
- •ВВЕДЕНИЕ
- •1. БАЗОВАЯ ИНФОРМАЦИЯ ДЛЯ ПРОЕКТИРОВАНИЯ ТЕХНОЛОГИЧЕСКИХ ПРОЦЕССОВ ПРОИЗВОДСТВА ДЕТАЛЕЙ МАШИН
- •3. ВЫБОР ЗАГОТОВКИ ИЗ СОРТОВОГО ПРОКАТА
- •5. РАСЧЁТ ЗАГОТОВКИ, ПОЛУЧАЕМОЙ СПОСОБОМ ГОРЯЧЕЙ ОБЪЁМНОЙ ШТАМПОВКИ
- •7. ОСНОВЫ ВЫБОРА ТЕХНОЛОГИЧЕСКИХ БАЗ
- •7.2. Базы и их выбор
- •8. АНАЛИЗ ТЕХНОЛОГИЧНОСТИ КОНСТРУКЦИИ ДЕТАЛИ
- •13. СХЕМЫ ФОРМИРОВАНИЯ И РАСЧЁТ ПРОМЕЖУТОЧНЫХ РАЗМЕРОВ ОБРАБАТЫВАЕМОЙ ДЕТАЛИ
- •15. ТЕХНИЧЕСКОЕ НОРМИРОВАНИЕ СТАНОЧНЫХ ОПЕРАЦИЙ
- •Библиографический список
- •Приложение 1
- •Приложение 2
- •Приложение 3
- •Приложение 4
5. РАСЧЁТ ЗАГОТОВКИ, ПОЛУЧАЕМОЙ СПОСОБОМ ГОРЯЧЕЙ ОБЪЁМНОЙ ШТАМПОВКИ
Направленность раздела:
1. Ознакомление с правилами расчёта размеров заготовки, получаемой способом горячей объёмной штамповки.
Чертёж поковки разрабатывается по чертежу готовой детали в соответст-
вии с ГО Т 7505-89 [10].
При разработке чертежа поковки (заготовки) необходимо прежде всего ре-
шить следующ е вопросы [1, 7]: |
|
|||
- установ ть положен е поковки в штампе; |
|
|||
- выбрать плоскость разъёма штампа; |
|
|||
- определ ть вел ч ну припусков и допусков. |
|
|||
С |
|
|
||
Форм рован е поковки производится в обеих частях штампа, что способ- |
||||
ствует более свободному |
звлечению поковки, улучшает её формирование. |
|||
Наиболее глубок е |
трудно заполняемые полости должны располагаться: |
|||
- |
штамповке на молоте - в верхней части штампа; |
|
||
- |
штамповке на кр вошипном горячештамповочном прессе (КГШП) - |
|||
при |
|
|||
в нижней части штампа. |
допусков зависят от исходного индекса, |
|
||
Велич ны пр пусков |
который |
|||
является обобщенным параметром, определяемым в зависимости от массы по- |
||||
ковки, группы стали, степени сложности и класса точности изготовления. |
||||
Ориентировочную величину расчётной массы поковки (Мпр) допускается |
||||
вычислить по формуле: |
Мпр = Мд * Кр, |
(5.1) |
||
где Мпр |
|
|
||
– предварительная расчётная масса поковки, кг; |
|
|||
Мд |
бА |
|
||
– масса готовой детали, кг. Определяется расчётным путём; |
|
|||
Кр –расчётный коэффициент. |
и т.д.) |
|||
Для |
поковок |
круглых |
в плане (шестерни, ступицы, фланцы |
Кр = 1,5…1,8.
Д Группа стали определяется в зависимости от среднегоИмассового содержа-
ния углерода и легирующих элементов (Si, Mn, Cr, Ni, W, V и т.д.).
ГОСТ 7505-89 предусматривает три группы стали:
М1 – сталь с массовой долей углерода до 0,35% или суммарной массовой долей легирующих элементов до 2%; М2 – сталь с массовой долей углерода свыше 0,35 до 0,65% или суммарной долей легирующих элементов от 2 до 5% включительно; М3 – сталь с массовой долей углерода свыше 0,65% или суммарной долей легирующих элементов свыше 5%.
Разделение сталей на указанные группы учитывает различное сопротивление деформированию и, следовательно, различный по интенсивности износ штампов.
