
Зорин В.М. Атомные электростанции
.pdfдок и условия эксплуатации оборудования, правил и должностных инструкций эксплуатационного персонала и т.п.
Конструкторские мероприятия реализуются при изготовлении устанавливаемого оборудования и направлены на обеспечение требуемых его характеристик (маневренности, например) при высокой эффективности локализуемых процессов.
Технологические мероприятия, как правило, суть результат функционирования вспомогательных систем.
Производство как технологический процесс или промышленное предприятие может быть опасным или неопасным. Опасным называется производство, на котором имеют место опасные факторы. Опасным считается производственный фактор, воздействие которого на работающего в определенных условиях (в спецодежде, например) приводит к травме или другому резкому ухудшению здоровья.
Тепловые электростанции, сжигающие органическое топливо, как
иАЭС, относятся к опасным производствам. Примеры опасных факторов на ТЭС: высокие температура и давление рабочего тела в большей части пароводяного тракта; горячие поверхности трубопроводов
иэлементов оборудования; применение токсичных (в системах регулирования турбины, например) и самовоспламеняющихся веществ (масел); возможность разрушения быстро вращающихся машин.
На атомных электростанциях ко всем опасным факторам, присущим ТЭС, добавляется опасность радиоактивного облучения персонала, а в случае аварии — опасность радиоактивного заражения окружающей среды и облучения населения, проживающего в зоне аварии.
Согласно Федеральному закону «О промышленной безопасности производственных объектов» аварией называются разрушение сооружения или технических устройств, применяемых на опасном производстве, неконтролируемый взрыв или выброс опасных веществ.
В ОПБ-88/97 [33] авария характеризуется применительно к атомным станциям (АС) как нарушение эксплуатации, при котором произошел выход радиоактивных веществ или ионизирующего излучения за предусмотренные проектом для нормальной эксплуатации границы в количествах, превышающих пределы безопасной эксплуатации. Таким образом, в результате аварии на АС создается непосредственная угроза причинения ущерба здоровью человека и окружающей среде.
Кроме пределов изменения контролируемых параметров в условиях нормальной эксплуатации устанавливаются пределы безопасной работы, выход за которые резко увеличивает вероятность аварии.
Слово «безопасность» равнозначно сочетанию «отсутствие опасности», т.е. безопасность любого технического объекта есть его спо-
461
собность выполнять свои функции без причинения какого-либо ущерба здоровью обслуживающего персонала, населению, а также окружающей среде.
Безопасность атомной станции, ядерная и радиационная, есть ее
свойство при нормальной эксплуатации и нарушении нормальной эксплуатации, включая аварии, ограничивать радиационное воздействие на персонал, население и окружающую среду установленными пределами [33].
Основные задачи обеспечения безопасности АС — предотвращение аварий и ограничение их последствий, если авария произошла. Чтобы обеспечить безопасность любого производства, нужны дополнительные технические решения (кроме направленных на реализацию основного технологического процесса), которые оказывают влияние на функциональные свойства производства — экономичность и надежность. Эти свойства определяют важнейшие характеристики выпускаемой продукции — ее стоимость и бесперебойность поставки потребителям.
Безопасность — это специфическая характеристика опасного производства, прямо не связанная с характеристиками его продукции. Теоретически можно представить объект, бесперебойно выпускающий недорогую продукцию, но наносящий ущерб окружению. Безопасность — это проявление заботы общества об обслуживающем персонале, населении, окружающей среде. В то же время обеспечение безопасности влияет на функциональные свойства объекта.
Чтобы сделать объект более безопасным, нужны дополнительные средства, т.е. его экономичность падает.
Надежность и безопасность не являются независимыми друг от друга характеристиками. Это можно подтвердить, рассматривая безаварийность как условие безопасности и безотказность как компонент надежности. Методы достижения этих характеристик различны. Обеспечение безотказности, иначе — наработки объектом определенного времени до отказа, — задача материаловедческая, в которой учитываются свойства конструкционного материала, зависящие и от случайных факторов, определяющих его состав и структуру, свойства локализуемой рабочей среды, процессы взаимодействия среды и материала, режимы работы объекта. Снижение вероятности аварии — это задача, прежде всего, системного анализа, при решении которой в наиболее полной мере (по сравнению с задачей наработки до отказа) учитываются все взаимосвязи как компонентов объекта, так и объекта с окружением. Ограничение последствий аварии — специфическая задача обеспечения безопасности. Нетрудно видеть, что обеспечение безопасности (уменьшение вероятности аварии и ограничение ее последствий) всегда положительно влияет на надежность
462
объекта. Именно поэтому безопасность нередко рассматривается как одна из составных частей надежности [5].
