
1168
.pdfтранспортные партии по n штук в каждой. Транспортная партия обрабатывается или собирается на каждой партии без перерывов. Ее можно подавать на следующую операцию, не ожидая окончания работы по другим транспортным партиям. При этом должно соблюдаться условие непрерывной работы на каждой операции при изготовлении всей партии.
Еще большее сокращение технологического цикла можно получить при использовании параллельного вида движения партий предметов труда по операциям, сущность которого заключается в том, что с операции на операцию предметы труда передаются транспортными партиями, при этом по каждой партии ведется работа на всех операциях технологического процесса без перерывов, т.е. без пролеживания.
Аналитические зависимости данного раздела соответствуют данным источника [1].
Длительность операционного цикла партии деталей на i-й операции определяется по формуле
tn |
|
n ti |
, |
(2.1) |
|
||||
|
|
Cпрi |
|
где n – количество деталей в партии, на i-й операции, мин; Спрi – принятое операции, шт.
шт.; ti – норма штучного времени число рабочих мест на i-й
Длительность технологического цикла при последовательном виде движений предметов труда определяется по формуле
m |
t |
i |
|
|
TЦтех(посл) n |
|
, |
(2.2) |
|
|
|
|||
i 1 |
Спрi |
|
где m – число операций в технологическом процессе.
Длительность технологического цикла при параллельном движении предметов труда
TЦтех(пар) (n p) |
ti max |
m |
t |
i |
|
|
|
p |
|
, |
(2.3) |
||
Спр i |
|
|
||||
|
i 1 |
Спр i |
|
где ti max – норма времени максимальной по продолжительности операции с учетом числа рабочих мест, мин; p – размер транспортной партии, шт.
23
Длительность технологического цикла при параллельнопоследовательном движении предметов труда определяют по формуле
m |
t |
i |
m 1 |
tk i |
|
|
|
TЦтех(пп) n |
|
(n p) |
|
, |
(2.4) |
||
Спр i |
Спр i |
||||||
i 1 |
i 1 |
|
|
где tk i – наименьшая норма времени между i-й парой смежных операций с учетом количества единиц оборудования, мин.
Длительность производственного цикла обработки деталей всегда больше технологического цикла на величину времени, затрачиваемого на транспортные и контрольные операции, естественные процессы, межоперационные перерывы и перерывы, регламентированные режимом работы.
На практике, как правило, учитываются только три основные составляющие длительности производственного цикла: длительность технологического цикла (ТЦ), длительность естественных процессов (tе) и время межоперационного пролеживания (tмо).
Длительность производственного цикла при последовательном движении предметов труда определяют по формуле
TЦпр(посл) TЦтех(посл) m tмо tе. |
(2.5) |
Длительность производственного цикла при параллельном движении предметов труда определяют по формуле
TЦпр(пар) TЦтех(пар) m tмо tе. |
(2.6) |
Длительность производственного цикла при параллельнопоследовательном движении предметов труда определяют по формуле
Tпр |
Tтех |
m t |
мо |
t |
е |
. |
(2.7) |
Ц(пп) |
Ц(пп) |
|
|
|
|
После вышеприведенных расчетов строят графики длительности производственного цикла при последовательном, параллельном и параллельно-последовательном движениях предметов труда.
При построении графика длительности производственного цикла при параллельно-последовательном движении предметов труда необходимо соблюдать следующие правила:
а) если продолжительность последующей операции меньше продолжительности предыдущей, то перед последующей операцией
24
создается запас заготовок, позволяющий выполнять эту операцию непрерывно;
б) если продолжительность последующей операции больше продолжительности предыдущей, то запас заготовок перед последующей операцией не создается, транспортная партия заготовок сразу передается на следующую операцию по завершении ее обработки.
Пример расчета длительности технологического процесса обработки деталей и построение графиков для различных видов движения предметов труда представлены в приложении 7.
