
1168
.pdf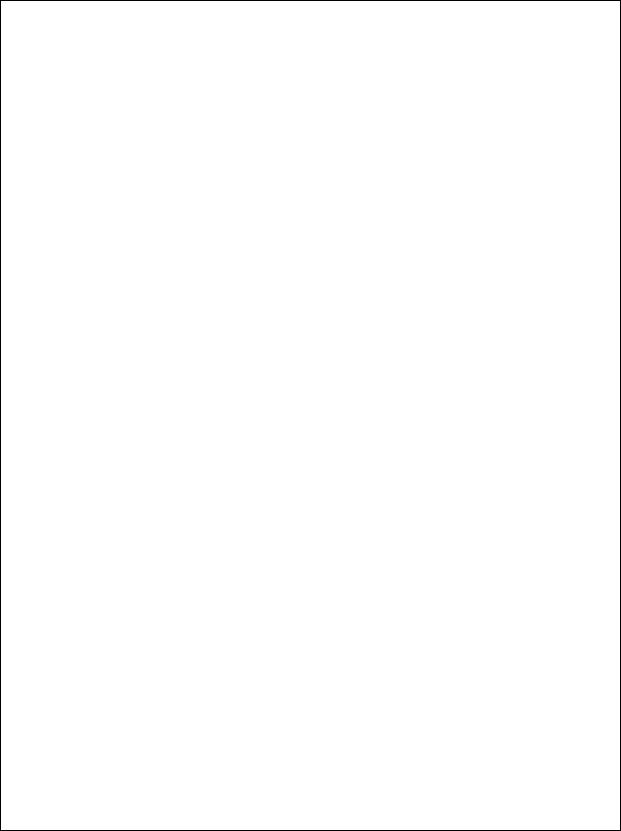
Приложение 6
Пример оформления библиографического списка
БИБЛИОГРАФИЧЕСКИЙ СПИСОК
1.Жаворонков Е.П. Организация производства и менеджмент : учебное пособие / Е.П. Жаворонков, В.Н. Иванов. – Омск: Изд-во СибАДИ, 2006. – 216 с.
2.Операционный менеджмент : учебник для вузов / С.Э. Пивоваров и [др.]. –
СПб.: Питер, 2011. – 544 с.: ил.
3.Основы отраслевых технологий и организации производства : учебник /
Ю.М. Аносов и [др.]; Под ред. В.К. Федюкина. – 4-е изд., стер. – СПб.:
Политехника, 2010. – 312 с.: ил.
4.Фатхутдинов Р.А. Производственный менеджмент: учебник для вузов. 6-е
изд. – СПб.: Питер, 2011. – 496 с.: ил.
5.Организация производства на предприятии : учебник для технических и экономических специальностей / О.Г. Туровец и [др.]; Под ред. О.Г.
Туровец и Б.Ю. Сербиновского. – Ростов-н/Д.: Изд. центр МарТ, 2002. – 464 с.
6.Синица Л.М. Организация производства : учебник для студентов высш.
учеб. заведений по специальности «Экономика и управление на предприятии» / Л.М. Синица. – Минск: ИВЦ Минфина, 2008. – 540 с.
7.Новицкий Н.И. Организация и планирование производства : Практикум /
Н.И. Новицкий. – Мн.: Новое знание, 2004. – 256 с.
8.Организация производства и менеджмент на машиностроительных предприятиях. Сборник задач. Учебное пособие / Н.Ф. Ревенко и [др.];
Под ред. Н.Ф. Ревенко. – М.: Высш. шк., 2007. – 214 с.
9.Организация и планирование машиностроительного производства
(производственный менеджмент) : Учебник / К.А. Грачева и [др.]; Под ред. Ю.В. Скворцова, Л.А. Некрасова. – М.: Высш. шк., 2003. – 470 с.
