
1168
.pdfИнструментальное хозяйство предприятия состоит из следующих подразделений:
1)инструментальный отдел – занимается определением потребности в инструменте, устанавливает нормы его износа, расхода
изапаса, составляет график производства инструмента, организует его ремонт, осуществляет технический надзор за его эксплуатацией и руководит всеми инструментальными службами;
2)инструментальный цех – осуществляет изготовление (при необходимости ремонт и восстановление) инструмента;
3)центральный инструментальный склад (ЦИС) – осуществляет прием, хранение, подготовку и выдачу инструмента в инструментально-раздаточные кладовые;
4)цеховые инструментально-раздаточные кладовые (ИРК) –
получают инструмент из ЦИСа, осуществляют его хранение, выдачу на рабочие места, в заточку и ремонт;
5)база восстановления инструмента – занимается сортировкой
ивосстановлением инструмента;
6)ремонтные отделения (базы, участки) в цехах;
7)заточные отделения в цехах.
Основными задачами инструментального хозяйства являются:
своевременное снабжение участков и рабочих мест необходимым инструментом;
своевременный ремонт, восстановление и заточка инструмента;
повышение качества инструмента и его рациональная эксплуатация;
снижение затрат на приобретение, изготовление, хранение и эксплуатацию инструмента.
Весь инструмент на предприятии классифицируется на определенные группы по следующим характерным признакам:
по назначению:
рабочий (осуществляется производственный процесс);
вспомогательный (связан с обслуживанием рабочих мест);
измерительный (служит для определения свойств и размеров продукции);
приспособления – устройства для закрепления продукции на рабочем месте;
по характеру использования:
специальный (используется на конкретной операции только для определенных изделий);
43
нормальный (для определенных работ независимо от вида изделий (обычно изготавливается на специальных заводах);
по виду обработки (операции):
литейный, кузнечный, станочный (механическая обработка), сборочный и т. п.;
по виду оборудования, на котором применяется инструмент:
токарный, сверлильный, фрезерный и т.д.;
по десятичной системе:
весь инструмент разбирается на 10 групп, группа – на 10 подгрупп, подгруппа – на 10 видов, каждый вид – на 10
разновидностей и т.д. При этом первая цифра обозначает класс инструмента, вторая – подкласс, третья – группу и т.д.
Индексация состоит в присвоении каждому типоразмеру инструмента условного обозначения – шифра, образуемого по специальной системе, соответствующей принятой классификации [4].
В представленном разделе приводятся расчетные формулы по расходу и потребности инструмента, по установлению норм запаса инструмента в местах его хранения [3].
Расход режущего инструмента определенного типоразмера Кр (шт.) рассчитывают по формуле
КР |
N tM |
nH |
, |
(2.38) |
60 T |
|
|||
|
(1 R) |
|
||
|
ИЗН |
|
|
|
где N – число деталей, обрабатываемых данным инструментом по годовой программе, шт.; tM – машинное время на 1 деталеоперацию, мин; nH – число инструментов, одновременно работающих на станке, шт.; TИЗН – машинное время работы инструмента до полного износа, ч; R – коэффициент преждевременного износа инструмента (принимается R = 0,05).
Машинное время работы инструмента до полного износа определяют по формуле
L |
|
tCT |
|
(2.39) |
||
TИЗН |
|
1 |
, |
|||
l |
||||||
|
|
|
|
|
где L – допустимая величина стачивания рабочей части инструмента при заточках, мм; l – средняя величина снимаемого слоя при каждой заточке, мм; tСТ – стойкость инструмента, машинное время его работы между двумя переточками, ч.
44
Расход инструмента может быть установлен на основе нормы расхода на какую-либо расчетную единицу (например, на 1000 деталей) и определяется по формуле
КР |
N Hp |
, |
(2.40) |
|
|||
|
np |
|
где Нр – норма расхода инструмента на расчетную единицу; np – число деталей, принятое за расчетную единицу, шт.
В единичном и мелкосерийном производствах расход инструмента может быть определен по формуле
KР |
FЭ KМ КУЦ |
, |
(2.41) |
|
|||
|
TИЗН (1 R) |
|
где KM – коэффициент машинного времени; KУЦ – коэффициент участия данного инструмента в обработке деталей.
Потребность в мерительном инструменте (шт.) рассчитывают по формуле
КМ.И |
N aE nB.H |
, |
(2.42) |
|
|||
|
nПР.И (1 R) |
|
где aE – число измерений на одну деталь; nB.H – выборочность контроля, дес. долей; nПР.И – количество измерений, выдерживаемых данным инструментом до полного износа.