2.4. Организация процесса сборки (разборки) изделия
Производственный цикл сложного процесса – общая продолжительность комплекса координированных во времени простых процессов изготовления и сборки изделия, входящих в сложный процесс изготовления изделия или их партии.
Цель координации процессов, составляющих сложный процесс, - обеспечение комплектности и бесперебойности хода производства при полной загрузке оборудования и рабочих мест, т.е. обеспечение подачи на сборку в точно установленное время всех необходимых деталей и узлов машины с таким расчетом, чтобы сборка партии осуществлялась бесперебойно. Поэтому для определения длительности производственного цикла сложного процесса необходимо по данным схемам сборки изделия построить цикловой график, т.е. линейную схему сборки, выполненной в масштабе календарного времени [3].
Аналитические зависимости данного и следующего разделов соответствуют данным источника [1].
Первоначально составляют схему сборки изделия с указанием номеров сборочных операций. Пример такой схемы приведен на рис. 2.2.
Минимальный размер партии собираемых (разбираемых) изделий определяют по формуле
|
|
|
m |
|
|
|
|
|
|
(100 aоб ) tпзi |
|
(2.8) |
|
n |
min |
|
i 1 |
, |
||
m |
||||||
|
|
|
|
aоб tопi i 1
25
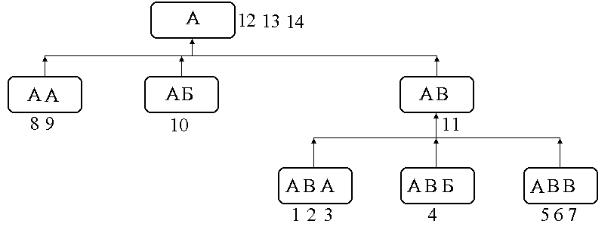
где tпз i – подготовительно-заключительное время на i-й операции сборки (разборки), мин; aоб – допустимые потери рабочего времени на переналадку и ремонт рабочих мест, %; tоп i – продолжительность выполнения i-й сборочной операции, которая определяется по формуле
t |
опi |
|
tk |
|
, |
(2.9) |
P K |
|
|||||
|
|
в |
|
|||
|
|
|
сб |
|
здесь tk – трудоемкость выполнения операции, нормо-ч; Pсб – количество рабочих, одновременно занятых выполнением одной операции; Kв – коэффициент выполнения норм времени.
Рис. 2.2 – Схема сборки (разборки) изделия
Период чередований партий изделий (ритм) определяют по формуле
Rp |
|
D nmin |
, |
(2.10) |
|
||||
|
|
NM |
|
где D – число рабочих дней в месяце; NM – месячная программа изготовления изделий, шт.
Оптимальный размер партии изделий
nО |
|
Ry NM |
, |
(2.11) |
|
||||
|
|
D |
|
где Ry – удобопланируемый ритм (выбирается кратным количеству рабочих дней, при этом он должен быть как можно ближе по своему значению к периоду чередований партий Rp, например – если в месяце 21 рабочий день, а Rp=2,5, то в качестве Ry выбирается ближайших из ритмов 21, 7, 3, 1).
При этом должны выполнятся следующие условия:
1)месячная программа кратна оптимальному размеру партии;
26
2) оптимальный размер партии изделий должен удовлетворять требованию
nmin nн NM .
Длительность операционного цикла партии изделий на i-й операции, мин, определяется по формуле
tоп ti' nн tпз i , |
(2.12) |
где ti' – норма штучного времени на i-й операции с учетом коэффициента выполнения норм, мин.
Длительность операционного цикла по партии сборочных единиц определяют по формуле
K |
|
tс ед tпсi , |
(2.13) |
i 1 |
|
где K – число операций, входящих в сборочную единицу.
