
2594
.pdf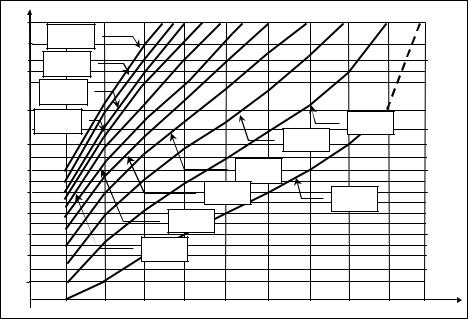
Территориально-разнесенный прием сигналов
Для увеличения КИД системы связи и снижения мощности передатчиков целесообразно использовать территориально-разнесенный прием сигналов. Для этого дополнительные приемные центры должны быть расположены на расстоянии 100-500 км. от базового ретранслятора [4]. В этом случае осуществляется декорреляция на индивидуальных приемных центрах замираний и станционных помех, попадающих в полосу частот, в которой передается сообщение.
Если условия связи обеспечивают вероятность передачи сообщения Р1 от абонента в сторону базового ретранслятора, тогда вероятность неприема сообщения Р0 равна:
|
|
Р0 = 1 – Р1 |
|
(1) |
Если считать, что условия приема сигналов от абонента во всей |
||||
области |
расположения |
дополнительных |
приемных |
центров |
приблизительно одинаковые (но взаимно независимые), то с учетом (1) вероятность Р0(1+N) одновременного неприема сообщения ретранслятором и всеми N дополнительными приемными центрами будет равна
Р0(1+N) = (1 – P1)N+1 |
(2) |
Из (2) следует, что вероятность Р1(1+N) приема сообщения хотя бы |
|
одним приемным центром из N или ретранслятором будет равна: |
|
Р1(1+N) = 1– P0(1+N) = 1 – (1 – P1)N+1 |
(3) |
На рисунке 3 приведена зависимость КИД канала связи с N дополнительными т-разнесенными приемными центрами от КИД канала связи без дополнительных приемных центров.
99 |
Н(1+N)% |
|
|
|
|
|
|
|
|
|
N=10 |
|
|
|
|
|
|
|
|
|
|
98 |
|
|
|
|
|
|
|
|
|
|
|
|
|
|
|
|
|
|
|
|
|
97 |
N=9 |
|
|
|
|
|
|
|
|
|
96 |
|
|
|
|
|
|
|
|
|
|
95 |
N=8 |
|
|
|
|
|
|
|
|
|
|
|
|
|
|
|
|
|
|
|
|
90 |
N=7 |
|
|
|
|
|
|
|
N=1 |
|
|
|
|
|
|
|
|
|
|
||
80 |
|
|
|
|
|
|
N=2 |
|
|
|
70 |
|
|
|
|
|
N=3 |
|
|
|
|
60 |
|
|
|
|
N=4 |
|
|
|
N=0 |
|
|
|
|
|
|
|
|
|
|
||
|
|
|
|
|
|
|
|
|
|
|
50 |
|
|
|
N=5 |
|
|
|
|
|
|
|
|
|
|
|
|
|
|
|
|
|
40 |
|
|
|
N=6 |
|
|
|
|
|
|
30 |
|
|
|
|
|
|
|
|
|
|
|
|
|
|
|
|
|
|
|
|
|
20 |
|
|
|
|
|
|
|
|
|
|
0 |
10 |
20 |
30 |
40 |
50 |
60 |
70 |
80 |
90 |
100 Н1% |
Рис. 3. Зависимость КИД канала связи сN дополнительными территориально-разнесенными |
||||||||||
приемными центрамиот КИД канала связибез дополнительныхприемных центров |
20
Сравнивая кривые надежности, изображенные на рисунке 2, соответствующие 50% и 99% видно, что для перехода с первой кривой надежности на вторую нужно увеличить мощность передатчика 43 дБ. Этот переход, без увеличения мощности, можно осуществить, применив шесть дополнительных приемных центров.
Вывод:
Благодаря использованию всех выше перечисленных средств повышения КИД КВ канала связи становится возможным создание эффективной КВ сети связи для контроля технического состояния транспортных средств и получения диспетчером их координат, определенных с помощью навигационных спутниковых систем. ГЛОНАСС/ GPS.
Библиографический список
1.Хазан В.Л. Математические модели дискретных каналов связи декаметрового диапазона радиоволн: - Омск ОмГТУ, 1998. – 106с.
