
2594
.pdfТаблица 3
Механические свойства сварных листовых образцов при разных температурах
Марка стали |
Температу- |
0,2 , |
, |
к , |
, |
, |
A1/A2 |
|
ра,оС |
МПа |
МПа |
% |
% |
% |
|
|
|
|
|
|
|
|
|
08кп |
20 |
170 |
380 |
19 |
79 |
16 |
0,23 |
|
|
|
|
|
|
|
|
|
70 |
205 |
355 |
24 |
77 |
18 |
0,06/0,21 |
|
|
|
|
|
|
|
|
|
-50 |
315 |
420 |
25 |
76 |
22 |
0,06/0,22 |
|
|
|
|
|
|
|
|
08ГСЮФ |
20 |
215 |
485 |
16 |
75 |
14 |
0,22 |
|
|
|
|
|
|
|
|
|
70 |
285 |
450 |
19 |
70 |
16 |
0,06/0,22 |
|
|
|
|
|
|
|
|
|
-50 |
435 |
525 |
22 |
78 |
18 |
0,04/0,22 |
07ГСЮФ |
20 |
220 |
345 |
13 |
74 |
10 |
0,11/0,19 |
|
|
|
|
|
|
|
|
|
70 |
235 |
345 |
20 |
79 |
15 |
0,06/0,19 |
|
|
|
|
|
|
|
|
|
-50 |
310 |
440 |
21 |
77 |
15 |
0,10/0,16 |
08пс |
20 |
285 |
370 |
29 |
70 |
20 |
0,02/0,18 |
|
70 |
260 |
345 |
27 |
71 |
17 |
0,03/0,17 |
|
|
|
|
|
|
|
|
|
-50 |
400 |
470 |
25 |
65 |
20 |
0,01/0,17 |
|
|
|
|
|
|
|
|
20кп |
20 |
290 |
417 |
18 |
52 |
11,5 |
0,04/0,16 |
|
|
|
|
|
|
|
|
|
70 |
266 |
410 |
17 |
51 |
14 |
0,12/0,16 |
|
|
|
|
|
|
|
|
|
-50 |
580 |
601 |
5 |
55 |
2.5 |
0,03 |
|
|
|
|
|
|
|
|
С ростом температуры испытания от -50 до +70°С стали 08пс параметры прочности σт, σ0,2, σв уменьшаются, а пластичности ψ - увеличиваются. При этом возрастание степени предварительной деформации εпр.д до 17…18% обусловливает повышение прочностных и понижение пластических характеристик во всем вышеуказанном диапазоне температур статического нагружения.
Величина показателя А2 у кривых деформационного упрочнения образцов из стали 08пс при температурах +70 и -50°С несколько ниже, чем при комнатной температуре. Однако для всех температур с ростом степени предварительной деформации εпр.д А существенно уменьшается, особенно при -50°С.
Механические свойства сварных листовых сталей 08кп, 08ГСЮТ и 07ГСЮФТ представлены в табл. 3.
У сварных образцов из стали 08ГСЮТ наблюдаются более высокие прочностные свойства σв и σ0,2 по сравнению со сталями 08кп и 07ГСЮФТ, у которых они практически одинаковые. Более высокая пластичность у стали 08кп; у сталей 08ГСЮТ и 07ГСЮФТ параметры δ и δр примерно одинаковы, a ψ различается незначительно.
180
Из анализа кривых деформационного упрочнения при температурах 20, 70 и -50°С сваренных встык образцов из сталей 08кп, 08ГСЮТ и 07ГСЮФТ следует, что критическая степень деформации, соответствующая перелому кривых, составляет ~ 2…5%. У сталей 08кп и 08ГСЮТ показатель А2 выше (0,23 и 0,22, соответственно), чем у стали 07ГСЮФТ (0,16…0,19).
Исходная микроструктура листовых сталей 08кп, 07ГСЮФТ и 08ГСЮТ состоит преимущественно из зерен феррита и небольшого количества перлита для 08кп, а также с карбидными включениями у стали 07ГСЮФТ и 08ГСЮТ. Размер зерна феррита стали 07ГСЮФТ равен 20…40 мкм, а сталей 08кп и 08ГСЮТ – 10…30 мкм.
