
паровые и газовые турбины для электростанций
.pdfную диафрагму ЧНД, сохранив лишь минимальный пропуск пара, требуемый для отвода из ЧНД теплоты вентиляционных потерь. В этом положении диафрагма должна быть зафиксирована, чтобы при изменении нагрузки она не закрывалась.
Переключатель на режим с противодавлением 9 представляет собой золотник, в котором сблокированы подводящий и два сливных дросселя. При работе турбины на конденсационных режимах с отбором и без отбора пара все дроссели полностью закрыты.
При смещении золотника переключателя вниз через верхний дроссель откроется настолько большой слив масла из импульсной линии Н, управляющей сервомотором ЧНД, что последний полностью закроется, несмотря на возрастающие площади сечений подвода масла в эту линию через дроссели
11 и 12, и останется в этом положении при любых перемещениях золотников регуляторов частоты вращения и давления.
Так как поворотная диафрагма ЧНД при режиме работы с противодавлением не участвует в компенсации изменения расхода пара в отбор и в работе остаются только регулирующие клапаны ЧВД, то, если не принять дополнительных мер, степень неравномерности регулирования давления значительно возрастет. Чтобы сохранить ее примерно на том же уровне, что и при конденсационном режиме с отбором пара, необходимо увеличить передаточное число от регулятора давления к сервомотору ЧВД. С этой целью средний дроссель переключателя параллельно импульсной линии В
подключает дополнительную линию В , сливом из
1
которой управляет еще один дроссель золотника регулятора давления. Так как воздействия регулятора на основную и дополнительную линии совпадают по знаку, то при одном и том же перемещении золотника регулятора давления сервомотор ЧВД будет перемещаться на больший ход, чем при конденсационном режиме с отбором пара. Это и позволяет предотвратить повышение неравномерности регулирования давления при работе по тепловому графику.
В заключение отметим, что в настоящее время на теплофикационных турбинах ТМЗ широко применяются электрогидравлические несвязанные статически автономные системы регулирования. Главные сервомоторы и весь контур регулирования частоты вращения выполняются гидравлическими, что обеспечивает соблюдение высоких требований по быстродействию и надежности. Процессы регулирования мощности, тепловой нагрузки отборов и температуры подпиточной воды на выходе из встроенного пучка конденсатора протекают сравнительно медленно. Это делает возможным примене-
ние серийно выпускаемых промышленностью электронных ПИ-регуляторов с исполнительными механизмами невысокого быстродействия типа МЭО (механизм электрический однооборотный).
9.8. СИСТЕМА ЗАЩИТЫ ТУРБИНЫ
Система защиты турбины должна предотвратить аварию турбоагрегата или, если она возникла, ограничить ее развитие, прекратив поступление пара в турбину быстрым закрытием стопорных и регулирующих клапанов, поворотных диафрагм, обратных клапанов на линиях регулируемых и регенеративных отборов. Система защиты является последней ступенью управления оборудованием турбоустановки.
Система защиты срабатывает и дает команду на отключение турбины при недопустимых:
•повышении частоты вращения ротора;
•увеличении осевого сдвига ротора;
•падении давления масла в линии смазки подшипников;
• повышении давления (падении вакуума)
вконденсаторе;
•повышении вибрации подшипников турбоагрегата;
•повышении температуры свежего пара или резком ее снижении;
•повышении уровня воды в ПВД —
инекоторых других нарушениях режима работы турбоустановки, грозящих повредить оборудование
итребующих экстренной остановки турбины, а во многих случаях отключения всего энергоблока.
Важнейшим требованием, предъявляемым к устройствам технологических защит, является надежность действия, определяемая как по отказам в работе, так и по ложным срабатываниям.
Основными способами повышения надежности системы защиты являются совершенствование ее компонентов и применение нескольких каналов защиты. Схема их включения выбирается в зависимости от последствий, к которым может привести отказ или ложное срабатывание защиты.
Наиболее простой является схема «один из одного», использующая один прибор или устройство, срабатывающие при достижении контролируемым параметром заданной уставки. Для защит, отказ в работе которых грозит тяжелыми повреждениями оборудования, а значит, и убытками более значительными, чем при ложном срабатывании, таких, как, например, защиты от недопустимого осевого сдвига ротора или снижения вакуума в конденсаторе, надежность приборов (реле осевого сдвига, вакуум-реле) должна быть особенно высока именно в отношении отказов.
261
В тех случаях, когда безопасность оборудования в значительной мере обеспечивается безотказностью защиты, а ложные срабатывания либо маловероятны, либо не ведут к тяжелым последствиям, наиболее предпочтительной является схема «один из двух», в которой устройства с одинаковой уставкой срабатывания включены параллельно (схема «ИЛИ»). Так выполняется, в частности, защита турбины от недопустимого повышения частоты вращения.
Наименьшая вероятность ложных срабатываний достигается в схеме «два из двух», когда приборы включаются последовательно (схема «И»), что, однако, связано с заметным повышением вероятности отказов в работе.
