
2594
.pdf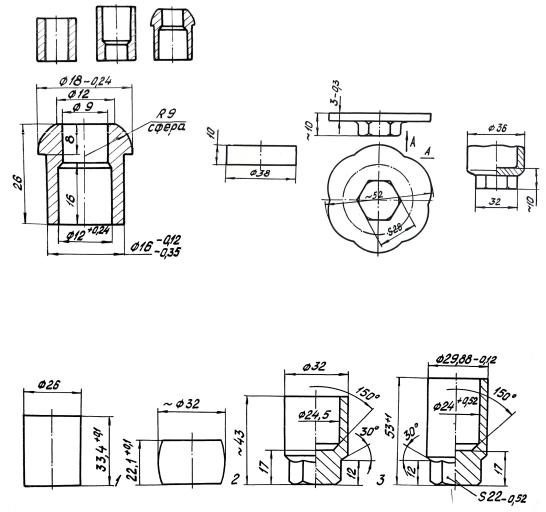
1 2 3
а) б)
Рис. 1. Технологические переходы штамповки ниппеля (а) и гайки (б): 1 – заготовка; 2 – осадка контурная; 3 – вытяжка-свертка
1 2 3
Рис. 2. Технологические переходы штамповки детали «Крышка»: 1 – осадка; 2 - выдавливание комбинированное; 3 – вытяжка с утонением
При рассмотрении вариантов технологий штамповки фасонных деталей следует в первую очередь рассматривать варианты со способами комбинированного выдавливания, так как последние выполняются при относительно небольших удельных деформирующих силах. Именно этот принцип использован при разработке технологии выдавливания детали «Гайка» (рис. 4). Можно рекомендовать также способы комбинированного выдавливания стержневых и полых деталей с использованием способов а, в (рис. 5) в условиях мелкосерийногопроизводства испособовб,г (рис.5)вовсехдругих[3].
В некоторых случаях (проверка технологий с использованием операций со сложной кинематикой течения металла) необходимо проводить опытную штамповку для определения текущего и конечного формоизменения, что увеличивает стоимость проектирования. Но в настоящее время ее можно заменить численными экспериментами при помощи системы автоматизации моделирования процессов холодной объемной штамповки [4].
150
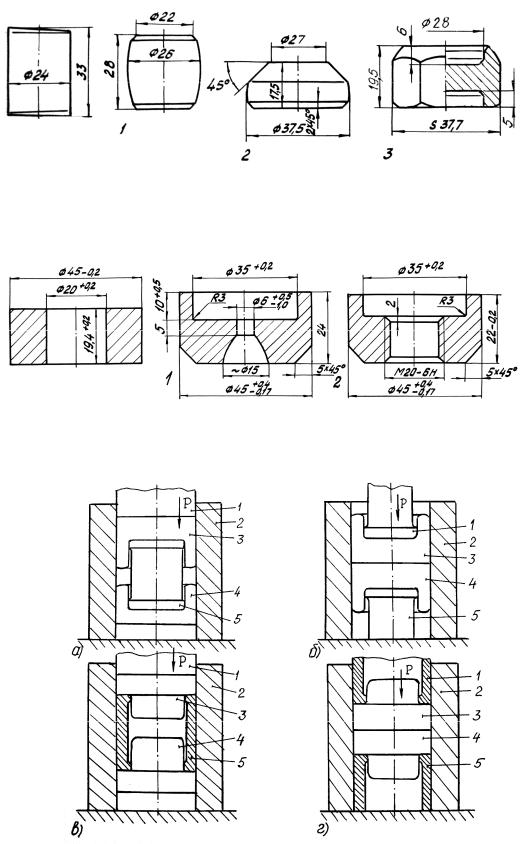
Рис. 3. Технология выдавливания гайки колесной: 1 – осадкакалибровка заготовки; 2 – формовка цилиндроконической заготовки; 3 – полуфабрикат перед заключительным переходом штамповки
Рис. 4. Переходы выдавливания детали «Втулка»: 1 - выдавливание комбинированное; 2- деталь
Рис. 5. Схемы инструментов для одновременной штамповки двух деталей в условиях комбинированного выдавливания: 1 – пуансон; 2 – матрица; 3, 4 – заготовки; 5 – контрпуансон
151
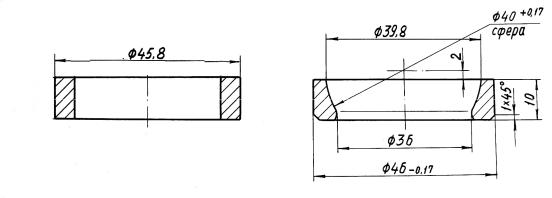
Покажем возможности моделирования на примере оценки формоизменения при выдавливании опоры шаровой (рис. 6 б) из трубной заготовки. Задача решалась в осесимметричной постановке, при этом сферическая поверхность инструмента аппроксимировалась (рис. 7а) двадцатью отрезками прямых линий.