2.Коноплева Е.Н. О расчете надежности радиосвязи на коротких волнах. // Электросвязь. – 1967. - № 11. – С. 36-38.
3.Хазан В. Л. Система декаметровой мобильной автоматической радиосвязи "МАРС" //Техника радиосвязи. 1998. Вып. 4. 59-66 с.
4.Хазан В.Л., Федосов Д.В., Майстренко В.В. Особенности построения и функционирования мобильных КВ сетей связи // Научно-технические ведомости
СПбГТУ. – 2008. №6. С. 38-48.
УДК 621.75. 828: 621
ЛАЗЕРНАЯ ОБРАБОТКА ДЕТАЛЕЙ ДВИГАТЕЛЕЙ
АВТОМОБИЛЬНОЙ ТЕХНИКИ
А.А. Соловьев, канд. ф-м. наук, проф.; Е.В. Шлякова, канд. техн. наук* Сибирская государственная автомобильно-дорожная академия
*Омский танковый инженерный институт
Проблема повышения стойкости к коррозионному разрушению касается автомобильной техники техники, находящейся и в условиях постоянной эксплуатации, и на хранении. После длительного хранения техники 65 - 80% неисправностей обусловлены коррозией и старением деталей, причем 30 - 40% таких неисправностей вызывают вынужденные остановки машин в пути, например во время эксплуатации в условиях Крайнего Севера. Поэтому защита узлов и деталей автомобильной техники от коррозии и повышение их износостойкости отнесена к основным направлениям научно-технического прогресса.
21
Химическая стойкость конструкционных металлических материалов, используемых в производстве и ремонте техники, зависит от природы, состава и структуры самого материала, от состава технологической среды
игидродинамических условий эксплуатации изделий.
Вдвигателях внутреннего сгорания наиболее подвержены коррозии гильзы цилиндров. Уже через 15-20 дней после остановки двигателя на рабочих поверхностях гильз появляются следы коррозии в виде небольших пятен. Через несколько месяцев коррозией поражается значительная часть поверхности гильз.
Продукты коррозии выступают над поверхностью стенок гильз и при последующем запуске срезаются поршневыми кольцами. Происходит интенсивный износ гильз цилиндров и поршневых колец, в результате чего снижается мощность двигателя, увеличивается расход топлива и масла, сокращается межремонтный срок службы.
Основной причиной коррозии гильз цилиндров являются продукты сгорания топлива, в котором содержится до 0,2% сернистых соединений. Образуются оксиды серы, которые, соединяясь с парами воды из отработавших газов, превращаются в серную и сернистую кислоты. На стенках гильз цилиндров серная кислота конденсируется во время работы двигателя при пониженном тепловом состоянии и небольших оборотах коленчатого вала.
Гильзы двигателей большой мощности выполняются из азотированной стали 35ХЮА, 35ХМЮА, 38ХМЮА с присадкой алюминия. Азотирование и термическая обработка гильзы значительно повышают твердость внутренней поверхности и уменьшают износ гильзы.
Перспективным представляется использование лазерного излучения для обработки поверхности металлов, что приводит повышению коррозионной стойкости, твердости, износо- и теплостойкости. Поэтому значительный научно-прикладной интерес представляет изучение коррозионной стойкости поверхности гильз цилиндров двигателя
внутреннего сгорания, обработанных лазерным лучом с целью исследования возможности замены традиционного длительного и трудоемкого процесса азотирования на быстрый и эффективный метод лазерной обработки.
Рассматривалось влияние лазерного излучения на повышение коррозионной стойкости гильз цилиндров и клапанов двигателя внутреннего сгорания. Было изготовлено 30 образцов стали 38Х2МЮА площадью 4 см2, которые подготавливались к коррозионным испытаниям по стандартным методикам.
25 образцов стали 38Х2МЮА подвергалась облучению на лазерной технологической установке ЛТУ-2М.
22

Режимы обработки:
1)плотность мощности q1 = 2 · 104 Вт/см2; q2 = 3 · 104 Вт/см2; q3 = 5 · 104 Вт/см2; q4 = 7 · 104 Вт/см2; q5 = 9 · 104 Вт/см2.
2)длительность импульса лазерного излучения =1,5 10-3 с;
3)коэффициент перекрытия 50%.
