
- •ВВЕДЕНИЕ
- •1. БАЗОВАЯ ИНФОРМАЦИЯ ДЛЯ ПРОЕКТИРОВАНИЯ ТЕХНОЛОГИЧЕСКИХ ПРОЦЕССОВ ПРОИЗВОДСТВА ДЕТАЛЕЙ МАШИН
- •3. ВЫБОР ЗАГОТОВКИ ИЗ СОРТОВОГО ПРОКАТА
- •5. РАСЧЁТ ЗАГОТОВКИ, ПОЛУЧАЕМОЙ СПОСОБОМ ГОРЯЧЕЙ ОБЪЁМНОЙ ШТАМПОВКИ
- •7. ОСНОВЫ ВЫБОРА ТЕХНОЛОГИЧЕСКИХ БАЗ
- •7.2. Базы и их выбор
- •8. АНАЛИЗ ТЕХНОЛОГИЧНОСТИ КОНСТРУКЦИИ ДЕТАЛИ
- •13. СХЕМЫ ФОРМИРОВАНИЯ И РАСЧЁТ ПРОМЕЖУТОЧНЫХ РАЗМЕРОВ ОБРАБАТЫВАЕМОЙ ДЕТАЛИ
- •15. ТЕХНИЧЕСКОЕ НОРМИРОВАНИЕ СТАНОЧНЫХ ОПЕРАЦИЙ
- •Библиографический список
- •Приложение 1
- •Приложение 2
- •Приложение 3
- •Приложение 4
15. ТЕХНИЧЕСКОЕ НОРМИРОВАНИЕ СТАНОЧНЫХ ОПЕРАЦИЙ
Направленность раздела:
1. Ознакомление с теоретическими основами расчёта рабочего времени. 2. Определение основного технологического (То) и вспомогательного (Тв)
времени аналитически-расчётным методом для токарной операции (черновое и чистовое точение или растачивание).
3. Определение норм времени (Тшт) на механическую обработку.
Одной з на более важных задач, решаемых при проектировании технологических процессов, является задача нормирования рабочего времени (нормирование труда) на выполнение определённой работы (ГОСТ 3.1109–82).
В маш ностроен |
нормы времени устанавливаются на технологическую |
С |
|
операцию [2, 25, 26, 27]. |
|
норм рован |
затрат труда используются различные методы: |
- техн ческое норм рование; |
|
- опытно-стат ст |
ческое нормирование. |
При |
|
бА |
Опытно-стат ст ческ м методом нормирования, применяемым в условиях единичного мелкосер йного производств, нормы затрат труда на операцию устанавл ваются не в результате расчёта и анализа её отдельных элементов, а на основе статистических данных о фактических затратах времени на анало-
гичные работы, выполняемые ранее.
Задачами технического нормирования являются выявление резервов ра-
бочего времени и улучшение организации труда на предприятии. При техническом нормировании устанавливаются на основе инженерно-аналитических расчётов нормы времени на выполнение технологических операций, называемые технически обоснованными нормами времени или просто техническими нормами времени.
Техническое нормирование имеет существенное преимущество перед
опытно-статистическим нормированием, так как позволяет использовать пере- |
|
довой производственный опыт, стимулирует производительность труда. Для |
|
|
Д |
определения технически обоснованной нормы времени используют аналитиче- |
|
ский метод нормирования, разновидностями которого являются: |
|
- дифференциальный метод; |
И |
- укрупнённый метод. |
|
|
При дифференциальном методе операцию разделяют на отдельные элементы – машинные, машинно-ручные, ручные, переходы, рабочие ходы, приемы и движения. При этом каждый элемент подвергается анализу как в отдельности, так и в сочетании со сложными элементами. Перед расчётом нормы времени производится анализ структуры нормируемой операции с целью её улучшения (например, исключение лишних приёмов и движений, применение многоместных приспособлений, применение прогрессивных режимов резания).
В условиях единичного и мелкосерийного производств экономически целесообразно расчленять операции на дифференцированные элементы для опре-
87
деления нормы времени. В этом случае пользуются укрупнёнными нормативами (на технологические переходы) или типовыми нормами, составленными аналитическим методом для типовых технологических процессов.