В процесс моделирования изменялись размеры заготовки (высота кольцевой заготовки H и её толщина L): 10 и 5 мм; 10 и 4,5 мм; 9 и 5 мм.
а) б)
Рис. 6. Технология выдавливания детали «Опора шаровая»: а – заготовка (без указания высоты и толщины стенки перед имитационным моделированием); б - деталь
Построение зависимостей изменения размеров заготовки от хода пуансона происходило автоматически за счет считывания координат точки на пересечении верхней торцовой и наружной поверхностей, а также точки на внутренней поверхности на уровне основания детали (рис. 7б).
По графикам (рис. 8) видно, что в третьем случае размеры выдавленного полуфабриката при ходе пуансона 6,0 - 6,5 мм наиболее близки к размерам детали (с учетом растачивания отверстия до диаметра
36 мм).
На рис. 9 и рис 10 представлены схемы инструментов для одновременной высадки утолщений на двух заготовках. В первом случае заготовки 2 и 4 устанавливаются в матрицы 1 и 3 параллельно друг другу на расстояниях между осями, обеспечивающих при совместной высадке контакт по плоскости, образующей грани (лыски) на каждой головке (б); таким образом исключаются операции фрезерования или обрезки (в). Во втором случае обеспечивается высадка полок (меньшей или большей толщины, чем толщина исходных заготовок) на плоских заготовках [5].
Детали типа конических стаканов возможно выдавливать только по схеме прямого выдавливания [7]. При этом должны быть обеспечены условия, когда радиальные и тангенциальные напряжения на кромке – сжимающие.
152
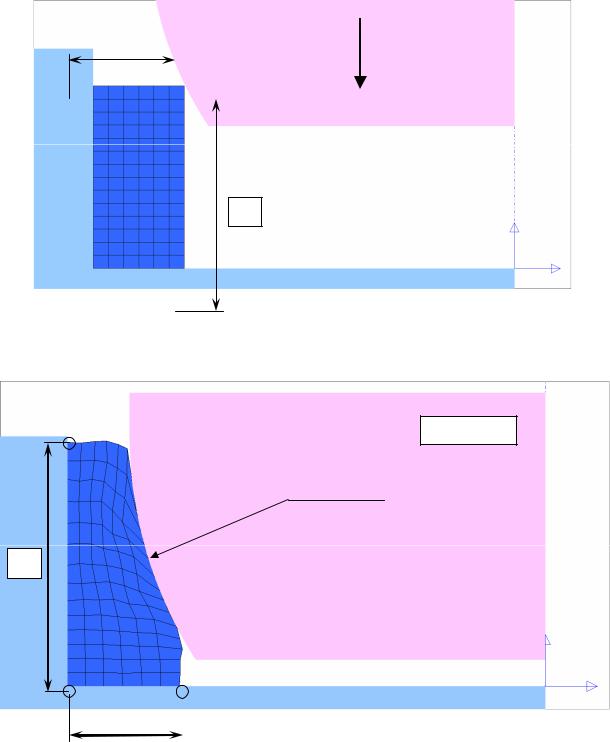
L |
|
|
|
|
|
|
|
P |
|
|
|
|
|
|
|
|
|
|
|
H
а)
Пуансон
сфера
H
|
|
|
|
L |
|
|
Матрица |
|
|
|
|
|
|
|
|
б)
Рис. 7. Картина формоизменения кольцевой заготовки при автоматизированном моделировании: а) до деформирования; б – в процессе деформирования