Безопасность технического объекта так же, как и условия нормальной эксплуатации, обеспечивается системой организационных, конструкторских и технологических мероприятий.
Корганизационным мероприятиям относятся федеральные законы (например, закон «О промышленной безопасности производственных объектов»), иные нормативные правовые акты Российской Федерации, а также нормативные технические документы, устанавливающие правила ведения работ на опасном производственном объекте.
Кконструкторским мероприятиям относятся технические решения, реализуемые в конструкции объекта или его составных частей.
Вкачестве примера назовем создание ряда последовательных барьеров на пути возможного выхода радиоактивных веществ.
Ктехнологическим мероприятиям относятся специальные системы (системы безопасности), воздействующие на объект при появлении признаков возможной аварии в целях ее предотвращения, а в случае аварии — в целях ограничения ее последствий.
В данном разделе основное внимание уделено лишь тем из вспомогательных технологических систем, которые непосредственно связаны с потоками теплоносителя или рабочего тела в пределах реакторной установки АЭС.
463

Глава 24
ВСПОМОГАТЕЛЬНЫЕ СИСТЕМЫ НОРМАЛЬНОЙ
ЭКСПЛУАТАЦИИ РЕАКТОРНОЙ УСТАНОВКИ
С ВВЭР-1000
Проектирование реакторной установки, как и другой основной технологической установки АЭС (ПТУ, НПЧ), начинают с принципиальной тепловой схемы при известном типе реактора и заданной его мощности. Принципиальная тепловая схема (рис. 24.1) отражает существо основного технологического процесса в РУ: нагрев теплоносителя в реакторе, его движение от реактора к парогенератору, передача теплоты в ПГ рабочему телу ПТУ, возврат теплоносителя в реактор с помощью циркуляционного насоса. О расчете параметров теплоносителя и рабочего тела в реакторе и парогенераторе, включая их расходы, излагалось в гл. 10. После разработки принципиальной схемы рассматриваются способы поддержания требуемых значений параметров в контуре теплоносителя, требования к его химическому составу, к массовому заполнению теплоносителем контура и его (теплоносителя) материальный баланс с учетом вводимых и выводимых из контура расходов во всех возможных режимах работы РУ: заполнение и дренирование контура; разогрев и расхолаживание; переход с одного уровня мощности на другой; стационарные режимы — минимального контролируемого уровня мощности
9
|
4 |
6 |
|
5 |
|
1 |
|
|
|
|
10
87
3
2
Рис. 24.1. Принципиальная тепловая схема двухконтурной паропроизводительной установки:
1 — ядерный реактор; 2 — активная зона; 3 — напорная (нижняя) камера; 4 — верхняя смесительная камера; 5 — горячая нитка главного циркуляционного трубопровода (ГЦТ); 6 — парогенератор; 7 — ГЦН; 8 — холодная нитка ГЦТ; 9 — пар к турбине; 10 — питательная вода от ПТУ
464
(МКУ), обеспечения собственных нужд энергоблока, номинальной мощности и частичных нагрузок. Удовлетворение этих требований приводит к необходимости установки вспомогательного оборудования, соединенного трубопроводами с основным контуром циркуляции теплоносителя. Объединенные определенным назначением элементы вспомогательного оборудования (теплообменники, насосы, баки), трубопроводы, арматура образуют вспомогательную систему РУ. Исходя из требований к вспомогательной системе рассчитываются ее характеристики — расходы теплоносителя в различных режимах работы РУ, подводимые или отводимые мощности, определяются условия работы оборудования, трубопроводов, арматуры. Удовлетворение всех требований к теплоносителю, поддержание значений его параметров в заданных пределах в любых режимах (кроме аварийных) суть нормальные условия эксплуатации РУ, а вспомогательные технологические системы, обеспечивающие выполнение этих требований, называются вспомогательными системами нормальной эксплуатации (ВСНЭ). Основное назначение этих систем — поддержание нормальных условий эксплуатации, а в случае их нарушений (выхода контролируемых параметров за установленные пределы) — обеспечение возврата к нормальным условиям.