Аналитический дифференциальный метод нормирования может быть:
-аналитически – расчётным;
-аналитически – исследовательским.
При аналитически – расчётном методе [2] продолжительность всех видов работ и затрат времени определяют расчётом.
В этом случае норма времени Т (за единицу нормирования принимается одна деталь) рассч тывается как сумма штучного времени Тшт и подготови- тельно-заключ тельного времени Тпз, отнесенного к количеству деталей в пар-
тии N: |
|
|
|
|
С |
Т = |
Тшт + Тпз / N. |
(15.1) |
|
заключительное период |
входят: время на ознаком- |
|||
В подготов тельно - |
||||
ление рабочего с чертежом |
технологическим процессом, время на подготовку |
|||
рабочего места, станка, пр спосо лений и инструмента, приведение в порядок |
||||
станка рабочего места после окончания работы. |
|
|||
Штучное время (Тшт) складывается из следующих составляющих: |
||||
и |
|
(15.2) |
||
|
Тшт = Топ + Тоб + Тотд, |
|||
где Топ – операт вное время, мин; Т |
– время обслуживания рабочего места, |
мин; Тотд – время перерывов на отдых и естественные надобности, мин.
Оперативноеобвремя – это время, затрачиваемое на выполнение заданной
технологической операции. Оно состоит из технологического времени То и вспомогательного Тв:
(точение, растачивание и т.д.).
Топ = То + Тв. |
(15.3) |
К основному технологическому времени относится время, затрачиваемое |
|
А |
|
непосредственно на обработку детали для каждого технологического перехода |
|
Д |
|
Основное технологическое время может быть:
- ручным (рабочий выполняет операцию вручную: – подвод и отвод режущего инструмента, слесарная обработка, шабрениеИ, измерение детали);
- машинно-ручным (обработка деталей на станках с ручной подачей); - машинным (обработка деталей с помощью механизмов станка без уча-
стия рук рабочего).
В случае, когда учитывается машинное время, То определяется по форму-
ле [2]:
То = Li / nct • S, (15.4)
где L– требуемое перемещение режущего инструмента в направлении рабочей подачи, мм; L = l + l1 + l 2 (см. рис. 15.1); l1 = t ·сtg φ + 1мм; φ – главный угол в плане при вершине резца; nct – cтандартное число оборотов шпинделя токарного станка для заданного перехода, об/мин.; S – подача, мм/об.;
i – необходимое количество проходов (снятие большого слоя напуска) при постоянстве режимов резания.
88
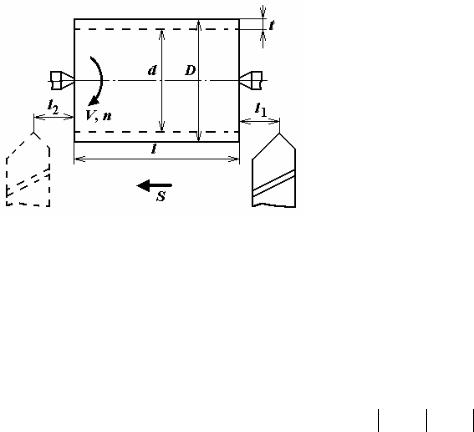
Вспомогательное время Тв на станочную операцию в условиях серийного производства определяют по формуле [2]
Тв = Туст + Тпер + Тизм,
где Туст – время на установку и снятие детали со станка, мин; Тпер – время, связанное с переходом на обработку другой поверхности, мин; Тизм – время на кон-
|
трольные измерения, мин. |
|
|
|
|
|
|
|
|
|
|
|
|
С |
|
|
|
|
|
|
|
|
|
|
|
|
|
|
