
- •ВВЕДЕНИЕ
- •1. БАЗОВАЯ ИНФОРМАЦИЯ ДЛЯ ПРОЕКТИРОВАНИЯ ТЕХНОЛОГИЧЕСКИХ ПРОЦЕССОВ ПРОИЗВОДСТВА ДЕТАЛЕЙ МАШИН
- •3. ВЫБОР ЗАГОТОВКИ ИЗ СОРТОВОГО ПРОКАТА
- •5. РАСЧЁТ ЗАГОТОВКИ, ПОЛУЧАЕМОЙ СПОСОБОМ ГОРЯЧЕЙ ОБЪЁМНОЙ ШТАМПОВКИ
- •7. ОСНОВЫ ВЫБОРА ТЕХНОЛОГИЧЕСКИХ БАЗ
- •7.2. Базы и их выбор
- •8. АНАЛИЗ ТЕХНОЛОГИЧНОСТИ КОНСТРУКЦИИ ДЕТАЛИ
- •13. СХЕМЫ ФОРМИРОВАНИЯ И РАСЧЁТ ПРОМЕЖУТОЧНЫХ РАЗМЕРОВ ОБРАБАТЫВАЕМОЙ ДЕТАЛИ
- •15. ТЕХНИЧЕСКОЕ НОРМИРОВАНИЕ СТАНОЧНЫХ ОПЕРАЦИЙ
- •Библиографический список
- •Приложение 1
- •Приложение 2
- •Приложение 3
- •Приложение 4
13. СХЕМЫ ФОРМИРОВАНИЯ И РАСЧЁТ ПРОМЕЖУТОЧНЫХ РАЗМЕРОВ ОБРАБАТЫВАЕМОЙ ДЕТАЛИ
Направленность раздела:
1. Освоение правил формирования линейных и диаметральных размеров на операциях и переходах механической обработки заготовок.
Основой формирования схем обработки являются припуски на механическую обработку и требования к точности получаемых размеров и качеству поверхностей детали.
Припуски на механ ческую обработку подразделяются так [12]:
- общ й пр пуск – это слой материала, который необходимо удалить с по-
верхности заготовки; |
|
|
|
С |
|
|
|
- общ й ном нальный (расчетный) припуск Z – это слой металла, опреде- |
|||
ляемый разностью ном |
нальных размеров исходной заготовки D исх и готовой |
||
детали D дет; |
|
|
|
- операц онный |
пуск – это слой материала, удаляемый с поверхности |
||
заготовки |
выполнен |
конкретной технологической операции |
|
при |
|||
(ГОСТ 3.1109–82). |
|
|
|
|
бА |
Общ й ном нальный припуск равняется сумме промежуточных припусков, назначенных на отдельные переходы, например, черновое точение, получистовое точение, чистовое точение, черновое развертывание, чистовое развертывание, предварительное (о дирочное, черновое) шлифование, окончательное
(чистовое, тонкое) шлифование и т.д.
После назначения промежуточных припусков производится расчет промежуточных размеров обрабатываемой детали: сначала линейных, затем диаметральных размеров, образующих размерные цепи, в которых замыкающим зве-
Д ваемой детали между операциями и переходами. И
ном являются размеры по рабочему чертежу готовой детали [23, 24].
Схемы формирования размеров позволяют выделить технологические размерные цепи, на основе которых осуществляется расчет размеров обрабаты-
Исходными данными для схем формирования линейных и диаметральных
технологических размеров являются: рабочий чертеж детали, чертеж заготовки и план механической обработки детали.
Методику построения схем формирования линейных и диаметральных размеров рассмотрим на примере детали “Зубчатое колесо” (рис. 13.1). План механической обработки рассмотрен ранее.
По плану механической обработки детали “Зубчатое колесо” получены технологические операционные промежуточные размеры снимаемых слоев общего номинального припуска для всех обрабатываемых поверхностей (табл.13.1), которые будут использованы для пояснения схем формирования линейных и диаметральных размеров.
73
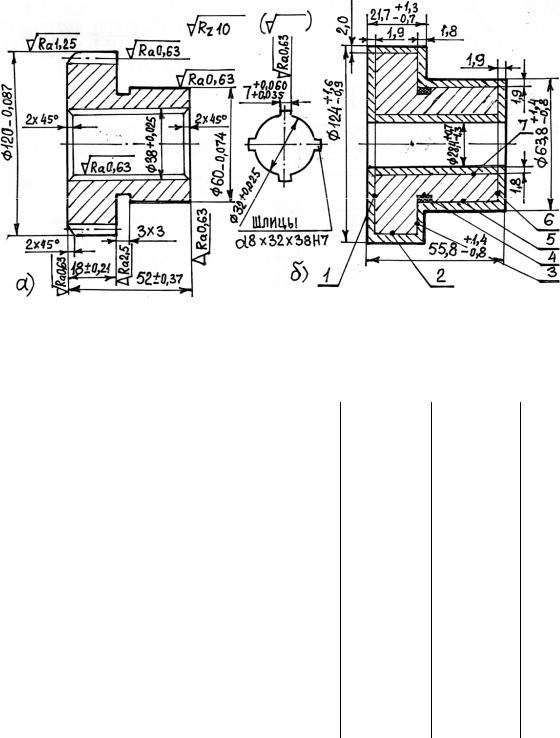
С |
|
|
|
|
|
|
|
|
|||
|
Чертежи |
|
|
Таблица 13.1 |
|||||||
|
|
|
бА |
|
|
|
|||||
|
Р с. 13.1. |
: а – ра очий; |
– заготовки детали “Зубчатое колесо” |
||||||||
|
Промежуточные размеры снимаемых слоев общего припуска, мм |
||||||||||
|
Номер |
|
1 |
|
2 |
|
3 |
5 |
6 |
7 |
|
|
поверхности |
|
|
|
|
|
|
|
|
|
|
|
Общий при- |
|
1,9 |
|
2,0 |
|
1,8 |
1,9 |
1,9 |
1,8 |
|
|
пуск на по- |
|
|
|
|
|
|
|
|
|
|
|
верхность де- |
|
|
|
|
|
|
|
|
|
|
|
тали |
|
|
|
|
|
|
|
|
|
|
|
Черновая об- |
|
Z 10.1=1,3 |
|
Z 10.2=1,4 |
|
Z 5.1=1,2 |
Z 5.3=1,3 |
Z 5.2=1,3 |
Z 5.4=0,55 |
|
|
работка |
|
|
|
|
|
|
|
|
|
|
|
Чистовая об- |
|
Z 15.1=0,35 |
|
Z15.3=0,35 |
|
Z 25.1=0,4 |
Z 25.5=0,35 |
Z25.3=0,35 |
Z 20.1=0,2 |
|
|
работка |
|
|
|
|
|
|
|
|
|
|
|
Тонкая обра- |
|
Z 15.2=0,2 |
|
Z 15.4=0,2 |
|
Z 25.2=0,2 |
Z 25.6=0,2 |
Z 25.4=0,2 |
|
|
|
ботка |
|
|
|
|
|
|
|
|
|
|
|
Протягивание |
|
|
|