Для калибров и скоб норму износа определяют по формуле
nПР.И V ag B ap , |
(2.43) |
где V – коэффициент допустимого средневероятного износа мерителя, V 0,7; ag – величина допустимого износа мерителя по ГОСТу, мкм; B – норма стойкости мерителя (число измерений на 1 мкм износа мерителя); ap – допустимое число ремонтов мерителя до полного износа.
Величину потребности матриц штампа определяют по формуле
|
КШ |
|
N |
, |
|
|
(2.44) |
||
|
|
|
|
||||||
|
|
|
|
nШ |
|
|
|
|
|
nШ |
L |
|
|
U k |
|
|
(2.45) |
||
|
|
1 |
Ш |
, |
|||||
|
|||||||||
|
l |
|
|
|
|
|
|
|
где nШ – норма износа матрицы штампа; L – величина допустимого стачивания матрицы, мм; l – средний слой металла, снимаемого при переточке, мм; U – число ударов между двумя переточками; kШ – коэффициент, учитывающий снижение стойкости штампа после переточки.
45
Размер цехового оборотного фонда инструмента ZЦ определяют по формуле
ZЦ ZP.M ZР.З ZK , |
(2.46) |
где ZP.M – количество инструментов, находящихся на рабочих местах, шт.; ZP.З – количество режущих инструментов, находящихся в заточке и на восстановлении, шт.; ZК – количество режущих инструментов, находящихся в инструментально-раздаточных кладовых, шт.;
Количество инструментов на рабочих местах при их периодической подаче определяют по формуле
ZР.М |
ТМ |
СПР |
|
nН |
|
CПР |
|
, |
(2.47) |
|
|
|
1 kЗ |
|
|
ТС
где ТМ – период между подачами инструмента к рабочим местам, ч; ТС
– период между сменами инструмента на станке, ч; nH – число инструментов, одновременно применяемых на одном рабочем месте; kЗ – коэффициент резервного запаса инструмента на каждом рабочем месте (как правило, kЗ = 1, а на многорезцовых станках kЗ =2 - 4).
Периодичность смены инструмента определяют по формуле
|
ТС tШТ tСП , |
|
(2.48) |
||
|
|
tМ |
|
|
|
где tШТ – штучное время на операцию, мин. |
в |
заточке, |
|||
Количество |
инструментов, |
находящихся |
|||
рассчитывают по формуле |
|
|
|
||
|
ZР.З |
ТЗ |
СПР nН , |
|
(2.49) |
|
|
|
|||
|
ТМ |
|
|
|
где ТЗ – время от поступления инструмента с рабочего места в инструментально-раздаточную кладовую до возвращения его из заточки, ч (для простого инструмента ТЗ = 8 ч, а для сложного – 16 ч).
Количество режущих инструментов, находящихся в запасе в инструментально-раздаточной кладовой, определяют по формуле
ZК QР tH 1 kЗ , |
(2.50) |
где QP – среднесуточный расход инструментов за период между очередными поступлениями их из центрального инструментального
склада, шт., QP |
|
kP |
; kЗ – коэффициент резервного (страхового) |
|
|||
|
360 |
|
запаса инструмента в инструментально-раздаточной кладовой (принимается kЗ = 0,1); tH – период между поставками инструмента из центрального инструментального склада в инструментально-
46
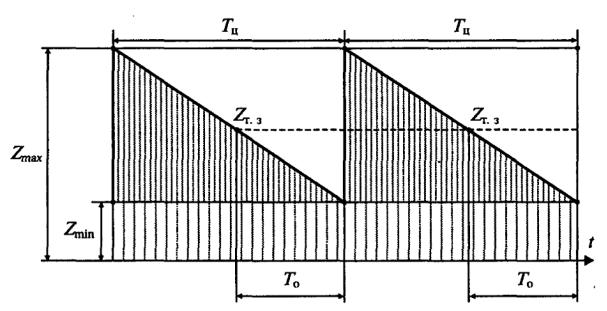
раздаточную кладовую цеха (как правило, поставки производят два раза в месяц, т.е. tH = 15 дней).
Норма запаса инструментов на центральном инструментальном складе устанавливается в соответствии с системой «минимуммаксимум» (рис. 2.3).
По этой системе создаются три нормы запаса:
1) минимальная норма запаса Zmin создается по фактическим данным в зависимости от величины расхода инструмента на случай задержки исполнения заказа на изготовление инструмента или перерасхода его цехами:
Zmin ZСТР ; |
(2.51) |
2) норма запаса, соответствующая точке, при достижении которой выдается заказ на изготовление или приобретение очередной партии инструмента:
ZТ.З Zmin TO QP, |
(2.52) |
где TO – период времени между моментом выдачи заказа и поступлением инструмента на центральный инструментальный склад, дней; QP – среднедневной расход инструмента за период исполнения заказа;
3) максимальная норма запаса Zmax достигается в момент поступления заказа инструмента:
Zmax Zmin TЦ QР, |
(2.53) |
где TЦ – время между двумя поступлениями партии инструмента (длительность цикла), дни.
