
2594
.pdf
СЕКЦИЯ 5 ОСОБЕННОСТИ ЭКСПЛУАТАЦИИ АВТОМОБИЛЕЙ
И ТТМ В УСЛОВИЯХ СИБИРИ И КРАЙНЕГО СЕВЕРА
УДК 629.083: 656.13
ОПТИМИЗАЦИЯ ПАРАМЕТРОВ СИСТЕМЫ РЕМОНТА АВТОМОБИЛЕЙ
В.И. Гурдин, к.т.н., профессор; А.В. Бердюгин, аспирант Сибирская государственная автомобильно-дорожная академия
Под параметрами системы понимаются величины, характеризующие ее свойства. Оптимизация параметров системы ремонта заключается в установлении таких значений этих параметров и такого их изменения во времени, при которых достигается максимально возможная в определенных условиях эффективность. Оптимизация параметров системы ремонта включает изучение составляющих элементов системы; составление модели исследования; получение численных значений исходных данных; разработку, отладку программ вычислений; составление плана исследований; осуществление исследований; анализ исследований; корректировку (при необходимости) модели и проведение повторных исследований; формирование рекомендаций.
Оптимизацию параметров системы ремонта можно проводить теоретическими, экспериментальными и экспериментальнотеоретическими методами.
При формулировании целей оптимизации Ц пользуются одним из следующих принципов:
ЦЭ max ,
З
ЦЗ min ,
ЦЭ max ,
где Э – эффект от функционирования системы; З – затраты на функционирование системы.
При проведении исследований по оптимизации параметров системы ремонта накладываются определенные ограничения. Имея целевую функцию и ограничения, можно составить математическую, модель оптимизации.
Типовая схема оптимизации параметров теоретическими методами (рис. 1) состоит из следующих блоков:
1 – блок исходных данных для получения: а – зависимости эффекта (Э) от оптимизируемых параметров (Рi), времени их введения (tВ), периода действия (ТД) и текущего времени;
190
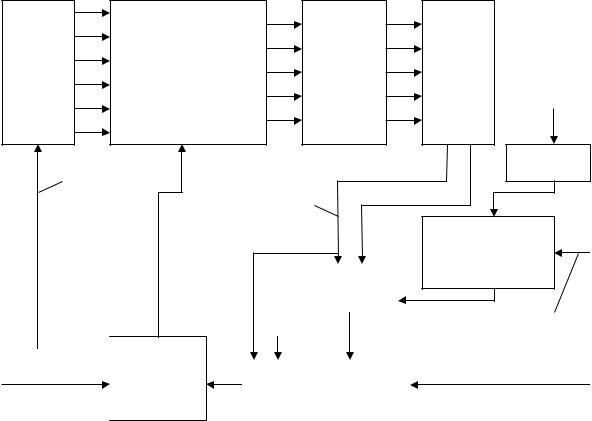
б – зависимости затрат (З) на разработку, производство, эксплуатацию и ремонт автомобилей и их составных частей; в –зависимости цели производства ремонта от эффекта затрат и времени;
г – зависимости параметров системы от научно-технических возможностей (ограничения) – Е; д –зависимости параметров системы от производственных возможностей,
материально-технического снабжения запасными частями, комплектующими изделиями, обеспеченность кадрами и т. д. – НР;
2– блок составления зависимостей а, б, в, г, д;
3– блок прогнозирования изменения исходных данных зависимостей в будущий период времени;