Наиболее универсальной, обеспечивающей высокую надежность как по правильным, так и по ложным срабатываниям, является схема «два из трех». Эта схема также дает возможность проводить проверку аппаратуры на работающем оборудовании без отключения защиты и обеспечивает наибольшую живучесть в аварийных ситуациях. Она получила наибольшее распространение на АЭС.
Схемы защит при их срабатывании должны обеспечить, как правило, одностороннее воздействие на оборудование, в результате чего не восстанавливается его исходное состояние после устранения причин, вызвавших срабатывание защиты. Этим предотвращается возможное повторение аварийной ситуации, так как причина, вызвавшая срабатывание защиты, может исчезнуть с отключением оборудования. Ввод оборудования в работу после действия защиты осуществляется оперативным персоналом или под его контролем.
При срабатывании защиты должна быть обеспечена полная отработка алгоритма, заложенного в ее устройство. Это гарантирует выполнение всех команд защиты даже в том случае, если после начала ее действия исчезла причина, вызвавшая ее срабатывание. Кроме того, этим исключается возможность вмешательства оперативного персонала в работу, которое может быть ошибочным.
При пуске турбины некоторые параметры (вакуум в конденсаторе, давление и температура свежего пара и др.) оказываются ниже аварийных уставок, что при включенных защитах делает пуск невозможным. Поэтому схемами защит должна быть предоставлена возможность ручного или автоматического отключения защит, препятствующих пуску, или предусмотрено автоматическое изменение аварийных уставок. Может быть реализован автоматический ввод защит в работу при выходе контролируемого параметра на заданный уровень.
Поскольку защиты вступают в работу тогда, когда система регулирования и оперативный пер-
сонал не обеспечили безопасную работу оборудования, их действию предоставляется высший приоритет по отношению к действиям оператора и системы регулирования.
Рассмотрим работу некоторых защит турбины.
Защита по повышению частоты вращения. Из всех защит турбины самой ответственной является защита от разгона (от недопустимого повышения частоты вращения). Это связано с тем, что разрушение турбины центробежными силами является одной из тяжелейших аварий на электростанции, влекущей за собой полный выход из строя оборудования, серьезные повреждения здания и другие тяжелые последствия.
Безопасность турбины при значительном повышении частоты вращения обеспечивается двумя независимыми системами — регулирования и защиты. Правильно спроектированная и нормально функционирующая система регулирования турбины должна обладать таким быстродействием, чтобы даже в случае полного сброса нагрузки с отключением турбогенератора от сети не допустить повышения частоты вращения ротора до уровня настройки защиты от разгона. Другими словами, система регулирования после сброса полной нагрузки должна удержать турбину на холостом ходу.
Важно отметить, что системы регулирования и защиты действуют совершенно независимо друг от друга — от измерителей частоты вращения (регулятора частоты вращения и автомата безопасности) до парозапорных органов (регулирующих и стопорных клапанов).
Большим преимуществом системы регулирования как первой линии защиты является возможность непрерывного контроля за ее функционированием в процессе нормальной эксплуатации. Вместе с тем безопасность турбоагрегата должна быть обеспечена и в самом неблагоприятном случае полного отказа системы регулирования, когда после сброса нагрузки регулирующие клапаны остаются максимально открытыми. Это и есть основная задача собственно защиты турбины от недопустимого повышения частоты вращения.
Импульсным органом системы защиты от разгона является автомат безопасности, бойки которого настраиваются на срабатывание при повышении частоты вращения на 11—12 % сверх номинального значения, т.е. при n = = 3330 … 3360 об/мин. После срабатывания автомата безопасности частота вращения еще заметно увеличивается из-за расширения пара, поступающего в турбину в процессе закрытия стопорных клапанов, а также аккумулированного в промежуточных ступенях турбины. Снижение уровня
262
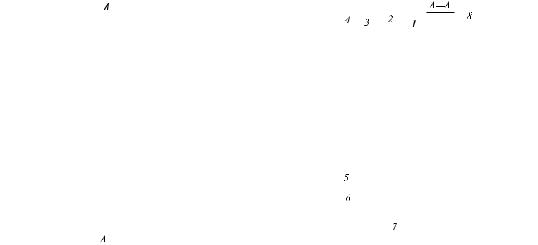
настройки срабатывания автомата безопасности уменьшает максимальное значение частоты вращения в переходном процессе, но делает затруднительным удержание турбины на холостом ходу с помощью системы регулирования. Срабатывание же автомата безопасности при сбросе нагрузки не позволяет судить о динамических качествах системы регулирования, об их изменении в процессе эксплуатации, что снижает ее надежность как первой линии защиты турбины от разгона.
На рис. 9.23 показана конструкция механического автомата безопасности с двумя кольцевыми бойками.
Автомат безопасности располагается на переднем конце вала турбины. С каждым кольцевым бойком резьбой жестко соединен стержень, направляемый втулками, закрепленными на валу автомата безопасности. В поперечной расточке вала находится пружина, которая через тарелку и стержень прижимает кольцо к валу.