153
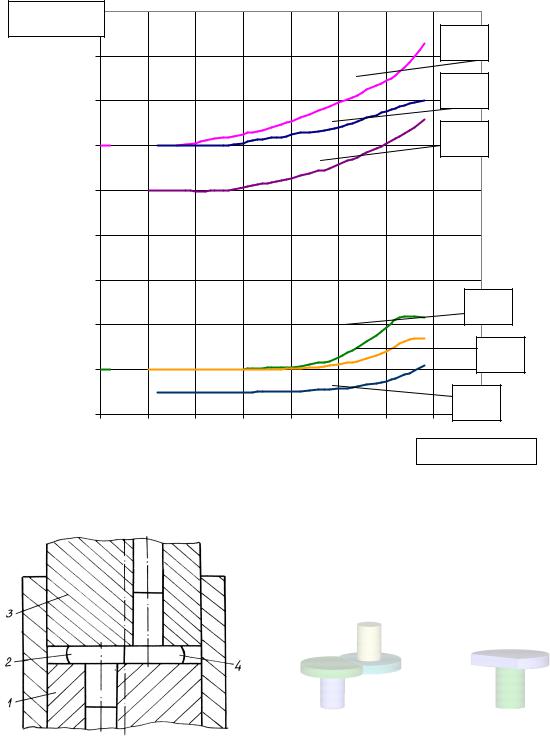
13 |
|
|
|
|
|
|
|
|
H, L (мм) |
|
|
|
|
|
|
|
|
12 |
|
|
|
|
|
|
|
H1 |
|
|
|
|
|
|
|
|
|
11 |
|
|
|
|
|
|
|
H2 |
|
|
|
|
|
|
|
|
|
10 |
|
|
|
|
|
|
|
H3 |
|
|
|
|
|
|
|
|
|
9 |
|
|
|
|
|
|
|
|
8 |
|
|
|
|
|
|
|
|
7 |
|
|
|
|
|
|
|
|
|
|
|
|
|
|
|
|
L1 |
6 |
|
|
|
|
|
|
|
|
5 |
|
|
|
|
|
|
|
L3 |
|
|
|
|
|
|
|
|
|
4 |
|
|
|
|
|
|
|
L2 |
|
|
|
|
|
|
|
|
|
0 |
1 |
2 |
3 |
4 |
5 |
6 |
7 |
8 |
|
|
|
|
|
|
|
Ход пуансона |
Рис. 8. Изменение высоты и толщины (по нижнему торцу) поковки для трех соотношений размеров исходной заготовки
а) |
б) |
в) |
Рис. 9. Инструмент и детали, высаживаемые при встречном движении матриц
154
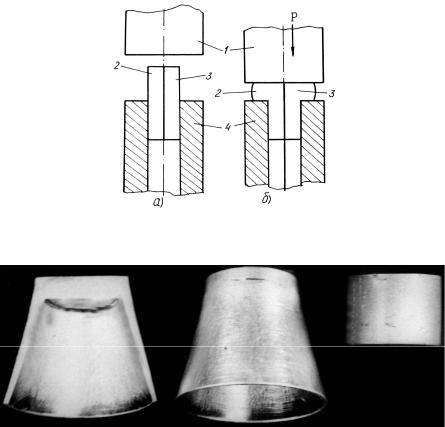
Рис. 10. Схема одновременной высадки полок: 1 – пуансон; 2, 3 – заготовки; 4 - матрица
а) б)
Рис. 11. Конический стакан, выдавленный по схеме прямого выдавливания в суживающуюся щель: а) деталь (штамповка); б) заготовка исходная
Библиографический список
1.Евстифеев В.В. Научное обоснование, обобщение и разработка прогрессивных технологий холодной объемной штамповки / Дис. …докт. техн. наук. М.: МГТУ им. Н.Э. Баумана,1994. 482 с.
2.Евстифеев В.В. Исследование кинематики течения металла и силового режима при холодной штамповке полых многогранных деталей / Дис. … канд. техн. наук. М.: МАМИ, 1969. 197 с.
3.Азаров В.Г. Исследование одновременного выдавливания двух заготовок / В.Г. Азаров, В.В. Евстифеев // Анализ и синтез механических систем: Сб. науч. тр. Омск: ОмГТУ, 1998. С. 80 – 83.
4.Евстифеев В.В. Проектирование, анализ и расчет процессов холодной объемной штамповки / В.В. Евстифеев, А.А. Александров,И.С. Лексутов. Омск: СибАДИ, 2009. 184 с.