Время на установку и снятие детали Туст предусматривает выполнение сле- |
||||||||||||
|
дующих приёмов: установку и закрепление детали, включение и выключение |
||||||||||||
|
станка, открепление детали, снятие детали со станка, очистку приспособления |
||||||||||||
|
от стружки. Главным фактором, определяющим величину этого времени, явля- |
||||||||||||
|
ется масса детали (табл.15.1), [27]. |
|
|
|
|
|
|
|
|
|
|
|
|
|
и |
|
|
|
|
|
|
|
|
|
|
|
|
|
Рис.15.1. Схема к определению необходимого |
|
|
|
|
||||||||
|
перемещения режущего инструмента |
|
|
|
|
||||||||
|
при точении на токарном станке |
|
|
|
|
|
|
||||||
|
|
Д |
|
|
|||||||||
|
бА |
|
|
Таблица 15.1 |
|||||||||
|
Время, затрачиваемое на установку и закрепление деталей |
|
|
||||||||||
|
|
|
|
|
|
|
|
|
|
|
|||
|
|
|
|
Масса детали, кг |
|
|
|
||||||
|
Способ установки и крепления |
0,25 |
0,5 |
1.0 |
|
3,0 |
И |
|
|||||
|
|
|
5,0 |
|
8,0 |
15,0 |
20,0 |
|
|||||
|
детали |
Время на установку и снятие детали Т уст, мин |
|
||||||||||
|
В самоцентрирующемся |
- |
0,15 |
0,17 |
|
0,23 |
|
0,27 |
|
0,30 |
0,40 |
0,50 |
|
|
патроне с креплением ключом |
|
|
|
|
|
|
|
|
|
|
|
|
|
В цанговом патроне с крепле- |
0,07 |
0,08 |
0,09 |
|
0,12 |
|
0,14 |
|
0,17 |
0,20 |
0,25 |
|
|
нием рукояткой рычага |
|
|
|
|
|
|
|
|
|
|
|
|
Время Тпер предусматривает выполнение следующего комплекса приёмов: подвод режущего инструмента (резца, сверла, развёртки, фрезы и т.д.) к обрабатываемой детали, включение и выключение подачи, измерение детали при снятии пробной стружки, а также отвод инструмента в исходное положение. При определении норматива этого времени в расчёт принимают размеры стан-
89
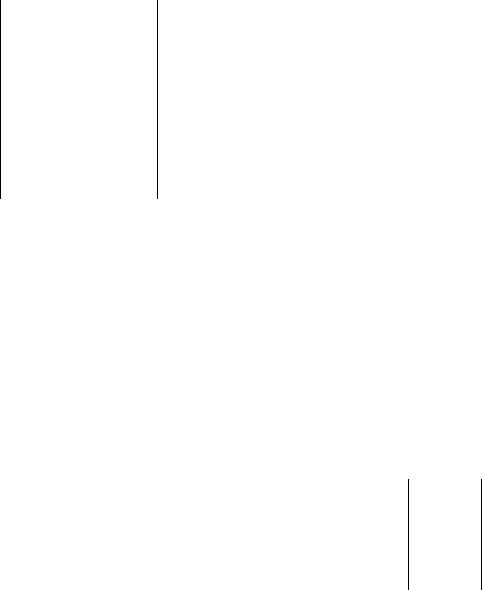
ка, на котором выполняется операции, размеры обрабатываемой поверхности, точность обработки, способ измерения, т.е. факторы, влияющие на продолжительность приёмов. В табл.15.2 приведены значения Тпер при работе на токарном станке.
Способ |
|
Таблица 15.2 |
||||
|
|
Значение времени перехода Тпер на обработку |
|
|||
|
другой поверхности при работе на токарном станке [27] |
|
||||
|
|
|
|
|
|
|
|
Характер |
установ- |
Измеряемый |
Наибольший диаметр изделия, |
||
|
работы |
ки нструмента |
размер, мм |
устанавливаемый |
||
|
точение |
|
над станиной, мм |
|||
|
|
|
|
|||
|
|
|
|
до 300 |
|
до 400 |
|
|
|
|
Время, связанное с переходом |
||
|
|
|
|
Тпер, мин |
|
|
|
Продольное |
бА |
0,08 |
|
0,11 |
|
|
Резцом, |
до 25 |
|
|||
|
наружное |
устанавл ваемым |
до 100 |
0,09 |
|
0,12 |
|
|
на размер |
cв.100 |
0,10 |
|
0,13 |
Время на контрольные измерения обработанной поверхности Тизм учитывается только при определении продолжительности выборочных контрольных измерений после окончания о ра отки (табл.15.3).
