
2510
.pdf-количество рабочих, выполняющих каждую операцию на рабочем посту или в звене, зависит не только от нормы времени, но и от состава работ, массы используемых предметов труда, степени механизации и автоматизации процесса;
-при правильной организации труда на стадии проектирования линии расчетная загрузка каждого рабочего на технологических операциях должна составлять от 90 до 110 %.
Рациональная расстановка рабочих по постам (или звеньям) обеспечивает синхронность работы этих постов, т.е. устойчивую и равномерную загрузку как оборудования, так и рабочих. Синхронность характеризуется следующим соотношением:
t1 |
|
t2 |
... |
ts |
rпр |
, |
(23) |
|
|
|
|||||
c1пр |
|
c2пр |
|
csпр |
л |
|
|
|
|
|
|
|
где ts - численное значение суммы норм времени выполняемых операций на s-ом посту или s-ым звеном рабочих, чел.-мин;
сsпр - принятое количество рабочих на s-ом посту или в s-ом звене рабочих, чел.;
s - количество постов или звеньев рабочих на линии. Синхронизировать работу поточной линии можно с использованием
трех типовых приемов:
-изменением количества операций, выполняемых на одном посту или одним звеном рабочих;
-размещением на одном посту нескольких предметов труда, обрабатываемых одновременно или последовательно;
-совершенствованием технологии и организации выполнения операций, позволяющим сократить продолжительность их выполнения. Результаты синхронизации можно представить в форме табл. 26. В ряде случаев, когда некоторые рабочие на линии загружены менее чем на 90 %, допускается в конце таблицы предусмотреть для них «прочие работы». Если в результате использования приемов синхронизации не удается полностью загрузить рабочего на одном посту, то приходится предусматривать выполнение им работ на другом посту, отразив соответствующие переходы в графике-регламенте загрузки рабочих. Однако, при поштучном выпуске продукции на непрерывно-поточной технологической линии при многократном переходе рабочего с одного места на другое уменьшается время выполнения за смену непосредственно технологических операций, что является нерациональным как с организационной точки зрения, так и с точки зрения психологии труда. Целесообразнее в этом случае организовать обработку предметов труда на постах партиями с меньшим количеством переходов рабочих за смену; это можно осуществить как в непрерывно-поточном, так и в прерывнопоточном производстве.
79
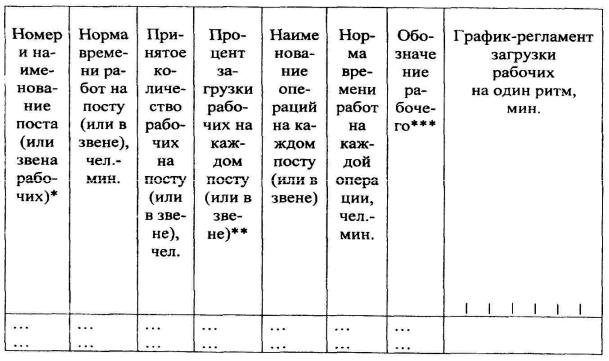
Выдержка из примера синхронизации работы формовочной линии с агрегатно-поточным способом производства многопустотных плит перекрытий с ритмом выпуска продукции 8,9 мин приведена в табл. 27.
Условно выполненные ранее расчеты показали необходимость организации при таком ритме и Ткр=12 мин двух параллельно расположенных участков на посту формования с двумя комплектами формовочного оборудования и одним общим пультом управления. На каждом из этих участков изделие формуют на протяжении двух ритмов, попеременно передавая на тепловую обработку по одной плите через каждый ритм. В примере принято, что рабочий А (оператор) с общего пульта управляет бетоноукладчиками, формовочными установками и порталами на обоих постах. Поэтому откорректированная норма времени на машинных операциях составила 15,6 чел.-мин или 7,8 чел.-мин за один ритм.
Таблица 26
Результаты синхронизации работы поточной линии
Примечания:
*в таблицу необходимо включить все рабочие посты, в т.ч. и те, на которых находится в обработке несколько предметов труда;
**процент загрузки группы рабочих на одном посту или в одном звене
определяют по формуле (ts /rлприн)∙100 %;
*** обозначение рабочих можно производить численными номерами или буквами, но каждый рабочий должен иметь свое обозначение.
Если бы пульты управления стояли на каждом участке отдельно, то норма времени составила бы 24,4 чел.-мин (или 12,2 чел.-мин за ритм), что следует из продол- жительности выполнения каждой операции отдельно, и потребовались бы два оператора.