В качестве электролита для коррозионных испытаний использовался 4н раствор серной кислоты. Выбор электролита обусловлен тем, что при сгорании дизельного топлива, содержащего серу, образуются оксиды серы (IV) и (VI), которые частично превращаются в сернистую и серную кислоты. Таким образом, данный раствор электролита моделирует агрессивную среду, возникающую в реальных условиях эксплуатации двигателей внутреннего сгорания. После выдержки в электролите от двух до восьми часов скорость коррозии образцов вычислялась весовым методом. Потеря массы в единицу времени, отнесенная к единице поверхности, позволяет определить скорость коррозии:
P m/ S |
(1) |
где Р – скорость коррозии, мг/ дм2 · час; ∆m – изменение массы, г; S – площадь поверхности образца, дм2; τ – время испытания, час.
Защитное действие лазерного облучения рассчитывается по формуле:
Z н o 100%
н
где Z – эффективность защиты, %;
ρн – скорость коррозии в необлученных образцах; ρо – скорость коррозии облученных образцов.
По результатам испытаний построен график зависимости скорости коррозии стали 38Х2МЮА в кислой среде от плотности мощности лазерного излучения.
|
|
|
|
Таблица 1 |
|
|
Результаты весового анализа образцов из стали 38Х2МЮА |
||||
|
|
|
|
|
|
№ |
q, |
Δmср., г |
ρ, |
Z, % |
|
п/п |
Вт/см2 |
|
г/см2 · час |
|
|
1 |
- |
0,0249±0,00296 |
0,00415 ± 0,00049 |
- |
|
2 |
2 · 104 |
0,00972±0,00041 |
0,00162 ± 0,00006 |
60,96 |
|
3 |
3 · 104 |
0,00708±0,00035 |
0,00118 ± 0,00005 |
71,57 |
|
4 |
5 · 104 |
0,00664±0,00037 |
0,00111 ± 0,00006 |
73,25 |
|
5 |
7 · 104 |
0,00816±0,00039 |
0,00136 ± 0,00006 |
67,23 |
|
6 |
9 · 104 |
0,00844±0,00039 |
0,00141 ± 0,00006 |
66,02 |
|
Очевидно, что лазерная обработка повышает коррозионную стойкость стали 38Х2МЮА. При плотности мощности лазерного излучения 5 · 104 Вт/см2 скорость коррозии снижается в ~ 3,74 раза. Эффективность лазерной
23
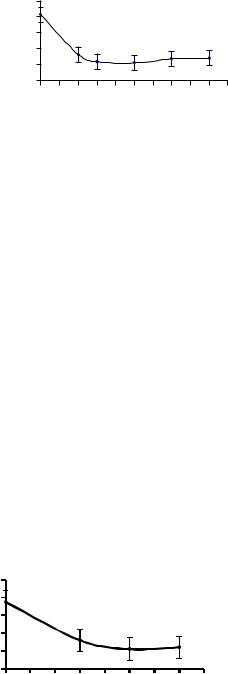
обработки как способа защиты поверхности стали 38Х2МЮА от коррозионного разрушения достаточно высока, наибольшая степень защиты
(Z) достигается при плотности мощностиизлучения 5 · 104 Вт/см2– 73,25%.
р, |
0,005 |
|
|
|
|
|
|
|
|
|
|
г/см2 . час |
0,004 |
|
|
|
|
|
|
|
|
|
|
|
0,003 |
|
|
|
|
|
|
|
|
|
|
|
0,002 |
|
|
|
|
|
|
|
|
|
|
|
0,001 |
|
|
|
|
|
|
|
|
|
|
|
0 |
|
|
|
|
|
|
|
|
|
|
|
0 |
1 |
2 |
3 |
4 |
5 |
6 |
7 |
8 |
9 |
10 |
|
|
|
|
q . 104, Вт/см2 |
|
|
|
|
Рис. 1. Зависимость скорости коррозии стали 38Х2МЮА от плотности мощности лазерного излучения
Таким образом, лазерное облучение способствует повышению коррозионной стойкости легированной стали 38Х2МЮА. Эффективность защиты определяется плотностью мощности лазерного излучения.
С целью подтверждения результатов исследования скорости коррозии весовым методом образцы стали 38Х2МЮА были подвергнуты электрохимическим испытаниям. Определение коррозионной стойкости стали проводилось электрохимическим способом методом построения потенциостатических поляризационных кривых. Поляризация осуществлялась с помощью потенциостата П-5827М в стационарной ячейке ЯСЭ-2 при температуре 250С. Электролитом служил 4н раствор серной кислоты.