4– блок составления целевой функции (Ц) и ограничений (Е и НР) по зависимостям а, б, в, г, д;
5– блок вычисления оптимальных параметров по целевой функции и ограничениям блока 4;
1 |
2 |
З |
|
|
|
3 |
З |
|
|
|
4 |
|
||
|
Составление исходных |
|
|
|
|
|
|
|
|
|
|
|
|
|
Полу- |
зависимостей: |
|
Э |
|
|
Прогнози- |
|
Э |
|
|
Форма- |
|
||
чение |
Затраты |
|
|
|
|
|
рование |
|
|
|
|
|
лизация |
|
Эффекты |
|
Z |
|
|
|
Z |
|
|
Процесс |
|||||
входной |
Связи м/у параметрами |
|
|
|
|
|
изменения |
|
|
|
|
|
целевой |
|
инфор- |
Научно-технические |
|
E |
|
исходных |
|
E |
|
функции |
изменения |
||||
мации |
возможности |
|
|
|
|
|
зависи- |
|
|
|
|
|
и |
параметров |
|
H |
|
H |
|||||||||||
|
Ограничения в виде |
|
мостей |
|
ограни- |
|
||||||||
|
неравенств |
|
|
|
|
|
|
|
|
|
|
|
||
|
|
|
|
|
|
|
|
|
|
|
|
|
чений |
|
Изменение
входной
информации
Изменение зависимостей
|
|
8 |
|
|
|
||
Дополнительная |
Принятие |
||
решения по |
|||
|
|
||
информация |
корректиров- |
||
|
|
ке модели |
Pi ,tb,T
Целевая функция Ограничения
Ц1(P1 P1,...,Pu Pu ,...)
|
|
|
|
5 |
|
|
||
|
|
|
|
Вычисление |
|
|||
|
|
|
|
|
|
|
|
|
|
|
Цopt |
|
|
|
|
|
|
Ц |
|
|
|
|
|
|
|
|
6 |
|
|
|
9 |
|
|||
|
Оценка |
|
|
Принятие |
|
|||
|
модели |
|
|
решения |
|
|||
|
|
|
|
|
|
|
|
|
7
Прогнозирование
отдельных
параметров
Дополнительная
информация
Дополнительная
информация
Рис. 1. Принципиальная схема оптимизации параметров системы ремонта теоретическими методами
191
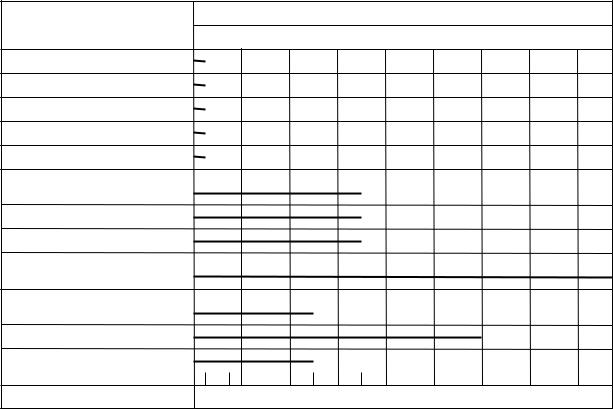
6 – блок оценки применимости модели, коррекции исходной информации и способов учета связей между параметрами, их изменений во времени и других факторов; 7 – блок непосредственного прогнозирования отдельных параметров;
8 – блок принятия решения по корректировке модели;
9 – блок принятия решения по параметрам системы.
Построение рациональной системы ремонта необходимо базировать на научно обоснованных данных: о видах ремонта, периодичности их проведения, перечне выполняемых операций, трудоемкости, производственных средствах [1].
Техника построения системы сводится к группированию видов работ по периодичности (рис. 2). Данные о периодичности работ получают по результатам стендовых и дорожных испытаний, из статистических обобщений данных опытной и повседневной эксплуатации автомобилей.
По результатам группирования работ по срокам выполнения определяются виды ремонта автомобилей, периодичность и перечень операций при каждом ремонте.