80

Таблица 27 Пример синхронизации работы двух постов формования агрегатно-поточной линии производства
многопустотных плит перекрытий при ритме выпуска изделий 8,9 мин и ритме работы каждого поста формования 17,8 мин
81
81

Окончание табл. 27
82
Примечание. На посту № 3 за 17,8 мин выполнены все операции для одного изделия, а на посту № 4 выполнена вторая половина операций для одного изделия и первая половина операций для второго изделия.
82
3.3.10.6. Организация рабочих мест
Под организацией рабочих мест понимают создание на каждом из них условий, способствующих полному использованию технологических возможностей оборудования при минимальной утомляемости рабочих и соблюдении требований охраны труда. Рациональная организация рабочего местаповышает производительность труда без значительных материальных и финансовых затрат.
Описание организации рабочих мест для каждого рабочего поста сопровождают схемами (пример приведен на рис. 8), которые в дальнейшем можно использовать как основу для компоновки технологической линии.
На схемах обозначают оборудование, оснастку, площадки для промежуточного складирования предметов труда, места основного расположения рабочих, наносят определяющие размеры.
В заключении этого пункта пояснительной записки подводят итог по явочной численности основных рабочих на линии. При этом к составу рабочих, полученному при выполнении предыдущего пункта, следует прибавить необходимое количество крановщиков и операторов, других транспортных средств, которых также можно отнести к категории основных рабочих.
3.3.10.7. Количество предметов труда в заделах на формовочных линиях
Принятая в проекте ритмичность производства на некоторых рабочих постах в силу ряда обстоятельств может нарушаться, что неизбежно вызывает сбои в работе других постов из-за нехватки или избытка предметов труда, предназначенных для обработки. Чтобы застраховать технологическую линию от подобных сбоев в проектах предусматривают так называемые технологические заделы. Величины заделов для непрерывно-поточных линий не рассчитывают, а принимают исходя из технологических и организационных соображений. Например, величину заделов перед камерами тепловой обработки периодического действия и после них принимают по их вместимости.
Соответственно величинам заделов предусматривают производственные площади для их промежуточного складирования.
83
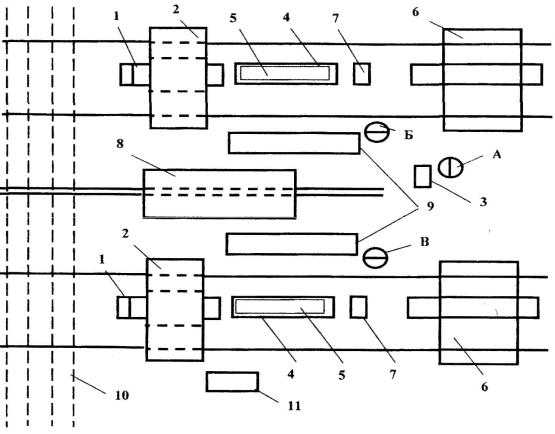
Рис. 8. Пример схемы организации рабочих мест на параллельных постах формования многопустотных плит перекрытий
на агрегатно-поточной линии с ритмом 8,9 мин:
1 - формовочная установка; 2 – бетоноукладчик; 3 - пульт управления; 4 – виброплощадка; 5 – поддон; 6 - портал со съемной бортоснасткой и пригрузом; 7 - оснастка для формования бетонных пробок;
8 - тележка для доставки арматурных изделий; 9 - площадка для промежуточного складирования арматурных изделий; 10 - бетоновозная эстакада; 11 - шкаф для хранения рабочих инструментов; А,Б,В - рабочие
Для прерывно-поточного производства с изменяющимся количеством предметов труда между рабочими постами расчеты заделов проводят на основании графика-регламента загрузки рабочих, который является основанием для определения величин изменения заделов ΔZi-j между i-ым и смежным с ним j-ым постом; эти изменения для наглядности изображают эпюрой заделов. При проектировании прерывно-поточного производства эпюру изменения заделов целесообразно совместить с графикомрегламентом загрузки рабочих. Пример такого изображения приведен в табл. 28.
Изменение величины задела можно рассчитать по формуле
T |
пост |
сL |
T |
пост |
сL |
|
|||
ZiL j |
1 |
i |
|
1 |
j |
, |
(24) |
||
|
|
|
|
||||||
|
|
ti |
|
|
|
tj |
|
|
|
84
где ZiL j - изменение величины задела (шт.) между i-ым и j-ым постами
на L-ом отрезке ритма с неизменной численностью рабочих на обоих смежных постах, т.е. при постоянной продолжительности выполнения операций;
T1пост - продолжительность работы на L-ом отрезке ритма с
постоянной численностью рабочих на каждом из двух смежных постов, мин.;
сiL ,cLj - неизменное количество рабочих i-го и j-го постов на L-ом отрезке ритма, чел.;
ti, tj - нормы времени на обработку одного предмета труда на i-ом и j-ом постах, чел.-мин/шт.