Центр масс кольца и связанных с ним подвижных деталей (стержня, пружины, тарелки пружины, регулировочного винта) смещен относительно оси ротора в направлении возможного движения кольца. Благодаря этому при вращении на кольцо действует равнодействующая центробежных сил, стремящаяся преодолеть силу натяжения пружины, которая регулируется таким образом, чтобы срабатывание (выбивание) бойка произошло при частоте
вращения n = (1,11 … 1,12) n . Для повышения
0
надежности защиты автомат безопасности выполнен как неустойчивый регулятор частоты вращения. В этом случае, как только боек начнет двигаться, приращение центробежной силы будет превышать приращение натяжения пружины, что
гарантирует движение бойка до упора. После срабатывания внешняя поверхность кольца становится эксцентричной по отношению к оси ротора, что приводит к удару кольца по рычагу, передающему это воздействие на золотники автомата безопасности, перемещение которых вызывает быстрое закрытие всех парозапорных органов турбины.
Уровень срабатывания автомата безопасности настраивается вращением стержня, меняющего натяжение пружины (грубая настройка), или перемещением внутри стержня регулировочного винта, изменяющего эксцентриситет центра масс бойка в сборе (тонкая настройка).
При нормальных эксплуатационных режимах элементы системы защиты неподвижны, и поэтому нет твердой уверенности в их надежной работе при возникновении аварийной ситуации. Отсюда вытекает необходимость периодической проверки работоспособности всего канала защиты — от первичных датчиков (автомата безопасности) до исполнительных механизмов (сервомоторов стопорных клапанов).
Наиболее надежной является проверка автомата безопасности повышением частоты вращения до значений, при которых он срабатывает. Такая проверка по ПТЭ обязательна после разборки автомата безопасности, перед испытанием системы регулирования на сброс нагрузки и после длительного простоя (более 1 мес). Для испытания турбина должна быть полностью разгружена и отключена от сети.
Хотя проверка защиты турбины разгоном проводится в условиях, максимально приближенных к тем, в которых она должна сработать, высокие напряжения в роторе от центробежных сил, возрас-
Рис. 9.23. Автомат безопасности:
1 — кольцевой боек; 2 — стержень; 3, 5 — втулки; 4 — вал; 6 — пружина; 7 — регулировочный винт; 8 — камеры для масла
263
тающие во время испытаний более чем на 20 %, отрицательно сказываются на надежности и сроке службы деталей ротора, ухудшают его вибрационное состояние. Поэтому ПТЭ допускается кроме упомянутых выше случаев проверка защиты без увеличения частоты вращения. Она проводится на холостом ходу или даже при работе турбины под нагрузкой.
Для испытания автомата безопасности без повышения частоты вращения в бойках имеются камеры для масла, которое подводится к каждому бойку раздельно. Попадая в камеры, масло смещает центр масс бойка. Равнодействующая центробежных сил, действующих на боек, получает приращение, и он срабатывает при номинальной или даже более низкой частоте вращения. После прекращения подачи масла к бойку камеры дренируются через отверстия малого диаметра.
Для возможности проведения испытания автомата безопасности под нагрузкой необходимо, чтобы под действием пружин бойки возвращались в исходное (рабочее) положение при частоте вращения, несколько большей номинальной.
Испытание бойков при работе турбины под нагрузкой ведется поочередно, для чего испытуемый боек отключается от системы защиты смещением рычага. Во время испытания защита турбины от разгона осуществляется другим бойком.
Если защита турбины от недопустимого повышения частоты вращения воздействует непосредственно на золотники автомата безопасности, то остальные защиты используют датчики с электрическим выходным сигналом и логические устройства для формирования команды на отключение турбины, которая передается через электромагнитные выключатели.
Защита по осевому сдвигу. Возрастание осевого усилия до уровня, превышающего несущую способность упорного подшипника, приводит к выплавлению баббитовой заливки на колодках подшипника, сопровождающемуся осевым сдвигом ротора. При достижении им заданной уставки реле осевого сдвига (РОС) немедленно отключает турбину, чтобы не допустить тяжелого повреждения ее проточной части.
Следует отметить, что осевое перемещение ротора в пределах разбега в упорном подшипнике при изменении направления осевого усилия является совершенно нормальным. Чтобы исключить ложное срабатывание РОС и необоснованное отключение турбины, при выборе уставки реле приходится допустить некоторое выплавление баббитовой заливки колодок упорного подшипника и тем самым его повреждение. Важно успеть отключить турбину раньше, чем выберется минимальный
осевой зазор в проточной части, когда последствия аварии будут значительно более тяжелыми.