Степень сложности С определяется путём вычисления отношения массы Мп (объёма Vп) поковки к массе Мф (объёму Vф) геометрической фигуры, в которую вписывается форма поковки:
26
С = Мп / Мф = Vп / Vф. |
(5.2) |
В зависимости от величины C установлены четыре степени сложности штамповочных поковок: С 1 – свыше 0,63; С 2 – от 0,32 до 0,63 включительно;
3 – от 0,16 до 0,32 включительно; С 4 – до 0,16.
Класс точности поковки устанавливается в зависимости от оборудования для её изготовления, а также исходя из предъявляемых требований к точности размеров поковки. Обычно класс точности при штамповке на паровоздушном
молоте равен Т5, при штамповке на кривошипном горячештамповочном |
про- |
|
цессе Т4, при штамповке на горизонтально-ковочной машине ещё выше – Т3. |
||
После определен я кол чественного значения всех установленных |
|
|
ГО Т 7505–89 параметров определяется исходный индекс. |
|
|
Для определен я сходного индекса в графе «Масса поковки» (ГОСТ |
||
7505–89) находят соответствующую данной массе строку и перемещаются по |
||
С |
|
|
горизонтали вправо |
ли по утолщенным наклонным линиям вправо вниз до пе- |
|
ремещен я с верт кальными линиями, соответствующими заданным значениям |
||
группы стали М, степени сложности С, класса точности Т, а затем до колонки |
||
«Исходный ндекс». |
|
|
на пр пуска на механическую обработку Z по ГОСТ 7505–89 уста- |
||
Велич |
|
|
навливается на |
атываемую поверхность и определяется в зависимости от |
|
исходного ндекса, размеров детали и шероховатости поверхности (табл.5.1). |
||
Номинальные диаметральные размеры поковки рассчитываются так: |
|
|
- для наружных поверхностей: |
|
|
обра |
(5.3) |
|
|
Dп = Dд +2 Z , |
|
где Dд - диаметр детали; |
|
|
- для внутренних поверхностей: |
|
|
|
dп = dд – 2 Z, |
(5.4) |
где dд - диаметр полостиА. |
|
|
|
Д |
|
При определении припуска на механическую обработку центрального отверстия следует иметь в виду, что наметки в поковках с последующей прошивкой делаются только при диаметре центрового отверстия готовой детали не менее 30 мм. Для небольших отверстий (диаметром менее 30 мм) и в высоких поковках делают неглубокие наметки с двух сторон. В этом случае отверстия получают не прошивкой на прессе, а сверлением и растачиванием. Наличие наме-
ток под отверстия несколько уменьшают объём механической обработки.
На поверхностях, входящих в состав линейныхИразмеров детали (длина L, высота H), размеры припусков могут различаться в связи с различием шерохо-
ватостей. Поэтому |
|