Таблица 15.3
Значение времени, затрачиваемого на контрольные измерения [27]
Измеритель- |
Точность |
Измеряе- |
|
|
Измеряемая длина, мм |
|
|
||
ный |
измере- |
мый диа- |
|
до 50 |
до 100 |
до 200 |
до 300 |
до 500 |
|
инструмент |
ния, |
метр, до |
|
Время на контрольные измерения Тизм., |
|
||||
|
мм |
мм |
|
мин |
|
|
|
|
|
|
|
|
|
Д |
|
|
|||
Штанген- |
|
50 |
|
0,12 |
0,15 |
0,18 |
0,20 |
0,24 |
|
|
100 |
|
0,13 |
0,16 |
0,19 |
0,22 |
0,24 |
|
|
циркуль |
0,05 |
200 |
|
0,16 |
0,17 |
0,21 |
0,23 |
0,25 |
|
|
|
300 |
|
0,19 |
|
|
|
|
|
|
|
400 |
|
0,22 |
|
И |
|
Время на обслуживание рабочего места Тоб – регламентированная часть штучного времени, направленная на поддержание технологического оборудо-
вания (станка) и рабочего места в необходимом состоянии. |
|
Тоб = Тто + Тоо, |
(15.5) |
где Тто – время технического обслуживания, т.е. каждодневное поддерживание оборудования (станка) в работоспособном состоянии, осуществляемое станоч-
90
ником (чистка станка после окончания рабочей смены, смазка станка, его подналадка, уборка стружки, заточка или замена затупившегося инструмента);
Тоо – время организационного обслуживания, т.е. поддержание рабочего места в нормальном организационном состоянии (уборка места в конце рабочей смены, раскладка технологической оснастки и заготовок по своим заранее отведённым местам, установка в удобное место подставки с рабочим чертежом, сдача рабочего места сменщику и т.п.);
Тоб – устанавливается в процентах от оперативного времени Топ. Конкретная величина Тоб зависит от вида выполняемой операции (перехода), используемых приспособлен й, размера детали и т.д. В среднем принимают равным 3,5–4,0% от Топ.
Время на отдых естественные надобности Тотд также принимают в про-
центах от Топ. В среднем Тотд принимают равным 2,0–4,0% от Топ. |
|
|
С |
|
|
|
образом, норма штучного времени определяется по следующей |
|
формуле: |
|
|
Тшт = (То + Тв) {1 + (α + αотд) / 100} = 1,08 (То + Тв), |
(15.6) |
|
где αоб αотд – проценты от оперативного времени Топ на обслуживание и |
||
отдыхТаким(в сумме пр мерно 8%). |
|
|
|
об |
|
|
А |
|
|
Контрольные вопросы |
|
1. |
Какие методы используются при нормировании затрат? |
|
2. |
Что такое техническая норма времени? |
|
3. |
В чем преимущество технического нормирования перед |
опытно- |
статистическим? |
Д |
|
|
||
4.Какие методы нормирования являются разновидностями аналитического |
||
метода, в чём их сущность? |
|
|
5. |
Что принимается за единицу нормирования при производстве деталей |
|
машин? |
|
|
6. |
Как определяется основное технологическое время То при обработке на |
|
токарном станке? |
И |
|
|
||
7. |
Как учитывается перебег резца при обработке поверхности в упор? |
|
8. |
Что входит в состав вспомогательного времени Тв, условия их определе- |
|
ния? |
|
|
16. ФОРМЫ И ПРАВИЛА ОФОРМЛЕН Я МАРШРУТНЫХ И ОПЕРАЦИОННЫХ КАРТ
Направленность раздела:
1. Освоение правил оформления маршрутных и операционных карт. Основными завершающими документами оформления технологических про-
цессов являются маршрутная карта (ГОСТ 3.1118-82, [19]) и операционная карта (ГОСТ 3.1404-86, [20]).
91
Маршрутная карта является составной и неотъемлемой частью комплекта технологических документов, разработанных на технологические процессы изготовления или ремонта изделий и их составных [19].
Выбор формы маршрутной карты определяется видом разработанного технологического процесса. В соответствии с ГОСТ 3.1118–82 установлено 6 форм маршрутных карт.
