
- •ВВЕДЕНИЕ
- •1. БАЗОВАЯ ИНФОРМАЦИЯ ДЛЯ ПРОЕКТИРОВАНИЯ ТЕХНОЛОГИЧЕСКИХ ПРОЦЕССОВ ПРОИЗВОДСТВА ДЕТАЛЕЙ МАШИН
- •3. ВЫБОР ЗАГОТОВКИ ИЗ СОРТОВОГО ПРОКАТА
- •5. РАСЧЁТ ЗАГОТОВКИ, ПОЛУЧАЕМОЙ СПОСОБОМ ГОРЯЧЕЙ ОБЪЁМНОЙ ШТАМПОВКИ
- •7. ОСНОВЫ ВЫБОРА ТЕХНОЛОГИЧЕСКИХ БАЗ
- •7.2. Базы и их выбор
- •8. АНАЛИЗ ТЕХНОЛОГИЧНОСТИ КОНСТРУКЦИИ ДЕТАЛИ
- •13. СХЕМЫ ФОРМИРОВАНИЯ И РАСЧЁТ ПРОМЕЖУТОЧНЫХ РАЗМЕРОВ ОБРАБАТЫВАЕМОЙ ДЕТАЛИ
- •15. ТЕХНИЧЕСКОЕ НОРМИРОВАНИЕ СТАНОЧНЫХ ОПЕРАЦИЙ
- •Библиографический список
- •Приложение 1
- •Приложение 2
- •Приложение 3
- •Приложение 4
8. АНАЛИЗ ТЕХНОЛОГИЧНОСТИ КОНСТРУКЦИИ ДЕТАЛИ
Направленность раздела:
1. Освоение понятия «технологичность конструкции», ее оценки.
2. Определение коэффициентов точности Кт и шероховатости Кш по заданному чертежу детали.
3. Качественная оценка технологичности детали.
В соответствии с ГОСТ-14.205–83 технологичность – это совокупность
свойств конструкц |
зделия, определяющих ее приспособленность к дости- |
жению опт мальных затрат при производстве, эксплуатации и ремонте с задан- |
|
ными показателями точности и качества, объема выпуска и условий выполне- |
|
ния работ [15, 16]. |
|
С |
|
Про зводственная технологичность детали – это степень ее соответствия |
|
требован ям на более про зводительного и экономичного изготовления. Чем |
|
меньше трудоемкость |
се естоимость изготовления, тем более технологичной |
является конструкц я. |
|
Оценка технолог |
конструкции детали бывает двух видов: качест- |
чности |
|
венная и кол чественная. |
|
бА |
Качественная оценка технологичности является предварительной,
обобщенной и характеризуется показаниями: «лучше-хуже», «рекомендуется - не рекомендуется», «технологично-нетехнологично» и т.п. Технологичной при качественной оценке следует считать такую геометрическую конфигурацию детали и отдельных ее элементов, при которой учтены возможности минималь-
-степени унификации следующихДэлементов (диаметров, длин, резьб, модулей, радиусов, перехода, жесткости и т.п.) в конструкции детали;
-наличия удобных для закрепления базирующих поверхностей, обеспечивающих возможность совмещения и постоянства базИ;
-возможности свободного подвода и вывода режущего инструмента при обработке. Например, представленные на рис. 8.1 конструкции деталей не являются технологичными, так как препятствуют подводу режущего инструмента
копределенным местам;
-удобства контроля точных параметров детали;
-возможности уменьшения протяжности точных обрабатываемых поверхностей;
-соответствия формы обрабатываемых деталей форме режущей части стандартного инструмента (резцы, фрезы, сверла, зенкера, развертки и т.д.) для их обработки.
Многочисленные примеры качественной оценки приведены в литературе [15,16].ного расхода материала и использования наиболее производительных и эконо-
48
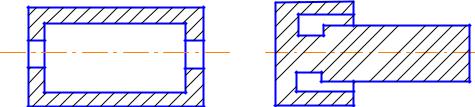
|
|
Р с. 8.1. Пр мер деталей, не являющихся технологичными |
||
|
для обработки резан ем (по препятствию подводу режущего инструмента) |
|||
СКоличественная оценка технологичности выражается показателем, чис- |
||||
ленное значен е которого характеризует степень удовлетворения требований к |
||||
технолог чности. Согласно ГОСТ 14.202–73 номенклатура показателей техно- |
||||
логичности |
здел я содержит 4 основных и 31 |
дополнительный показатель. |
||
Применительно к маш ностроительному производству количественную оценку |
||||
технологчностипроводят: |
|
|
||
- по суммарной трудоемкости Тшт (штучное время), т.е. по затратам труда |
||||
на технолог ческ е основные и прочие операции. При проектировании техно- |
||||
логических операций одним из основных |
является требование минимума за- |
|||
трат труда на их выполнение, что зависит от их технологичности; |
||||
- по технологической се естоимости Ст. Технологической себестоимостью |
||||
детали называется та часть ее полной себестоимости, элементы которой суще- |
||||
ственно изменяются для различных вариантов технологического процесса; |
||||
- по техническим показателям, которые можно определить по чертежу дета- |
||||
|
|
бА |
||
ли. К ним относятся: |
|
|
||
- коэффициент точности Кт =1–1/Тср, |
|
(8.1) |
||
где Тср – среднее значение параметров точности, Тср = ∑Тi ni / ∑ni; |
||||
|
Тi – квалитеты точности элементов детали; |
|||
|
ni – |
количество размеров каждогоДквалитета; |
||
- коэффициент шероховатости Кш = 1 / Rср, |
(8.2) |
|||
где Rср – среднее значение параметров шероховатости, мкм, |
||||
где Ri |
|
Rср = ∑Ri ni / ∑ ni, |
|
|
– параметры шероховатости обрабатываемых поверхностей, мкм; |
||||
ni |
|
|
|
И |
– количество поверхностей с определенным параметром шероховатости. |
||||
В качестве примера покажем оценку технологичности деталей «Вал» |
||||
(рис. 8.2) и «Втулка» (рис. 8.3). |
|
|
49
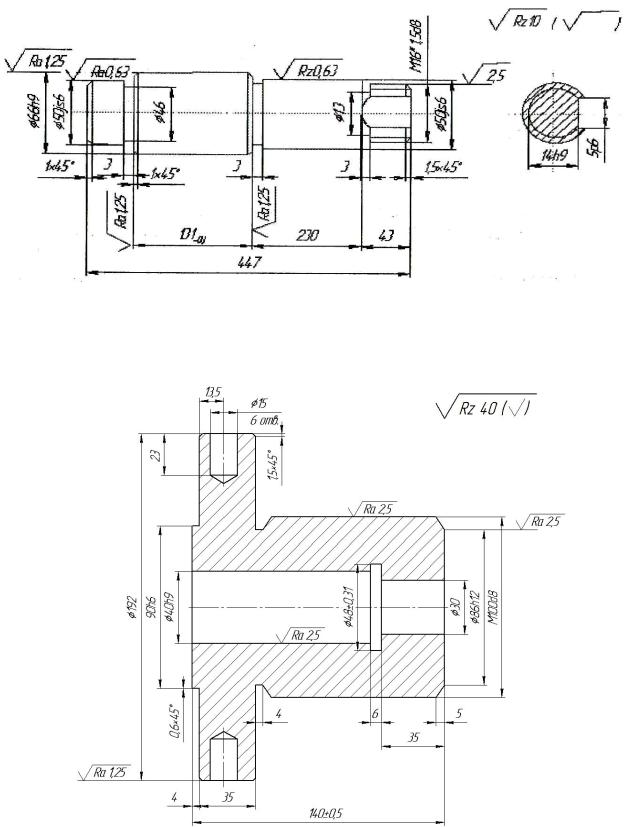
Си Р с.8.2бА. Деталь «Вал». Материал – сталь 40. Вид заготовки – прокат
Д И
Рис. 8.3. Деталь «Втулка». Материал – сталь 30Л. Вид заготовки – отливка
50
Деталь «Вал» является технологичной, т.к. конструкция ее несложная, осесимметричная, перепады диаметров основных частей детали небольшие, что позволяет использовать в качестве заготовки для изготовления детали сортовой прокат. Это не вызовет больших расходов на материал. Поскольку относительная длина детали достаточно большая (4<l/d<10), то для обеспечения необходимой жесткости при ее обработке можно использовать способ базирования с опорой правого торца вала на центровое отверстие. При обработке всех элементов детали можно применять стандартный режущий инструмент, подвод и отвод которого к обрабатываемым поверхностям прост. Три канавки одинаковой ширины обрабатываются одним прорезным резцом. Что касается материала, то сталь 40 также является технологичной при обработке резанием, т. к. стружка с
детали сн мается без |
наростов на передней поверхности резца |
[17]. уммарное кол чество размеров детали – 13, из которых три размера вы- |
|
С |
|
полняются по 6-му квал тету точности, один – по 8-му, три – по 9-му и |
|
шесть– по 14-му квал тету. |
|
В этом случае коэфф ц ент точности Кт=1–1/Тср=1–1/10,54=0,905 при |
|
Тср = ∑Тi i / ∑ |
i, = (14·6+9·3+8·1+6·3)/13=10,54. |
образованияn n |
|
бА |
Суммарное кол чество о ра атываемых поверхностей составляет 15, из которых девять имеют среднеарифметическое отклонение профиля RZ=10 мкм, одна поверхность – с шероховатостью Rа=2,5 мкм, три поверхности – с шероховатостью Rа=1,25мкм и две поверхности с шероховатостью Rа=0,63 мкм.
Поэтому Кш = 1 / Rср = 1/6,50 = 0,153 при
Rср = ∑Ri ni / ∑ ni = (10·9+2,5·1+1,25·3+0,63·2)/15Д= 6,50.