5.Патент РФ № 2227989 МПК В21D 22/02, В21J 5/08. Способ изготовления Г – образных деталей / Евстифеев В.В., Пантюхова К.Н. 20.06.2006. Бюл. № 17. 4 с., ил.
6.Евстифеев В.В. Прогнозирование возникновения дефектов на стадии разработки технологии холодной высадки / В.В. Евстифеев, А.А. Александров, И.С. Лексутов, К.Н.
Пантюхова // Матер. III Междунар. технологич. конгресса «Военная техника, вооружение и технологии двойного применения». Омск: ОмГУ, 2005. Ч. I. С. 124 – 125.
7.Евстифеев В.В. Методика построения геометрии инструмента при холодном выдавливании конических стаканов / В.В. Евстифеев, Г.П. Подколзин // Кузнечноштамповочное производство, 1978. № 3. С. 11-13.
155
УДК 621.074
НОВЫЕ КОМПОЗИЦИОННЫЕ МАТЕРИАЛЫ ДЛЯ МАШИНОСТРОЕНИЯ
В.В. Естифеев, д-р. техн. наук, проф., В.И. Гурдин, канд. техн. наук, проф., В.В. Седельников, канд. техн. наук, А.В. Бердюгин, аспирант Сибирская государственная автомобильно-дорожная академия
Непрерывное обновление и совершенствование машин и приборов, применяемых в современном машиностроении, требует создания материалов с высокими эксплуатационными свойствами. Особая роль в их разработке отводится методам порошковой металлургии, которые являются энерго- и ресурсосберегающими. Во многих случаях они могут обеспечивать уникальные свойства за счет возможности соединения различных компонентов композиционных материалов (КМ), обладающих разными физико-механическими свойствами.
Наиболее широко применяются КМ из спеченных железных порошков. Повышение плотности и механических свойств изделий из спеченных порошковых КМ достигается за счет применения высоких давлений уплотнения, легирования матрицы КМ, прессования с применением специальных способов получения материалов и изделий (горячее статическое и динамическое прессование, повторное прессование и т.д.) Однако эти методы повышают энергоемкость процессов, а значительная часть получаемых материалов и изделий характеризуется большей или меньшей остаточной пористостью. Применение жидкой фазы, образующейся в прессованном изделии в результате плавления более легкоплавкой составляющей или контактного плавления легирующих добавок между собой (или в паре с основным компонентом при нагреве и последующем жидкофазном спекании), не позволяет получать изделия с минимальной усадкой.
Увеличение плотности прессовки может быть достигнуто инфильтрацией предварительно спеченного каркаса более легкоплавким компонентом (пропитывающим сплавом). Композиционные материалы, полученные методом пропитки сплавами определенного химического состава и последующего жидкофазного спекания, могут обеспечить высокие эксплуатационные свойства изделий.
Повышение конкурентоспособности продукции автомобилестроения требует создания новых материалов, обладающих высоким уровнем механических свойств и высоким сопротивлением термомеханической усталости, а также новых, более совершенных способов получения КМ.
156
Важную роль в решении этой задачи играют армированные КМ со спеченной металлической порошковой матрицей, имеющие высокое сопротивление усталостному разрушению. При получении материалов, армированных металлическими волокнами, необходимо обеспечить прочную связь на границе раздела фаз «волокно – матрица», обеспечивающую передачу нагрузки на волокна. При жидкофазном спекании создаются условия для сближения поверхностей частиц пропитывающего сплава с поверхностью волокон на достаточно малые расстояния и образования химической связи между этими фазами.
Совершенство гетерогенной структуры материалов, определяющее термомеханическую стабильность КМ, может быть достигнуто за счет совмещения процессов пропитки и легирования компонентов КМ при жидкофазном спекании. Поэтому проблема создания КМ на основе спеченной железной матрицы, имеющих высокие механические и теплофизические свойства, является актуальной и представляется важной в теоретическом и практическом отношениях.