|
|
|
|
|
Z 30.1=1,0 |
|
|
шлицевого |
|
|
|
|
|
|
|
И |
|
|
|
|
|
|
|
|
Д |
|
|
|||
|
отверстия |
|
|
|
|
|
|
|
|||
|
Шлифование |
|
Z 45.3=0,05 |
|
Z45.1=0,05 |
|
|
Z 45.2=0,05 |
Z 50.2=0,05 |
Z50.1=0,05 |
|
|
чистовое |
|
|
|
|
|
|
|
|
|
|
|
окончательное |
|
|
|
|
|
|
|
|
|
|
|
Размеры по рабочему чертежу |
детали на схеме обозначают: линейные – |
|||||||||
|
символом S, диаметральные – символом D. Им присваивается произвольно по- |
||||||||||
|
рядковый номер. В приводимом примере размеры детали “Зубчатое колесо” |
||||||||||
|
обозначим: |
линейные – 52±0,37 (S1); |
18±0,21 (S2); диаметральные – |
|
|
d 120 – 0,087(D1); d 60 – 0,074 (D2) и d32 + 0,025 (D3), (см. рис. 13.1).
Размеры исходной заготовки обозначают: линейные – А0, диаметральные – d0, которым присваивается произвольно порядковый номер. В данном случае
74
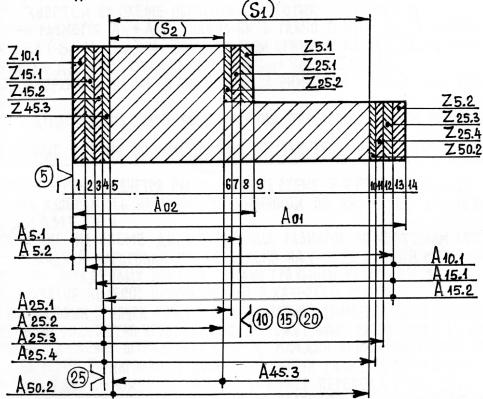
размеры заготовки обозначим: линейные –55,8 10,,48(А01), 21,7 10,,37(А02); диамет-
ральные –D124 10,,68(d01), D63,8 10,,48(d02), D28,4 10,,37 (d03 ) (см. рис.13.1,б).
При формировании схемы линейных размеров ось заготовки рекомендуется располагать на схеме горизонтально [23].
Си
Рис. 13.2.бАСхема формирования линейныхД(технологических) размеров при механической обработке заготовки детали “Зубчатое колесо”
Схема формирования линейных технологических размеров строится в соответствии с разработанным планом механической обработки. На эскизе заготовки (рис. 13.2) проставляются линейные пронумерованныеИсимволы разме-
ров. В данном примере для детали – это S1 и S2, для исходной заготовки – A01
и A02.
Общий номинальный припуск каждой обрабатываемой линейной поверхности разделяется на количество необходимых промежуточных слоев (табл.13.1), которые разделяются на схеме штриховкой (см. рис. 13.2). Каждый снимаемый слой общего припуска на схеме формирования линейных размеров обозначают символом Zlj, где i – номер операции, j – номер перехода
(см. рис. 13.2).
Составляющими звеньями размерных цепей являются технологические размеры Аlj (размеры при каждом переходе), где i – номер операции, j - номер
перехода. Размеры Аlj наносятся на схему в порядке выполнения операций и
75
переходов; стрелки для конкретного перехода проставляются в сторону снимаемого слоя припуска с указанием шариком поверхности, от которой производится контроль получаемого размера.
хему обработки следует проверить [23]:
- количество технологических размеров А0 Аlj должно быть на единицу
меньше, чем число поверхностей на схеме обработки (рис.2). В приведенном примере (см. рис. 13.2) имеется А0 два размера ( А01и А02) и 11 размеров Аlj ,
т.е. их сумма составляет 13 технологических размеров, т.е. на единицу меньше, чем число поверхностей на схеме обработки, которых 14;
- кол чество размеров А0 Аlj должно быть равно сумме S0 (в данном
примере х два (S01 |
S02 ) и Zlj (в данном примере их 11), т.е. численность |
|||||||||||
А (А А |
) А |
13 |
совпадает с S |
0 |
(S |
01 |
S |
02 |
) Z |
ljj |
13. |
|
С0 01 02 lj |
|
|
|
|
|
|||||||
Базовые поверхности на схеме о означаются символом, где i – номер опе- |
||||||||||||
рации. |
|
зображается |
|
|
|
|
||||||
метру. |
|
|
|
|
|
|||||||
Удален е |
напуска на схеме формирования линейных размеров не указы- |
|||||||||||
вается. |
|
|
|
|
|
|
|
|
|
|
|
|
Припостроен схемы формирования диаметральных размеров ось заго- |
||||||||||||
товки рекомендуется располагать на схеме вертикально [24]. |
||||||||||||
lj |
|
|
|
А |
||||||||
Заготовка |
|
|
уменьшенной по высоте, но увеличенной по диа- |
Общий номинальный припуск для каждой обрабатываемой диаметральной поверхности разделяется на количество необходимых промежуточных слоев (см. табл.13.1). На схеме они штрихуются в разные стороны. Каждый снимаемый слой на схеме формирования диаметральных размеров обозначают символом Z , где i – номер операции, j – номер перехода (рис. 13.3).