Энергоблок с ВВЭР-1000 (реакторная установка В-320) принят в качестве базового в Стратегии развития атомной энергетики РФ. Это обусловлено длительной проверкой и доводкой основных технических решений в процессе эксплуатации многих энергоблоков, в том числе и блоков с ВВЭР меньшей мощности. Именно поэтому здесь прежде всего будут рассмотрены ВСНЭ реакторной установки с ВВЭР-1000. В табл. 10.1 приведены основные параметры паропроизводительных установок с ВВЭР, которые будут полезны при ознакомлении с характеристиками вспомогательных систем.
24.1. Система компенсации давления
Первый контур теплоносителя на АЭС с ВВЭР-1000 включает в себя ядерный реактор и подключенные к нему четыре петли, в каждую из которых входят главные циркуляционные трубопроводы (ГЦТ) с диаметром и толщиной стенки 990×70 мм, главный циркуляционный насос, коллекторы теплоносителя и внутренний объем труб теплообменной поверхности парогенератора. Объем первого контура [без компенсатора давления (КД), который будет рассмотрен далее]
3
составляет примерно 280 м . Заполняется он водой, т.е. практически несжимаемой средой. При разогреве контура от холодного (от темпе-
ратуры ниже 70 °C) до горячего (t = 306 °C; р = 15,7 МПа) состояния
ср
объем воды увеличивается почти на 37 %, т.е. в горячем состоянии
3
более 100 м воды оказывается «лишней». При изменении темпера-
465
туры теплоносителя в контуре на 1 °С (от 305 до 306 °С) изменение его объема при постоянном давлении будет равно примерно 0,3 %
3
(0,85 м ). Если при увеличении температуры на 1 °С объем теплоносителя оставить прежним, то давление увеличится на 1 МПа (на 6,5 %). Эти примеры показывают необходимость поддержания давления и объема практически несжимаемой среды в замкнутом контуре. Цель может быть достигнута двумя способами. Первый — применение устройства, демпфирующего изменение давления. В качестве демпфирующей среды используют либо газ, либо пар той же жидкости, которая заполняет контур. Второй способ — применение системы с насосом, подкачивающим жидкость в контур, и с регулирующим дроссельным клапаном, через который избыток жидкости сбрасывается из контура. Очевидно, что второй способ — более сложный, менее экономичный и надежный. На отечественных АЭС с ВВЭР применяются паровые компенсаторы давления.
Система компенсации давления РУ с ВВЭР-1000 предназначена:
1)для создания и поддержания давления в первом контуре в заданных пределах в стационарных режимах;
2)для ограничения отклонений давления в переходных и аварийных режимах;
3)для недопущения кипения теплоносителя в первом контуре (за исключением поверхностного кипения воды в активной зоне) в следующих режимах:
• плановых изменений мощности в пределах от нагрузки собственных нужд (СН) до максимальной (предусмотренной проектом)
всторону как увеличения, так и уменьшения;
•отключения одного или двух ГЦН без срабатывания аварийной защиты (АЗ) реактора;
•сброса нагрузки турбогенератором до уровня СН без срабатывания АЗ реактора; при сбросе нагрузки от номинального уровня система получает максимальное положительное возмущение по скорости возрастания объема теплоносителя и его полному изменению;
•срабатывания АЗ реактора; в случае работы блока на номинальной мощности система получает максимальное отрицательное объемное возмущение вследствие резкого снижения температуры теплоносителя из-за падения тепловыделения в реакторе при сохранении теплоотвода в парогенераторе.
Пределы изменения давления в первом контуре при нормальной
2
работе системы составляют 11,8—17,7 МПа (120—180 кгс/см ), что соответствует температуре насыщения воды 323—355 °С.