Деталь «Втулка» более сложная. Использование для ее изготовления заготовки из сортового проката экономически не оправдано, так как это приведет к большому расходу материала и большому объему работИна обработку резанием. С ориентацией на материал детали – литейную сталь 30Л – целесообразно получать исходную заготовку литьем. Заготовка в этом случае будет приближена к форме готовой детали. Деталь осесимметричная, нежестких элементов у детали нет, геометрические элементы конструкции детали являются унифицированными. Однако технологичность конструкции детали усложнена наличием канавки внутри центрового отверстия, доступ к которой расточным резцом осложнен при подводе с обеих сторон: с правой стороны – в связи с малым отверстием диаметром Ø 30 мм и глубиной врезания 9 мм, с левой стороны – в связи с большим расстоянием до канавки, равным 105 мм. Суммарное количество размеров составляет 17, из которых один размер выполняется по 6-му квалитету точности, один – по 8-му, один – по 9-му, один – по 12-му, остальные десять размеров – по 14-му квалитету. Тогда Кт=1–1/Тср = 1–1/12,5 = 0,92 при
51
Тср = ∑Тi ni / ∑ni = (14٠10+12·1+9٠1+8·1+6٠1) /14=12,5.
По параметрам шероховатости суммарное количество обрабатываемых поверхностей составляет 13, из которых девять могут иметь среднеарифметическое отклонение профиля до RZ = 40 мкм, три поверхности – с шероховатостью Rа= 2,5 мкм, одна поверхность – с шероховатостью Rа = 1,25 мкм. Тогда
|
Кш = 1 / Rср = 1/28,36 = 0,035 при |
|
Rа= (40·9+2,5·3+1,25·1)/13 = 28,36 мкм. |
|
Контрольные вопросы |
1. |
По какой совокупности свойств определяется технологичность конст- |
Срукции ? |
|
2. |
Каковы в ды оценки технологичности конструкции детали? |
3. |
В чем состо т качественная оценка технологичности? |
4. |
Какая конструкц я детали препятствует подводу режущего инструмента |
к местам обработки? |
||
детали5. В чем состо т кол чественная оценка технологичности детали? |
||
6. |
Как оцен вается технологичность конструкции детали при большой тру- |
|
доёмкости её |
зготовлен я? |
|
7. |
Какие виды количественной оценки технологичности являются рацио- |
|
нальными? |
б |
|
8. |
Как определяется коэффициент точности Кт? |
|
9. |
Как определяется коэффициент шероховатости Кш? |
|
|
|
А |
|
|
9. ПРОЕКТИРОВ НИЕ М РШРУТА |
|
|
ИЗГОТОВЛЕНИЯ ЕТ ЛИ |
Направленность раздела: |
||
1. |
Практическое освоение основныхДпринципов проектирования техноло- |
гических процессов (разработка маршрута изготовления детали).
2.Обоснование способа получения исходной заготовки и ее подготовки к механической обработке (отрезка, правка прутка или очистка, обрубка, обрезка отливок и штамповок и т.д.).
3.Разработка маршрута механической обработки и выбор технологических баз.
4.Определение периодов технического контроля.
5.Назначение видов очистки и подготовки детали к хранению. Разрабатываемый процесс должен быть инновационным, обеспечивающимИ
повышение производительности труда и качества деталей, сокращение трудовых и материальных затрат на его реализацию, уменьшение вредных воздействий на окружающую среду.
52
Технологический процесс разрабатывают на основе единичного, типового или группового технологического процесса [1, 2].
Различают два вида технологического процесса:
-рабочий;
-перспективный.
Рабочим технологическим процессом называется процесс изготовления од-
С |
|
ного или нескольких изделий в соответствии с требованиями принятой для |
|
данных условий производства рабочей технологической документации. |
|
Единичный технологический процесс разрабатывают только на уровне |
|
предприят я |
пр меняют для изготовления или ремонта одного конкретного |
предмета про |
зводства. |
документации |
|
Этапы разработки рабочего единичного технологического процесса сле- |
дующие [1]: |
|
- анал з сходных данных для разработки технологического процесса; |
|
- выбор формы |
для оформления технологического процесса; |
- выбор сходной заготовки; |
|
- выбор технолог ческ |
х аз; |
- составлен е технолог |
ческого маршрута обработки; |
- разработка технолог |
ческих операций; |
- форм рован е технологического процесса; - определение тре ований экологии и безопасности жизнедеятельности; - расчет экономической эффективности; - оформление технологического процесса.
бА Этап 1. Базовой исходной информациейДдля разработки технологического
Рассмотрим первые пять этапов разработки рабочего единичного техно-
логического процесса.
процесса служат:
- рабочий чертеж детали и технические требования, регламентирующие точность, параметры шероховатости поверхностей и другие требования качества;
-форма типового технологического маршрутаИмеханической обработки деталей в условиях мелкосерийного и среднесерийного производства;
-формы и правила оформления маршрутных карт (ГОСТ 3.1118–82), в которых содержится описание технологического процесса изготовления детали по всем операциям в определенной последовательности с указанием параметров оборудования, приспособлений (оснастки), режущего инструмента, материалов
ит.д. (заполняются формы МК: 1 и 1б);- объем годового выпуска изделий (тип производства). Тип производства
53
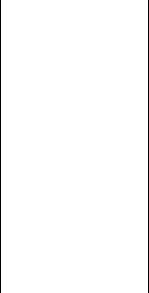
|
|
|
|
|
|
|
Таблица 9.1 |
|
Приближенные данные по выбору типа производства |
||||||
|
|
|
Крупные изделия |
Изделия средних |
Мелкие изде- |
||
|
Тип производ- |
тяжелого машино- |
|||||
|
размеров |
лия |
|||||
|
ства |
|
|
строения |
|
||
|
|
|
|
|
|
||
|
|
|
|
|
|
Число изделий |
|
|
|
|
|
|
|
|
|
|
Единичное |
|
|
<5 |
|
<10 |
<100 |
|
|
|
|
|
|
|
|
|
Мелкосер йное |
|
5–100 |
|
10–200 |
100–500 |
|
|
|
|
|
|
|
||
|
оформления |
|
200–500 |
500–5000 |
|||
|
реднесер йное |
100–300 |
|
||||
С |
|
|
|
|
|||
|
Крупносер йное |
300–1000 |
|
500–5000 |
5000–50000 |
||
|
Массовое |
|
|
>1000 |
|
>5000 |
>50 000 |
|
|
бА |
|
||||
|
-формы прав ла |
|
документов на операции обработки реза- |
нием (ГОСТ 3.1404–86). В операционной карте содержится описание операций технолог ческого процесса с расчленением операций по переходам, указанием режимов резания, расчетных норм времени (заполняются операционные карты), Приложение 2 (формы 2 и 2а);
- карта эскизов (ГОСТ 3.1105–84), в которой приводится графическая иллюстрация технологии изготовления детали и отдельных ее элементов;
-операционная карта контроля (ГОСТ 3.1502–85), в которой приводятся средства контроля и контролируемые размеры для каждого перехода (заполняется форма 2).
Этап 3. Выбор исходной заготовки производят исходя из минимальной себестоимости готовой детали. Чем в большей степени форма и размеры заготовки приближаются к форме и размерам детали, тем проще и дешевле ее по-
ное оборудование. Поэтому окончательное решение о выборе метода получения заготовки принимается на основе технико-экономических расчетов по нескольким конкурирующим методам.
следующая механическая обработка, и меньше расход материала. |
получе- |
ния точных заготовок требуется дорогая технологическая оснастка и специаль- |
|
Для |
|
И |
Значительная часть деталей небольших размеров в условиях единичного и мелкосерийного производства изготавливается из сортового проката при коэффициенте использования материала 0,5 – 0,7, так как затраты на оснастку для предварительного формообразования точных заготовок обычно превосходят экономию от сокращения расхода материала.
При изготовлении крупных деталей (блоки цилиндров двигателей, корпуса коробок передач, станины станков, погоны башен , корпуса мостов автомобилей, валки прокатных станов и др.) необходимо прорабатывать вопрос переформовки проката в заготовки – поковки, получаемые свободной ковкой с ис-
54
пользованием подкладных инструментов (осадка с целью увеличения поперечных размеров; высадка фланцев или утолщений, раскатка колец и др.) или применения технологий литейного производства (литье в песчано-глинистые или стержневые формы), когда не требуется изготовления сложной технологической оснастки.
Основными методами получения заготовок в условиях крупносерийного и Смассового производства являются литье (в песчано-глинистые формы, по выплавляемым моделям, в оболочковые формы, в кокиль и др.) и обработка металлов давлением (выдавливание холодное, полугорячее или горячее, высадка, горячая объемная штамповка, раскатка поперечно-клиновая, раскатка продольная и др.), а также перспективные методы: порошковая металлургия, лазерная
обработкапри, электроф з ческие и электрохимические методы.
Если при спользовании заготовок в виде проката отходы металла в стружку составляют 30–50%, то при использовании способов литья и обработки металлов давлен ем, которых фасонные заготовки приближаются к форме деталей (л тьесебестов кок ль, под давлением, по выплавляемым моделям; штамповка на ковочных горячештамповочных прессах, горизонтально-ковочных машинах и холодновысадочных автоматах, холодное выдавливание, накатывание шестерен с зубом др.), отходы сокращаются до 5–20%.
Снижен я мости заготовок можно добиться при изготовлении их на пресс-автоматах (горячештамповочныхА, холодновысадочных, горизонталь- но-ковочных машинах с горизонтальным разъемом матриц, оборудованных средствами автоматизации, литьевых машинах различных конструкций и др.), роторных и роторно-конвейерных линиях, автоматических и автоматизированных линиях, прессах, оснащенных подающими и передающими устройствами или роботами, станах поперечно-клиновойДпрокатки и зубопрокатных.
Этап 4. Технологические базы и схемы базирования выбираются для всего технологического процесса обработки. Выбор основных контактных баз начинается с выбора базы для выполнения первой операции – черновой базы.
Черновая база используется только один раз с целью обработки поверхностей заготовки для ее последующего закрепления. И Закрепление заготовки на обработанных резанием поверхностях называют чистовыми базами.