Защита по давлению в системе смазки. При падении давления в системе смазки до первого предела подается предупредительный сигнал, автоматически включаются резервный маслонасос переменного тока и аварийный маслонасос постоянного тока. Если это не приводит к восстановлению давления и оно продолжает падать, то при достижении второго предела защита отключает турбину. Масло
вподшипники при выбеге ротора подается из аварийных бачков, размещенных на крышках подшипников. Во избежание ложных отключений турбины при кратковременных провалах давления, например при переходе с рабочего на резервный насос смазки, сигнал на отключение турбины подается с выдержкой времени.
Защита по вакууму в конденсаторе. Тяжелым нарушением режима работы является глубокое падение вакуума в конденсаторе, сопровождающееся повышением температуры выходных патрубков ЦНД и в паровом пространстве конденсатора. При этом нарушается центровка, растет вибрация, возможно задевание в проточной части из-за относительного укорочения ротора, резко возрастают динамические напряжения в рабочих лопатках последней ступени, не исключено нарушение вальцовки трубок в трубных досках конденсатора.
При повышении абсолютного давления в конденсаторе до первого предела подается предупредительный сигнал, при достижении второго предела защита отключает турбину.
Защита турбины по температуре свежего пара. Резкое снижение температуры свежего пара приводит к высоким температурным напряжениям
вдеталях паровпуска, роторе и лопаточном аппарате, угрожает забросом влажного пара и даже воды в турбину. Поэтому при падении температуры до второго предела турбина отключается. Защита выводится из работы при пуске турбины на скользящих параметрах и при контролируемом расхолаживании, когда турбина выводится в ремонт.
Наряду с защитами собственно турбины предусмотрены так называемые локальные защиты вспомогательного оборудования турбоустановки (регенеративных и сетевых подогревателей, насосов и др.), нарушение режимов работы которого может иметь тяжелые последствия и для турбины. Рассмотрим одну из них.
Защита по уровню воды в ПВД. Среди причин, по которым может повыситься уровень воды
вПВД, наиболее вероятной и опасной является повреждение его трубной системы. Поступающая
впаровое пространство подогревателя питательная вода быстро заполнит его полностью. Если
264
обратный клапан на линии подвода пара к подогревателю не закроется, вода попадет в турбину, а если закроется — давление в корпусе подогревателя станет близким к давлению питательных насосов, которое значительно превышает расчетное для ПВД.
Защита действует следующим образом. При повышении уровня воды в любом из ПВД до первого предела выдается предупредительный сигнал. Если уровень воды достигнет второго предела, защита отключает всю группу ПВД по питательной воде и по пару, переводит питание котла на байпас
ПВД. Если подъем уровня и после этого не прекращается и он доходит до третьего предела, отключаются питательные насосы и энергоблок выводится из работы.
Сервомоторы стопорных клапанов как исполнительные органы системы защиты должны закрываться особенно быстро, причем закрываться даже при полном падении давления рабочей жидкости. Такими свойствами обладают только односторонние пружинные сервомоторы, которые всегда и выбираются для привода стопорных клапанов.
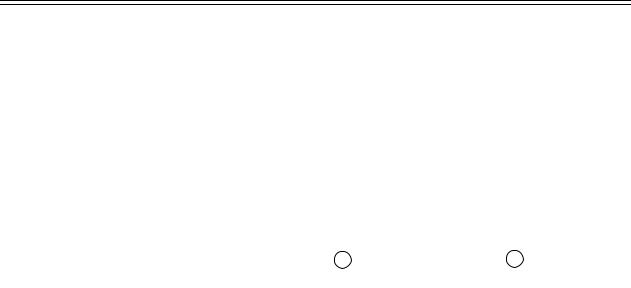
Глава десятая
СИСТЕМЫ МАСЛОСНАБЖЕНИЯ ТУРБИН
10.1. ЕДИНАЯ СИСТЕМА МАСЛОСНАБЖЕНИЯ
В течение длительного времени в системах регулирования турбин в качестве рабочей жидкости использовалось исключительно минеральное масло нефтяного происхождения, что давало возможность объединить маслоснабжение систем регулирования, защиты и смазки агрегата.
Минеральное масло как рабочая жидкость системы регулирования обладает ценными качествами: хорошей смазочной способностью, что облегчает достижение высокой чувствительности регулирования; оно не агрессивно и поэтому допускает применение обычных материалов; практически несжимаемо, чем определяется высокая скорость передачи сигналов по гидравлическим связям и др.
Система маслоснабжения в значительной мере определяет надежность работы турбины, так как даже кратковременное прекращение подачи масла к подшипникам может привести к выплавлению их баббитовой заливки и тяжелому повреждению турбины, а оставить без масла систему регулирования — значит потерять управление турбиной.
По соображениям надежности маслоснабжения длительное время в качестве главного масляного насоса (ГМН) турбины выбирался насос объемного типа: вначале зубчатый, а впоследствии винтовой, как имеющий большую подачу и экономичность. Во многом это связывалось с тем, что насосы объемного типа обладают ценным свойством самовсасывания и для них неопасно попадание воздуха в линию всасывания. Подача насоса объемного типа пропорциональна частоте вращения, и он не срывает маслоснабжение даже при очень низкой частоте вращения. Благодаря этому возможен безаварийный останов турбины при отказе всех вспомогательных масляных насосов. Принципиальная схема маслоснабжения турбины с насосом объемного типа приведена на рис. 10.1.