Hп(п) = Hд(Lд) + Z1 +Z2, |
(5.5) |
если припуски Z1 и Z2 на противоположных сторонах не равны.
27
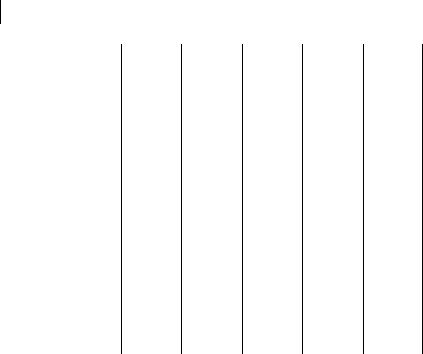
Таблица 5.1
Основные пр пуски на механическую обработку (на сторону) [10]
|
|
|
и |
|
|
|
|
|
|
|
|
|
|
|
|
|
||||||
Исходный индекс |
|
|
|
|
|
Дл на, ш р на, диаметр, глубина и высота детали, мм |
|
|
|
|
|
|||||||||||
|
|
До 40 |
|
От 40 до 100 |
|
От 100 до 160 |
От 160 до 250 |
0т 250 до 400 |
||||||||||||||
|
С |
|
|
|
|
|
|
|
|
|
|
|
|
|||||||||
|
|
|
|
|
Шероховатость поверхности детали, мм |
|
|
|
|
|
|
|
||||||||||
|
100 |
10 |
1,25 |
100 |
|
|
10 |
1,25 |
100 |
|
10 |
1,25 |
100 |
|
10 |
|
1.25 |
100 |
10 |
1,25 |
||
|
12,5 |
1,6 |
|
|
|
б |
1,6 |
|
12,5 |
|
1.6 |
|
|
|
12,5 |
1.6 |
|
|||||
|
|
12,5 |
|
1,6 |
|
12,5 |
|
|
|
|
|
|
|
|||||||||
9 |
1,0 |
1,3 |
1,4 |
1,1 |
|
|
1,4 |
1,5 |
1,2 |
|
1,5 |
1,6 |
1,3 |
|
1,6 |
|
|
1,8 |
1,4 |
1,7 |
1,9 |
|
10 |
1,1 |
1,4 |
1,5 |
1,2 |
|
|
1,5 |
1,6 |
1,3 |
|
1,6 |
1,8 |
1,4 |
|
1,7 |
|
|
1,9 |
1,5 |
1,8 |
2,0 |
|
11 |
1,2 |
1,5 |
1,6 |
1,3 |
|
|
1,6 |
1,8 |
1,4 |
|
1,7 |
1,9 |
1,5 |
|
1,8 |
|
|
2,0 |
1,7 |
2,0 |
2,0 |
|
12 |
1,3 |
1,6 |
1,8 |
1,4 |
|
|
1,7 |
1,9 |
1,5 |
|
1,8 |
2,0 |
1,7 |
|
2,0 |
|
|
2,2 |
1,9 |
2,3 |
2,5 |
|
13 |
1,4 |
1,7 |
1,9 |
1,5 |
|
|
1,8 |
А |
1,9 |
|
2,3 |
|
|
2,5 |
2,0 |
2,5 |
2,7 |
|||||
|
|
2,0 |
1,7 |
2,0 |
2,2 |
|
|
|
||||||||||||||
14 |
1,5 |
1,8 |
2,0 |
1,7 |
|
|
2,0 |
2,3 |
1,9 |
2,3 |
2,5 |
2,0 |
|
2,5 |
|
|
2,7 |
2,2 |
2,7 |
3,0 |
||
15 |
1,7 |
2,0 |
2,2 |
1,9 |
|
|
2,3 |
2,5 |
2,0 |
2,5 |
2,7 |
2,2 |
|
2,7 |
|
|
3,0 |
2,4 |
3,0 |
3,3 |
||
16 |
1,9 |
2,3 |
2,5 |
2,0 |
|
|
2,5 |
2,7 |
2,2 |
2,7 |
3,0 |
2,4 |
|
3,0 |
|
|
3,3 |
2,6 |
3,2 |
3,5 |
||
17 |
2,0 |
2,5 |
2,7 |
2,2 |
|
|
2,7 |
3,0 |
2,4 |
3,0 |
3,3 |
2,6 |
|
3,2 |
|
|
3,5 |
2,8 |
3,5 |
3,8 |
||
18 |
2,2 |
2,7 |
3,0 |
2,4 |
|
|
3,0 |
3,3 |
2,6 |
Д |
|
3,8 |
3,0 |
3,8 |
4,1 |
|||||||
|
|
3,2 |
3,5 |
2,8 |
|
3,5 |
|
|
||||||||||||||
19 |
2,4 |
3,0 |
3,3 |
2,6 |
|
|
3,2 |
3,5 |
2,8 |
3,5 |
3,8 |
3,0 |
|
3,8 |
|
|
4,1 |
3,4 |
4,3 |
4,7 |
||
20 |
2,6 |
3,2 |
3,5 |
2,8 |
|
|
3,5 |
3,8 |
3,0 |
3,8 |
4,1 |
3,4 |
|
4,0 |
|
|
4,7 |
3,7 |
4,7 |
5,1 |
На все полученные размеры поковки по табл.5.2 определяются поля допусков и допускаемые отклонения размеров. По полученным данным формируются чертежи «холодной поковкиИ» (рис. 5.1), а затем чертежи «горячей поковки». Последние отличаются тем, что все размеры изменяются на 1,5 % (усадка), а высотные размеры проставляются от
линии разъема.