В данной работе представлено одно из возможных решений указанной проблемы, которое базируется на предложенной идее применения в качестве пропитывающих материалов борсодержащих сплавов эвтектического состава на основе железа, никеля и кобальта, обладающих высокой жидкотекучестью, низким поверхностным натяжением и высоким уровнем физико-механических свойств, что позволяет разрабатывать технологии их получения методом пропитки борсодержащими сплавами эвтектического состава и последующего жидкофазного спекания на основе структурно-энергетического подхода к определению состава и технологических режимов, обеспечивающих получение гетерогенной структуры с высокими механическими и теплофизическими свойствами. На рисунке 1 представлена схема пропитки пористого изделия борсодержащими сплавами эвтектического состава.
Использование в качестве пропитывающих материалов новых эвтектических борсодержащих сплавов на основе железа, кобальта и никеля требует определения температуры плавления сплавов, температуры образования и разложения различных химических соединений в присутствии железа, кобальта и никеля, так как эти данные либо вообще отсутствуют, либо носят противоречивый характер [1, 2].
Эти характеристики пропитывающих материалов определялись дифференциально-термический анализом (ДТА) на дериватографе типа ОД-103 Венгерского оптического завода.
Эксперименты показали, что в интервале температур плавления эвтектических сплавов происходит резкое изменение энтальпии. Экстремальный минимум соответствует поглощенной теплоте плавления
157

пропитывающих сплавов, то есть изменению энтальпии системы при переходе из твердого состояния в жидкое.
Частица
порошка
бора
Частица
железного
порошка
Рис. 1. Схема пропитки пористого изделия
Особый интерес представляют физико-химические явления, происходящие в процессе пропитки пористых прессовок эвтектическими сплавами: взаимодействие между жидкой фазой (пропитывающим сплавом) и твердой пористой прессовкой; взаимная диффузия элементов пропитывающего сплава и пористой матрицы и т.д.
158
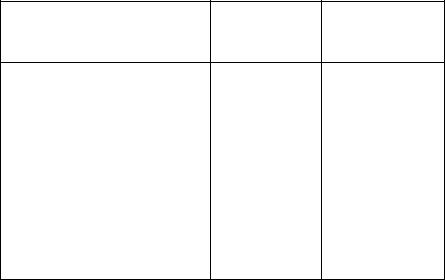
Проведенный термодинамический анализ процесса получения композиционных материалов методом пропитки железной матрицы борсодержащими пропитывающими сплавами эвтектического состава на основе железа, кобальта, никеля и последующего жидкофазного спекания показал, что в системе «пропитывающий сплав – пористая железная прессовка» при определенных температурах развивается термодинамический процесс, включающий:
-плавление пропитывающего сплава (фазовый переход), сопровождающее-ся резким изменением энтальпии системы, которое соответствует поглощенной теплоте плавления пропитывающего сплава, т.е. изменению энтальпии системы при переходе из твердого в жидкое состояние;
-проникновение пропитывающего сплава в поры железной матрицы под действием капиллярных сил, сопровождающееся выделением тепла.
Исследования показали, что процесс пропитки (проникновение жидкой фазы в твердую пористую матрицу) начинается сразу после появления первых капель жидкой фазы в брикете питателя и заканчивается почти одновременно с полным расплавлением пропитывающего сплава.
Втабл. 1 представлены результаты экспериментов. Видно, что прочность композиционных материалов тем выше, чем больше величина WA.
Таблица 1
Результаты ДТА процесса пропитки и свойства композиций
Пропитывающий сплав |
WA, |
σв, МПа |
|
кДж / моль |
|||
материал матрицы |
|||
|
|
|
|
Ni 4% B |
|
||||
|
|
|
|
3,1 |
360 – 380 |
||
|
|
||||||
|
|
Fe 100% |
|
||||
|
|
Сo 4% B |
|
||||
|
|
|
4,3 |
400 - 420 |
|||
|
|||||||
|
|
Fe 100% |
|
||||
|
Fe 14 %ФБ20 |
|
|||||
|
|
|
2,15 |
280 – 300 |
|||
|
|
||||||
|
|
Fe 100% |
|
||||
|
|
Fe 3,8%B |
|
||||
|
|
0,49 |
240 – 260 |
||||
|
|||||||
|
|
Fe 100% |
|
Это дает основание полагать, что при пропитке железной прессовки материалами составов Ni + 4 % В и Со + 4 % В идет энергичное смачивание жидкой фазой твердого каркаса; активнее протекает взаимодействие этих двух фаз с образованием промежуточных соединений, что приводит к повышению работы адгезии.
159