Структура листовой стали 08пс преимущественно состоит из зерен α- твердого раствора, которые в результате пластической деформации получают определенную вытянутость, что отражается на повышении, в связи с этим, прочностных характеристик и снижении показателя упрочнения (табл. 1,2).
Как и в случае ферритной, в ферритно-перлитных сталях 08кп, 07ГСЮФТ и 08ГСЮT с величиной зерна 10…40 мкм происходит внутризеренное, относящееся к разным системам, неоднородное скольжение, отличительной особенностью которого является наличие следов механизмов пересечения и поперечного скольжения. С увеличением степени деформации скольжение по полосам становится множественным, а плотность следов скольжения возрастает. Момент появления микротрещин и последующее разрушение обусловливаются сдвиговыми актами внутри зерен феррита в условиях сильно развитого множественного скольжения. Стали 07ГСЮФТ и 08ГСЮT имеют карбидные включения, которые препятствуют движению дислокаций при пластическом деформировании и с ростом степени деформации повышают прочностные характеристики (табл. 1). Однако они являются также источниками образования микротрещин при растяжении.
Поверхности разрыва при растяжении образцов из сталей 07ГСЮФТ, 08кп и 08ГСЮТ, испытанных при температурах 20, 70 и -50°С, свидетельствуют о вязком характере разрушения. Марка стали и температура испытания практически не изменяют морфологию поверхности разрыва образцов. При этом в изломе сталей 08ГСЮТ и 07ГСЮФТ наблюдаются карбидные частицы размером около 4 мкм, расположенные преимущественно в ямках поверхности разрыва.
Выводы: С увеличением степени предварительной деформации величины условного предела текучести и предела прочности материалов возрастают, а относительных сужения и удлинения – уменьшаются. При этом кривые упрочнения располагаются выше и становятся положе.
Высокие значения параметров пластичности ферритной стали 08кп характеризует ее лучшую штампуемость. В условиях эксплуатации автобусов
181
ПАЗ (северное и южное исполнение) удалось повысить стабильность прочностных свойств штампованных деталей, сократить номенклатуру марок сталей на заводе и снизить (примерно на 5%) металлоемкость.
Библиографический список
1.Пачурин, Г.В. Микромеханизмы высокотемпературной усталости и ползучести металлов и сплавов: учеб. пособие / Г.В. Пачурин, С.М. Шевченко, В.Н. Дубинский и др.
– Н. Новгород: НГТУ, 2006. – 116 с.
УДК 620.178.3.539:620.194.8
ЭКОНОМИЯ ПРИРОДНЫХ РЕСУРСОВ ЗА СЧЕТ ПОВЫШЕНИЯ КАЧЕСТВА МЕТАЛЛОПРОКАТА ПОД ХОЛОДНУЮ ВЫСАДКУ КРЕПЕЖНЫХ ИЗДЕЛИЙ
А.А. Филиппов, аспирант; Г.В. Пачурин, д-р. техн. наук, проф. Нижегородский государственный технический университет им. Р.Е. Алексеева
Одной из важнейших задач современного этапа развития промышленного производства является улучшение качества исходной металлопродукции и изготавливаемых из нее деталей, повышение их работоспособности, надежности, долговечности, а также доведение этих показателей до мировых уровней с целью обеспечения конкурентоспособности российской продукции на мировом рынке.
Для изготовления крепежных изделий холодной высадкой используются конструкционные углеродистые стали с содержанием углерода не выше 0,5%. Марки, химический состав и другие свойства сталей, предназначенных для холодной штамповки, регламентирует ГОСТ 10702-78. К технологическим свойствам металла, подвергаемого холодной высадке, относятся его способность выдерживать без разрушения (без появления трещин и надрывов поверхности) испытание на осадку под воздействием деформирующего инструмента, имеющего плоскую поверхность. Наилучшая способностьсталей к холодной высадке практически обеспечивается в том случае, если образец выдерживает испытание на осадку до 1/Зh и менее. Недостатком испытания на осадку является то, что полученные результаты не полностью характеризуют всю партию и даже отдельный бунт контролируемого металла. Это объясняется невозможностью обеспечения контроля всей партии металла и неравномерностью распределения дефектов по всей длине бунтового материала при установленныхстандартами нормах отбора образцов.