Число рабочих мест для сборки изделий
|
|
m |
|
|
|
|
tпс i |
|
|
Спр |
|
i 1 |
. |
(2.14) |
|
||||
|
|
Ry |
|
Результаты расчетов помещают в сводную таблицу технологического процесса сборки изделия. После этого закрепляют операции за рабочими местами и строят цикловой график сборки изделия с учетом загрузки рабочих мест (стандарт-плана). Цикловой график сборки может быть выполнен согласно табл. 2.1.
Таблица 2.1 – Цикловой график сборки изделия
Условное |
|
Опережение, |
|
|
|
|
|
Ритм, дни, смены |
|
|
||||||||||
обозначение |
tс ед, |
|
ч |
|
|
R=3 дня |
|
|
R=3 дня |
|
|
|||||||||
сборочной |
ч |
выпу |
|
запус |
1 |
|
2 |
|
3 |
1 |
|
2 |
|
3 |
||||||
единицы |
|
ска |
|
ка |
1 |
2 |
|
1 |
2 |
|
1 |
2 |
1 |
|
2 |
1 |
2 |
|
1 |
2 |
|
|
|
|
|
|
|
|
|
|
|
|
|
|
|
|
|
|
|
|
|
|
|
|
|
|
|
|
|
|
|
|
|
|
|
|
|
|
|
|
|
|
|
|
|
|
|
|
|
|
|
|
|
|
|
|
|
|
|
|
|
|
|
По графику производится расчет опережения запуска-выпуска сборочных единиц.
В приложении 8 рассмотрен пример типовой задачи с пошаговым решением.
27
2.5. Организация вспомогательных хозяйств
При выполнении данного, раздела студент должен самостоятельно определиться, какие из вспомогательных хозяйств, необходимы для организации производства выбранного им изделия. Свой выбор необходимо обосновать в письменной форме.
Работы по техническому обслуживанию производства на предприятиях выполняются вспомогательными цехами и обслуживающими хозяйствами производственного назначения.
Среди них наиболее важное значение имеют ремонтное, энергетическое, инструментальное, транспортное и складское хозяйства. Организация работы этих хозяйств непосредственно влияет на показатели производственно-хозяйственной деятельности предприятия, качество выпускаемой продукции.
2.5.1.Организация ремонтного хозяйства
Впроцессе эксплуатации машины и оборудования подвергаются физическому и моральному износу: теряется работоспособность, точность. Их прежние качества восстанавливаются путем ремонта, под которым понимается возобновление в первоначальной натуральной форме отдельных частей и деталей машин, износившихся в процессе работы предприятия.
Ремонтное хозяйство – это совокупность общезаводских и цеховых подразделений, осуществляющих комплекс мероприятий по ремонту, уходу и надзору за состоянием оборудования, в результате чего решаются следующие задачи:
1) обеспечивается постоянная рабочая готовность всего оборудования; 2) удлиняется межремонтный срок оборудования;
3) повышается производительность труда ремонтных рабочих и снижаются затраты на ремонт.
Практика показывает, что затраты на ремонт и обслуживание оборудования постоянно увеличиваются, растут мощности ремонтных служб и численность ремонтных рабочих. Эти обстоятельства выдвигают задачи организации ремонта оборудования в ряд наиболее актуальных проблем.
28
Ремонтное хозяйство возглавляется главным механиком предприятия,
вфункции которого входят:
паспортизация и аттестация оборудования;
разработка технологических процессов ремонта и их оснащения;
планирование и выполнение работ по техническому обслуживанию и ремонту оборудования;
модернизация оборудования;
совершенствование организации труда работающих, занятых в
этой службе.
Различают три формы организации ремонта: централизованную, децентрализованную и смешанную.
При централизованной форме все виды ремонта и технического обслуживания производит ремонтно-механический цех предприятия.
При децентрализованной форме ремонт и техническое обслуживание оборудования производится силами цеховых ремонтных баз. Здесь же изготавливают новые и восстанавливают изношенные детали и узлы.