47
Рис. 2.3 – График изменения запаса инструментов на центральном инструментальном складе по системе «минимум-максимум»
Пример типовой задачи с пошаговым ее решением по разделу «Организация инструментального хозяйства» представлен в приложении 11.
2.5.4.Организация транспортного хозяйства
Впроцессе производства на предприятиях регулярно перемещаются огромные массы сырья, материалов, полуфабрикатов, топлива, инструментов и т.п. Доставка грузов на предприятия, их последующее перемещение, а также вывоз готовой продукции и отходов производства осуществляются промышленным транспортом. От его работы зависят ритмичная работа рабочих мест, участков, цехов и равномерный выпуск предприятием готовой продукции. Время, затрачиваемое на внутри- и межцеховые перевозки, непосредственно влияет на длительность производственного цикла.
Транспортное хозяйство – комплекс технических средств промышленного предприятия, предназначенных для перевозки материалов, полуфабрикатов, готовой продукции, отходов и других грузов на территории предприятия и на его подъездных путях. Транспортное хозяйство предприятия состоит из:
1) транспортных средств; 2) устройств общезаводского назначения – депо, гаражи, ремонтные
мастерские, рельсовые и безрельсовые пути и т.п.
Восновные функции транспортного хозяйства предприятия входят:
перевозка грузов, погрузочно-разгрузочные и экспедиционные операции.
Основными задачами транспортного хозяйства являются:
1) своевременное и бесперебойное обслуживание производства необходимым транспортом; 2) правильный выбор и наиболее эффективное использование транспортной техники;
3) механизация и автоматизация транспортных операций;
4)снижение затрат, связанных с перевозкой грузов.
Затраты на содержание транспортного хозяйства и транспортировку грузов на некоторых предприятиях составляют 20-30 % от суммы всех косвенных расходов в себестоимости продукции.
48
Транспорт промышленных предприятий классифицируется по назначению и месту действия, видам, способам действия и другим признакам. По назначению и месту действия он подразделяется на внешний, меж- и внутрицеховой. В последней группе выделяется межоперационный транспорт. Внешний транспорт доставляет сырье, материалы, топливо, покупные изделия и другие предметы материально-технического обеспечения на групповые или прицеховые склады предприятия.
С помощью межцехового транспорта производится транспортировка сырья, материалов и других грузов с общезаводских складов в заготовительные цехи предприятия; готовой продукции – из сборочных цехов в цехи готовой продукции, а также деталей и сборочных единиц между цехами предприятия.
Внутрицеховой транспорт перемещает заготовки, детали, узлы в процессе изготовления между рабочими местами и участками внутри цеха. Внутрицеховые транспортные операции в большинстве случаев являются составной частью производственного процесса.
По видам транспортные средства подразделяются на железнодорожные (рельсовые), безрельсовые и механические. В качестве внутризаводского железнодорожный транспорт применяется лишь на предприятиях тяжелого машиностроения, где большие габариты изделий. К безрельсовому транспорту относятся тягачи, тракторы, автомобили, тележки. Он применяется для меж- и внутрицеховых перевозок.
Механический транспорт в основном служит для внутризаводских и межоперационных перевозок. Это подвесные пути, лифты, элеваторы, конвейеры, рольганги.
По способу действия различают транспортные средства непрерывного (конвейерные системы, транспортеры всех видов) и прерывного или периодического (автомашины, электрокары, мостовые краны и т.п.) действия.
По направлению движения группируют транспортные средства для горизонтального, вертикального (лифты, элеваторы и т. п.) и смешанного перемещения грузов (краны и т.п.).
Транспортные средства классифицируются и по уровню механизации и автоматизации (автоматические, механизированные, ручные).
В гибких автоматизированных производствах применяются автоматизированные и автоматические транспортно-накопительные системы (АТНС), которые могут быть разных уровней: межцеховыми,
49
цеховыми и локальными, обслуживающими отдельные производственные модули. К основному оборудованию, используемому для комплектации этих систем, относятся автоматические стеллажи и мостовые краны-штабелеры, транспортные и перегрузочные устройства, перегрузочные и ориентирующие устройства, питатели, накопители, автоматические склады, транспортно-складская тара.
При организации перевозок грузов большое значение имеет системный подход, требующий рассмотрения всей системы транспортных связей, от которых зависит перемещение и хранение грузов.
Погрузочно-разгрузочные, транспортные и складские (ПРТС) работы включают комплекс операций перемещения, связанных с погрузкой, разгрузкой, транспортировкой и хранением различных грузов.