Поляризация начиналась через 10-15 минут после погружения образца и установления стационарного потенциала. Катодная и анодная ветви устанавливались в прямом направлении от стационарного потенциала последовательно, не вынимая образца из раствора. Выдержка при каждом заданном потенциале составляла три минуты, после чего фиксировалось значение тока. Результаты показаны на рис.2.
i, мА/см2 1 0,8
0,6
0,4
0,2
0
0 1 2 3 4 5 6 7 8 q . 104, Вт/см2
Рис.2. Зависимость плотности тока коррозии от плотности мощности лазерного излучения
24
По результатам электрохимических исследований скорости коррозии можно сделать следующие выводы:
1.Электрохимическое определение скорости коррозии стали 38Х2МЮА подтверждает результаты весовых испытаний. После лазерной
обработки в импульсном режиме при плотности мощности лазерного излучения до 7·104 Вт/см2 токи коррозии образцов стали 38Х2МЮА уменьшаются, что указывает на снижение скорости коррозии исследуемых образцов в 4н растворе серной кислоты.
2.Снижение скорости коррозии в исследуемых образцах происходит за счет торможения анодного процесса растворения железа, что вызвано растворением карбидов и равномерным их распределением в поверхностном слое металла.
Азотирование и термическая обработка стали 38Х2МЮА значительно повышают твердость поверхности и уменьшают ее износ.
Поэтому представляет интерес изучение влияния лазерной обработки на коррозионную стойкость поверхности стали 38Х2МЮА, с целью исследования возможности замены процесса азотирования лазерной обработкой.
Было изготовлено 20 образцов стали 38Х2МЮА. На 10 образцах путем шлифования и полирования был удален азотированный слой. Дальнейшая подготовка образцов осуществлялась одинаково: промывание проточной и дистиллированной водой, обезжиривание и обезвоживание спиртоэфирной жидкостью, кратковременная выдержка на воздухе, высушивание в эксикаторе с термически обработанным силикагелем.
Лазерной обработке подвергалось 5 азотированных и 5 неазотированных образцов. Обработка велась на лазерной
технологической установке ЛТУ-2М. Длительность импульса лазерного излучения 1,5 · 10-3с, плотность мощности лазерного излучения 5 · 104 Вт/см2. Для снижения коэффициента отражения лазерного излучения поверхность образцов покрывалась тонким слоем поглощающего покрытия (сажа).
В качестве электролита для коррозионных испытаний использовался 4н раствор серной кислоты. Для определения скорости коррозии были проведены весовые и электрохимические испытания, методика которых описана ранее.
Полученныепривесовыхиспытанияхусредненныерезультатыпредставлены
втаблице2,результатыэлектрохимическихиспытаний–нарис.3.
Таким образом, сравнивая электрохимическое поведение стали 38Х2МЮА в 4 н растворе серной кислоты с азотированным слоем и без него, приходим к выводу, что лазерная обработка усиливает защитное действие азотирования как способа повышения коррозионной стойкости поверхности.
25
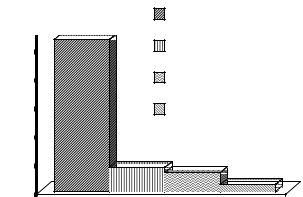
|
Скорость коррозии стали 38Х2МЮА |
Таблица 2 |
|
|
|
||
|
|
|
|
Образцы стали 38Х2МЮА |
|
р, г/см2 · ч |
|
Необлученные |
азотированные |
|
0,00226 ± 0,00005 |
образцы |
|
|
|
неазотированные |
|
0,00415 ± 0,00049 |
|
Облученные |
азотированные |
|
0,00120 ± 0,00005 |
образцы |
|
|
|
неазотированные |
|
0,00111±0,00006 |
i, мА/см2 |
необлученные неазотироанные |
3 |
|
2,5 |
необлученные азотированные |
2 |
облученные неазотированнные |
1,5 |
облученные азотированнные |
1 |
|
0,5 |
|
0 |
|
Рис.3. Плотность тока коррозии образцов стали 38Х2МЮА |
Были проведены также металлографические исследования образцов стали 38Х2МЮА до и после облучения лазером.
На поверхности образца, не обработанного лазерным излучением, наблюдался ярко выраженный коррозионный износ глубиной до 35 мкм, в то время как для образца после лазерной обработки – 10 мкм. После лазерной обработки на поверхности образуется «белый слой», который обладает высокими противокоррозионными свойствами. Глубина этой зоны в зависимости от режимов обработки достигает 750 мкм. Это довольно значительная глубина и она не уступает глубине азотированного слоя, которая достигается весьма затруднительно.