73
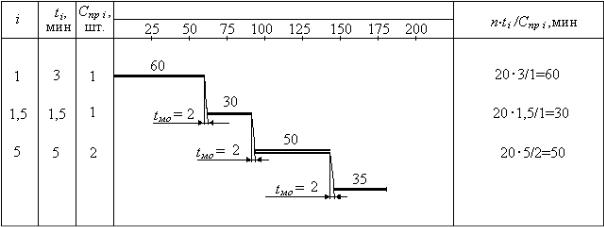
Приложение 7
Пример решения задачи по разделу «Организация простого производственного процесса во времени» [3]
Задача.
Определить длительность технологического и производственного циклов обработки партии деталей при разных видах движений, построить графики процесса обработки партии деталей при следующих исходных данных: величина партии деталей n = 20 шт.; величина транспортной партии р = 10 шт.; среднее межоперационное время tмо = 2 мин; режим работы – двухсменный; длительность рабочей смены tсм = 8 ч; длительность естественных процессов tе = 35 мин; технологический процесс обработки представлен в табл. 7.1.
Талица 7.1 – Технологический процесс обработки деталей
Номер |
Операция |
Количество единиц |
Норма времени, |
|
операции |
оборудования, шт. |
мин |
||
|
||||
1 |
Токарная |
1 |
3,00 |
|
2 |
Сверлильная |
1 |
1,50 |
|
3 |
Шлифовальная |
2 |
5,00 |
Решение.
1.Расчет длительности технологического цикла при последовательном виде движений предметов труда ведется по формуле (2.2)
Tтех |
3,00 |
|
1,50 |
|
5,00 |
|
|
||
20 |
|
|
|
|
|
|
|
140 мин. |
|
|
|
|
|||||||
Ц(посл) |
|
1 |
|
1 |
|
2 |
|
|
|
|
|
|
|
2.Расчет длительности производственного цикла при последовательном виде движений предметов труда ведется по формуле (2.5)
TЦпр(посл) 140 3 2 35 181 мин.
3.График длительности производственного цикла при последовательном виде движений предметов труда представлен на рис. 7.1.
Рис. 7.1 – График длительности производственного цикла при последовательном виде движений
74
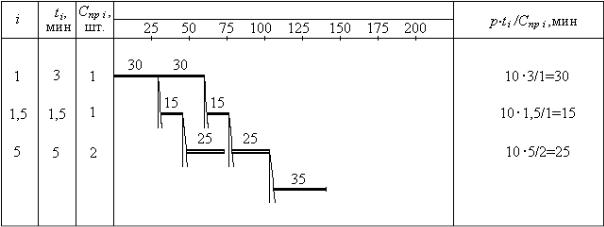
4.Расчет длительности технологического цикла при параллельном виде движений предметов труда ведется по формуле (2.3)
|
3,00 |
3,00 |
|
1,50 |
|
5,00 |
|
|
|||
Tтех |
20 10 |
|
10 |
|
|
|
|
|
|
|
100 мин. |
|
|
|
|
||||||||
Ц(пар) |
1 |
|
1 |
|
1 |
|
2 |
|
|
||
|
|
|
|
5.Расчет длительности производственного цикла при параллельном виде движений предметов труда ведется по формуле (2.6)
TЦпр(пар) 100 3 2 35 141 мин.
6.График длительности производственного цикла при параллельном виде движений предметов труда представлен на рис. 7.2.
Рис. 7.2 – График длительности производственного цикла при параллельном виде движений
7.Расчет длительности технологического цикла при параллельнопоследовательном движении предметов труда ведется по формуле (2.4)
Tтех |
3,00 |
|
1,50 |
|
5,00 |
1,50 |
|
1,50 |
|
|
|||||
20 |
|
|
|
|
|
|
|
(20 10) |
|
|
|
|
|
110 мин. |
|
|
|
|
|
|
|
|
|||||||||
Ц(пп) |
|
1 |
|
1 |
|
2 |
|
1 |
|
1 |
|
|
|||
|
|
|
|
|
8.Расчет длительности производственного цикла при параллельнопоследовательном движении предметов труда ведется по формуле (2.7)
TЦпр(пп) 110 3 2 35 151 мин.
9. График длительности производственного цикла при параллельнопроизводственном движении предметов труда представлен на рис. 7.3.