Величину задела удобно считать в количестве предметов труда, размещенных на площадках между рабочими постами; соответственно норму времени принимают на один предмет труда, а не на всю партию.
Проиллюстрируем использование формулы (24) для расчетов изменений величин заделов между смежными постами 2 и 3 на графикерегламенте загрузки рабочих, представленного в табл. 28.
Анализ графиков-регламентов загрузки рабочих на представленных постах позволил выделить три отрезка времени ритма с неизменным количеством рабочих.
Первый отрезок (L = 1) характеризуется неизменным количеством рабочих как на втором, так и на третьем посту (по два человека); продолжи-
тельность работ на этом отрезке T пост |
составляет 48 минут. На втором |
1 |
|
отрезке (L = 2) вдвое уменьшилось количество рабочих на втором посту при неизменном составе звена на третьем. При этом длительность выполнения работ на втором посту по сравнению с первым отрезком увеличилась вдвое, а на третьем посту не изменилась, но тем не менее в пределах второго отрезка времени длительность выполнения работ на
Tпост
обоих постах не изменялась. Продолжительность работ 2 (54 минуты)
равна разнице между временем занятости рабочих Д и Е на третьем посту
Tпост
(102 минуты) и продолжительностью работ 1 (48 минут).
На третьем отрезке (L = 3) на втором посту остается один рабочий, а на третьем - ни одного; тем не менее длительность выполнения работ на каждом из этих постов постоянна, равная, в частности, на третьем посту нулю. Как видно из графика-регламента, продолжительность работ на этом
участке T3пост=18 минутам. Таким образом, расчетные значения изменений величин заделов по участкам составят:
85
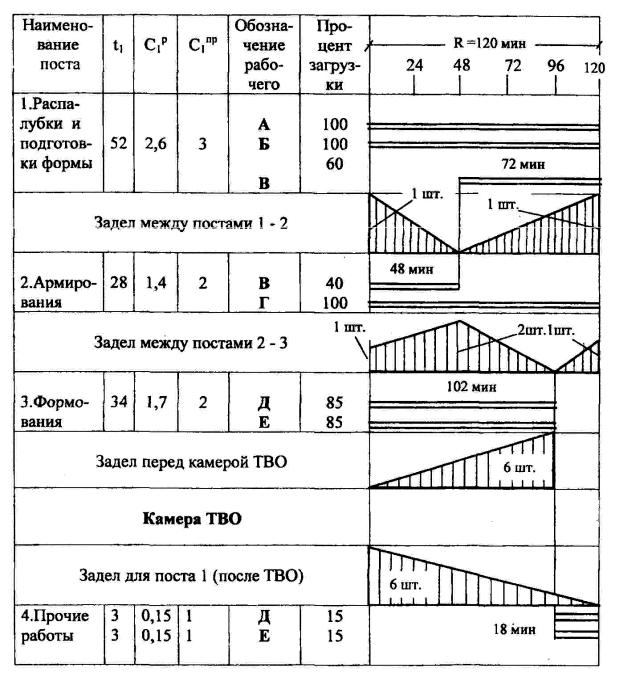
Таблица 28
Пример графика-регламента, совмещенного с эпюрой заделов (партия из 6 изделий с условным ритмом выпуска каждого – 20 мин, нормы времени на один предмет труда приняты условные, вместимость камеры – 6 форм с изделиями)
Примечание. Время загрузки рабочего на посту получено как произведение длительности ритма на относительное значение степени загрузки рабочего.