Этап 5. Разработка технологических процессов начинаются с определения технологического маршрута, в который включается все – от производства заготовки, ее отделки для механической обработки (очистка, обрубка, правка, термическая обработка и т.д.), затем планирование операций механической обработки, этапы контроля размеров изготавливаемой детали, вплоть до завершающих операций:
- очистка изготовленной детали, нанесение на неё антикоррозийного покрытия и т.д. [1,18].
В маршруте обработки производится сокращенно описание всех технологических операций в последовательности их выполнения без указания их переходов и технологических режимов.
55
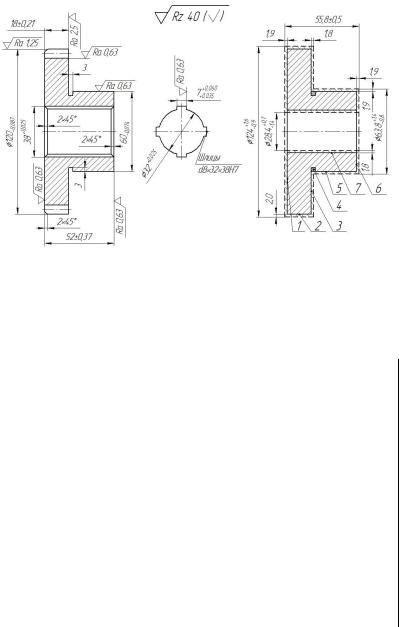
Маршрутное описание технологических процессов обычно используется в единичном или мелкосерийном производствах.
Примеры маршрутов обработки деталей различного типа приведены в справочнике технолога [18].
В табл. 9.2 приведен пример оформления маршрута обработки детали «Зубчатое колесо» со шлицевым отверстием (рис. 9.1). Материал: сталь 20Х. Вид за-
С |
|
|
|
|
|
|
|
||
|
готовки – холодная объемная штамповка. |
|
|
|
|
|
|
||
|
и |
|
|
|
|
|
|
|
|
|
|
бА |
|
|
|
|
|||
|
|
а |
|
б |
|
|
|
|
|
|
|
Рис. 9.1.Чертежи: а – деталь «Зу чатое колесо»; б – заготовка |
|
|
|
||||
|
|
|
|
|
|
Таблица 9.2 |
|||
|
Маршрут обработки детали «Зу чатое колесо» со шлицевым отверстием |
||||||||
|
Опера- |
Содержание или наименование |
|
|
|
|
|
|
|
|
ция |
Станок, оборудование |
Оснастка |
|
|||||
|
операции |
|
|
||||||
|
|
|
|
|
|
|
|
|
|
|
|
|
|
|
|
|
|
|
|
1 |
2 |
|
|
3 |
|
4 |
|
|
|
|
005 |
Отрезать заготовку от проката |
|
бразивно-отрезной |
Тиски |
|
|
|
|
|
|
|
|
станок 8В262 |
|
|
|
|
|
|
010 |
Штамповочная |
|
Пресс |
|
Штамп |
|
|
|
|
015 |
Термическая обработка |
|
|
И |
|
|||
|
|
|
|
|
– |
|
– |
|
|
|
020 |
Черновая подрезка торцов 3, 6. |
|
Д |
|
|
|
||
|
|
Черновое обтачивание поверхности 5. |
Токарно-винторезный |
Патрон |
|
трехку- |
|
||
|
|
Черновое растачивание отверстия 7. |
16К20 |
|
лачковый |
само- |
|
||
|
|
Черновая база–поверхность 2 с опо- |
|
|
центрирующийся |
|
|||
|
|
рой в торец 1 |
|
|
|
ГОСТ 2675–80 |
|
||
|
|
|
|
|
|
|
|||
|
|
|
|
|
|
|
|
|
|
Примечание. В мелкосерийном производстве рекомендуется [1] с целью повышения точности обработки сначала провести черновую обработку всех поверхностей, а затем выполнить чистовую обработку тех поверхностей, для которых она необходима.
56
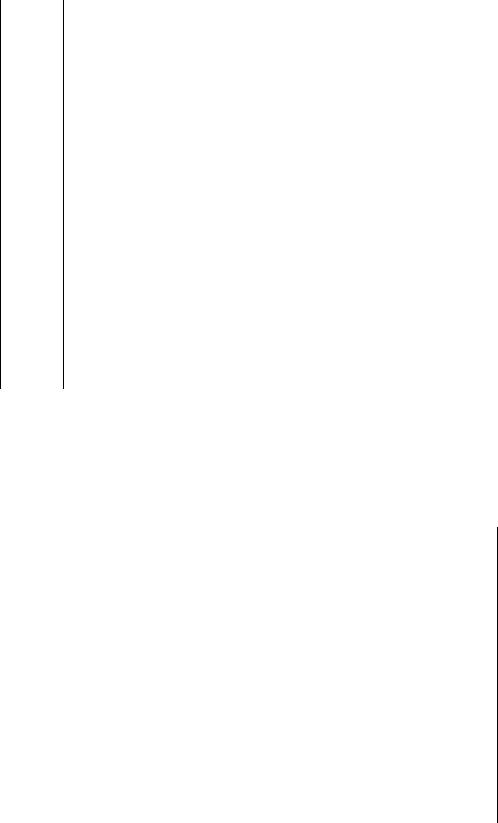
|
|
|
|
|
|
|
|
|
|
|
|
|
Продолжение табл. 9.2 |
||||
|
|
|
|
|
|
|
|
|
|
|
|
|
|
|
|
|
|
1 |
|
|
|
2 |
|
|
|
|
|
|
3 |
|
4 |
|
|
||
|
025 |
|
|
Черновая подрезка торца 1. Черновое |
|
Тот же |
|
Та же |
|
|
|||||||
|
|
|
|
обтачивание поверхности 2. |
|
|
|
|
|
|
|
|
|
|
|||
|
|
|
|
Чистовая база – поверхность 5 с опо- |
|
|
|
|
|
|
|
||||||
|
|
|
|
рой в торец 3. |
|
|
|
|
|
|
Тот же |
|
Та же |
|
|
||
С |
1 под шлифование |
|
|
|
|
|
|
|
|||||||||
030 |
|
|
Подрезать торец |
|
|
|
|
|
|
|
|||||||
|
|
|
|
Обточить поверхность 2 под шлифо- |
|
Тот же |
|
Та же |
|
|
|||||||
|
|
|
|
вание. Расточить отверстие 7 до Ø30 |
|
|
|
|
|
|
|
||||||
|
|
|
|
для протяг ван я шл цевого отвер- |
|
|
|
|
|
|
|
||||||
|
|
|
|
ст я. Обточ ть фаски. |
|
|
|
|
|
|
|
|
|
|
|
||
|
|
|
|
Ч стовая база – поверхность 5 с опо- |
|
|
|
|
|
|
|
||||||
|
|
точить |
|
|
|
|
|
|
|
|
|
||||||
|
|
|
|
рой в торец |
3. |
|
|
|
|
|
|
|
|
|
|
|
|
035 |
|
|
Подрезать торец 3 окончательно, |
|
|
|
|
|
|
|
|||||||
|
|
|
|
выдерж вая размер 18±0.21, подре- |
|
|
|
|
|
|
|
||||||
|
|
|
|
зать торец 6 окончательно, выдержи- |
|
|
|
|
|
|
|
||||||
|
|
|
|
база |
|
|
|
|
|
|
|
||||||
|
|
|
|
вая размер |
52±,0.370, |
о |
|
по- |
|
|
|
|
|
|
|
||
|
|
|
|
верхность 5 под шл фование. Про- |
|
Тот же |
|
Та же |
|
|
|||||||
|
|
|
|
точ ть паз 4 окончательно и |
о то- |
|
|
|
|
|
|
|
|||||
|
|
|
|
ч ть фаску. |
-поверхность 2 с опо- |
|
|
|
|
|
|
|
|||||
|
|
|
|
Ч стовая |
|
|
|
|
|
|
|
||||||
|
|
|
|
рой в торец 1 |
|
|
|
|
|
|
|
|
|
|
|
|
|
|
|
|
|
|
|
А |
|
|
|
|
|||||||
|
Примечание. После завершения всех операций по формообразованию детали начинают |
||||||||||||||||
|
операции местной обра отки на ранее о ра отанных поверхностях: фрезеруют канавки, |
на- |
|||||||||||||||
|
резают канавки и зубья, сверлят отверстия и выполняют отделочную обработку основных, |
||||||||||||||||
|
наиболее ответственных поверхностей. |
|
Д |
|
|
||||||||||||
|
|
|
|
|
|
|
|
|
|
|
|
|
Продолжение табл. 9.2 |
|
|
||
|
|
|
|
|
|
|
|
|
|
|
|
|
|
|
|
|
|
1 |
|
|
|
2 |
|
|
|
|
|
|
3 |
|
4 |
|
|
||
|
040 |
|
|
Протянуть |
четырехшлицевое |
от- |
|
Протяжной 7512 |
Жесткая опора |
|
|
||||||
|
|
|
|
верстие ø32 Н7х38Н11х4 |
|
|
|
|
|
И |
|
||||||
|
045 |
|
|
Технический контроль |
|
|
|
|
|
|
|
||||||
|
050 |
|
|
Фрезеровать 44 зуба (m=2,5) |
|
|
|
|
|
|
|||||||
|
|
|
|
|
Зубофрезерный 53А20В |
Приспособление |
|
|
|||||||||
|
055 |
|
|
Зачистить |
заусенцы |
на торцах |
|
Одношпиндельный ав- |
Кулачковый патрон |
|
|||||||
|
|
|
|
зубьев |
|
|
|
|
|
томат 5Б525 |
|
|
|
|
|
||
|
060 |
|
|
Термическая обработка |
|
|
|
– |
|
|
|
– |
|
|
|||
|
065 |
|
|
Шлифовать поверхности 2 и 5, |
|
Круглошлифовальный |
Грибковая оправка |
|
|||||||||
|
|
|
|
торец 1 окончательно |
|
|
|
3Т161Д |
|
|
|
|
|
|
|||
|
070 |
|
|
Шлифовать поверхность 7 и торец |
|
Внутришлифовальный |
Приспособление |
|
|
||||||||
|
|
|
|
6 окончательно |
|
|
|
|
3А227АФ2 |
|
|
|
|
|
|||
|
075 |
|
|
Шлифовать |
боковые |
стороны |
|
Специальный |
|
Трехкулачковый |
па- |
|
|||||
|
|
|
|
шлицев окончательно |
|
|
|
|
|
|
|
трон |
|
|
|||
|
080 |
|
|
Шлифовать 44 зуба (m=2,5) окон- |
|
Зубошлифовальный |
Оправка |
|
|
||||||||
|
|
|
|
чательно |
|
|
|
|
|
5В833 |
|
|
|
|
|
|
Примечание. После завершения операций механической обработки деталь промывается перед завершающим техническим контролем и последующей отделкой для ее хранения.