28
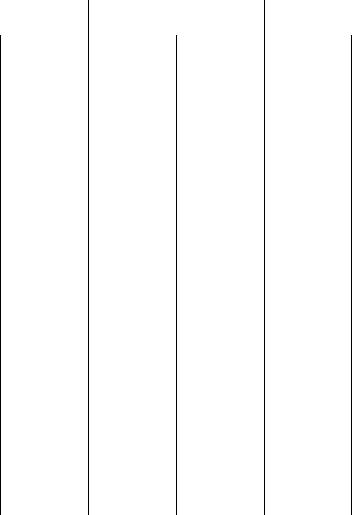
|
С |
|
|
|
|
|
|
|
|
Таблица 5.2 |
|||||
|
|
|
|
Допуски |
допускаемые отклонения линейных размеров поковок [10] |
|
|
|
|||||||
|
|
|
|
рина |
|
|
|
|
|
|
|
|
|||
Исходный |
|
|
|
|
Дл на, ш |
, диаметр, глубина и высота поковок, мм |
|
|
|
||||||
индекс |
|
|
До 40 |
От 40 до 100 |
|
От 100 до 160 |
От 160 до 250 |
От 250 до 400 |
|||||||
9 |
|
1,2 |
|
+0,8 |
1,4 |
+0,9 |
|
1.6 |
|
+1,1 |
2,0 |
+1,3 |
2,2 |
|
+1,4 |
|
|
|
|
-0,4 |
|
-0,5 |
|
|
|
-0,5 |
|
-0,7 |
|
|
-0,8 |
10 |
|
1,4 |
|
+0,9 |
1,6 |
+1,1 |
|
2,0 |
|
+1,3 |
2,2 |
+1,4 |
2,5 |
|
+1,6 |
|
|
|
|
-0,5 |
|
-0,5 |
|
|
|
-0,7 |
|
-0,8 |
|
|
-0,9 |
11 |
|
1,6 |
|
+1,1 |
2,0 |
+1,3 |
|
2,2 |
|
+1,4 |
2,5 |
+1,6 |
2,8 |
|
+1,8 |
|
|
|
|
-0,5 |
|
-0,7 |
|
|
|
-0.8 |
|
-0,9 |
|
|
-1,0 |
12 |
|
2,0 |
|
+1,3 |
2,2 |
А |
2,8 |
+1,8 |
3,2 |
|
+2,1 |
||||
|
|
+1,4 |
|
2,5 |
|
+1,6 |
|
||||||||
|
|
|
|
-0,7 |
|
-0,8 |
|
|
|
-0,9 |
|
-1,0 |
|
|
-1,1 |
|
|
|
|
|
б |
|
|
|
|
|
|
||||
13 |
|
2,2 |
|
+1,4 |
2,5 +1,6 2,8 |
|
+1,8 |
3,2 |
+2,1 |
3,6 |
|
+2,4 |
|||
|
|
|
|
-0,8 |
|
-0,9 |
|
|
|
-1,0 |
|
-1,1 |
|
|
-1,2 |
14 |
|
2,5 |
|
+1,6 |
2,8 |
+1,8 |
|
3,2 |
|
+2,1 |
3,6 |
+2,4 |
4,0 |
|
+2,7 |
|
|
|
|
-0,9 |
|
-1,0 |
|
Д |
-1,2 |
|
|
-1,3 |
|||
|
|
|
|
|
|
|
|
-1,1 |
|
|
|
||||
15 |
|
2,8 |
|
+1,8 |
3,2 |
+2,1 |
|
3,6 |
|
+2,4 |
4,0 |
+2,7 |
4,5 |
|
+3,0 |
|
|
|
|
-1,0 |
|
-1,1 |
|
|
|
-1,2 |
|
-1,3 |
|
|
-1,5 |
16 |
|
3,2 |
|
+2,1 |
3,6 |
+2,4 |
|
4,0 |
|
+2,7 |
4,5 |
+3,0 |
5,0 |
|
+3,3 |
|
|
|
|
-1,1 |
|
-1,2 |
|
|
|
-1,3 |
|
-1,5 |
|
|
-1,7 |
17 |
|
3,6 |
|
+2,4 |
4,0 |
+2,7 |
|
4,5 |
|
И |
5,6 |
|
+3,7 |
||
|
|
|
|
+3,0 |
5,0 |
+3,3 |
|
||||||||
|
|
|
|
-1,2 |
|
-1,3 |
|
|
|
-1,5 |
|
-1,7 |
|
|
-1,9 |
18 |
|
4,0 |
|
+2,7 |
4,5 |
+3,0 |
|
5,0 |
|
+3,3 |
5,6 |
+3,7 |
6,3 |
|
+4,2 |
|
|
|
|
-1,3 |
|
-1,7 |
|
|
|
-1,7 |
|
-1,9 |
|
|
-2,1 |
19 |
|
4,4 |
|
+3,0 |
5,0 |
+3,3 |
|
5,6 |
|
+3,7 |
6,3 |
+4,2 |
7,1 |
|
+4,7 |
|
|
|
|
-1,5 |
|
-1,7 |
|
|
|
-1,9 |
|
-2,1 |
|
|
-2,4 |
29
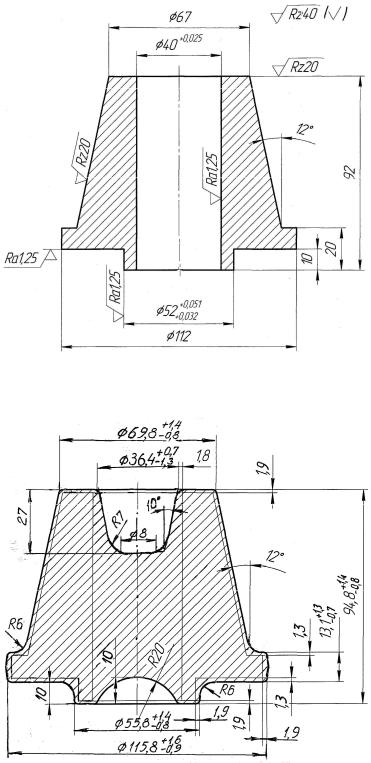
С |
|
и |
|
бА |
|
|
а |
|
Д |
б |
И |
|
Рис.5.1. Чертежи: а – детали «опора»; б – заготовки-штамповки (тонкими линиями нанесены контуры детали)
30
|
Контрольные вопросы |
1. |
Какое оборудование применяется при горячей объёмной штамповке? |
2. |
Как должна располагаться поковка в штампе? |
3. |
Что такое исходный индекс, как он определяется? |
4. |
Как определяется степень сложности поковки? |
С |
|
5. |
К какой группе сталей относятся стали марки 30ХГТ, 30, 30ХН3А, 50Х? |