Операциями перемещения считают все операции, при которых изменяется положение груза в пространстве, но при этом не изменяются его физические свойства. Если операции связаны с изменением вида транспортной тары, то такие операции также относят к операциям перемещения (например, укладка грузов на поддон, в контейнер и др.).
Операции перемещения различают по видам: погрузочные – грузы захватывают с места и укладывают на транспортные средства;
разгрузочные – грузы захватывают с транспортных средств и укладывают на место хранения; перевалочные – грузы захватывают с одних транспортных средств и укладывают на другие;
транспортные – выполняют только перемещение груза от места погрузки до места разгрузки.
ПРТС работы считаются механизированными, если основные операции перемещения выполняются с помощью машин (рабочие только управляют машинами), а вспомогательные операции (открытие и закрытие дверей, зачистка вагонов, строповка и т.п.) – вручную. Комплексно-механизированными ПРТС работами считаются те операции (основные и вспомогательные), которые выполняют машины. Рабочие заняты только на управлении машинами и на их обслуживании.
Автоматизированными ПРТС работами считаются те, выполнение которых осуществляет комплекс подъемно-транспортных машин и
50
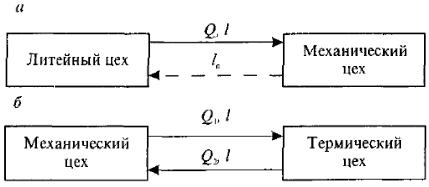
устройств, имеющий централизованное управление с диспетчерского пульта или работающий по заданной программе. Рабочие заняты только обслуживанием подъемно-транспортных машин и средств дистанционного и автоматического управления.
Для механизации меж- и внутрицехового транспорта широко применяются различные конвейерные устройства.
Перевозка грузов может производиться по разовым и постоянным маршрутам. Разовые маршруты случайны как по направлениям, так и по количеству транспортируемого груза. Они вводятся для выполнения неповторяющихся отдельных заявок, как правило, в условиях единичного и мелкосерийного производства.
Постоянные маршруты проходят по заранее установленным направлениям и выбираются с учетом грузопотока и применяемых транспортных средств. Они характерны для выполнения систематически повторяющихся заявок в крупносерийном и массовом производстве [4] Различают три системы маршрутных перевозок: маятниковую,
веерную и кольцевую. При маятниковой системе перевозки
транспортное средство осуществляет перевозку грузов между двумя определенными пунктами. Маршрут может быть односторонним, когда транспортное средство в одну сторону движется с грузом, а в другую – без груза (порожним) (рис. 2.4, а) и двусторонним, когда грузы транспортируются в обоих направлениях. В этом случае транспортные средства используются на 80-95% при отсутствии холостых пробегов (рис. 2.4, б).
Рис. 2.4 – Схемы одно- (а) и двустороннего (б) маятникового маршрута [4]: Q – объем перевезенного груза (грузопоток); l – груженный пробег, м; lп - порожний пробег.
51
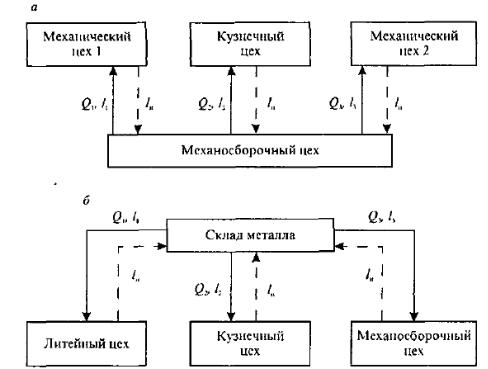
При веерной системе перевозка грузов осуществляется из нескольких пунктов в один или из одного пункта в несколько других и представлена на рис. 2.5.
Кольцевая система перевозки используется при обслуживании ряда грузовых пунктов, связанных путем последовательной передачи грузов от одного пункта к другому. Кольцевые маршруты могут быть с равномерным, нарастающим и уменьшающимся грузопотоком и представлены на рис. 2.6.
Рис. 2.5 – Схемы веерных маршрутов [4]:
а – с единым пунктом назначения; б – с единым пунктом отправления.
Разновидностью кольцевой системы перевозки грузов является система цикловых маршрутов. Применение системы цикловых маршрутов целесообразно на крупных предприятиях с большим числом цехов, расположенных на обширных территориях. Эта система представляет собой совокупность нескольких замкнутых кольцевых систем, связанных между собой специальным кольцевым маршрутом, на котором имеются площади для передачи грузов с одного кольца на другое, без перевалки грузов.
Кольцевые маршруты имеют ряд преимуществ перед другими видами межцеховых перевозок. Они сокращают порожние пробеги, повышают производительность труда, сокращают потребность в транспортных средствах. Однако для их внедрения требуется большая
52