Периодичность, тыс. км
Виды работ
20 |
40 |
60 |
80 |
100 |
120 |
140 |
0 |
Очистные
Диагностические
Регулировочные
Крепежные
Смазочные
Разборочно-сборочные: при замене деталей,
при замене узлов,
при замене агрегатов,
при восстановлении ресурса
Ремонтные: арматуры, оперения,
базисных деталей,
небазисных деталей
Группы работ |
1 2 |
3 |
3 |
4 |
5 |
Рис. 2. Схема построения системы технического обслуживания и ремонта
Группирование работ проводится по каждому агрегату и автомобилю в целом. Близкие друг другу по периодичности работы округляются в
192

сторону уменьшения. В приведенном примере (рис. 2) все работы можно объединить в следующие группы:
1 – через 3,5 – 5 тыс. км – ТО-1; 2 – через 14 – 20 тыс. км – ТО-2;
3 – по потребности – текущий ремонт агрегатов и автомобиля; 4 – через 120 тыс. км – капитальный ремонт отдельных агрегатов; 5 – через 200 тыс. км капитальный ремонт автомобиля.
Периодичность проведения технических обслуживании и ремонтов зависит: от конструкции автомобилей, надежности их составных частей, климатических и дорожных условий эксплуатации, качества обслуживания и вождения, применяемых сортов горюче-смазочных материалов, условий использования [1].
Трудоемкость выполнения операций при каждом из видов технического обслуживания и ремонта рассчитываются применительно к определенному производству.
|
Неисправные |
|
|
|
|
|
|
|
|
Исправные |
||
|
автомобили |
|
|
|
Производственные |
|
автомобили |
|||||
|
Вход |
|
|
|
средства, |
|
Выход |
|||||
|
|
|
|
Процесс ремонта |
|
|||||||
|
Запасные части |
|
|
|
|
Неисправные детали |
||||||
|
|
|
|
|
|
|
|
|
||||
|
|
|
|
|
|
|
|
|
|
|
|
|
|
|
|
|
|
|
|
|
|
|
|
||
|
|
|
|
|
|
|
|
|
|
|
|
|
|
|
|
|
|
|
|
|
|
|
|
|
|
|
|
Управление |
|
|
|
|
|
Ограничения |
||||
|
|
|
|
|
|
|
|
|
|
|||
|
Получение информации, ее переработка, |
|
|
Нормативы, нормы, |
||||||||
|
|
|
||||||||||
|
принятие решений, контроль |
|
|
ТУ, Положения |
Рис. 3. Принципиальная схема функционирования системы ремонта
Эффективность функционирования системы ремонта (рис. 3) зависит от параметров входа, выхода, производственных средств и управления. Основными параметрами входа являются: поток требований на ремонты, распределение этого потока по маркам автомобилей, видам ремонта, характеристики ремонтного фонда по видам работ и трудоемкости.
Выходящий поток характеризуется: потоком отремонтированных автомобилей, распределением их по маркам, качеством выполнения ремонтных работ, надежностью отремонтированных автомобилей, трудовыми и материальными затратами, общей себестоимостью ремонта.
Превращение неисправных автомобилей в исправные осуществляется производственными средствами, которые характеризуются ведомственной принадлежностью, специализацией, производственной мощностью, адаптацией к смене обстановки.
193
Ограничениями в системе являются: себестоимость, расход трудовых и материальных ресурсов на единицу ремонта, специализация производственных средств, их мощность, размещение по территории, ведомственная принадлежность, размеры поставок материалов, запасных частей, комплектующих изделий и др.
Исходными данными для проектирования рациональной системы ремонта автомобиля являются [3]:
-значения доремонтных и межремонтных ресурсов автомобилей и их агрегатов; -численность, возрастной состав, техническое состояние парка по маркам
автомобилей, его разбивка на группы эксплуатации; -интенсивность и условия эксплуатации автомобилей;
-средняя трудоемкость единичного ремонта изделий, поступающих в ремонтные средства; -порядок финансирования и возмещения затрат на построение и функционирование ремонта;
-размещение ремонтного фонда по территории, обслуживаемой системой ремонта, порядок и календарные сроки его поступления на ремонтные предприятия; -наличие и резервы трудовых ресурсов в районах функционирования системы ремонта;
-правовые нормы взаимоотношений с автотранспортными предприятиями, органами снабжения, и другими организациями; -достижения науки и практики по организации производства, технологии
выполнения ремонтных работ, управлению и другим вопросам деятельности ремонтных предприятий и объединений.