57
При проектировании маршрутов обработки валов контактными технологическими базами, как правило, являются вспомогательные, например, центровые отверстия, которые не являются конструктивной частью детали, а служат только для установки вала при его механической обработке.
Контрольные вопросы
1. На основе каких технологических процессов разрабатывается конкретный технологический процесс?
2. Что входит в этапы разработки рабочего единичного технологического процесса?
3.Что является базовой исходной информацией для разработки технологи-
ческого процесса? |
|
|
|
||
4. |
Как е формы технологической документации используются при проек- |
||||
С |
х процессов? |
||||
|
|
технолог |
ческ |
||
5. |
Как е основные факторы определяют выбор заготовки? |
||||
6. |
Как е группы операций входят в состав маршрута обработки? |
||||
7. |
Что такое черновая |
аза? Её назначение и период использования. |
|||
8. |
Как план руется |
ра отка поверхностей с высокими требованиями |
|||
тировании |
|
||||
точности размеров |
шероховатости? |
|
|||
9. |
Как |
|
|
ра атываемые поверхности детали в операциях ме- |
|
ханической обработки? |
|
|
|||
10. Планируется ли в маршруте работки детали снятие конкретных слоёв |
|||||
|
|
обозначаются |
|||
металла с поверхностей заготовки? |
|
||||
11. При каком типе производства рекомендуется составление маршрута |
|||||
обработки детали? |
|
|
|
||
|
10. СОСТАВЛЕНИЕАК РТ ТОЧНОСТИ И КАЧЕСТВА |
||||
Направленность раздела: |
Д |
||||
|
|
|
|
|
1.Освоение правил составления карт точности и качества.
2.Определение необходимого количества операций и переходов для достижения заданных точности размеров и шероховатости каждой поверхности заданной детали.
3.Составление карты точности и качества.
Главной задачей при проектировании маршрутаИобработки детали является решение вопроса по выбору необходимого количества операций и переходов обработки каждой поверхности детали для достижения заданных точности их размеров и качества (шероховатости) поверхности при минимальных затратах труда. Поэтому, если точность размера детали составляет IT ≥ 13–12, а требуемый параметр шероховатости поверхности Rz ≥ 80, то назначаются операции (токарная, фрезерная, строгальная, сверлильная и т.д.), на которых возможно полное снятие общего припуска за один переход.
Большее количество операций и переходов требуется при более высокой точности размера и меньшей шероховатости обрабатываемой поверхности.
58
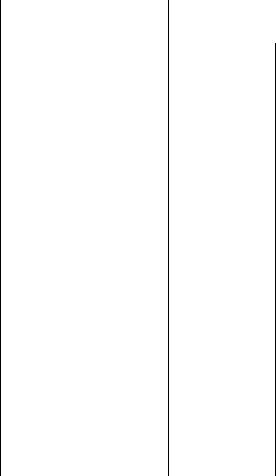
Ориентировочные данные о достигаемых точности и шероховатости при различных видах обработки приведены в табл. 10.1 и 10.2.
Экономическая точность механической обработки – точность, которая достигается при минимальной себестоимости обработки. При этом имеются в виду нормальные производственные условия, исправный станок, наличие требуемых приспособлений и инструментов; квалификация рабочего, соответствующая характеру работы.
Достижимая точность – та максимальная точность, которая может быть достигнута при обработке детали рабочим высокой квалификации, работаю-
|
щим на одном |
том же станке при неограниченной затрате времени (указана в |
||||||||
|
скобках табл. 10.2). Естественно, что достижимая точность обработки выше |
|||||||||
|
экономической точности обработки. Такая точность чаще всего неоправданна |
|||||||||
|
из-за больш х затрат на обработку, поэтому в большинстве случаев придержи- |
|||||||||
С |
|
|
|
|
|
|
|
|
||
|
ваются эконом ческой точности. |
|
|
|
|
|
|
|
|
|
|
Карта точности качества составляется путём введения в установленную |
|||||||||
|
форму показателей точности (IТ) параметров качества (Rz, Ra) обработки всех |
|||||||||
|
поверхностей детали (та л. 10.3). |
|
|
|
|
|
|
|
|
|
|
В качестве пр мера пр |
|
составление карты точности и качества де- |
|||||||
|
водится |
|
|
|
|
|
|
|
||
|
тали «Зубчатое колесо» (р с.10.1). |
|
|
|
|
Таблица 10.1 |
||||
|
|
|
|
|
|
|
||||
|
Достигаемая точность о ра отки наружных поверхностей деталей [21] |
|||||||||
|
|
|
|
|
|
|||||
|
Вид обработки |
Квалитет точности |
Параметры шерохова- |
|||||||
|
|
|
|
размеров |
|
|
тости |
|
|
|
|
|
|
|
|
|
Rz |
|
|
Ra |
|
|
Обтачивание: черновое |
|
13–12 |
|
80 |
|
|
1 |
|
|
|
получистовоебА11–9 |
40–20 |
|
|
- |
|
||||
|
чистовое |
|
8–7 |
|
- |
|
|
2,5 |
|
|
|
тонкое |
|
7–6 |
|
- |
|
1,25–0,63 |
|
||
|
Сверление: |
|
|
12–11 |
|
40–20 |
|
|
- |
|
|
Зенкерование: черновое |
|
12–11 |
|
40 |
|
|
- |
|
|
|
|
получистое |
|
Д11 20 |
|
- |
|
|||
|
|
чистовое |
|
9–8 |
|
- |
|
|
2,5 |
|
|
Развёртывание: черновое |
|
9–8 |
|
- |
|
2,5–1,25 |
|
||
|
|
чистовое |
|
7–6 |
|
- |
|
0,63–0,32 |
|
|
|
|
тонкое |
|
6 |
|
- |
|
|
0,16 |
|
|
|
|
|
|
И |
|
||||
|
Растачивание: |
черновое |
|
13–12 |
|
80–40 - |
||||
|
|
получистое |
|
11–10 |
|
40–2 |
|
|
- |
|
|
|
чистовое |
|
9–7 |
|
- |
|
2.5–0,63 |
|
|
|
|
тонкое |
|
6…5 |
|
- |
|
0,32–0,08 |
|
|
|
Подрезка торца резцом: черновая |
|
12 |
|
40 |
|
|
- |
|
|
|
|
чистовая |
|
11 |
|
20 |
|
|
- |
|
|
|
тонкая |
|
8-7 |
|
- |
|
2,5–1.25 |
|
|
|
|
|
|
|
|
|
|
|
|
|
59
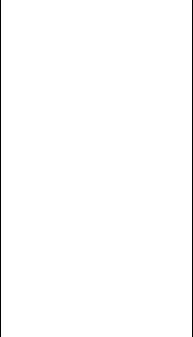
Карта точности и качества позволяет экономить время на поиск информации по точности и качеству обработанной детали на различных операциях и переходах технологического процесса.
