбоагрегата — это совокупность облопаченных, соединенных между собой роторов последовательно расположенных цилиндров и генератора. Роторы цилиндров соединяются посредством муфт.
Конструкция роторов валопровода зависит от условий работы их цилиндров, главными из кото-
рых являются два: объемный расход пара, покидающего цилиндр, и температура пара, поступающего в цилиндр.
Роторы ЦНД. Мощные конденсационные турбины имеют один или несколько двухпоточных ЦНД. Температура на входе в ЦНД (даже в турбинах с промежуточным перегревом пара) невысока и не вызывает ползучести. Вместе с тем объем пара, покидающего ЦНД, достаточно велик, поскольку давление в конденсаторе мало. Это привело к широкому распространению сборных роторов
(рис. 11.1), диски и вал которых изготавливаются отдельно, а затем собираются в единое целое с помощью горячей посадки дисков на вал. Поэтому такие роторы часто называют роторами с насадными дисками.
Сборный ротор состоит из ступенчатого вала, на который насаживаются диски, втулки концевых
Рис. 11.1. Сборный ротор ЦНД турбины Т-250/300-23,5 TМЗ (показан один из двух потоков):
1 — ступенчатый вал; 2—4 — насадные диски соот-
ветственно первой — третьей ступеней ЦНД; 5 —
втулка концевого уплотнения; 6 — втулка масляного
уплотнения корпуса подшипника; 7 — осевая шпонка;
8 — торцевые шпонки; 9 — шейка вала (под вкладыш
опорного подшипника скольжения)
275
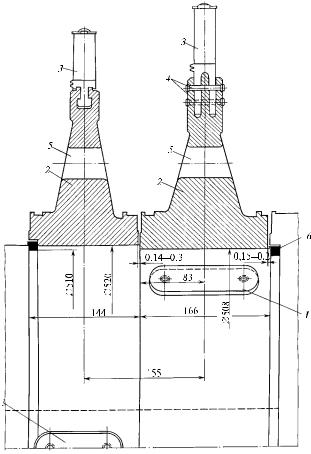
уплотнений, а также втулки масляных уплотнений корпусов подшипников. На валу выполняются шейки под вкладыши подшипников и концевые участки для насадки полумуфт.
Каждый диск обычно состоит из о б од а, в котором выполняют профильные пазы для размещения хвостовиков лопаток, п ол от н а (профильной части) и с ту п и ц ы, внутренняя поверхность расточки которой сопрягается с посадочной поверхностью вала. Полотно диска профилируют так, чтобы обеспечить прочность диска при максимально возможной частоте вращения. Из этих же соображений выбирают ширину ступицы.
Перед посадкой диска на вал размер его внутренней расточки несколько меньше, чем диаметр поверхности посадки вала. Разность радиусов вала и расточки дисков до посадки называется н атя - гом. Обычно натяг составляет 0,4—0,5 мм. Перед насадкой диск разогревают для того, чтобы его внутренний диаметр стал больше диаметра вала. Вал ставят вертикально и надевают на него диск. После охлаждения диаметр расточки диска уменьшается, диск плотно садится на вал и в месте их сопряжения возникает контактное давление, препятствующее провороту диска на валу. Передача крутящего момента с диска на вал осуществляется за счет контактного давления между ними.
Контактное давление зависит от частоты вращения. Если ротор не вращается, то оно максимально. При увеличении частоты вращения диск расширяется в радиальном направлении сильнее, чем вал, и в результате при некоторой частоте вращения, называемой о с в о б ож д а ю щ е й, контактное давление исчезает и крутящий момент не может передаться на вал через посадку. Поэтому освобождающая частота вращения диска должна быть больше, чем любая возможная частота вращения.
Чем больше натяг посадки, тем выше освобождающая частота вращения. Однако натяг создает дополнительную напряженность в диске, и поэтому чрезмерный натяг вреден. При проектировании натяг рассчитывают очень точно для того, чтобы обеспечить достаточный запас по освобождающей частоте вращения по отношению к рабочей, но не создать без необходимости излишние напряжения от посадки.