На основе этих исходных данных можно провести расчет элементов подсистемы капитального ремонта автомобилей.
Выход автомобилей в ремонт обусловливается предельно допустимыми отклонениями параметров технического состояния автомобилей и их составных частей.
Установление предельно допустимых отклонений параметров технического состояния составных частей автомобиля производят по одному из следующих критериев: техническому, технологическому, экономическому. Как правило, предельное состояние деталей и сопряжений устанавливается по одному критерию, другие являются вспомогательными. Для передаточных механизмов автомобиля основным критерием является технический (наступление форсированного износа), для органов управления и тормозов — технологический (качество работы), для двигателя и автомобиля в целом — экономический критерий.
Определение оптимального допустимого отклонения параметра технического состояния составных частей автомобиля производятся по
194
следующей методике [2]. В процессе эксплуатации через определенные наработки tк составные части диагностируют и определяют потребность в ремонте из условия:
u1(tк ) Do , или u1(tк ) Do ,
где u1(tк ) – значение параметра технического состояния; Do – допустимое отклонение параметра технического состояния.
При этом может оказаться, что:
-ресурс составной части автомобиля меньше наработки до первого контроля (в механизмах наблюдается форсированный износ); -остаточный ресурс, оставляемый для работы составной части автомобиля, меньше межконтрольной наработки (автомобиль выйдет в текущий ремонт до контрольной проверки); -ресурс составных частей автомобиля используется полностью
(автомобиль будет выходить в ремонт в планируемые периоды). Изменение допустимого отклонения параметра технического
состояния или межконтрольной наработки влияет на вероятность отказа
составных частей автомобиля |
Q Do,tк и на их средний, фактически |
|
используемый, ресурс tф Do,tк . |
|
улучшает один из показателей Q Do,tк |
Любое изменение Do или |
tк |
или tф Do,tк одновременно ухудшая другой.
Оптимальное допустимое отклонение параметра техническогосостояния из условия обеспечения минимума удельных издержек на эксплуатацию и ремонт при заданной межконтрольной наработке определяется минимумом следующей функции:
|
|
|
|
|
|
|
|
|
|
|
|
|
|
|
|
|
|
|
|
|
|
|
|
|
|
|
|
|
|
||
|
|
Ф Do |
min |
A Q D |
|
|
|
c1 Q(D ) |
|
|
|
||||||||||||||||||||
|
|
|
|
|
|
|
|
|
o |
|
|
|
|
|
|
|
|
|
|
o |
|
. |
|
|
|||||||
|
|
|
|
|
|
|
|
|
|
|
|
t |
|
|
(D ) |
|
|
|
|
||||||||||||
|
|
|
O D U1 t |
ф |
(D ) |
|
|
|
|
|
|
ф |
|
|
|
|
|
|
|||||||||||||
|
|
|
|
|
|
|
|
|
|
o |
|
|
|
|
|
|
|
|
o |
|
|
|
|
|
|
||||||
При |
любом |
Do 1 |
вероятность |
|
|
отказа |
|
|
Q(Do ) 1, |
а |
средний, |
||||||||||||||||||||
фактически используемый ресурс составной части tф Do Tcp . |
|
|
|||||||||||||||||||||||||||||
Вероятность отказа вычисляется по формуле |
|
|
|
|
|
|
|||||||||||||||||||||||||
|
|
|
|
|
|
|
|
|
|
|
|
|
|
|
|
|
|
|
i 1 |
|
|
|
|
|
|||||||
|
|
|
n |
|
|
|
|
To |
|
|
|
|
|
|
|
|
|
|
|
To |
|
|
|
||||||||
|
|
|
|