К поверхностным дефектам горячекатаного и калиброванного проката относятся раскатные газовые пузыри, волосовые трещины, рванины, закаты [1]. Неизменным дефектом поверхности металлопроката является
182
образование обезуглероженного слоя вследствие выгорания части углерода при нагреве металла как на стадии прокатки, так и при термической обработке перед калибровкой. Обезуглероживание и окалинообразование существенно снижают механические свойства в поверхностных слоях металлопроката. Основными причинами их возникновения являются дефекты металлургического производства. В результате поверхность становится восприимчивой к образованию рисок, задиров, царапин при прокатке, калибровке и холодной высадке.
Характеристика дефектов поверхности регламентирована в ГОСТ 21014-88 «Прокат черных металлов. Термины и определения дефектов поверхности».
При изготовлении ответственного крепежа моторной группы автомобилей применяют различные виды и способы удаления поверхностных дефектов – механическая обточка, химическое травление в концентрированных растворах кислот при повышенных температурах и другие дорогостоящие, мало экологичные и затратные методы подготовки поверхности проката.
Исходной заготовкой для производства крепежных изделий (болты, гайки), получаемых методом холодной высадки, является горячекатаный прокат. Его пластичность и деформируемость во многом определяют способность стали к дальнейшему калиброванию и холодной высадке. Качество горячекатаного проката под холодную высадку оценивается соответствием его требуемым геометрическим параметрам согласно ГОСТ 2590-88 «Прокат стальной горячекатаный круглый», соответствием химическому составу и необходимым механическим свойствам получаемого калиброванного проката. Кроме того, горячекатаный прокат должен иметь высокую чистоту поверхности и бездефектное поперечное сечение.
Структура и механические свойства исходного горячекатаного проката еще не гарантируют отсутствие брака в крепежных изделиях при обработке холодной высадкой [2, 3].
Наиболее распространенным видом дефектов металлургического происхождения являются неметаллические включения - частицы шлака и огнеупоров. При холодной пластической деформации проката трещины образуются в местах наибольших скоплений неметаллических включений.
Металлургические поверхностные дефекты, как правило, носят прерывистый характер. Испытания на осадку исходного горячекатаного проката до ½ h не позволяют выявить в нем металлургические дефекты, которые раскрываются в виде трещин только при холодной высадке.
Наиболее часто встречающиеся дефекты исходного горячекатаного проката – трещины и рванины. Они, в свою очередь, являются причинами дефектов на получаемых методом объемной штамповки крепежных изделиях - разрывов по граням шестигранных гаек и болтов.
183
Результат статистического анализа периодических проверок при поставках горячекатаного проката в бунтах сталей 10пс, 20, 45, 38ХА, 40Х, 20Г2Р и 30Г1Р для производства метизов методом холодной высадки, поступавшего с металлургических заводов показал следующее.
Количество горячекатаного проката с отклонением на входном контроле составило:
-ОАО «Северсталь» -29294 кг или 3,1 %;
-ОАО «ЭОМК» - 4178 кг или 0,001%.
Основные отклонения металлопроката производства (ОАО
«Северсталь» / ОАО «ОЭМК») указаны в табл. 1.
Таблица 1
Отклонения на входном контроле металлопроката под холодную высадку производства (ОАО «Северсталь» / ОАО «ОЭМК»)
№ п/п |
Отклонения на входном контроле |
Количество, кг |
% |
1 |
Наличие поверхностных дефектов |
12097/2625 |
1,3/0,1 |
2 |
Не выдержали испытание на осадку до 1/3 h |
15547/1553 |
1,6/0,06 |
3 |
Отклонение по структуре проката |
0/0 |
0/0 |
4 |
Отклонение по химическому составу сталей |
0/0 |
0/0 |
5 |
Закаливаемость проката 20Г2Р |
1650/0 |
0,18/0 |
6 |
Отклонение по геометрическим параметрам |
0/0 |
0/0 |
|
согласно ГОСТ 5990 |
|
|
7 |
Величина обезуглероженного слоя |
0/0 |
0/0 |
8 |
Отклонения по механическим свойствам |
0/0 |
0/0 |
|
согласно ГОСТ 10702-78 |
|
|
9 |
Наличие неметаллических включений |
0/0 |
0/0 |
Выводы: Переработка горячекатаного проката с металлургическими дефектами увеличивает количество бракованных крепежных изделий, и, следовательно, приводит к повышенному расходу металла. При поступлении металлопроката необходим качественный входной контроль с целью выявления браковочных признаков и соответствия требованиям нормативно-технологической документации.