Наряду с достоинствами насосы объемного типа имеют и существенные недостатки. При тех расходах масла, которые необходимы в современных турбинах, по условиям кавитации насос приходится выполнять с пониженной частотой вращения
|
|
|
|
|
Рис. 10.1. Принципиальная схема маслоснабжения турбины
с главным масляным насосом объемного типа:
1 — главный масляный насос; 2 — редукторная передача; 3 —
масляный бак; 4 — система регулирования; 5 — редукционный
клапан; 6 — предохранительный клапан; 7 — маслосбрасываю-
щий клапан; 8 — маслоохладитель; 9 — пусковой масляный
насос высокого давления; 10 — аварийный масляный насос низ-
кого давления; 11 — обратный клапан; 12 — масло к подшипни-
кам
вала и соединять с ротором турбины с помощью редукторной передачи, как правило, зубчатой. Такая передача не только усложняет конструкцию блока переднего подшипника, но и, что более существенно, недостаточно надежна из-за высокой скорости в зацеплении и пульсации ротора на масляной пленке в подшипниках. Авария передачи, вызывающая остановку главного масляного насоса, может привести к тяжелым последствиям для турбины.
Кроме того, насос объемного типа имеет неблагоприятную характеристику (рис. 10.2), что особенно проявляется в переходных процессах регулирования. Теоретическая характеристика насоса вертикальна. Из-за неизбежных перетечек из напорной линии во всасывающую действительная характеристика слабопадающая, т.е. с ростом давления за насосом его подача несколько уменьшается. На установившихся режимах работы турбины гидравлическое сопротивление внешней сети насоса определяется практически постоянным расходом масла, идущего на смазку подшипников, и достаточно стабильным потреблением масла промежуточными сервомоторами с проточными золотниками. В сервомоторах с
266
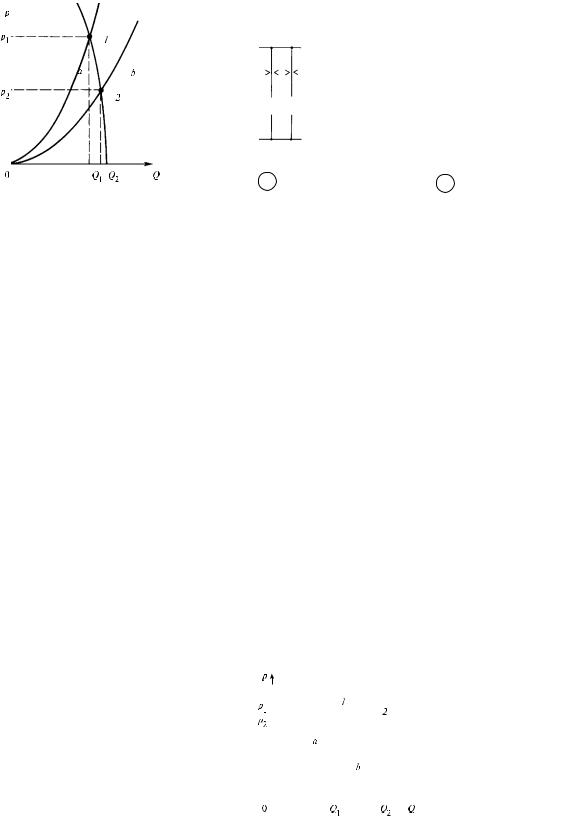
Рис. 10.2. Характеристика насоса объемного типа
отсечными золотниками покрываются только утечки масла. Характеристика внешней сети насоса в статике на рис. 10.2 изображена линией а с рабочей точкой 1, которая определяет развиваемое насосом давление р и подачу Q .
11
Впереходных процессах, когда при смещении отсечного золотника из среднего положения в сервомотор системы регулирования направляется большой поток масла, сопротивление внешней сети насоса резко падает (характеристика b на рис. 10.2), давление в напорной линии снижается до уровня
p |
при практически неизменной подаче Q |
Q . |
2 |
2 |
1 |
Такой глубокий провал давления масла в напорной линии системы регулирования в наиболее ответственный момент ее работы недопустим, поэтому приходится устанавливать редукционный клапан 5
(рис. 10.1), который поддерживает давление в системе регулирования, сокращая подачу масла в систему смазки, что компенсируется возрастающим сливом масла из главного сервомотора. Редукционные клапаны показали себя в эксплуатации недостаточно надежными. Колебания клапана при резких изменениях расхода масла приводили к заметным пульсациям напорного давления и к гидроударам, которые иногда влекли за собой повреждения маслопроводов и даже вызывали пожары. Если редукционный клапан после завершения переходного процесса не откроется, то давление в системе регулирования может существенно возрасти. Чтобы исключить эту опасность, приходится устанавливать предохранительный клапан 6. Давление масла, направляемого в систему смазки, поддерживается пружинным маслосбрасывающим клапаном 7.