6. От каких параметров зависит припуск на механическую обработкудетали? |
|
7. |
Каков принцип определения исходного индекса? |
8. |
При как х размерах отверстий в деталях можно намечать их в поковках |
под прош вку? |
|
и |
6. АНАЛИЗ ВОЗНИКНОВЕНИЯ ПОГРЕШНОСТЕЙ ОБРАБОТКИ ДЕТАЛЕЙ ТИПА ВАЛОВ ПРИ ТОЧЕНИИ
Валы являютсябАодними из наиболее распространенных и ответственных деталей, от точности и качества изготовления которых во многом зависит срок эксплуатации машин.
НА ТОКАРНЫХ СТАНКАХ
Направленность раздела:
1. Ознакомлен е с пр чинами возникновения погрешностей обработки де-
талей типа валов при точен и на токарных станках.
2. Определение величины упругих отжатий заготовки вала удинзаг (Х) от вер-
шины резца при точении.
3. Определить условия, при которых возможно обеспечить максимальную
точность обработки деталей типа валов. Д
Основными техническими требованиями являются:
-прямолинейность и соосность участков вала;
-правильность геометрической формы в поперечных и продольных сечениях вала (отсутствие овальности, конусности, бочкообразности и т. д.).
Так как конструкция вала предрасположена к упругим деформациям от действия режущего инструмента, то для выполнения вышеперечисленных технических требований необходимо создание определенных условий закрепления деталей на станке, которые обеспечивали бы наименьшие упругие деформации вала в процессе его обработки. Основным критерием при выборе способа закрепления заготовки вала на токарном станке является отношение её длины ℓ к её диаметру d.
Цилиндрические детали малой относительной длины (ℓ/d ≤ 4) хорошо закрепляются консольно в трехкулачковом самоцентрирующем патроне.
Для цилиндрических деталей средней относительной длины (4 < ℓ/d ≤ 10)
сцелью повышения их жесткости при обработке используются дополнительные опоры. В качестве дополнительной опоры правого конца вала применяютсяИ
31
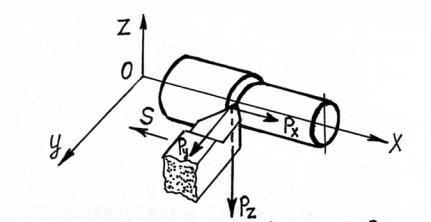
жесткие (невращающиеся и вращающиеся) центры, которые устанавливаются в пиноли задней бабки. На правом торце заготовки в этом случае засверливают центровое конически-цилиндрическое отверстие, в которое входит конец центра. Центровые отверстия выполняют по ГОСТ 14034–74 специальными центровочными сверлами. При этом левый конец вала может закрепляться либо в трехкулачковом самоцентрирующем патроне, либо опираться на передний
Сцентр (этот способ закрепления детали называют “обработка в центрах”. При обработке в центрах крутящий момент на деталь передается поводковым патроном и хомутиком.