Библиографический список
1.Филиппов А.А., Пачурин Г.В. Анализ поверхностных дефектов заготовок горячекатаного проката для холодной высадки метизов // Заготовительные производства в машиностроении, 2008. №5. С. 35-37.
2.Владимиров Ю.В., Герасимов В.Я. Технологические основы высадки стержневых изделий. М.: Машиностроение, 1984. 120 с.
3.Локша О.Г., Напалков А.В. О причинах дефектов при производстве крепежа // ШиГ, 2001. №5. С.12-14.
184
УДК 620.178.3.539:620.194.8
ЭКОЛОГИЧНАЯ ЭЛЕКТРОННО-ПЛАЗМЕННАЯ ОЧИСТКА ПОВЕРХНОСТИ СТАЛЬНОГО ЛИСТОВОГО ПРОКАТА
А.А. Филиппов, аспирант; Г.В. Пачурин, д-р. техн. наук, проф. Нижегородский государственный технический университет им. Р.Е. Алексеева
Холоднокатаный листовой прокат в рулоне, предназначенный для холодной штамповки, должен иметь чистую и блестящую поверхность, свободную от окалины, жировых и других загрязнений.
Горячекатаный или термически обработанный холоднокатаный прокат имеют на поверхности окалину, которая должна быть удалена для предупреждения износа валков стана и получения чистой и точной по толщине холоднокатаной ленты.
Основным способом удаления окалины с листового проката в рулоне является химическое травление в растворах кислот при повышенных температурах. При относительной простоте этот метод очистки имеет ряд существенных недостатков – образование длинных заправочных концов ленты, большая площадь травильных и промывочных ванн, высокая температура воды (50-70ºС), продолжительное время операции травления (30-50 мин.), образование вредных отработанных растворов.
Использование ингибиторов позволяет избежать «недотрав» или «перетрав» проката. Во время травления полосовой стальной ленты образуются вредные запахи, которые постоянно должны удаляться через бортовые отсосы в течение всего технологического процесса. Химическая утилизация вредных отработанных растворов трудоемка и связана с энергетическими и материальными затратами. Продолжительность травления при очистке химическим способом соответствует скорости 0,18 м/мин без учета затрат времени на вспомогательные и транспортные операции [1].
Возможна очистка металлических листов и лент шириной до 1600 мм из различных марок сталей в закрытых агрегатах. Скорость очистки в проходных агрегатах в зависимости от вида проката и возможностей перемоточных механизмов может достигать 10 м/с [2]. Использование электронно-плазменной технологии очистки горячекатаной ленты в рулоне позволяет исключить ряд операций, которые используются при травлении полосовой ленты в растворах кислот, и обеспечить экологичность производственного процесса. Листовой прокат, обработанный способом электронно-плазменных технологий, обладает высокой адгезионной способностью, которая в 2-3 раза выше, чем при использовании других способов очистки.
185

Удельные затраты электроэнергии составляют 0,3 - 0,6 квт.ч/м² [2]. Скорость очистки при электронно-плазменной технологии определяется е мощностью, подводимой к рабочему электронно-плазменному модулю. Максимальная скорость очистки плоского проката определяется только параметрами перемоточного устройства и прочностью очищаемой ленты.
Практическое опробование показало, что электронно-плазменная очистка представляет собой высокопроизводительный и экологически чистый способ очистки горячекатаного плоского проката и термически обработанной ленты в рулоне. Устройство для осуществления предлагаемого способа очистки представлено на рис. 1.