При построении графика длительности производственного цикла при параллельно-последовательном движении предметов труда необходимо соблюдать следующие правила:
а) если продолжительность последующей операции меньше продолжительности предыдущей, то перед последующей операцией создается запас заготовок, позволяющий выполнять эту операцию непрерывно;
б) если продолжительность последующей операции больше продолжительности предыдущей, то запас заготовок перед последующей операцией не создается, транспортная партия заготовок сразу передается на следующую операцию по завершении ее обработки.
75
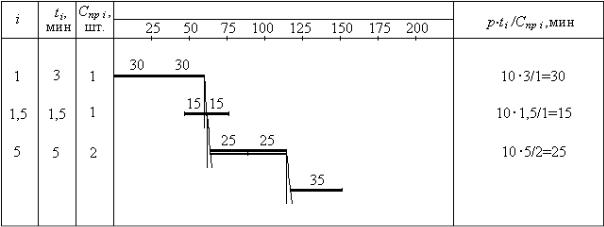
Рис. 7.3 – График длительности производственного цикла при параллельно-последовательном виде движений
76
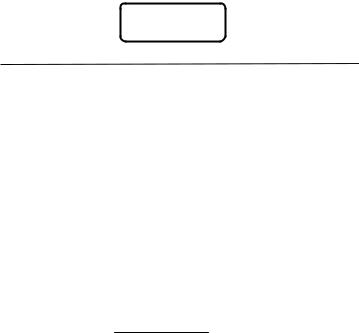
Приложение 8
Пример решения задачи по разделу «Организация процесса сборки (разборки) изделия» [3]
Задача.
На участке производится сборка изделия А. Технологический процесс сборки прибора представлен в табл. 8.1 (колонки 1-7). Месячная программа выпуска изделий составляет 700 шт. Количество рабочих дней в месяце – 21.
Режим работы сборочного участка – двухсменный. Продолжительность рабочей смены – 8 ч. Время на плановые ремонты и переналадку рабочих мест составляет 2%. Необходимо: построить веерную схему сборки изделия А; определить оптимальный размер партии изделий; установить удобопланируемый ритм; определить длительность операционного цикла партии изделий по сборочным единицам; рассчитать необходимое количество рабочих мест; построить цикловой график сборки изделия А; закрепить операции за рабочими местами исход из коэффициента их загрузки; построить цикловой график сборки изделия с учетом загрузки рабочих мест; рассчитать опережение запускавыпуска сборочных единиц изделия; определить длительность производственного цикла сборки партии изделий.
Решение
1. Построение веерной схемы сборки изделия А, представлено на рис. 8.1.
А17, 18, 19, 20
|
|
|
|
|
|
|
|
|
|
|
|
|
|
|
|
|
|
|
|
|
|
|
|
|
|
|
|
13,14,15,16 |
АА |
|
АБ |
|
|
|
АВ 6 |
|
|
||||
|
|
|
|
|
|
|
|
|
|
|
|
|
|
|
|
|
7, 8, 9, 10, 11, 12 |
|
|
|
|
|
|
|
|
||
|
|
|
|
|
|
|
|
|
|
|
|||
|
|
|
|
|
|
|
|
|
|
|
|
|
|
|
|
|
|
|
|
АВ1 |
|
|
|
|
АВ2 |
||
|
|
|
|
|
|
|
|
|
|
|
|
|
|
|
|
|
1, 2 |
|
3, 4, 5 |
|
Рис. 8.1 – Веерная схема сборки изделия А
2.Определение минимального размера партии изделий А осуществляется по формуле (2.8)
100 2 200
nmin 80шт.
3. Определение удобопланируемого размера партии изделий А осуществляется по формуле (2.10)
R |
|
|
21 80 |
2,4дня. |
p |
|
|||
|
700 |
|
Из удобопланируемых ритмов (21, 7, 3, 1) выбираем Rу = 3 дням.