Перечисленные и некоторые другие недостатки насосов объемного типа привели к тому, что в настоящее время они практически не используются в системах маслоснабжения турбин и заменены центробежными насосами.
|
|
|
|
|
|
|
|
|
|
|
|
|
|
|
|
|
|
|
|
|
|
|
|
|
|
|
Рис. 10.3. Принципиальная схема маслоснабжения турбины
с главным масляным насосом центробежного типа:
1 — главный масляный насос; 2 — инжектор первой ступени;
3 — масляный бак; 4 — система регулирования; 5 — инжектор второй ступени; 6 — обратные клапаны; 7 — маслоохладитель; 8 — пусковой масляный насос высокого давления;
9 — аварийный масляный насос низкого давления; 10 —
масло к подшипникам
Принципиальная схема маслоснабжения турбины с главным масляным насосом центробежного типа приведена на рис. 10.3. Центробежный насос
легко может быть выполнен быстроходным и поэтому соединяется непосредственно с валом турбины. Насос имеет благоприятную характеристику (рис. 10.4) и в динамике существенно увеличивает
подачу Q при незначительном падении давления
2
p по сравнению со значениями Q |
и p при уста- |
|
2 |
1 |
1 |
новившихся режимах работы. |
|
|
Так |
как давление, развиваемое |
центробежным |
насосом, пропорционально квадрату частоты вращения вала и плотности его рабочей жидкости, то насос не может эвакуировать воздух из всасывающей линии, т.е. не обладает свойством самовсасывания, и перед пуском должен быть заполнен перекачиваемой жидкостью. Естественно, нельзя допустить попадания воздуха во всасывающую полость насоса, так как в этом случае он прекратит
Рис. 10.4. Характери-
стика насоса центробеж-
ного типа
267
подачу жидкости. С этой целью во всасывающей линии поддерживается небольшое избыточное давление с помощью инжектора — струйного насоса, работающего на масле главного насоса и установленного ниже уровня масла в баке.
В одноинжекторных схемах давление масла за инжектором, выбираемое из потребностей системы смазки, превышает 0,1 МПа. Для предотвращения срыва насоса достаточно иметь значительно меньшее давление (около 0,03—0,05 МПа на уровне оси насоса). Так как КПД инжектора невысок, более экономичной оказывается двухинжекторная схема, в которой вторая ступень инжектора забирает часть масла после первой ступени и повышает его давление до уровня 0,1—0,15 МПа, необходимого для преодоления сопротивления маслоохладителей и коммуникаций системы смазки. Применение двух инжекторов вместо одного не снижает надежности маслоснабжения, так как в инжекторах нет движущихся частей, они просты по устройству и не требуют обслуживания.
Между инжектором второй ступени и подшипниками устанавливаются поверхностные маслоохладители, чтобы на всех режимах работы температура масла перед подшипниками не превышала 50 °С. Для того чтобы при нарушении плотности маслоохладителей вода не попадала в масляную систему, давление масла в маслоохладителях поддерживается выше давления воды. Предполагается, что утечка масла будет своевременно обнаружена эксплуатационным персоналом. Однако масло, попавшее в систему циркуляционного водоснабжения, загрязняет водоемы электростанции, нанося ущерб окружающей среде. Поэтому в настоящее время все чаще давление воды в маслоохладителях выбирается бóльшим, чем давление масла. Одновременно принимаются меры, направленные на повышение герметичности маслоохладителей.
Для создания давления в системе регулирования при пуске турбины предусмотрен пусковой масляный насос высокого давления 8 (рис. 10.3), который, кроме того, через инжектор заполняет маслом корпус главного насоса. По мере повышения частоты вращения турбины давление, развиваемое ГМН, растет, и, когда оно превысит давление за пусковым насосом, откроется обратный клапан 6 за ГМН. Начиная с этого момента маслоснабжение систем регулирования, защиты и смазки обеспечивается ГМН и пусковой насос, обратный клапан за которым закроется, может быть остановлен.
Падение давления в системе смазки приводит к автоматическому пуску вспомогательного масляного насоса низкого давления 9, подающего масло только к подшипникам и приводимого электродвигателем постоянного тока.
10.2. ПРОТИВОАВАРИЙНОЕ МАСЛОСНАБЖЕНИЕ ПОДШИПНИКОВ
Задачей системы смазки паровой турбины является надежная подача необходимого количества масла к подшипникам для того, чтобы:
• уменьшить потери мощности на трение
вподшипниках;
•предотвратить износ поверхностей трения;
•отвести теплоту, выделяющуюся при трении,
атакже передаваемую от горячих частей турбины.