Рис. 1. Устройство дляочистки листового проката:1 – вакуумная камера; 2– кольцевые пустотелыеэлектроды;3– крышка вакуумной камеры; 4– системавакуумирования;5 – правильные ролики;6– протяжные ролики; 7– рама; 8 – система электропитания (соленоиды, выпрямители, сварочныевыпрямители, осцилляторы, дроссели),[3]
Установка полностью автоматизирована, занимает небольшое пространство (около 40 м²) и отвечает требованиям техники безопасности и охраны окружающей среды.
Результаты опытных работ по очистке горячекатаного проката в рулоне стали марки 08кп с химическим составом, указанным в табл. 1, приведены в табл. 2.
|
|
|
Химический состав стали марки 08кп |
Таблица 1 |
||
|
|
|
|
|||
|
|
|
|
|
|
|
Марка |
|
|
|
Содержание элементов в % |
|
|
стали |
|
|
|
|
|
|
С |
Mn |
|
Si |
P |
S |
|
08кп |
0,07 |
|
0,19 |
0,01 |
0,005 |
0,013 |
Визуальный осмотр листового проката стали марки 08кп свидетельствует об однородности поверхности. Следов окалины не обнаружено. Микроструктура поверхностного слоя образцов после химического травления в растворах кислот и после электронно-плазменной обработки практически не отличается от сердцевины. Это подтверждается результатами измерения микротвердости.
186
Таблица 2
Качество поверхности горячекатаного проката в рулоне стали марки 08кп
Характеристика |
Микроструктура |
Наличие |
|
Микротвердость |
поверхности |
|
упрочненного слоя |
|
HV 100 |
|
|
|
|
|
|
Химическое травление в растворах кислот |
|
||
Рябизна; |
Феррит + |
Отсутствует |
|
215 |
шероховатость |
третичный |
|
|
|
Rz 2,8 |
цементит |
|
|
|
|
Электронно-плазменная обработка |
|
||
Рябизна; |
Феррит + |
Отсутствует |
|
217 |
шероховатость |
третичный |
|
|
|
Rz 2,8 |
цементит |
|
|
|
Выводы: Применение электронно-плазменных методов очистки поверхности плоского проката в рулонах позволяют обеспечить экологически чистый оптимальный состав окружающей рабочей среды.
Библиографический список
1.Ширшов, И.Г. Электродуговая вакуумная очистка стального листового проката / И.Г. Ширшов. // Судостроение, 1993. №10. С. 33-35.
2.Сенокосов, Е.С. Плазма, рожденная Марсом / Е.С. Сенокосов, А.Е. Сенокосов // Металлоснабжение и сбыт, 2001. №4. С. 50-51.
3.Патент № 2139151 «Способ очистки металлических поверхностей и устройство для его осуществления».
УДК 620.18:621.793.7
СОВЕРШЕНСТВОВАНИЕ ТЕХНОЛГГИИ РЕМОНТА БРОНЗОВЫХ ЦИЛИНДРИЧЕСКИХ ПОВЕРХНОСТЕЙ МЕТОДОМ ХИМИКО-ТЕРМИЧЕСКОЙ ОБРАБОТКИ
М.Я. Швец канд. техн. наук, доц.; В.В. Акимов д-р. техн. наук, проф.; А.Ф. Мишуров ст. преп.; Р.Ф.Салихов канд. техн. наук, доц.
Одной из важных проблем современного машиностроения является восстановление деталей машин в ремонтном производстве, особенно тех, которые выходят из строя по причине поверхностного износа: распределительные валы, клапаны, цилиндровые втулки, коленчатые валы, валы шестеренчатых насосов и так далее. Технологический процесс восстановления поверхности позволяет создать достаточно долговечные детали машин, требующие лишь периодического ремонта (если повреждения сердцевины незначительны).