Схема системы компенсации давления представлена на рис. 24.2. Основным ее элементом является компенсатор давления (рис. 24.3). Он представляет собой толстостенный вертикальный цилиндриче-
466
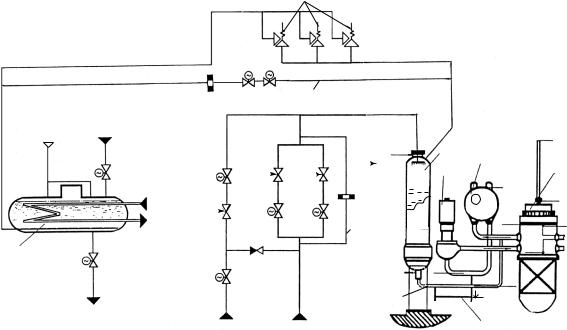
10
467
11
¾219ç20
13 |
14 |
|
|
|
|
|
|
|
|
|
|
|
|
|
|
|
|
|
|
¾135ç14 |
15917 ¾ç |
2,5 ç |
|
|
|
|
|
|
|
|
|
||||||||
|
|
|
|
|
|
|
|
|
4 |
||||||||||
|
|
|
|
|
|
|
|
|
34,86 |
|
|
|
|
|
|||||
|
|
|
|
|
|
|
|
|
|
18 |
|
|
|
|
|
|
|
|
3 |
|
|
|
|
|
|
|
|
|
|
|
|
|
|
|
|
|
|
||
|
15 |
|
|
|
|
|
|
|
¾ |
|
|
|
|
|
|
|
|
|
|
|
|
|
|
|
|
|
|
|
|
|
|
|
|
|
|
|
|
||
|
|
|
|
|
|
|
|
|
|
|
|
|
|
|
|
|
|
||
|
|
|
|
|
|
|
|
|
|
|
|
|
|
|
|
|
|
||
|
|
|
|
|
|
|
|
|
|
|
|
|
|
|
|
|
|
||
|
|
|
|
|
|
|
|
|
|
|
|
|
|
|
|
|
|||
|
|
26,4 |
|
|
|
|
|
|
9 |
|
|
|
|
|
|
|
|
|
12
20,62
5 ~
16
78
34,31
2
1
31,89
30,24
27,55 27,34
22,71
~19,34 20,14
6
Рис. 24.2. Система компенсации давления первого контура:
1 — реактор; 2 — парогенератор; 3 — главный циркуляционный насос; 4 — компенсатор давления; 5 — «дыхательный» трубопровод;
6 — трубопровод связи дренажа КД с дренажом «холодной» нитки 4-й петли; 7 — вода от насоса подпитки первого контура; 8 — вода с напора ГЦН 1-й петли; 9 — байпасная линия с дроссельной шайбой; 10 — импульсно-предохранительные устройства; 11 — байпасная линия переходных режимов; 12 — бак-барботер; 13 — подвод азота; 14 — подвод дистиллята; 15 — охлаждающая вода промконтура;
16 — дренаж в систему организованных протечек; показаны диаметры основных трубопроводов системы, мм, и высотные отметки основного оборудования РУ, м
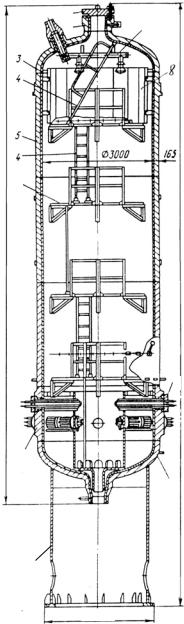
2
|
|
|
|
|
1 |
|
|
|
9 |
|
|
|
|
|
|
|
|
|
|
|
|
|
|
||
|
|
|
|
|
|
|
|
|
|
|
|
|
|
|
|
|
|
|
|
|
|
||||
3 |
|
|
|
|
|
|
|
|||||
|
|
|
|
|
|
|
|
|
|
|
8 |
|
|
|
4 |
|
|
|
|
||||||
|
|
|
|
|
|
|
|
|
||||
|
|
|
|
|
|
|
|
|
|
|
|
|
|
|
5 |
|
|
|
|
|
|
|
|||
|
|
|
|
|
|
|
|
|
|
|||
|
|
|
|
|
|
|
|
165 |
||||
|
|
|
|
|
3000 |
|
||||||
4 |
||||||||||||
|
|
|
|
|
|
|
|
|
|
|||
|
|
|
|
|
|
|
|
|
|
|||
10 |
|
|
|
|
|
|
|
13 490
16 270
7
6
3
11
2970
Рис. 24.3. Компенсатор давления:
1 — горловина; 2 — крышка; 3 — днище; 4 — лестница; 5 — корпус; 6 — обечайка блоков ТЭН; 7 — блок ТЭН; 8 — экран; 9 — коллектор впрыскивающих форсунок;
10 — площадка обслуживания; 11 — опора
468
ский сосуд с эллиптическими днищами. Корпус и днища изготовлены из низколегированной стали 10ГН2МФА. В нижней части корпуса по его окружности в два ряда установлены 28 блоков термоэлектронагревателей (ТЭН) общей мощностью 2520 кВт. К штуцеру в нижнем днище приварен «дыхательный» трубопровод, по которому вода может перетекать из первого контура в КД или в обратном направлении. Трубопровод подсоединен к горячей нитке (к главному циркуляционному трубопроводу с теплоносителем, идущим от реактора) 4-й петли. Такое подсоединение КД объясняется стремлением обеспечить возможно меньшую разность температур воды в КД, находящейся в состоянии насыщения при температуре 346 °С, и воды, поступающей в него из первого контура (температура в горячей нитке 320 °С).