В условиях эксплуатации возможно временное ослабление посадки диска на валу, например при быстром увеличении температуры в проточной части, когда диск может прогреться быстрее вала. Для того чтобы гарантировать передачу крутящего момента в таких условиях, между диском и валом
устанавливают о с е в ы е |
ш п о н к и (рис. 11.2). |
|
Соседние |
диски насаживают на вал обязательно с |
|
о с е в ы м |
т е п л о в ы м |
з а з о р ом (0,14—0,3 мм), |
Рис. 11.2. Диски с осевыми призматическими шпонками:
1 — осевые шпонки; 2 — насадные диски; 3 — рабочие лопатки;
4 — штифты; 5 — разгрузочные отверстия; 6 — фиксирующие кольца, разъемные по диаметру
не препятствующим их взаимному тепловому расширению и исключающим изгиб ротора. На самом валу диски фиксируют в осевом направлении разъемными кольцами.
В углах шпоночного паза диска резко увеличиваются напряжения. При появлении в них трещин может произойти хрупкое внезапное разрушение диска. Поэтому осевые шпонки устанавливают только под легкими дисками, напряжения в которых невелики даже с учетом осевых шпонок. Для нагруженных дисков, в частности для дисков
последних |
ступеней, используют |
то р ц е в ы е |
ш п о н к и, |
устанавливаемые между |
торцевой |
поверхностью диска и легкой деталью, насаживаемой на вал (рис. 11.3). Диск 1 насаживается на вал 5
обычным образом. На правой торцевой поверхности с двух противоположных сторон выполнены шпоночные пазы 2. Во втулку 4 уплотнения с небольшим натягом запрессовываются шпонки 3, входящие в пазы на диске. Втулка 4 имеет малые
276
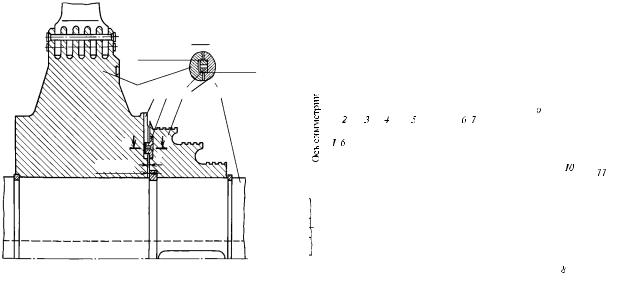
|
|
|
|
|||
|
|
|
|
|||
|
|
|
|
|
|
|
|
|
|
|
|
|
|
|
|
|
|
|
|
|
|
|
|
|
|
|
|
|
|
|
|
|
||
|
|
|
||||
|
|
|
|
|
|
|
|
|
|
|
|
|
|
|
|
|
|
|
|
Рис. 11.3. Передача крутящего момента с диска на вал с помощью торцевой шпонки
размеры, возникающие в ней напряжения от центробежных сил невелики, поэтому ее можно насадить на вал с большим натягом и даже на осевой шпонке.
На рис. 11.4 показан сборный ротор ЦНД некоторых турбин ХТЗ. Все диски насаживаются на вал без осевых шпонок. Первые диски связаны торцевыми шпонками, а крутящий момент от них передается на вал (в случае ослабления посадки) с помощью торцевых шпонок, установленных между торцевыми поверхностями выступа вала и первого диска. Крутящий момент с двух последних дисков передается на вал через торцевые шпонки, расположенные между ними и специальными шпоночными кольцами, насаженными на вал с натягом и на осевой шпонке.
Диск на валу в осевом направлении фиксируют с помощью буртика, до которого надвигается диск при горячей посадке, и кольца, устанавливаемого также в горячем состоянии в специальную расточку вала (см. рис. 11.3). Иногда такое фиксирующее кольцо делают разъемным. После установки двух половин кольца на него надвигается диск или втулка, соседствующая с рассматриваемым диском. Несмотря на фиксирующие кольца, диск должен иметь возможность свободно расширяться в осевом направлении, не вступая в контакт с соседними дисками, втулками или кольцами. Если такой контакт возникнет, то, поскольку он не может осуществляться по всей торцевой поверхности, произойдет изгиб вала и возникнет вибрация.