77
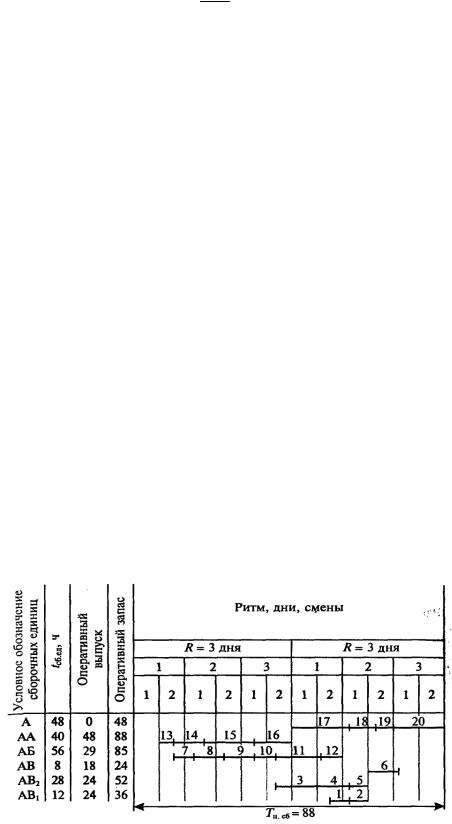
4. Определение оптимального размера партии изделий.
n 3 700 100шт.
o |
21 |
|
При этом выполняются все необходимые условия 80 100 700 – условие выполняется.
5.Определение длительности операционного цикла партии изделий по каждой i-й операции осуществляется по формуле (2.10).
Например, по первой операции длительность цикла составляет
tоп1 |
|
4,7 100 10 |
8ч. |
|
|||
|
60 |
|
По второй операции длительность операционного цикла составит соответственно
tоп2 |
|
2,3 100 10 |
4ч. |
|
|||
|
60 |
|
и т.д. по всем операциям. Результаты расчетов заносятся в табл. 8.1 в колонку 8.
6.Определение длительности операционного цикла партии изделий по сборочным единицам осуществляется по формуле (2.13).
Например, по сборочной единице АВ1 длительность цикла составляет
tс.ед 8 4 12ч. и т.д.
Результаты расчетов заносятся в колонку 9 (табл. 8.1).
7. Расчет необходимого количества рабочих мест ведут по формуле (2.14)
С |
|
|
192 |
4рабочих места. |
пр |
|
|||
|
|
3 2 8 |
8.Построение циклового графика сборки изделий А без учета загрузки рабочих мест. График строится на основании веерной схемы сборки (рис. 8.1) и длительности циклов сборки каждой i-й операции (табл. 8.1 колонки 8 и 9). Как правило, такой график строится в порядке, обратному ходу технологического процесса – начиная с последней операции (рис. 8.2).
Рис. 8.2 – Цикловой график сборки изделий без учета загрузки рабочих мест
78
Таблица 2.1 – Технологический процесс сборки изделия А
Условные |
Номер |
|
|
|
|
Подача |
Длительность |
Длительность |
|
обозначения |
ti, мин |
|
ti, мин |
tп.зi, |
сборочных |
операционного |
операционного цикла |
||
операции |
Кв |
||||||||
сборочных |
i |
|
|
|
мин |
единиц к |
цикла партии |
партии изделий по |
|
единиц |
|
|
|
|
операции, шт. |
изделий, ч |
сборочной единице, ч |
||
|
|
|
|
|
|||||
1 |
2 |
3 |
4 |
5 |
6 |
7 |
8 |
9 |
|
АВ1 |
1 |
5,0 |
1,06 |
4,7 |
10 |
6 |
8,0 |
12,0 |
|
2 |
2,5 |
1,09 |
2,3 |
10 |
6 |
4,0 |
|||
|
|
||||||||
АВ2 |
3 |
8,0 |
1,13 |
7,1 |
10 |
6 |
12,0 |
28,0 |
|
4 |
6,6 |
1,12 |
5,9 |
10 |
6 |
10,0 |
|||
|
5 |
4,0 |
1,14 |
3,5 |
10 |
6 |
6,0 |
|
|
АВ |
6 |
5,0 |
1,06 |
4,7 |
10 |
20 |
8,0 |
8,0 |
|
|
7 |
4,0 |
1,14 |
3,5 |
10 |
18 |
6,0 |
|
|
|
8 |
6,3 |
1,07 |
5,9 |
10 |
18 |
10,0 |
|
|
АБ |
9 |
7,0 |
1,07 |