При смешанной форме организации ремонта трудоемкие работы, такие, как капитальный ремонт и модернизация оборудования, изготовление запасных частей и восстановление изношенных деталей
иузлов, производятся в ремонтно-механическом цехе предприятия, а техническое обслуживание и текущий ремонт оборудования осуществляется в цеховых ремонтных базах. Такой ремонт и обслуживание обычно выполняется комплексными бригадами слесарей, закрепленных за отдельными участками.
В практике работы предприятий чаще всего применяются три метода организации ремонта.
1. Ремонт по потребности, т.е. по мере остановки станка. Это может вызвать срыв выполнения планового задания, брак продукции
ит.д. Увеличиваются время и затраты на ремонт оборудования в связи с износом сопряженных деталей. При этом методе работу ремонтно-механического цеха невозможно планировать.
2. Метод по дефектным ведомостям, выполняется осмотр оборудования и составляется дефектная ведомость, в которой отражается, что и когда надо ремонтировать. Заранее служба главного механика здесь также не может планировать ремонтные работы.
3. Третий метод организации ремонтного хозяйства базируется на системах планово-предупредительного ремонта (ППР) и технического обслуживания и ремонта (ТОР). Они представляют
29
собой совокупность организационно-технических мероприятий по уходу, надзору, обслуживанию и ремонту оборудования, по заранее составленному плану. В основе этих систем лежат принципы плановости и профилактики. Цель этого метода – предупредить остановку оборудования из-за возможных отказов и аварий.
Эти системы включают в себя:
1)уход за оборудованием основными рабочими в начале и в конце смены, что повышает их ответственность за состояние оборудования. Кроме того, за состоянием оборудования повседневно наблюдают дежурные слесари, электрики, смазчики, устраняющие возникшие мелкие неисправности;
2)техническое обслуживание, включающее комплекс операций по поддержанию работоспособности оборудования: осмотры выполняются дежурными слесарями 1-2 раза в месяц, промывки, проверки на точность, последние производятся наладчиком или слесарем совместно с представителем отдела технического контроля;
3)ремонты. Система ППР включает три вида ремонта: малый (М), средний (С) и капитальный (К). В основном она применяется для устаревшего оборудования. Для нового, дорогостоящего оборудования рекомендуется система ТОР, включающая два вида ремонта: текущий (Т) и капитальный (К). Основной же упор в ней сделан на техническое обслуживание оборудования.
Текущий и малый ремонты – это минимальные по объему ремонты, при которых заменяются и восстанавливаются отдельные части (детали, узлы) оборудования, выполняется регулировка его механизмов. Проводятся они на месте и в процессе эксплуатации оборудования в нерабочее время. Цель таких ремонтов – обеспечить работоспособность оборудования до очередного планового ремонта. При среднем ремонте производится частичная разборка агрегата изношенных деталей и узлов. По своему объему он занимает промежуточное положение между малым и капитальным ремонтами. При системе ТОР он не производится.
Капитальный ремонт – это наибольший по объему и сложности вид ремонта. При нем полностью разбирается оборудование, заменяются все изношенные детали и узлы, производится регулировка механизмов для восстановления полного или близко к полному ресурса. Обычно он сопровождается модернизацией оборудования.
Под модернизацией оборудования понимается внесение в конструкцию машин изменений с целью частичной ликвидации
30
последствий морального износа. Типовые проекты модернизации оборудования разрабатываются в централизованном порядке предприятиями, изготавливающими данное оборудование. Проекты частичной модернизации могут разрабатываться силами машиностроительных предприятий, эксплуатирующих соответствующее оборудование.
Выбор формы обновления оборудования производится путем составления капитальных вложений, себестоимости продукции и производительности оборудования по вариантам: капитальный ремонт, модернизация, новое оборудование.
При системах ППР и ТОР объемы и содержание работ планируются и строго соблюдаются независимо от фактического состояния оборудования. Эти системы базируются на точно установленных нормативах.