|
|
|
|
|
|
|
|
|
|
|
|
|
|||||||||||||||
|
|
|
|
|
|
|
|
|
|
|
|
Do |
|
|
|
|
|
|
|||||||||||||
|
|
Q Do |
|
|
|
|
|
i |
|
|
|
|
|
|
|
|
, |
|
|
||||||||||||
|
|
|
|
|
|
|
|
|
|
|
|
|
|
|
|||||||||||||||||
|
|
|
Fo |
o |
|
Fo |
|
|
|
|
|
o |
|
|
|
|
|||||||||||||||
|
|
|
|
|
|
|
|
|
|
|
|
|
|
|
|
|
|
|
|
|
|||||||||||
|
|
|
|
|
|
|
|
|
|
|
|
|
|
|
|
|
|
|
|
|
|
|
|
|
|
|
|
|
|
|
|
|
|
|
|
|
|
|
|
|
|
|
|
|
|
|
|
|
|
|
|
|
|
|
|
|
|
|
|
|
|
|
|
где Fo |
– нормированная |
и |
|
центрированная |
|
функция |
нормального |
||||||||||||||||||||||||
распределения |
случайной |
|
|
|
величины; |
|
|
|
|
i |
|
–порядковый |
номер |
||||||||||||||||||
межконтрольного периода; |
|
|
|
|
|
|
|
|
|
|
|
|
|
|
|
p |
|
|
|
|
|
|
|
|
|
||||||
|
|
|
n |
|
|
1 |
|
|
; |
|
|
o |
|
, |
|
|
|
|
|
|
|
||||||||||
|
|
|
1 D |
|
|
t |
м |
|
|
|
|
|
|
|
|
||||||||||||||||
|
|
|
|
|
|
|
|
|
|
|
|
|
|
|
|
|
|
|
|
|
|||||||||||
|
|
|
|
|
|
|
|
|
|
o |
|
|
|
|
|
|
|
|
|
|
|
|
|
|
|
|
|
где o – среднее квадратичное значение ресурса автомобиля.
195

Допустимые отклонения параметров и остаточный ресурс составных частей агрегатов определяется на основе подконтрольной эксплуатации определенного количества автомобилей, в процессе которой фиксируются изменение параметров во времени и от пробега, а также экономические затраты на техническое обслуживание и ремонт.
Вкачестве показателей ресурса и наработки элементов на отказ принимают: средний ресурс; коэффициент вариации ресурса; наработку на отказ; наработку до момента контроля; наработку между техническими обслуживаниями и ремонтами.
Вкачестве характеристик изменения параметра технического состояния составной части агрегата принимается: номинальное значение параметра; предельное значение параметра; изменение параметра в процессе приработки; изменение параметра через определенные подконтрольные наработки, а также при технических обслуживаниях и ремонтах; среднее квадратичное отклонение параметра и показатель степени, функций.
Вкачестве экономических характеристик технического обслуживания
иремонта принимают: средние издержки на диагностирование составной части по данному параметру; средние издержки на предупредительное восстановление, в которые входят издержки на проверки, регулировки, ремонт с целью доведения параметра до номинального значения; средние издержки на устранение отказа составной части по данному параметру.
Условия эксплуатации автомобилей, влияние климата и другие особенности учитывают при расчетах ресурсов с помощью поправочных коэффициентов.
Трудоемкость единичных ремонтов автомобилей зависит от конструкции и технического состояния автомобилей, специализации и мощности ремонтных предприятий, уровня организации и механизации труда, объема восстановления изношенных и поврежденных деталей, применяемой технологии и оснащения производства необходимым оборудованием.
При проектировании системы, в которой предусмотрен ремонт новых моделей автомобилей, нормы времени определяют по статистическим данным о нормах на ремонт основных моделей автомобилей с учетом коэффициента приведения [1].