Высокая надежность маслоснабжения в турбинах с докритическими параметрами пара в значительной мере обеспечивалась приводом главного масляного насоса от вала турбины. При реализации этого принципиального решения, подтвержденного мировым опытом эксплуатации в течение десятилетий, при проектировании мощных паровых турбин на сверхкритические параметры пара возникли серьезные трудности. С повышением давления масла в системе регулирования выросли размеры насосной группы, что усложнило компоновку ее в блоке переднего подшипника. Значительные осевые перемещения корпуса подшипника затруднили организацию самокомпенсации маслопроводов большого сечения. Возрастание объема масла в баке, расположенном непосредственно под передним подшипником турбины вблизи горячих паропроводов, усугубило пожарную опасность турбоустановки. Слабым элементом оказалась и зубчатая муфта привода насоса от вала турбины, а нарушение работы насоса требовало останова турбины.
Переход на независимый привод насосов смазки от электродвигателей стал возможным благодаря достаточно высокой надежности питания собственных нужд на современных мощных электростанциях. Снятие главного масляного насоса с вала турбины и переход к автономным насосам с электроприводом были ускорены применением различных жидкостей в системах регулирования (воды или огнестойкого синтетического масла) и смазки (минерального масла).
Применение независимого привода насосов смазки дает немалые преимущества:
•независимый привод насосов смазки в сочетании с 100 %-ным резервом позволяет ремонтировать любой из насосов без остановки турбины;
•можно удалить масляный бак от горячих элементов турбоустановки и разместить его на нулевой отметке, что существенно повышает пожаробезопасность;
•отпала необходимость в применении инжекторной группы для создания избыточного давления на всасывании ГМН и подачи масла на смазку;
•появилась возможность в исключительных случаях, например при пожаре, остановить насос
268
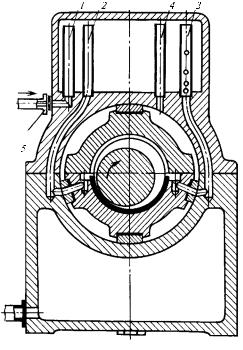
смазки, специальными мероприятиями обеспечив безаварийный останов турбины;
• можно выполнить централизованную систему смазки — главной турбины, всех питательных насосов и другого оборудования.
Отмеченные преимущества независимого привода насосов смазки могут быть реализованы только при условии, что будет обеспечено надежное маслоснабжение при переключениях насосов, а также в аварийных режимах — при потере питания собственных нужд.
Привод главного насоса от вала турбины надежнее автономного привода от электродвигателя из-за возможной потери напряжения в сети собственных нужд электростанции, хотя на этот случай в системе маслоснабжения подшипников предусматриваются аварийные масляные насосы с приводом от электродвигателей постоянного тока, питаемых от аккумуляторной батареи станции. Тем не менее надежность маслоснабжения подшипников оказывается несколько сниженной из-за невозможности мгновенно запустить двигатель насоса и падения напряжения на шинах аккумуляторной батареи при включении большой нагрузки (вместе с аварийными масляными насосами одновременно включаются и многие другие потребители аварийного резерва).
Задача резервирования маслоснабжения подшипников кардинально решается применением
противоаварийных емкостей — бачков, встроенных в крышки подшипников агрегата (рис. 10.5). Масло от насоса поступает в бачок, откуда по двум трубкам подводится к вкладышу подшипника. По одной из них масло подается при нормальной работе, когда бачок находится под давлением. При прекращении подачи масла от основных и аварийных насосов давление в бачке снижается до атмосферного и масло поступает в подшипник по другой трубке самотеком. Одновременно защита по падению давления в системе смазки отключает генератор от сети. Даже если бы турбина останавливалась со «срывом» вакуума и выбег ее не превышал 20 мин, подача номинального расхода масла в течение всего выбега потребовала бы слишком большого запаса масла в бачке. Исследования показали, что в этом нет необходимости и расход масла можно сокращать пропорционально снижению частоты вращения ротора.
Предложен простой и надежный способ программного регулирования расхода вытекающего масла. По высоте трубки выполняется несколько отверстий разного диаметра. В начале выбега масло в подшипник поступает через все отверстия и открытый верхний торец трубки. По мере опорожнения бачка уровень масла, а следовательно, и
269
Рис. 10.5. Подвод масла к опорному подшипнику через про-
тивоаварийную емкость:
1 — подача из напорного коллектора; 2 — подвод масла при
нормальной работе; 3 — аварийный подвод масла; 4 — воздуш-
ник; 5 — дозирующая шайба
напор снижаются и, кроме того, уменьшается число отверстий, через которые вытекает масло. Выбором расположения отверстий и значений их диаметров можно обеспечить требуемый закон подачи масла в подшипник. Чтобы поступление масла из бачка не прекратилось до его полного опорожнения, пространство над уровнем масла в бачке соединяется переливной трубой или воздушником с атмосферой.