Операционная карта содержит описание операций с указанием последовательности переходов, наименование технологического оборудования, сведений о режимах, нормах времени, материалах, смазочно-охлаждающих жидкостях и т.д.
|
|
Пояснен я по оформлению технологических карт |
||||
С |
обработки деталей резанием |
|
|
|||
|
|
|
|
|||
В карту технолог ческого процесса (маршрутная карта) записывают все |
||||||
операции |
|
заготовки (детали), включая термическую обработку и |
||||
контроль качества. В та л. 16.1 приведена расшифровка символов технологи- |
||||||
ческих карт. |
|
|
|
|
|
|
обработки |
|
Таблица 16.1 |
||||
|
|
|
С мволы технологических карт |
|||
|
|
|
|
|
||
|
|
|
|
|
|
|
1 |
|
|
2 |
|
|
|
|
Служеб- |
|
|
|
|
|
|
ный |
|
|
Содержание информации |
|
|
|
символ |
|
|
|
|
|
|
А |
Номер цеха, участка, рабочего места, операции, код и наиме- |
|
|||
|
|
бА |
|
|
||
|
|
нование операции, обозначение документов, применяемых |
|
|||
|
|
для выполнения операции |
|
|
||
|
Б |
Код, наименование оборудования и информация по |
|
|||
|
|
трудозатратам |
|
|
|
|
|
М |
Информация о применяемом основном материале и исходной |
|
|||
|
|
заготовке |
Д |
|
||
|
|
|
|
|
||
|
МО1 |
Наименование, сортамент, размер и марка материала, обозна- |
|
|||
|
|
чение стандарта, технических условий. анные записывают |
|
|||
|
|
дробью в виде: круг 0 58 Гост 2590–2006/45 Гост 1050-2013. |
|
|||
|
|
Здесь заготовка –прокат круглый 58 мм из стали 45. |
|
|||
|
|
|
|
И |
|
92

|
|
|
|
Окончание табл. 16.1 |
|
|
|
|
|
|
|
1 |
|
|
2 |
|
|
|
МО2 |
|
Код материала по классификатору |
|
|
|
О |
|
Содержание перехода (операции) |
|
|
|
Т |
|
Технологическая оснастка. Записывают в следующей последо- |
|
|
С |
вательности: приспособление, вспомогательный инструмент, |
|
|||
|
|
|
|
||
|
|
|
режущий инструмент, слесарно-монтажный инструмент, сред- |
|
|
|
|
|
ства измерений с указаниями ГОСТов |
|
|
|
Р |
|
Реж м обработки |
|
|
|
ЕВ |
|
Код ед н цы величины (массы, длины, площади и т. П.) По |
|
|
детали\ КИМ Коэфф ц ент использования материала |
|
||||
|
|
|
класс ф катору СОЕВС |
|
|
|
МД |
|
Масса |
по конструкторскому документу |
|
|
Проф. |
|
Код профессии по классификатору ОКПДТР |
|
|
|
ЕН |
|
Ед н ца нормирования, на которую установлена норма расхо- |
|
|
|
|
|
да матер ала или норма времени, например 1, 10, 100 |
|
|
|
Н.расх. |
|
Норма расхода материала |
|
|
|
|
|
|
|
|
|
Проф ль, |
Проф ль |
размеры исходной заготовки. Пример записи: ø60 х |
||
|
размеры |
360, л ст 1 х 710 х 1420, 115 х 270 х 390 (для отливки) |
|
||
|
|
|
|
|
|
|
КД |
|
Число деталей, изготавливаемых из одной заготовки |
||
|
МЗ |
|
Масса заготовки |
|
|
|
СМ |
|
Код степени механизации. Заполнение не обязательно |
|
|
|
РАЗРЯД |
Разряд работы для выполнения операции |
|
||
|
|
бА |
|
||
|
УТ |
|
Код условий труда по классификатору окпдтр, 1 - нормальные; |
||
|
|
|
2 - тяжелые и вредные; 3 - особо тяжелые и особо вредные |
|
|
|
КР |
|
Число рабочих, занятых при выполнении операции |
|
|
|
КОИД |
|
Число одновременно изготавливаемых (ремонтируемых) де- |
|
|
|
|
|
талей (станочных единиц) при выполнении одной операции |
|
|
|
|
|
Д |
|
|
|
ОП |
|
Объем производственной партии (шт.). опускается графу не |
||
|
|
|
заполнять |
|
|
|
|
|
Коэффициент штучного времени при многостаночном обслу- |
|
|
|
Кшт |
|
живании. Зависит от количества обслуживаемых станков. При |
|
|
|
|
|
1 станке – 1, при 2 – 0,65; при 3 – 0,48; при 4 – 0,35; при 5–6 – 0,32 |
|
|
|
|
|
И |
|
|
|
Тиз |
|
Норма подготовительно-заключительного времени на операцию |
||
|
Тшт |
|
Норма штучного времени на операцию |
|
|
|
ПИ |
|
Номер позиции инструментальной наладки. Заполняется для |
|
|
|
|
|
станков с ЧПУ |
|
Операции нумеруют по порядку – 005, 010, 015 и т. д.