Карта точности и качества содержит:
- наименование и содержание каждой операции технологического процесса
|
механической обработки детали; |
|
|
|
|||
С |
|
|
|
|
|||
|
- номер всех обрабатываемых поверхностей, нанесенных на чертеж ис- |
||||||
|
ходной заготовки (прокат, поковка, отливка); |
|
|
||||
- |
параметры точности и шероховатости каждой поверхностей детали, за- |
||||||
|
данные на рабочем чертеже; |
|
|
|
|||
- |
параметры точности |
шероховатости поверхностей, |
полученные в про- |
||||
|
обработки |
|
|
|
|||
|
цессе |
|
; |
|
|
|
|
|
- указывается точность и качество изготовления заготовки; |
||||||
|
- на каждой операц |
технологического процесса указывается точность и |
|||||
|
качество для тех элементов заготовки, которые подвергаются механической об- |
||||||
|
работке. |
|
|
|
|
|
|
|
|
|
|
|
|
Таблица 10.2 |
|
|
|
|
Шероховатость поверхности и экономическая точность |
||||
|
|
|
при различных методах обработки резанием [3] |
||||
|
|
|
|
|
|
|
|
|
|
|
Метод обра отки |
|
Шероховатость по- |
Квалитет |
|
|
|
|
|
|
верхности |
|
|
|
|
|
1 |
|
2 |
3 |
|
|
Точение: |
черновое (обдирочное) |
Д |
|
|||
|
Rz 320–40 |
11 |
|
||||
|
|
|
чистовоебАRz 20–Ra1,25 |
9–10 |
|
||
|
|
|
тонкое |
|
Ra 0,63 |
6–8 |
|
|
Строгание: черновое (обдирочное) |
Rz 320–40 |
12–13 |
|
|||
|
|
|
чистовое |
|
Rz 20–Ra1,25 |
11–13 |
|
|
|
|
тонкое |
|
И |
|
|
|
|
|
|
Ra1,25–0,63 |
9–10 |
|
|
|
Фрезерование: |
|
Rz 80–40 |
|
|
||
|
|
|
черновое (обдирочное) |
12–13 |
|
||
|
|
|
чистовое |
|
Rz 20–Ra2,5 |
11 |
|
|
|
|
тонкое |
|
Ra1,25–0,63 |
9–10 |
|
|
Сверление |
|
Rz80–20 |
11–13 |
|
||
|
|
|
|
|
|
||
|
Зенкерование |
|
Rz40–Ra2,5 |
11–13 |
60
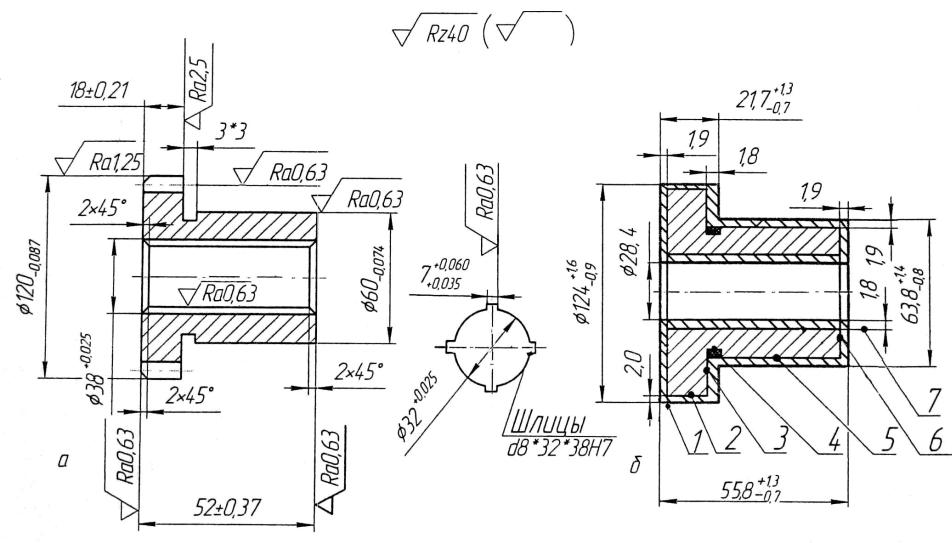
61
|
|
С |
|
и |
|
|
бА |
|
Д |
|
|
Рис.10.1 . Рабочий чертеж (а) и чертеж заготовки (поковки) (б) детали «Зубчатое колесо». Материал: сталь 20Х |
||
И |
|
|
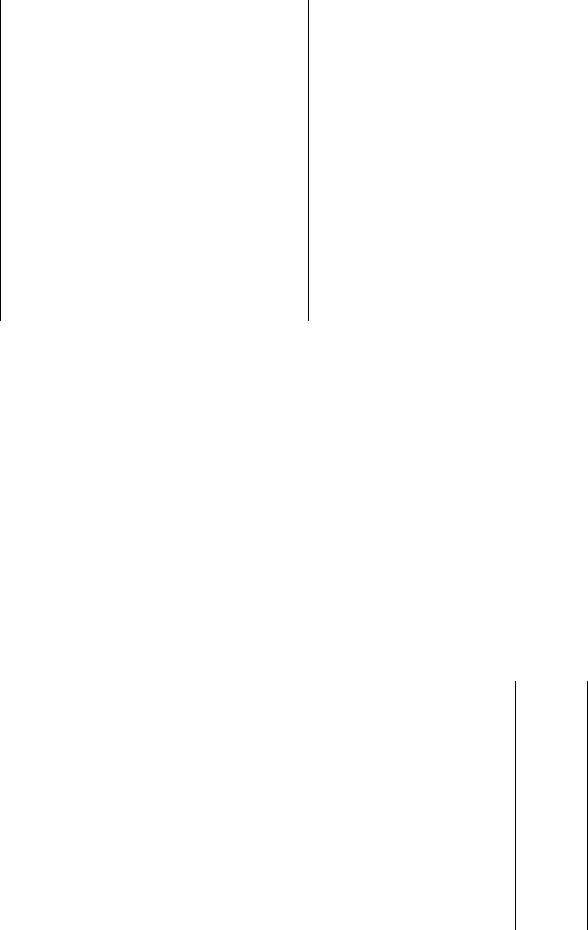
|
|
|
|
|
|
|
|
|
|
|
|
|
Окончание табл.10.2 |
|||||||
|
|
1 |
|
|
|
|
2 |
|
|
|
|
3 |
|
|
|
|
||||
|
Развёртывание: |
|
|
|
Rz20–Ra2,5 |
|
|
|
9–10 |
|
|
|
||||||||
|
|
черновое |
|
|
|
Ra2,5–0,63 |
|
|
|
6–8 |
|
|
|
|||||||
|
|
чистовое |
|
|
|
Ra0,63–0,32 |
|
|
|
8– (5–6) |
|
|||||||||
|
|
тонкое |
|
|
|
|
|
|
|
|
|
|
|
|
|
|
|
|
|
|
С |
|
|
|
Rz2,5–0,16 |
|
|
|
6–10 (5–6) |
|
|||||||||||
|
Протягивание |
|
|
|
|
|
|
|
||||||||||||
|
Шлифование круглое и плоское: |
|
|
|
|
|
|
|
|
|
|
|
|
|
|
|
||||
|
|
|
черновое (обд рочное) |
|
Rz40–Ra2,5 |
|
|
|
11 |
|
|
|
||||||||
|
|
|
ч стовое |
|
|
|
Ra1,25–0,63 |
|
|
|
9–10 |
|
|
|
||||||
|
|
|
тонкое |
|
|
|
Ra0,32–0,16 |
|
|
|
10–5(6) |
|
||||||||
|
Хонингован |
|
Ra1,25–0,01 |
|
|
|
8–5 |
|
|
|
||||||||||
|
Притирка |
|
|
|
|
|
|
|
|
|
|
|||||||||
|
|
|
е |
|
|
|
Ra0,32–0,02 |
|
|
|
8–5 |
|
|
|
||||||
|
уперфин ш рован е |
|
|
|
Ra0,32–0,01 |
|
|
|
|
|
|
|
|
|
||||||
|
Полирован е |
бА |
|
|
|
|
|
|
|
|
||||||||||
|
|
|
|
|
R21,25–0,04 |
|
|
|
|
|
|
|
|
|
||||||
|
|
|
|
Карта точности и качества |
|
|
|
Таблица 10.3 |
||||||||||||
|
1 |
|
2 |
|
3 |
|
4 |
|
5 |
|
|
6 |
|
7 |
|
|
8 |
|
|
|
|
|
|
|
|
Номер обрабатываемой поверхности по чертежу |
|
||||||||||||||
|
|
|
|
|
1 |
|
2 |
|
3 |
|
|
5 |
|
6 |
|
|
7 |
|
|
|
|
операции |
|
|
|
IT14 |
|
IT9 |
|
|
IT14 |
IT9 |
IT14 |
IT7 |
|
||||||
|
|
|
|
|
Точность и качество, задаваемые по чертежу |
|
||||||||||||||
|
|
Наименование |
|
|
Д |
|
|
|
||||||||||||
|
|
|
|
|
|
детали, IT14 / Ra2,5 |
|
|
|
|||||||||||
|
Номер |
и содержание операции |
Ra0,63 |
Ra1,25 |
Ra2,5 |
Ra0,63 |
Ra0,63 |
Ra0,63 |
|
|
||||||||||
|
|
|
|
|
|
Качество поверхностей заготовки |
|
|
|
|||||||||||
|
000 |
Заготовительная |
|
|
|
|
|
|
IT17/Rz50 |
|
|
|
|
|
|
|||||
|
|
|
|
|
|
|
|
|||||||||||||
|
|
|
Точность и качество, обеспечиваемые технологией |
|
|
|
||||||||||||||
|
|
|
|
|
|
|
|
|
|
|
|
|
|
|
|
|
|
|
|
|
005 |
Токарная |
|
|
|
|
|
|
IT14 |
|
IT12 |
IT14 |
|
IT12 |
|
|
|||||
|
|
Точение: черновое |
|
|
|
|
|
|
|
|
|
|||||||||
|
|
|
|
|
|
|
|
Rz80 |
|
Rz80 |
Rz80 |
|
Rz80 |
|
|
|||||
|
|
|
|
|
|
|
|
|
|
|
|
|
||||||||
|
|
|
|
|
|
|
|
|
|
|
|
|
|
|
|
|
|
|
|
|
010 |
Токарная |
|
IT14 |
|
IT12 |
|
|
|
И |
|
|
|||||||||
|
|
Точение: черновое |
|
|
|
|
|
|
|
|||||||||||
|
|
|
Rz80 |
|
Rz80 |
|
|
|
|
|||||||||||
|
|
|
|
|
|
|
|
|
|
|
|
|
|
|
|
|
|
|
||
|
|
|
|
|
|
|
|
|
|
|
|
|
|
|
|
|
|
|
|
|
015 |
Токарная |
|
IT14 |
|
IT10 |
|
|
|
|
|
|
|
|
|
|
|
|
|
||
|
|
Точение: чистовое |
|
Rz20 |
|
Rz20 |
|
|
|
|
|
|
|
|
|
|
|
|
|
|
|
|
Точение: тонкое |
|
IT14 |
|
IT9 |
|
|
|
|
|
|
|
|
|
|
|
|
|
|
|
|
|
|
|
Ra1,25 |
Ra1,25 |
|
|
|
|
|
|
|
|
|
|
|
|
|
|
|
020 |
Токарная |
|
|
|
|
|
|
|
|
|
|
|
|
|
|
IT8 |
|
|
|
|
|
Точение: чистовое |
|
|
|
|
|
|
|
|
|
|
|
|
|
|
|
|||
|
|
|
|
|
|
|
|
|
|
|
|
|
|
|
|
Ra1,25 |
|
|
||
|
|
|
|
|
|
|
|
|
|
|
|
|
|
|
|
|
|
|
||
|
|
|
|
|
|
|
|
|
|
|
|
|
|
|
|
|
|
|
|
|
62
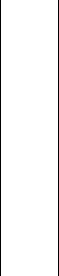
Окончание табл.10.3
|
1 |
|
2 |
|
|
3 |
|
4 |
5 |
6 |
7 |
8 |
|
025 |
|
Токарная |
|
|
|
|
|
|
|
|
|
|
|
|
Точение: чистовое |
|
|
|
|
IT14 |
IT10 |
IT14 |
|
|
|
|
|
|
|
|
|
|
|
Rz20 |
Rz20 |
Rz20 |
|
|
|
|
Точение: тонкое |
|
|
|
|
|
IT14 |
IT9 |
IT14 |
|
|
|
|
|
|
|
|
|
|
Ra2,5 |
Ra1,25 |
Ra1,25 |
|
|
030 |
|
Протяжка |
|
|
|
|
|
|
|
|
IT8 |
|
|
|
|
|
|
|
|
|
|
|
|
Ra1,25 |
|
045 |
|
Шл фовальная |
|
|
IT14 |
|
IT9 |
|
IT9 |
|
|
|
|
|
Шл фован е: тонкое |
|
|
|
|
|
||||
|
|
|
|
Ra0,63 |
Ra1,25 |
|
Ra0,63 |
|
|
|||
|
|
|
|
|
|
|
|
|
||||
|
|
|
|
|
|
|
|
|
|
|
||
|
050 |
|
и |
|
|
|
|
|
|
|
||
|
|
Шл фовальная |
|
|
|
|
|
|
|
IT14 |
IT7 |
|
|
|
|
Шл фован е: тонкое |
|
|
|
|
|
|
Ra0,63 |
Ra0,63 |
|
С |
|
|
|
|
|
|
|
|||||
|
|
|
бА |
|
|
|||||||
|
|
|
|
|
Контрольные вопросы |
|
|
|
||||
|
|
1. Что определяется по карте точности и качества? |
|
|
|
|||||||
|
|
2. Что является ор |
ент ром для составления карты точности и качества? |
|||||||||
|
|
3. Какие переходы нео ходимы для обработки поверхности с квалитетом |
||||||||||
|
IТ6 и качеством Rа 0,16? |
|
|
|
|
|
|
|
|
|||
|
|
4. На какие слои раз ивается о щий припуск на каждой обрабатываемой |
||||||||||
|
поверхности детали при составлении карты точности и качества? |
|
||||||||||
|
|
5. Какие переходы необходимы для обработки поверхности с квалитетом |
||||||||||
|
IТ5 и качеством Rа 0,02? |
|
|
Д |
|
|||||||
|
|
|
|
|
|
|
|
|
11. РАЗРАБОТКА ТЕХНОЛОГИЧЕСКИХ ОПЕРАЦ Й МЕХАНИЧЕСКОЙ ОБРАБОТКИ
Направленность раздела:
1.Обеспечение точности механической обработки деталей при различных методах обработки (табл.11.1).