При работе в стационарном режиме водообмен между КД и первым контуром практически отсутствует, вода в «дыхательном» трубопроводе не движется, и за счет теплообмена с окружающим воздухом ее температура может значительно снизиться. Поступление такой воды в КД привело бы к значительным термическим напряжениям металла корпуса, нижнего днища и штуцера КД. Чтобы не допустить этого, организована постоянная циркуляция теплоносителя в «дыхательном» трубопроводе. Для этого перемычкой соединены отводы, предназначенные для дренажей КД и первого контура (см. рис. 24.2). Циркуляция происходит по замкнутому контуру: горячая нитка ГЦТ — «дыхательный» трубопровод — дренажный отвод КД — трубопровод связи (перемычка) — дренажный трубопровод 4-й петли — всас ГЦН4 — реактор — горячая нитка ГЦТ.
Движущей силой в контуре является напор ГЦН.
Работа системы КД происходит следующим образом.
При пуске энергоблока после заполнения первого контура водой в
нем повышается давление, которое создается паровой подушкой, образующейся в верхней части КД при кипении в нем воды. Кипение происходит в результате подвода теплоты от электронагревателей. В установившемся режиме давление поддерживается с помощью регулируемого подогрева: включается или отключается часть ТЭН для поддержания температуры на уровне 346 °С. В нормальном стационарном режиме в КД поддерживается также постоянный уровень воды изменением подачи подпиточного насоса системы продувкиподпитки первого контура (см. § 24.2). При этом объем воды в КД
3 3
составляет 55 м , а объем пара — 24 м .
При изменении средней температуры теплоносителя первого контура в переходных режимах, обусловленных изменением мощности блока или нарушениями в работе оборудования, часть его перетекает из КД в контур или из контура в КД по «дыхательному» трубопро-
469
воду. При этом ограничение отклонений давления достигается за счет сжатия или расширения паровой подушки в КД. При уменьшении давления вода оказывается перегретой, частично испаряется, уменьшая тем самым возможное расширение пара и способствуя восстановлению давления. При росте давления пар сжимается, частично конденсируется на поверхности воды, которая оказывается недогретой до состояния насыщения, и рост давления замедляется.
Для конденсации пара в паровой подушке и восстановления давления при его увеличении предусмотрена система впрыска воды, температура которой ниже температуры насыщения. Обычно берется охлажденная в парогенераторе вода после ГЦН 1-й петли. Необходимый расход воды на впрыск устанавливается регулирующими клапанами (см. рис. 24.2). По параллельно установленному трубопроводу меньшего диаметра без арматуры и с дроссельной шайбой организуется постоянный проток воды на впрыск. Он необходим для поддержания трубопровода и штуцера впрыска, расположенного на корпусе КД, в разогретом состоянии и для постоянного выравнивания концентрации борной кислоты в первом контуре и в компенсаторе давления. В режимах расхолаживания, когда для поддержания нужной скорости уменьшения температуры и давления в первом контуре впрыск воды с напора ГЦН оказывается неэффективным, используется вода от насоса подпитки, температура которой ниже. Чтобы относительно холодная вода не попадала на стенки корпуса КД, вызывая тем самым температурные напряжения в металле, внутри корпуса установлен металлический экран (см. рис. 24.3).
При значительном положительном возмущении по давлению срабатывают одно, два или три импульсно-предохранительных устройства (ИПУ), каждое из которых настроено на все возрастающее давление, и избыточный объем теплоносителя первого контура в виде пароводяной смеси сбрасывается в бак-барботер (ББ). Для отвода парогазовой смеси из КД в режиме разогрева первого контура предусмотрена байпасная линия с двумя запорными задвижками и дроссельной шайбой, ограничивающей расход парогазовой смеси. Избыточный объем воды, образующийся в режиме разогрева, сливается через дренажную линию в дренажный бак системы организованных протечек (см. рис. 24.8).
Входящий в систему бак-барботер (рис. 24.4) предназначен для приема пара, парогазовой или паровоздушной смеси в нормальных условиях эксплуатации и в аварийных режимах. Его основные технические характеристики следующие:
• объем дистиллята или химочищенной воды в межтрубном про-
странстве — 20 м3;
2
• площадь теплообменной поверхности — 35 м ;
470