6,5 |
10 |
18 |
11,0 |
56,0 |
|
10 |
3,1 |
1,03 |
2,9 |
10 |
18 |
5,0 |
|||
|
|
||||||||
|
11 |
10,0 |
1,05 |
9,5 |
10 |
18 |
16,0 |
|
|
|
12 |
5,0 |
1,06 |
4,7 |
10 |
18 |
8,0 |
|
|
|
13 |
2,5 |
1,09 |
2,3 |
10 |
17 |
4,0 |
|
|
АА |
14 |
5,0 |
1,06 |
4,7 |
10 |
17 |
8,0 |
40 |
|
15 |
10,4 |
1,09 |
9,5 |
10 |
17 |
16,0 |
|||
|
|
||||||||
|
16 |
8,0 |
1,12 |
7,1 |
10 |
17 |
12,0 |
|
|
|
17 |
12,0 |
1,06 |
11,3 |
10 |
– |
19,0 |
|
|
А |
18 |
5,0 |
1,06 |
4,7 |
10 |
– |
8,0 |
48 |
|
19 |
3,1 |
1,07 |
2,9 |
10 |
– |
5,0 |
|||
|
|
||||||||
|
20 |
10,0 |
1,05 |
9,5 |
10 |
– |
16,0 |
|
|
Итого |
– |
122,5 |
1,06 |
115,2 |
200 |
– |
192,0 |
192,0 |
Примечание. Оптимальный размер партии для всех сборочных единиц в результате расчета составляет 100 шт.
79
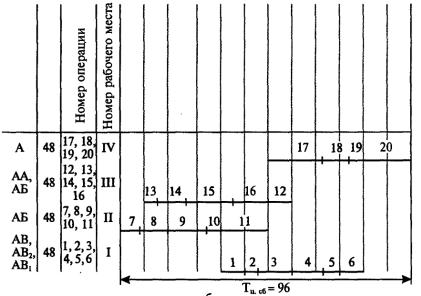
9.Закрепление операции за рабочими местами. Для достижения равномерности загрузки рабочих мест производится закрепление за ними определенных операций. Для этого на каждое рабочее место набирается объем работ, длительность операционного цикла которых была бы равна принятому ритму (пропускной способности рабочих мест) (см. табл. 8.2).
Таблица 2.2 – Закрепление операций за рабочими местами
Номер |
Номер |
Условные |
Суммарная |
Пропускная |
Коэффицие |
|
операции, |
обозначен |
длительност |
||||
способност |
нт загрузки |
|||||
рабочего |
закрепленной |
ия |
ь |
ь рабочего |
рабочего |
|
места |
за рабочим |
сборочны |
операционно |
|||
места, ч |
места |
|||||
|
местом |
х единиц |
го цикла, ч |
|
|
|
IV |
17, 18, 19, 20 |
А |
48 |
48 |
1,0 |
|
III |
12, 13, 14, 15, 16 |
АА, АБ |
48 |
48 |
1,0 |
|
II |
7, 8, 9, 10, 11 |
АБ |
48 |
48 |
1,0 |
|
I |
1, 2, 3, 4, 5, 6 |
АВ, АВ1, |
48 |
48 |
1,0 |
|
АВ2 |
||||||
|
|
|
|
|
10. Построение циклового графика сборки изделия А с учетом загрузки рабочих мест (стандарт-плана).
При построении графика с учетом загрузки рабочих мест необходимо стремиться к тому, чтобы длительность циклов отдельных операций графика (рис. 8.2) являлись проекциями на соответствующие рабочие места графика (рис. 8.3). В этом случае сохраняется длительность производственного цикла графика (рис. 8.2), построенного без учета загрузки рабочих мест. Но осуществить это удается не всегда. В нашем примере сдвинуты сроки начала выполнения операций 7, 8, 9, 10, 11, 12, 1, 2.