При обработке дл нных валов (ℓ/d >10) применяют люнеты, предохра-
няющие заготовку от прог ба. Люнет выступающими регулируемыми опорами настраиваютУсилв прот воположную по отношению к режущему инструменту
сторону вала. Пр меняются неподвижные люнеты (станина люнета крепится на станине станка) подв жные (корпус люнета крепится на суппорте станка).
ями, вызывающ ми упругую деформацию всех составляющих системы ПИД (станокбА– пр спосо ление – инструмент – деталь), являются составляющ е с лы резан я Px, Py, Pz в направлениях осей прямоугольной системы коорд нат XYZ (р с. 6.1).
Рис. 6.1. СоставляющиеДсилы резанияИ:
Px – осевая; Py – радиальная; Pz – тангенциальная
Жесткостью СПИД, J (кгс/мм), называется отношение радиальной составляющей силы резания Py (кгс) к суммарному смещению Y (мм) лезвия режущего инструмента относительно обрабатываемой поверхности заготовки, измеряемому в направлении нормали к этой поверхности [12], т.е.
J = Pу / Y.
Система СПИД при работе станка может подвергаться динамическим нагрузкам, которые зависят от состояния поверхности обрабатываемой заготовки, степени износа режущего инструмента, режимов резания (глубина резания, величина подачи, скорость резания) и многого другого.
Чтобы охарактеризовать систему СПИД в рабочем состоянии вводится динамический коэффициент µ, который, как показывают опытные результаты,
32
изменяется в достаточно широких пределах. Так, например, с повышением скорости резания от 7,6 до 237,5 м/мин µ при черновом точении и в зависимости от способа закрепления детали на станке возрастает [12]:
-при консольном закреплении в патроне – от 1,10 до 1,22;
-при закреплении в патроне и в центре – от 1,16 до 1,47;
-при закреплении в центрах – от 1,15 до 1,61.
Радиальная составляющая силы резания Py рассчитывается по [2]:
где Cp, x, y, n – зав сят от конкретных условий обработки [2]; t – длина лезвия
|
резца; S – подача; υ –скорость резания; Kp – поправочный коэффициент. |
|
|
|||||||||||||
|
ми параметрамиматер алом ра очей части резца, глубину срезаемого слоя в |
|||||||||||||||
|
В данном случае часть коэффициентов приведена в табл. 6.1. |
|
|
|
||||||||||||
Следует меть в в ду, что усилие резания Ру определяется для каждой кон- |
||||||||||||||||
|
кретной операц |
|
перехода, |
для выполнения которых технолог прежде всего |
||||||||||||
|
планирует ( спользуя со ственный практический опыт и рекомендации спра- |
|||||||||||||||
|
|
бА |
|
|
|
|
|
|||||||||
|
вочной л тературы) вы ор спосо а установки (закрепления) обрабатываемой |
|||||||||||||||
|
детали на станке, |
т п режущего инструмента с необходимыми геометрически- |
||||||||||||||
|
зависимости от пр пуска выполняемого перехода (черновое, |
чистовое точе- |
||||||||||||||
|
ние и т.д.), вел ч ну подачи и т.д. Ориентиром является и марка обрабатывае- |
|||||||||||||||
|
мого материала. |
|
|
|
|
|
|
|
|
|
|
|
|
|
|
|
|
|
|
|
|
|
|
|
|
|
|
|
|
Таблица 6.1 |
|||
|
Обрабатываемый |
|
Материал |
Вид |
|
|
|
Коэффициент и показатели сте- |
|
|||||||
|
материал |
|
|
рабочей |
обработки, |
Д |
|
|