Комплекс проведенных исследований позволяет сделать вывод о перспективности лазерной обработки поверхностей деталей двигателей автомобильной техники с целью предупреждения коррозионного разрушения и износа, что приводит к значительному повышению сроков эксплуатации. Лазерная обработка может быть рекомендована на основных и ремонтных предприятиях.
Библиографический список
1.Соловьев А.А., Шлякова Е.В., Мозговой И.В. Исследование механизма коррозионной стойкости гильз цилиндров двигателей после лазерной обработки. Доклады Омского отделения МАНЭБ. – Омск, 2002. – Выпуск 1(3). – Т. 2. – С. 62-64.
2.Соловьев А.А., Шлякова Е.В., Мозговой И.В. Влияние лазерной обработки стали на ее коррозионную стойкость. Материалы I региональной научной конференции,
26
посвященной памяти главного конструктора ПО «Полет» А.С. Клинышкова «Проблемы разработки, изготовления и эксплуатации ракетно-космической и авиационной техники». – Омск: Изд-во ОмГТУ, 2004. – С. 263-267.
3.Соловьев А.А., Шлякова Е.В., Мозговой И.В. Исследование коррозионной стойкости сплавов после лазерного облучения. Материалы межрегиональной научнопрактической конференции «Многоцелевые гусеничные и колесные машины: разработка, производство, боевая эффективность, наука и образование» (Броня-2004). – Омск: Изд-во ОТИИ. – С. 159-162.
4.Мозговой И.В., Соловьев А.А., Шлякова Е.В. Антикоррозионная поверхностная обработка материалов. Монография. – Омск: Изд-во ОмГТУ, 2006. – 188 с.
УДК 629.113.017
СКОРОСТИ ДВИЖЕНИЯ АТС В СИСТЕМЕ ВАД
И.В. Ходес д-р техн. наук, проф., О.Б. Ригин, Тхе Мань Нгуен Волгоградский государственный технический университет
Для водителей, особенно перевозящих пассажиров, ценные грузы, уникальное оборудование, необходимо организовать бортовую компьютерную систему предупреждения, которая заблаговременно информировала бы об опасности воспроизводимого режима движения изза возможной потери управляемости с учётом параметров АТС, дорожных условий, т.е. в системе водитель–автомобиль–дорога ВАД.
Ключевые слова: система предупреждения, автотранспортное средство, предельная скорость, системе водитель–автомобиль–дорога, психоэмоциональное состояние.
Безопасность движения в условиях непрерывно возрастающей интенсификации дорожных потоков с преобладанием в них энергонасыщенных АТС приобретают все большую актуальность: чем динамичнее АТС, тем оно, несмотря на все увеличивающееся количество применяемых на нем средств пассивной безопасности, представляет собой большую угрозу для себя и окружающих. Причем последствия ДТП оказываются наиболее тяжелыми в самых, на первый взгляд, благоприятных условиях движения. Одно из последних подтверждений тому лавина катастроф, в том числе с автобусами, прокатившаяся по России в августе 2009 г. Во всех этих случаях главной причиной ДТП стал человеческий фактор: водитель значительно превышает скорость в сочетании с разгоном, торможением, резкими поворотами рулевого колеса, засыпает за рулем и т.п. Другими словами, основная причина таких ДТП психоэмоциональное и физическое состояния водителя.
В связи с этим напрашивается вывод: для водителей, особенно тех, кто занят перевозкой пассажиров, опасных или ценных грузов, уникального
27
оборудования и т.д., необходимы бортовые средства технической поддержки активной безопасности. И прежде всего средства, способные заблаговременно информировать его об опасности воспроизводимого режима движения с учетом параметров АТС, дорожных условий, его собственных свойств (возраст, род занятий, эмоциональное состояние, состояние здоровья и т.п.). И надо сказать, что созданием таких устройств занимаются многие специалисты. В частности, авторы предлагаемой вниманию читателей статьи разработали два варианта решения проблемы.
Первый из них, который авторы назвали АХ1 ("Ангел хранитель"), сводится к оснащению АТС системой датчиков, выдающей в бортовой компьютер информацию о воспроизводимых режимах движения и дорожных условиях. Компьютер обрабатывает эту информацию, учитывая технические параметры и характеристики, записанные в базе данных, и определяет величину предельной скорости (vпр), которая допустима в конкретных дорожных условиях. И если фактическая скорость приближается к vпр, то водителю выдается предупреждающий сигнал.