Основное достоинство сборных роторов состоит в том, что их можно выполнить очень больших размеров с высоким качеством дисков и вала. Основные
Рис. 11.4. Сборный ротор двухпоточного ЦНД турбины ХТЗ:
1 — выступ вала; 2 — 5 — диски первой — четвертой ступеней;
6 — торцевая шпонка; 7 — шпоночное кольцо; 8 — осевая шпонка; 9 — балансировочный груз; 10 — кольцо для осевой фиксации диска; 11 — шейка вала под вкладыш подшипника
недостатки сборных роторов связаны с высокой напряженностью насадных дисков, возможностью ослабления посадки и появления трещин из-за коррозии под напряжением в шпоночных пазах.
Сварной ротор (рис. 11.5) изготавливают из отдельных дисков и концевых частей, соединяемых кольцевыми сварочными швами по специальной технологии. Как и у сборного ротора, радиальные размеры сварного ротора не ограничиваются технологическими возможностями изготовления крупных поковок высокого качества.
Напряжения, вызванные вращением, в сварном роторе меньше, чем в сборном, так как в нем отсутствуют центральное отверстие (это снижает напряжения более чем в 2 раза) и посадка диска на вал. В свою очередь, эти два обстоятельства позволяют исключить у дисков ступицу, а профиль диска сделать таким, чтобы напряжения в нем мало изменялись по радиусу. Вместе с тем требования сварки и последующего отпуска не позволяют применить для сварных роторов высокопрочные стали.
Определенным недостатком сварного ротора является затрудненный контроль состояния его металла при капитальных ремонтах.
На ЛМЗ для ЦНД турбины К-1000-5,9/50 для работы с ВВЭР изготовлен цельнокованый ротор без центрального отверстия (рис. 11.6). Этот ротор выполнен из металла с высоким уровнем прочности, а его конструкция имеет многие преимущества сварного ротора, но не имеет сварных швов.
277
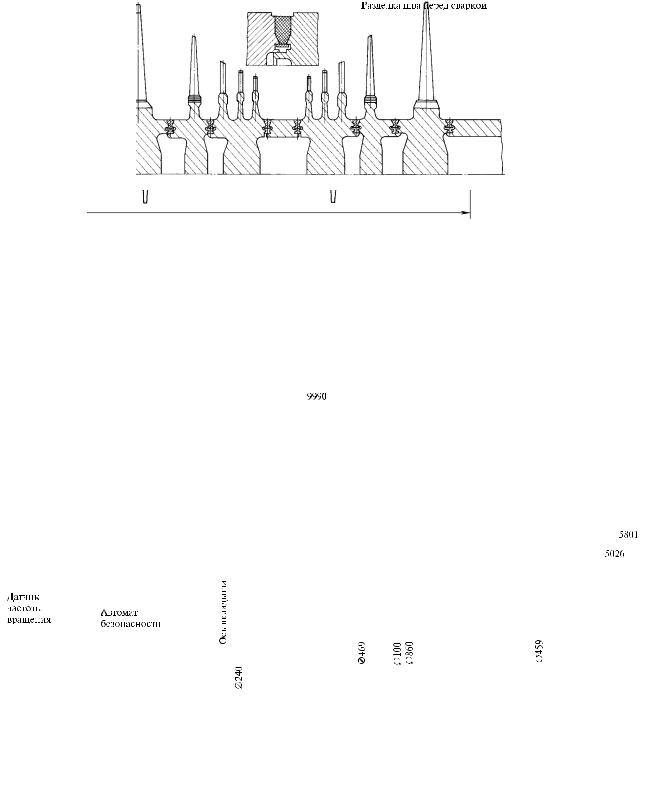
Рис. 11.5. Сварной ротор двухпоточного ЦНД турбины ХТЗ
Рис. 11.6. Цельнокованый ротор для ЦНД турбины К-1000-5,9/50 ЛМЗ
Цилиндры высокого, а в турбинах с промежу-
точным перегревом и среднего давления работают
при высоких температурах, при которых интен-
сивно развивается релакс ация напряжений —
уменьшение напряжений в деталях за счет пере-
хода части упругой деформации в необратимую
деформацию ползучести. Например, контактное
давление между диском и валом при высокой тем-
пературе со временем будет уменьшаться, освобож-
дающая частота вращения падать, и в результате
Рис. 11.7. Цельнокованый ротор ЦВД
278
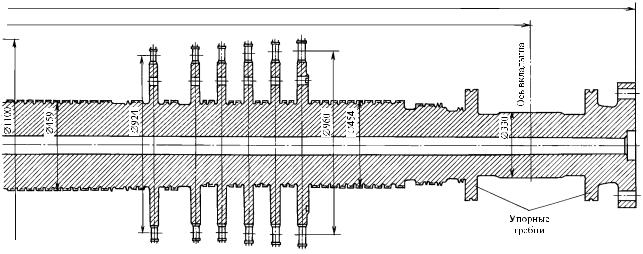
произойдет освобождение диска. Поэтому использование насадных деталей в зоне высоких температур, в частности сборных роторов, недопустимо.