2.Определение необходимого количества переходов в операциях для достижения заданных точности размеров и шероховатости поверхностей деталей.
3.Принцип назначения размеров слоёв металла, снимаемых с поверхностей заготовки.
4.Оформление переходов операций механической обработки.И
После составления маршрута обработки заготовки начинается следующий этап разработки технологического процесса – назначение технологических операций механической обработки [2]. При этом каждая операция разделяется на ряд переходов, необходимых для получения заданных точности размера и шероховатости для каждой обрабатываемой поверхности детали.
63
Составление плана механической обработки осуществляется на основе рабочего чертежа детали, чертежа заготовки, маршрута обработки и данных о точности и качестве заготовки. План обработки является одним из основных этапов подготовки технологического процесса к производству детали.
План механической обработки оформляется на бланке, в который входят: - номер операции;
С- наименование операции (например, токарная, сверлильная, фрезерная, шлифовальная и т.д.), точность обработки поверхности (например, точение черновое, точение чистовое, шлифование предварительное и т.д.), вид обработки и номер обрабатываемой поверхности (например: точить поверхность 2, рас-
точить поверхность 7, шл фовать поверхность 5 и т.д.); рациидиаметральный-; порядковые номера технологических переходов в пределах каждой опе-
-операц онные эск зы. Оформляются для каждой операции. Указываются базовые поверхности с условным о означением способа их закрепления. Обра-
-наименованиебАи модель станка, используемого на данной операции;
-оснастка и приспосо ления на станке, необходимые для осуществления данной операции.
Для выбора нео ходимых переходов для каждой обрабатываемой поверх-
ности детали служит карта точности и качества.
В качестве первых операций механическойДобработки применяют операции, при выполнении которых снимают максимальный слой металла (до 70% размера общего припуска) вплоть до полного снятия общего припуска тех поверхностей детали, точность размеров которых IT 13 ≥ 13–12 и шероховатости
данных поверхностей Rz80 и более. Это переходы черновой (обдирочной) или предварительной обработки. И
Количество последующих чистовых переходов зависит от точности размера и шероховатости каждой обрабатываемой поверхности, которые задаются, ориентируясь по данным табл. 11.1.
Разработка плана механической обработки начинается с назначения величин промежуточных размеров снимаемых слоев металла для каждой поверхности детали в зависимости от величины общего (исходного) припуска и потребного количества переходов для черновой и чистовой обработки (см. табл. 11.1).
64
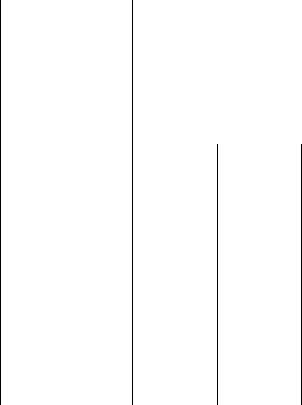
|
|
|
|
|
|
|
|
Таблица 11.1 |
||
|
Промежуточные размеры снимаемых слоев общего припуска, мм |
|||||||||
|
|
|
|
|
|
|
|
|
|
|
|
Номер |
|
1 |
2 |
3 |
5 |
|
6 |
|
7 |
|
поверхности |
|
|
|||||||
|
|
|
|
|
|
|
|
|
||
|
Общий |
|
1,9 |
2,0 |
1,8 |
1,9 |
|
1,9 |
|
1,8 |
|
припуск |
|
|
|
||||||
|
|
|
|
|
|
|
|
|
|
|
С |
|
|
Слои материала (Zi), |
|
|
|
||||
|
Вид |
|
|
|
|
|
|
|||
|
обработки |
|
снимаемые за i - е операции (10.1 и т.д.) |
|
||||||
|
Черновая |
|
Z10.1 =1,3 |
Z10.2 =1,4 |
Z5.1 =1,2 |
Z5.3 =1,3 |
|
Z5.2 =1,3 |
|
Z5.40=0,55 |
|
обработка |
|
|
|
|
|
|
|
|
|
|
отверстшлицевогоя |
Z15.3= |
Z25.1= |
Z25.5= |
|
Z25.3= |
|
Z20.1 = |
||
|
Чистовая |
|
Z15.1= |
|
|
|||||
|
обработка |
|
0,35 |
0,35 |
0,4 |
0,35 |
|
0,35 |
|
0,2 |
|
Тонкая |
|
Z15.2 =0,2 |
Z15.4 =0,2 |
Z25.2=02 |
Z25.6 =0,2 |
|
Z25.4 =0,2 |
|
- |
|
обработка |
|
|
|
||||||
|
|
|
|
|
|
|
|
|
|
|
|
|
бА |
|
|
|
|
|
|||
|
Протяг ван е |
- |
- |
- |
- |
|
- |
|
Z30.1 =1,0 |
|
|
Шлифован е |
Z45.3 = |
Z45.1 = |
|
Z45.2 = |
|
Z50.2= |
|
Z50.1= |
|
|
чистовое |
|
0,05 |
0,05 |
- |
0,05 |
|
0,05 |
|
0,05 |
|
окончательное |
|
|
|
|
|
|
|
|
|
|
На каждом последующем переходе чистовой обработки следует назначать |
|||||||||
меньшую величину снимаемого слоя металла. Например, при тонком |
точении |
|||||||||
|
|
|
|
Д |
глубина резания t при Rа ≤ 0,63 должна составить не более 0,1–0,4мм. При
предварительном (черновом) шлифовании снимаемый слой припуска может назначаться до 0,5 мм и более. При окончательном (тонком) шлифовании величина снимаемого слоя припуска не должна превышать 0,025–0,05мм [1].