Составляющими звеньями размерных цепей являются технологические размеры dlj , которые наносятся на схему в порядке выполнения операций и
переходов; стрелки для конкретного перехода проставляются в сторону сни-
маемого слоя припуска. |
Д |
|
|
Базовые поверхности на схеме обозначаются символом, как и на схеме |
|
формирования линейных размеров, i – номер операции. |
|
Поверхности по рекомендации [24] на схеме пронумеровываются теми же |
|
индексами, которыми обозначены размеры заготовки, операции переходы. |
|
Известными составляющими размерных цепей являются номинальные |
|
|
И |
размеры готовой детали и заготовки, которые в приведенном примере состав- |
|
ляют: S1 52мм, S2 18мм, |
А01 55,8мм, А02 21,7мм. |
Номинальные промежуточные размеры снимаемых слоев общего номинального припуска приведены в табл.13.1 и рис. 13.2. Неизвестными являются размеры Аlj , получаемые в ходе выполнения операций и переходов.
76
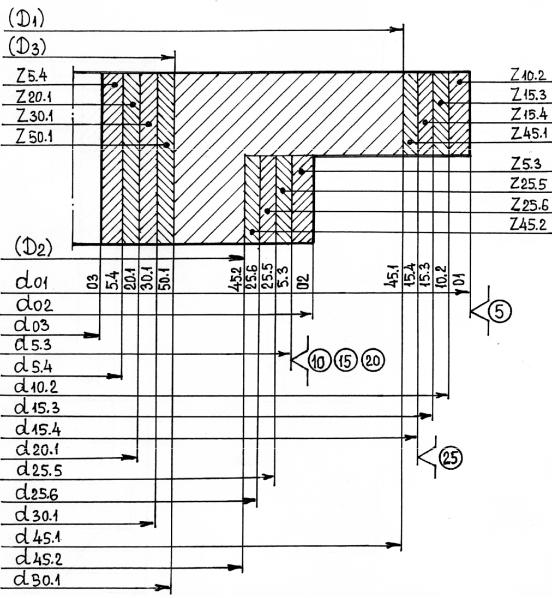
Си бА
Рис.13.3. Схема формированияДдиаметральных размеров при механической обработке заготовкиИ
Размеры необходимо знать, так как они служат для настройки станков, контроля получаемых промежуточных размеров в процессе механической обработки детали и т.д. S1 и S2 в данном случае являются итоговыми линейными размерами детали, поэтому с них и следует начинать определение значений промежуточных размеров Аlj. Результаты расчёта линейных промежуточных раз-
меров:
1)А45.3 S2 18мм;
2)А25.2 S2 Z45.3 18,0 0,05 18,05мм;
3)А25.1 А25.2 Z25.2 18,05 0,2 18,25мм;
4)А5.1 А02 Z5.1 21,7 1,2 20,5мм;
5)А50.2 S1 52мм;
77
6)А25.4 S1 Z45.3 Z50.2 52 0,05 0,05 52,10мм;
7)А25.3 А25.4 Z25.4 52,1 0,2 52,3мм;
8)А15.2 А25.3 Z25.3 52,3 0,35 52,65мм;
9)А15.1 А15.2 Z15.2 52,65 0,2 52,85мм;
|
10) |
A10.1 A15.1 Z15.1 |
52,85 0,35 53,2мм; |
|||||||||
|
11) |
A5.2 A01 Z5.2 55,8 1,3 54,5мм. |
||||||||||
|
На каждый промежуточный размер назначается допуск в соответствии со |
|||||||||||
среднеэкономической точностью выбранного метода [1]. |
||||||||||||
|
Расчет промежуточных диаметральных технологических размеров заклю- |
|||||||||||
чается в последовательном прибавлении к номинальному размеру, заданному |
||||||||||||
на чертеже, ном нальных значений промежуточных припусков. Так как номи- |
||||||||||||
нальные значен я пр пусков Z |
lj |
задаются на поверхность (на сторону), поэто- |
||||||||||
С |
|
|
|
|||||||||
му |
|
|
|
|
|
|
промежуточные технологические размеры рассчитываются |
|||||
по формуле |
|
|
|
|
|
|
|
|
|
|||
|
|
|
|
|
|
|
|
d i 1 j |
dij 2Z ij |
|||
|
диаметральные |
|
||||||||||
|
Знак «+» – для расчетов наружных размеров, а знак «–» –для внутренних |
|||||||||||
цилиндрическ |
х поверхностей. |
|
|
|
||||||||
|
Результаты расчета диаметральных промежуточных размеров |
|||||||||||
(D1 120мм,D2 |
60мм,D3 |
32мм,d01 124мм,d02 63,8мм,d03 28,4мм): |
||||||||||
|
1) |
|
|
|
бА |
|||||||
|
d45.1 D1 120мм; |
|
|
|
|
|||||||
|
2) |
d45.2 D2 60мм; |
|
|
|
|
||||||
|
3) |
d50.1 D3 32мм; |
|
|
|
|
||||||
|
4) |
d30.1 d50.1 2Z50.1 |
32 2 0,05 31,9 |
мм; |
||||||||
|
5) |
d20.1 d30.1 2Z30.1 |
31,9 2 1,0 29,9 |
мм; |
||||||||
|
6) |
d5.4 d20.1 2Z20.1 29,9 2 0,2 29,5 |
мм; |
|||||||||
|
7) |
d25.5 d45.2 2Z45.2 |
60 2 0,05 60,1 |
мм; |
||||||||
|
8) |
d |
25.5 |
d |
25.6 |
2Z |
25.6 |
60,1 2 0,2 |
60,5мм; |
|||
|
|
|
|
|
|
|
|
|
Д |
|||
|
9) |
d5.3 d25.5 2Z25.5 60,5 2 0,35 |
61,2мм; |
|||||||||
|
10) d15.4 d45.1 2Z45.1 120 2 0,05 |
120,1мм; |
||||||||||
|
11) d15.3 d15.4 |
2Z15.4 |
120,1 2 0,2 |
120,5мм; |
||||||||
|
12) d10.2 d15.3 |
2Z15.3 |
120,5 2 0,35 121,2ммИ. |
На каждый технологический размер назначается допуск в соответствии со среднеэкономической точностью выбранного метода [1].