Коэффициент приведения KП определяется по формуле:
G2
KП 3 12 ,
G2
где G1 – масса новой модели автомобиля; G2 – масса модели, принятой за аналог; –поправочный коэффициент, = 0,95, если; G1 G2 ; =1,05, если G1 G2 .
196
Так же учитывается влияние на трудоемкость других факторов. Проектную трудоемкость рассчитывают по формуле
TП Ti КП КМ КС Кi ,
где Ti – трудоемкость ремонта модели, принятой за аналог; КМ ,КС ,Кi — коэффициенты, учитывающие соответственно мощность, специализацию и оснащенность ремонтных предприятии.
Оценка эффективности функционирования системы производится по количественным, качественным и экономическим показателям, что позволяет определить производительность, стоимость, фондовооруженность системы, трудоемкость и себестоимость ремонта, качество и надежность отремонтированных автомобилей, время нахождения автомобилей в системе и др.
Библиографический список
1.Маслов Н. Н. Эффективность и качество ремонта автомобилей – 2-е изд. перераб. и доп. – М.: Транспорт, 1995. – 304с. – (надежность и качество)
2.Писарев И. С. Перспективы создания информационных систем в ремонте агрегатов автомобилей / В. Н. Катаргин, И. С. Писарев // В сб. научных трудов Вестник Краснояр. гос. техн. ун-та Вып. 34. Транспорт. – Красноярск, 2004. – С. 164–168.
3.Трегуб Г. Г., Дюмин И. Е. Ремонт автомобилей: Учебник для вузов./ Под ред. И.Е. Дюмина. М.: Транспорт, 1995. 280с.
УДК 621.43
АНАЛИЗ КОНСТРУКЦИЙ ДАТЧИКА КОНЦЕНТРАЦИИ КИСЛОРОДА И ВЛИЯЮЩИХ НА НЕГО ЭКСПЛУАТАЦИОННЫХ ФАКТОРОВ
И.П. Залознов, канд. техн. наук, доц.; О.В. Куксгаузен, соискатель Сибирская государственная автомобильно-дорожная академия
На современном автомобиле проблемы нейтрализации токсичных веществ в отработавших газах (ОГ) двигателя решается с применением специальных газонейтрализаторов. Эти устройства более надежно работают совместно с системой впрыска бензина, которая оснащена датчиком (датчиками) концентрации кислорода (ДКК) в выпускном тракте двигателя [1]. Основной задачей ДКК является определение количества кислорода в отработавших газах.
В системах впрыска, как правило, регулирование топливоподачи осуществляется по сигналу обратной связи от ДКК. Принцип работы системы регулирования топливоподачи с обратной связью по составу смеси заключается в следующем: в соответствии с величиной выходного сигнала установленного в выпускной системе кислородного датчика,
197
характеризующей мгновенный фактический состав сгоревшей смеси, система регулирования обеспечивает такое изменение топливоподачи, которое бы компенсировало текущее отклонение состава смеси от стехиометрического[4].
Современные ДКК для систем управления двигателем, в зависимости от метода определения концентрации кислорода, выполняются в следующих вариантах:
-как химический источник тока с изменяемой по концентрации кислорода электродвижущей силой: чувствительный элемент таких датчиков в основном изготавливается из двуокиси циркония (ZrO2), но возможно применение и других электролитов с подобными свойствами[1,5,6,7,8,9];
-как хеморезистор, у которого величина электрического сопротивления зависит от парциального давления кислорода в омываемых датчик выхлопных отработавших газах: чувствительный элемент датчиков такого типа выполняется, как правило, из двуокиси титана (TiO2), но возможно применение и других электролитов с подобными свойствами (CaO, CoO,MgO2)[1,10,11,12];
-как термопара с термоэдс, зависящей от концентрации кислорода[1];
-парамагнитный датчик, принцип действия которого основан на использовании парамагнитных свойств кислорода: при периодической подаче в зазор датчика газа, содержащего кислород, магнитный поток в контуре изменяется, вследствие чего изменяется и возбуждаемый им электрический ток, и по колебаниям тока судят о содержании в газе кислорода[13];
-датчик для измерения парциального давления кислорода, принцип действия которого основан на анализе акустических волн[14];
-оптический датчик содержания кислорода, чувствительный диск которого из палладия, соединенный тремя оптическими волоконными светодиодами с источником света, отражательная способность диска зависит от парциального давления кислорода в отработавших газах[15].