В качестве примера представлен план механической обработки (табл. 11.2)
детали “Зубчатое колесо” (рис.11.1). |
И |
|
65
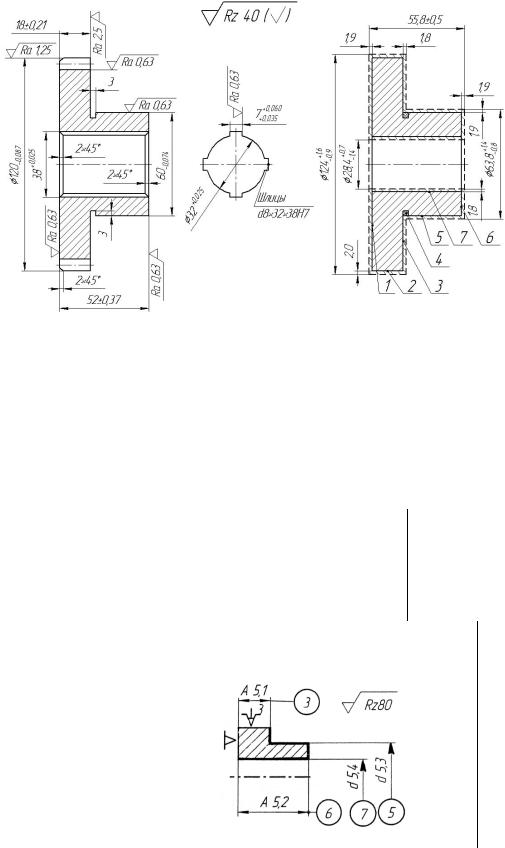
С |
|
|
|
|
|
|
|
|
|
||
|
и |
|
|
|
|
Таблица 11.2 |
|||||
|
|
Зубчатое |
|
|
|||||||
|
|
а |
|
|
|
|
|
|
б |
|
|
|
|
Р с. 11.1. Ра очий чертеж ( |
) и чертеж заготовки (поковка) (б) |
||||||||
|
|
|
детали “ |
|
колесо” |
|
|
|
|||
|
|
План механической о ра отки детали «Зубчатое колесо» |
|||||||||
|
|
|
|
|
|
|
|
|
|
|
|
|
|
|
|
|
|
|
|
Наиме- |
|
|
|
|
операции |
|
перехода |
|
Д |
|
|
||||
|
|
Наименование |
|
АОперационные эскизы |
нова- |
Станочное |
|
||||
|
|
и содержание опе- |
|
ние |
приспо- |
|
|||||
|
|
рации |
|
|
|
|
|
|
и мо- |
собление |
|
|
№ |
№ |
|
|
|
|
|
дель |
|
||
|
|
|
|
|
|
|
|
|
|||
|
|
|
|
|
|
|
станка |
|
|
||
|
|
|
|
|
|
|
|
|
|
|
|
|
1 |
2 |
3 |
|
|
4 |
|
|
5 |
6 |
|
|
000 |
Заготовительная |
- |
|
Эскиз заготовки |
И |
|
||||
|
|
|
|
|
|
||||||
|
|
Токарная |
|
|
|
|
|
|
|
Патрон |
|
|
|
Точение черновое: |
|
|
|
|
|
Токар- |
трехкулач- |
|
|
|
|
подрезка торцов3, 6, |
1,2 |
|
|
|
|
|
но- |
ковый |
|
|
005 |
точение поверхно- |
|
|
|
|
|
винто- |
самоцент- |
|
|
|
|
сти 5, |
3 |
|
|
|
|
резный |
рирующийся |
|
|
|
|
растачивание отвер- |
|
|
|
|
|
|
16К20 |
ГОСТ |
|
|
|
стия 7 |
4 |
|
|
|
|
|
|
2675–80 |
|
|
|
|
|
|
|
|
|
|
|
|
|
66
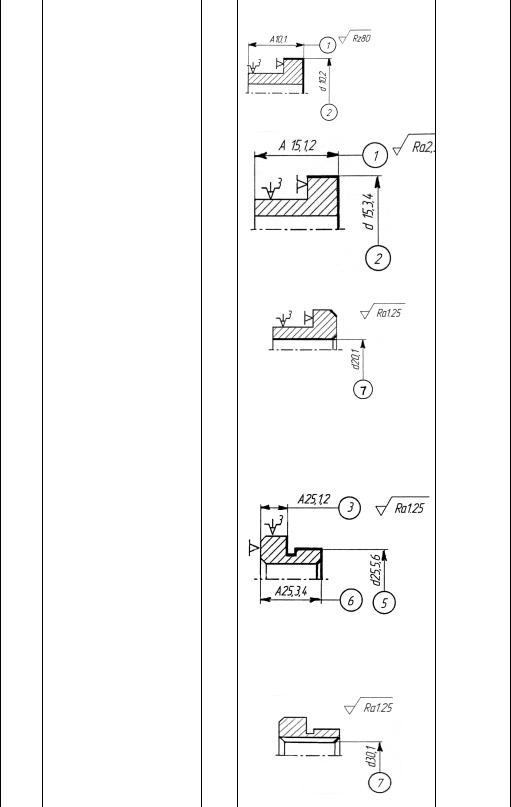
|
|
|
|
|
|
|
Продолжение табл.11.2 |
||||
|
|
1 |
2 |
3 |
|
4 |
|
|
5 |
6 |
|
|
|
|
|
|
|
|
|
|
|
|
|
|
|
010 |
Токарная |
|
|
|
|
|
|
|
|
|
|
Точение черновое: |
|
|
|
|
|
|
|
|
|
|
|
|
подрезка торца 1; |
1 |
|
|
|
|
То же |
То же |
|
|
|
|
точение поверхно- |
|
|
|
|
|
|
|
|
|
|
|
сти 2 |
2 |
|
|
|
|
|
|
|
|
|
|
|
|
|
|
|
|
|
|
|
С |
|
|
|
|
|
|
|
|
|||
015 |
Токарная |
|
|
|
|
|
|
|
|
||
Точение чистовое и |
|
|
|
|
|
|
|
|
|||
|
|
|
тонкое: |
|
|
|
|
|
|
|
|
|
|
|
подрезать торец 1 |
1,2 |
|
|
|
|
То же |
То же |
|
|
|
|
под шл фован е; |
|
|
|
|
|
|||
|
|
стишл цевого отвер- |
1 |
|
|
|
|
То же |
То же |
|
|
|
|
|
точен е поверхно- |
|
|
|
|
|
|
|
|
|
|
|
2 под шл фова- |
3.4 |
|
|
|
|
|
|
|
|
|
|
н е |
|
|
|
|
|
|
|
|
|
|
|
Токарная |
|
|
|
|
|
|
|
|
020 |
Точен е ч стовое: |
|
|
|
|
|
|
|
|
||
|
|
|
расточ ть отверст е |
|
|
|
|
|
|
|
|
|
|
|
7 под протяг ван е |
|
|
|
|
|
|
|
|
|
|
|
ст я; |
|
|
|
|
|
|
|
|
|
|
|
снять фаски |
|
|
|
|
|
|
|
|
|
|
|
|
|
|
|
|
|
|
|
|
|
|
|
Токарная |
|
|
|
|
|
|
|
|
025 |
подрезать торец 3 |
1,2 |
|
Д |
|
|
|||||
|
|
|
окончательно; |
|
|
|
|
||||
|
|
|
подрезать торец 6 |
|
|
|
|
||||
|
|
|
|
|
|
|
|
|
|
|
|
|
|
|
под шлифование; |
3,4 |
|
|
|
|
|
|
|
|
|
|
точениебАповерхно- |
То же |
То же |
|
|||||
|
|
|
сти 5 под шлифова- |
|
|
|
|
|
|
|
|
|
|
|
ние; |
5,6 |
|
|
|
|
|
|
|
|
|
|
проточить канавку 4 |
|
|
|
|
|
|
|
|
|
|
|
окончательно; |
|
|
|
|
|
|
|
|
|
|
|
снять фаску отвер- |
7 |
|
|
|
|
|
|
|
|
|
|
стия |
|
|
|
|
|
|
|
|
|
|
|
|
|
|
|
|
|
|
|
|
030 |
Протяжная |
|
|
|
|
|
|
|
|
||
|
|
|
протянуть четырех- |
|
|
|
|
Протяж- |
Жесткая |
|
|
|
|
|
шлицевое отверстие |
1 |
|
|
|
|
|||
|
|
|
|
|
|
ной 7512 |
опора |
|
|||
|
|
|
Ø32Н7х38Н11х4 |
|
|
|
|
|
|||
|
|
|
|
|
|
И |
|
||||
|
|
|
под шлифование |
|
|
|
|
|
|
|
|
67
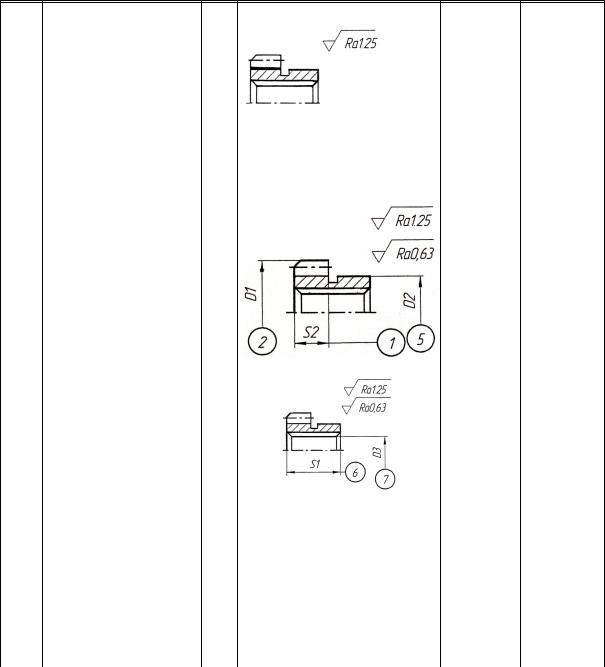
Окончание табл. 11.2
1 |
2 |
3 |
4 |
5 |
6 |
035 |
Фрезерная |
|
|
Зубофре- |
|
|
фрезеровать 44 зуба |
1 |
|
Приспо- |
|
|
(m=2,5) под шлифо- |
|
|
зерный |
|
|
вание |
|
|
53А20В |
собление |
|
|
|
|
|
|
|
|
|
|
|
|
С |
1 |
|
|
|
|
||
040 |
Фрезерная |
|
Полу- |
Трех- |
|||
|
|
зачистить заусенцы |
|
|
кулачко- |
||
|
|
на торцах зубьев |
|
|
автомат |
вый па- |
|
|
|
|
|
|
5Б532 |
трон |
|
|
045 |
Шл фовальная |
|
|
|
|
|
|
ности |
|
|
|
|
||
|
|
Шл фован е ч сто- |
1,2 |
|
|
|
|
|
|
вое |
|
|
Кругло- |
Гриб- |
|
|
|
шл фовать поверх- |
3 |
|
шлифо- |
||
|
|
2, 5 торец 1 |
|
|
ковая оп- |
||
|
|
окончательно |
|
|
вальный |
равка |
|
|
|
|
|
3Т161Д |
|||
|
|
|
|
|
|
|
|
|
|
|
|
|
|
|
|
050 |
Шл фовальная |
1 |
|
Внутри- |
|
|
|
|
|
Шл фован е ч сто- |
|
|
|
|
|
|
|
вое |
2 |
|
шлифо- |
|
|
|
|
шлифовать поверх- |
|
|
вальный |
Приспо- |
|
|
|
ность 7и торец 6 |
|
|
3А227А |
собление |
|
|
|
окончательно |
|
|
Ф2 |
|
|
|
|
|
|
|
|||
055 |
но |
Д |
|||||
Шлифовальная |
|
|
Специ- |
Трех- |
|||
|
|
ШлифоватьбАбоковые - |
альный |
кулачко- |
|||
|
|
стороны шлицев |
|
|
|
вый па- |
|
|
|
окончательно |
|
|
|
трон |
|
|
060 |
Шлифовальная |
|
|
Зубо- |
|
|
|
|
Шлифовать 44 зуба |
- |
И |
|||
|
|
(m=2,5) окончатель- |
|
шлифо- |
Оправка |
||
|
|
|
|
вальный |
|
|
|
|
|
|
|
|
|
|
|
|
|
|
|
|
5В833 |
|
|
|
|
|
|
|
|
|
|
|
|
|
Контрольные вопросы |
|
|
|
1. Как обозначаются обрабатываемые поверхности детали?