78
Контрольные вопросы
1. Как разделяется общий припуск на промежуточные слои при разработке плана механической обработки?
2. Какие размеры указываются на линейных и диаметральных схемах при расчёте промежуточных размеров заготовки на каждом переходе?
3. Как обозначаются на линейных и диаметральных схемах промежуточные слои?
4. Как определяются промежуточные размеры и их квалитет для запланированных переходов?
5. Как форм руются л нейные и диаметральные схемы?
6. Как м образом |
проверяется правильность построения схем формирова- |
|
ния промежуточных размеров? |
||
С |
о означаются номинальные линейные и диаметральные |
|
7. Как |
|
|
размеры детали заготовки? |
||
8. Как |
|
промежуточные слои припусков на схемах формиро- |
вания промежуточных размеров заготовки? |
||
9. Как |
|
азовые поверхности на схемах формирования про- |
буквами |
||
межуточных размеров? |
|
|
10. Особенность построения схемы формирования диаметральных размеров? |
||
|
обозначаются |
|
|
|
14. РАСЧЁТ РЕЖИМОВ РЕЗАНИЯ |
|
ПРИ МЕХ НИЧЕСКОЙ ОБРАБОТКЕ |
|
|
|
НА ТОК РНОМ СТАНКЕ |
|
|
А |
|
|
Д |
Направленность раздела:
1. Освоение элементов режимов резания (глубина резания, подача, скорость резания), принципов их назначения и расчёта.
2.Установление потребного количества рабочих переходов, значений глубины резания и подачи для назначенных рабочих переходов, обеспечивающих наименьшую продолжительность обработки и заданную точность размеров и шероховатости обрабатываемой поверхности детали.
3.Определение скоростей резания Vрасч. для всех назначенных переходов, частоты вращения nрасч. обрабатываемой детали.
Кэлементам резания относятся [2]: И
-глубина резания t, мм;
-подача S, мм/об;
-скорость резания V, м/мин.
При назначении элементов режима резания учитывается:
-характер обработки(точение,сверление,развёртывание,фрезерование ит.д.);
-тип и размеры инструмента (резцы, свёрла, фрезы и т.д.);
79
- материал режущей части инструмента (быстрорежущая сталь, твёрдый сплав и т. д.);
- материал заготовки и его состояние (вязкость, твёрдость и т. д.); - состояние поверхности заготовки (без корки, с коркой на прокате, поков-
ке или отливке); - тип и состояние оборудования (мощность, жёсткость и точность станка и
Ст. д.).
Назначение режимов резания начинается с установления размеров снимаемых слоёв припуска, т. е. глубины резания, в зависимости от класса точности размеров шероховатости обрабатываемой поверхности. Глубину резания t при
роховатости данной поверхности Rz80 и более [2, 3].
черновой (предвар тельной) обработке назначают по возможности максималь- лированиеную (до 70% размера пр пуска) вплоть до полного снятия припуска на обработку за од н проход при точности размера детали IT13– IT12 квалитета и ше-
При более высок х тре ованиях по точности размеров и шероховатости обрабатываемой поверхности назначают чистовые переходы (получистовое, чистовое или тонкое точен е), вплоть до отделочных операций – шлифование, по-
поверхностей набАстанках токарной группы приведены в табл.14.1 [21].
, хон нгован е, суперфиниширование.
На каждом последующем переходе назначается меньшая глубина резания, чем на предыдущем, с оставлением минимального слоя припуска для окончательной обработки. Например, при чистовой окончательной обработке для Ra3,2 глубина резания может составлять t = 0,5 – 1,0 мм, а при Ra ≤0,63 глубина
резания не может быть олее t = 0,1 – 4 мм.
Ориентировочные данные по точности обработки наружных и внутренних
Данные табл.14.1 позволяют рациональноДпланировать необходимое число перехода (черновое точение, получистовое, чистовое и т.д.) для достижения заданной точности размеров и шероховатости обрабатываемой поверхности детали. При этом число рабочих ходов перехода не должно превышать необходи-
мое, т.к. это уменьшит производительность труда, увеличит себестоимость деталей.
Подача S (мм/об) при черновом точении принимается максимально допус-
тимой по мощности оборудования, жёсткости системы СП |
(станок – при- |
способление – инструмент - деталь), прочности твёрдосплавной пластины резца |
|
и прочности его державки. Обычно эти значения при черновом точении для не- |
больших размеров деталей составляют: для сталей S = 0,3 – 3,0 мм/об; для чу- |
|
гунов S = 0,4 – 5,0 мм/об. |
И |
Рекомендуемые подачи при черновых и чистовых точениях приведены в табл. 14.2–14.4.