Наименование операций определяется типом станка независимо от характера выполняемой работы. Например, токарно-винторезная, токарно-
93
револьверная, токарно-карусельная. Обработка на станках с ЧПУ записывается так: токарная с ЧПУ, шлифовальная с ЧПУ и т.д.
Допускается использовать сокращенную форму записи операций: токарная, сверлильная, фрезерная, строгальная, протяжная, шлифовальная, отделочная (хонинговальные, суперфинишные, доводочные, полировальные станки), зубообрабатывающие (зубофрезерн).
СВ табл.16.2 [3] приведены примеры полной и сокращенной записи содержания переходов при обработке резанием.
Вспомогательные технологические переходы записываю следующим образом: «установ ть, закреп ть, снять заготовку (деталь)».
- при операц онном оп сании и применении карты эскизов (КЭ) и соответствующих операц онных карт (ОК), когда существует графическое изображение обрабатываемой заготовки с указанием условных обозначений применения
баз опор.
Вспомогательные переходы допускается не записывать: -заготовкипри маршрутном оп сании технологических операций;
следует выделятьбАцветным карандашом.
Число эск зов на каждую операцию должно соответствовать числу установок . При о ра отке заготовки на многопозиционном станке эскизы дают для всех поз ц й (кроме установочной). Обрабатываемые поверхности
Наименование станка приводят полностью с указанием модели, например: вертикально-сверлильный 2Н135а.
Наименование режущих, вспомогательных и измерительных инструментов дают полностью, приводят о означение по госту и номер госта. Для шлифовальных кругов дают обозначение формы, размеров круга, его характеристики и номер госта. Примеры обозначенийДданы в приложении.
Число одновременно применяемых единиц технологической оснастки следует указывать после кода (обозначения) оснастки, заключая в скобки. Например, абвг ххххххх.ххх (2) фреза дисковая.
Технологический процесс в маршрутной карте расписывается построчно. Содержание каждого типа строки обозначается буквамиИрусского алфавита, которые являются обозначением служебного символ:
А – номер и наименование операции. Например, 015 Токарная; Б – наименование и марка оборудования. Например, 16К20 Станок токар-
но-винторезный; О – содержание операции (перехода). Например, точить, сверлить и т.п.
Т – информация о применяемой при выполнении операции технологической оснастки.