2. Как разбивается общий припуск на обработку на промежуточные слои, снимаемые с поверхностей?
3. Какие переходы используются при обработке на токарном станке?
4. Какова рекомендуемая глубина резания при тонком точении на токарном станке?
5. Каковы рекомендуемые величины снимаемых слоев при окончательном шлифовании?
6. Как указываются запланированные в плане механической обработки переходы?
68
7. Каковы условия завершения операций черновой обработки всех поверхностей?
8.Что указывается на операционном эскизе?
9.Как указываются номера операций, их наименование и содержание?
10.Как обозначается закрепление на станке обрабатываемой заготовки?
С12. ОСНОВЫ ВЫБОРА РЕЖУЩЕГО ИНСТРУМЕНТА
ПРИ ТОЧЕНИИ НА ТОКАРНОМ СТАНКЕ
Направленность раздела:
плашки1.Освоен е услов й выбора типа резца с соответствующими геометрическими параметрами его режущей части.
2. Выбор необход мых резцов с указанием материала режущей части для всех обрабатываемых поверхностей заготовки.
При обработкебАдеталей на токарных станках основным режущим инструментом являются резцы; спользуются также сверла, зенкера, развертки, метчики, , фрезы.
Конф гурац режущ х частей резцов и используемых для них инструментальных матер алов разноо разны, их конкретные названия установлены соответствующими стандартами в зависимости от вида обработки заготовок. Названия проходных (наружное о тачивание) и расточных (внутреннее растачивание) резцов по ГОСТу установлены в зависимости от положения обрабатываемой поверхности по отношению к соседней поверхности детали на пути резания. Например, при растачивании отверстияДрезец выбирается в зависимости от формы отверстия (сквозное или глухое). Также выбираются и проходные резцы, т.е. если при обтачивании наружной поверхности проходному резцу не препятствует прямой выступ другой поверхности (ступень детали), то выбирается резец проходной отогнутый или проходной прямой, а если препятствует,
-токарный прорезной резец с пластиной из твердогоИсплава (ГОСТ 18894 – 73),
рис. 12.1, 2;
-токарный резьбовой резец с пластиной из твердого сплава для нарезания наружной резьбы (ГОСТ 18885 – 73), рис. 12.1, 3;
-токарный проходной упорный резец с пластиной из твердого сплава
(ГОСТ 18879 – 73), рис. 12.1, 4;
–токарный подрезной отогнутый резец с пластиной из твердого сплава (ГОСТ 18880 – 73), рис. 12.1, 5;(-то проходной упорный.
69
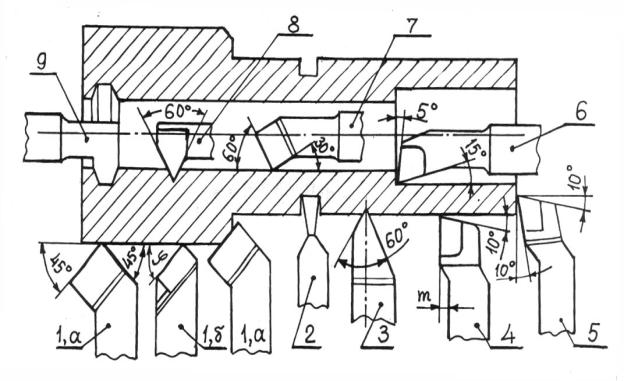
– токарный расточной резец с пластиной из твердого сплава для обработки глухих отверстий (ГОСТ 18883 – 73), рис. 12.1, 6;
– токарный расточной резец с пластиной из твердого сплава для обработки сквозных отверстий (ГОСТ 18882 – 73), рис. 12.1, 7;
– токарный резьбовой резец с пластиной из твердого сплава для нарезания резьбы в отверстиях (ГОСТ 18885 – 73), рис. 12.1, 8;
С– токарный прорезной резец с пластиной из твердого сплава для нарезания канавок в отверстиях, рис. 12.1, 9.
Примечание. 1. Резцы проходные отогнутые и прямые с φ = 45° используются для снятия фасок (см. р с.12.1).
В том случае, если указывается материал пластины (быстрорежущая сталь или твердый сплав), то обязательно проставляется марка этого материала. Например, при токарной обработке углеродистых и легированных сталей используется Т15К6, при обработке чугуна – ВК6 и т.д.
и бА Д Рис.12.1. Типы токарных резцовИ
Большинство инструментов изготавливается составными (рис. 12.2): рабочая часть резца (пластина) – из инструментального материала; крепежная (стержень и головка резца) – из конструкционных сталей. Пластины из твердых сплавов соединяют с крепежной частью пайкой. Многогранные твердосплавные пластины закрепляют прихватами, винтами, клиньями и т.д. [2].
В зависимости от направления движения подачи различают левые и правые резцы (рис. 12.2).
70
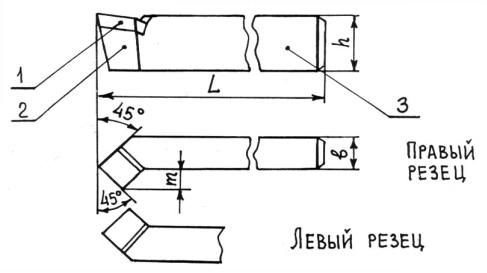
Тип токарного резца, размеры h × b стержня, вид и марка инструментального материала, способ заточки резца и конфигурация режущей части резца выбирается в зависимости от:
- типа токарного станка; - обрабатываемого материала;
- вида операции и перехода;
С |
|
|
- применяемой смазывающе-охлаждающей жидкости. |
||
и |
|
|
бА |
||
Рис. 12.2. |
Основные элементы токарных резцов: 1 – пластина |
|
из инструментального материала; 2 – головка резца, |
||
на которой крепится пластина; 3 – стержень резца |
||
|
Должны |
|
При закреплении резца в резцедержателе вершина режущей части резца |
||
должна быть на уровне оси шпинделя. |
быть выбраны необходимые |
размеры h × b стержня резца. Для станка16К20 размеры h × b равны 25×16 мм. Контроль установки резца производится по опорному центру, и при необходи-
-для чернового точения (обдирки) на точильноИ-шлифовальных станках, абразивными кругами из электрокорунда; из зеленого карбида кремния для резцов, оснащенных пластинами из твердого сплава.
-для получения заданных на рабочем чертеже детали классов точности размеров и качества обрабатываемых поверхностей при чистовых и тонких переходах рабочие поверхности подвергают не только заточке, но и доводке.
Алмазную заточку выполняют на станках с охлаждением зоны заточки специальной жидкостью.
71
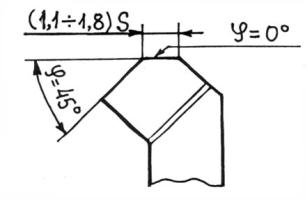
После заточки твердосплавные резцы подвергают доводке (без охлаждения) на алмазных доводочных кругах. Алмазная доводка шлифованием увеличивает долговечность резца в 1,5–2 раза.
целью повышения качества обрабатываемых поверхностей при чистовой завершающей обработке вершину резца делают округленной радиусом r. При завершающей чистовой или тонкой обработке используется подача значительно меньшая, чем при предварительной черновой и получистовой обработках. Вершина резца закругляется r =0,4 мм; 0,8 мм; 1,2 мм или 1,6 мм.
При чистовой и тонкой обработке снижается глубина резания t, но число оборотов шп нделя n, об/м н, увеличивается.
Когда черновая обработка определенной поверхности является завершаю- |
|
щей (класс точности по 14 квалитету, а требования по качеству поверхности |
|
RZ ≥ 80 мкм), то резец для такой завершающей черновой обработки должен |
|
С |
|
иметь режущую кромку с углом φ = 0 (рис. 12.3). При этом срезаются обра- |
|
зующиеся |
знач тельной черновой подаче остаточные гребешки [22]. |
при |
|
|
Рис. 12.3. Проходной резец при точении с большой подачей S |
|
бА |
Рациональныйразмеррежущейкромкиприφ=0долженсоставлять(1,1– 1,8)S. |
|
|
Контрольные вопросы |
1.Какие режущиеинструменты используются приточении на токарномстанке? |
|
|
Д |
2. Из каких инструментальных материалов изготавливают режущий инст- |
|
|
И |
румент?
3.Какподразделяютсярезцывзависимостиотвидаобрабатываемойповерхности? 4. Из каких марок твёрдого сплава изготавливают пластины резцов для об-
работки сталей и для обработки чугунов?
5. Из каких основных частей состоит токарный резец?
6. Какие изготавливаются резцы в зависимости от направления движения подачи?
7. Из каких условий выбираются размеры стержня резца?
8. На каких станках затачиваются лезвия резцов для черновой обработки? 10.На каких станках затачиваются лезвия резцов для чистовой и тонкой об-
работок?
72