80
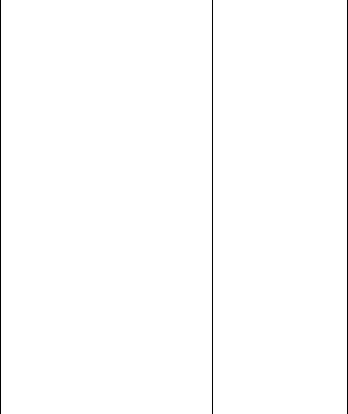
|
|
|
|
|
|
|
|
|
|
|
|
|
|
|
Таблица 14.1 |
|||
|
|
|
Точность обработки поверхностей на токарных станках |
|||||||||||||||
|
|
|
|
|
|
|
|
|
|
|
|
|
||||||
|
|
Вид обработки |
Квалитет точ- |
|
Параметр шероховатости, МКМ |
|||||||||||||
|
|
|
|
|
|
|
ности |
|
|
RZ |
|
|
|
Ra |
|
|||
|
|
Обтачивание: |
|
|
|
|
|
|
|
|
|
|
|
|
|
|
|
|
С |
|
13–12 |
|
|
80 |
|
|
|
|
|
|
|
||||||
|
|
черновое |
|
|
|
|
|
|
|
|
|
|
|
|||||
|
|
получистовое |
|
11–9 |
|
|
40–20 |
|
|
|
|
|
|
|||||
|
|
чистовое |
|
|
|
8–7 |
|
|
|
|
|
|
2,5 |
|
|
|||
|
|
тонкое |
|
|
|
|
7–6 |
|
|
|
|
|
1,25–0,63 |
|
||||
|
|
верление |
|
|
|
|
12–11 |
|
|
40–20 |
|
|
|
|
|
|
||
|
|
чистовоетонкое 6 |
|
|
|
|
|
|
0,16 |
|
|
|||||||
|
|
Зенкерован |
е: |
|
|
|
|
|
|
|
|
|
|
|
|
|
|
|
|
|
черновое |
|
|
12–11 |
|
|
40 |
|
|
|
|
|
|
|
|||
|
|
получ |
|
|
|
|
11 |
|
|
20 |
|
|
|
|
|
|
|
|
|
|
|
|
|
|
|
|
9–8 |
|
|
|
|
|
|
2,5 |
|
|
|
|
|
Развёртыван |
|
бА |
|
|
|
|
|
|
||||||||
|
|
|
: |
|
|
|
7–6 |
|
|
|
|
|
0,63–0,32 |
|
||||
|
|
Растачиван е: |
|
|
|
|
|
|
|
|
|
|
|
|
|
|
|
|
|
|
черновое |
|
|
13–12 |
|
|
80–40 |
|
|
|
|
|
|
||||
|
|
получистовое |
|
11–10 |
|
|
40–20 |
|
|
|
|
|
|
|||||
|
|
чистовое/тонкое |
9–7/6–5 |
|
|
|
|
|
2,5–0,63/0,32–0,08 |
|
||||||||
|
|
|
|
|
|
|
|
|
|
|
|
|
|
Таблица 14.2 |
||||
|
|
|
|
|
|
|
|
Д |
||||||||||
|
|
Подачи при черновом наружном точении резцами |
|
|
|
|
||||||||||||
|
|
с пластинами из твёрдого сплава и быстрорежущей стали[2] |
||||||||||||||||
|
|
|
|
|
|
|
|
|
Обрабатываемый материал |
|
||||||||
|
|
Диаметр |
|
Размер |
|
Сталь |
|
|
|
Чугун |
|
|||||||
|
|
|
|
|
И |
|
|
|||||||||||
|
|
детали, мм. |
державки |
|
|
|
|
|
|
и медные сплавы |
|
|||||||
|
|
|
|
|
резца, мм. |
|
Подача S, мм/об, при глубине резания t, мм |
|
||||||||||
|
|
|
|
|
|
|
|
До 3 |
|
Св.3 до 5 |
|
|
о 3 |
|
Св.3 до 5 |
|
||
|
|
Св. 20 до 40 |
От 16 X 25 |
|
0,4 – 0,5 |
|
0,3 – 0,4 |
|
0,4 – 0,5 |
|
|
|
|
|||||
|
|
|
|
|
до 25 X 25 |
|
|
|
|
|
|
|
|
|
|
|
|
|
|
|
Св. 40 до 60 |
От 16 X 25 |
|
0,5 – 0,9 |
|
0,4 – 0,8 |
|
0,6 – 0,9 |
|
0,5 – 0,8 |
|
||||||
|
|
|
|
|
до 25 X 40 |
|
|
|
|
|
|
|
|
|
|
|
|
|
|
|
Св. 60 до 100 |
От 16 X 25 |
|
0,6 – 1,2 |
|
0,5 – 1,1 |
|
0,8 – 1,4 |
|
0,7 – 1,2 |
|
|
|||||
|
|
до 25 X 40 |
|
|
|
|
|
Примечания: Нижние значения подач соответствуют меньшим размерам державки резца и более прочным обрабатываемым материалам, верхние значения подач – большим размерам державки резца и менее прочным обрабатываемым материалам.
81
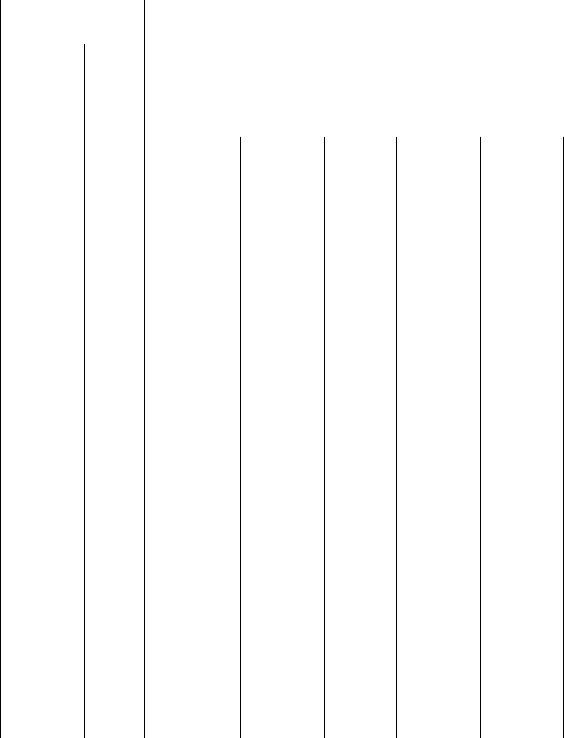
Таблица 14.3
Подачи при черновом растачивании резцами с пластинами из твёрдого сплава и быстрорежущей стали [2]
|
Резец или |
|
|
|
Обрабатываемый материал |
|
|
||||||
|
оправка |
|
|
|
|
|
|
|
|
|
|
|
|
|
Диаметр |
|
Сталь конструкционная углероди- |
|
Чугун |
|
|||||||
|
кругло- |
|
|
|
|||||||||
|
|
стая, легированная и жаропрочная |
|
и медные сплавы |
|