94
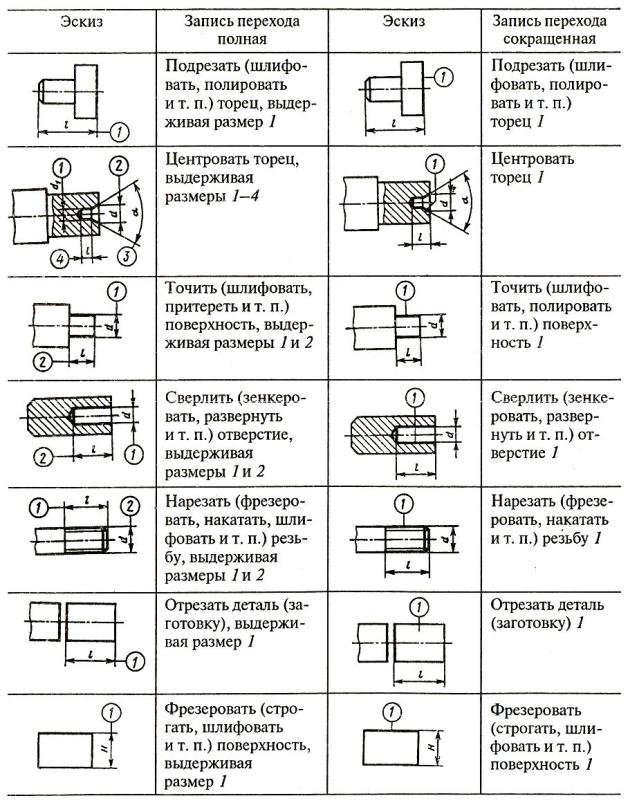
Таблица 16.2
Примерыполнойисокращенной записи содержанияпереходовобработки
Си бА Д И
95
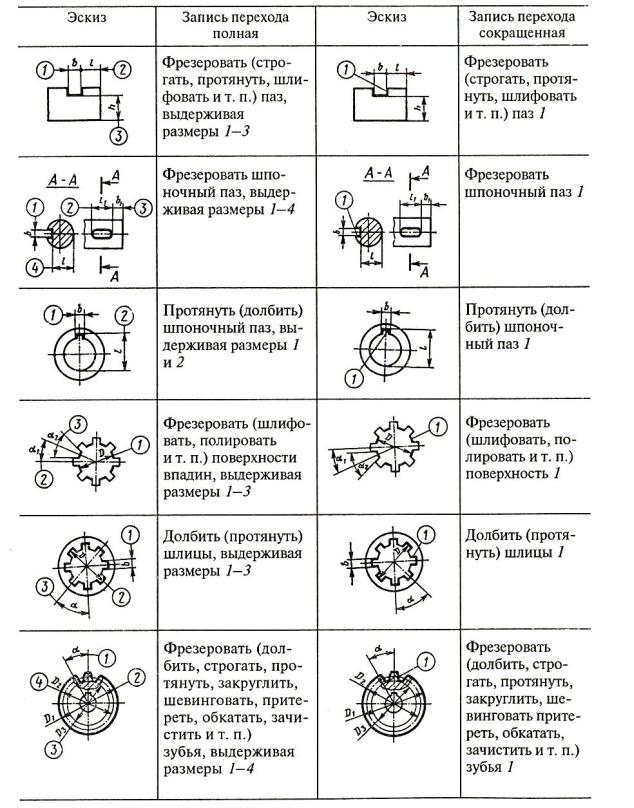
Окончание табл. 16.2
Си бА Д И
96
При заполнении строк маршрутной карты следует руководствоваться следующими требованиями ГОСТ 3.1118-82:
- очерёдность заполнения служебных символов при оформлении единичных технологических процессов, выполняемых с применением различных методов обработки: сначала А, затем Б, затем О, затем Т;
- запись информации следует выполнять в технологической последовательности по всей длине строки; при необходимости запись продолжается на последующих строках с простановкой служебного символа;
- при операц онном описании технологического процесса номер перехода
следует проставлять в начале строки;
приспособленспец альный нструмент, применяемый при выполнении специфических
- информац ю по пр меняемой на операции технологической остнастке
(символ Т) зап сывают в следующей последовательности: |
|
С |
|
- |
я; |
- вспомогательный нструмент; |
|
- режущ й |
нструмент; |
- слесарно-монтажный нструмент; |
технолог ческ х процессов (операций), например, при сварке, штамповке, и т.п.; - средства змерен я.
Разделение информации по каждому средству технологической оснастки следует выполнять через знак «;» (пример заполнения форм 1 и 1б маршрутной карты в приложении 1–2).