||||||||
|
|
|
пени в формулах для составляю- |
|
||||||||||||
|
|
|
|
части |
точение |
|
|
|
|
щих |
|
|
||||
|
|
|
|
резца |
|
|
|
|
|
|
радиальной Py |
|
|
|||
|
|
|
|
|
|
|
|
|
|
Ср |
х |
|
|
y |
n |
|
|
Конструкционные |
|
Твердый |
Продольное, |
|
|
|
|
|
|
|
|
||||
|
стали, σ=750МПа |
|
сплав |
поперечное |
|
243 |
0,9 |
|
|
0,6 |
-0,3 |
|
||||
|
Поправочный коэффициент Кр, учитывающий фактические условия реза- |
|||||||||||||||
|
ния, определяется по [2]: |
|
|
|
|
|
|
|
|
|
|
|
|
|||
|
|
|
|
Кр Кмр Кφр Кγр Кrр , |
|
|
|
|
|
|
||||||
|
где Кмр – коэффициент, учитывающий влияние обрабатываемогоИматериала на |
|||||||||||||||
|
силовые зависимости. |
|
|
|
|
|
|
|
|
|
|
|
|
|||
|
При обработке резцами с твердым сплавом, |
|
|
|
|
|
|
|
||||||||
|
|
|
|
|
|
σ |
в |
0,75 |
|
|
|
|
|
|
|
|
|
|
|
|
|
Кмр |
|
|
, |
|
|
|
|
|
|
||
|
|
|
|
|
750 |
|
|
|
|
|
|
|||||
|
|
|
|
|
|
|
|
|
|
|
|
|
|
где σв – предел прочности обрабатываемой стали, МПа;
33
Кφр – коэффициент, учитывающий величину главного угла в плане проход-
ного резца (при φ = 45º, Кφр = 1,0 [2];
Кγр – коэффициент, учитывающий величину переднего угла режущей части резца (при γ = 10º, Кγр = 1 [2];
Кλр – коэффициент учитывающий величину угла наклона главного лезвия резца (при λ = 5º, Кλр = 1,25 [2];
Кrp – коэффициент, учитывающий величину радиуса закругления вершины
режущей части резца (при r = 1 мм, |
Кrр = 0,82 [2]. |
|
|||||||||
Упруг е отжат я заготовки определяются для случаев: |
|||||||||||
а) для услов |
й абсолютно жесткого станка упругое отжатие гладкого вала |
||||||||||
упругости |
|
|
|
|
|
|
|
|
|
||
Yзаг (Х), консольно-закрепленного в патроне, можно подсчитать по известным |
|||||||||||
Сформулам сопрот влен я материалов [13]: |
|
|
|||||||||
|
|
|
|
|
|
P 3 |
|
|
|||
|
|
|
Yзаг |
|
y |
|
, |
|
|
||
|
|
|
|
|
|
|
|||||
бА |
|||||||||||
|
|
|
|
|
|
3E J |
|
|
|||
где Е – модуль |
|
о ра атываемого материала, ГПА; |
|||||||||
J – момент |
нерц |
поперечного сечения вала, |
|||||||||
|
|
|
|
J |
|
πd4 |
|
|
|||
|
|
|
|
|
64 . |
|
|
|
|||
С учетом динамичности процесса точения |
|
|
|||||||||
|
|
дин |
|
P 3 64 |
|
|
|||||
|
|
|
y |
|
|
|
|
|
|||
|
|
Yзаг |
|
3Eπd4 . |
|
|
|||||
|
|
|
|
|
Д |
||||||
Определив значение Yдин (Х) для заданных отношений /d можно построить |
|||||||||||
|
|
заг |
|
|
|
|
|
|
|
|
|
упругую линию в произвольно выбранном масштабе и определить увеличение |
|||||||||||
диаметра вала ∆d(Х) |
по расчетной длине, оценить величину отклонений по |
||||||||||
классу точности. |
|
|
|
|
|
|
|
|
|
|
|
б) для условий абсолютно жесткого станка прогиб заготовки Yзаг (Х)при об- |
|||||||||||
работке в центрах определяется по [3]: |
|
x |
2 |
И |
|||||||
|
|
||||||||||
|
|
|
|
Py x |
2 |
|
|||||
|
|
Yзаг |
|
, |
|||||||
|
|
|
|
||||||||
|
|
|
|
|
|
3EJ |
|
|
|||
где x – расстояние от передней бабки станка. |
|
|
|||||||||
Наибольший |
прогиб заготовки |
вала |
|
находится в его средней части при |
x= 0,5ℓ.
Сучетом динамичности процесса точения
|
P X 2 |
|
X 2 μ64 |
||
Y дин |
y |
|
|
|
. |
заг |
3Eπd 4 |
|
34