Вавтомобилестроении применяются ДКК изготавливаемые по первым трем вариантам. На сегодняшний день наибольшее распространение получили ДКК как химические источники тока с чувствительным элементом из ZrO2[3]. Такие датчики имеют различное конструктивное исполнение и их можно разделить на три группы[2].
1. Двухступенчатые ДКК.
Пористая керамика на основе ZrO2 (рисунок 1) легированная оксидом иттрия, является твердым электролитом, т.е. проводит ионы кислорода. После прогрева до рабочей температуры между электродами Pt/ZrO2/Pt возникает напряжение, величина которого определяется разностью содержания кислорода в отработавших газах двигателя (0,1…2,0 %) и в наружном воздухе (21 %). Чем больше концентрация кислорода в отработавших газах, тем меньше выходное напряжение на кислородном датчике. Диапазон рабочих температур обычных датчиков составляет 300..400°С. Диапазон выходного
198
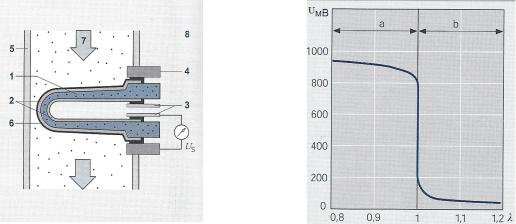
напряжения кислородного датчика составляет 10-1200мВ и определяется его конструкцией. При стехиометрическом составе смеси (14,7:1) среднее значение выходного напряжения составляет примерно 450-500мВ. Следует отметить, что в зоне оптимального состава смеси (при λ=1) напряжение ДКК характеризуется достаточно высокой крутизной выходной характеристики (рисунок 2). То есть при таком составе смеси его выходное напряжение резко изменяется даже при незначительных изменениях содержания кислорода в отработавших газах. Данное свойство двухступенчатых ДКК является недостатком, так как блок управления двигателем по такому сигналу не может определить содержание кислорода в ОГ в зоне обедненных смесей[3,7,8,9].
1– керамический элемент ДКК (ZrO2);
2– платиновые электроды; 3 – контакты;
4– контакт корпуса; 5 – выпускная труба;
6– керамический защитный слой (пористый)
7– отработавшие газы; 8 – атмосфера Рис. 1. Принципиальная схема двухступенчатого ДКК
а – богатая смесь (недостаток воздуха); b – бедная смесь (избыток воздуха)
Рис. 2. Характеристическая кривая напряжения на контактах ДКК
2. Планарные ДКК.
Планарные датчики кислорода по своим характеристикам соответствует двухступенчатым ДКК со скачкообразной характеристикой кривой при λ=1 (рисунок 2). Твердый электролит этого датчика состоит из ряда отдельных, наслаивающихся друг на друга пленок (рис. 3).
Планарные ДКК как и двухступенчатые работают по принципу гальванического элемента с твердым электролитом (принцип Нернста). При достижении температуры 350˚С, керамический элемент датчика становится проводящим для ионов кислорода. Так как при работе в зоне стехиометрической смеси (λ=1) имеет место резкое изменение концентрации кислорода в измерительном слое ДКК, это приводит к тому, что между обеими пограничными поверхностями датчика возникает электрическое напряжение из-за разности концентрации кислорода внутри и снаружи зонда[2,16,17]. Возможен вариант планарного датчика, когда контрольный канал заполнен кислородом и не сообщается с атмосферой.
199