Количество одновременно применяемых единиц технологической оснастки следует указывать после кода (обозначения) оснастки, заключая в скобки, на-
пример, АБВГ хххххх.ххх(2) фреза дисковая. |
|
Графы формбА1 и 1б обозначают и подлежат заполнению: |
|
М01 – марка и ГОСТ материала; |
Д |
М02: |
|
|
-Код – код материала;
-ЕВ – код единицы измерения;
-МД – масса детали по конструкторскому документу;
-ЕН – единица нормирования, например, 1, 10, 100, и т.д.;
-Н.расх. – норма расхода материала;
-КИМ – коэффициент использования материала;
-Код заготовки – указывается вид заготовки – прокат, отливка, поковка и т.д.;
-Профиль и размеры – профиль и размеры исходной заготовки;
-МЗ – масса заготовки; И
А:
-Цех – номер (код) цеха, в котором выполняется операция;
-Уч. – номер (код) участка, конвейера, поточной линии и т.д.;
-РМ – номер (код) рабочего места;
-Опер.- номер операции;
97
- Код, наименование операции – код операции по технологическому классификатору, наименование операции (токарная, фрезерная, и т.п.); Б:
- Код, наименование оборудования, код оборудован7ия по классификатору; - М – степень механизации; - Проф. – код профессии;
- Р – разряд работы, необходимый для выполнения операции; - УТ – код условий труда;
-КР – количество исполнителей (рабочих), занятых при выполнении операции; -КОИД – кол чество одновременно изготавливаемых (обрабатываемых,
ремонтируемых) деталей при выполнении одной операции;
- ОП – объём про зводства, шт.; |
|
- КШТ. – коэфф ц ент штучного времени при многостаночном обслуживании; |
|
С |
|
ТПЗ. – норма подготов тельно-заключительного времени; |
|
ТШТ. – норма штучного времени на операцию. |
|
Операц онная карта |
спользуется для оформления разработанных техно- |
логическ х процессов |
, выполняемых с применением универсально- |
операций го оборудованобозначениея – форма 2 (первый или заглавный лист) и форма 2а (после-
дующие л сты) (см. пр ложения 3–4) [20].
Содержан е перехода следует указывать по всей длине строки с переносом
ской оснастке; А Р – указание данных по технологическим режимам. Указываются после за-
при необходимости на последующие строки.
Буквенное |
служе ного символа при оформлении операцион- |
ной карты: |
|
О – содержании операции (перехода);
писи состава применяемой технологической оснастки.
Т – информация о применяемой при выполнении операции технологиче- Д
При указании данных по технологической оснастке следует руководство-
ваться требованиями соответствующих классификаторов, государственных и отраслевых стандартов на кодирование (обозначение) и наименование технологической оснастки, при этом информацию следует записывать в последовательности:
- приспособления; |
И |
- вспомогательный инструмент; |
|
- режущий инструмент; |
|
- средства измерения. |
Разделение информации по каждой технологической оснастке следует выполнять через знак «;» (смотрите пример заполнения форм 2 и 2а операционной карты в приложении к данному учебному пособию).
При описании содержания операции необходимо указывать ТО, ТВ, ТПЗ, ТШТ. Пояснение отдельных граф формы 2:
- ЕВ – код единицы величины (массы, длины, площади и т.п.) детали, заготовки;
98
-МД – масса детали;
-профиль и размеры – профиль и размеры исходной заготовки;
-МЗ – масса заготовки;
-КОИД – количество одновременно обрабатываемых деталей;
-ПИ – заполняется для станков с ЧПУ – номер позиции накладки;
-D или В – расчётный размер обрабатываемого диаметра (ширины) детали;
С |
|
|
|
- L – расчётный размер длины рабочего хода. |
|||
|
|
Контрольные вопросы |
|
1. |
Каково назначен е маршрутных карт? |
||
последовательности |
|
||
2. |
Как е формы маршрутных карт установлены ГОСТ 3.1118–82? |
||
3. |
Для как х технолог ческих процессов установлены маршрутные карты |
||
1 и 1б (ГОСТ 3.1118–82)? |
|
||
4. |
Что обозначают служе ные символы А, Б, О и Т в маршрутных картах? |
||
5. |
Какова очерёдность введения служебных символов при оформлении |
||
единичных технолог ческ |
х процессов в маршрутных картах? |
||
6. |
В какой |
|
(под символом Т) записывается технологи- |
ческая оснастка, какая? |
|
|
7.Как е графы включены в формы 1 и 1б маршрутной карты, что они обозначают?
8.Что включается в операционные карты?
9.Какие формы операционных карт установлены ГОСТ 3.1404-86 для оформления технологических процессов с применением универсального оборудования?
10.Как записываются и обозначаются переходы технологического процесса при заполнении операционных карт?
11.Какие служебные символы используются при заполнении операционных карт?
12.По какому служебному символу и при какой очерёдности заполнения операционной карты указываются установленные технологические режимы?бАД
И
99