Второй вариант, АХ2, – автономное электронное устройство предупреждения, ориентируется индивидуально для водителя или его можно устанавить на любое АТС. Но в его базу данных необходимо предварительно вводить следующую информацию: код АТС (01 переднеприводное, 02 заднеприводное, 03 полноприводное); значения его снаряженноймассы mсн и массы тгр перевозимого им груза; габаритные его длину Lг, ширину Вг и высоту Нг; базу L и колею В; типоразмер шин Во/НоRd; передаточное число рулевого привода ip ; значение вероятной скорости встречного воздушного
потока vw, высоты его центра давления hw и др. Кроме того, перед каждой поездкой вводятся главные параметры ожидаемых условий движения значения коэффициента сцепления шин с опорной поверхностью (для сухого асфальта = 0,8, для мокрого 0,5, для снежного покрова 0,3 и для гололеда0,15) и коэффициента дорожного сопротивления ( = 0,15). То есть, по сути, те же, что и в случае АХ1. Но там они либо уже заложены, либо получаются в ходе обработки сигналов датчиков.
Однако есть и отличия. Они касаются водителя: в АХ1 характеристики водителя фиксируются автоматически с учётом их проявления по скорости, управляющим действиям при разгоне, торможении, поворота руля и др. В АХ2
–характеристики конкретного водителя, получаются методом экспертной оценки. Часть этих параметров конкретного водителя постоянна (таблица 1), а часть зависит от продолжительности поездки, психического, физического его состояния, состояния внешней среды и т.д., поэтому их желательно корректировать в процессе движения (таблица 2) с периодичностью порядка 3- 4 ч (например, на остановках для отдыха).
28
В обоих случаях данные параметры позволяют оценить время tpзадержки реакции водителя, среднеквадратичное отклонение р этой задержки, точность о воспроизведения поворота управляемых колес АТС с учетом экспертных коэффициентов Kj состояния водителя и, в
конечном счете, выдавать значение Vпр, соответствующее параметрам АТС, дорожным условиям и конкретному состоянию водителя.
Таков алгоритм применения разработанных авторами устройств. Что же касается его математического обоснования, то оносводится к следующему.
Вычисляются массогабаритные параметры АТС его полная масса т, расстояния его центра масс от передней (а) и задней (в) осей, коэффициенты λ1, λ2 распределения массы АТС по его осям и коэффициенты λ', λ" динамического распределения нормальных реакций на переднюю и заднюю оси (см. таблица 3 формулы № 1 4). При этом принимается, что вероятное ускорение va торможения или разгона АТС равно 0,3g.
Далее по формуле № 5 подсчитывается востребованный поворот Ѳ управляемых колес при прямолинейном движении с корректировкой подруливанием. Например, для автомобиля ВАЗ-2109, судя по экспериментальным данным, при передаточном числе рулевого привода 20 имеем амплитуду угла поворота на руле θp= ± 8° и на управляемых Ѳ0 = 0,007 рад. Учитывая, что база этого автомобиля равна L=2,46 м, находим значение установившегося радиуса R поворота: R=2,46/0,007≈350 м. В общем случае, т. е. для АТС с базой Li, по формуле № 6 определяем технически востребованный поворот техi управляемых колес. Для режима же движения после предупреждающих знаков “поворот”, учитывая возможное уменьшение радиуса в 2,5–3 раза, получаем техi =0,0071Li.
После этого для варианта АХ1 компьютерной обработкой рассчитывается среднеквадратическое отклонение σпр угла поворота управляемых колес при прямолинейном движении и с вероятностью р=0,998 – предельная величина их поворота: θпр=±3σпр при корректировке прямолинейного движения, а для случая предупреждающих знаков “поворот” при известном радиусе R поворота для данной конкретной категории дороги – угол поворота управляемых колес (формула № 7).
Затем при торможении и разгоне вычисляются нормальные реакции на осях, (формулы 8), а также тангенциальные силы Fz тяги на мостах: для передне-приводного АТС это формулы № 9-10 и № 11-12); для заднеприводного – формулы №13-14 и № 11-12, для полноприводного – формулы № 15, 16 и см. № 11, 12.
Если |
|
g ,то |
дается |
сообщение-рекомендация уменьшить |
|
φ≤0,3=v/ |
|||||
скорость |
до 30–40 |
км/ч |
и тормозить осторожно, |
преимущественно |
|
двигателем, но если в варианте АХ1 |
|
|
|||
v/ g <0,3, то следует принять v/ g =0,3. |
29