||||||||
|
го сече- |
Вы- |
|
|
|||||||||
|
|
|
|
|
|
|
|
|
|
|
|
||
|
ния |
Подача S, мм/об, при глубине резания t, мм |
|
|
|||||||||
|
лет |
|
|
||||||||||
|
оправки |
|
|
||||||||||
|
резца |
|
|
|
|
|
|
|
|
|
|
|
|
|
или |
|
|
|
|
|
|
|
|
|
|
|
|
|
ли |
|
|
|
|
|
|
|
|
|
|
|
|
|
размеры |
|
|
|
|
|
|
|
|
|
|
|
|
|
|
|
|
|
|
|
|
|
|
|
|
|
|
Соп- |
|
|
|
|
|
|
|
|
|
|
|
||
|
прямо- |
рав- |
|
|
|
|
|
|
|
|
|
|
|
|
уголь- |
2 |
|
3 |
|
5 |
2 |
|
3 |
|
5 |
|
|
|
ного |
ки, |
|
|
|
|
|
|
|
|
|
|
|
|
мм |
|
|
|
|
|
|
|
|
|
|
|
|
|
|
|
|
|
|
|
|
|
|
|
|
|
|
|
резца, |
|
|
|
|
|
|
|
|
|
|
|
|
|
сечения |
|
|
|
|
|
|
|
|
|
|
||
|
мм |
|
|
|
|
|
|
|
|
|
|
|
|
10 |
50 |
0,08 |
|
|
|
|
0,12– |
|
|
|
|
||
|
|
|
|
0,16 |
|
|
|
|
|
||||
|
|
|
|
|
|
|
|
|
|
|
|
|
|
12 |
60 |
0,1 |
|
0,08 |
|
0,12– |
0,12– |
|
|
|
|||
|
|
0,20 |
|
0,18 |
|
|
|
||||||
|
|
|
|
|
|
|
|
|
|
|
|
||
16 |
80 |
0,1– 0,2 |
|
0,15 |
0,10 |
0,2–0,3 |
0,15– |
|
0,1–0,18 |
|
|||
|
0,25 |
|
|
|
|||||||||
|
|
|
|
|
|
|
|
|
|
|
|
|
|
20 |
100 |
0,3–0,5 |
0,15– |
0,12 |
0,3–0,4 |
0,25– |
|
0,12– |
|
||||
|
|
|
|
|
|
|
|||||||
|
|
бА |
|
0,35 |
|
0,25 |
|
||||||
|
|
|
|
0,25 |
|
|
|
|
|
|
|||
25 |
125 |
0,35–0,50 |
0,15– |
0,12– |
0,4–0,6 |
0,3–0,5 |
|
0,25– |
|
||||
|
|
|
|
0,40 |
|
0,2 |
|
|
|
|
0,35 |
|
|
30 |
150 |
0,4–0,7 |
0,2–0,5 |
0,12– |
0,5–0,8 |
0,4–0,6 |
|
0,25– |
|
||||
|
|
|
|
|
|
|
0,3 |
|
|
|
|
0,45 |
|
|
|
|
|
|
|
Д |
|
|
|
||||
40 |
200 |
|
0,25– |
0,15– |
|
|
0,6–0,8 |
|
0,3–0,8 |
|
|||
|
0,60 |
|
0,4 |
|
|
|
|
||||||
|
|
|
|
|
|
|
|
|
|
|
|||
|
|
150– |
|
0,6–1,0 |
0,5–0,7 |
|
|
0,7–1,2 |
|
0,5–0,9 |
|
||
|
40X40 |
300 |
|
|
|
|
|
||||||
|
|
0,4–0,7 |
0,3–0,6 |
|
|
0,6–0,9 |
|
0,4–0,7 |
|
||||
|
|
|
|
|
|
|
|
||||||
|
|
|
|
|
|
|
|
И |
|
||||
|
60X60 |
150– |
|
0,9–1,2 |
0,8–1,0 |
|
|
1,0–1,5 |
0,8–1,2 |
|
|||
|
300 |
|
0,7–1,0 |
0,5–0,8 |
|
|
0,9–1,2 |
0,7–0,9 |
|
||||
|
|
|
|
|
|
82
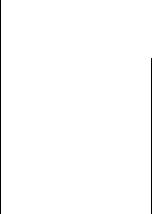
Таблица 14.4
Подачи при чистовом точении, мм/об [2]
|
Параметр шероховатости |
Радиус при вершине резца r, мм. |
||||
|
поверхности, мкм |
0,4 |
0,8 |
1,2 |
1,6 |
|
|
|
|
||||
С |
Rz |
|
|
|
|
|
|
Ra |
|
|
|
|
|
|
0,63 |
|
0,07 |
0,10 |
0,12 |
0,14 |
|
1,25 |
|
0,10 |
0,13 |
0,165 |
0,19 |
|
2,5 |
|
0,144 |
0,20 |
0,246 |
0,29 |
|
|
20 |
0,25 |
0,33 |
0,42 |
0,49 |
|
период |
0,35 |
0,51 |
0,63 |
0,72 |
|
|
|
40 |
||||
|
|
80 |
0,47 |
0,66 |
0,81 |
0,94 |
Примечан . Подачи даны для о ра отки сталей с σв = 700 – 900 МПа и чугунов; для сталей с σв=500 – 700 МПа значения подач умножить на коэффициент Ks=0,45; для сталей с σв=900 – 1100 МПа значен я подач умножить на коэффициент Ks=1,25.
T – стойкость резца, ра оты режущего инструмента до затупления. Среднее значен е стойкости резца T при одноинструментальной обработке составляет 30 – 60 м н. При проведении расчёта скорости резания стойкость резца T принимается ориентировочно в зависимости от прочности обрабаты-
ваемого материала.