Рис. 8.3 – Цикловой график сборки изделия с учетом загрузки рабочих мест
80
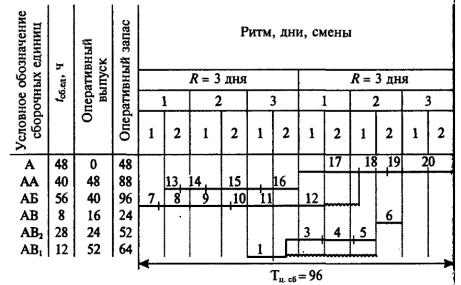
11.Построение уточненного циклового графика сборки изделия А. Уточненный график сборки изделия А (рис. 8.4) строится на основе графиков, представленных на рис. 8.2 и 8.3, показывающем действительную длительность производственного цикла сборки партии изделий. В рассматриваемой задаче длительность производственного цикла составляет 96 ч. Волнистые линии на рис. 8.4 показывают время смещения запуска соответственно сборочных единиц АБ и АВ1.
Рис. 8.4 – Уточненный цикловой график сборки изделий
12. Расчет опережения запуска-выпуска сборочных единиц изделия А ведется непосредственно на самих графиках в третьей и четвертых колонках рис. 8.2 и рис. 8.3. В связи с необходимостью смещения запуска сборочных единиц АБ и АВ1 на более ранние сроки на рис. 8.4 изменилось и опережение запускавыпуска этих сборочных единиц.
81
Приложение 9
Пример решения задачи по разделу «Организация ремонтного хозяйства» [3]
Задача. В механообрабатывающем цехе установлено 44 металлорежущих станка (см. приложение 14). Режим работы цеха двухсменный. Продолжительность смены 8 часов. Условия работы оборудования нормальные. Обрабатываются конструкционные стали, следовательно, коэффициенты, учитывающие тип производства, свойства обрабатывающего материала, условия эксплуатации, характеристику станков принимаются равными единице. Нормативное время работы станка в течение межремонтного цикла А=24000 ч. Структура межремонтного цикла для установленных станков имеет вид
К1 – О1 – Т1 – О2 – Т2 – О3 – С1 – О4 – Т3 – О5 – Т4 – О6 –
– С2 – О7 – Т5 – О8 – Т6 – О9 – К2.
Нормы времени для выполнения ремонтных работ представлены в табл. 9.1. Годовой эффективный фонд времени работы одного рабочего составляет 1835 ч. Нормы обслуживания на 1рбочего в смену по межремонтному обслуживанию составляют: Нобст 1650 рем. ед.; Нобсл 500 рем. ед.; Нобсм 1000 рем. ед.;
Нобш 3390 рем. ед.
Коэффициент, учитывающий расход материала на осмотровые и межремонтное облуживание (λ), равен 1,12. Норма расхода материала на один капитальный ремонт оборудования на одну ремонтную единицу составляет 14 кг конструкционной стали. Коэффициент, характеризующий соотношение нормы расхода материала при среднем и капитальных ремонтах (L), равен 0,6; коэффициент, характеризующий соотношение нормы расхода материала при текущем и капитальном ремонтах (В), равен 0,2.
Таблица 5.2 - Нормы времени на выполнение ремонтных работ на одну ремонтную единицу для технологического оборудования, н.-ч.
Виды работ |
|
Работы |
|
Всего |
|
слесарные |
станочные |
прочие |
|||
|
|
||||
Осмотр (О) |
0,75 |
0,10 |
– |
0,85 |
|
Ремонты: |
|
|
|
|
|
– текущий (Т) |
4,00 |
2,00 |
0,10 |
6,10 |
|
– средний (С) |
16,00 |
7,00 |
0,50 |
23,50 |
|
– капитальный (К) |
23,00 |
10,00 |
2,00 |
35,00 |
Ежегодно капитальному ремонту подвергается 10% оборудования, среднему ремонту – 25% и текущему ремонту – 100% оборудования.
Определить длительность межремонтного цикла, межремонтного и межосмотрового периодов, трудоемкость ремонтных и межремонтных работ, численность персонала по категориям для выполнения ремонтных работ и
82