В качестве метода восстановления и упрочнения поверхностей деталей машин является нанесение на них износостойких
187
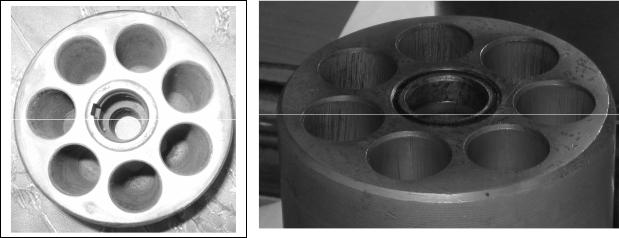
самофлюсующихся покрытий, в результате которого выполняются следующие операции: химико-термическая обработка деталей с покрытием; механическая обработка защитного слоя. При нанесении износостойких покрытий термическая обработка будет существенно влиять на структуру и свойства упрочненных деталей машин. При восстановлении изношенных деталей с износостойким покрытием недопустимо охрупчивание, снижение трещиностойкости, а также разупрочнение основы. Невыполнение данных условий приводит к снижению конструктивной прочности деталей. Причиной этого является неблагоприятное строение, низкие механические свойства зон наплавления, термического влияния на материал.
В данной работе представлен термодиффузионный способ восстановления бронзовых деталей машин. Метод позволяет увеличить размеры изношенных деталей от (0,1до 0,5) мм в зависимости от толщины стенок деталей, состава диффузионной смеси и режима насыщения, а также получать слои, обладающие повышенной износостойкостью с исходной бронзой.
Значительным преимуществом этого метода является простота выполнения технологических операций, несложностью оборудования, недефицитностью использованных материалов, что позволяет снизить расход запасных частей примерно на 5%.
Для проведения экспериментальных работ в качестве образцов использовали блок цилиндров гидронасоса (рис.1).
Для восстановления образцов использовали диффузионные смеси следующего состава: порошок цинка-20%, хлористый аммоний-1%, огнеупорная глина-79%. Время выдержки при диффузионном насышении при температуре 725оС -1,5 час.
б) а)
Рис. 1. Блок цилиндров качающего узла гидронасоса: а- до восстановления; б- после восстановления
188
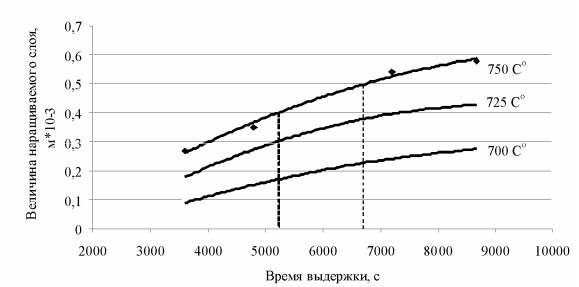
Толщина наращиваемого слоя должна составлять для блоков качающего узла гидронасоса (0,4-0,5) мм. Это обусловлено величиной припуска на механическую обработку и обеспечением шероховатости внутренней поверхности отверстий цилиндров. Толщина наращиваемого слоя должна составлять для блоков качающего узла гидронасоса (0,4-0,5) мм.Это обусловлено величиной припуска на механическую обработку и шероховатости внутренней поверхности отверстий цилиндров.На рис.2 представлена графическая зависимость величины наращенного слоя от времени выдержки диффузии при различных температурах.
Рис.2.Зависимость величины наращиваемого слоя от времени диффузионного процесса при различных температурах.
Были определены оптимальные диапазоны температуры нагрева 750 о С и времени диффузионного процесса (5000-7000) с до наращиваемого необходимого слоя покрытия. Снижение температуры и времени выдержки уменьшают толщину слоя, а увеличение приводит к перенасыщению цинком восстанавливаемой детали и охрупчиванию наращиваемого слоя.
Библиографический список
1.Бороисов, Ю.С. Газотермические покрытия из порошковых материалов: справочник / Ю.С. Борисов, Ю.А. Харламов, С.А. Сидоренко, Е.Н. Ардатовская.- Киев: Наукова думка, 1987.-543с.
2.Супрунов, Г.И. Исследование износостойкости плазменных покрытий деталей почвообрабатывающей техники и комбикормового оборудования при трении в свободном абразиве/ Г.И. Супрунов, Б.Е Лопарев // Омский научный вестник., 2009.- № 1 (77).- С. 45-47.
3.Минкевич, Б.А, Котов В.А. Химико-термическая обработка меди и латуни./ Б.А.
Минкевич, В.А.Котов. - М.: Машгиз, 1960.-36с.
4.Колачев,Б.А., Металловедение и термическая обработка цветных металлов и сплавов /.Б.А.Колачев, В.А. Ливанов., В.И. Елагин. М. : Металлургия, 1972.-480с.
189