Скорость резания V, м/мин при наружном продольном и поперечном точе-
нии и растачивании рассчитывают по эмпирической формуле [2] |
|
|
V = Cv·Kv/Tm·tx·Sy . |
|
(14.1) |
Д |
|
|
Значения бАкоэффициента Cv, показателей степени x, y и m |
приведены в |
|
табл. 14.5 в зависимости от вида обработки и факторов, характеризующих ус- |
||
ловия обработки (качество обрабатываемого материала, состояние поверхности |
||
заготовки, качество материала режущего инструмента и т. д.). |
|
|
И |
83
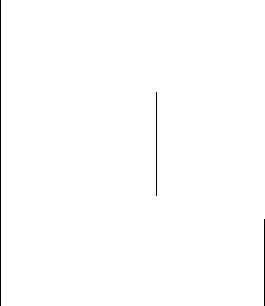
Таблица 14.5
Значения коэффициента Cv и x, y, m [2]
|
|
|
Материал |
Характеристи- |
Коэффициент и показатели |
|||||
|
Вид обработки |
режущей |
|
ка подачи |
|
степени |
|
|||
|
|
|
части резца |
|
S, мм/об |
Cv |
x |
y |
m |
|
С |
|
|
|
|
|
|
|
|||
|
Обработка конструкционной углеродистой стали, σв=750 МПа |
|
||||||||
|
Наружное про- |
|
|
|
S до 0,3 |
420 |
0,15 |
0,20 |
0,20 |
|
|
дольное точен е |
|
T15K6* |
|
S cвыше 0,3 |
350 |
0,15 |
0,35 |
0,20 |
|
|
проходными рез- |
|
|
|
|
|
|
|
|
|
|
проходными |
|
свыше 0,7 |
340 |
0,15 |
0,45 |
0,20 |
|||
|
цами |
|
|
|
|
|||||
|
|
|
|
Обработка серого чугуна, HB190 |
|
|
|
|||
|
Наружное про- |
|
|
|
S≤0,40 |
292 |
0,15 |
0,20 |
0,20 |
|
|
дольное точен е |
|
|
|
|
|
|
|
|
|
|
обра |
|
|
|
|
|||||
|
|
рез- |
|
BK6* |
|
S>0,40 |
243 |
0,15 |
0,40 |
0,20 |
|
цами |
|
|
|
||||||
|
|
|
|
|
|
|
|
|
|
* Без охлажден я.
Примечан я: При внутренней о ра отке (растачивании, прорезании канавок в отвер- |
||
|
А |
|
стиях, внутреннем фасонном точении) принимать скорость резания, равную скорости реза- |
||
ния для наружной |
отки с введением поправочного коэффициента 0,9. |
|
Поправочный коэффициент Kv определяется по формуле [2]: |
|
|
|
Kv = KMv · KПv · KИv , |
(14.2) |
где KMv – коэффициент, учитывающий качество обрабатываемого материала;
KПv – коэффициент, учитывающий состояние поверхности заготовки; |
|||
KИv – коэффициент, учитывающий качество материала инструмента. |
|||
|
|
И |
|
|
ДТаблица 14.6 |
||
Коэффициент KMv, учитывающий влияние физико-механических |
|||
свойств обрабатываемого материала на скорость резания [2] |
|||
|
|
Примечания: 1. σв и HB – фактиче- |
|
Обрабатывае- |
Расчётная формула |
||
мый |
ские параметры, характеризующие об- |
||
|
|||
материал |
|
рабатываемый материал, для которого |
|
|
|
рассчитывается скорость резания. |
|
Сталь |
KMv = Kr · (750/ σв)nv |
||
2.Коэффициент Kr, характери- |
|||
|
|
зующий группу стали по обрабатывае- |
|
|
KMv = (190/HB)nv |
||
Серый чугун |
мости и показатель степени nv приве- |
||
|
|
дены в табл. 14.7. |
|
|
|
84
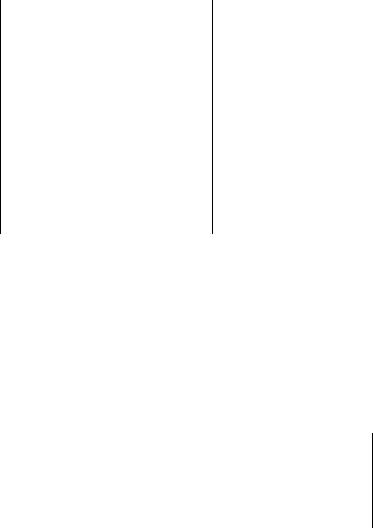
|
|
|
|
|
|
|
|
|
|
|
|
|
|
|
|
|
|
Таблица 14.7 |
|||||||||
|
|
|
Значения коэффициента Kr и показатели степени n [2] |
|
|
|
|
|
|||||||||||||||||||
|
|
|
|
|
|
|
|
|
|
|
|
|
|
||||||||||||||
|
|
|
|
|
|
|
|
Kr для материала инструмента |
|
nv при обработке резца- |
|||||||||||||||||
|
Обрабатываемый |
|
|
|
|
|
|
|
|
|
ми |
|
|
|
|
|
|
|
|
|
|
||||||
|
|
|
Из |
|
|
|
Из |
|
Из быст- |
|
|
|
Из |
|
|||||||||||||
|
материал |
|
|
|
|
|
|
|
|
|
твёрдого |
|
|
|
|||||||||||||
|
|
|
|
|
|
|
|
|
|
|
|
|
|
|
|
|
|
|
|||||||||
С |
|
быстрорежущей |
|
твёрдого |
|
рорежу- |
|
|
|
сплава |
|
|
|
||||||||||||||
|
|
|
|
|
|
|
|
|
|
|
|
|
|
|
|
||||||||||||
|
|
|
|
|
|
|
|
|
стали |
|
|
|
сплава |
|
щей стали |
|
|
||||||||||
|
|
|
|
|
|
|
|
|
|
|
|
|
|
|
|
|
|
|
|||||||||
|
|
|
|
|
|
|
|
|
|
|
|
|
|
|
|
|
|
|
|
|
|
|
|||||
|
таль углерод стая |
|
1,0 |
|
|
|
1,0 |
|
-1,0 |
|
|
|
|
|
1,0 |
|
|
|
|||||||||
|
(с≤0,6%:) σв < 450 МПа |
|
|
|
|
|
|
|
|
|
|
|
|
|
|||||||||||||
|
|
|
|
|
|
|
|
|
|
|
|
|
|
|
|
|
|
|
|
|
|
||||||
|
σв = 450 – 550 МПа |
|
|
|
|
|
|
|
|
|
|
|
|
|
|
|
|
|
|
|
|
|
|||||
|
поверхности |
|
|
1,0 |
|
1,75 |
|
|
|
|
|
1,0 |
|
|
|
||||||||||||
|
|
|
|
|
|
|
|
1,0 |
|
|
|
|
|
|
|
|
|
|
|
|
|||||||
|
ерый чугун |
|
|
|
|
|
|
|
|
|
|
|
|
|
1,7 |
|
|
|
|
|
1,25 |
|
|
|
|||
|
|
|
бА |
Таблица 14.8 |