Нормативы системы ППР. К нормативам системы ППР относятся: длительность ремонтного цикла и его структура, продолжительность межремонтного и межосмотрового периодов, категория сложности ремонта и ремонтная единица, нормы затрат рабочего времени, материалов и простоев оборудования в ремонте. Все нормативы дифференцированы по группам оборудования.
Ремонтный цикл – это промежуток времени от ввода оборудования в эксплуатацию до капитального ремонта или между двумя капитальными ремонтами. Он измеряется оперативным временем работы оборудования. Время простоя в ремонте в цикл не включается.
Структура межремонтного цикла, т.е. перечень последовательных работ по ремонту и техническому обслуживанию оборудования, приведена в табл. 2.2.
Таблица 2.2 – Структура ремонтного цикла [4]
Оборудование |
|
Количество |
|
Структура ремонтного |
|
ремонтов |
|
|
|||
|
осмотров |
цикла |
|||
|
средних |
малых |
|
||
1 |
2 |
3 |
|
4 |
5 |
Легкие и средние |
|
|
|
|
|
станки массой до |
|
|
|
|
|
10 т со сроком |
|
|
|
|
|
службы: |
|
|
|
|
|
свыше 10 лет |
2 |
6 |
|
9 |
К-О3-М1-О2-М2-О3-С1-О4- |
|
|
|
|
|
М3-О5-М4-О6-С2-О7-М5- |
|
|
|
|
|
О1-М6-О9-К |
31
|
|
|
|
Окончание табл. 2.2 |
1 |
2 |
3 |
4 |
5 |
до 10 лет |
1 |
4 |
6 |
К-О-М-О-М-О-С-О-М-О- |
|
|
|
|
М-О-К |
Крупные и |
2 |
6 |
27 |
К-О-О-О-М-О-О-О-М-О- |
тяжелые станки |
|
|
|
О-О-С-О-О-О-М-О-О-О- |
массой 10-100 т |
|
|
|
М-О-О-О-С-О-О-О-М-О- |
|
|
|
|
О-О-М-О-О-О-К |
Особо тяжелые |
2 |
9 |
36 |
К-О-О-О-М-О-О-О-М-О- |
металлорежущие |
|
|
|
О-О-М-О-О-О-С-О-О-О- |
станки массой |
|
|
|
М-О-О-О-М-О-О-О-М-О- |
свыше 100 т и |
|
|
|
О-О-С-О-О-О-М-О-О-О- |
уникальные |
|
|
|
М-О-О-О-М-О-О-О-К |
Примечание: К – капитальный, С – средний, М – малый ремонт, О – осмотр.
Для оценки сложности ремонта оборудования, его ремонтных особенностей введена категория сложности ремонта R, которая определяется по техническим характеристикам оборудования на основе расчетных формул. В каждой группе оборудования один из агрегатов принят за эталон, которому по системе ППР (ТОР) установлена категория сложности ремонта.
Для планирования и расчетов объема ремонтных работ вводится понятие «ремонтная единица» – r (р.е.), т.е. показатель, характеризующий нормативные затраты на ремонт оборудования первой категории сложности. Таким образом, категория сложности ремонта R показывает, во сколько раз трудоемкость ремонта данной модели оборудования превышает трудоемкость ремонтной единицы r. Для каждого отдельного оборудования категория сложности ремонта и соответствующее этому оборудованию число ремонтных единиц совпадают, т.е. R = r*.
* Например, символ 10R означает, что станок относится к 10-й категории сложности ремонта и у него 10 р.е.
Нормы затрат труда по видам ремонта и профилактических операций устанавливаются на одну ремонтную единицу в зависимости от вида работ и представлены в табл. 2.3.
Нормы расхода материалов при ремонте оборудования определяются расчетным методом. Единые нормативы расхода материалов при ремонте оборудования установлены на углеродистые и легированные стали, стальное литье, фасонный прокат, цветные металлы и т.п.
Таблица 2.3 – Нормы затрат труда по видам работ [4]
32