Роторы ЦВД и ЦСД. Для ЦВД в основном используются цельнокованые роторы (рис. 11.7). Собственно ротор, состоящий из вала и дисков, изготавливается из одной поковки. На периферии дисков выполняют пазы для установки рабочих лопаток.
Цельнокованые роторы (как и валы для сборных роторов) почти всегда выполняют с центральным отверстием, поскольку при затвердевании слитка, начинающемся с периферии, именно в центральной зоне концентрируются вредные примеси и дефекты, которые необходимо удалять. Эти дефекты тем более опасны, что расположены они в зоне максимальных напряжений. Центральное отверстие, хотя и увеличивает напряжения, позволяет проверить его поверхность и устранить дефекты, которые могут быть в нем. Используется оно и для периодического контроля за появлением и ростом дефектов в процессе эксплуатации. После осмотра полости отверстия его еще раз тщательно очищают и закрывают пробками, исключающими попадание в него воды, масла, а также посторонних предметов.
В тех случаях, когда на входе в цилиндр температура высокая, а объемный расход пара на выходе достаточно большой (например, в ЦСД), используют комбинированный ротор: его паровпускная часть выполняется цельнокованой, а выходная — с насадными дисками (рис. 11.8).
Соединительные муфты связывают отдельные роторы цилиндров турбины и генератора в единое
целое — валопровод. Муфты передают крутящий момент с ротора на ротор и не должны разрушаться даже при его кратковременном повышении в 4—6 раз, например при коротком замыкании в генераторе.
Качество изготовления, сборки и центровки полумуфт в значительной степени определяет вибрационное состояние турбоагрегата. При соединении роторов с расцентровками или изломами естественной линии прогиба вала возникает интенсивная вибрация, делающая эксплуатацию турбоагрегата невозможной. В современных турбинах используют жесткие и полужесткие муфты.
Жесткие муфты для исключения вибрации требуют центровки очень высокого качества.
Пример простейшей жесткой муфты, чаще всего используемой для соединения роторов ЦВД и ЦСД, показан на рис. 11.9. Полумуфты 1 и 3 выполнены в виде фланцев заодно с валами соединяемых роторов. Центровка полумуфт обеспечивается с помощью кольцевого выступа, расположенного на одной полумуфте, и впадины, находящейся на другой. Перед подъемом краном любого из роторов их раздвигают с помощью отжимных винтов, ввинчиваемых в отверстия 4. Полумуфты стягиваются призонными болтами 2, устанавливаемыми в строго соосные тщательно обработанные отверстия в полумуфтах с зазором 0,001—0,025 мм. Болты затягивают равномерно, контролируя их удлинения. Крутящий момент в жестких муфтах передается за счет сил трения между торцами полумуфт, возникающих из-за сжатия призонными болтами. Для точной повторяемости сборки валопровода после рассоединения используются конические болты 5.
турбины Т-250/300-23,5 TМЗ
279

Рис. 11.8. Комбинированный ротор
Рис. 11.9. Простейшая жесткая муфта
На рис. 11.10 показана конструкция жесткой муфты с насадными полумуфтами, служащей для передачи крутящего момента с ротора турбины на ротор генератора.
Концы валов турбины 6 и генератора 9, на которые насаживаются полумуфты 3 и 8, выполняют с небольшой конусностью (примерно 0,5 %), а их посадочные поверхности пригоняют друг к другу по краске на длине 80—90 % посадочного участка. Затем полумуфту нагревают в кипящей воде или
A
1
3 4 5 6 |
7 A—A A |
8 9 |
Рис. 11.10. Жесткая муфта
280