|||||||||||||||||||||||
|
|
|
|
|
|
|
|
|
|
|
|
|
|
|
|
|
|
||||||||||
|
Поправочный коэфф циент KПv, учитывающий влияние состояния |
||||||||||||||||||||||||||
|
|
|
|
|
|
|
|
заготовки на скорость резания [2] |
|
|
|
|
|
|
|
|
|||||||||||
|
|
|
|
|
|
|
|
|
|
|
|
|
|
|
|
|
|
|
|
|
|
|
|
|
|
|
|
|
|
|
|
|
|
Состояние поверхности заготовки |
|
|
|
|
|
|
|
|
|
|
|||||||||||
|
|
|
|
|
|
|
|
|
|
|
с коркой |
|
|
|
|
|
|
|
|
|
|
|
|
|
|||
|
Без |
|
|
|
|
|
|
|
Стальные и чугунные отливки |
|
|
|
|
Медные и |
|
||||||||||||
|
|
|
|
|
|
|
|
|
|
|
при корке |
|
|
|
|
|
|
|
|
||||||||
|
корки |
|
Прокат |
Поковка |
|
|
|
|
|
сильно– |
|
|
|
алюминиевые |
|
||||||||||||
|
|
|
|
|
|
|
|
|
|
|
|
|
|
|
|
|
|
|
|
|
|
|
|
||||
|
|
|
|
|
|
|
|
|
|
|
Д |
|
сплавы |
|
|||||||||||||
|
|
|
|
|
|
|
|
|
нормальной |
|
загрязнённой |
|
|
|
|
|
|||||||||||
|
1,0 |
|
0,9 |
|
0,8 |
|
0,8 – 0,85 |
|
0,5 – 0,6 |
|
|
|
|
|
0,9 |
|
|
|
|||||||||
|
|
|
|
|
|
|
|
|
|
|
|
|
|
|
|
|
|
|
|
Таблица 14.9 |
|||||||
|
|
|
Поправочный коэффициент КИv, учитывающий влияние |
||||||||||||||||||||||||
|
|
|
инструментального материала на скорость резания [2] |
||||||||||||||||||||||||
|
|
|
|
|
|
|
|
|
|
|
|
|
|
|
|
|
|
|
|
|
|
|
|
|
|
||
|
Обрабатывае- |
|
|
|
|
Значения коэффициента К v в зависимости |
|
|
|||||||||||||||||||
|
мый |
|
|
|
|
|
|
||||||||||||||||||||
|
|
|
|
|
|
|
от марки инструментального материала |
|
|
||||||||||||||||||
|
материал |
|
|
|
|
|
|
||||||||||||||||||||
|
|
|
|
|
|
|
|
|
|
|
И |
|
|
||||||||||||||
|
Сталь |
|
|
|
|
|
|
|
|
|
|
|
|
|
|
|
|
|
|
|
|||||||
|
конструкци- |
|
Т5К12В |
Т5К10 |
Т14К8 |
Т15К6 |
Т15К6 |
Т30К4 |
|
ВК8 |
|
||||||||||||||||
|
онная |
|
|
0,35 |
|
0,65 |
|
0,8 |
|
1.0 |
1,15 |
|
|
|
1,4 |
|
0,4 |
|
|
|
|||||||
|
|
|
|
|
|
|
|
|
|
|
|
|
|
|
|
|
|
|
|
|
|
|
|
|
|
||
|
Серый чугун |
|
ВК8 |
ВК6 |
|
ВК4 |
|
ВК3 |
ВК3 |
|
|
|
|
- |
|
|
- |
|
|
|
|||||||
|
|
0,83 |
|
1,0 |
|
1,1 |
|
1,15 |
1,25 |
|
|
|
|
|
|
|
|
|
|
|
|||||||
|
|
|
|
|
|
|
|
|
|
|
|
|
|
|
|
|
|
|
|||||||||
|
|
|
|
|
|
|
|
|
|
|
|
|
|
|
|
|
|
|
|
|
|
|
|
|
|
|
|
85
Установив все необходимые данные, по формуле (14.1) определяется расчётная скорость резания Vрасч. для конкретного рабочего хода перехода.
По полученному значению расчётной скорости резания Vрасч. определяется расчётная частота вращения детали (обрабатываемой заготовки):
С |
nрасч. = 1000·Vрасч./π·Dзаг , |
(14.3) |
|
|
|
где Dзаг – наибольший диаметр обрабатываемой заготовки, мм. |
||
По расчётной частоте вращения (nрасч.) определяют фактическую частоту |
||
вращения шп нделя станка nф, меньшую или равную означенной в паспорте |
||
станка; nф. ≤ nрасч. |
|
|
документации |
скорость резания Vф. |
|
После установлен я nф вычисляется фактическая |
||
(м/мин): |
Vф. = π ·D · nф./1000. |
(4) |
|
|
обра |
|
Режимы резан я устанавливаются и рассчитываются для каждого перехо- |
||
да механ ческой |
отки. |
|
В технолог ческой |
на изготовление деталей обрабатываемая |
|
при переходе поверхность выделяется утолщённой линией. |
||
|
|
Контрольные вопросы |
1. |
В какой последовательности устанавливаются режимы |
|
Резания? |
|
|
2. |
Какие факторы влияют на назначение и расчёт режимов резания? |
|
3. |
|
Д |
Что такое рабочий ход перехода? |
||
4. |
Какими принципамиАпользуются при назначении глубины резания? |
|
5. |
В зависимости от каких параметров детали назначаются чистовые пере- |
|
ходы? |
|
|
6. |
Какая точность обработки может быть достигнута на токарном станке |
|
при точении (при растачивании, при сверлении)? |
||
7. |
Какие дефектами поверхности могут иметь заготовки? |
|
8. |
Какие факторы учитываются при назначении величины подачи? |
|
9. |
Какой величины устанавливается конкретная величина подачи? |
10. |
В какую сторону округляется величина выбранной подачи и расчетная |
частота вращения детали по отношению к паспортным данным станка? |
|
11. |
Что учитывается поправочным коэффициентомИКV при расчёте скоро- |
сти резания V7?
86