10.3. ПОВЫШЕНИЕ ПОЖАРНОЙ БЕЗОПАСНОСТИ ТУРБИН
Применение минерального (нефтяного) масла в системах регулирования и защиты, а также для смазывания подшипников турбины и генератора таит в себе значительную потенциальную опасность возникновения пожара в турбоустановке. Это обусловлено тем, что температура самовоспламенения минерального масла (около 370 °С) значительно ниже температуры свежего пара и пара после промежуточного перегрева (540 °С). Полностью исключить возможность прорыва масла из трубопроводов и узлов систем регулирования и смазки практически невозможно. Попав на достаточно горячие детали турбоустановки, оно воспла-
менится. Такие пожары быстротечны и наносят значительный материальный ущерб, связанный с расходами на восстановление или ремонт поврежденного основного и вспомогательного оборудования, щитов управления и кабельных связей, строительных конструкций машинного зала, а также с недовыработкой электрической энергии и возможным ограничением ее для потребителей.
При проектировании, изготовлении и эксплуатации систем регулирования, защиты и смазки турбин всегда применяются те или иные традиционные мероприятия, повышающие пожарную безопасность:
•тщательный контроль маслопроводов, в частности просвечивание сварных швов гаммаили рентгеновскими лучами;
•испытание всех маслопроводов в сборе с узлами регулирования двойным рабочим давлением;
•снятие масляного насоса с вала турбины и переход к электроприводу, что позволяет удалить масляный бак от турбины;
•использование аварийного маслоснабжения подшипников, что дает возможность предотвратить развитие пожара отключением насосов.
Вместе с тем сосредоточить, как это раньше часто делалось, максимальное число узлов системы регулирования, работающих на масле высокого давления, в одном блоке, например в корпусе подшипника, в турбинах большой мощности с промежуточным перегревом пара и индивидуальными сервомоторами не удается.
Длительный опыт эксплуатации показал, что наиболее радикальным путем предотвращения загорания масла на электростанциях является замена минерального турбинного масла негорючими жидкостями — водой или синтетическим огнестойким маслом.
Привлекательность применения воды в системах регулирования обусловлена тем, что она является рабочим телом паротурбинной установки. Это открывает возможность существенно упростить систему питания и ее резервирование, так как могут быть использованы конденсатные и питательные насосы, другое оборудование турбоустановки.
В эксплуатируемых в настоящее время водяных системах регулирования мощных турбин ХТЗ и ТМЗ успешно разрешены многие трудные проблемы, обусловленные малой вязкостью воды и ее агрессивностью по отношению к материалам. Это позволило значительно уменьшить пожарную опасность турбоагрегатов. Однако при замене нефтяного масла на воду в подшипниках столкнулись со столь серьезными трудностями, что эти работы не получили пока промышленного распространения.
Другим направлением повышения пожарной
безопасности, получившим развитие в отечественной и мировой энергетике, является применение синтетических огнестойких масел.
Отечественное синтетическое огнестойкое
масло, разработанное ВТИ и получившее наименование ОМТИ (огнестойкое масло теплотехнического института), по многим физико-химическим свойствам близко к минеральному турбинному маслу, но некоторые их свойства существенно различаются, что должно учитываться при проектировании и эксплуатации систем регулирования и смазки.
Рассмотрим свойства ОМТИ, в большей или меньшей степени существенные для систем регули-
рования и смазки турбин.
Огнестойкость масла оценивается температурой самовоспламенения на воздухе, составляющей приблизительно 720 °С. Важно также, что ОМТИ не поддерживает горения при исчезновении источ-
ника открытого огня.
Смазывающие свойства масла характеризуются, в частности, его способностью обеспечивать малое трение без масляного клина (граничная смазка). Это качество особенно важно для систем регулирования, в которых не применяется гидравлическая самоцентровка золотников, в частности для систем регулирования турбин ЛМЗ. Смазывающие свойства ОМТИ лучше, чем минерального масла, поэтому специального подбора материалов
для трущихся пар не требуется.
Вязкость и зависимость ее от температуры у ОМТИ такие же, как у турбинного масла. Поэтому может быть использован богатый опыт проектирования и эксплуатации систем регулирования на
минеральном масле.
Теплоемкость ОМТИ в 1,5 раза меньше, чем теплоемкость минерального масла. При использовании ОМТИ в системе смазки, где отводится большое количество теплоты, такая особенность явля-
ется существенной.
Плотность ОМТИ в 1,3 раза выше, чем плотность
|
|
|
|
3 |
минерального масла |
(ρ |
= |
1,14 … 1,17 г/см , |
|
|
|
ОМТИ |
|
|
|
|
3 |
|
|
ρ |
= 0,87 … 0,89 |
г/см ), |
что |
учитывается при |
|
м.м |
|
|
|
выборе насосов регулирования. Повышенная плотность ОМТИ влияет также на выделение попавшей в масло воды, которая собирается на поверхности масла и испаряется. Затрудняется отделение механических примесей из-за уменьшения разницы
|
3 |
в плотностях (ρ |
= 1,3 … 1,5 г/см ). |
м.п |
|
Насыщаемость |
воздухом ОМТИ и минераль- |
ного масла примерно одинакова, однако средние размеры пузырьков воздуха в ОМТИ меньше и выделение его идет в несколько раз медленнее.
270