86
|
|
Z21 |
3 |
T1пост |
c12 |
|
T1пост c31 |
|
|
|
|||||||||||
|
|
|
|
|
|
|
|
|
t3 |
|
|||||||||||
|
|
|
|
|
|
|
|
|
|
|
|
t2 |
|
|
|
|
|
||||
|
48мин 2чел. |
|
|
|
48мин 2чел. |
0,6шт. |
|
||||||||||||||
28чел. мин/чел. |
34 чел. мин/чел. |
|
|||||||||||||||||||
|
|
|
|
||||||||||||||||||
|
Z2 |
|
54 1 |
|
54 2 |
|
1,93 3,18 1,25шт. |
|
|||||||||||||
|
|
|
|
|
|
||||||||||||||||
|
2 3 |
|
28 |
|
|
|
|
|
34 |
|
|
|
|
|
|
|
|
||||
|
Z3 |
|
|
18 1 |
|
18 0 |
0,65 0 0,65шт. |
|
|||||||||||||
|
|
|
|
|
|||||||||||||||||
|
2 3 |
|
|
|
28 |
|
|
|
|
34 |
|
|
|
|
|
|
|
пост |
|||
Положительное значение ΔZ означает, что задел на протяжении T |
|||||||||||||||||||||
|
|
|
|
|
|
|
|
|
|
|
|
|
|
|
|
|
|
|
|
1 |
увеличивается за счет меньшей длительности выполнения работ звеном рабочих на посту №2 по сравнению с постом №3, отрицательное значение
Tпост
показывает, что задел на протяжении 2 уменьшается за счет меньшей
длительности выполнения работ на посту №3 по сравнению с постом №2. Рассчитанные таким образом значения ΔZ являются только изменением величин заделов, а абсолютные значения самих заделов Z необходимо
принять после сопоставления всех расчетных значений ΔZ для двух сравниваемых смежных операций. Принятые значения заделов должны быть представлены целыми числами. Для принятия окончательного решения руководствуются следующими положениями:
-должно обеспечиваться равенство значений величин заделов в начале и в конце ритма выпуска партии изделий, т.к. конец одного ритма является одновременно и началом для следующего;
-уменьшать задел можно только от положительного (плюсового) значения до нуля, так как отрицательного количества предметов труда не может быть.
Исключением из первого положения могут быть заделы до и после аппаратов тепловой обработки периодического действия, если формирование этих заделов происходит постепенно от нуля до количества изделий, загружаемых затем сразу в аппарат или наоборот - после выгрузки всей партии из аппарата с постепенной передачей их на рабочий пост.
Рассмотрим один из возможных вариантов изменения заделов на при-
мере анализа результатов приведенных выше расчетов Z21 3.
Расчетное значение Z22 3 = -1,25 означает, что на втором отрезке
ритма (54 мин) рабочий Г на втором посту успевает выполнить армирование всего двух форм (54 мин/28 чел.-мин), а рабочие на третьем посту успевают заформовать более трех изделий (54 мин 2 чел./34 чел.-мин). Следовательно, для работы без простоев им необходимо иметь в заделе две формы, а ΔZ будет изменяться от 2 до 0; на следующем, третьем отрезке
87
ритма (18 мин) задел увеличится от 0 до 1. Так как величины заделов в начале и в конце ритма должны быть одинаковы, то на первом его отрезке (L=1) задел, увеличиваясь на одну единицу, должен измениться от одной до двух форм.
На основании такого анализа построена эпюра изменения заделов между постами 2 и 3. В этом примере величина задела для ямной камеры возрастает от 0 до 6 (в соответствии с вместимостью камеры), а после тепловлажностной обработки - убывает от 6 до 0.
Закончить этот пункт следует сводкой принятых и обоснованных решений по заделам, по величине каждого из них, по принятым способам размещения заделов в пространстве (по отдельности, в штабеле), по необходимым для этого производственным площадям с учетом проходов и проездов, которые должны быть учтены при компоновке линии в пространстве.
3.3.10.8. График производственного процесса на формовочной линии
Рациональное размещение поточной линии в пространстве невозможно без использования таких сведений об организации производственного процесса во времени, которые характеризуют его ритмичность, продолжительность аппаратурных процессов и перерывов (технологических, организационных). Эти сведения дают возможность определить:
-минимальное количество форм (или поддонов, вагонеток, стендов, кассетных установок и т. д.) для устойчивой непрерывной работы;
-минимальное количество аппаратов тепловой обработки периодического действия или вместимость аппаратов непрерывного действия;
-площади для промежуточного складирования или комплектования заделов предметов труда;
-длительность операционного цикла на проектируемой линии. Перечисленные показатели наиболее полно и точно получают с помощью графика производственного процесса, при разработке которого целесообразно использовать следующие правила:
-минимальное количество форм или других предметов (объектов) труда определяют по тому их количеству, которое участвует в производственном процессе до тех пор, пока первый объект труда не возвратится к первому посту (или звену рабочих) после прохождения всего операционного цикла на проектируемой поточной линии;
-вместимость одного аппарата тепловой обработки (ТО) периодического действия (т. е. количество объектов труда, загружаемых в него на один цикл обработки) принимают при обосновании технологии исходя из общих технических характеристик аппаратов, изделий и т. п.;
88